ESD protective workwear is your first line of defense against costly static discharge damage in electronics manufacturing. You'll need essential items like wrist straps, anti-static footwear, and ESD-safe garments containing at least 2% carbon content. Verify that your workwear meets resistance standards of <1.0 x 10^11 ohms and complies with IEC 61340-1-5 & ANSI/ESD standards. Maintain humidity levels between 40-60% and implement regular testing protocols for all ESD gear. Proper care, including cold water washing and air drying, extends the life of your protective clothing. The following guide will equip you with everything needed to establish a complete ESD protection program.
Understanding ESD Protection Basics
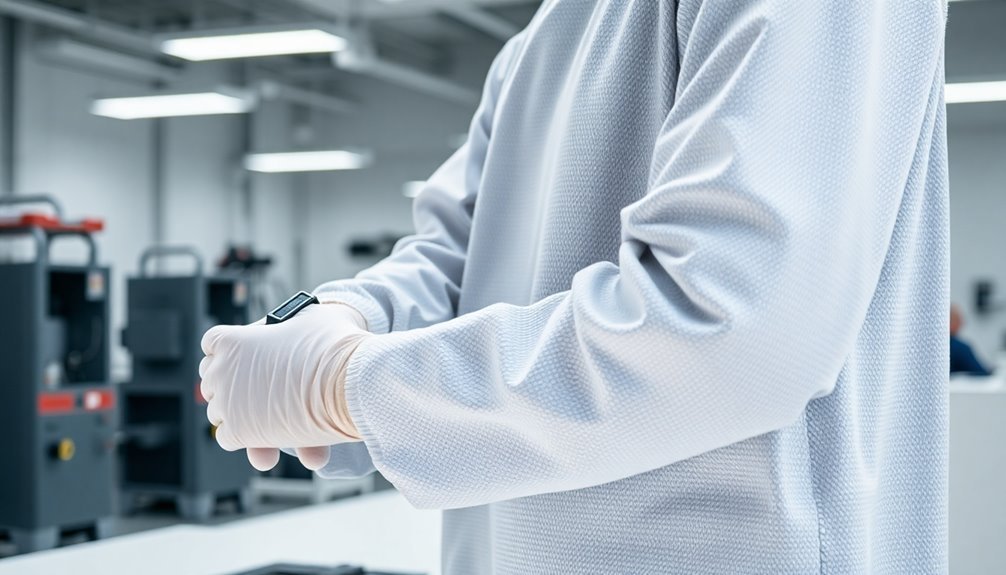
Electronics manufacturing's most critical safeguard lies in understanding ESD protection fundamentals. When you work with sensitive electronic components, you're dealing with devices that can be instantly damaged by electrostatic discharge – the sudden flow of electricity between objects at different electrical potentials. You'll find that this invisible threat occurs through simple actions like movement or material handling. The risks increase significantly when friction between surfaces generates static electricity, such as walking across carpeted areas.
You need to recognize that ESD damage isn't always immediately apparent. Your components might seem fine initially but fail prematurely during use, leading to substantial financial losses and reliability issues.
That's why you must implement thorough ESD protection in your manufacturing facility, particularly in designated ESD Protected Areas (EPAs).
Your EPAs require specific controls: anti-static flooring, grounded workstations, and proper humidity levels. You'll need to guarantee your team uses essential protective equipment, including wrist straps and anti-static footwear.
Remember that compliance with standards like ANSI/ESD S20.20 isn't optional – it's a fundamental requirement for electronics manufacturing. By maintaining proper temperature and humidity levels while minimizing external interference, you'll create an environment that markedly reduces ESD risks and protects your valuable components.
Types of ESD Protective Gear
Now that you understand the basics of ESD protection, you'll need the right protective gear to implement an effective ESD control program. The essential workwear components include PU-coated fingertip gloves, ESD aprons, caps, and antistatic slippers, all designed to prevent damaging static discharge when handling sensitive electronics. Regular training helps ensure all employees understand the proper use of protective gear and ESD control methods.
Proper grounding equipment forms your first line of defense. You'll need wrist straps to dissipate static charges from your body, along with appropriate footwear and clearly marked common point grounds.
Don't forget to install static dissipative worksurfaces at your workstations.
For component protection during storage and transport, you'll want to invest in shielding bags, corrugated boxes, and specialized ESD packaging materials. Make sure you're using ESD-safe tools during assembly and handling processes to maintain protection throughout your operations.
To guarantee your ESD protection remains effective, you'll need testing equipment and regular maintenance procedures. Keep ESD testers on hand and implement routine equipment inspections.
You should also maintain ongoing training programs for your staff and continuously monitor your workplace's ESD protection measures to meet compliance standards.
Material Requirements for ESD Workwear
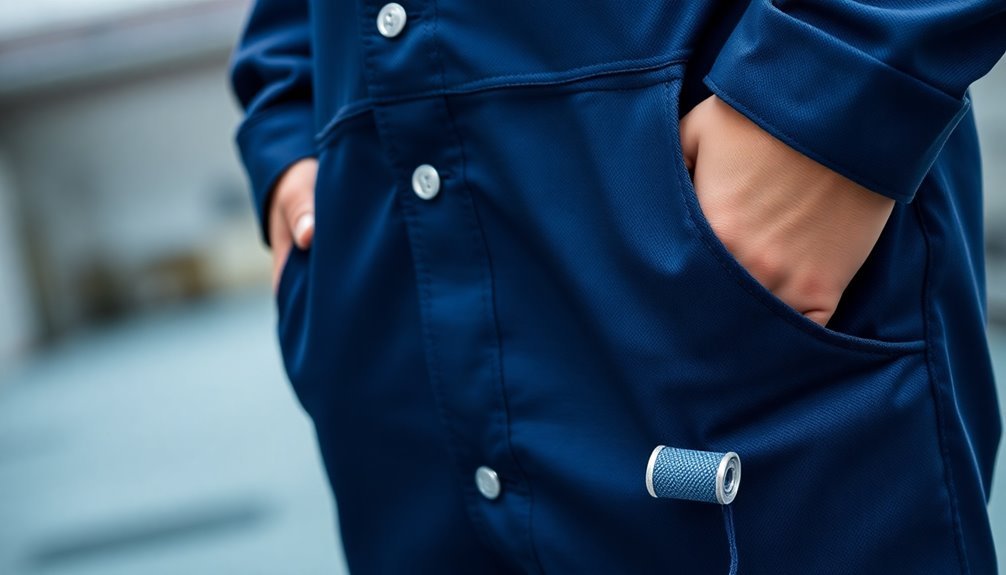
Selecting the right materials for ESD workwear isn't just about comfort – it's vital for protecting sensitive electronic components. Your ESD garments must contain at least 2% carbon content and feature conductive fibers arranged in a grid pattern to effectively dissipate static charges. These specially designed fabrics need to meet resistance standards of <1.0 x 10^11 ohms to be considered ESD compliant. Annual ESD audits are required to maintain safety compliance and verify garment effectiveness.
Property | Requirement |
---|---|
Carbon Content | Minimum 2% |
Resistance Level | <1.0 x 10^11 ohms |
Wash Durability | Multiple cycles without degradation |
Testing Standards | IEC 61340-1-5 & ANSI/ESD STM2.1:2018 |
You'll want to make certain your ESD workwear is made from water-resistant materials that can withstand regular washing without losing their protective properties. The fabric should incorporate carbon-infused monofilaments, typically woven into polyester or cotton blends. Regular testing is essential – you'll need to perform point-to-point and sleeve-to-sleeve measurements using calibrated equipment to verify compliance. Remember that proper grounding capability is essential, as these garments must effectively redirect static charges to protect your sensitive electronics.
Testing and Maintenance Procedures
You'll need to establish regular inspection protocols for your ESD workwear, including resistance testing and visual checks for wear and tear.
Your testing equipment must be properly calibrated and verified before each use, guaranteeing accurate measurements of both resistance top-to-top (RTT) and point-to-groundable point (RTG) readings.
Keep detailed maintenance records of all inspections, washing cycles, and test results to track your ESD garments' performance over time and guarantee compliance with safety standards. Staff members should use combo testers when entering ESD-protected work areas to verify their protective gear is functioning correctly.
Regular Inspection Protocols
Regular inspection protocols consist of three critical components: testing procedures, maintenance routines, and compliance verification. You'll need to test your ESD garments quarterly, measuring their electrical conductivity using resistance tests that meet IEC 61340-5-1 standards. Verify that your garments maintain surface resistance levels below specified thresholds: 1 x 10^11 Ohms for static control and 1 x 10^9 Ohms for groundable static control. The testing process requires garments to be placed on an electrically isolated surface for accurate measurements.
For maintenance, wash your ESD garments at 40°C and regularly check for wear and tear that could compromise their protective properties. Store them properly and keep your test equipment calibrated for accurate measurements.
Inspection Component | Key Requirements |
---|---|
Testing Frequency | Quarterly verification |
Resistance Testing | Conduct on insulative surface |
Maintenance | Wash at 40°C, check for damage |
Compliance Audits | Regular documentation |
Equipment Calibration | Maintain test meter accuracy |
Your compliance verification audits should follow ANSI/ESD S20.20 and IEC 61340-5-1 guidelines. Keep detailed records of your findings and any corrective actions taken. Remember to train your employees on proper ESD control procedures and verify that your suppliers provide certification that workwear meets required standards.
Equipment Verification Methods
Proper verification of ESD workwear requires three essential testing components: surface resistance measurements, grounding system checks, and integrated wrist strap testing.
Regular maintenance of humidity levels at 40-60 percent relative humidity helps minimize static generation during testing procedures.
You'll need to use an ESD meter kit to perform resistance top-to-top (RTT) and point-to-groundable point (RTG) tests across garment panels, ensuring accurate measurements by placing insulative sleeve inserts to isolate fabric sides.
For surface resistance testing, you must position the garment on an insulative surface with front panels opened flat. Connect the electrodes to your meter and measure the resistance paths between points, keeping in mind that the total system resistance should remain below 3.5 x 10^7 Ohms for integrated wrist strap garments. Don't forget to record the lowest resistance path to assess panel-to-panel conductivity.
Your grounding system verification should include regular testing of wrist straps and foot grounders, maintaining resistance levels below 3.5 x 10^7 Ohms and 1 x 10^9 Ohms respectively.
You'll want to implement continuous monitors to verify ongoing ESD integrity and use combo testers at work area entrances for wrist straps and foot grounders.
Maintenance Record Documentation
Having established equipment verification methods, maintaining accurate documentation of all ESD protective workwear testing and maintenance becomes the next priority.
You'll need to implement a thorough record-keeping system that tracks daily testing of wrist straps, footwear checks, and garment inspections. Your test log sheets must include employee initials confirming successful completion of required tests. Continuous monitoring systems can provide automated documentation of wrist strap testing results.
Your documentation should cover specific maintenance procedures, particularly for ESD garments. Record washing parameters, typically at 40°C, and note any deviations that might affect the garment's conductive properties.
You'll want to maintain detailed records of resistance measurements, from cuff-to-cuff and panel-to-panel testing, ensuring they meet the required standards of less than 3.5 x 10^7 ohms for wrist straps and below 1 x 10^11 ohms for garments.
Keep certificates of conformity from suppliers and maintain audit logs showing regular compliance checks. Your ESD coordinator should oversee these records, ensuring they're properly updated and stored.
Document all maintenance schedules, failed tests, and subsequent corrective actions. Don't forget to maintain training records that demonstrate your employees understand and follow proper ESD procedures.
Common ESD Control Mistakes
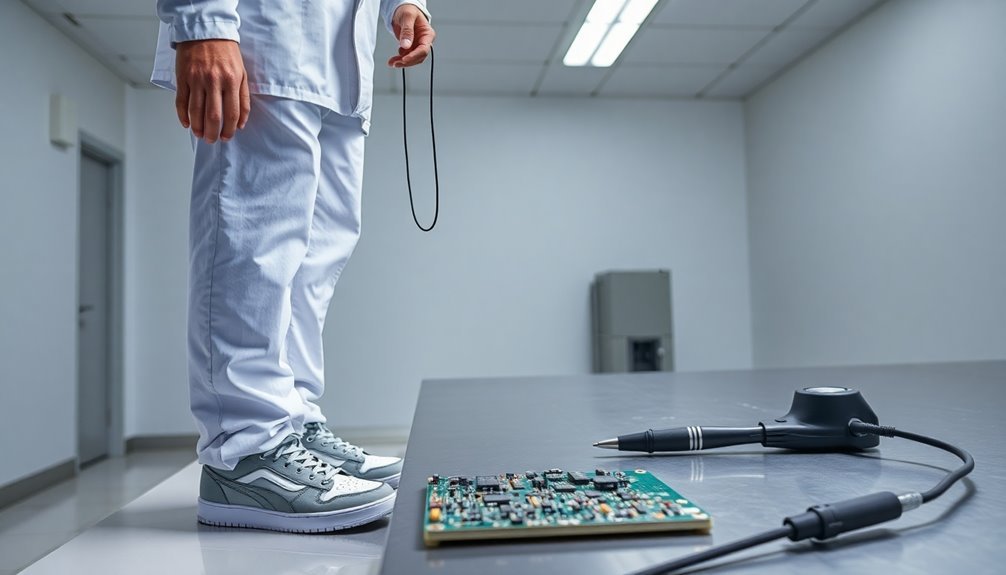
Despite the best intentions, electronics manufacturers often fall into several common traps when implementing ESD control measures. Training oversights rank among the most frequent mistakes, with many companies failing to provide thorough ESD awareness education to all personnel or neglecting to conduct regular refresher courses. Ensuring all staff members follow detailed ESD guidelines for wrist straps and grounding ports is crucial for maintaining safety standards.
You'll find that without proper testing and follow-up, employees may forget essential protective measures over time.
Equipment and material-related errors can severely compromise your ESD protection program. Using non-ESD safe packaging, ungrounded workbenches, or inappropriate cleaning products can create unnecessary risks. You're particularly vulnerable when staff members use standard tools instead of ESD-safe alternatives.
Personal protective equipment mistakes are equally problematic. If you're not regularly testing wrist straps and heel grounders or enforcing strict wearing policies, you're creating gaps in your ESD defense system. Worn-out ESD clothing that's lost its antistatic properties won't protect your components effectively.
Don't overlook maintenance and testing errors. You should regularly audit your ESD control measures, maintain ionizers properly, and validate reused shielding bags. Without consistent testing and documentation of your ESD protection measures, you can't guarantee reliable protection for sensitive electronic components.
Workplace Implementation Best Practices
You'll need to prioritize thorough ESD training for your staff, ensuring they understand proper grounding techniques and the consistent use of protective gear.
Establish clearly marked ESD-protected areas (EPAs) with all necessary safety equipment, including wrist straps, dissipative mats, and appropriate signage at entry points.
Your implementation should include regular audits of these safety zones to verify that all personnel are following protocols and that equipment remains properly grounded and functional.
Training Staff Effectively
Three key elements make ESD training an essential component of electronics manufacturing: thorough education, consistent reinforcement, and practical application. You'll need to establish a detailed training program that covers both theoretical knowledge and hands-on experience to guarantee your staff understands ESD risks and prevention methods.
Implement regular training sessions that combine classroom learning with practical demonstrations. You should conduct refresher courses quarterly or bi-annually to prevent complacency and maintain high safety standards.
Don't limit ESD training to just technical staff – include everyone in your facility to create a culture of ESD awareness.
Your training program should include these critical components:
- Hands-on demonstrations of proper grounding techniques and workstation protocols
- Case studies highlighting real consequences of ESD damage
- Regular toolbox talks to reinforce daily ESD safety practices
- Practical exercises using ESD measurement tools and protective equipment
- Assessment mechanisms to verify understanding and compliance
Remember to document all training activities and conduct regular audits to guarantee compliance with industry standards like ANSI/ESD S20.20-2016.
Setting Up Safety Zones
Building on your staff's ESD training, implementing well-designed safety zones forms the backbone of an effective ESD protection strategy. Start by identifying areas where ESD-sensitive components are handled and designate these as Electrostatic Protected Areas (EPAs).
You'll need to conduct a thorough risk assessment to determine where your highest ESD risks exist.
Within your EPAs, install proper grounding infrastructure, including conductive flooring and workstation mats connected to a common ground point. Equip these zones with essential protective gear such as wrist straps and footwear for your personnel.
Consider adding ionizers to neutralize static electricity in areas where sensitive components are frequently handled.
Develop clear standard operating procedures (SOPs) that outline specific ESD control measures for each safety zone. You'll want to detail proper grounding techniques, handling protocols, and required protective equipment.
Keep your EPAs clean and free from static-generating materials, and restrict access to authorized personnel only.
Remember to regularly test your ESD equipment and update your procedures as needed. By maintaining strict control over these designated safety zones, you'll substantially reduce the risk of ESD damage to your electronic components.
Selecting Appropriate ESD Clothing
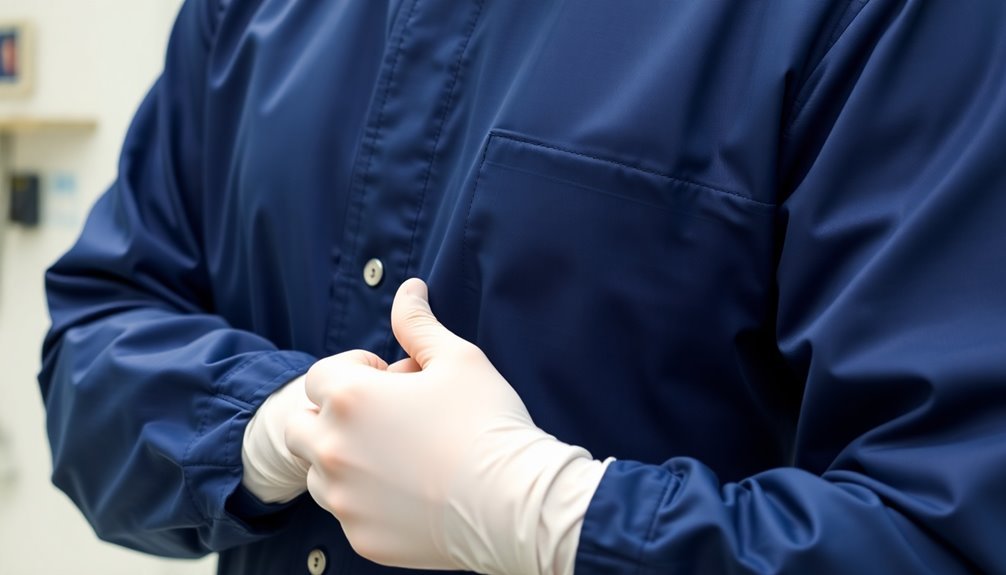
Selecting the right ESD clothing comes down to understanding your specific work environment and the level of protection needed. You'll need to take into account factors like the type of electronics you're handling and the duration of exposure to sensitive components.
When choosing ESD protective wear, focus on garments that incorporate conductive fibers and meet the CEI EN 61340-5-1 standard. The clothing should provide complete coverage while guaranteeing comfort during long work hours.
You'll find various options ranging from lab coats to polo shirts, each designed for specific work scenarios.
Key considerations when selecting ESD clothing:
- Look for garments with well-designed cuffs that maintain skin contact for proper grounding
- Choose materials that blend comfort with protection, such as cotton-polyester with conductive yarn
- Verify that the clothing provides adequate coverage for your specific work position
- Select appropriate sleeve lengths based on your facility's requirements
- Evaluate the garment's durability and maintenance needs for long-term cost-effectiveness
Remember to pair your ESD clothing with proper footwear and regularly inspect all items for wear and tear. You'll need to follow specific washing instructions to maintain the garments' protective properties throughout their lifecycle.
Cost Analysis and ROI
While choosing the right ESD workwear is important, understanding its financial impact helps justify the investment. With annual ESD losses ranging from half a billion to five billion dollars, you'll find that implementing proper protection measures isn't just a safety requirement—it's a smart business decision.
Studies have consistently shown that ESD protection delivers remarkable returns, with ROI ranging from 900-2300%. You can expect to see a significant reduction in defect rates, with some companies reporting a 3:1 improvement after implementing ESD controls.
When you consider that just 25 electrostatic volts can destroy an integrated circuit, the cost of protection becomes minimal compared to potential losses.
While you might be tempted to opt for cheaper ESD workwear options, this approach often leads to higher long-term costs. Instead, focus on quality garments that offer durability, easy maintenance, and effective static dissipation properties.
Companies have reported annual savings of up to $2 million through thorough ESD control measures. By investing in high-quality ESD protective clothing that meets international standards like ANSI/ESD S20.20, you're not just buying garments—you're investing in protection that delivers measurable cost savings.
Global Standards for ESD Protection
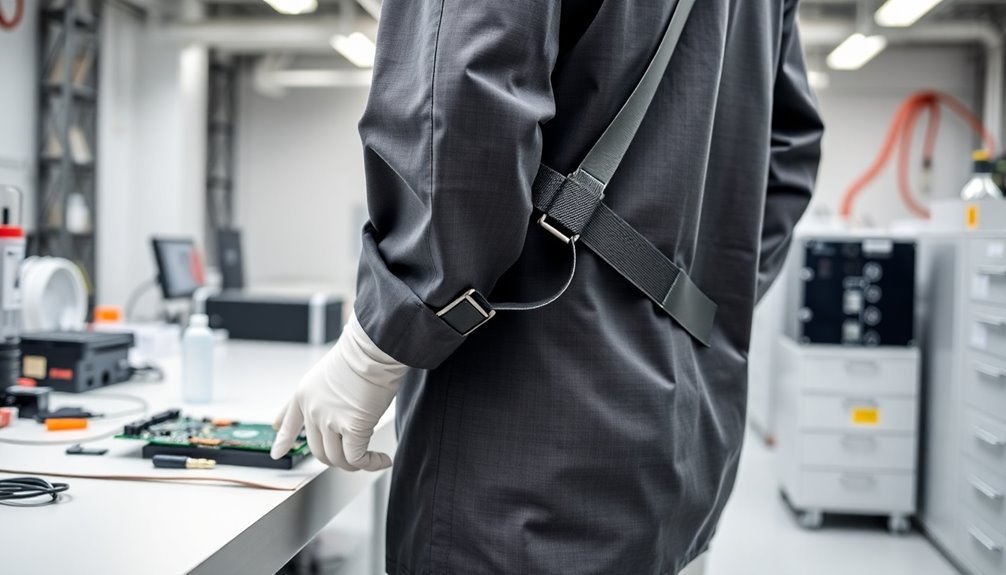
Traversing global ESD protection standards can seem intimidating, but understanding the key requirements is essential for electronics manufacturers. You'll need to comply with several major standards, including ANSI/ESD S20.20, IEC 61340-5-1, and JEDEC JESD625B, depending on your market and products.
To guarantee your workwear meets global standards, you'll want to focus on these critical requirements:
- Establish thorough ESD control programs that include protective clothing and accessories
- Implement proper grounding techniques through wrist straps and other conductive elements
- Maintain documentation of your ESD protection measures and regular testing results
- Train personnel in proper ESD control practices and provide certification
- Conduct regular audits to verify compliance with applicable standards
Your workwear program must align with both regional and industry-specific requirements. For instance, if you're operating in Europe, you'll need to follow DIN EN 61340-5-1 guidelines.
Military suppliers must adhere to MIL-STD-1686 specifications. Remember that compliance isn't just about meeting standards—it's about maintaining your competitive edge and protecting your business opportunities in the global marketplace.
Frequently Asked Questions
How Often Should ESD Protective Workwear Be Replaced?
You'll need to replace your protective wear based on usage and environment, typically every 200 hours or 3 months in high-risk areas. Test regularly and replace more frequently if strict standards require it.
Can ESD Protective Clothing Be Washed With Regular Laundry Detergent?
You can use regular liquid detergent, but don't choose ones with fabric softeners or bleach. It's best to use non-ionic detergents to maintain the garment's electrostatic properties and extend its protective lifespan.
Do Employees Need ESD Protection When Working Remotely With Electronics?
Yes, you'll need ESD protection when working remotely with electronics. You must use grounded workstations, wear ESD-protective clothing, and follow proper handling procedures to prevent damage to sensitive electronic components.
What Happens if ESD Clothing Gets Torn During Work?
You'll need to change your torn ESD garment immediately as it won't protect against static discharge. Your damaged clothing can expose devices to harmful static electricity and compromise workplace safety standards.
Can ESD Protective Gear Be Shared Between Different Shift Workers?
You shouldn't share ESD protective gear between shifts. It'll compromise hygiene, reduce grounding effectiveness, and affect proper fit. Using personal gear guarantees consistent protection and helps maintain compliance with safety standards.
In Summary
You'll find that proper ESD protective workwear is essential for safeguarding your electronic manufacturing operations. Don't underestimate the importance of choosing certified gear, maintaining it correctly, and training your staff in proper usage. By following global standards and implementing thorough ESD control measures, you're protecting your products, reducing costly failures, and ensuring workplace safety. Make ESD protection a non-negotiable part of your manufacturing process.
Leave a Reply