To implement an effective ESD control program, you'll need to follow five key steps. Start by designing a thorough plan that aligns with ANSI/ESD S20.20 standards and defines clear objectives. Next, set up protected areas with proper signage, entry procedures, and grounding systems. Then, install appropriate ESD control equipment like work surfaces, flooring, and protective gear. Train your personnel thoroughly on ESD principles and safety protocols, ensuring they understand the importance of compliance. Finally, maintain program effectiveness through regular audits and continuous improvement strategies. Exploring these steps in detail will help you create a robust ESD protection system for your facility.
Designing Your ESD Program Plan
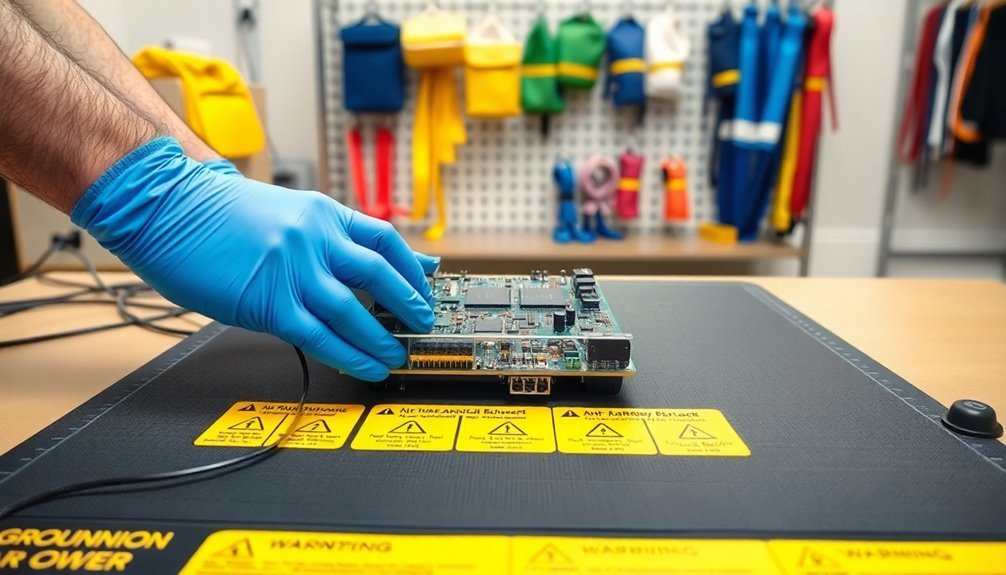
Establishing an effective ESD control program starts with carefully defining your objectives and technical requirements. You'll need to align your program with industry standards like ANSI/ESD S20.20-2014 while identifying ESD-susceptible items in your facility. Top management support must be secured to ensure program success.
Reference the Reliability Analysis Center V-ZAP data book or manufacturer specifications to determine which components require protection. Once you've identified vulnerable components, determine their withstand voltage levels to establish appropriate protection thresholds. Regular compliance verification plans must specify measurement limits and technical requirements to ensure ongoing effectiveness.
You'll then need to develop technical requirements for essential ESD control items, including worksurfaces, flooring, seating, and garments. Document these specifications in your ESD Control Program Plan, which serves as your primary implementation guide.
Your plan should include an extensive list of approved ESD protective products and detailed technical requirements. Don't forget to create supporting documentation, such as your Training Plan and Compliance Verification Plan.
These documents will outline who needs training, when they need it, and how you'll verify compliance. Keep detailed records of all verification activities and training sessions to demonstrate your program's conformity with technical requirements and maintain accountability across your organization.
Setting Up Protected Areas
Once you've documented your ESD control program plan, your next major task is implementing protected areas where you'll handle ESD-sensitive components.
Start by identifying all locations where you'll work with ESD-sensitive items, including manufacturing, assembly, and testing areas. You'll need to clearly mark these areas with proper signage and establish strict entry and exit procedures. Untrained persons must be escorted when entering protected areas.
Your primary focus should be eliminating static differences by connecting all ESD control elements to a protective Earth or equipotential bonding system. Daily verification of compliance verification plans ensures your protected areas maintain their effectiveness.
Install proper grounding methods, including floor mats and work surface mats, and guarantee they're regularly maintained and inspected for effectiveness.
You'll need to implement specific control measures throughout your protected areas. These include using ESD-safe materials, requiring ESD-protective clothing, and installing appropriate work surfaces and storage containers.
Don't forget to clearly label all ESD-sensitive items and areas requiring special handling.
To maintain effectiveness, you must conduct regular audits and static surveys of your protected areas.
Keep detailed records of all inspections and compliance checks, and use external auditors when possible to guarantee unbiased evaluations.
Use this feedback to continuously improve your ESD control measures.
Choosing Control Equipment
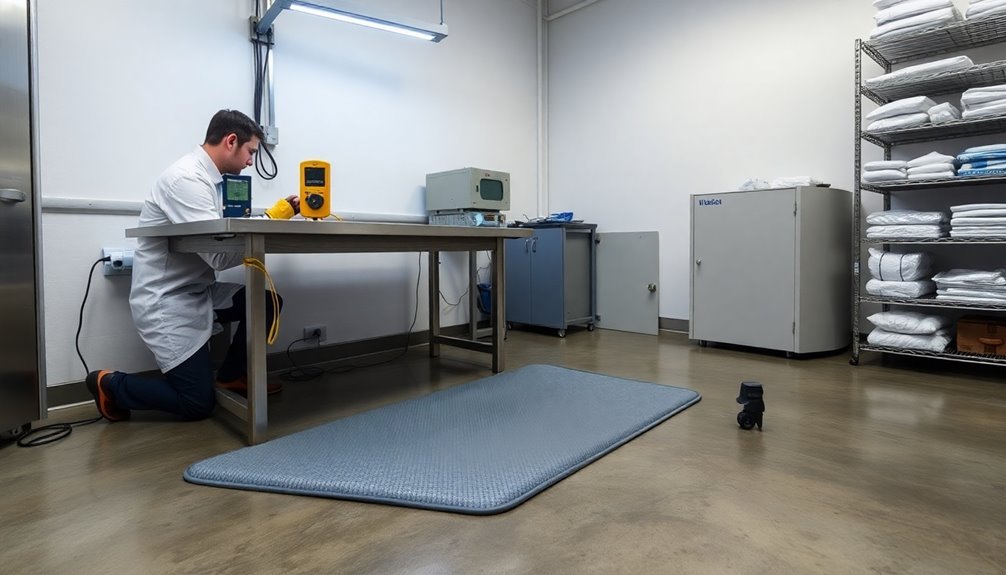
When selecting ESD control equipment, you'll need to match your choices to both industry standards and the sensitivity levels of components you're handling. Your equipment must comply with standards like ANSI/ESD S20.20 and IEC 61340-5-1, while providing adequate protection for your specific ESD-sensitive items.
Start with the essential equipment: ESD workbenches, wrist straps, protective clothing, proper flooring, and specialized storage solutions. Confirm each piece features proper conductive paths and meets required resistance levels. Senior management support is vital for securing the necessary capital expenditure for quality ESD equipment.
You'll want to verify that your equipment can effectively dissipate static charges and works well within your facility's humidity conditions. Maintaining proper environmental controls through ionization and humidification helps minimize static buildup.
Don't forget to establish a robust maintenance program for your control equipment. You'll need to implement regular testing schedules, perform calibrations according to manufacturer specifications, and maintain detailed records of all maintenance activities.
Set up clear procedures for equipment inspection and replacement when items become faulty or worn.
Remember to document everything – from initial equipment selection to ongoing performance metrics. You'll want to keep detailed records of your equipment's specifications, maintenance history, and verification results.
This documentation will prove invaluable during audits and help confirm your ESD control program remains effective.
Training Personnel Effectively
To build an effective ESD control program, you'll need to implement extensive personnel training that addresses both technical and practical aspects of static prevention. Start by clearly defining your training objectives and identifying which personnel require ESD awareness training, particularly those handling sensitive components.
Develop a thorough curriculum that covers essential topics like ESD principles, device sensitivities, and proper grounding techniques. You'll want to use varied training methods, including hands-on activities and interactive exercises, to guarantee better retention of prevention techniques.
Make sure you're documenting all training sessions and maintaining detailed records for audit purposes. Focus on making your training accessible to all staff members, including non-technical employees.
Include regular assessments to verify understanding and delegate specific ESD control responsibilities to team members. You'll need to establish both initial and recurring training schedules to maintain consistent awareness throughout your organization.
Integrate your training program with your overall ESD control strategy by aligning it with your company's Control Program Plan. Don't forget to secure management support and regularly update your training materials based on audit results and employee feedback.
Maintaining Program Compliance
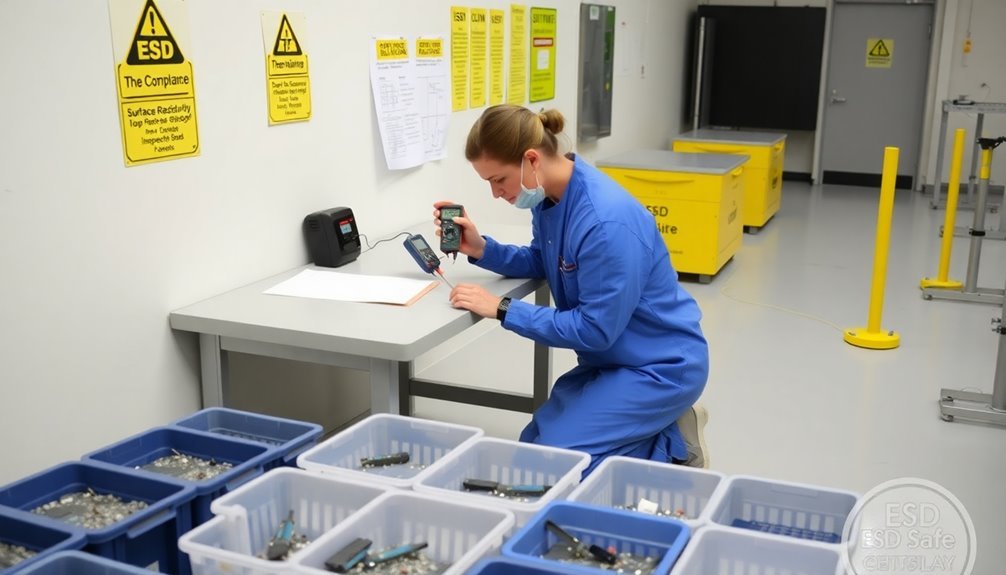
A successful ESD control program demands rigorous compliance monitoring and continuous verification. You'll need to establish a thorough compliance verification plan that aligns with ANSI/ESD S20.20-1999.1 standards and documents all steps for reviewing, analyzing, and improving your ESD program.
You must conduct regular audits of your ESD protected areas and equipment, including static surveys and electrical tests of control items like wrist straps and footwear. It's crucial to maintain detailed records of all compliance verification activities, test methods, and results to demonstrate conformity to technical requirements.
Your ESD control plan should be a controlled document that's approved by upper management and regularly updated. You'll need to establish clear audit criteria and schedules, conducting evaluations at appropriate frequencies – monthly for static surveys and annually for system compliance.
Don't forget to include external auditors to guarantee unbiased assessments.
To maintain effective compliance, you should implement a continuous improvement process that incorporates feedback from audits, encourages employee participation, and stays current with technological advances in ESD control methods.
When you identify deficiencies, take immediate corrective actions and document the results.
Frequently Asked Questions
How Long Does It Typically Take to See ROI From ESD Program Implementation?
You'll typically see ROI from your ESD program within 6-18 months, depending on your initial investment, device sensitivity, damage frequency, and how effectively you've implemented and maintained the program's controls.
What Are the Cost Implications of Not Implementing an ESD Program?
You'll face significant financial losses through damaged components, production delays, and increased warranty claims. Without ESD controls, you're risking your product quality, customer satisfaction, and long-term market competitiveness, costing far more than implementation.
Can Temporary Workers Be Part of the ESD Control Program?
Yes, you can include temporary workers in your ESD control program. You'll need to provide them with proper training, supervision, and ESD protective equipment while ensuring they follow established compliance procedures.
How Often Should ESD Protection Equipment Be Replaced?
You'll need to replace your ESD equipment based on regular testing results and wear. Check wrist straps daily, replace them yearly, and inspect other items like mats quarterly or when they show signs of damage.
What Insurance Considerations Are Involved With Implementing an ESD Control Program?
You'll need to assess insurance coverage for ESD equipment, liability protection, employee safety, and business interruption. Check your policy's terms for ESD-related incidents and consider adjusting coverage to meet program needs.
In Summary
Your ESD control program's success depends on consistent monitoring and adaptation. You'll need to regularly audit your protected areas, verify equipment functionality, and guarantee staff compliance with protocols. Don't forget to update your training materials and procedures as technology evolves. By following these five implementation steps and maintaining vigilant oversight, you're protecting your sensitive components and safeguarding your operations from costly ESD damage.
Leave a Reply