For maximum protection of your production line, you'll want to invest in a dual-wire continuous monitoring system. These systems offer real-time ESD threat detection, redundant grounding paths, and immediate alerts if anything goes wrong. Unlike basic single-wire monitors, dual-wire systems provide backup protection if one conductor fails, making them ideal for sensitive component handling. You'll benefit from extensive data logging, automated compliance reporting, and elimination of daily testing requirements. While they cost more upfront than simpler options, the enhanced protection and long-term savings make them worth exploring further.
Understanding ESD Monitor Types
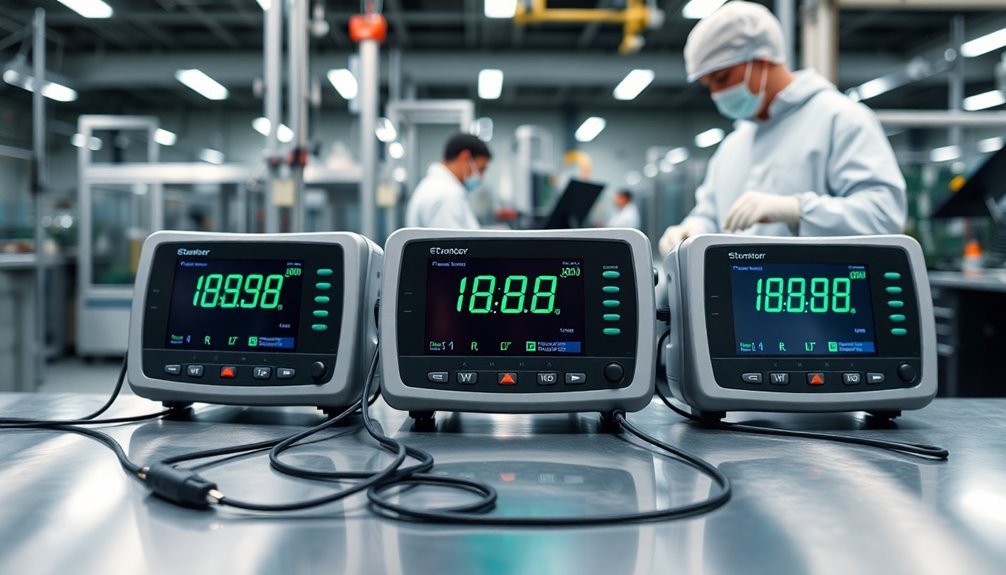
Throughout the electronics manufacturing industry, ESD monitors serve as critical safeguards against static discharge damage.
You'll find four main types of monitors, each designed for specific production needs and protection levels.
Single-wire impedance monitors offer you the most cost-effective solution, using AC voltage to detect grounding path issues through impedance changes. These monitors help reduce testing time and manual logging requirements before shifts begin.
They're simple to operate and work well with standard wrist straps, though they lack redundant grounding paths.
Dual-wire resistance monitors provide enhanced protection by continuously checking the resistance loop through two conductors.
You'll need special dual-wire wrist straps, but you'll gain reliable redundancy if one conductor fails.
When you need to monitor specific areas or tools, ESD event monitors detect discharge pulses using electromagnetic sensing.
They're compact and adaptable, with adjustable thresholds and integration capabilities for your factory systems.
For extensive protection, continuous monitoring systems track real-time ESD conditions across your production environment.
These systems use fieldmeters to detect static buildup and are particularly effective in SMT and FATP lines, where you'll need constant vigilance against ESD risks.
Cost Versus Protection Benefits
Balancing cost considerations with protection advantages requires careful analysis of your production needs. When evaluating ESD monitors, you'll need to weigh the initial investment against long-term savings and protection capabilities. Modern manufacturing's increased reliance on automation makes comprehensive ESD monitoring more critical than ever.
Continuous monitoring systems eliminate daily testing requirements, saving you time and labor costs while detecting intermittent failures that periodic testing might miss.
You'll find that single wire monitors offer a cost-effective solution, working well with standard wrist straps and using capacitance technology to reduce false alarms. However, if you're handling highly sensitive components, dual wire systems provide enhanced reliability through resistance monitoring, despite their higher cost.
The protection advantages justify the investment, as continuous monitors provide immediate feedback through audible and visual alarms when grounding failures occur. You're getting real-time protection that guarantees consistent grounding and reduces the risk of static damage.
Advanced systems can monitor multiple operators and worksurfaces simultaneously, while factory-calibrated units eliminate the need for adjustments or recalibration. When you factor in the potential costs of ESD damage and production delays, investing in extensive monitoring systems often proves more economical in the long run.
Single Wire Monitoring Solutions
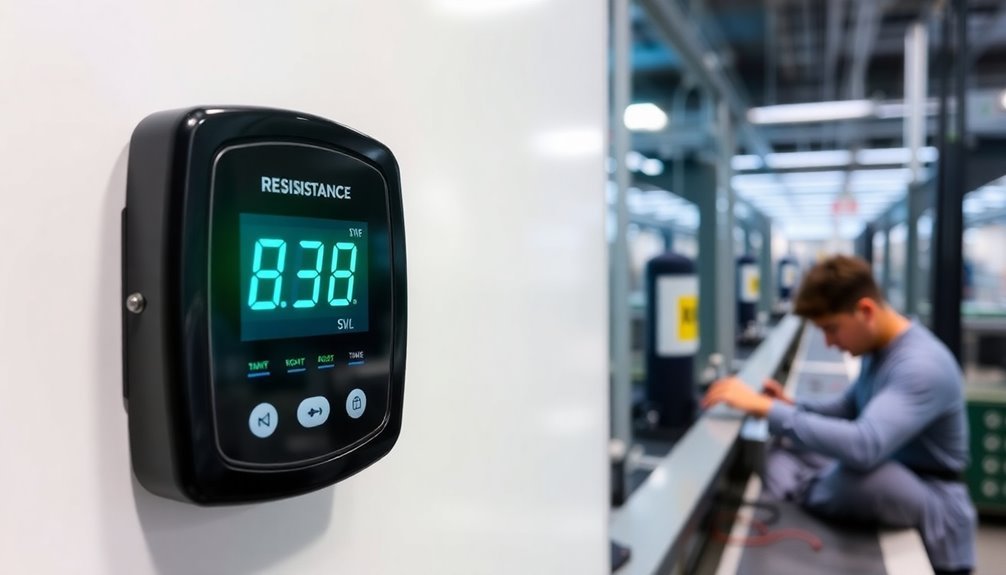
You'll find single wire monitoring solutions offer a cost-effective approach to ESD protection while maintaining essential safety standards through capacitance-based impedance detection.
Your installation process becomes remarkably straightforward since these monitors only require connecting a single wire to the operator's wrist strap and mounting the unit under a workbench. The go/no-go system ensures easy verification without complex calibration procedures.
With built-in alarms and continuous monitoring capabilities, you're getting reliable protection without the complexity and expense of dual-wire systems.
Cost-Effective Protection Solutions
When seeking cost-effective ESD protection solutions, single-wire monitoring systems stand out as an economical choice for production lines. You'll find these systems particularly appealing if you're working with standard single-wire wrist straps and coil cords, as they integrate seamlessly with existing equipment. Clean room conditions are crucial for maximizing the effectiveness of these monitoring systems.
The straightforward setup and operation make them ideal for less critical applications where you need basic ESD protection without a substantial investment.
- You can leverage your current single-wire wrist strap inventory, eliminating the need for complete equipment replacement.
- You'll benefit from simple installation and minimal training requirements, reducing implementation time and costs.
- You're able to scale your ESD protection across multiple workstations without significant financial impact.
While single-wire monitors rely on capacitance for ground detection, you should be aware of their limitations. They may not detect all resistance issues and can be susceptible to false readings.
If you're operating in a critical production environment, you'll want to weigh these limitations against the cost savings, as dual-wire systems offer more reliable monitoring despite their higher price point. Consider your specific production needs and risk tolerance when making your decision.
Impedance Detection Benefits
Impedance detection technology enhances the reliability of single-wire monitoring systems through continuous measurement of the ground loop. Your monitor will detect subtle changes in the impedance between the wrist strap, cord, and operator using low AC voltage, ensuring consistent protection against ESD risks.
You'll benefit from the monitor's ability to sense phase differences between current and voltage, which helps identify potential grounding issues before they cause damage. The system continuously checks the entire ground path, including proper skin contact, and immediately alerts you through visual and audio signals if there's a problem. Operating at a price range of $30-$100, these monitors provide an economical solution for static control needs.
You won't need to worry about regular calibration since these monitors come factory-calibrated, and you can easily install them under your workstation to save space.
While you'll find the single-wire technology more cost-effective than dual-wire systems, you should be aware of its limitations. The monitor's sensitivity can vary based on operator size and clothing, and you might need to tune it specifically for your installation.
Despite these considerations, you'll get reliable protection that meets ANSI ESD S20.20 standards, making it a practical choice for most production environments where continuous ESD monitoring is essential.
Simplified Installation Process
Building on the reliable protection offered by impedance detection, the installation process for single-wire monitoring systems stands out for its straightforward approach.
You'll find that these systems require minimal setup – just plug in your wrist strap, and you're ready to start monitoring. The fixed resistor system eliminates complex configuration steps, making it an efficient choice for production environments where time is critical. Single-wire monitors utilize parasitic capacitance technology for functionality.
The simplified installation process delivers several key advantages for your production line:
- You won't need ongoing calibration adjustments since these monitors come factory-calibrated and maintain their settings.
- You can quickly connect standard single-wire wrist straps without special adapters or additional equipment.
- You'll save time on setup as the monitor automatically begins functioning once properly connected.
While setting up your single-wire monitoring system, you should consider the specific requirements of your workstation.
Though the basic installation is straightforward, you might need to adjust the monitor's sensitivity based on your environment and operators.
The system's compatibility with most standard wrist straps means you can integrate it seamlessly into existing ESD protection protocols without replacing your current equipment.
Advanced Features Worth Considering
Modern ESD monitoring systems come with an array of powerful features that you'll want to contemplate for your production line. Key among these is real-time monitoring capability that alerts you instantly to static charge buildup through visual and audible alarms.
You'll benefit from hyperlinked facility layouts that let you quickly navigate to problem areas and track thorough static field histories for each PCBA. Ground path impedance monitoring ensures optimal tool reliability and safety.
The system's data collection abilities provide valuable insights through static charge heat maps, helping you identify trouble spots before they cause damage. You can generate detailed reports for any time period and categorize faults by type and duration, enabling data-driven decisions about line readiness.
You'll appreciate the customization options, including remote adjustment of monitor limits through a dedicated app and variable antenna orientations for specific applications.
The system integrates seamlessly with your existing factory monitoring setup, using off-the-shelf components for easy deployment. For larger facilities, you can scale the solution while maintaining reliable data storage through digital conversion and local servers.
Annual calibration guarantees ISO certification compliance, providing you with a robust ESD management system that surpasses traditional audit requirements.
Installation and Maintenance Requirements
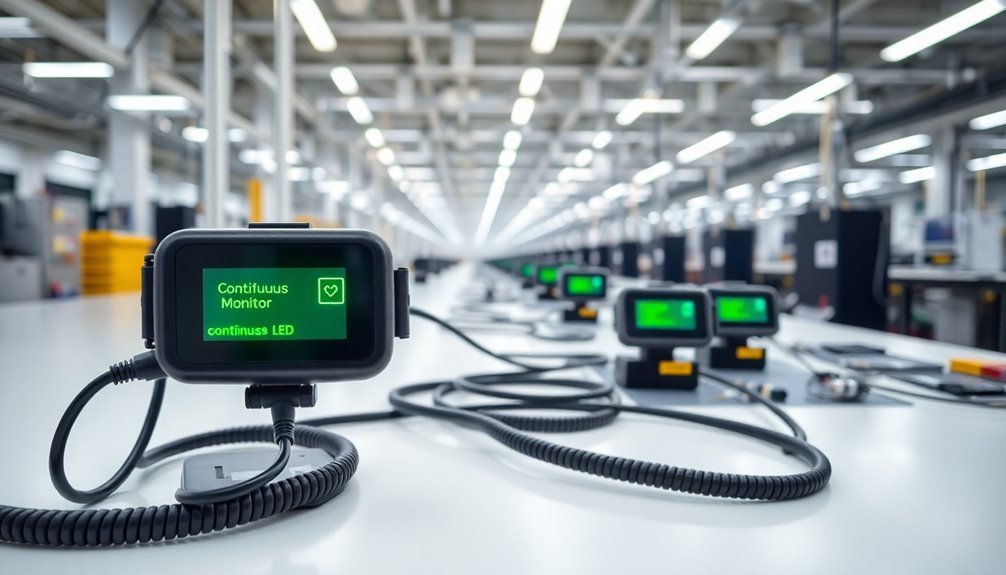
While advanced monitoring features enhance your ESD protection, proper installation and maintenance verify their effectiveness.
You'll need to start by connecting your ground cords to a green wire building ground point and setting up your workstation properly. Install your wrist band directly on bare skin, lay the table mat flat with snaps facing you, and ascertain all ground connections are secure. Place the floor mat in front of your workbench with snaps toward bench.
Maintaining your ESD monitoring system requires consistent attention to these critical elements:
- Test your workstation's continuity immediately after installation using a surface resistivity meter and perform daily checks on wrist strap/operator combinations.
- Clean your ESD mats quarterly with specialized static mat cleaners and remove all nonessential plastic items from the area.
- Use constant monitors to verify your ESD protection system's effectiveness continuously.
For proper grounding, you've got several reliable options.
You can ground through an AC adapter, use a workstation monitor ground wire, or implement a one megohm mat ground cord. Remember to select appropriate test voltages and resistance limits based on your specific requirements, and mount your monitor where operators can easily see the indicator lamps.
Performance Standards and Compliance
Under strict industry regulations, your ESD monitoring system must comply with ANSI/ESDA S20.20 standards and undergo regular performance evaluations.
You'll need to maintain thorough monitoring of all grounding points, including metal grounds, static-dissipative surfaces, and operator connections. Regular audits and continuous verification guarantee your static control procedures remain effective.
Your monitoring system should include multiple capabilities to guarantee complete protection. Impedance monitors use low AC voltage to detect changes, while resistance monitors check the complete operator-to-ground loop.
You'll want work surface and tool monitoring features for additional safety, along with data logging capabilities to track ESD events and maintain compliance records.
To evaluate performance effectively, you'll need to monitor static voltage levels, ionization parameters, and ESD events in real-time. Calculate Ppk values to determine if you need additional ionization measures.
Your system must satisfy ISO logging requirements and help prevent latent damage to sensitive components. By maintaining reliable grounding and continuous monitoring, you'll protect your production line from ESD-related issues while meeting industry standards and quality control requirements.
Frequently Asked Questions
Can ESD Monitors Detect Faulty Wristbands Before They Completely Fail?
Yes, continuous ESD monitors can detect when your wristbands are starting to fail. They'll alert you to issues like over-flexed cords and resistance problems before complete failure occurs, helping prevent component damage.
How Often Should ESD Monitors Be Tested for Accuracy?
You should test your ESD monitors daily for frequently used equipment, especially wrist straps. For continuous monitoring systems, perform calibration checks monthly and full calibration annually to guarantee reliable protection and accuracy.
Do Temperature and Humidity Affect ESD Monitor Performance?
Yes, temperature and humidity can affect your ESD monitor's performance. While they don't directly impact accuracy, these factors influence static electricity levels in your workspace, which your monitor needs to measure and control effectively.
Can Multiple Operators Share the Same ESD Monitoring Station?
Yes, you can share ESD monitoring stations with multiple operators. Many monitors support two or more workers simultaneously, but you'll need to guarantee each operator has their own wrist strap connected to the monitoring system.
Are Wireless ESD Monitoring Systems as Reliable as Wired Ones?
While wireless ESD monitoring systems offer flexibility, they're not as reliable as wired ones. You'll face potential signal interference, battery concerns, and security risks that you won't encounter with traditional wired systems.
In Summary
When choosing your ESD monitor, you'll need to balance cost, protection level, and operational needs. Single wire monitors offer basic protection, while continuous monitors provide enhanced security. Remember to factor in maintenance costs and compliance requirements. You won't regret investing in advanced features if they align with your production demands. Make your selection based on your specific manufacturing environment and budget constraints.
Leave a Reply