Protect your electronic components by choosing the right anti-static foam for your manufacturing needs. You'll find three main types: conductive foam (black, <10^6 ohms resistance), anti-static foam (pink, 10^9-10^12 ohms), and static dissipative foam (10^5-10^9 ohms). For sensitive components, use high-density foam to maximize protection against shock and vibration. Don't forget to take into account reusability – conductive foam can be reused, while anti-static foam typically can't be. Always pair your foam with proper grounding systems and establish clear static control protocols in your workspace. The deeper you explore foam protection options, the better equipped you'll be to safeguard your valuable electronics.
Understanding Anti-Static Foam Properties
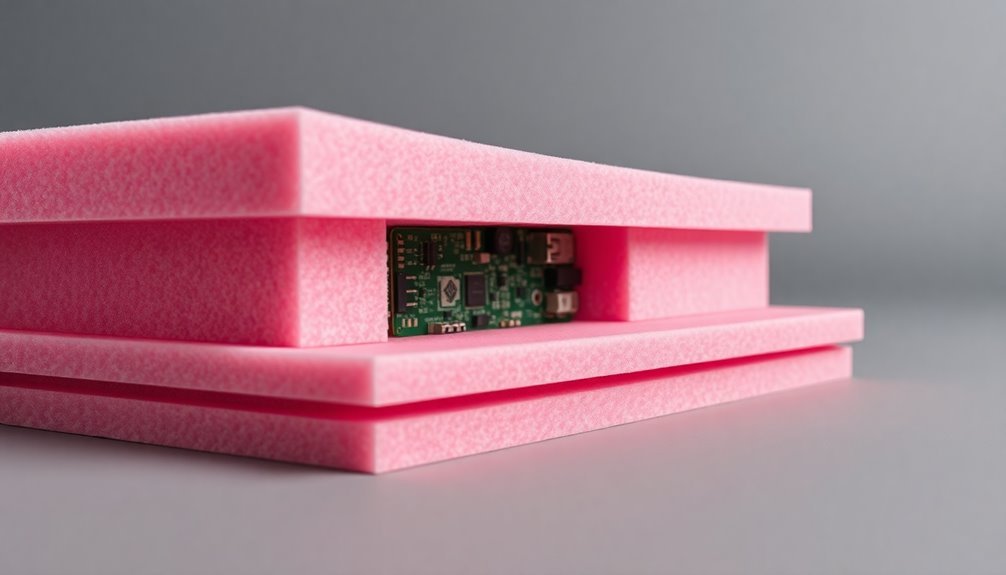
Protection against static electricity is essential in electronics manufacturing, and anti-static foam plays a critical role in safeguarding sensitive components.
Conductive foam, typically black in color, contains carbon-filled polyethylene and offers surface resistance below 10^6 ohms. It acts as a Faraday cage to block electromagnetic fields, but you'll need to insulate it to prevent battery drainage.
Anti-static foam, usually pink, uses static dissipative polyurethane and polyethylene with resistance between 10^9 and 10^12 ohms, though it isn't reusable and requires additional shielding. The foam's superior cushioning abilities make it ideal for protecting circuit boards and computer chips during transport.
Static dissipative foam allows charges to flow slowly to ground, with resistance ranging from 10^5 to 10^9 ohms. You'll see it in pink or black varieties, and it's effective at preventing initial discharges from human contact.
The foam's structure varies by material type – PE and EVA foams feature closed-cell structures, while PU foam has an open-cell design.
When selecting foam, you'll need to evaluate surface resistance, reusability, and whether additional shielding is required for your specific application.
Selecting Proper Foam Density
Choosing the right foam density is crucial when protecting electronic components from physical damage and environmental factors. You'll need to understand that higher density foams provide enhanced protection through better shock absorption and vibration dampening, while lower density options offer less protection but may be suitable for less sensitive components.
When you're selecting foam density, consider that the manufacturing process profoundly influences the foam's protective properties. The isocyanate index and water content during production directly affect the foam's density and porosity. Custom foam inserts provide precise dimensional control for optimal component protection.
You'll want to pay attention to these factors as they'll determine the foam's ability to protect your electronics.
For critical electronic components, you should opt for higher density foams, especially in aerospace or medical equipment applications. These denser materials will maintain stable operating temperatures and provide superior insulation.
You can also consider multilayer packaging solutions that combine different foam densities for thorough protection.
For ESD-sensitive components, you'll need to select anti-static foams with specific densities that match your protection requirements. Remember that you can customize foam densities to meet your specific electronic packaging needs, ensuring the best protection for your components.
Essential Foam Protection Features
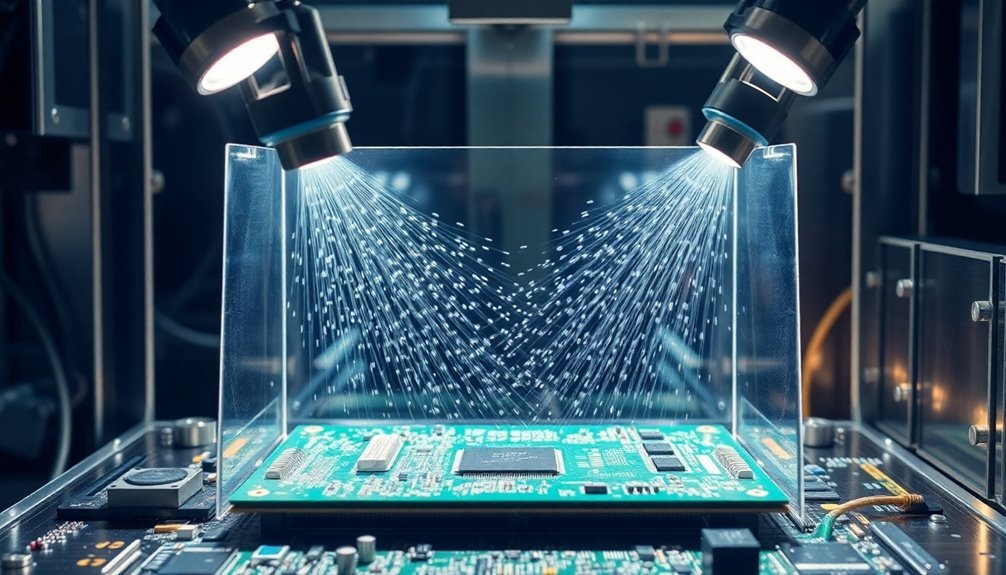
When you're selecting foam protection for electronics manufacturing, you'll need to carefully evaluate the strategic density requirements for each component type you're protecting.
Your foam density choices should match the specific weight, fragility, and vibration sensitivity of different electronic parts while accounting for potential impact forces during handling and shipping.
You must also identify critical protection zones where components are most vulnerable, ensuring enhanced cushioning and anti-static properties are concentrated in these areas. Consider using closed-cell polyethylene foam to provide superior shock absorption and vibration dampening for sensitive electronics.
Strategic Foam Density Selection
Four essential features define strategic foam density selection in electronics manufacturing: versatility, shock absorption, static protection, and environmental resilience.
When selecting foam density for your electronic components, you'll need to match specific materials with your protection requirements. Polyurethane and polyethylene foams offer customizable solutions for various component shapes, while EPS provides excellent stress resistance for impact protection. For static-sensitive devices, you'll want to incorporate anti-static or conductive foams that prevent ESD damage by creating a protective Faraday cage effect. Proper foam selection leads to reduced shipping damage and fewer product returns.
Foam Type | Key Benefits | Best Applications |
---|---|---|
Polyurethane | Lightweight, customizable density | Delicate components |
Polyethylene | Durable, impact resistant | Heavy electronics |
EPS | Cost-effective, stress resistant | General packaging |
Environmental factors will substantially influence your foam density selection. You'll need to take into account moisture resistance, particularly when using EPE foam, and account for ambient conditions that might affect foam performance. Remember to evaluate your product's fragility level to determine the appropriate density for shock protection, and implement quality control measures to maintain consistent foam performance throughout your manufacturing process.
Critical Protection Zones
Strategic foam density selection naturally leads to understanding the key protective zones required for electronics manufacturing. You'll need to focus on multiple critical areas where your electronic components require thorough protection against both physical and electrical threats.
The most effective anti-static foam solutions address these zones through tailored protection features that work together to safeguard your valuable components. Regular ESD control audits help verify the ongoing effectiveness of foam protection measures.
- Conductive outer layers with resistance values of 10^3-10^5 provide your first line of defense against static discharge
- Custom-cut cradle zones that perfectly fit your components guarantee stability and minimize movement during transport
- Impact absorption areas featuring PE or PU materials protect against sudden shocks and vibrations
- Moisture-resistant barrier zones help shield sensitive electronics from environmental damage
- Anti-abrasion surfaces with class A finishing prevent scratches and surface wear
When implementing these protection zones, you'll want to guarantee your foam solutions meet RoHS compliance standards while maintaining proper static dissipation properties.
The combination of ESD containers with precisely tailored foam inserts creates a complete protection system that addresses both static and physical threats to your electronic components.
Custom Packaging Solutions
When you're selecting custom packaging solutions for electronics, you'll need to think about specific material properties like anti-static capabilities, compression strength, and chemical resistance.
The size and shape of your foam packaging must accommodate your electronic components precisely, with options ranging from die-cut inserts to molded foam enclosures that provide exact dimensional control. Custom thermoformed packaging solutions can be manufactured efficiently for high-volume production needs.
Your foam density selection is vital, as it must balance protective cushioning with cost-effectiveness, typically requiring between 1.5 and 6 pounds per cubic foot depending on the component's weight and fragility.
Material Selection Guidelines
Material selection serves as the cornerstone of effective custom packaging solutions in electronics manufacturing. When you're choosing materials for your electronic packaging needs, it's critical to consider both the physical properties and environmental impact of your selections.
You'll need to evaluate density, firmness, and flexibility while guaranteeing proper ESD protection for sensitive components. Materials like conductive cardboard trays are commonly integrated into transport and storage solutions.
To make informed decisions about packaging materials, focus on these key considerations:
- Select antistatic foam materials that prevent ESD buildup, particularly when working with sensitive electronic components
- Choose materials that offer appropriate density and firmness to protect against shock and vibration during transport
- Consider recyclable and biodegradable options like polyethylene foam to minimize environmental impact
- Evaluate the material's compatibility with your manufacturing processes, including die cutting and CNC routing
- Guarantee the selected material allows for precise customization to match your specific component dimensions
You'll want to work closely with foam material suppliers to identify the best solutions for your unique requirements. Remember that proper material selection impacts not just protection but also the long-term reliability of your electronic devices.
Size and Shape Options
Custom packaging solutions come down to getting the right fit for your electronic components through precise size and shape specifications. You'll find multiple options available, from sheet forms that can be cut to your exact requirements to die-cut forms designed for specific electronic devices.
When you're selecting the right size and shape option, you'll want to take into account vacuum form trays for components that need a precise fit, or textile bag packaging for more flexible storage needs. If you're looking for long-term solutions, reusable containers can be customized to your specific dimensions and component organization requirements. The pure nitrogen gas manufacturing process used in Evazote foams ensures consistent surface quality across all packaging shapes.
The manufacturing process you choose will impact your final packaging shape. You can opt for thermal die cutting when you need intricate cuts for precise components, or CNC routing for detailed packaging designs.
Water jet cutting offers high precision for delicate electronics, while foam processing allows for tailored solutions that conform to various electronic shapes.
Remember to factor in your component dimensions and shape adaptability requirements. Your packaging must provide adequate cushioning while maintaining efficient storage capabilities, all while ensuring proper static protection for sensitive electronic components.
Density Level Requirements
Understanding foam density levels stands at the forefront of effective electronics protection. You'll find that density ranges typically span from 0.5 to 2.2 lbs/ft^3 for anti-static foams, with each density level serving specific protection needs.
When selecting the right density for your electronics packaging, think about both the weight and fragility of your components.
For the best protection of your electronic components, you'll need to match the density to your specific requirements. Low-density conductive foams work best for transit packaging and cushioning static-sensitive components, while high-density options provide better support for legged components and heavier items.
- Low-density foams (0.5-2.2 lbs/ft^3) offer superior flexibility and cushioning for circuit boards
- High-density foams (1.7-4.0 lbs/ft^3) provide rigid support for pin protection
- PE foams (45kg/m^3) deliver excellent moldability for custom shapes
- EVA foams (85kg/m^3) offer enhanced durability and shock absorption
- Conductive foams feature lower surface resistivity for ideal grounding
Remember that environmental factors like humidity can affect foam performance, so you'll want to think about these conditions when selecting your density level. Your choice should balance cushioning needs with the required conductivity for your specific application.
Types of Electronic Foam
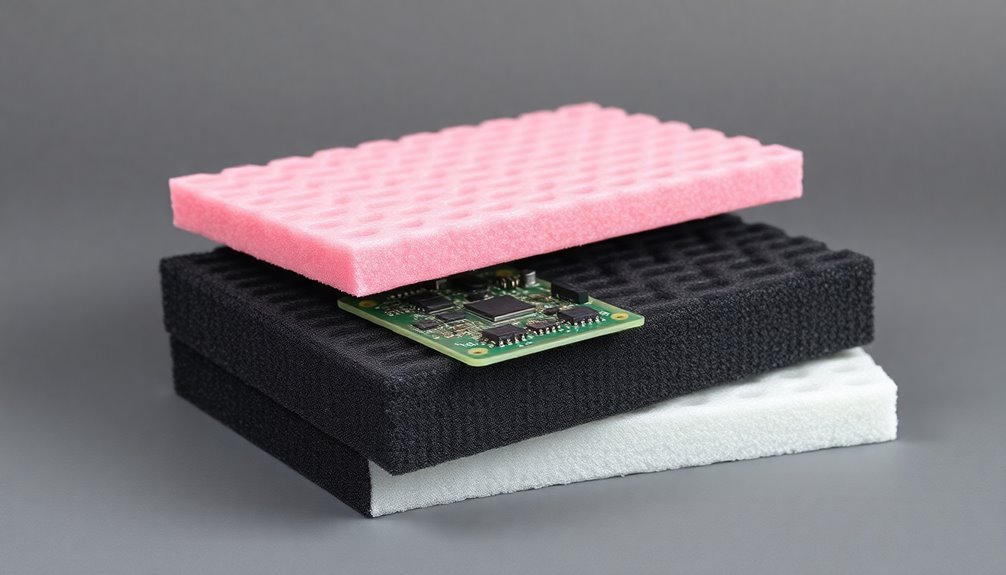
Several distinct types of electronic foam serve crucial roles in protecting sensitive components during manufacturing, storage, and transit.
Conductive foam, typically black in color, offers thorough protection by creating a Faraday cage around your components, effectively preventing static buildup. This type eliminates the need for additional static shielding bags.
Pink anti-static foam provides a different level of protection by dissipating static charges that build up from friction. While it's not as protective as conductive foam, you'll often use it alongside static shielding bags for complete protection.
Blue static dissipative foam offers a middle ground, allowing for gradual discharge that prevents sudden static shocks.
You've also got specialized options at your disposal. Carbon-based foams provide EMI shielding with lightweight flexibility, while nickel-coated variants offer enhanced conductivity for demanding applications.
If you're looking for specific material properties, EVA foam delivers higher density than PE foam, and EPE foam features a closed-cell structure with anti-static properties.
For varied packaging needs, PU foam comes in both conductive and anti-static versions to suit your requirements.
Static Control Best Practices
Every successful electronics manufacturing operation relies on robust static control practices to protect sensitive components. You'll need to implement a thorough approach that combines proper grounding techniques, ionization solutions, and static charge reduction methods.
Start by establishing a detailed grounding program that connects all work surfaces, equipment, and personnel to a common ground. Install ionizers in critical areas to neutralize static charges, particularly in assembly and packaging zones where sensitive components are handled. Make sure you're regularly maintaining these systems to achieve optimal performance.
Here are key practices you'll want to implement:
- Set up clearly defined Electrostatic Protected Areas (EPA) with proper signage and access controls
- Replace static-generating materials with conductive or dissipative alternatives
- Install thorough grounding systems with regular testing protocols
- Position ionizers strategically throughout your manufacturing areas
- Provide ongoing training to guarantee staff understand and follow ESD procedures
Remember to regularly inspect your static control measures and update your ESD program as needed. You should focus on minimizing static-generating processes while maintaining proper grounding connections and ionization equipment.
This systematic approach will help protect your electronic components from costly damage.
Storage and Transportation Guidelines
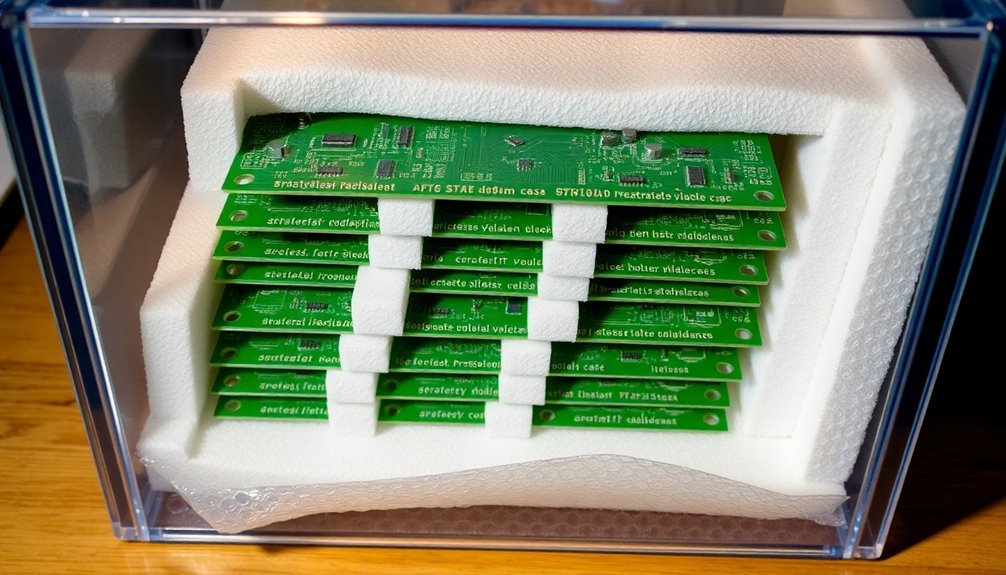
Protecting electronic components during storage and transportation demands meticulous attention to specialized packaging materials and handling procedures. You'll need to implement proper static protection measures using anti-static foam and ESD bags to safeguard sensitive electronics from electrostatic discharge.
When storing components, you must maintain a controlled environment that shields them from extreme temperatures, humidity, and light exposure. Make certain you're using properly sealed packaging to prevent dust and moisture infiltration.
You'll want to establish a systematic inventory management approach to minimize handling and reduce the risk of static damage.
For transportation, you should select custom-fit anti-static foam packaging that prevents movement and reduces friction-generated static electricity. It's crucial to secure all packages properly and use climate-controlled vehicles during transit.
You'll need to implement tracking systems to monitor shipments and guarantee timely delivery.
When choosing foam materials, you must consider factors like density, surface resistance, and flexibility. Select foam that meets industry standards such as EIA-541 and holds relevant ISO certifications.
Don't forget to evaluate the foam's reusability and environmental impact while guaranteeing it provides adequate physical protection against shocks and vibrations.
Foam Quality Testing Methods
In accordance with industry standards, foam quality testing requires rigorous evaluation through multiple standardized methods. You'll need to follow ASTM D3574 guidelines for thorough mechanical testing, which covers essential properties like compression, tensile strength, and tear resistance.
For electronics manufacturing protection, it's vital to conduct both static and dynamic foam analysis to achieve optimal performance.
When testing your foam materials, you should focus on these key aspects:
- Indentation Force Deflection (IFD) and Compression Force Deflection (CFD) measurements using universal testing machines
- Dynamic foam stability analysis through light transmission and bubble size distribution tracking
- Time-resolved imaging to monitor structural changes and foam degradation
- Mechanical property assessment using specialized software like TestXpert
- Ross-Miles or Rudin testing for foam height and stability evaluation
You'll want to utilize both standard and specialized testing methods to get a complete picture of your foam's protective capabilities. The combination of mechanical testing and dynamic analysis helps guarantee your anti-foam protection meets the stringent requirements for electronics manufacturing.
Remember to document all test results and maintain consistent testing conditions for reliable comparisons between different foam samples.
Environmental Impact of Foam Materials
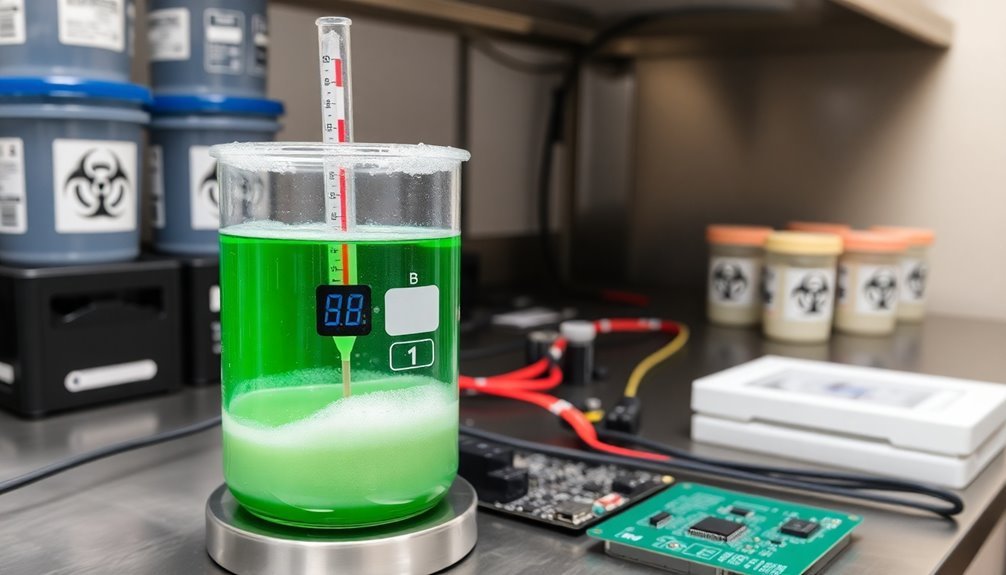
The environmental footprint of foam materials in electronics manufacturing raises significant concerns that you'll need to address. Traditional foam production relies heavily on petroleum-based chemicals and releases harmful hydrofluorocarbons (HFCs), which have a global warming potential thousands of times greater than carbon dioxide.
When you're selecting foam materials for your electronics manufacturing processes, you'll find that many conventional options aren't easily recyclable and contribute to landfill waste. They also release volatile organic compounds (VOCs) during production, which can impact both air quality and worker health.
However, you can now choose from several eco-friendly alternatives that minimize environmental impact. Consider using foams made from sustainable or recycled materials, such as biodegradable polyurethane or sodium alginate-based options. These materials reduce your reliance on non-renewable resources while maintaining protective qualities.
You'll also benefit from incorporating natural fillers like cellulose or activated carbon, which enhance sustainability without compromising performance.
To further reduce your environmental impact, you should prioritize foam suppliers who use renewable energy in their production processes and implement waste reduction strategies in your manufacturing operations.
Frequently Asked Questions
How Long Does Anti-Static Foam Maintain Its Protective Properties?
Your anti-static foam's protective properties can vary widely, typically lasting 1-2 years under ideal conditions. You'll need to test it regularly since humidity, handling, and storage conditions affect its effectiveness over time.
Can Anti-Static Foam Be Reused for Different Electronic Components?
You shouldn't reuse anti-static foam for different electronics as it loses effectiveness over time. The foam's protective properties decline with use, and different components require specific static protection levels for safety.
What Temperature Range Can Anti-Static Foam Safely Operate In?
You'll find different ranges depending on the foam type: Polyethylene works from -10 to 85°C, Polyurethane spans -10 to 85°C, while Silicone foam offers the widest range from -100 to +250°C.
Does Humidity Affect the Performance of Anti-Static Foam?
Yes, humidity substantially affects your anti-static foam's performance. You'll get the best results between 30-70% RH, with 40% being ideal. Higher humidity enhances static dissipation, while low humidity reduces the foam's effectiveness.
How Should Anti-Static Foam Be Disposed of After Its Lifecycle?
You'll need to properly identify your anti-static foam type first. Dispose of it through recycling if possible, or use specialized facilities for hazardous materials. Follow local regulations and manufacturer's guidelines for safe disposal.
In Summary
You'll maximize your electronics' protection by choosing the right anti-static foam and following proper handling protocols. Remember to test foam quality regularly, maintain appropriate storage conditions, and consider eco-friendly options when possible. By implementing these protective measures and staying current with static control best practices, you're ensuring your electronic components remain safe throughout manufacturing, storage, and transport.
Leave a Reply