The three most effective protective foam options for your electronics are conductive, anti-static, and static dissipative foam. Each type serves a specific protection level: conductive foam (10^3-10^5 ohms) offers Faraday cage protection for highly sensitive components, anti-static foam (10^6-10^9 ohms) prevents basic static buildup, and static dissipative foam (10^8-10^11 ohms) allows gradual discharge for work-in-progress items. You'll find these foams available in both polyethylene (closed-cell, moisture-resistant) and polyurethane (open-cell, flexible) varieties. Understanding the key differences between these foam types will help you make the best choice for your electronic protection needs.
Anti-Static Foam Protection Basics
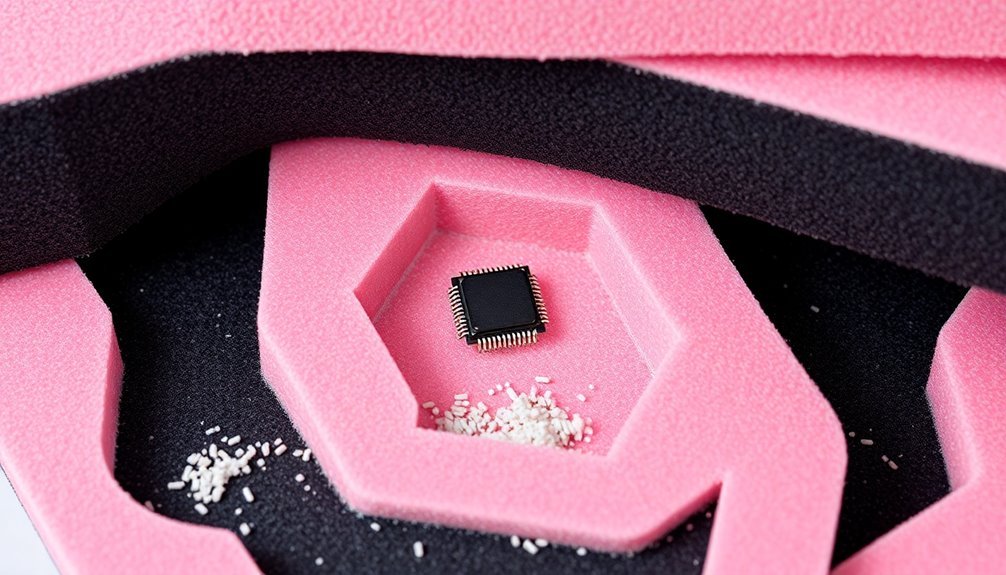
Most electronic components are highly sensitive to static electricity, making anti-static foam protection essential for safe handling and transport.
Pink-colored foam makes it easy to identify anti-static materials at a glance during packaging and handling operations.
Anti-static foam, made from polyurethane or polyethylene with conductive fillers, creates a protective path that safely dissipates electrostatic charges. With a surface resistance of 10^6-10^9 ohms, this specialized foam effectively prevents static buildup that could damage your sensitive electronics.
When you're selecting anti-static foam, you'll need to evaluate your specific requirements. The foam comes in various thicknesses and surface patterns, including smooth and eggcrate designs, to match your packaging needs. You can choose between rigid or soft options depending on your components' weight and sensitivity.
The foam not only dissipates static charges but also provides excellent cushioning against physical impacts. Whether you're shipping circuit boards, computer chips, or other electronic components, you can customize the foam by cutting it to fit your specific items.
For complete protection, you might want to combine anti-static foam with additional shielding solutions, such as conductive bags, especially for highly sensitive components.
Polyethylene Vs Polyurethane Performance
A key distinction between polyethylene and polyurethane foam lies in their fundamental structures and performance characteristics. While polyethylene features a closed-cell structure that's dense and resistant to liquids, polyurethane has an open-cell composition that allows air to flow freely. This structural difference substantially impacts their performance in electronics protection. Its high adhesion power helps secure components firmly in place during transport and storage.
You'll find polyethylene foam offers superior moisture resistance and durability, making it an excellent choice for protecting sensitive electronic components. Its closed-cell structure prevents water penetration, and its firm nature provides consistent protection against impacts.
The foam's ability to be laminated adds extra protection against heat and gases.
When considering polyurethane foam, you're looking at a material that's softer and more flexible. While it provides excellent cushioning, its open-cell structure makes it more susceptible to moisture damage, especially in ester-based variants. This characteristic might make it less suitable for long-term electronics storage in humid environments.
For electronics protection, polyethylene's moisture resistance and structural stability often make it the more reliable choice. However, if your application requires specific cushioning properties and isn't exposed to moisture, polyurethane could still serve your needs effectively.
ESD Foam Application Guide
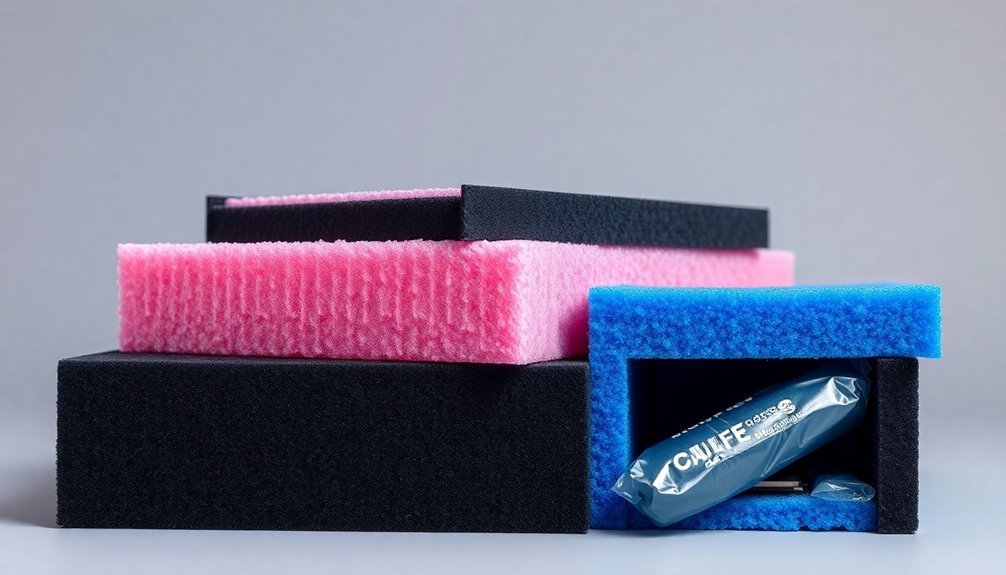
The selection of appropriate ESD foam requires understanding three distinct categories: conductive, anti-static, and static dissipative foams. Each type serves specific protection needs for your electronic components during storage, handling, and transportation.
Foam Type | Resistance (Ohms) | Best For |
---|---|---|
Conductive | 10^3-10^5 | High-sensitivity components requiring Faraday cage protection |
Anti-static | 10^6-10^9 | Components needing basic static build-up prevention |
Static Dissipative | 10^8-10^11 | Work-in-progress items requiring gradual discharge |
When you're handling highly sensitive electronics that need complete shielding, you'll want to use conductive foam with its surface resistivity under 10^4 ohms/sq. It'll act as a Faraday cage, eliminating the need for additional static shielding bags. For less sensitive components where you're primarily concerned with preventing static build-up, pink anti-static foam will suffice. If you're working with components that need controlled discharge rates, choose blue static dissipative foam. It'll allow charges to dissipate gradually, preventing sudden static shocks that could damage your delicate electronics. While conductive foam costs more, it offers superior protection for long-term storage and transportation needs. The open-cell structure of PU foam variants allows for customization to precisely fit specific electronic components.
Frequently Asked Questions
How Long Does Protective Foam Maintain Its Shock-Absorption Properties Over Time?
You'll find that high-quality protective foams like PORON polyurethane and BISCO silicone maintain their shock-absorption properties for years due to their open-cell structure, which resists compression set and stress relaxation.
Can Protective Foam Be Safely Recycled With Regular Household Recyclables?
No, you can't recycle protective foam with regular household recyclables. You'll need to find specialized drop-off locations or recycling facilities that handle foam specifically, as most curbside programs don't accept it.
What Temperature Ranges Can Different Protective Foam Types Safely Withstand?
You'll find different foams have varying temperature tolerances: polyurethane (-20 to 100°C), polyethylene (-40 to 80°C), conductive foam (-10 to 85°C), and specialized insulation foams can handle up to 300°C in extreme conditions.
Does Colored Protective Foam Offer the Same Protection Level as Standard Versions?
Yes, you'll get the same protection level regardless of foam color. The foam's protective qualities come from its material composition and anti-static/conductive properties, not its color. Pink, black, or other colors work equally well.
How Do Humidity Levels Affect the Protective Qualities of Different Foams?
You'll find that humidity substantially impacts foam protection. Low humidity makes foam brittle and increases static risks, while high humidity can cause deterioration. For best results, maintain levels between 30-70% relative humidity.
In Summary
You'll find that choosing the right protective foam makes all the difference in safeguarding your electronics. Whether you select polyethylene for its durability, polyurethane for its cushioning, or specialty ESD foam for static-sensitive components, proper application is key. Remember to measure your items carefully and consider the foam's density rating before making your final choice. With these options, you're well-equipped to protect your valuable electronics.
Leave a Reply