You'll find seven critical ESD runner materials essential for static control: vinyl, rubber, nitrile, EPDM compound, multi-layer laminates, PVC, and conductive composites. Each material offers unique benefits – vinyl provides durability against chair casters, rubber excels in heat resistance, nitrile works well in cleanrooms, EPDM withstands extreme conditions, laminates offer layered protection, PVC guarantees versatile applications, and composites deliver specialized conductivity ranges. These materials comply with ANSI/ESD S20.20 standards and require specific maintenance protocols. Understanding the distinct properties of each material will enhance your ability to make an informed choice for your facility's needs.
Vinyl ESD Runners
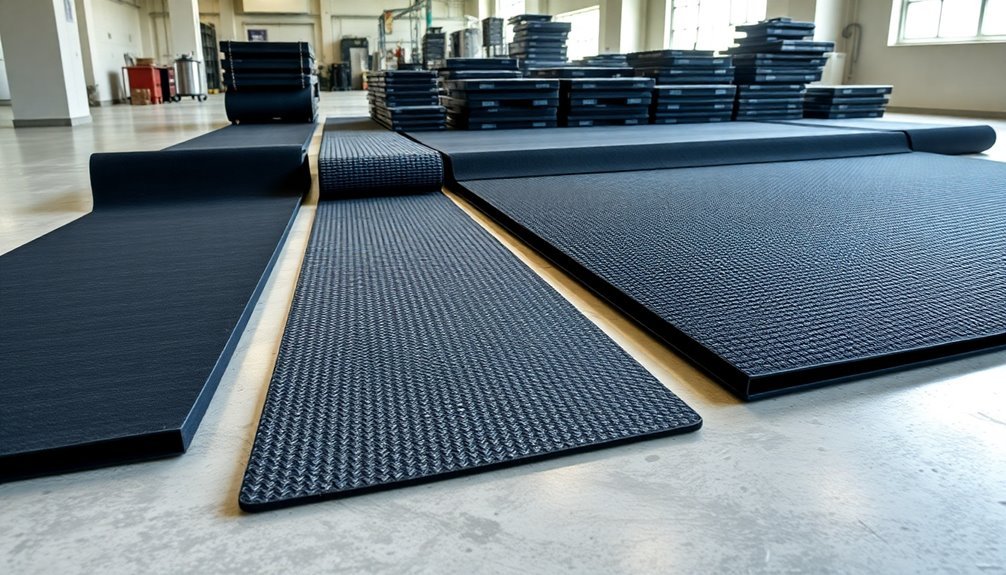
You won't need to worry about durability – these runners resist damage from chair casters while maintaining their ESD properties.
Made from PVC, these runners offer exceptional strength and resilience for long-term use.
They're also chemically resistant to various substances, including acids, detergents, and mineral oils.
Meeting ANSI/ESD S20.20 standards ensures consistent performance in static-sensitive environments.
When it comes to maintenance, you can easily clean them with neutral cleaners.
For grounding options, you can choose factory-installed snaps and low-profile cords, ensuring proper static dissipation.
Whether you're protecting carpets or creating static-safe work areas, these runners provide reliable ESD protection while withstanding heavy foot traffic.
Rubber Material Properties
You'll find that rubber ESD runners excel in both heat and chemical resistance, making them ideal for industrial environments where exposure to harsh substances is common.
The less than 20 volts generated with ESD footwear demonstrates rubber's superior static control capabilities in industrial settings.
The multi-layer construction options, including single, double, and triple-layer variants, let you choose the perfect balance of durability and static dissipation for your specific needs.
Your team will appreciate the anti-fatigue benefits that come from rubber's natural cushioning properties, especially during long shifts of standing work.
These mats require regular inspection to maintain their effectiveness and ensure continued protection of sensitive electronic components.
Heat and Chemical Durability
The heat and chemical durability of ESD runner materials is essential for maintaining consistent performance in demanding industrial environments.
You'll find that quality ESD runners are made from rigid solid vinyl with a buried conductive layer, which provides exceptional resistance to various chemicals and heat exposure. The pebble pattern surface adds extra grip and stability to the material. These materials are manufactured in the USA to ensure consistent high quality standards.
These materials effectively withstand both inorganic and organic acids, reducing agents, and common industrial substances like detergents, alcohols, and mineral oils. At 0.090 inches thick, the single-layer conductive vinyl maintains its electrical properties while delivering surface resistance of 10^3 – 10^6 ohms/square for reliable static dissipation.
You'll appreciate that these runners comply with important flammability standards, including DOT FMVSS 302 and CPSC FF 1-70. The material's chemical stability guarantees that its electrical properties remain intact even after exposure to harsh substances.
When you're cleaning your ESD runners, use neutral cleaners to preserve the material's structural integrity and prevent insulative electrical readings. You can also cut and repair the material as needed, and if you require additional safety features, you can request grounding snaps to be added to your runners.
Multi-Layer Construction Options
Building upon the durability advantages of solid vinyl, multi-layer ESD mats offer enhanced protection through their sophisticated construction design.
You'll find these mats typically feature a conductive layer sandwiched between a dissipative top surface and a foam base layer, creating a thorough defense system against electrostatic discharge. The foam backing provides extra cushioning comfort for operators during extended use periods.
When you're selecting multi-layer ESD runners, you'll discover they're available in both rubber and vinyl compositions. Heat and chemical resistant rubber compositions are particularly favored in industrial settings.
Vinyl options provide easier cutting capabilities and can include cushioned varieties for additional physical protection.
The surface resistivity of vinyl mats ranges from 10^7 to 10^8 Ω, while the conductive layer maintains a minimum point-to-point resistance of 1 × 10^4 Ω for effective CDM protection.
You'll want to take into account three-layer constructions like VinylStat B, which incorporates a conductive metalized fleece for superior performance.
These multi-layer mats comply with ANSI/ESD S20.20 and ANSI/ESD STM4.1 standards, ensuring reliable protection for your sensitive equipment.
They're compatible with constant monitoring systems and require proper grounding to earth for ideal ESD protection, making them perfect for workstations and production areas where static control is essential.
Anti-Fatigue Performance Benefits
Standing up to the demands of industrial environments, rubber anti-fatigue mats deliver exceptional performance through their unique material properties.
You'll find that rubber's natural elasticity and shock-absorption capabilities create an ideal foundation for reducing worker fatigue in extended standing situations. The closed-cell foam structure provides superior density and support, while the material's inherent malleability allows for customized comfort levels.
The key anti-fatigue benefits you'll experience include:
- Enhanced thermal insulation against cold floors
- Superior shock absorption for joint protection
- Consistent support through dense foam construction
- Extended durability in high-traffic areas
- Reliable slip resistance for workplace safety
You'll notice immediate improvements in workplace comfort and productivity when you implement these mats.
The ergonomic design actively works to reduce muscle strain and improve circulation, while the chemical-resistant properties guarantee longevity in industrial settings.
Whether you're outfitting an assembly line or a commercial kitchen, the versatile nature of rubber anti-fatigue mats means they'll adapt to your specific needs while maintaining their performance characteristics.
You can count on these mats to deliver consistent support and protection throughout their extended service life.
Nitrile Runner Construction
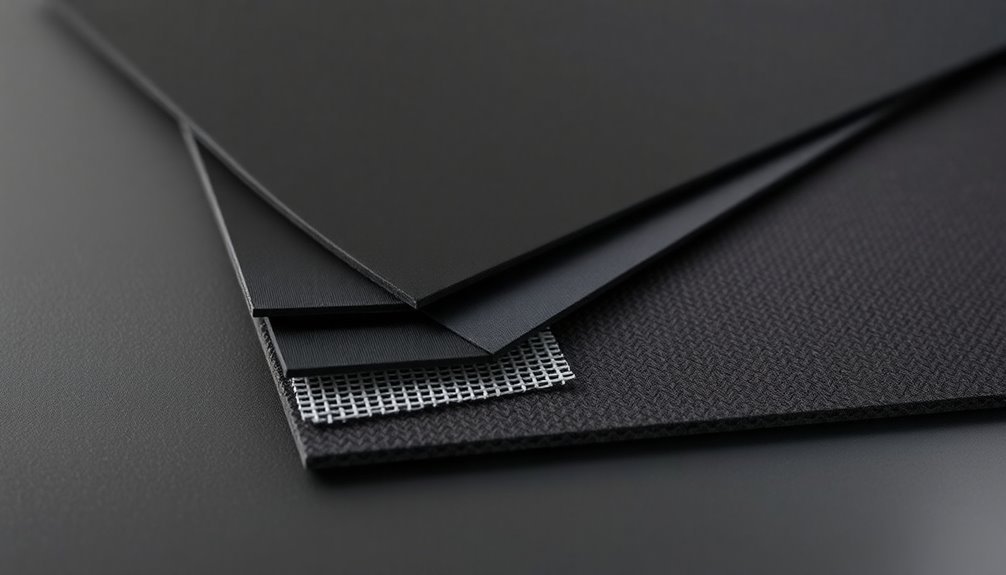
Many industrial settings rely on nitrile rubber compounds for constructing ESD runners due to their superior durability and static dissipative properties. You'll find these runners are more resilient than standard vinyl sponge matting, offering enhanced protection against static electricity while maintaining excellent chemical resistance.
Feature | Benefit | Application |
---|---|---|
Static Dissipative | Protects sensitive equipment | Electronics manufacturing |
Chemical Resistant | Withstands industrial spills | Production facilities |
Flame Retardant | Enhances workplace safety | Areas with sparking equipment |
Ergonomic Design | Reduces worker fatigue | Standing workstations |
Durable Construction | Guarantees long-term value | High-traffic areas |
When you're selecting nitrile runners for your facility, you'll want to take into account their versatile applications in cleanrooms, electronics assembly, and general industrial environments. They're particularly effective when properly grounded, and you can maintain them easily with regular cleaning using mild soap or ESD-safe solutions. You'll appreciate that these runners come in various sizes and configurations, with custom options available for specific requirements. Their compatibility with different environments makes them an ideal choice for areas where you need both static control and protection against chemical exposure.
EPDM Compound Benefits
EPDM compounds offer exceptional long-term resistance to extreme temperatures, UV radiation, and chemical exposure, making them ideal for your static-control flooring needs.
You'll find that EPDM runners consistently meet the electronics industry's strict ESD standards while maintaining their protective properties throughout their 50-year lifespan.
Your facility's static-sensitive components receive reliable protection thanks to EPDM's stable electrical insulation properties, which remain consistent even under heavy foot traffic and varying environmental conditions.
Long-Term Resistance Performance
What sets EPDM compounds apart in ESD applications is their exceptional long-term resistance performance. You'll find that these compounds maintain stable conductivity over time while resisting environmental degradation, making them ideal for demanding ESD applications.
When properly formulated with graphene nanotubes, EPDM compounds deliver consistent electrical performance across a wide temperature range from -40°C to 150°C. You won't have to worry about carbon release or surface contamination, as these compounds minimize these issues compared to traditional carbon black alternatives.
Key advantages of EPDM's long-term resistance include:
- Stable conductivity range of 1×10^4 to 1×10^6 ohms
- Superior chemical resistance against acids and oils
- Minimal carbon release, maintaining clean surfaces
- Enhanced tear strength and tensile performance
- Consistent properties in extreme temperatures
You'll appreciate that EPDM compounds retain their electrical and mechanical properties even when exposed to harsh chemicals and environmental factors.
Their ability to maintain performance while resisting degradation makes them a reliable choice for ESD runners and floor mats in manufacturing and electronics environments, where consistent static dissipation is essential.
Electronics Industry Standards
Three core attributes make EPDM compounds the preferred choice for meeting electronics industry standards.
First, EPDM's electrical insulation properties provide reliable ESD protection, which you'll find vital for sensitive electronic components. The material excels in cable jacket manufacturing and creates effective seals that keep moisture away from critical electrical parts while dampening unwanted vibrations.
The second attribute you'll appreciate is EPDM's exceptional chemical resistance profile. You can count on its ability to withstand ozone exposure, UV radiation, and various chemical agents without degrading. This resistance guarantees your electronic components remain protected in challenging environments where exposure to harsh elements is common.
Temperature stability rounds out EPDM's core strengths in electronics applications. You'll find it maintains consistent performance across an impressive temperature range from -65°F to +300°F.
This thermal stability is essential when you're dealing with electronic components that generate heat or operate in extreme conditions. EPDM's versatility allows manufacturers to customize formulations for specific applications, whether you need gaskets, seals, or protective elements.
These properties guarantee your electronic components meet industry standards for reliability and longevity.
Laminate Runner Systems
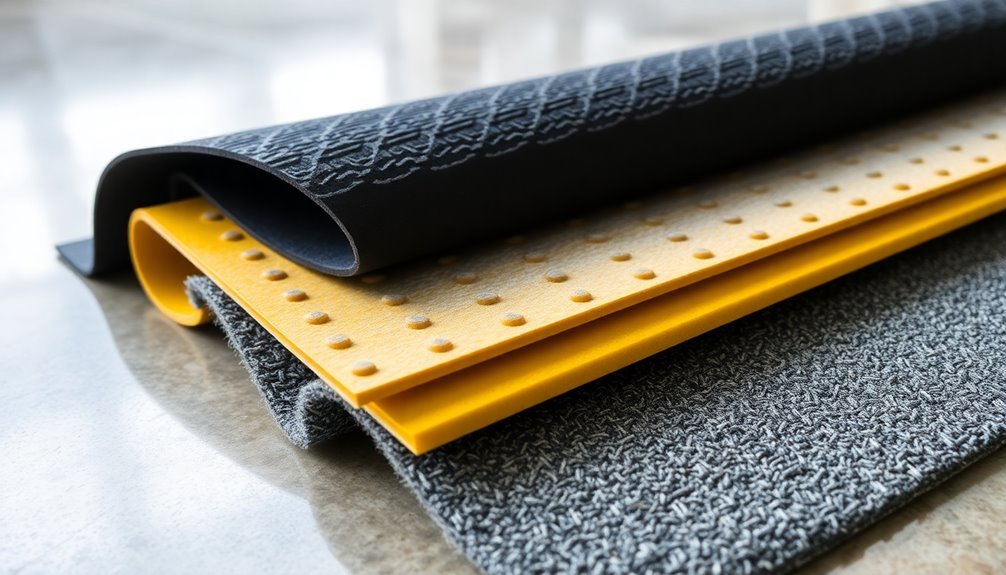
Laminate runner systems offer extensive ESD protection through high-pressure laminates specifically engineered for workstations handling static-sensitive electronics.
You'll find these systems particularly valuable in electronics assembly, cleanrooms, and medical facilities where static control is essential. With a surface resistance of less than 1 x 10^9 ohms Rtg, they meet ANSI/ESD S20.20 worksurface requirements.
You can count on these runners' impressive protective features, including:
- Chemical resistance against hot solder and most solvents
- Smooth, radiused edges that prevent particle accumulation
- Consistent path-to-ground through conductive layer impregnation
- Durable construction for long-term reliability
- Easy-to-clean beige surface for maintenance efficiency
When you're setting up your workspace, you'll need to guarantee proper grounding for effective ESD protection.
The laminate's design creates a reliable path-to-ground for electrical charges, protecting your sensitive electronic components during manufacturing and assembly processes.
While these runners aren't meant for high-traffic floor areas, they're perfect for workstation surfaces where you need dependable ESD protection.
You'll appreciate their ability to shield work surfaces from dust and damage while maintaining compliance with relevant ESD standards.
PVC Runner Applications
Today's PVC runner applications offer versatile ESD protection across multiple industries, from electronics assembly to fiber optics manufacturing. You'll find these runners are made from a homogeneous PVC polymer mix that's 1/8" thick and delivers surface resistance between 10^8 to 10^9 ohms/sq.
These runners excel in performance with their V-groove embossed surface that prevents slips while maintaining essential ESD protection. You won't need to worry about chemical exposure, as they're resistant to various substances, including acids and detergents.
Application | Features | Benefits |
---|---|---|
Production Rooms | ESD-safe surfaces | Protects sensitive components |
Hospitals | Chemical resistant | Easy maintenance |
Electronics | ANSI/ESD compliant | Meets industry standards |
Fiber Optics | Non-slip surface | Enhanced workplace safety |
Solar Industry | Grounding options | Reliable static discharge |
When you're setting up your ESD-protected area, you'll appreciate that these runners can be cut to size and fitted with grounding snaps. They're RoHS and REACH compliant, ensuring you're meeting safety regulations while protecting your sensitive equipment. With a minimum tensile strength of 700 lbs./in.² and 150% elongation, you're getting durability that'll last through heavy traffic.
Material Performance Testing Standards
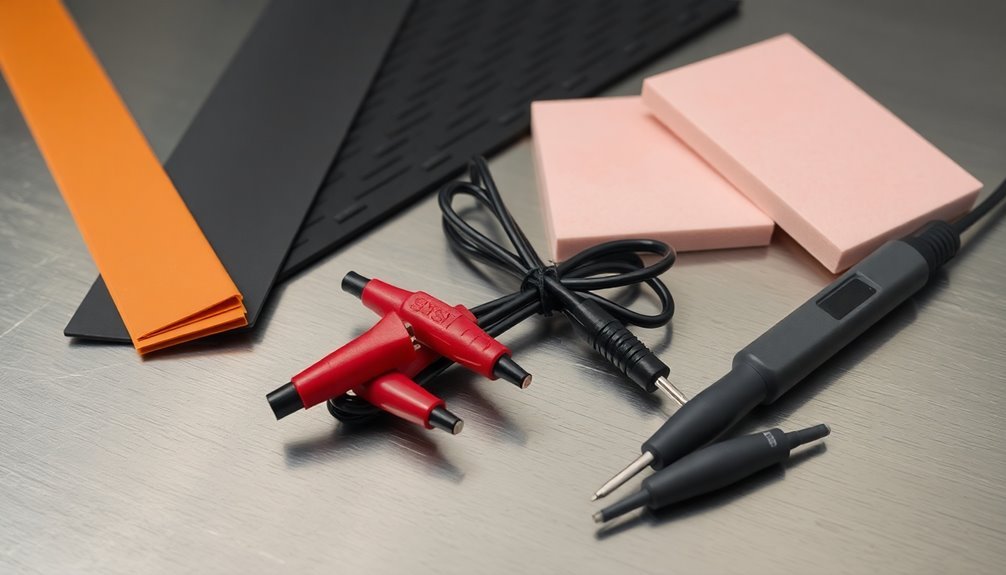
Building on the established quality of PVC runners, material performance testing standards guarantee your ESD flooring meets strict industry requirements.
You'll need to verify your flooring materials comply with key standards like ANSI/ESD S20.20 and ASTM F150, which define essential performance criteria for static control programs.
When testing your ESD runner materials, you must follow these critical requirements:
- Point-to-point resistance must measure less than 1.0 x 10^9 ohms
- Body voltage generation should stay under 100 volts
- Materials need conditioning at 12% humidity for 72 hours before testing
- Testing requires proper equipment like AEMC Megohmmeter and five-pound probes
- Test leads must maintain minimum three-foot separation
You'll want to establish a regular testing schedule using an independent laboratory for accurate results.
Your compliance verification process should include both initial qualification testing and ongoing maintenance checks.
Don't forget to maintain detailed records of all testing results, including technical reports and maintenance logs.
When cleaning your ESD runners, only use approved products to maintain proper resistance levels and verify continued effectiveness of your static control system.
Frequently Asked Questions
Can ESD Runners Be Installed Over Carpet or Uneven Surfaces?
You can install ESD runners over carpet and uneven surfaces, but you'll need proper preparation. Use double-sided tape or leveling compounds for uneven areas, and make sure the surface is clean and stable first.
How Often Should ESD Runners Be Tested for Electrical Performance?
You should test your ESD runners monthly in high-traffic areas and quarterly in low-traffic zones. You'll need to conduct immediate testing after installation and whenever you notice wear or environmental changes.
What Happens if an ESD Runner Gets Damaged or Torn?
If your ESD runner gets damaged or torn, you'll need to replace it immediately. The damage can compromise its static dissipative properties, putting your electronic equipment at risk of ESD-related failures.
Do Temperature Changes Affect the Static Dissipative Properties of ESD Runners?
Yes, temperature changes can affect your ESD runner's static dissipative properties. You'll notice reduced effectiveness at extreme temperatures, as heat and cold can alter the material's resistivity and its additives' performance.
Are There Color Options Available That Don't Compromise ESD Protection?
Yes, you'll find ESD runners in various colors that maintain full static protection. Common options include blue, grey, and black, while specialty colors are available. All colors meet the same ESD protection standards.
In Summary
You'll want to carefully evaluate these seven ESD runner materials based on your specific facility needs and budget constraints. Consider factors like durability, static dissipation rates, and chemical resistance when making your selection. Don't forget to verify that your chosen material meets industry testing standards and certification requirements. Regular maintenance and proper installation will guarantee your ESD runners provide reliable protection for years to come.
Leave a Reply