You'll need several essential pieces of test equipment for an effective static control program. Start with a digital surface resistance meter to measure static dissipative materials and surfaces. Include wrist strap and footwear testers to verify personnel grounding systems daily. Add a static field meter to detect electrostatic charges on objects and surfaces, plus a charged plate monitor to test ionizer performance. Don't forget ground continuity measurement tools and environmental monitors for tracking humidity and temperature. Following ESD standards and maintaining proper documentation will open up a world of insights about your static control program's effectiveness.
Surface Resistance Testing Equipment
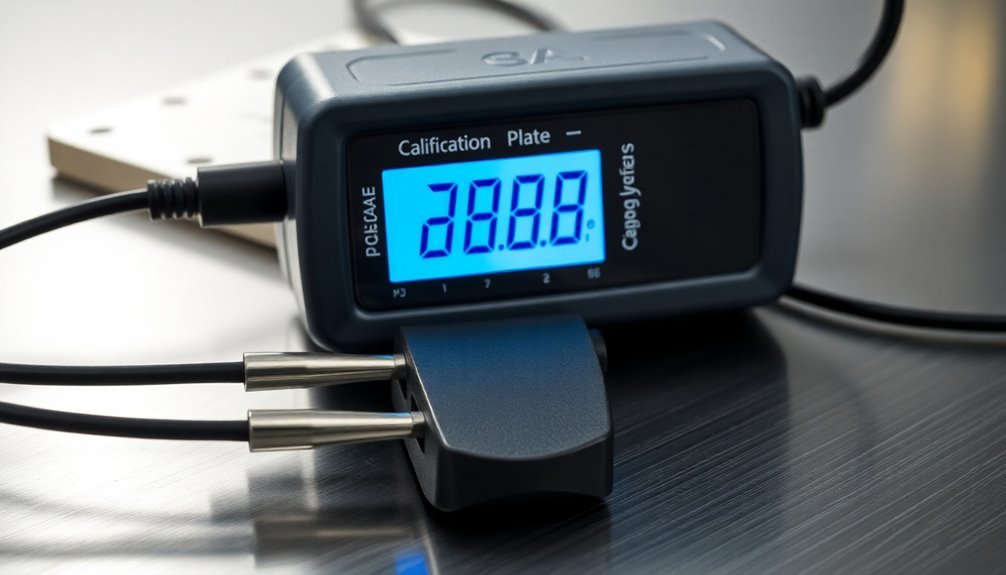
A reliable surface resistance meter serves as the cornerstone of any effective static control program. You'll need this essential tool to measure electrical resistance between points and from surfaces to ground, ensuring your ESD control surfaces meet industry requirements outlined in ANSI/ESD S20.20 standards.
When selecting your surface resistance testing equipment, you'll find both analog and digital options available. Digital kits offer precise readings with features like automatic zeroing, while analog versions automatically switch between 10V and 100V test voltages. Remember that periodic test frequency depends on the risk level between testing intervals.
Both types should include shielded test leads and 5-pound electrodes for accurate measurements.
To conduct proper testing, you'll need to follow specific procedures. For resistance-to-ground (RTG) measurements, connect one lead to ground and place the electrode on your test surface. For point-to-point (RTT) testing, position two electrodes 10 inches apart.
You don't need to clean surfaces unless absolutely necessary, and you should remove all ESD-sensitive items before testing.
Your testing equipment should measure within 1 x 10E3 to 1 x 10E13 ohms and be portable enough for field testing. Plan to test worksurfaces and carts quarterly to maintain compliance with industry standards.
Personnel Grounding Verification Tools
Throughout your static control program, personnel grounding verification tools serve as critical instruments for testing wrist straps and footwear systems. You'll need to verify these grounding devices daily before handling any ESD-sensitive components to guarantee proper static control and prevent costly damage.
You'll find several types of testers available to meet your specific needs. Wrist strap testers check the entire system, including the band, cord, and skin contact, while combination testers can verify both wrist straps and footwear. Regular testing is essential since grounding devices can fail after thousands of flex cycles.
For different workplace setups, you can choose between portable units or wall-mounted options, and some models even include data logging capabilities for automatic record keeping.
When you're implementing these tools, you'll need to follow specific standards like ANSI/ESD S20.20 and IEC 61340-5-1. These guidelines define the pass/fail criteria and testing frequency requirements.
You must maintain detailed records of all tests for compliance purposes, and your personnel should receive proper training on correct testing procedures.
Some advanced systems offer continuous monitoring features, providing real-time verification of your grounding equipment's functionality throughout the workday.
Static Field Detection Meters
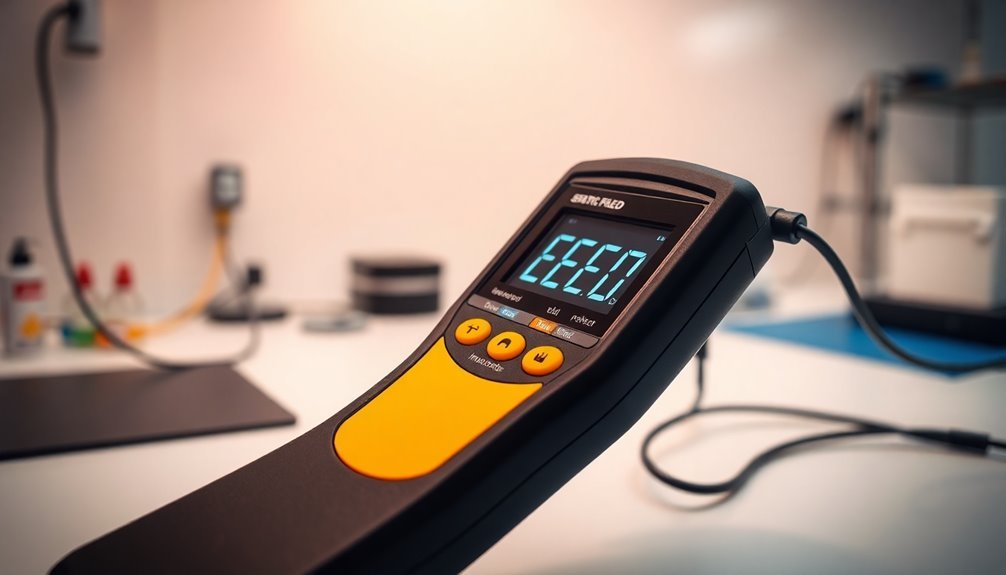
Static field detection meters serve as essential diagnostic tools for measuring electrostatic charges in your ESD-protected workspace. These handheld devices provide non-contact measurement capabilities, displaying readings in volts, volts per meter (V/m), or kilovolts per meter (kV/m), with remarkable accuracy regardless of probe-to-surface distance variations.
You'll find these meters equipped with digital displays and critical features like chopper-stabilized circuitry, which guarantees accurate readings even in ionized environments. The built-in hold function lets you retain measurements, while polarity indication helps identify the charge type you're dealing with. The field influence principle allows these meters to measure charges without withdrawing energy from the electric field.
Each meter comes with traceable calibration certificates for reliability.
When you're conducting static surveys or compliance verification audits, these meters help you identify and eliminate static-generating items that could harm your sensitive electronic components. They're particularly valuable in electronics manufacturing, where you need to maintain strict ESD control standards.
You'll need to establish your own testing frequencies based on your ESD-sensitive items' critical nature and the risk levels involved. Remember to keep your meters properly calibrated according to vendor specifications and guarantee that your measurements correlate with laboratory standards to maintain compliance with ANSI/ESD S20.20 and IEC 61340-5-1 requirements.
Ionization Performance Testing Devices
Professional testing of ionization equipment requires specialized devices like Charged Plate Monitors (CPMs) to measure critical performance parameters. You'll need to use CPMs to evaluate two key metrics: discharge time and offset voltage.
The CPM's isolated conductive plate measures 15 cm by 15 cm with a capacitance of 20 ± 2 picofarads, guaranteeing standardized measurements across different testing scenarios. Most testing is performed with the CPM plate charged to 1000V and timed until discharge reaches 10% of the initial voltage.
When you're testing ionization equipment, you'll need to follow ANSI/ESD STM3.1 standards for consistent results. You should perform tests at repeatable locations and distances that match your specific application requirements.
For non-standard equipment like air-assist bar ionizers or soft x-ray ionizers, you'll need to use newly developed test methods designed for these specialized devices.
You can't just test once and forget about it – regular monitoring is essential. You'll need to conduct periodic verification tests following ESD TR53 guidelines and ANSI/ESD SP3.3 test methods to guarantee your ionizers maintain their effectiveness.
This ongoing testing helps you identify maintenance needs early and confirms that your ionization equipment continues to meet your static control requirements.
Ground Continuity Measurement Systems
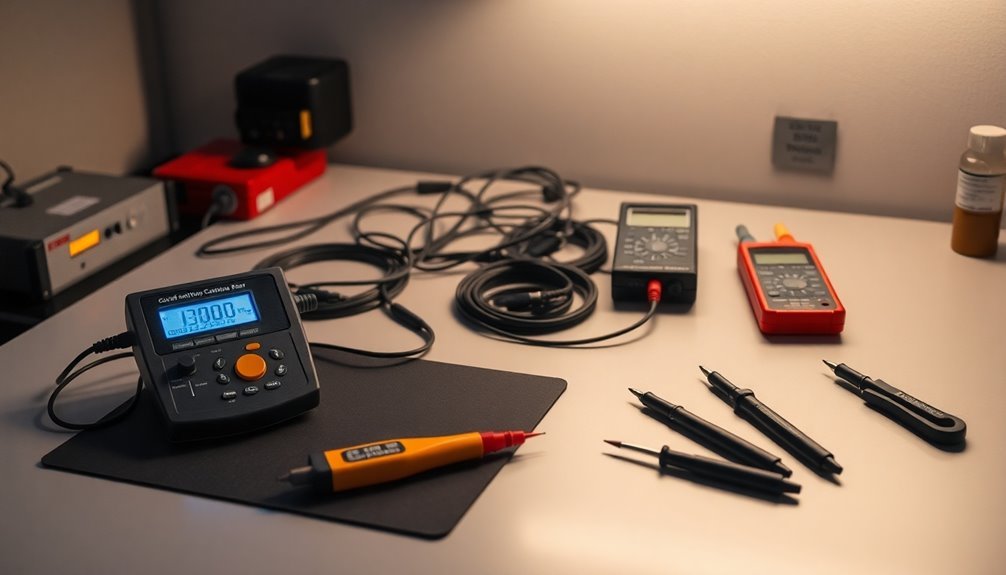
Measuring ground continuity requires specialized equipment and precise testing methods to guarantee electrical safety in your facility. You'll need reliable ground continuity testers (GCTs) and ground bond testers (GBTs) to verify that your equipment's metal components maintain proper connections with ground wires.
When you're testing ground continuity, you'll want to use devices that can generate low-current DC signals to measure resistance between connections. Your measurements should show resistance under 1 ohm for satisfactory results. The most efficient testers can complete measurements in three seconds while maintaining accuracy.
For more accurate testing, you'll need Kelvin cables, particularly when conducting ground bond tests.
In challenging environments like wet manufacturing areas, you'll need specialized equipment such as the Safearth CS3, which can effectively measure DC resistance even with electrical noise present.
You must also comply with OSHA regulations, which require daily inspection of ground conductors and cordsets before use and after any maintenance work. If you're working on construction sites, you can either implement GFCIs or use automatic cord-mounted ground continuity monitors to eliminate daily testing requirements.
Remember to document all test results to maintain compliance with safety standards.
Environmental Monitoring Instruments
In your static control program, environmental monitoring instruments serve as the eyes and ears of your facility's ESD protection system. These specialized tools help you maintain thorough oversight of static-related risks and environmental conditions that could impact your operations.
You'll need static field meters to detect and measure electrostatic charges throughout your facility. Modern ionizer systems like the SJ-H series can eliminate static in 0.5 seconds while monitoring charge levels. These devices let you identify static sources and verify the effectiveness of your control measures.
Surface resistance testers are essential for confirming that your ESD-safe surfaces meet required standards and maintaining compliance with ANSI/ESD specifications.
Install electrostatic sensors for continuous monitoring of static levels in critical areas. They'll automatically trigger alarms when static exceeds safe thresholds and integrate with your control systems for automated responses.
Don't overlook the importance of humidity and temperature monitors – they're vital for understanding how environmental conditions affect static generation in your facility.
Frequently Asked Questions
How Often Should Test Equipment Be Calibrated to Maintain Accuracy?
You'll need to calibrate your test equipment annually at minimum, but adjust intervals based on usage frequency, manufacturer recommendations, and regulatory requirements. Consider more frequent calibration for critical measurements or unstable instruments.
What Temperature and Humidity Levels Affect Static Control Measurements?
You'll notice significant static control issues when temperatures fluctuate and humidity drops below 40%. Keep your environment between 40-60% relative humidity and maintain stable temperatures to guarantee accurate measurements.
Can Test Equipment From Different Manufacturers Be Used Together?
You can mix test equipment from different manufacturers, but you'll need to verify compatibility and integration first. Check for standards compliance and consider potential performance variations that could affect your measurements' accuracy.
What Backup Procedures Exist When Test Equipment Malfunctions?
When your test equipment malfunctions, you'll need to implement full backup testing, maintain redundant systems, and follow established protocols. You should also have automated monitoring and alert systems in place for quick responses.
How Long Should Test Results Be Retained for Compliance Documentation?
You'll need to retain most test results for 2 years, but some specialties like immunohematology and pathology require 10-year retention. Keep cytology and histopathology slides with malignancy findings for 10 years.
In Summary
You'll find these essential test instruments critical for maintaining an effective static control program. By regularly using surface resistance testers, personnel grounding verifiers, static field meters, ionization testers, ground continuity meters, and environmental monitors, you're ensuring your ESD protection measures work as intended. Don't skip these crucial tools – they're your best defense against costly static-related damage and failures.
Leave a Reply