Your ESD protection plan needs thorough documentation covering four key areas: program scope, personnel training, zone identification, and verification protocols. You'll need to maintain detailed records of your ESD coordinator assignments, training completion certificates, and EPA zone markings that align with ANSI/ESD S20.20 standards. Your documentation must include equipment grounding test results, static survey data, and regular audit schedules. Don't forget to specify your protective materials requirements and compliance verification procedures. The depth of your documentation directly impacts your facility's ESD protection effectiveness and audit success.
ESD Control Program Scope
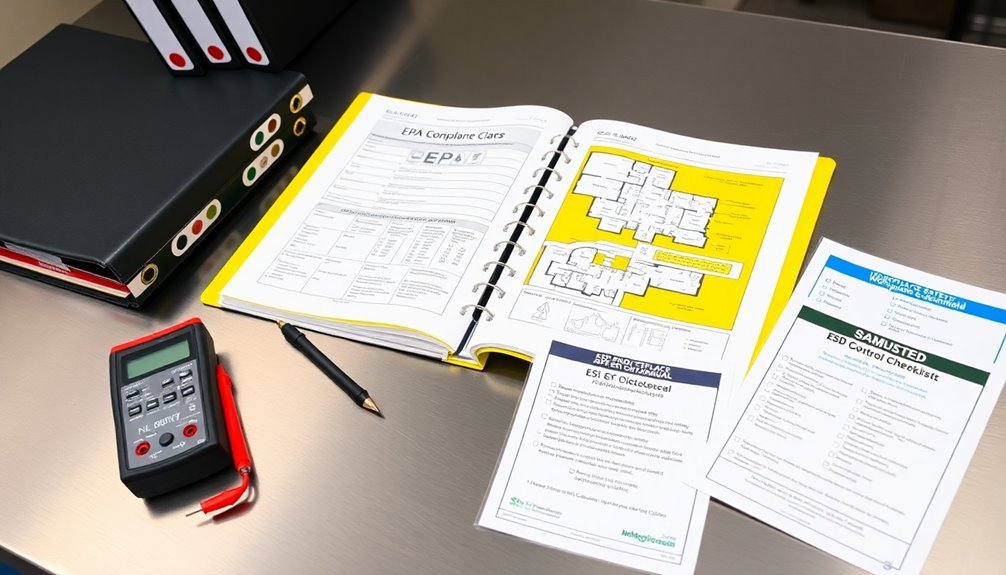
Through careful planning and documentation, an ESD Control Program establishes the framework for protecting sensitive electronic components from static discharge damage. You'll need to clearly define your program's scope by identifying all tasks and activities required to safeguard ESD-sensitive items in your facility.
Start by documenting the specific Human-Body Model (HBM) and Charged-Device Model (CDM) sensitivity levels of your ESD-susceptible components. Your scope should align with industry standards like ANSI/ESD S20.20 and IEC 61340-5-1, which provide the foundation for your program's administrative and technical requirements.
Establishing an ESD coordinator and team is essential for implementing and maintaining your control program effectively. You'll want to outline the procedures necessary to protect ESDS items throughout their handling, storage, and transportation. This includes identifying the ESD Protected Areas (EPAs) where these components will be processed.
Your documentation should specify the required materials, equipment, and control measures needed in these areas.
Make sure you're maintaining detailed records of your program's technical specifications, including approved ESD protective products and verification processes.
Your scope documentation should serve as a thorough guide that connects all elements of your ESD control strategy while meeting both industry standards and your company's specific needs.
Personnel Training Documentation Requirements
A well-defined ESD Control Program must include thorough documentation of personnel training requirements. You'll need to maintain records of all training materials, completion certificates, and compliance verifications for your entire workforce, including line workers, management, and contractors.
Your training documentation should detail the content covering static electricity fundamentals, ESD control procedures, and specific role requirements. Regular retraining needs must be tracked through an established system.
You must keep records of the various training methods used, such as live instruction, videos, and computer-based programs. It's crucial to document how you've adapted these materials for different educational levels and cultural considerations across your facilities.
Store all training-related documents in a central repository, including ANSI/ESD S20.20 standards, technical papers, and educational resources.
You'll need to maintain measurement records for three years and audit documentation for ten years in your Quality Assurance Office.
Document your compliance verification process, including the use of test equipment like electrostatic field meters and resistance meters.
Keep detailed records of any non-compliance incidents, including warnings issued, retraining provided, and disciplinary actions taken.
Make sure you document the certification process and maintain proof of successful completion for each employee.
EPA Zone Identification
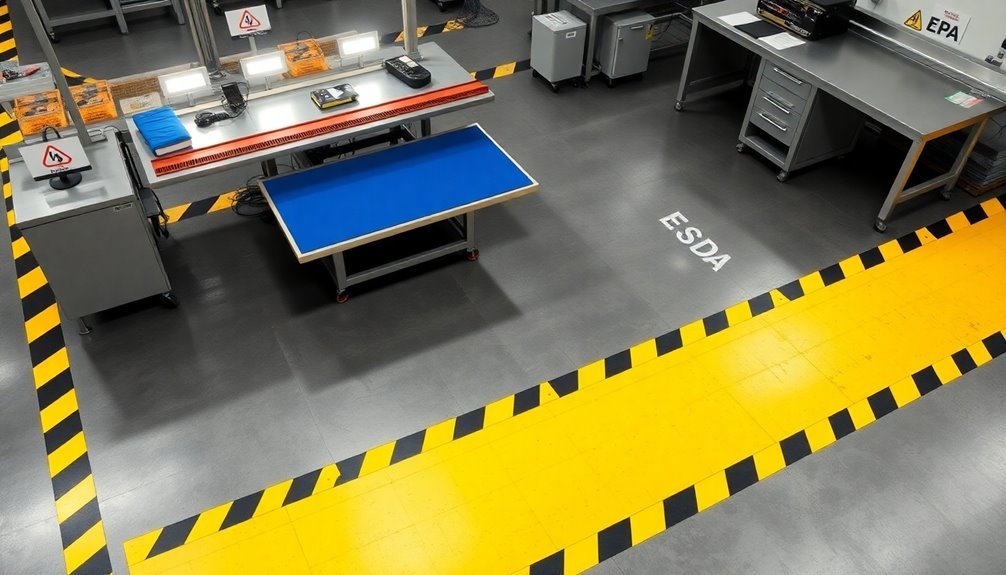
To establish clear EPA zone boundaries, you'll need to implement physical markers like ESD tape, floor markings, and barrier systems that define protected areas from non-protected spaces.
Maintaining proper humidity levels in these zones helps minimize static buildup and ensures effective static control measures.
You must control access to these zones through designated entry points equipped with appropriate ESD protection measures, including wrist strap testers and footwear checking stations.
Within the EPA, you're required to display prominent signage and warning labels that communicate ESD protocols, identify sensitive areas, and remind personnel of necessary precautions.
EPA Boundary Marking Systems
When establishing an Electrostatic Protected Area (EPA), clearly marked boundaries serve as critical visual indicators that alert personnel to ESD-sensitive zones.
You'll need to guarantee your boundary markings comply with 61340-5-1 standards and remain visible from all angles, particularly in areas with multiple workstations. The ESD Coordinator determines proper placement and selection of all EPA boundary markings.
You can implement several effective marking methods. Standard signage should be positioned at entrance points and above workstations, while floor tape, color-coded flooring, or distinctive carpet patterns can provide additional visual cues.
If you're dealing with high-voltage areas, you'll need to include supplementary safety signage to meet requirements.
Your boundary marking system must work alongside proper grounding procedures. You'll want to maintain a low resistance path to ground (less than 2 Ω) through your EPA ground system.
It's essential that you regularly evaluate these systems and guarantee all equipment within the EPA complies with standards.
Remember that your primary goal is maintaining constant awareness of EPA boundaries among personnel. Whether you choose signs, floor markings, or a combination of methods, they must effectively communicate EPA zones to everyone in the facility.
Zone Access Control Methods
Effective zone access control within your EPA requires a multi-layered system of physical and procedural safeguards.
You'll need to implement strict access control measures using swipe cards and door locks while maintaining detailed documentation of all personnel movement within the protected areas.
Start by defining clear access levels and guaranteeing that only properly trained and certified staff can enter specific zones. You'll want to establish designated ESD test areas and implement exhaustive grounding systems for both personnel and equipment.
Make sure your staff uses appropriate wrist straps and ESD control footwear when entering sensitive areas. The common point ground system must be established to ensure all workstation components maintain the same electrical potential.
Your documentation should include regular audit records, training certifications, and maintenance logs for all grounding equipment. You'll need to carefully control the materials entering the EPA, allowing only ESD-safe items and implementing proper handling procedures for sensitive components.
Design your EPA layout to minimize external interference and reduce triboelectric charging risks. Create clearly marked zones and arrange workstations strategically to maintain ESD safety.
Don't forget to regularly test and certify your EPA to guarantee ongoing compliance with ESD control standards and regulations.
Signage and Warning Labels
Building upon your access control system, proper signage and warning labels serve as the visual backbone of your EPA safety protocol. You'll need to guarantee all EPA boundaries are clearly marked and visible from at least three feet away, using the standardized ESD symbol in black on a yellow background.
For ESD-sensitive devices, you must apply caution labels on protective packages that include phrases like "ATTENTION STATIC SENSITIVE DEVICES" and "HANDLE ONLY AT STATIC SAFE WORK STATIONS." These labels should follow EIA-471 standards. Similar to electrical enclosures, these signs must be plainly visible for safety compliance.
Element | Requirement | Positioning |
---|---|---|
EPA Signs | Black ESD symbol on yellow | Boundary entrances |
Warning Labels | ESD caution symbol | Protective packages |
Boundary Markers | Contrasting colors | Floor perimeter |
Work Station Signs | "ESD HANDLING REQUIRED" | Each station |
Container Labels | ESD warning text | All storage units |
You can mark EPA boundaries using floor tape, colored tiles, or carpet sections. Remember that your EPA can range from a single workstation to an entire factory floor. Whatever method you choose, it must effectively alert personnel to the EPA boundary and communicate the need for ESD precautions within that area.
Equipment Grounding Verification Records
You'll need to maintain detailed records of your daily ground test results to guarantee compliance with ANSI/ESD S20.20-2007 standards and regulatory requirements.
Your resistance measurements must meet specific standards, including less than 10,000 ohms for static grounding points, while using approved testing methods like the three-point or fall-of-potential method.
Regular inspection logs of your grounding systems serve as essential evidence of conformity and must document all tests performed immediately after installation, repairs, modifications, and annual verifications. A Compliance Verification Plan must be established to ensure all technical requirements are met and documented properly.
Daily Ground Test Results
Regular documentation and records of daily ground test results stand out as one of the most critical components in maintaining electrical static protection.
You'll need to include specific time and date entries for each test you perform, along with precise resistance measurements obtained during testing procedures. When you notice any readings that fall outside acceptable parameters, you must document these deviations immediately.
Your daily ground test documentation should detail any corrective measures you've implemented to address problems discovered during testing. You'll want to use a clamp-on ground resistance tester for non-intrusive measurements and follow ANSI/ESD standards when measuring resistance from probe to ground. The fall-of-potential method should be used when thorough and reliable ground resistance measurements are required.
It's essential that you conduct these tests after any modifications to your electrical system.
Store all your test results in a secure yet accessible location, maintaining a thorough historical database of measurements. You'll need to perform walking voltage tests and body voltage assessments to verify your static control measures remain effective.
Remember to conduct ground fault coordination studies at each voltage level and include these findings in your documentation. This systematic approach helps you maintain compliance while creating a reliable record of your grounding system's performance.
Resistance Measurement Standards
Maintaining accurate resistance measurement standards requires adherence to specific verification methods and testing protocols. You'll need to employ the Fall-of-Potential Test, a 3-point measurement method that uses a voltmeter to determine ground resistance.
When conducting this test, you must position the auxiliary potential rod outside the effective resistance area to guarantee accurate readings.
You're required to meet specific resistance limits that vary by application, with 1 kV installations demanding 4 Ohms or less. OSHA and NEC standards mandate annual testing after installation, repairs, or modifications, and you'll need to maintain detailed records available for inspection.
Your testing equipment must include meters capable of measuring high voltages and currents, with true DC metering capability for precise data analysis.
You'll need certified personnel to perform these tests correctly, as improper testing can void equipment warranties. Your documentation should include thorough site surveys, specification reviews, and written reports with recommendations.
Don't forget to obtain certificates of certification to validate your test results. Remember that clamp-on induced frequency tests are also acceptable methods for resistance measurement verification.
Grounding System Inspection Logs
Grounding system inspection logs serve as critical documentation for tracking and verifying equipment grounding performance. You'll need to maintain detailed records of annual resistance testing, which must be readily available upon request.
When you conduct tests immediately after installation, repairs, or modifications, you must document these results to demonstrate compliance with MSHA standards, particularly 56/57.12028.
You should include soil resistivity test results in your logs, as they're essential for proper grounding system installation. Your documentation must reflect the use of clamp-on testing methods and adherence to IEEE and NETA standards.
Make sure you're recording all visual inspection findings that verify proper bonding and grounding connections.
Your logs need clear labeling with safety symbols, specific grounding connection points, and testing dates. You'll want to document your common point ground connections and ESD control measures.
These records aren't just paperwork – they're your proof of maintaining electrical safety and preventing hazards. By keeping thorough inspection logs, you're protecting against costly downtime and ensuring compliance with safety regulations.
Remember to include measurements from your most recent tests, as these values are vital for tracking system performance over time.
Static Survey Protocols
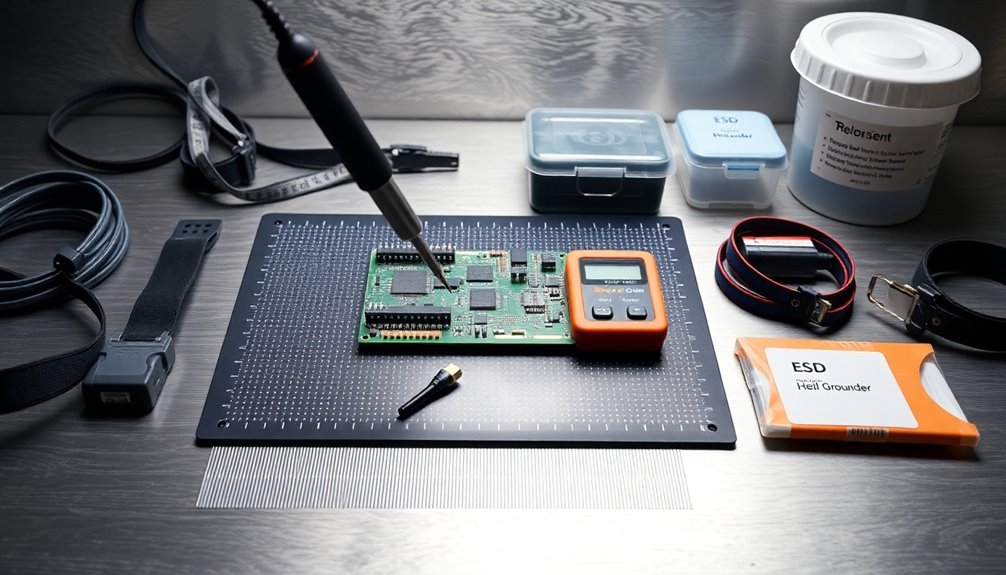
A facility's static survey protocols form the foundation of effective ESD control programs by establishing systematic procedures for evaluating and monitoring static electricity risks. You'll need to regularly assess your facility's static control measures through thorough surveys that examine all critical areas where static-sensitive components are handled.
To implement effective static surveys, you'll want to focus on measuring key parameters and documenting your findings systematically. Your surveys should cover grounding systems, ionization effectiveness, and material conductivity while identifying potential static generation sources.
Survey Component | Measurement Required | Action Steps |
---|---|---|
Ground Points | Resistance to Earth | Test & log readings monthly |
Ionizers | Ion balance & decay time | Calibrate quarterly |
Flooring/Surfaces | Surface resistivity | Verify compliance annually |
Personnel Equipment | Wrist strap continuity | Test daily before use |
Environmental | Humidity & temperature | Monitor continuously |
Don't forget to maintain detailed records of your survey findings and implement corrective actions when measurements fall outside acceptable ranges. Your protocols should also include regular review periods to guarantee they're keeping pace with any facility changes or new equipment installations.
Compliance Verification Procedures
Effective compliance verification procedures build upon static survey protocols by establishing systematic methods to confirm your ESD control program's ongoing effectiveness. You'll need to implement regular audits, typically monthly, using sampling techniques and statistical analysis to track performance consistently.
Your compliance verification plan must specify the technical requirements, measurement limits, and verification frequencies for each ESD control item. You'll want to create a detailed EPA equipment checklist that includes working surfaces, personnel grounding devices, and ionizers.
Make sure you're using test equipment that's capable of making all required measurements, such as electrostatic field meters and high-range resistance meters.
You must document your test methods and maintain detailed records that demonstrate conformity with technical requirements. When you're conducting process monitoring, verify that any alternative test methods you use correlate with referenced standards like ANSI/ESD S20.20 and IEC 61340-5-1.
It's crucial to perform checks before installation, during initial setup, and periodically afterward according to your verification schedule. Remember to maintain continuous monitoring and keep thorough records as evidence of your program's compliance and effectiveness.
Protective Materials Specifications
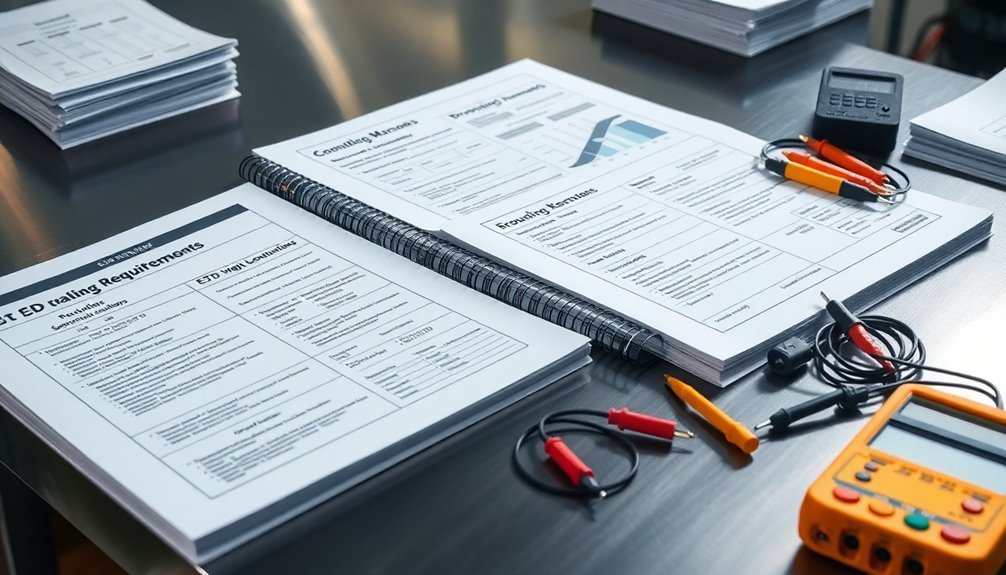
Precise material selection lies at the heart of any ESD protection strategy. You'll need to document specifications for four primary categories of protective materials: electrostatic shielding, conductive, antistatic, and static dissipative materials.
For electrostatic shielding materials, you must verify and document surface resistivity below 1 x 10^4 ohms per square and volume resistivity under 1 x 10^3 ohm-centimeter per millimeter. These materials should maintain their properties at 12 ±3% relative humidity and 73 ±3° Fahrenheit.
When specifying conductive materials, guarantee they meet surface resistivity requirements of less than 1 x 10^5 ohms per square for surface conductive types, and volume resistivity below 1 x 10^4 ohm-centimeter for volume conductive materials.
Your antistatic materials documentation should confirm surface resistivity between 1 x 10^5 and 1 x 10^12 ohms per square, with volume resistivity between 1 x 10^4 and 1 x 10^11 ohm-centimeter.
For static dissipative materials, document surface resistivity ranges from 1 x 10^5 to 1 x 10^12 ohms per square, and verify compliance with standards like ESD ADV 1.0, MIL-263B, and EIA-625.
Audit Schedule Planning
Building upon the foundation of material specifications, your organization's static protection strategy requires systematic audit planning to verify ongoing compliance.
You'll need to establish a thorough audit strategy that considers your company's size, operational complexity, and existing control measures. Your audit plan should detail specific risk assessment procedures and testing protocols while maintaining alignment with ANSI/ESD S20.20 standards.
To maintain effective static control, you'll want to implement regular audit schedules that allow for timely adjustments and continuous improvement. Your documentation should include detailed plans for evaluating grounding systems, protective materials, and process flows that could generate static electricity.
- Schedule periodic audits based on your facility's risk level, with increased frequency in areas handling sensitive components.
- Document specific testing procedures for each audit type, including grounding measurements, material evaluations, and personnel compliance checks.
- Maintain flexibility in your audit schedule to accommodate operational changes, new materials introduction, or updated safety standards.
You'll need to regularly review and update your audit documentation to reflect changes in your operations and maintain continuous effectiveness of your static protection program.
Risk Assessment Documentation
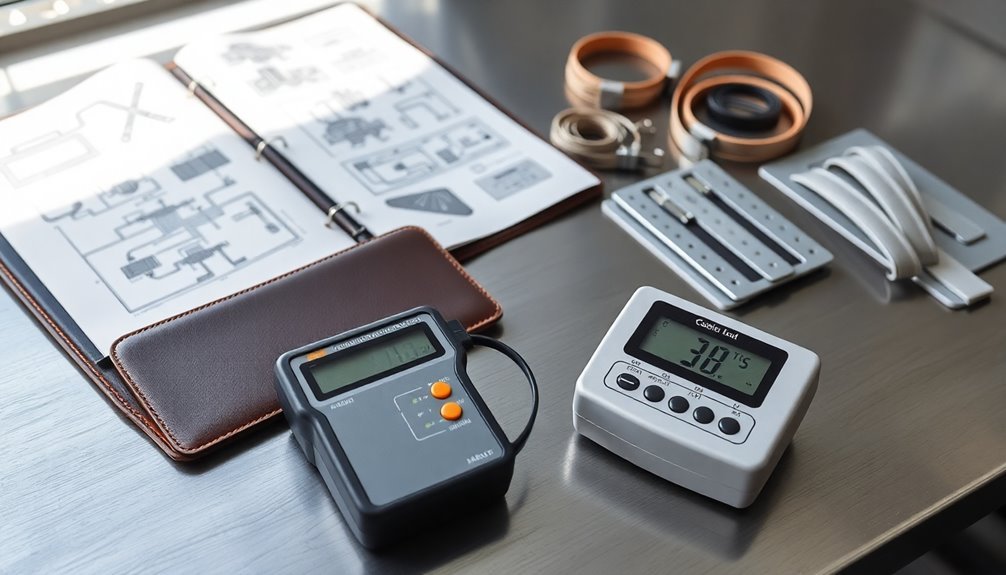
A thorough risk assessment documentation forms the backbone of your static protection program. You'll need to maintain detailed records that demonstrate your systematic evaluation of static electricity risks throughout your facility, including material handling processes and environmental conditions that could contribute to static buildup.
Your documentation must include extensive findings from facility assessments, focusing on equipment grounding, bonding integrity, and work practice evaluations. You should categorize identified risks using severity levels (A through D) and document specific measurements of potential electrostatic discharge energy in areas with flammable atmospheres.
You're required to document the properties of materials used in your processes, particularly their static accumulation characteristics and combustibility factors. Make sure you've included detailed records of expert consultations, diagnostic tool readings, and implemented safety measures.
Don't forget to incorporate training records showing how you've educated your staff about electrostatic hazards and safe practices.
You must establish a regular review schedule for your documentation to reflect any changes in processes, equipment, or safety protocols. Keep your records current with findings from continuous monitoring activities and effectiveness assessments of your control measures.
Control Measures Implementation Plan
Once you've completed your risk assessment, implementing effective control measures becomes your next critical step. Your implementation plan should clearly outline control objectives, principles, and key elements needed to protect against electrostatic discharge (ESD).
You'll need to focus on establishing proper grounding procedures, identifying sensitive areas, and using appropriate ESD control materials within your designated electrostatic protected areas (EPAs).
To guarantee successful implementation, you must document these essential components:
- Detailed activities and timelines for ESD control implementation, including specific roles and responsibilities for your team members
- Cost estimations and budget allocations for necessary materials, training programs, and monitoring equipment
- Regular compliance checks and evaluation procedures to maintain effectiveness and meet industry standards
Your implementation plan should address potential challenges and resource constraints while maintaining focus on continuous improvement.
Don't forget to include thorough training programs for all personnel handling ESD-sensitive items. You'll need to regularly monitor and evaluate your control measures' effectiveness through systematic audits and compliance checks.
Remember to document any modifications or improvements to your control measures as your program evolves.
Technical Requirements Matrix
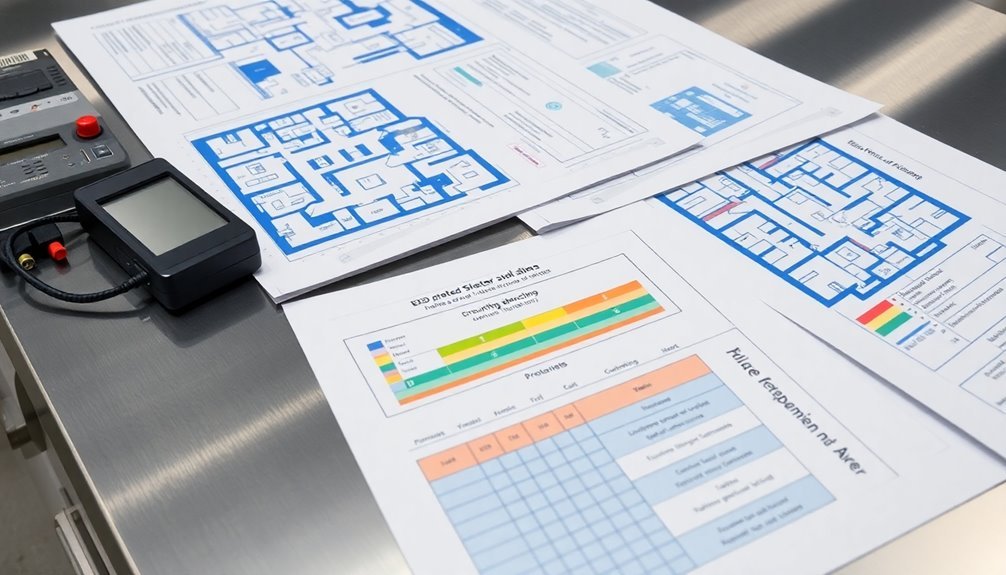
Proper implementation of control measures requires a clear understanding of specific technical requirements.
You'll need to document and maintain precise resistance specifications for your grounding systems, where worksurfaces must maintain point-to-ground resistance below 1.0 x 10^9 ohms, and wrist strap systems must operate between 0.8 x 10^6 and 1.2 x 10^6 ohms.
Your technical requirements matrix should specify that all personnel must be properly grounded through wrist straps when seated and heel straps when standing.
For packaging requirements, you'll need to document that conductive materials must have resistance below 1.0 x 10^4 ohms, while dissipative packaging should range from 1.0 x 10^4 to 1.0 x 10^11 ohms.
Include specifications for your Electrostatic Protected Areas (EPAs), ensuring they're clearly marked and equipped with appropriate grounding systems.
Document that your footwear/flooring system must maintain system resistance below 1.0 x 10^9 ohms with peak voltage under 100 volts.
You'll also need to specify that all mobile equipment and storage shelving must maintain point-to-point and point-to-ground resistance below 1.0 x 10^9 ohms.
Frequently Asked Questions
How Often Should ESD Wrist Straps and Footwear Be Replaced?
You'll need to replace your ESD wrist straps based on wear and testing results, typically every 3-12 months. For footwear, replace them every three months or after 200 hours of use for maximum protection.
What Temperature and Humidity Levels Are Optimal for Esd-Protected Environments?
You'll want to maintain temperatures around 70°F and relative humidity between 40-60%. This range offers ideal ESD protection while avoiding issues like corrosion. Don't let humidity drop below 30% or exceed 60%.
Can Mobile Phones Be Allowed Inside EPA Zones?
You should avoid bringing mobile phones into EPA zones as they can pose ESD risks. If necessary, make certain your phone is properly grounded or contained within an ESD-safe case before entering the area.
How Should Esd-Sensitive Components Be Stored During Facility Power Outages?
You'll need to store ESD-sensitive components in antistatic containers, maintain proper humidity levels, limit access to trained personnel, and guarantee everyone follows proper grounding protocols even during power outages.
What Cleaning Products Are Safe to Use in Esd-Protected Areas?
You'll need to use ESD-specific cleaners like UniClean, DisplayClean, or StaticWorx products. They're specially formulated to maintain surface resistivity and won't leave harmful residues in your ESD-protected areas.
In Summary
You'll need to maintain thorough records of your ESD control program to guarantee compliance and effectiveness. Keep your documentation updated for training logs, static surveys, grounding tests, and risk assessments. Don't forget to regularly review your control measures and audit schedules. Your technical requirements matrix will help you track all elements of your static protection planning, guaranteeing nothing falls through the cracks.
Leave a Reply