Custom antistatic warning labels are essential to protect your sensitive electronic equipment from costly static electricity damage that can lead to catastrophic failures and expensive repairs. You'll need these labels to meet specific industry standards like MIL-STD-129 and guarantee proper handling procedures are followed in your workspace. By using customized labels with clear symbols, text, and specialized features like barcodes or static dissipative surfaces, you're enhancing workplace safety while maintaining regulatory compliance. With proper ESD labeling systems in place, you can substantially reduce return rates and potentially save millions in prevention costs. Discover how implementing the right warning labels can transform your ESD control program.
Meeting Industry Specific Standards
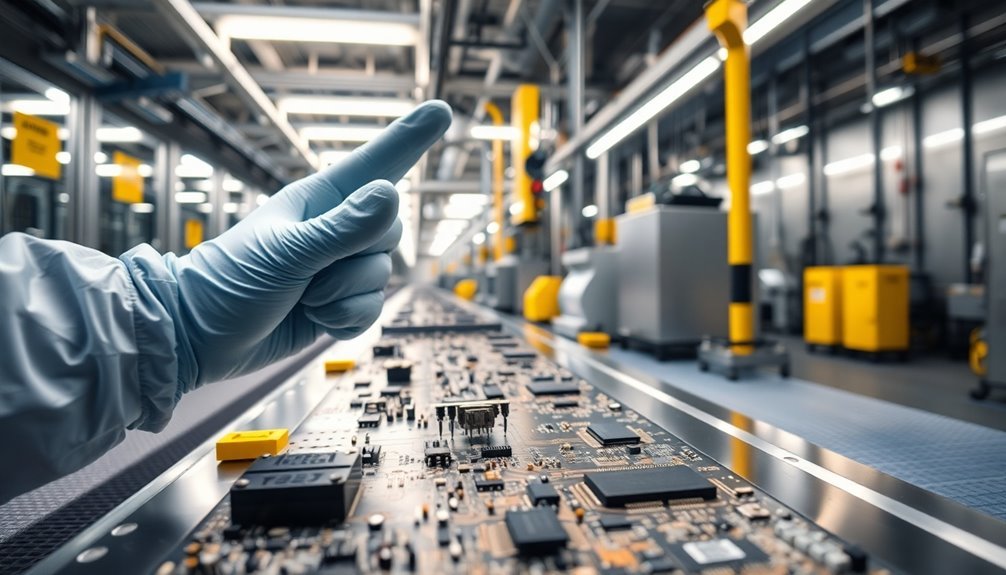
Traversing the complex landscape of antistatic warning labels requires strict adherence to multiple industry standards. When you're designing custom antistatic warning labels, you'll need to follow MIL-STD-129 requirements, which specify distinct labeling for unit packs, intermediate containers, and exterior containers.
For unit packs, you must include the ESD sensitive device attention label with the triangle and reaching hand symbol, along with specific text on a yellow background with black lettering. Temporary markings can be used if preprinted ESD labels are unavailable.
Your intermediate and exterior containers need similar warnings, but with different text requirements. You'll need to use 2" x 2" labels for intermediate containers and 4" x 4" labels for larger exterior containers.
You'll also need to comply with ANSI/ESD S20.20 standards for protecting against Human Body Model discharges, and follow JEDEC-14 standards for proper identification.
Your labels must be made from durable materials like polyester or polyimide, with adhesives strong enough to stick but clean enough to remove when needed.
Remember to verify your labels are visible from three feet away and include the standardized yellow background with black lettering and the required ESD symbol.
Protecting Sensitive Electronic Equipment
You'll need to understand how static electricity can instantly damage or create latent failures in sensitive electronic components, potentially leading to costly repairs and returns.
To protect these components, you must implement proper handling measures like using ESD-protected workstations, antistatic mats, and specialized wrist straps that ground workers during assembly or maintenance. Attention labels serve as critical visual warnings to ensure proper handling procedures are followed.
Your facility should also maintain effective monitoring control systems to guarantee consistent humidity levels and verify that all ESD protection measures remain functional and compliant with industry standards.
Static Impact on Components
Static electricity poses a significant threat to electronic components, with the potential to cause three distinct types of damage: catastrophic failure, latent damage, and upset failure. You'll find that catastrophic failures are immediately apparent, causing instant component malfunction, while latent damage might not show symptoms until much later in the product's life cycle. Implementing a static control program is essential for preventing these types of damage and ensuring long-term product reliability.
Damage Type | Characteristics | Impact |
---|---|---|
Catastrophic | Immediate failure | Easily detectable, least costly |
Latent | Hidden damage | Costly repairs, reliability issues |
Upset | Temporary disruption | Requires reset, intermittent problems |
When you're handling electronic components, it's vital to understand that static discharges can reach up to 25,000 volts, though damage can occur with as little as 4,000 volts. Your everyday activities, like walking across a carpet or brushing your hair, can generate enough static electricity to harm sensitive electronics. While catastrophic failures are easier to identify and address during manufacturing, latent damage presents a more significant challenge as it's harder to detect and can lead to expensive warranty claims and customer dissatisfaction. That's why you need proper static control measures to protect your electronic investments.
Preventive Handling Measures
Effective preventive handling measures form your first line of defense against static damage to sensitive electronic equipment. You'll need to implement thorough storage, handling, and personnel protocols to safeguard your components.
Start by using anti-static packaging materials and maintaining controlled storage environments with stable temperature and humidity levels. Keep sensitive electronics in anti-static shielding bags until they are ready for immediate use.
Your workspace setup is vital. Install proper grounding systems, anti-static mats, and workbenches to create ESD-safe areas. You'll want to equip your personnel with essential protective gear like wrist straps, foot straps, and static dissipative tools. Make sure you're using ESD-safe materials for all items that contact sensitive electronics, including labels and packaging materials.
Don't overlook the importance of training your staff in proper handling techniques. You'll need to guarantee they understand how to use static control devices and follow established safety protocols.
Keep your workspace clean and dry, as debris and moisture can increase static risks. Regular inspections will help you identify potential ESD hazards before they cause damage.
Monitoring Control Systems
Building upon proper handling measures, thorough monitoring control systems provide the next layer of protection for sensitive electronic equipment. You'll need integrated systems that combine protective devices, measuring equipment, and control mechanisms to effectively monitor your sensitive components.
Modern digital protection relays and intelligent electronic devices (IEDs) enable real-time monitoring and quick response to potential threats. These systems facilitate fault recording analysis to diagnose issues and improve reliability.
You can enhance your monitoring capabilities by implementing remote operation systems that improve response times and reliability. These systems should collect statistical data, including operation records and periodic reports, to help you analyze performance trends and identify potential issues before they escalate.
The integration of high-speed communication networks guarantees rapid response to faults and anomalies in your protected environments.
To maximize effectiveness, you'll want to incorporate advanced self-diagnostics and self-supervision features that maintain high system availability. Your monitoring control system should comply with IEC 61850 standards to guarantee interoperability and reliability.
Remember to include robust security management measures that protect against both physical and digital threats, as these are vital for maintaining the integrity of your monitoring systems.
Cost Savings Through ESD Prevention
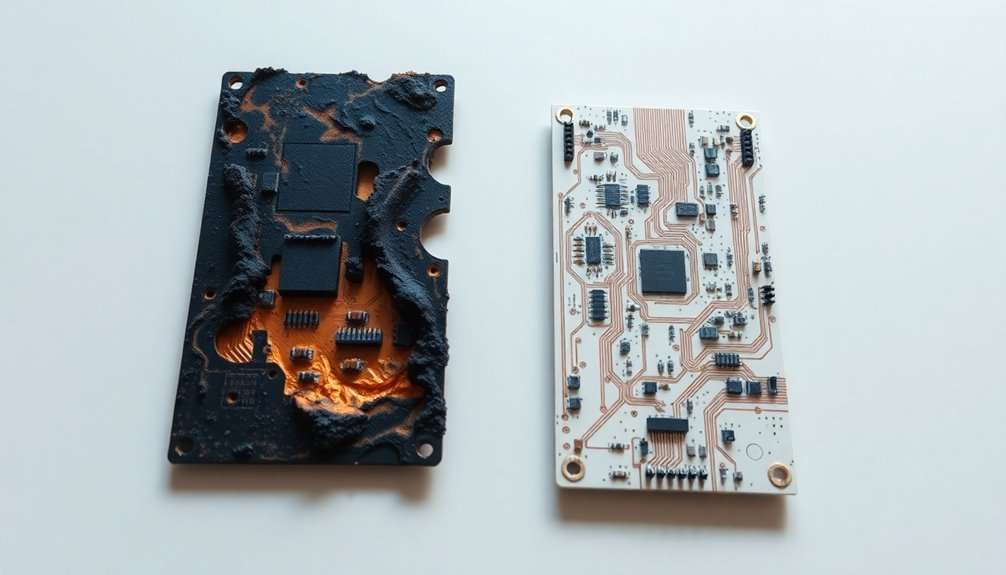
Financial data shows that electrostatic discharge wreaks havoc on company profits, with annual industry losses ranging from $500 million to $5 billion. You'll find that implementing proper ESD control programs can dramatically reduce these costs, as proven by industry leaders like AT&T, who cut their return and repair costs by more than 50%. Latent defects and failures can surface weeks or months after ESD exposure, making prevention critical.
Company | Investment Type | ROI/Savings |
---|---|---|
Lucent Technologies | ESD Control Program | 1,000% ROI |
Western Electric | Control Measures | 900-2300% ROI |
Lockheed M&S | Prevention Systems | $2M Annual Savings |
AT&T | Return/Repair Program | 50%+ Cost Reduction |
Industry Average | No ESD Control | Up to 7% Loss |
You can achieve these savings by implementing thorough ESD protection measures. Start with proper grounding systems, antistatic mats, and conducting wrist straps. Don't forget to use ESD-safe labels that reduce charge build-up during application. By establishing electrostatic protected areas (EPAs) and regularly evaluating your control measures, you'll prevent both immediate and latent damage to sensitive components. Remember, investing in ESD prevention isn't just about avoiding immediate failures – it's about protecting your long-term profitability and customer satisfaction.
Customizable Designs For Manufacturing Needs
Today's manufacturing environments demand labels that adapt to diverse production needs and regulatory requirements. You'll find that custom antistatic warning labels offer unprecedented flexibility in material choices, adhesive options, and design specifications to match your specific manufacturing processes.
Whether you're dealing with harsh solder conditions or need specialized tracking features, these labels can be tailored to meet your exact requirements while maintaining ESD protection. Like a customizable loading message, these labels can display different default messages to suit various workplace scenarios.
Your manufacturing operations can benefit from labels that incorporate:
- Multiple material options including gloss, matte, or uncoated surfaces with permanent or removable adhesives
- Custom designs featuring your company logo, specific ESD warnings, and essential product information
- Barcode integration for enhanced tracking and traceability across your production line
- Specialized features like low-charging adhesive systems and static dissipative faces for superior ESD protection
- Durable construction that withstands high temperatures, fluxes, and harsh manufacturing conditions
These customizable labels don't just meet industry standards like MIL-STD-129 P and JEDEC-14; they can be designed to address your unique production challenges.
You'll get the visibility you need through UV-resistant inks and fluorescent colors, ensuring your warning messages remain clear and effective throughout your manufacturing process.
Clear Communication Of ESD Risks
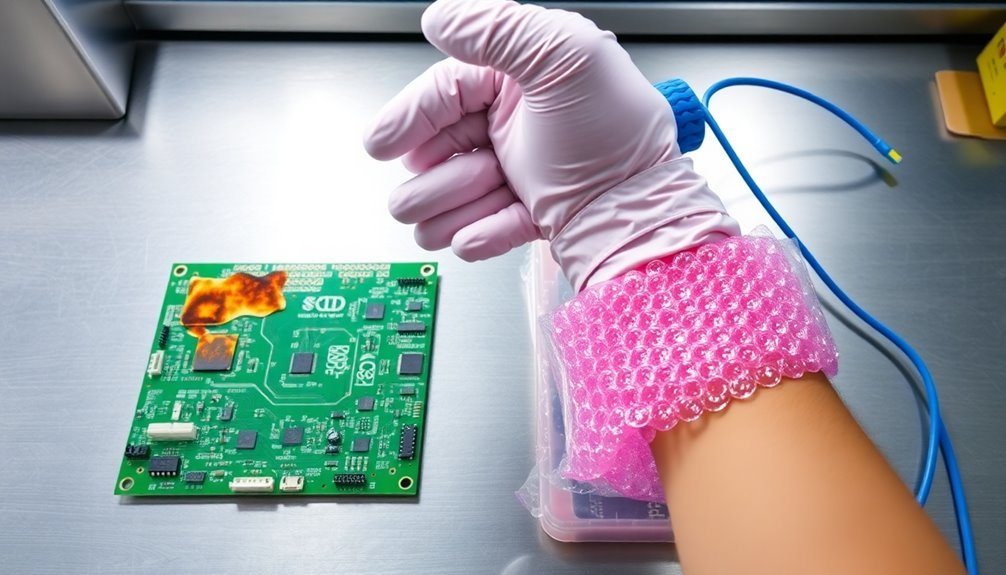
Clear communication serves as the cornerstone of effective ESD risk management in your workplace. When you implement custom antistatic warning labels, you're not just putting up signs – you're establishing a crucial system of risk awareness that protects both your employees and sensitive electronic components.
You'll need to guarantee your ESD risk messages are easily understood by everyone, from technical experts to new employees. Your warning labels should use clear, concise language while avoiding overly technical terms that might confuse non-experts.
By incorporating visual aids and recognizable symbols, you'll make the information more accessible and memorable.
To maximize effectiveness, you should coordinate your labeling system with thorough training programs and multiple communication channels. Your custom labels can serve as constant visual reminders that reinforce proper ESD handling procedures learned during training sessions.
Remember to think about cultural sensitivity and inclusivity when designing your warning labels, guaranteeing they're understood by your diverse workforce.
Enhanced Workplace Safety Measures
Implementing enhanced workplace safety measures through custom antistatic warning labels creates multiple layers of protection for your facility. By establishing thorough ESD control programs and using proper signage, you'll substantially reduce the risk of electrostatic discharge incidents.
Your workplace safety measures should include designated ESD-protected areas, properly grounded equipment, and essential protective materials like antistatic mats and wrist straps.
To maintain OSHA and ANSI compliance while protecting your sensitive equipment, you'll need to focus on these vital safety elements:
- Install clear, visible ESD warning signs in strategic locations to constantly remind employees of potential hazards.
- Provide thorough ESD safety training and regular updates to maintain employee awareness.
- Implement access control measures to guarantee only trained personnel enter ESD-sensitive areas.
- Conduct regular audits of your ESD control measures to verify their effectiveness.
- Maintain detailed records of safety protocols and incidents for continuous improvement.
Your workplace safety program should include regular maintenance of ESD control measures and quality assurance checks to guarantee all protective equipment meets industry standards. This thorough approach helps safeguard both your employees and sensitive electronic equipment from ESD-related damage.
Regulatory Compliance And Documentation
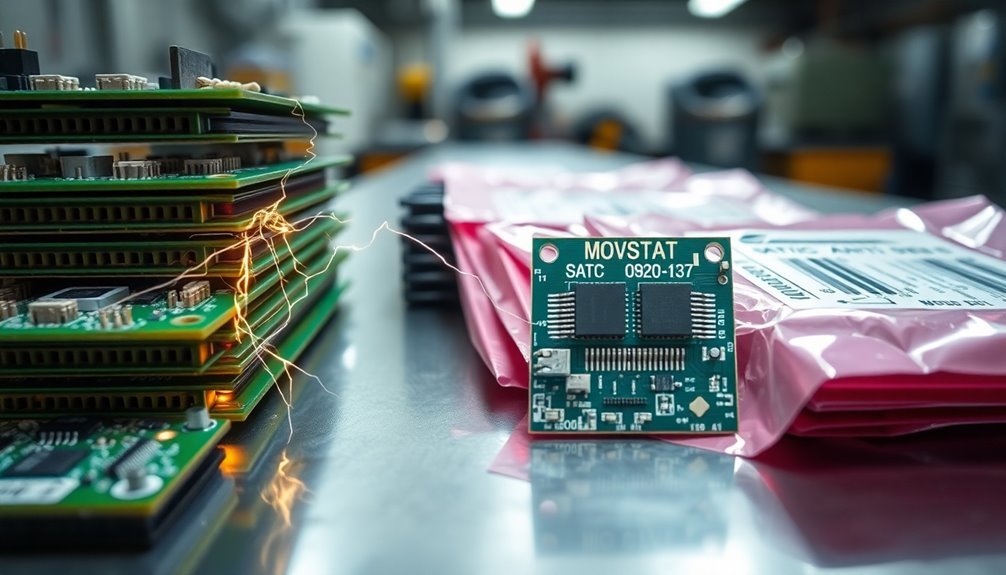
Meeting stringent regulatory requirements for ESD control demands meticulous attention to proper labeling and documentation protocols. You'll need to guarantee your labels clearly indicate whether packaging is "ESD shielding," "Conductive," or "Antistatic" to comply with standards like MIL-STD-129 and EIA-625.
For electronic devices that are static-sensitive, you must include the special marking code "39" on packaging to meet military specifications outlined in MIL-STD-129 and MIL-PRF-81705.
You're required to use labels made from static dissipative materials with low-charging adhesives that are suitable for your specific environment, whether it's a cleanroom or manufacturing facility.
Your documentation must maintain thorough records of product handling and storage. You'll need to include essential information like manufacturer name, lot number, and manufacture date on your labels for proper traceability.
Remember that non-compliance can result in penalties and damage to your company's reputation. By following these labeling requirements and maintaining detailed documentation, you're not only meeting industry standards like S20.20, 61340, and JESD625B but also protecting your static-sensitive components during handling and storage.
Frequently Asked Questions
How Long Do Antistatic Warning Labels Typically Last Before Needing Replacement?
You'll typically need to replace antistatic warning labels every 4 years under normal conditions (+20°C, 50% humidity). However, if they're exposed to harsh environments, sunlight, or chemicals, you should replace them sooner.
Can Antistatic Warning Labels Be Applied in Extreme Temperature Environments?
Yes, you can use antistatic labels in extreme temperatures, especially when they're made from polyimide. They'll maintain their ESD-protective properties while withstanding high heat, but you'll need proper mechanical attachments instead of adhesives.
Are There Color-Blind Friendly Options Available for Antistatic Warning Labels?
Yes, you'll find color-blind friendly antistatic warning labels that use contrasting blues and reds instead of problematic red-green combinations. These labels feature distinct shades and lightness levels for better visibility and comprehension.
What Cleaning Solutions Are Safe to Use on Antistatic Warning Labels?
You'll want to use non-toxic, static-reducing cleaners like Brillianize or Ohm-Stat Dissipative Mat Cleaner. Make sure your cleaning solution's compatible with label materials and meets industry standards for ESD protection.
Do Antistatic Warning Labels Need Special Storage Conditions Before Application?
Yes, you'll need to store your antistatic labels at 15-25°C with 35-65% relative humidity. For best results, aim for 22°C and 50% humidity. Improper storage can cause adhesive issues and label damage.
In Summary
Custom antistatic warning labels are essential for your facility's ESD protection program. You'll guarantee compliance with industry standards while protecting valuable electronic components from costly damage. They're your first line of defense in communicating ESD risks to workers and visitors. By investing in customized labels that match your specific needs, you're maximizing workplace safety and reducing the potential for expensive equipment failures.
Leave a Reply