You'll need these 10 essential tips for a static-safe soldering setup: Use an ESD-safe rubber mat with proper grounding, wear a wrist strap with a 1 megohm resistor, maintain humidity between 40-60%, choose an ESD-safe soldering iron with grounded tip, keep your workspace clutter-free, store components in anti-static bags, handle boards by their edges, position fume extraction properly, set iron temperature between 315-370°C, and regularly test all grounding connections. Each of these protective measures plays a vital role in safeguarding your sensitive electronic components from costly ESD damage.
Selecting Your ESD-Safe Work Surface
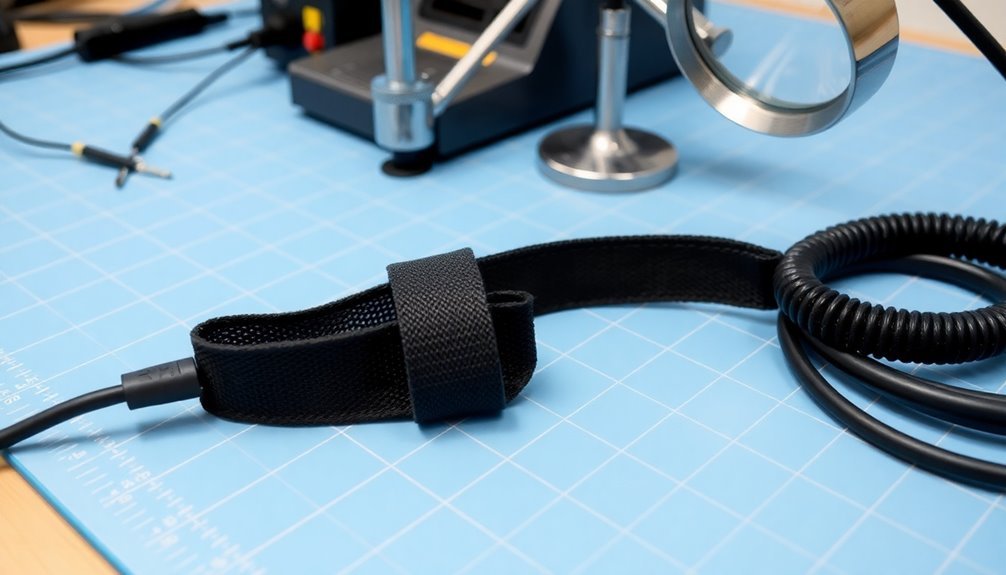
Properly selecting an ESD-safe work surface is essential for protecting sensitive electronic components during soldering.
When choosing your mat, you'll need to think about both the material and construction type. Rubber mats, particularly those made from Hydrin, offer superior heat and chemical resistance while providing inherent ion-conductive properties without requiring additives. These features make them ideal for soldering applications. A lower initial cost compared to permanent ESD solutions makes matting an attractive choice for many workstations.
You'll want to focus on multi-layer mats that combine a dissipative top layer with a conductive bottom layer. This construction helps prevent CDM ESD damage and guarantees consistent resistance across the entire surface.
Look for mats that meet the minimum point-to-point resistance requirement of 1 × 10^4 Ω and maintain their properties over time without needing re-treatment.
Don't forget to verify certifications. Your mat should comply with IEC 61340-5-1 standards and have appropriate certifications like RoHS. If you're working in a cleanroom environment, check for outgassing compliance.
Choose high-quality mats that won't require frequent replacement – they'll save you money in the long run while providing reliable static protection for your soldering work.
Ground Connections Matter
Establishing proper ground connections forms the backbone of any static-safe soldering setup. You'll need to guarantee all your equipment meets the IEC-61340-1-5 International Standard, with ground resistance not exceeding 2.0 ohms and potential differences staying below 2 millivolts RMS.
Start by connecting an ESD wrist strap to a reliable ground point – but don't use water pipes in multi-household buildings unless you're certain about the plumbing's integrity. The wrist strap should include a 1 megohm resistor for safety compliance.
Your soldering iron should have a three-wire grounded power cord, and if you're using a non-grounded or battery-powered iron, attach a grounding wire to its cooler metal parts.
Set up your workstation with an ESD mat connected to ground through appropriate grounding cords. If you're working in a mobile setting, consider using heel grounders as an alternative grounding method.
All your soldering equipment, including tips and accessories, should maintain proper grounding connections.
Don't forget to inspect and maintain your ground connections regularly. Clean your ESD mats, check your wrist straps, and document all maintenance activities.
Replace any worn-out equipment immediately to maintain the integrity of your static-safe environment.
Essential ESD Protection Equipment
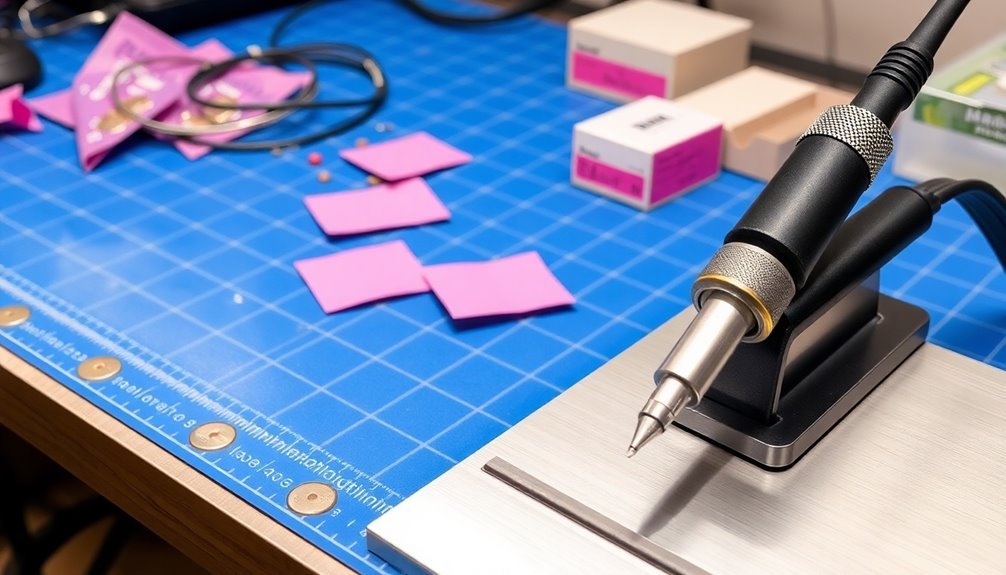
A successful ESD-protected workspace relies on several key pieces of equipment. You'll need an ESD mat as your primary work surface, connected to a proper ground point. When you're handling sensitive components, always wear an ESD wrist strap that's securely fastened and properly grounded. Don't forget to use ESD-safe storage containers for your components when they're not in use. Setting up your workspace in a well-ventilated area helps protect you from harmful fumes while soldering.
Your soldering station needs specific protection too. Make sure you're using an ESD-safe soldering iron with a grounded tip, and keep ESD-safe gloves nearby for handling temperature-sensitive parts. In dry environments, you'll want to maintain proper humidity levels using anti-static sprays or humidifiers.
Equipment Type | Purpose | Important Features |
---|---|---|
ESD Mat | Surface Protection | Conductive, Grounded |
Wrist Strap | Personal Grounding | Secure Connection |
Storage Containers | Component Safety | Anti-static Material |
Soldering Iron | Safe Soldering | Grounded Tip |
Hand Tools | Component Handling | Dissipative Handles |
Remember to regularly check your equipment's effectiveness using an ESD assessment kit. Keep your workspace clear of static-generating materials and maintain consistent grounding connections for all your tools.
Workstation Layout Best Practices
Building on your ESD protection knowledge, the right workstation layout can maximize your safety and efficiency. Start by installing an ESD mat on your work surface and connect it to a proper ground point.
Position your wrist strap and foot grounders within easy reach to maintain continuous grounding while you work.
Keep your workspace minimalist and clutter-free to prevent accidental damage. You'll want to store components in anti-static containers and limit unnecessary movement that could generate static electricity. Contact and friction between materials during movement can create unwanted static charges.
Install proper lighting and use a magnifier for detailed work, and don't forget to set up a fume extractor for ventilation.
Maintain humidity levels between 40-60% to reduce static buildup. If you're working in a dry environment, you'll need to use a humidifier or anti-static sprays.
Connect all your equipment to a common ground point to equalize potential.
When handling components, always grip them by their edges and guarantee you're properly grounded before touching any sensitive devices. Use ESD-safe soldering equipment and avoid placing PCBs on static-generating surfaces like wood.
Store and transport your components in anti-static bags to maintain protection throughout your workflow.
Temperature-Controlled Soldering Station Setup
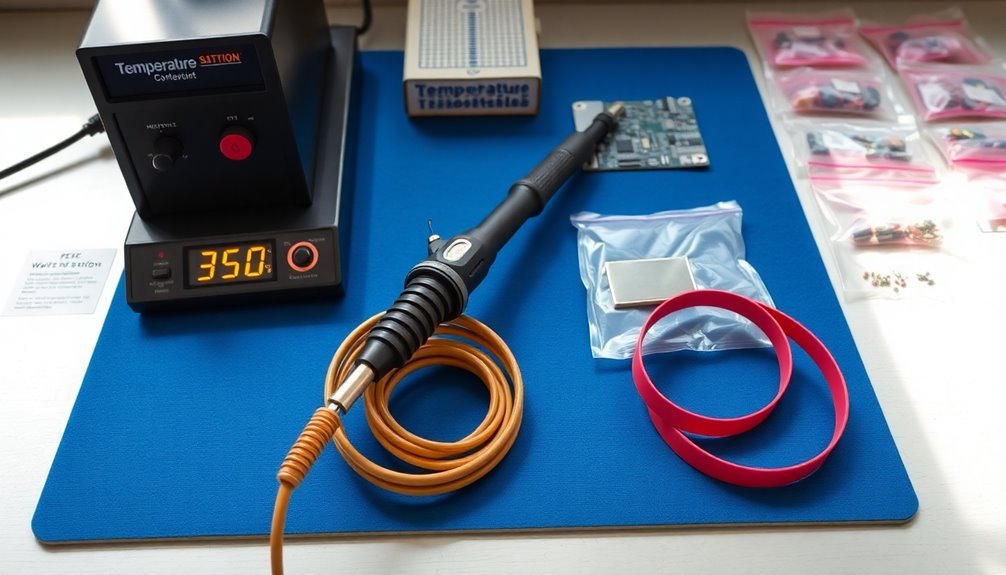
You'll want to position your temperature-controlled soldering station at a comfortable height and angle, keeping the display easily visible and controls readily accessible.
For best results, set your soldering iron temperature between 315°C and 370°C for most general-purpose electronics work, while monitoring the digital display to maintain consistent heat levels.
Keep your station's temperature sensor properly calibrated and maintain a clean tip to achieve reliable heat transfer and precise temperature control during your soldering tasks. Connect the K-Type thermocouple carefully to ensure accurate temperature readings from your soldering iron tip.
Optimal Heat Range Control
The ideal temperature range for soldering requires careful attention to both precision and control when setting up your workstation. You'll want to maintain temperatures between 200°C and 450°C, depending on your specific application.
For delicate electronics, you should stay within the 200-250°C range to prevent component damage.
When you're working with temperature control, make sure you've matched your power output to the task at hand. Use 20-40W for sensitive electronics and 40-80W for heavier applications. Your iron's digital temperature display will help ensure precise adjustments during operation.
You'll need to regularly calibrate your equipment to guarantee consistent readings and peak performance.
To achieve the best results, you'll want to focus on proper heat management techniques. Start by preheating your workpiece to improve solder flow, and keep your tip well-tinned for efficient heat transfer.
Don't forget to adjust your temperature settings in small increments for precise control.
Your soldering station should include a reliable K-type thermocouple sensor and proper heat sink management features. These components work together to maintain temperature stability and prevent damage to sensitive parts.
Remember to regularly check your temperature settings and make adjustments based on your specific soldering needs.
Safe Station Placement Guidelines
Proper placement of your soldering station forms the foundation of a safe and effective workspace. Position your station on a stable, heat-resistant surface with adequate ventilation to protect yourself from harmful fumes. Using a temperature-controlled station will help maintain consistent solder joints and prevent component damage.
You'll need to keep flammable materials away and manage cable placement to prevent tripping hazards.
Implement ESD protection measures by using an ESD mat and wearing a grounded wrist strap while handling components. Don't forget to use ESD-safe tools and store sensitive parts in protective packaging when they're not in use. This prevents costly damage from static discharge.
Keep your station's performance at its best through regular maintenance. Clean your iron tip frequently, calibrate the temperature controls as specified, and inspect components for wear.
Store your iron in its protective case between uses to extend its life.
Consider your workspace environment carefully. While you'll want to minimize air circulation for thermal stability, make certain there's enough ventilation for safety.
Keep your station away from moisture, direct sunlight, and strong magnetic fields. Position it where you can easily access it for maintenance while maintaining a clutter-free workspace.
Regular inspection of your station's power supply and wiring will help prevent potential hazards.
Temperature Monitoring Best Practices
Maintaining precise temperature control stands at the heart of successful soldering operations. You'll need to leverage digital displays and thermocouple sensors to monitor your soldering station's temperature in real-time. Start with lower temperatures and gradually adjust upward based on your specific components and solder type. Automated systems can help control soldering duration for consistent results.
Keep your setup's accuracy by performing regular calibration checks and cleaning your tips to prevent oxidation. When you're working with different components, remember to check manufacturer specifications for maximum safe temperatures and adjust accordingly.
Temperature Control Action | Direct Benefit |
---|---|
Monitor Digital Display | Real-time accuracy feedback |
Clean Tips Regularly | Consistent heat transfer |
Check Component Specs | Prevent component damage |
Use Proper Thermal Mass | Stable temperature during use |
Calibrate Equipment | Maintain long-term precision |
Your microcontroller-based station offers programmable settings that you can customize for specific tasks. Take advantage of these features by creating temperature profiles for your most common operations. Don't forget to preheat larger components or multilayer boards to guarantee even heat distribution and reduce thermal stress. When you're moving between different tasks, allow time for temperature adjustments while maintaining an efficient workflow.
Managing Static-Sensitive Components
You'll need to store your static-sensitive components in protective containers like anti-static bags or clamshells until you're ready to work with them at your static-controlled workstation.
When handling PCBs and components, always use a properly grounded wrist strap and handle boards by their edges while minimizing movement to prevent static buildup.
For extra protection during soldering work, consider using an ionizer near your workspace to neutralize static charges in the air, particularly during low humidity conditions.
Proper Component Storage Methods
For successful static-sensitive component storage, you'll need a combination of specialized ESD-safe containers and proper handling procedures. Consider using conductive polypropylene boxes with high or low-conductive packing foam for enhanced protection.
You can also opt for customizable fibreboard ESD containers with hardwood stacking runners and removable dividers to organize your components efficiently.
When storing your components, maintain a relative humidity level between 20% and 80% to prevent static buildup. Don't place PCBs within 0.6 meters of chargeable plastics or within 0.3 meters of computer monitors.
You'll want to use static-shielding bags or clamshells for additional protection during storage and transport.
For moving components around your workspace, use ESD-protected carts equipped with conductive casters and aluminum split sleeves. Metro's SmartTrays, made from Metrostat, offer premium protection and compatibility with various cart systems.
If you're working with SMT reels, utilize Super Erecta wire shelving platforms for secure storage.
Remember to handle all components in static-controlled locations with proper grounding equipment, including wrist straps and floor mats, to maintain ESD safety throughout your storage system.
Static-Free Handling Techniques
Throughout the handling of static-sensitive components, proper grounding serves as your first line of defense against damaging electrostatic discharge. You'll need to wear an ESD wrist strap connected to a grounded source and place components on antistatic mats to safely dissipate charges. Make sure you're testing these grounding connections regularly to maintain their reliability.
When you're working with static-sensitive devices, only handle them in static-controlled areas. You'll want to keep components in static shielding bags or clamshells until you're ready to work with them.
Hold devices by their edges or frames, and don't touch solder joints, pins, or exposed circuitry. Remember to limit your movements to reduce static buildup.
To create a safe workspace, you'll need to maintain humidity levels between 20% and 80%. Keep your components away from chargeable plastics and computer monitors, and use antistatic sprays on surfaces prone to static buildup.
If you're working in the field, use portable grounding kits when static-controlled facilities aren't available. Always use ESD-safe tools and equipment during handling, and don't set components down outside their protective packaging.
Ionization During PCB Work
Ionization systems play a vital role in protecting static-sensitive components during PCB work. You'll need these devices when you can't effectively ground all items in your workspace, especially insulators and isolated conductors on PCBs.
Ionizers create both positive and negative ions that neutralize static charges, preventing potential damage to sensitive electronic components.
When you're working with PCBs, you'll find that ionizers help in multiple ways. They neutralize electrostatic fields on process-essential insulators, reduce electrostatic attraction, and remove charged particles that could contaminate your work. This is particularly important because friction between surfaces commonly generates static charges that can harm your components.
You should position ionizers at your workstation where you handle ESD-sensitive devices. They'll serve as a backup to your other static control methods and help maintain a static-free environment.
Remember that ionization fits into an extensive ESD control program – it's not a standalone solution. By using ionizers effectively, you'll minimize triboelectric charging and prevent equipment latch-up issues that could compromise your PCB work.
This protection is essential when you're dealing with sensitive electronic components that could be damaged by uncontrolled static discharge.
Proper Tool Organization
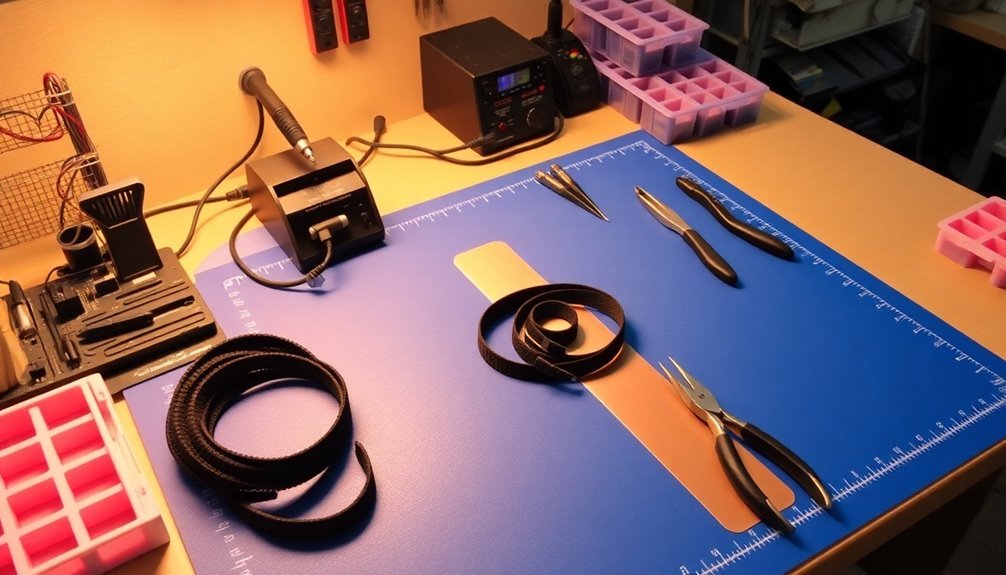
Organizing a static-safe soldering workspace revolves around three core elements: proper tool placement, component management, and safety equipment positioning. You'll want to start with a large anti-static silicone mat featuring magnetic areas and grooves to keep your tools secure and accessible.
To maximize efficiency, arrange your workspace using this essential setup guide:
Equipment | Positioning |
---|---|
Soldering Iron | Right side (for right-handed users), connected to grounded station |
ESD Wrist Strap | Within arm's reach, secured to grounding point |
Component Storage | Left side, using magnetic sections of the mat |
Cleaning Tools | Next to iron holder, brass sponge ready for use |
Heat Sinks/Clips | Front edge of mat for quick access |
You'll need to maintain your tools properly once positioned. Keep your soldering iron tip clean using a brass sponge or copper scouring pad, and always tin it before use. Position copper alligator clips nearby to act as heat sinks when needed. Pre-arrange storage areas for components and tools you'll use frequently, ensuring they're within easy reach but away from potential heat damage.
Environmental Controls For Safety
Creating a static-safe soldering environment requires careful control of multiple environmental factors. You'll need to maintain humidity levels between 40-60% to minimize static buildup, using humidifiers and anti-static sprays in dry conditions. Monitor your workspace's humidity regularly and adjust your humidification strategy based on your local climate.
Set up proper ventilation systems to protect yourself from harmful soldering fumes. Install fume extractors and position fans to direct air flow away from your work area.
You'll want to maintain good air quality by regularly cleaning your workspace and monitoring for hazardous substances.
Eliminate static-generating materials from your workstation, including plastics and synthetic fabrics. You'll need to wear anti-static clothing and use ESD-safe storage containers for sensitive components.
Install ESD mats at your workstation and connect them to a proper ground point. Don't forget to use ESD wrist straps when handling components, and guarantee all your equipment is properly grounded.
Minimize unnecessary movement around your workspace to reduce friction-based static buildup. Regular grounding checks will help maintain the effectiveness of your static control measures.
ESD Monitoring Systems
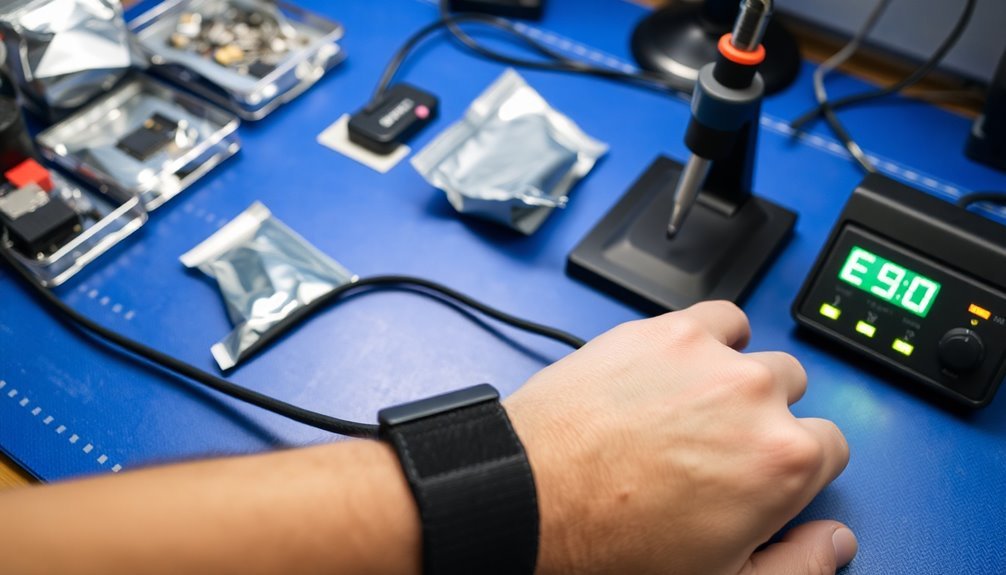
Reliability in ESD protection depends heavily on proper monitoring systems. You'll find several types of continuous monitors available, including capacitance, impedance, and resistance-based systems. Dual-wire monitors offer superior reliability compared to single-wire solutions, though they're typically more expensive.
When setting up your monitoring system, you can install it on your ESD mat, bench, or underneath. The system will provide instant feedback through LED indicators – green for proper grounding and red for faults – along with audible alarms when problems occur.
This continuous monitoring eliminates the need for manual testing and catches split-second failures that periodic checks might miss.
Here's what you should consider when choosing an ESD monitoring system:
- Dual-wire systems provide the most reliable protection and are ideal for critical applications
- Single-wire monitors offer a cost-effective solution for basic protection needs
- Visual and audible alarms confirm immediate awareness of any grounding issues
You'll find various options from suppliers like SCS, Desco, and Transforming Technologies, with prices ranging from $50 to $800. Your choice should primarily depend on your application's criticality and budget constraints.
Maintaining Your Static-Safe Workspace
A well-maintained static-safe workspace relies on multiple overlapping safety measures working together. You'll need to regularly inspect and maintain each component of your ESD protection system to guarantee continuous protection.
Start by checking your ESD table mats and floor mats for wear or damage, making sure they're properly connected to grounding receptacles. Test your wrist straps daily and verify they're securely fastened to their grounding points.
Keep your workspace clean and organized, as dust and debris can contribute to static buildup. Remove or replace any materials that generate static electricity, and consider using an ESD air ionizer if you're working in a particularly static-prone environment.
Don't forget to check your soldering equipment – guarantee your soldering station is properly grounded and inspect power cords for signs of wear.
Maintain your tools by using only ESD-safe equipment and keeping them properly stored when not in use. Clean and tin your soldering tips regularly, and always place irons in sturdy holders.
Remember to unplug equipment when you're finished working, and periodically verify that all your grounding connections are secure and functioning correctly.
Frequently Asked Questions
How Often Should Anti-Static Wrist Straps Be Tested for Conductivity?
You should test your anti-static wrist strap daily before use to guarantee proper conductivity. For critical applications, you'll need continuous monitoring, while quarterly or semi-annual testing is suitable for less critical environments.
Can Humidity Levels Affect the Effectiveness of ESD Protection Measures?
Yes, humidity levels substantially affect your ESD protection measures. You'll find ESD controls work best between 30-70% relative humidity. When it's too dry, you'll need additional safeguards like ionizers for effective protection.
What's the Shelf Life of Esd-Safe Cleaning Solutions for Soldering Equipment?
You'll typically get 12-24 months of shelf life from ESD-safe cleaning solutions. However, you should check the manufacturer's specific recommendations and storage guidelines, as some solutions may expire sooner if improperly stored.
Are Wireless Devices Safe to Use in Static-Controlled Soldering Environments?
You'll need to be cautious with wireless devices in static-controlled soldering areas. They can generate static and interfere with components, so you should minimize their use and follow proper grounding procedures when necessary.
Should Different Metals Require Different ESD Protection Approaches When Soldering?
Yes, you'll need different ESD protection approaches for various metals since they have unique conductivity and sensitivity levels. You should adjust your grounding methods and protection components based on each metal's specific characteristics.
In Summary
You'll get the most out of your static-safe soldering setup by following all these protective measures consistently. Don't skip steps or take shortcuts – proper ESD protection requires a complete system working together. Remember to test your grounding connections regularly, maintain your equipment, and keep your workspace clean and organized. When you've established good habits, static-safe soldering becomes second nature.
Leave a Reply