To achieve electronics assembly certification, you'll need to master these seven critical steps: Set up an ESD-protected workspace with proper grounding and anti-static equipment, learn proper component handling techniques, master through-hole and surface mount soldering skills, understand visual inspection methods following IPC standards, complete hands-on training for rework and repair, document all ESD control procedures, and maintain certification through regular testing and updates. You'll need to demonstrate proficiency in identifying various components like SOTs and SOICs while practicing defect recognition. These fundamentals form just the foundation of your journey toward becoming a certified electronics assembly professional.
Understanding ESD Safety Fundamentals
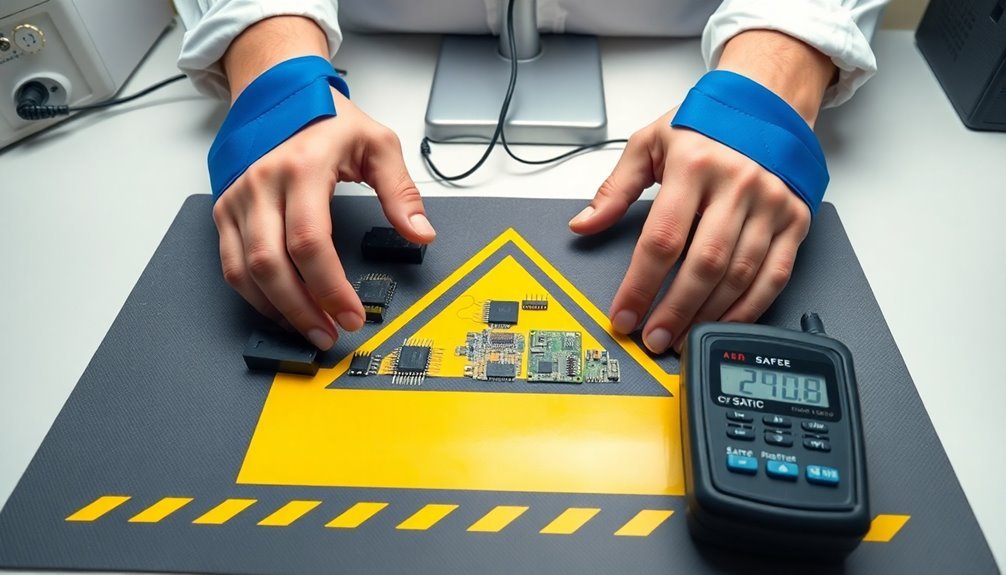
The foundation of electronics assembly safety lies in understanding and implementing proper ESD (Electrostatic Discharge) protection measures. You'll need to create a thorough ESD-friendly environment that includes static-dissipative mats, properly grounded workstations, and controlled humidity levels of around 30% relative humidity to dissipate static charges safely.
To protect sensitive components, you must use ESD-safe tools and equipment throughout your facility. This includes specialized tweezers, vacuum pick-ups, and conductive chairs with proper grounding. Regular training sessions are essential to ensure all personnel understand proper ESD handling procedures.
You'll also need to implement conductive flooring and use anti-fatigue mats to prevent static buildup during movement.
Your ESD safety program should align with key industry standards like ANSI/ESD S20.20 and IEC 61340-5-1. You're required to use standardized test methods and follow specific guidelines for grounding and packaging materials.
When handling components, you must minimize direct contact and use ESD-protective packaging such as static shielding bags and antistatic foam.
Regular audits of your ESD protection practices will guarantee continuous compliance and effectiveness of your safety measures.
Proper Personal Grounding Equipment
You'll need to understand the key components of grounding straps, including the wrist band, coiled cord, and grounding point connection, to guarantee proper ESD protection during electronics assembly.
Static control work stations must incorporate grounded surfaces, ionized air systems, and designated common point grounds to create a complete ESD-safe environment. A properly installed dual-conductor strap provides redundant grounding paths for enhanced protection against static discharge.
Your body-to-ground connection requires either a wrist strap or foot grounder properly attached to the common ground point, with regular testing to verify functionality and conductivity.
Essential Grounding Strap Components
Within electronics assembly, proper grounding straps serve as vital safety equipment to protect both personnel and sensitive components from electrostatic discharge (ESD). You'll need to guarantee your grounding straps include several essential components to maintain safety and effectiveness in your assembly work.
The core component of your grounding strap should be high-quality tinned copper braid, which provides superior conductivity for redirecting electrical charges safely to ground. Following proper implementation standards helps ensure protective bonding effectiveness for long-term safety.
You'll want to verify that your straps feature properly crimped sleeve ends, as these connections are essential – remember, your ground assembly is only as strong as its weakest point.
When selecting your grounding equipment, you must consider the fault current ratings and length requirements specific to your application. You'll need to choose grounding heads rated to withstand potential fault currents for their entire duration.
Make sure you're using pre-assembled grounding sets that have been tested and certified to meet safety standards.
For retrofit applications or when you need additional shielding, you can install supplementary grounding straps between terminals. These components will provide you with a reliable, low-impedance path for fault currents while guaranteeing maximum protection against ESD events.
Static Control Work Stations
Safety protocols require proper static control workstations to prevent ESD damage to sensitive electronic components. You'll need to establish a common point ground that connects all workstation components and personnel to the same electrical ground point.
This connection must link to the equipment grounding conductor or the green wire ground connection, with any auxiliary grounds properly bonded to minimize potential differences.
Your workstation must include ESD protective surfaces with resistance between 1.0 x 10^6 and 1.0 x 10^9 ohms. The use of advanced static-dissipative flooring in your workstation area provides an additional layer of protection against harmful static charges.
You'll need to wear groundable static control garments that create a bond between your skin and the ground path.
Install constant monitors to verify continuous grounding effectiveness, and use ionizers to neutralize airborne static charges.
For personal grounding, you must use dual-conductor wrist straps, grounding mats under workstations, and heel grounders when standing.
Maintain total system resistance below 35 megohms, including your body, garment, and grounding cord.
Don't forget to use ESD-safe furniture and tools, and regularly evaluate your grounding system's effectiveness.
Control humidity levels and incorporate static-dissipative materials in your workstation setup to further minimize static risks.
Body-to-Ground Connection Methods
Maintaining proper body-to-ground connections is essential for protecting sensitive electronic components during assembly. You'll need to understand three primary grounding methods to guarantee effective static discharge protection.
Wrist straps serve as your primary grounding tool when you're seated and handling sensitive components. You'll connect the conductive cuff to an unpainted surface or grounded workstation through a coiled ground cord, which keeps you at ground potential while allowing movement. This setup actively prevents shock hazards by directing any static electricity safely to ground.
ESD mats offer another vital grounding solution for your workstation. You'll place these antistatic surfaces on tables or floors, connecting them to an electrical outlet via a grounding cable. They'll create a safe path for static dissipation whether you're standing or seated.
For increased mobility, you'll want to use footwear grounding systems. These include heel straps, toe straps, or boot straps that work with dissipative floor mats or conductive floors. They'll maintain continuous grounding as you move throughout your work area.
Remember that all grounding methods must comply with safety standards and codes. You'll achieve the best protection by guaranteeing the lowest possible impedance between yourself and the power system source.
Static-Safe Workstation Setup
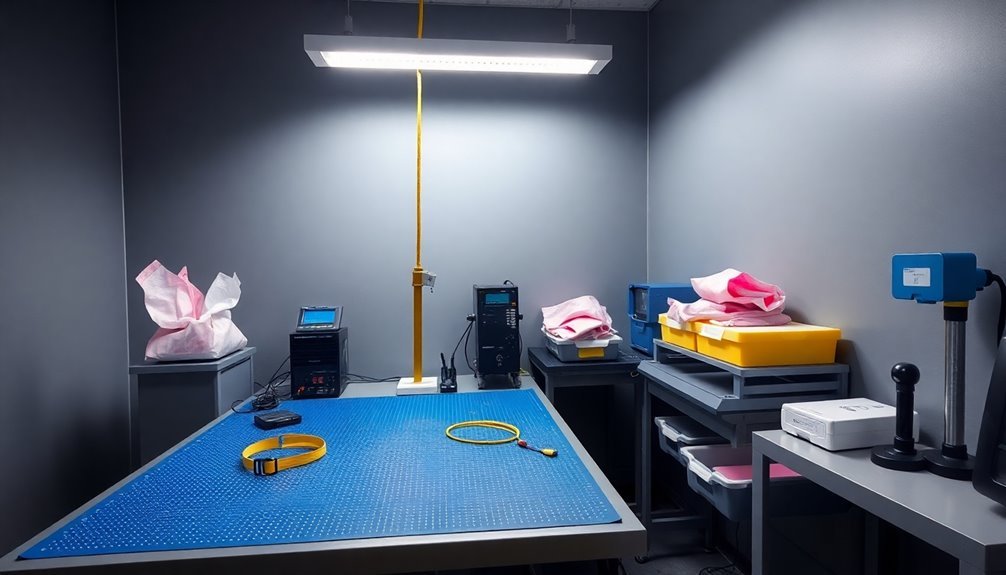
To create a static-safe workstation, you'll need essential ESD protection components including a grounded table mat, floor mat, and wrist strap with a common point ground connection.
You must properly ground all components by connecting them to verified grounding points, ensuring the table mat links to the common point ground and the wrist strap connects to the same ground point. Test connections with an ohmmeter to maintain proper resistance levels.
Your workstation setup isn't complete until you've removed or replaced non-ESD items with static-safe equivalents and verified all grounding connections are secure and functional.
ESD Protection Components
Within electronics assembly facilities, establishing a properly equipped static-safe workstation forms the foundation of effective ESD protection.
Implementing proper ESD controls helps prevent costly damage and failures that impact over 25% of electronics damaged for unknown reasons.
You'll need to implement several essential components to create a thorough ESD-protected environment. Start with static-dissipative work surfaces made of rubber or vinyl, which channel harmful charges away from sensitive electronics.
Install proper grounding points throughout your workstation to dissipate static charges effectively. You'll want to connect all work surfaces, tools, and equipment to these grounding points.
Don't forget to equip your staff with wrist straps and ESD-safe tools like specialized tweezers and vacuum pick-ups to minimize direct contact with components. Make sure you're using ESD bags and proper packaging for component storage and transport.
Consider your facility's environmental controls as well. You'll need to maintain appropriate humidity levels and implement ESD-controlled flooring solutions like anti-static mats.
Make certain your workers wear appropriate PPE featuring conductive filaments. For enhanced protection, install ionizers to neutralize static charges on insulators.
Remember to regularly inspect and maintain all ESD protection components to make certain they're functioning correctly and providing consistent protection for your sensitive electronic assemblies.
Proper Grounding Methods
A well-grounded workstation serves as your first line of defense against costly ESD damage. You'll need to establish a proper grounding foundation by installing an ESD table mat made of vinyl for general assembly or rubber for soldering work. Connect all components to a common point ground to maintain consistent electrical potential throughout your workspace. Using a surface resistivity meter allows you to verify proper grounding continuity from the ground point to all workstation parts.
Start by laying your bench mat flat and connecting it to the grounding cord, which you'll plug into a mains socket.
You'll need to eliminate all insulators from your work area or cover them with grounded materials. Install metal shelving instead of wood or plastic to facilitate quick static dissipation. Your static dissipative mats should maintain surface resistance between 1 megohm and 1 gigohm.
Don't forget your personal grounding equipment. You must wear an ESD wrist strap connected to the EBP bar and earth point. If you're standing, use foot grounders with an ESD floor mat.
While ESD clothing helps reduce static generation, it won't replace proper grounding methods. Remember to test your wrist straps and heel grounders regularly using a dedicated tester to verify they're functioning correctly.
Testing and Monitoring Procedures
Testing and monitoring procedures serve as electronics assembly's quality backbone, encompassing multiple inspection methods and automated systems.
You'll need to master both visual inspection techniques using tools like loupes and microscopes while following IPC-A-610H standards for acceptable assemblies.
You must implement automated testing methods including AOI for surface inspection and X-ray testing for internal layer examination. In-circuit testing and flying probe testing will help you verify electrical connectivity, while burn-in testing guarantees long-term reliability.
Don't forget to verify calibration labels on all measurement tools before use.
For mechanical validation, you'll perform peel testing, solder float tests, and micro-sectioning analysis to evaluate structural integrity.
Your quality assurance process should include thorough functional testing and board bring-up procedures. Always document your inspections using assembly drawings and work instructions that match customer specifications.
Throughout the process, you'll need to conduct incoming inspections of materials and parts, verify component placement using reference designators, and complete a final inspection.
This extensive approach guarantees your assemblies meet both quality standards and functional requirements while maintaining certification compliance.
ESD Control Documentation Requirements
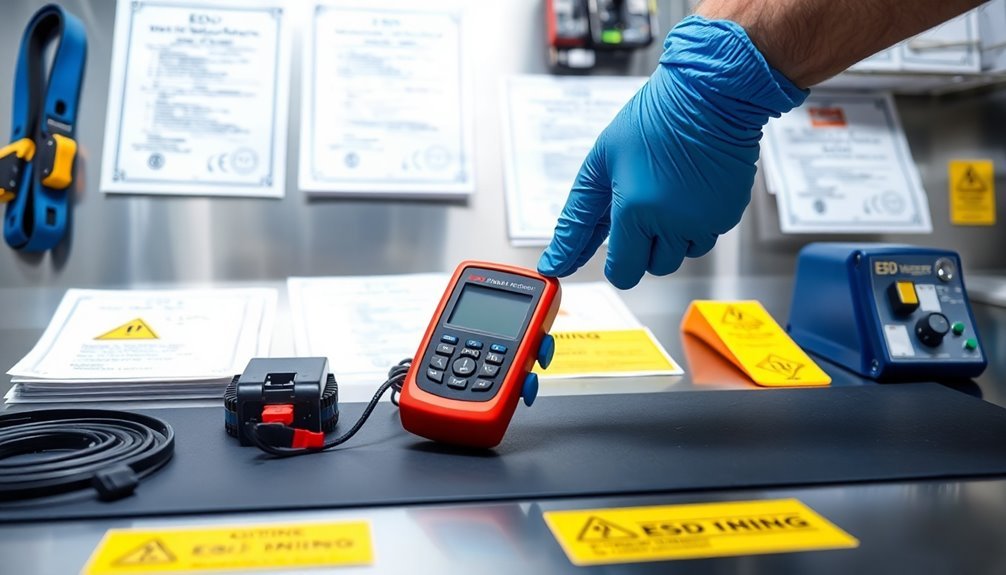
Building on your test and monitoring expertise, proper ESD control documentation forms the foundation of your electronics assembly certification compliance. You'll need to create a thorough plan that details both administrative and technical requirements while documenting the lowest ESD sensitivity levels your facility can handle.
Your documentation must include specific training procedures, compliance verification methods, and record-keeping protocols.
To maintain certification standards, you'll want to focus on these critical documentation components:
- A detailed ESD control plan outlining your facility's protected areas, equipment specifications, and grounding requirements
- Clear procedures for personnel training, including initial certification and periodic retraining schedules
- Verification and audit documentation, covering test methods, equipment calibration records, and compliance activities
You must maintain accurate records of all compliance verification activities and regular audits. This includes keeping detailed logs of humidity control measures, grounding system checks, and equipment maintenance.
Don't forget to document your designated ESD Control Program Manager's responsibilities and authority. Remember to regularly update your documentation to reflect any changes in procedures or equipment specifications, ensuring your records always align with current practices and industry standards.
Hands-On Certification Training
Ready to elevate your electronics assembly skills? Hands-on certification training offers you an immersive learning experience that'll transform your theoretical knowledge into practical expertise.
You'll work directly with electronic components, tools, and equipment while receiving real-time feedback from experienced instructors.
During your training, you'll master essential skills like soldering techniques for both through-hole and surface mount technology. You'll learn to identify various components, including SOTs, SOICs, and QFPs, while practicing assembly processes such as wave and hand soldering.
The program will teach you essential inspection criteria to spot defects like insufficient solder, bridging, and overhang, along with critical rework and repair techniques.
You can choose from flexible program durations ranging from one to five days, with options for training at dedicated facilities or your workplace. The courses follow industry standards like IPC-A-610E and can be customized to match your company's specific requirements.
Upon completion, you'll receive certification that validates your skills, enhances your career prospects, and confirms you're compliant with industry regulations.
The collaborative learning environment will help you retain knowledge better while building practical problem-solving abilities.
Annual Recertification Guidelines
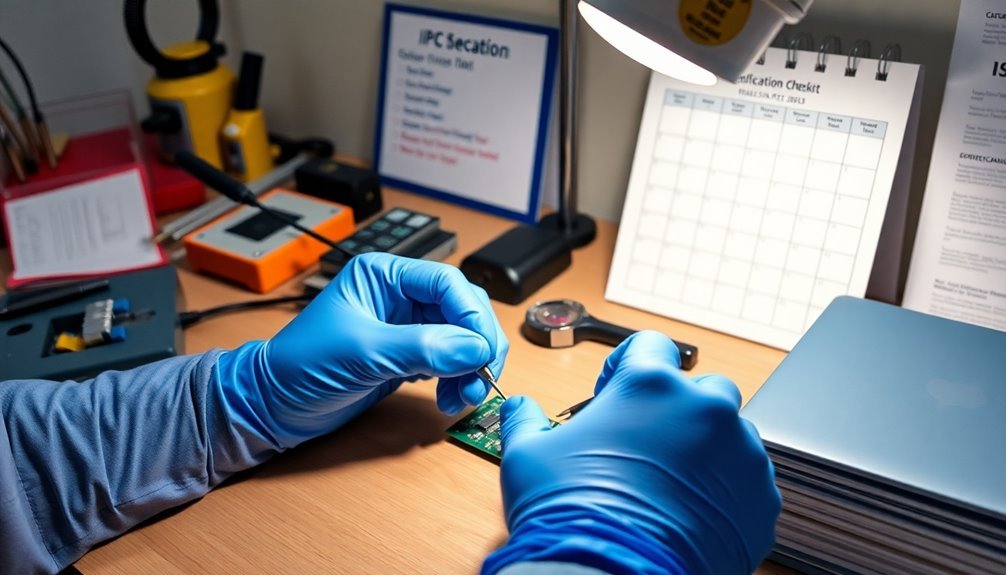
Regularly maintaining your electronics assembly certification requires careful attention to timing and renewal procedures. You'll need to complete your renewal within six months before your certification expires to maintain continuous certification status.
Once renewed, your certification remains valid for another two years from your current expiration date.
The renewal method you choose depends on your experience level and certification type. If you're confident in your knowledge, you can opt for a challenge test. Alternatively, you can attend a recertification class, which is particularly beneficial if you need updates on recent standard revisions.
Different certification levels have specific renewal requirements:
- CIS holders can renew through training programs or qualifying exams
- CSE professionals must either retest or complete 25 hours of technical committee work
- MITs need continuing education credits and 25 IPC certification renewal points
Don't let your certification expire – there aren't any extensions available, and you'll have to start the initial certification process all over again. This means more time and resources spent on regaining your credentials.
Maintaining your certification is vital for meeting contractual requirements and quality system standards in the electronics assembly industry.
Frequently Asked Questions
How Much Does Electronics Assembly Certification Typically Cost?
You'll typically spend around $1,780 for a 40-hour electronics assembly certification program, which includes your training and exam fees. Additional costs may vary depending on materials and specific certification requirements.
Can I Transfer My Certification Between Different Employers?
Yes, you can transfer your IPC certification between employers. Since it's granted to you personally, not your company, your certification remains valid and active regardless of where you work, maintaining the same recertification timeline.
What Happens if I Fail the Certification Exam?
If you fail, you'll typically have up to three attempts to retake the exam after waiting periods. You'll need to purchase additional attempts, but some programs offer a free retest. Focus on improving weak areas.
Are There Age Restrictions for Obtaining Electronics Assembly Certification?
You won't face age restrictions when pursuing electronics assembly certification. The focus is on your skills, knowledge, and completion of required courses rather than your age. Certification is available to qualified individuals at any age.
Can Certification Be Completed Entirely Through Online Courses?
You can't complete all certifications entirely online. While theoretical components and discrimination training are available virtually, you'll need hands-on practical training and in-person skills assessment for most electronics assembly certifications.
In Summary
You'll need to consistently maintain these seven critical ESD safety steps to protect sensitive electronic components and stay certified. Don't skip regular workstation checks, documentation updates, or annual recertification requirements. By following proper grounding procedures and keeping your static-safe practices current, you're ensuring quality assembly work and maintaining professional standards in electronics manufacturing.
Leave a Reply