Your electronics manufacturing operation needs proper anti-static foam protection to prevent costly ESD damage. You'll want to choose between four main types: ESD PE foam for high-level protection, ESD EVA foam for flexibility, ESD EPE foam for softer cushioning, and ESD PU foam for stable conductivity. Select foam density based on your specific needs – from ultra-low for delicate components to high density for maximum impact resistance. Implement proper workstation safety by using grounded surfaces and custom-cut foam inserts. The deeper you explore these protective measures, the more you'll safeguard your valuable electronic components.
Types of Anti-Static Foam Materials
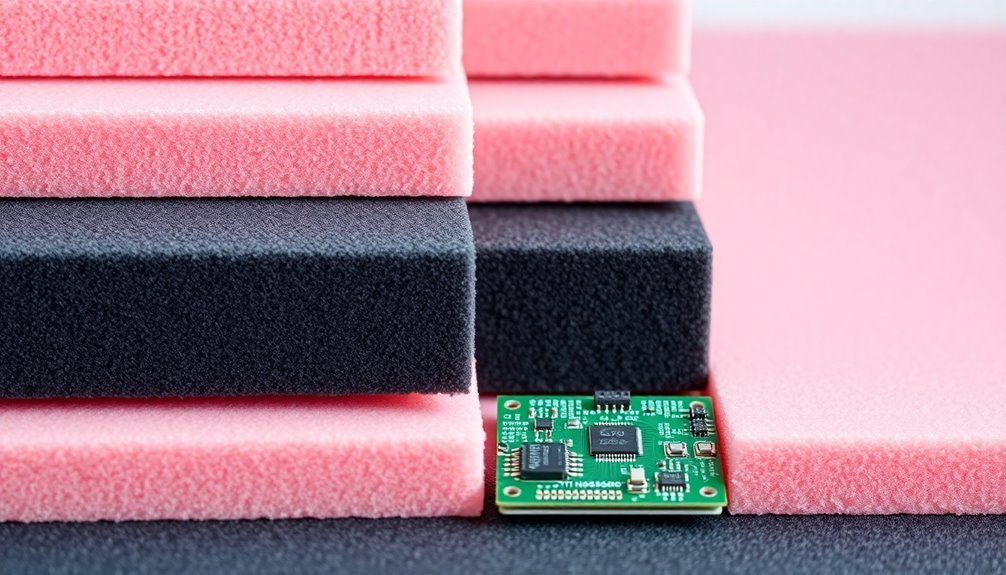
Anti-static foam materials come in four primary varieties for electronics manufacturing: ESD PE, ESD EVA, ESD EPE, and ESD PU foam. Each type offers distinct characteristics that make it suitable for specific electronic protection needs.
ESD PE foam, produced through crosslinking and foaming of permanent antistatic polyethylene, provides high-level anti-static protection and can be transformed into sheets, rolls, and blocks. These materials maintain a regular density of 45-67kg/m3.
ESD EVA foam is particularly versatile due to its superior flexibility and molding capabilities, with single layer thickness reaching up to 70mm – making it ideal for general electronic component packaging.
If you're looking for a softer option, ESD EPE foam features a non-cross-linked closed-cell structure with surface resistance of 10^8-10^11. It's typically available in pink or red and receives its anti-static properties through specialized liquid treatment.
For sensitive electronic components, you might want to take into account ESD PU foam, which features an open-cell structure with an internal conductive network. Its anti-static properties remain stable even after post-processing, and you can customize it to meet specific size requirements while maintaining consistent protection levels.
Essential Properties of ESD Protection
Effective ESD protection relies on four fundamental material properties that work together to safeguard electronic components. You'll find conductive materials that allow electrons to flow easily, dissipative materials that control charge flow to ground, anti-static materials that prevent charge buildup, and insulative materials that limit electron movement. The use of grounding wrist straps is essential for safely dissipating static charges from workers handling components.
When you're working with these materials, it's vital to maintain proper environmental conditions, as temperature and humidity substantially impact their performance.
To guarantee the best protection of your electronic components, you'll need to store them in specially designed ESD-safe containers that meet industry standards like IEC 61000-4-2. These containers work with your controlled environment to provide thorough protection against static damage.
- Picture a clean room where humidity monitors display ideal readings between 30-70%
- Visualize metallic packaging material smoothly conducting charges away from sensitive components
- See static-dissipative foam gently cradling circuit boards in protective cases
- Imagine anti-static bags creating a protective shield around delicate electronic parts
Foam Density and Performance Factors
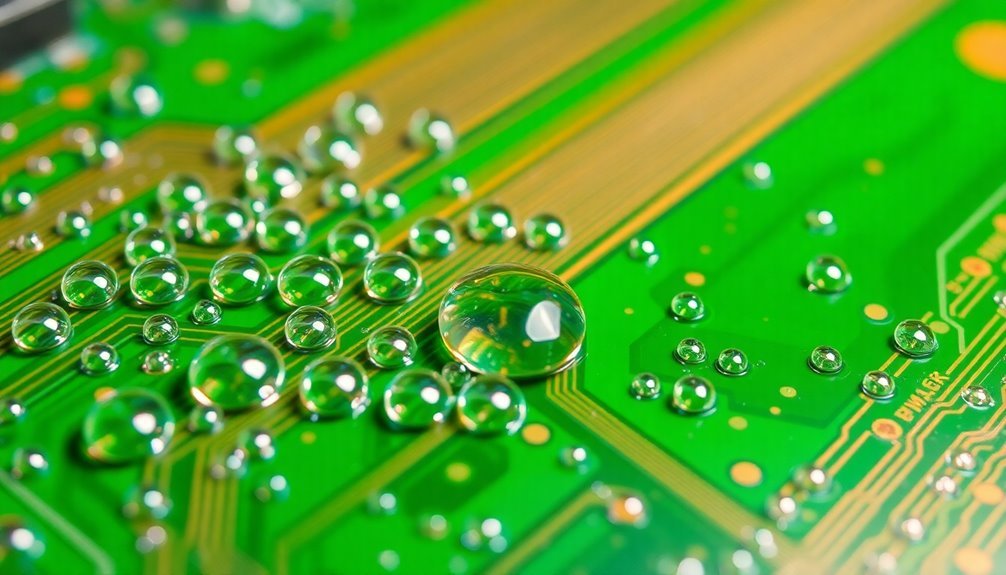
Density stands as a critical factor in determining foam's protective capabilities for electronics manufacturing. When selecting protective foam for electronic components, you'll need to take into account how density affects both mechanical strength and insulation performance. Higher-density foams provide better resistance to impact and mechanical stress, making them ideal for protecting sensitive electronic equipment during transit and storage. The foam's closed-cell structure contributes significantly to its moisture resistance and overall protective qualities.
Density Level | Protection Features | Best Applications |
---|---|---|
High Density | Superior impact resistance, better ESD protection, lower water absorption | Sensitive electronics, long-term storage, high-value components |
Medium Density | Balanced protection, good compression resistance, moderate flexibility | General electronics packaging, routine shipping needs |
Low Density | Enhanced flexibility, lighter weight, better cushioning | Light components, short-term storage, basic transit protection |
Ultra-Low Density | Maximum flexibility, highest cushioning, minimal weight | Delicate surface protection, temporary packaging |
You'll find that production factors like CO2 foaming technology and chemical additives markedly influence foam density. For ESD-sensitive components, you should opt for high-density conductive foams, as they provide better long-term protection. Remember that while lower-density foams might offer adequate cushioning, they may lack the structural integrity needed for protecting heavier electronic equipment or components requiring precise positioning during transport.
Workstation Safety With Anti-Static Foam
Properly equipping your electronics workstation with anti-static foam creates a vital defense against electrostatic discharge (ESD) damage. You'll need to select high-quality anti-static foam materials that integrate specialized agents to prevent static buildup while maintaining non-contaminating and non-corrosive properties for your sensitive components. The foam's density of 2.5-6.25 lb/ft provides ideal cushioning properties for electronics protection.
Your workstation setup should incorporate custom-cut foam inserts that provide precise component protection within ESD containers and tray liners. When you're handling electronic parts, these foam materials will dissipate static charges slowly, substantially reducing the risk of component damage.
You'll want to guarantee your entire workspace is properly grounded and equipped with anti-static surfaces.
- Pink or blue anti-static foam lining your component storage drawers
- Custom-cut black foam inserts cradling circuit boards in their exact shape
- Anti-static foam tape securing delicate components to workstation surfaces
- Cleanroom-grade foam mats providing a static-safe work surface
Remember that compliance with ESD safety standards isn't optional – it's essential throughout the entire product lifecycle. Your choice of foam materials must match your specific application needs, considering factors like surface resistance, hardness, and intended use in electronics manufacturing.
Custom Packaging Design Guidelines
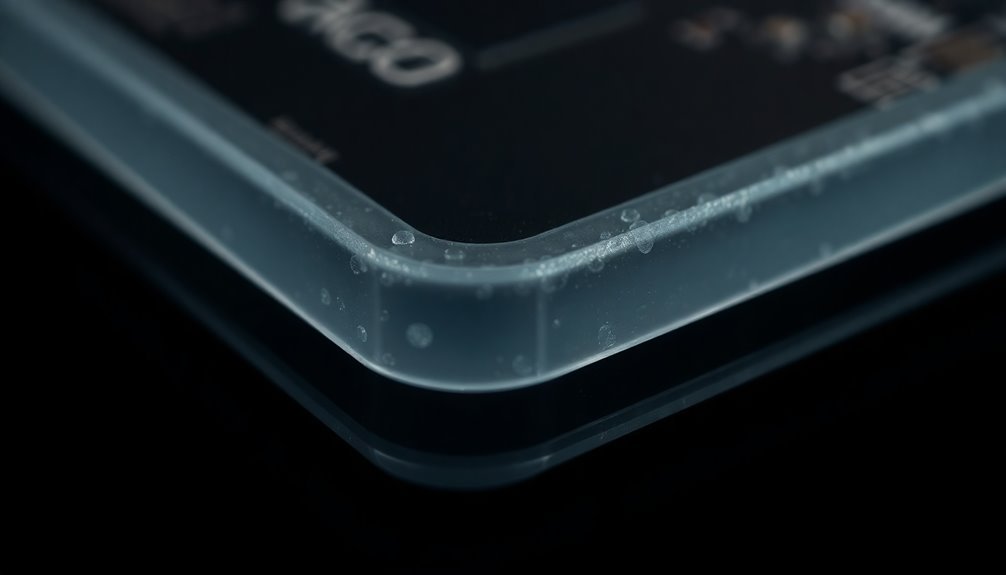
When you're designing custom packaging for electronics, you'll need to carefully assess both the material's anti-static properties and its physical protection capabilities to match your specific component requirements.
Your material selection should prioritize foam types that offer the right balance of hardness, thickness, and static dissipation properties, such as PE foam for lighter components or EPE foam for heavier items. Implementing quality control checks during the foam selection process helps ensure every product receives appropriate protective materials.
For effective foam cavity design, you'll want to create precise cutouts that match your component dimensions with a snug fit, leaving appropriate clearance for easy insertion and removal while maintaining protection against movement and shock.
Material Selection Criteria
Selecting the right materials for custom electronics packaging demands careful consideration of multiple critical factors. You'll need to evaluate density, flexibility, and surface resistance properties to guarantee the best protection for your electronic components. EPS foam materials like Styrofoam provide excellent insulation for temperature-sensitive products during transit.
When choosing materials, focus on their ability to dissipate static electricity and manage thermal conditions while maintaining environmental resistance.
Consider these key material characteristics for effective protection:
- Dense foam materials that compress and bounce back when impacted, creating a protective cushion around delicate circuit boards
- Flexible anti-static materials that wrap snugly around components, preventing harmful static discharge
- Moisture-resistant barriers that shield sensitive electronics from humidity and condensation
- Temperature-regulating materials that maintain stable conditions during shipping and storage
You'll want to balance cost-effectiveness with protection level, guaranteeing your selected materials meet both your budget and safety requirements. Pay special attention to the material's durability and reusability potential, as these factors impact long-term value.
Don't forget to verify that your chosen materials comply with industry regulations and standards for electronic component protection. Working directly with manufacturers can help you identify the most suitable materials for your specific applications.
Foam Cavity Design Techniques
Building on proper material selection, effective foam cavity design requires precision engineering to create custom packaging solutions for electronics. You'll need to employ various cutting-edge techniques to achieve the best component protection while maintaining cost-effectiveness.
Start by utilizing 3D modeling to design your foam cavities with precise measurements that guarantee a snug component fit. CNC machining and laser die cutting offer exceptional accuracy (within ±0.005 inches) for creating complex cavities in closed-cell foams.
For delicate electronic parts, think about water-jet cutting, which won't create thermal stresses or distort edges. Rate-responsive foam can provide additional protection by firming up during sudden impacts while remaining soft during normal handling.
You'll want to focus on space efficiency while designing your cavities, guaranteeing each component has adequate protection against shock, vibration, and ESD damage. Thermoforming and hot-wire cutting can help you achieve complex shapes that maximize space usage.
Don't forget to think about thermal management – your foam cavities should provide proper insulation from heat and cold.
Before moving to mass production, create prototypes to test and refine your designs. Work closely with manufacturers to guarantee your foam cavity designs meet industry standards and specific electronic component requirements while maintaining sustainability and reusability considerations.
Manufacturing Process Quality Control
You'll need to establish a rigorous quality control system that includes daily resistance testing of anti-foam materials to verify their protective properties.
Regular foam density checks should be performed using calibrated instruments to guarantee consistent shock absorption and cushioning characteristics across manufacturing batches.
Implement strict cross-contamination prevention protocols by maintaining separate storage areas, using dedicated tools, and regularly cleaning equipment that comes in contact with anti-foam materials. Maintain detailed documentation records of all testing procedures and results to ensure traceability and compliance with quality standards.
Testing Resistance Values Daily
Daily resistance testing stands up to rigorous manufacturing standards by guaranteeing consistent quality control in electronics production. You'll need to implement proper testing techniques while following established best practices to maintain accuracy in your measurements.
When you're testing resistance values, always guarantee the circuit's power is off and isolate the component before connecting your multimeter.
Use these proven methods to maintain quality control in your daily testing routine:
- Set your high-precision multimeter to the ohms (Ω) setting and connect quality test leads to component terminals
- Choose between two-wire, three-wire, or four-wire measurement techniques based on your specific resistance range
- Document readings and compare them against manufacturer specifications for immediate verification
- Maintain regular calibration schedules for all testing equipment to prevent drift in measurements
You'll want to account for potential lead resistance errors, especially when measuring low resistance values. For high-resistance measurements, consider using the voltage-forcing technique.
Remember to isolate components completely from the circuit to avoid interference from other elements.
Foam Density Quality Checks
Implementing reliable foam density quality checks requires precise measurement technologies to maintain consistent production standards. You'll find several effective methods to measure and verify foam density during manufacturing processes.
Capacitance sensors offer a non-contact solution that's ideal for production environments. They use electric fields to measure foam density and thickness simultaneously, while the Clausius-Mossotti equation helps correlate capacitance changes to density values.
For more advanced measurements, you can employ terahertz technology, which doesn't require calibration and works effectively through multiple material layers.
To calculate relative density, you'll need to compare your foam part's weight against the weight of an equal volume of solid material. This measurement helps you determine the foam's porosity and confirm it meets your specifications. For metal foams, you'll typically target density ranges between 4% and 12%.
When monitoring foam density in tanks, you can utilize guided wave radar or differential pressure transmitters. These systems provide accurate measurements even in challenging conditions, and they're particularly useful when you need to maintain consistent density levels throughout your manufacturing process.
Cross-Contamination Prevention Protocols
Through rigorous protocols and systematic controls, effective cross-contamination prevention starts with thorough material segregation and robust quality management systems.
You'll need to implement dedicated containers for different anti-foam materials and establish clear labeling protocols using automated tracking systems. Regular equipment maintenance and validation processes are vital to maintain your manufacturing environment contamination-free.
Your employees must undergo extensive training programs focusing on proper hygiene practices and handling procedures. It's imperative to maintain detailed documentation of all training sessions and regularly update protocols to align with current food safety regulations, even in electronics manufacturing.
- Separate storage areas with color-coded containers for different anti-foam materials, each clearly labeled and tracked
- Clean rooms with automated air filtration systems and pressure differentials to prevent particle cross-contamination
- Dedicated workstations with specialized cleaning protocols and validation checkpoints
- Personal protective equipment stations with proper disposal systems for contaminated materials
Implement real-time monitoring systems to track quality metrics throughout your manufacturing process. Regular in-process inspections and end-of-line testing will help you identify potential contamination issues before they affect your final product.
Your quality control system should include thorough data management to guarantee traceability and a swift response to any deviations.
Storage and Handling Best Practices
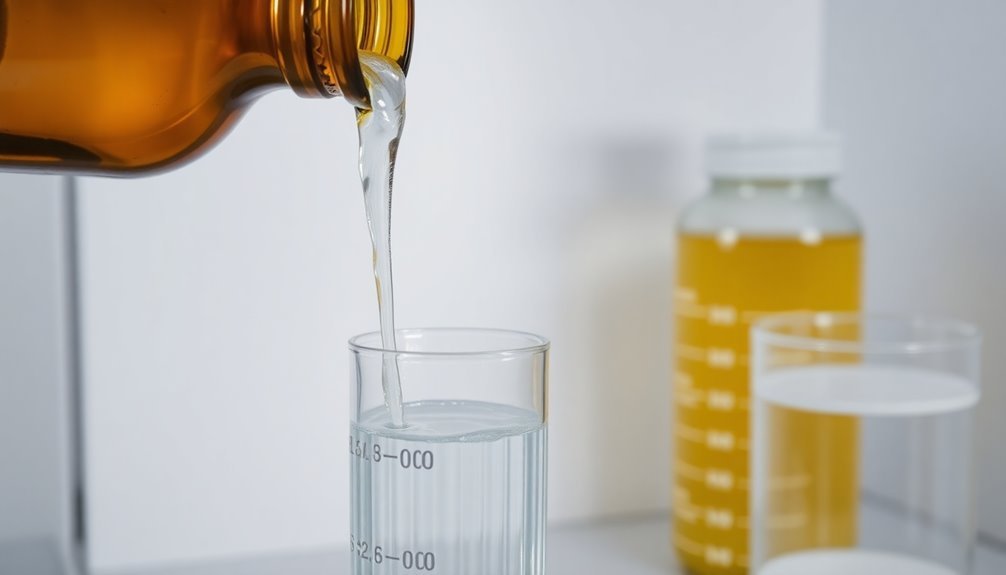
Proper storage and handling practices serve as the foundation of electronics manufacturing protection. You'll need to select antistatic polyurethane or polyethylene foam with open-cell structures, guaranteeing they meet industry standards for ESD protection.
When storing components, use ESD-safe containers equipped with custom-fit foam inserts that match your specific needs.
You must implement strict handling protocols by using antistatic gloves and wrist straps while working with sensitive components. Keep your workstations and tools ESD-safe, and regularly inspect your antistatic equipment for signs of wear. Don't forget to ground all work surfaces to prevent static buildup.
Store your electronic components in controlled environments to minimize temperature and humidity fluctuations. You'll want to avoid stacking components and guarantee proper container sealing to prevent moisture intrusion.
When transporting items, use antistatic foam inserts and conductive bags for additional protection. Consider implementing custom-cut foam solutions to maximize space efficiency and component protection.
Remember to regularly assess your storage layout and make adjustments as needed to maintain top-notch organization and safety standards.
Resistance Values and Applications
While protective storage measures safeguard your components, understanding resistance values and their applications helps you select the right components for your manufacturing needs.
You'll find that resistance series, from E3 to E96, offer varying levels of precision to match your manufacturing requirements. When you're working with general electronics, standard resistors with 5% or 10% tolerance often suffice, but medical devices and aerospace instruments demand precision resistors with tolerances as low as 0.005%.
Remember that manufacturing variance affects every resistor, which is why you'll need to account for tolerance ratings in your designs. For instance, if you're using a 570Ω resistor with 10% tolerance, the actual resistance could vary by ±57Ω.
Imagine a delicate medical sensor where precise current control could mean the difference between accurate and false readings.
Picture an aerospace instrument panel where component reliability determines flight safety.
Visualize a high-end audio amplifier where exact resistance values guarantee pristine sound quality.
Think of a telecommunications network where proper voltage regulation maintains clear signal transmission.
Choose your resistors based on your application's precision requirements and operating conditions to guarantee optimal performance in your electronic assemblies.
Environmental Impact of Protection Materials
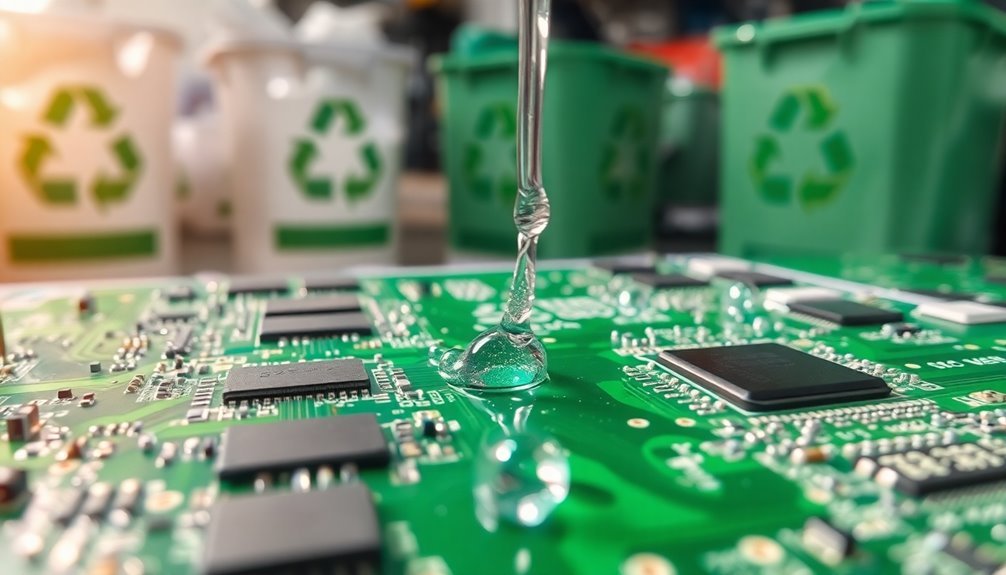
Environmental stewardship in electronics manufacturing demands careful consideration of protection materials and their ecological footprint. When you're selecting protection materials for your electronics, you'll need to balance performance requirements with environmental impact throughout the product's lifecycle.
Modern protection materials like polyurethane and polyethylene foams offer recyclable alternatives to traditional hazardous substances. These materials don't just protect your components – they're part of a broader circular economy approach that considers sourcing, design, manufacturing, and end-of-life management.
To minimize environmental impact, you should focus on materials that provide multiple benefits. For instance, anti-static foams can prevent electrostatic discharge while offering thermal insulation properties, extending component lifespan and reducing waste.
Custom-fit protection solutions will help you optimize material usage and reduce excess packaging waste.
When implementing protection materials, you'll need to guarantee compliance with regulations like RoHS while maintaining material efficiency in your manufacturing processes. Consider working with suppliers who prioritize sustainable practices and can provide documentation of their environmental commitments.
This approach helps you contribute to industry-wide efforts toward reducing electronic waste and promoting responsible manufacturing.
Testing and Certification Standards
Testing and certification standards build upon environmental considerations to guarantee your protection materials meet rigorous industry requirements.
You'll need to guarantee your anti-static foams comply with ANSI/ESD S541 specifications, maintaining surface resistivity below 10^12 Ohms/square and effectively dissipating 5000-volt charges to 50 volts in under two seconds.
When you're selecting protection materials, look for UL certification and compliance with ANSI/ESD S20.20 standards. Your materials must perform consistently at 23°C and 12% relative humidity, demonstrating reliable static dissipation throughout their lifespan of three or more years.
- Technicians in white lab coats methodically testing foam samples under controlled conditions
- Precision measuring equipment displaying real-time surface resistivity readings
- Environmental chambers cycling through temperature and humidity variations
- High-voltage testing stations measuring charge dissipation rates
You can utilize ETHACALC software to determine the right foam specifications for your application. Whether you're working with ETHAFOAM products or custom polyurethane solutions, make sure they're certified for both static protection and cushioning performance.
Frequently Asked Questions
How Long Does Anti-Static Foam Maintain Its Protective Properties Before Needing Replacement?
You'll get 3 years of guaranteed protection from high-quality anti-static foam, but you should replace it sooner if you notice wear and tear or decreased performance during your regular quality checks.
Can Anti-Static Foam Be Reused After Initial Packaging and Shipping?
You shouldn't reuse anti-static foam after initial shipping, as it loses its protective properties over time. For your electronics' safety, it's best to use fresh foam for each new packaging application.
What Cleaning Methods Are Safe for Maintaining Anti-Static Foam Surfaces?
You can safely clean anti-static foam using ESD-safe swabs, compressed air, or specialized foam cleaners. Don't use harsh chemicals, and always work in a controlled environment to maintain the foam's protective properties.
Does Extreme Temperature Affect the Anti-Static Properties of Protective Foam?
Yes, extreme temperatures will affect your anti-static foam's performance. You'll notice reduced effectiveness above 85°C or below -10°C, as these temperatures can degrade the foam's static dissipation properties and elasticity.
Are There Special Disposal Requirements for Used Anti-Static Foam Materials?
You'll need to check local regulations as disposal requirements vary. If contaminated with hazardous materials, you must use licensed contractors. For non-hazardous foam, you can dispose through regular waste streams after compaction.
In Summary
Protecting your electronics during manufacturing requires choosing the right anti-static foam materials and following proper handling protocols. You'll need to balance density, resistance values, and environmental factors when selecting protective solutions. Remember to maintain certified testing standards and regularly assess your workstation safety measures. By implementing these foam protection guidelines, you're safeguarding your components and optimizing your manufacturing process.
Leave a Reply