You'll need several key tools to verify your static control program effectively. Start with ESD guns and simulators (16-30kV range) for discharge testing, surface resistivity meters to evaluate materials, and field monitors to measure static charges. Don't forget wrist strap and footwear testers to verify personnel grounding equipment. Your verification process should include regular ground system testing, environmental monitoring of temperature and humidity, and thorough static control audits. Maintain detailed documentation of all testing procedures and confirm your equipment gets annual calibration checks. The right combination of tools and methods will strengthen your ESD protection strategy.
ESD Measuring Equipment Selection
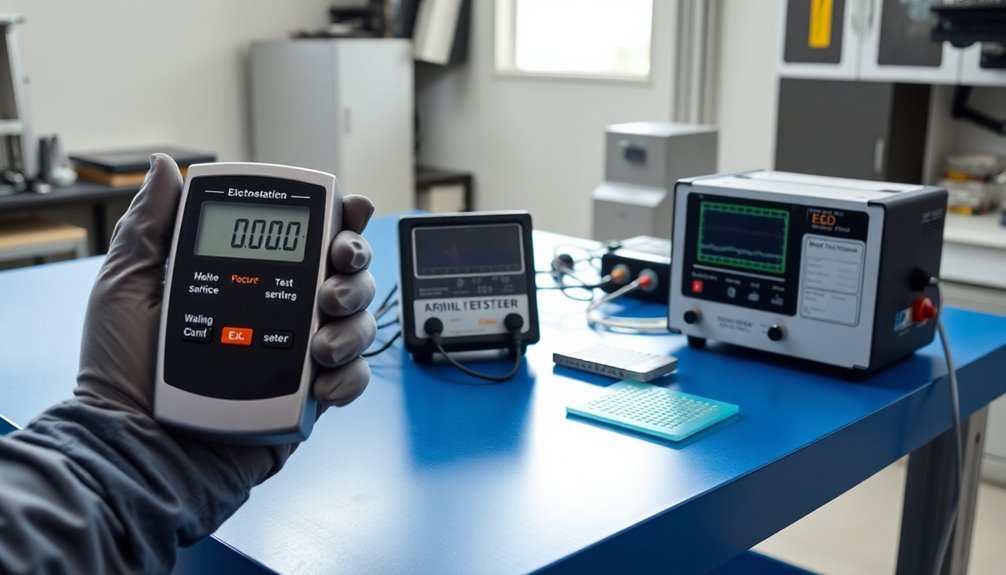
When selecting ESD measuring equipment for your static control program, you'll need to take into account four essential categories of testing devices. Each type serves a specific purpose in maintaining effective static control and guaranteeing compliance with safety standards. Regular annual calibration checks are crucial for maintaining accuracy and reliability of all testing equipment.
ESD guns or simulators should be programmable for voltages between 16kV and 30kV, allowing you to conduct thorough discharge testing. You'll want to verify that these handheld devices are properly calibrated to meet international testing standards.
For surface testing, you'll need resistivity meters that can measure from 10^3 to 10^12 ohms, capable of evaluating conductive, dissipative, and insulative materials.
Don't overlook electrostatic field monitors, which you'll use to measure static charges in your EPA environment. These portable devices work effectively even in low-light conditions and confined spaces.
Finally, you'll require wrist strap and footwear testers that can measure resistance between 750 kilohms and 100 megohms. These testers are vital for verifying that personal grounding equipment maintains its effectiveness over time, and you can often integrate them into extensive testing stations for efficient workplace monitoring.
Ground System Testing Protocols
After selecting your ESD measuring equipment, establishing proper ground system testing protocols becomes your next key focus. You'll need to maintain a resistance threshold of 10 Ohms or less while following NFPA 77 and IEC TS 60079-32-1 guidelines for effective static electricity dissipation.
Regular testing helps you detect loose, corroded, or broken connections before they compromise your system's integrity. Green flashing LEDs provide visual confirmation of proper grounding connections during testing procedures.
Your ground system testing protocol should include these essential components:
- Resistance testing using appropriate meters to verify conductivity and grounding reliability
- Extensive static control audits to evaluate your entire ESD program's effectiveness
- Regular verification of grounding paths and equipotential balance between all items
- Environmental monitoring to account for temperature and humidity impacts on conductivity
You'll need to document all testing procedures and confirm your personnel are properly certified in static electricity risk management. Combine visual indication systems with your grounding setup for enhanced control.
When testing ESD floors, incorporate resistance measurements, walking body voltage tests, and regular audits to maintain compliance with ANSI/ESD S6.1 standards. Remember to verify that all conductors and dissipative materials maintain proper electrical connection to your ground points.
Personnel Grounding Verification Tools
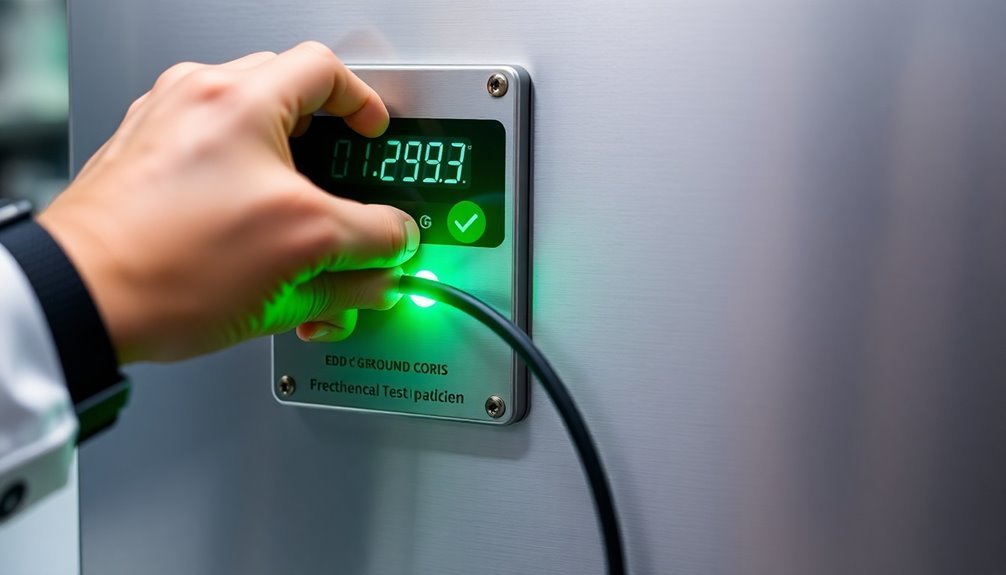
To verify personnel grounding safety, you'll need reliable testing tools that monitor both wrist straps and footwear systems. These testers come in various configurations, from simple wrist strap verifiers to thorough units that check both wrist straps and footwear simultaneously. Visual checks alone cannot reliably detect grounding equipment failures.
You'll find them available as portable devices, wall-mounted units, or fitted testing stations.
When testing wrist straps, you must wear them during verification to confirm all components function properly. Without a constant monitor, you'll need to perform these tests at least daily.
For footwear testing, you'll use testers with either continuous or split footplates that verify your shoes' grounding capabilities.
Many modern testers now include data logging features, which you'll find helpful for maintaining quality control records and conducting audits. These systems can track each operator's testing compliance and provide immediate feedback on grounding effectiveness.
To meet ANSI/ESD S20.20 requirements, you'll need to confirm your testing equipment verifies that all personnel grounding devices maintain proper resistance levels. Remember, grounding devices can fail without visible signs, making regular testing vital for maintaining your static control program's integrity.
Environmental Monitoring Equipment
Maintaining a static-safe environment requires thorough monitoring equipment to detect, measure, and control electrostatic charges. You'll need various sensors and detectors to continuously monitor static levels in your facility.
Static sensors like the IZD10 paired with monitors provide fixed-point observation, while handheld electrostatic meters help you diagnose specific areas of concern. Common point grounding is essential for ensuring all monitoring equipment maintains the same electrical potential.
Your environmental monitoring strategy should include extensive static neutralization equipment. Ion boxes and air flow ionizers effectively neutralize charges, while nozzle and bar ionizers target specific areas based on your application needs.
You'll want to integrate continuous monitoring systems to provide real-time feedback on static levels throughout your controlled environments.
Essential monitoring equipment for your ESD Protected Area includes:
- Static sensors and detectors for ongoing observation
- Ionization equipment to neutralize static charges
- Surface resistance testers to verify control measures
- ESD event counters to track protection effectiveness
Regular testing and auditing of your monitoring equipment guarantees reliable static control. Remember to verify grounding and bonding connections frequently, as they're critical components of your static control program's success.
Don't forget to document all monitoring results to maintain compliance and track program effectiveness.
Surface Resistivity Testing Methods
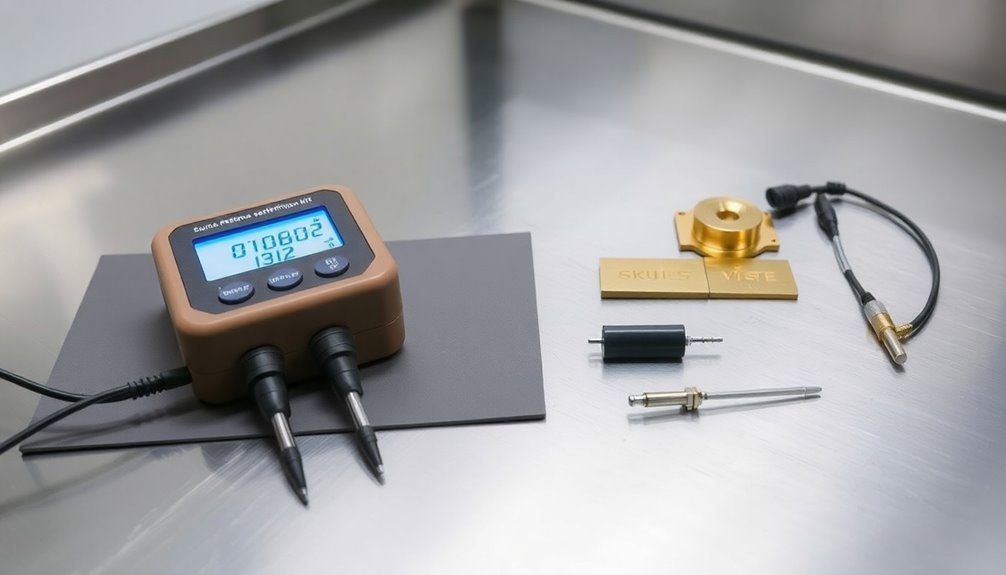
Surface resistivity testing plays a vital role in verifying your static control measures through two primary methods: ASTM D257 for ESD materials and AASHTO standards for concrete surfaces.
When you're testing ESD materials, you'll need to follow ASTM D257, which requires electrodes under load to measure surface resistance. You'll calculate surface resistivity by multiplying the resistance by the electrode perimeter and dividing by the gap distance. Maintaining good contact between your sample and electrodes is critical to obtain accurate readings.
For concrete testing, you'll use the four-probe Wenner electrode array following AASHTO TP 95 and T 358 standards. This method's particularly efficient, as you can complete readings in under 5 minutes, compared to the traditional RCPT test that takes over 2 days. Probe spacing must be greater than the largest aggregate size to ensure measurement accuracy.
You'll apply a low-frequency alternating current through the outer electrodes while measuring electrical resistance with the inner probes.
You'll find that both methods are cost-effective for quality control. Many states have already adopted surface resistivity testing in their specifications, particularly for concrete applications, due to its reliability and time efficiency. The equipment's relatively inexpensive, and you can perform tests on-site with minimal sample preparation.
Static Charge Detection Devices
Detection devices form the backbone of any effective static control program, allowing you to identify and measure electrostatic charges across your facility. You'll find three main categories of detection equipment: handheld static meters, in-line static meters, and static charge indicators.
Handheld meters like the FMX-004 give you portable measurement capabilities and quantitative data for both positive and negative charges. These meters can measure static voltages of up to ±30 kilovolts at one inch distance.
When you need continuous monitoring in production environments, in-line meters such as the IQ Static Sensor Bar integrate directly into your manufacturing lines.
For quick troubleshooting, you'll find static charge indicators particularly useful, though they won't provide precise measurements.
Your measurement accuracy depends on proper technique and device selection. Consider these key factors:
- Surface potential sensors rely on electrostatic induction to measure field strength
- Distance between the sensor and charged object must remain consistent
- Voltage feedback-type meters offer enhanced precision by matching object charge
- Environmental conditions can affect measurement reliability
You'll need to choose your detection method based on your specific application requirements. Whether you're monitoring a production line or conducting spot checks, these devices help verify your static control measures are working effectively.
Package Testing Equipment
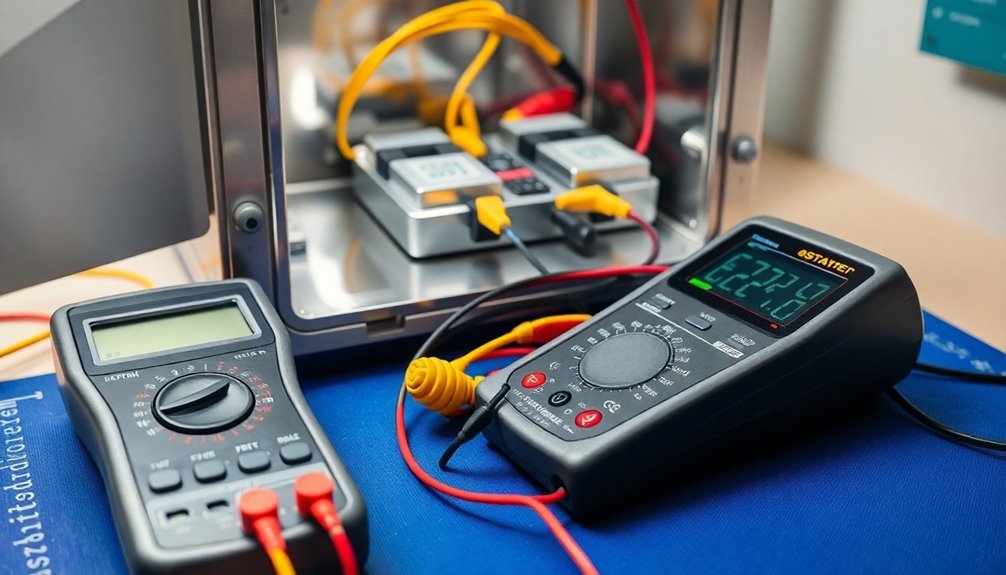
Quality assurance in ESD control requires thorough package testing equipment to verify the effectiveness of your protective materials. You'll need specific tools to measure surface resistance, surface resistivity, volume resistance, and volume resistivity of your packaging materials. These measurements help predict how well your materials will dissipate static charges.
For extensive testing, you'll want to include static shielding tests like ESD STM11.31, which measures energy penetration through protective bags. Charge plate monitors can help assess the performance of your static control measures.
Your testing equipment should comply with commercial and military standards, including ANSI/ESD S20.20 and ANSI/ESD S541. You'll need to conduct tests at different humidity levels to guarantee protection across various environmental conditions.
Essential equipment includes electrostatic test devices, environmental control products, and specialized fixtures for specific testing requirements.
You'll find ESD Test Suite Manager software helpful for generating reports on peak current and energy measurements. Don't forget to implement regular testing schedules based on your product value and ESD failure risks.
To maintain compliance, you should perform assessments that verify your ESD protective packaging meets industry standards and provides adequate discharge shielding for sensitive components.
Wrist Strap Testing Instruments
Your static control program requires daily testing of wrist straps using specialized equipment like the WST200 or GTS600K testers to verify proper resistance levels.
You'll need to maintain resistance measurements within ANSI/ESD S20.20 standards of less than 3.5 x 10^7 ohms for maximum protection.
For enhanced safety, you can implement continuous monitoring systems like the CM400 or CM410, which provide instant feedback if your wrist strap fails during operation.
Regular inspection of wrist straps helps identify potential issues like dirty cuff interiors that could compromise grounding effectiveness.
Daily Testing Equipment Requirements
To guarantee reliable ESD protection, wrist strap testing instruments must meet specific technical requirements for daily verification.
You'll need equipment that operates with a 14V open circuit voltage and accurately measures resistance within a range of 750 kilohms to 120 megohms, maintaining a ±1% tolerance level.
Your testing equipment should include clear visual indicators to verify proper functionality. When you're conducting tests, a green LED will illuminate if the resistance falls within acceptable parameters, while a red LED alerts you to out-of-range measurements.
- Test equipment must comply with ANSI/ESD S20.20 standards for verification
- Calibration should be performed annually using reference resistors
- Testing instruments should include a low battery indicator system
- Equipment must be capable of measuring from 750 kilohms to 10 megohms for standard verification
You'll need to perform daily testing of all wrist straps to maintain compliance with ESD control requirements. While continuous monitoring systems can replace daily testing in high-sensitivity applications, you must still maintain regular verification procedures.
Keep detailed records of your testing results using trend charts to track ESD control effectiveness and implement corrective actions when needed.
Continuous Monitoring Systems
Reliability in ESD protection reaches new heights with continuous monitoring systems for wrist strap testing. You'll find two main types: single-wire monitors for less critical applications and dual-wire monitors for essential operations requiring redundant ground paths. Both systems eliminate the need for periodic testing while providing instant feedback on wrist strap functionality.
Feature | Single-Wire | Dual-Wire |
---|---|---|
Cost | Lower life-cycle cost | Higher initial investment |
Application | Less critical operations | Critical manufacturing |
Reliability | Basic monitoring | Redundant monitoring |
You'll benefit from these systems through real-time tracking of both operators and workstations. They'll test electrical connections between ground points, cords, wristbands, and operators while alerting you to failures through visual and audible alarms. What's more, you can integrate these monitors into your facility's ESD management program for thorough protection.
When implementing continuous monitoring, you can utilize remote management software for real-time data analysis and quick issue resolution. You'll need to follow standard protocols like ESD TR20.20 for ideal results, ensuring your static control program maintains its effectiveness throughout your facility.
Resistance Measurement Standards
Beyond continuous monitoring, precise resistance measurement stands as a cornerstone of effective wrist strap testing. You'll need specialized equipment like the Vermason 225220 Wrist Strap Tester or comparable resistance meters to confirm compliance with ANSI/ESD S1.1 and EN 61340-5-1 standards.
When testing, you must verify that interior resistance remains ≤1×10^5 ohms while exterior resistance stays ≥1×10^7 ohms.
Your testing protocol should include these essential measurements:
- Point-to-point resistance between interior and exterior surfaces
- Resistance to ground from the wrist strap to the connection point
- Complete system resistance including cuff, cord, and skin contact
- Verification of groundable point connectivity and conductivity
You'll want to use a shielded lead for ground testing, connecting the black lead to your ground point. Remember to conduct regular tests – your frequency may vary from once per shift to multiple daily checks, depending on your facility's requirements.
Each measurement should be documented using your test station's logging capabilities to maintain compliance records. If you're using portable testers, they'll provide immediate pass/fail results to help you quickly identify any wrist straps that don't meet the ≤10 megohm functional limit.
Frequently Asked Questions
How Often Should ESD Control Program Training Be Renewed for Certified Personnel?
You'll need to renew your ESD control program training every 24 months to maintain certification. You must pass a written test with at least an 80% score during each renewal session.
What Humidity Levels Are Optimal for Minimizing ESD Risks?
You'll want to maintain relative humidity between 40% and 60% for ideal ESD control. Anything below 30% substantially increases discharge risks, while too much humidity can cause condensation problems.
Can Mobile Phones Be Allowed in Esd-Protected Areas?
You shouldn't allow mobile phones in ESD-protected areas due to their static electricity generation and EMI risks. If they're necessary, use designated zones or shielded containers and guarantee proper grounding measures.
How Long Do Static Dissipative Floor Finishes Typically Last?
You'll find that static dissipative floor finishes typically last 12-18 months with proper maintenance. However, you'll need to guarantee regular cleaning and avoid using generic floor waxes to maintain their effectiveness.
Should Visitors Wear Full ESD Protection When Briefly Touring Manufacturing Areas?
Yes, you must wear full ESD protection, even for brief tours. Static damage can occur instantly, and you'll need ESD smocks and shoe coverings to protect sensitive electronic components in manufacturing areas.
In Summary
You'll need these tools and testing methods to maintain an effective static control program. By regularly using ESD measuring equipment, verifying ground systems, and checking personnel grounding, you're protecting sensitive components from damage. Don't forget to monitor your environment, test surface resistivity, and verify packaging materials. Make wrist strap testing a daily habit – it's your first line of defense against costly ESD events.
Leave a Reply