ESD container standards require strict adherence to ANSI/ESD S20.20 and IEC 61340-5-1 specifications. You'll need containers with surface resistivity between 1 x 10^4 and 1 x 10^11 ohms/square, tested under controlled conditions of 23°C ± 3°C and 12% ± 3% relative humidity. Your containers must maintain a ground path resistance of less than 10 ohms and provide metal-to-metal bonding connections. Testing should follow ANSI/ESD STM11.11-2015 for surface resistance and STM11.12-2015 for volume resistance measurements. The technical requirements extend far beyond these basic parameters, encompassing essential aspects of material selection, verification methods, and industry-specific compliance.
Understanding ESD Standards Classifications
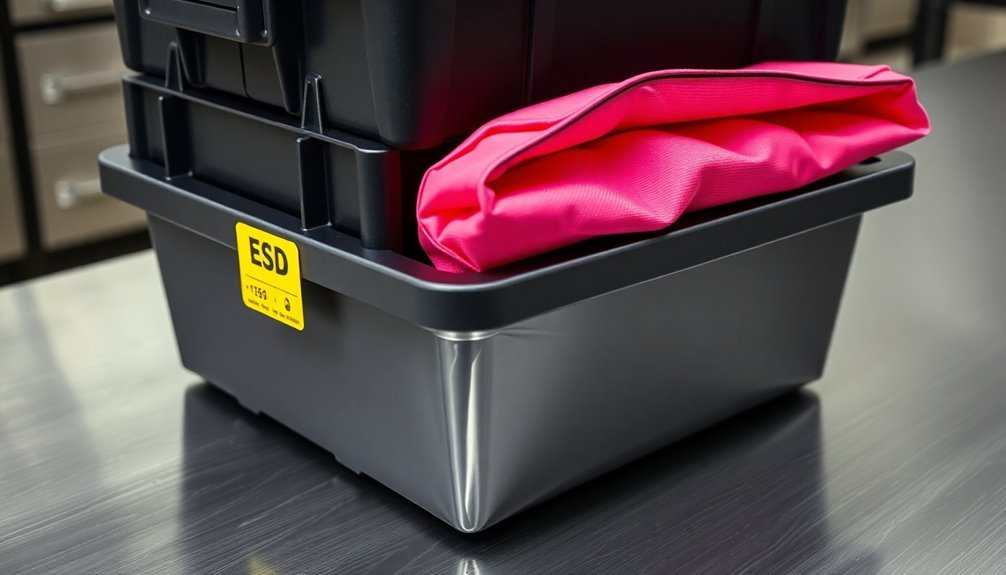
When working with electronic components, understanding ESD (Electrostatic Discharge) standards classifications is essential for protecting sensitive devices. You'll need to focus on three main models: the Human Body Model (HBM), Charge Device Model (CDM), and Machine Model (MM), each governed by specific standards documents.
For HBM classifications, you'll encounter levels ranging from Class 0 (<250V) to Class 3B (=8000V). The test uses a 100 pF capacitor discharge to accurately simulate human contact with components.
Your components need classification using both HBM and CDM standards, as they may have different ratings for each model. For instance, a device might be rated as Class 2 HBM (2000-4000V) but have a different CDM classification.
These classifications serve multiple purposes: they help you develop and measure on-chip protection, compare different devices, and guide your ESD design and monitoring processes. Remember that these classifications are guidelines rather than real-world scenarios.
When implementing ESD controls, you'll need to follow standardized test procedures to guarantee reliable, repeatable results. This systematic approach helps you maintain consistent protection levels across your handling and storage procedures.
Surface Resistivity Requirements
You'll need to measure surface resistivity values between 1 x 10^4 and 1 x 10^11 ohms/square to guarantee your ESD containers meet dissipative material requirements.
Your testing must account for temperature variations, as rigid plastics can show significant changes in resistivity under different environmental conditions.
You can verify compliance using a Surface Resistance Test Kit following ANSI/ESD STM11.11-2015 procedures, which require a 15-second electrification period and measurements of both point-to-point and point-to-ground resistance.
Conductive shielding is essential when transporting or storing ESD-sensitive components outside an EPA to maintain protection against electrostatic discharge.
Measuring Surface Resistivity Values
Surface resistivity measurements follow strict standardized procedures outlined in IEC 61340-2-3:2016. You'll need to use a standard electrode configuration consisting of a central disk surrounded by a concentric conductive ring, both making direct contact with your test material's surface. Common surface resistance meters like DESCO model 19786 are used to ensure accurate measurements.
Apply either 100V or 500V for 60 seconds to obtain the surface resistance value in ohms, which you'll then convert to surface resistivity (Ω/sq).
You must maintain environmental conditions at 23°C ± 3°C during testing. When you're measuring, remember that surface contamination can substantially affect your readings, and some degree of volume resistance will always be present in your measurements. While surface resistivity is an inherent material property, environmental factors can influence your results.
To classify your materials accurately, you'll measure against these thresholds: conductive materials should show less than 1 x 10^5 Ω/square, while static dissipative and antistatic materials should range between 1 x 10^5 and 1 x 10^12 Ω/square. For volume resistivity in conductive materials, you're looking for values less than 1 x 10^4 Ω-cm.
Always follow specific test procedures like ESD STM11.12 for verification of volume resistance.
Testing Temperature Effects
During temperature testing of ESD materials, maintaining strict environmental controls becomes crucial for accurate surface resistivity measurements. You'll need to follow IEC 61340-2-3:2016 specifications, which require testing at 23°C ± 3°C.
The standard conditions also call for 12% ± 3% relative humidity with a minimum conditioning period of 48 hours at 73°F ± 5°F. Certification requirements mandate that all materials undergo physical qualification testing rather than relying on visual inspection alone.
You must understand that temperature substantially impacts ESD performance. Testing at elevated temperatures reveals that breakdown voltage can decrease by up to 27.32%, while holding voltage drops approximately 8.49%. These changes affect the material's ability to maintain required surface resistivity values: less than 1 x 10^5 ohm/square for conductive materials and between 1 x 10^5 and 1 x 10^12 ohms per square for antistatic materials.
When conducting temperature effect tests, you'll need to follow established protocols like ANSI/ESD STM11.11-2015 and STM11.12-2015. These standards guarantee consistent evaluation of surface and volume resistance.
Remember that your ESD materials must maintain their protective characteristics throughout temperature variations during storage and application, making thorough temperature testing essential for qualifying ESD containers.
Compliance Testing Methods
Testing for ESD compliance requires adherence to specific surface resistivity standards outlined in ANSI/ESD S541. You'll need to guarantee your packaging materials maintain a surface resistivity of less than 1 x 10^5 ohm/square or less than 1 x 10^3 ohm/cm. This applies to both surface conductive and volume conductive materials, particularly those in direct contact with electronic devices.
These standards help ensure effective ESD process control across the electronics industry as devices become increasingly sensitive due to higher circuit density. You must conduct your testing under strictly controlled environmental conditions. Run your tests at 12 ±3% relative humidity and 73 ±3°F for at least 48 hours.
You'll need to employ several standardized testing methods, including ANSI/ESD STM11.11-2015 for surface resistance and ANSI/ESD STM11.12-2015 for volume resistance measurements inside bags. Don't forget to perform electrostatic decay testing using MIL-STD-3010C, Method 4046-2013.
For antistatic materials, you'll want to verify that surface resistivity falls between 1 x 10^5 and 1 x 10^12 ohm/square. Your volume conductive materials should demonstrate resistivity less than 1 x 10^4 ohm-cm.
Remember to check that your materials maintain their protective characteristics throughout storage, shipment, and application without harmful outgassing or containing destructive substances.
Material Testing and Verification Methods
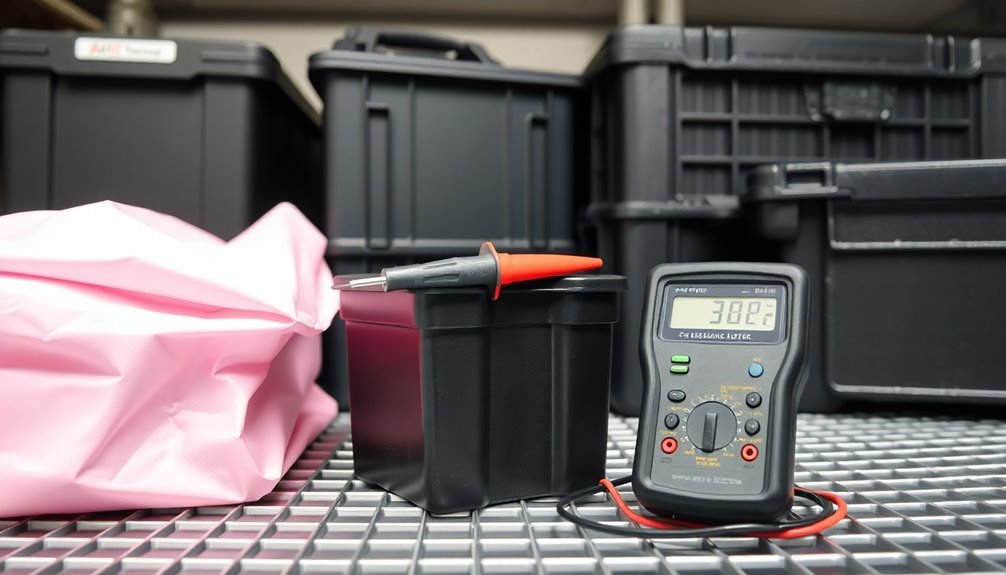
Material verification stands at the forefront of ESD container certification, requiring strict adherence to established testing standards like ANSI/ESD STM11.11-2015 and IEC 61000-4-2. You'll need to conduct thorough testing using specialized equipment to guarantee your containers meet these requirements. Testing should be conducted in controlled temperature and humidity conditions to ensure consistency of results.
Surface and volume resistance measurements form the cornerstone of material validation, helping you determine if your containers provide adequate ESD protection.
When testing ESD containers, you'll want to focus on these essential methods:
- Surface resistance testing using concentric ring fixtures and electrometers to measure the material's ability to dissipate static charges
- Volume resistance evaluation through ANSI/ESD STM11.12-2015 protocols to verify internal conductive properties
- Charge transfer measurements to assess the container's discharge characteristics
You must perform these tests using calibrated equipment like ESD generators and ground reference planes under controlled environmental conditions.
Don't forget to take into account industry-specific requirements – if you're supplying containers for medical devices, you'll need to comply with EN 60601-1-2, while automotive applications require ISO 10605 compliance.
Regular verification guarantees your containers maintain their protective properties throughout their lifecycle.
Static Decay Performance Measurements
You'll need properly calibrated static decay meters and specialized fixtures to set up accurate ESD container testing equipment.
Using standard meters like the M 4406 with its ±50ms accuracy ensures reliable test results across different materials and conditions.
Your voltage measurement protocols must follow FTMS 101C Method 4046 guidelines, which typically require measuring the dissipation of a 5,000-volt charge.
To meet standard acceptance criteria, your ESD containers should demonstrate a static charge decay time of less than 2 seconds to reach 10% of the initial voltage level.
Decay Testing Equipment Setup
A reliable static decay measurement starts with proper equipment setup and calibration. You'll need to confirm your static decay meter meets industry standards like Federal Test Standard 101C and EIA-541, while operating within specified environmental conditions of 23ºC ± 3ºC and 12% ± 3% relative humidity.
When setting up your decay testing equipment, focus on these critical components:
- A Faraday cage isolation system to shield your measurements from external electromagnetic interference
- An environmental chamber that maintains consistent temperature and humidity for specimen preconditioning
- Proper grounding mechanisms to guarantee accurate charge dissipation measurements
Before testing, you'll want to verify your equipment's calibration, confirming it can accurately measure within the ±50ms tolerance at specified conditions. The triboelectric and corona methods require different setup considerations, as each can affect material properties differently.
Configure your charge voltage settings, typically ranging from 0 to ±5KV, based on your testing requirements. The equipment should be capable of recording decay times from milliseconds to hours, depending on your material's characteristics.
Remember to enable the data storage function if you're conducting multiple tests, as this will help maintain accurate records for quality control and compliance documentation.
Voltage Measurement Protocols
Properly measuring static decay performance requires strict adherence to standardized voltage measurement protocols. You'll need to follow established standards like IST 40.2, MIL STD 3010, and GB 19082 to guarantee accurate and repeatable results.
Your testing process should begin by force-charging your test specimens to 5,000 volts under controlled temperature and humidity conditions.
You must start timing immediately when you shut down the applied voltage and ground the specimen. Your measurements should track the decay time until the voltage reaches "technical 0" (less than 50 volts).
You'll want to use specialized static decay analyzers with high-resolution timing capabilities – these can measure intervals from 0 to 99.99 seconds with precision down to 0.01 seconds.
Your testing setup should include appropriate control units, test fixtures, and environmental chambers to maintain consistent conditions. You'll need to guarantee your high voltage power supply and measuring instruments are properly calibrated.
It's best to utilize automatic test procedures whenever possible to minimize manual errors, and you should employ real-time display software to capture and analyze your measurement data accurately.
Decay Rate Acceptance Criteria
Several standardized acceptance criteria govern static decay performance measurements for ESD containers. You'll need to verify your containers meet specific test conditions, including preconditioning at 23°C ± 3°C and 12% ± 3% relative humidity.
The decay times must reach technical zero, which means dropping to less than 50 volts under standardized measurement protocols.
Key testing requirements include:
- Using calibrated equipment like the Electro-Tech Systems Model 4406 or IST 40.2 Charge Decay Analyzer
- Testing materials within a Faraday cage to isolate samples and guarantee measurement accuracy
- Conducting repeated tests to account for material property variations and charging times
When measuring decay rates, you'll need to follow established standards such as Federal Test Standard 101C Method 4046 or ANSI/ESD S20.20. Remember that material characteristics, including conductive layers and laminations, can substantially affect your test results.
While charge decay tests are essential, they shouldn't be your only evaluation method. It's recommended to complement them with resistance measurements for a thorough assessment of your container's ESD protection capabilities.
Container Design Specifications
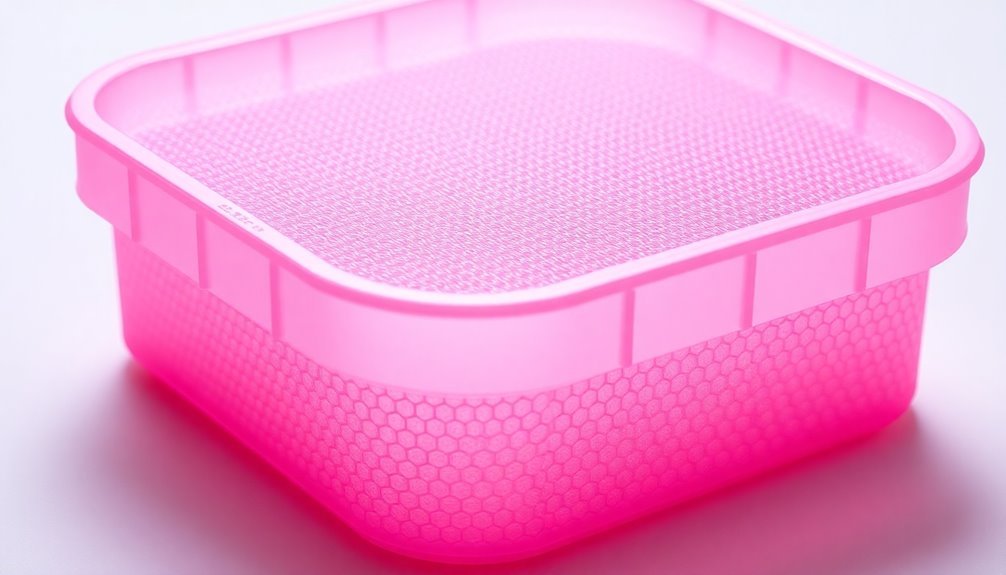
Within the domain of ESD protection, container design specifications play a crucial role in guaranteeing both functionality and compliance. You'll find that modern ESD containers come in various standardized dimensions, with common sizes including 594x396x280 mm and 600x400x220 mm, offering volume capacities between 46 and 48 liters.
Feature | Specification | Purpose |
---|---|---|
Handles | Closed/Integrated | Safe handling |
Stacking | Dynamic load rated | Warehouse efficiency |
Lids | Hinged options | Component protection |
Design | Foldable/Rigid | Space optimization |
When you're selecting ESD containers, you'll need to evaluate their stacking capabilities, as they're designed to bear specific stack loads during both static and dynamic conditions. The containers incorporate different handle designs, with both closed/integrated and opened options available to suit your handling requirements.
For space efficiency, you'll find that foldable containers are particularly advantageous, offering up to 80% space savings when not in use. These containers feature integrated fasteners that guarantee safe and straightforward folding operations while maintaining their protective properties. When hinged lids are required, they can be specially ordered to provide additional protection for sensitive components.
Compliance and Certification Guidelines
Manufacturing and handling ESD containers requires strict adherence to compliance and certification guidelines. You'll need to undergo mandatory audits conducted by approved auditors who'll verify your ESD control program meets IEC 61340-5-1 standards.
These audits evaluate your ESD awareness, EPA setup, grounding procedures, and overall compliance with established protocols.
To maintain certification, you'll need to:
- Complete thorough training covering ESD awareness, static charge management, and EPA setup requirements
- Participate in annual renewal audits and keep detailed CPD logs
- Implement regular compliance verification through testing and measurements
Your certification process involves working with recognized bodies like the EOS/ESD Association, Inc., which provides necessary training and issues compliance certificates. You'll find that certification offers significant advantages, including increased credibility with customers and reduced risk of ESD damage during container handling.
The training can be completed online or through physical sessions, combining theoretical knowledge with hands-on practice. Remember, you must regularly update your training to stay current with evolving ESD standards and maintain your certification status.
Grounding and Bonding Requirements
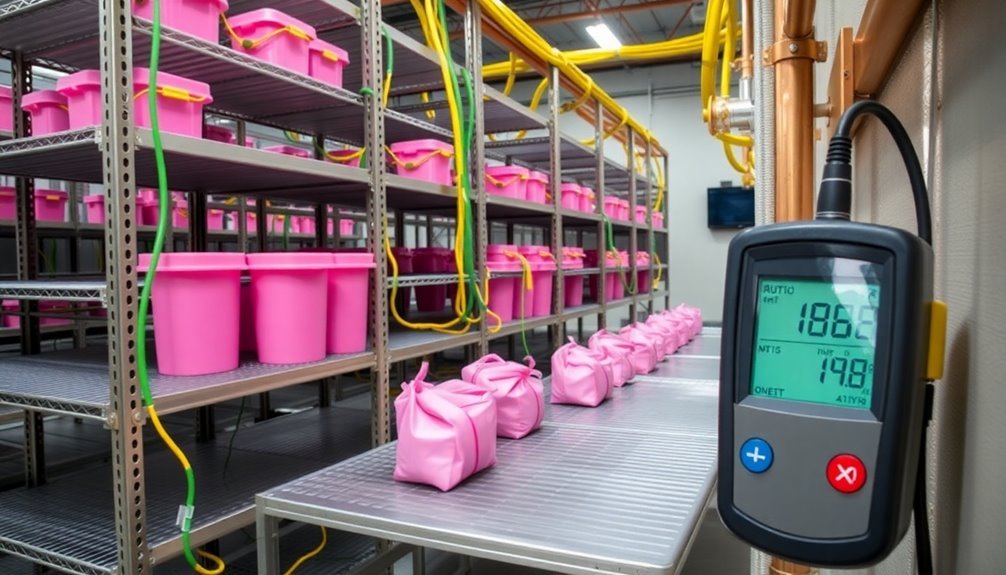
You'll need to meet specific resistance limits when establishing ground paths for ESD containers, typically maintaining less than 10 ohms from container to earth ground.
Your bonding connections must create metal-to-metal contact through clamps with sharp teeth, ensuring an unimpeded electrical pathway between containers during liquid transfers.
Regular verification of your grounding equipment's effectiveness through resistance testing helps maintain compliance with NFPA 30 and OSHA requirements for safe handling of flammable materials.
Ground Path Resistance Limits
Several essential resistance limits govern ESD container and flooring safety standards. For ideal ESD protection, you'll need to verify point-to-point and surface-to-ground resistance stays between 1.0 x 10E6 and 1.0 x 10E9 ohms for floors and floor coverings. This range effectively prevents static charge accumulation while maintaining safety for personnel and equipment.
Your ESD flooring must provide a clear path to ground that's ≤ 1.0 x 10E9 ohms, measured according to ANSI/ESD STM7.1.
When implementing grounding solutions, remember these key requirements:
- Install one copper grounding strap per 1000 square feet of ESD flooring
- Maintain worksurface resistance between 1 x 10^6 and 1 x 10^9 ohms
- Verify shelving and drawer surfaces stay within the technical range of < 1 x 10^9 ohms
For effective grounding, you can connect straps to electrical outlets, conduit, building steel, or a dedicated grounding bar.
If you're working with floors installed on-grade or below grade, drive a copper grounding rod into the ground.
Don't forget to think about the primary path to ground for worksurfaces, as this is vital for preventing Charged Device Model (CDM) damage.
Bonding Connection Standards
In accordance with ANSI/ESD standards, proper bonding connections require metal-to-metal contact with clean, unobstructed surfaces. You'll need to remove all paint, dirt, rust, and other contaminants from connection areas to guarantee effective bonding.
When establishing these connections, you can choose between permanent and temporary solutions based on your needs.
For permanent installations, you should use solid or braided wires with screw-type clamps or welded connections. If you're setting up temporary bonds, opt for braided wires with spring clamps or magnetic attachments.
You must establish conductive paths between all components and link them to a common ground point, as specified by ESD Association standards.
You'll need to implement regular inspection procedures to verify that all connections maintain their metal-to-metal contact and remain damage-free. It's vital to follow written procedures for your bonding techniques to prevent ESD damage and maintain compliance with ANSI/ESD S6.1 and other relevant standards.
Remember that proper training in ESD control principles is vital for your team to maintain effective bonding practices and guarantee ongoing protection of sensitive components.
Equipment Grounding Verification
Proper bonding connections work hand-in-hand with equipment grounding verification to create a complete ESD protection system. You'll need to verify that your equipment grounding conductor maintains an impedance of no more than 1.0 ohm, connecting to the AC equipment ground that serves as your ESD Grounding/Bonding Reference Point.
To guarantee effective equipment grounding verification, you must:
- Use an AC Outlet Analyzer or Circuit Tester to check electrical receptacle wiring and impedance
- Verify auxiliary grounds are electrically bonded to the AC equipment ground
- Conduct periodic testing with a DC Ohmmeter to confirm proper resistance values
When performing verification tests, you'll need to place your equipment on an insulative support surface with resistance greater than 1.0 x 10^13 ohms/square.
Regular testing isn't optional – it's essential for maintaining ANSI/ESD S20.20 compliance and guaranteeing your ESD protection remains effective. Remember to document all verification results and maintain a regular testing schedule.
If you're using air ionizers, you'll also need to incorporate a Charged Plate Monitor into your verification process to confirm proper functionality.
Packaging Material Selection Criteria
Selecting appropriate ESD packaging materials requires careful consideration of multiple critical factors, including device sensitivity, distribution environment, and material properties. You'll need to evaluate your product's ESD sensitivity level and match it with packaging that provides adequate protection through the entire distribution chain.
Selection Factor | Key Considerations |
---|---|
Device Sensitivity | Surface resistivity must be <1.0 x 10^3 ohm-cm for sensitive components |
Material Properties | Choose between dissipative, anti-static, or conductive materials |
Distribution Path | Consider environmental hazards and handling requirements |
Cost Effectiveness | Balance protection needs with total package value |
When selecting materials, you must guarantee compliance with standards like ANSI/ESD S541 and IEC 61340-5-1. Test your chosen materials to verify they meet the required specifications for conductivity and static dissipation. Consider whether you'll need intimate packaging that directly contacts the product or proximity packaging that provides both physical and ESD protection.
Your packaging system should incorporate appropriate marking to indicate ESD protective properties and maintain continuous grounding capabilities throughout the distribution process. Remember to factor in both primary protection needs and secondary packaging requirements when designing your complete ESD protection strategy.
Industry Applications and Usage
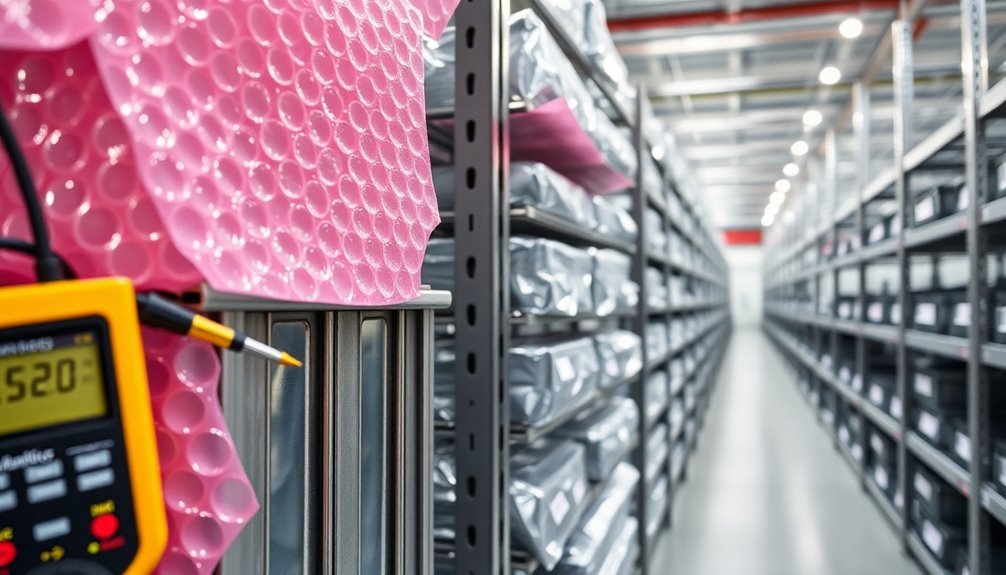
Building on the fundamentals of material selection, ESD containers serve specific purposes across diverse industries, each with unique requirements and challenges. You'll find these containers extensively used in electronics manufacturing, where they protect sensitive components from static discharge while meeting ANSI/ESD S20.20 and IEC 61340 standards.
Medical device manufacturers rely on ESD containers to guarantee both static protection and contamination control. You'll need to select containers that comply with industry-specific regulations while maintaining the integrity of sensitive medical components during handling and transport.
Key applications across industries include:
- Electronics production lines using custom ESD trays for component protection during assembly and transportation
- Automotive manufacturing facilities implementing conductive packaging solutions for electronic control units and sensors
- Specialized industries handling explosive materials or conducting sensitive research requiring strict static control measures
When you're selecting ESD containers for your specific industry, you'll need to think about both regulatory compliance and practical application requirements. The automotive sector, for instance, demands containers that protect increasingly complex electronic systems while maintaining efficient production flow.
Research facilities require solutions that safeguard sensitive equipment while allowing easy access for testing and analysis.
Environmental Impact and Recyclability
Despite ongoing technological advances in ESD protection, the environmental impact of traditional ESD containers presents significant challenges for sustainability efforts. Most ESD bags aren't recyclable due to their complex material composition, and even when they're technically recyclable, like pink bags, they face significant processing hurdles in municipal recycling centers.
You'll find that current reuse options are limited by reliability concerns and the logistical challenges of collecting and inspecting used containers.
However, you can now explore emerging sustainable alternatives. Companies like Blue Lake Packaging are developing biodegradable ESD bags from cellulose, while Cortec's EcoSonic ESD Paper offers recyclable solutions from renewable tree sources.
When selecting ESD packaging, you'll need to evaluate EPA's Five Guiding Principles and comply with SCS Global Services standards for recycled content claims. You must maintain detailed documentation and submit to audits for verification.
To make environmentally conscious decisions, you should assess the full life cycle impact of your ESD packaging choices and consider new eco-friendly designs that incorporate both ESD and corrosion protection while minimizing environmental impact.
Frequently Asked Questions
How Often Should ESD Containers Be Replaced in Regular Industrial Use?
You'll need to replace ESD containers based on regular inspections and testing, typically every 12-18 months with normal use. However, replace them immediately if you notice damage or they fail conductivity tests.
Can ESD Containers Be Safely Stacked Without Compromising Their Protective Properties?
You can safely stack your ESD containers without compromising protection, as long as you follow weight limits, stack them evenly, and guarantee they're properly nested. They're specifically designed for secure stacking in industrial settings.
What Cleaning Methods Are Safe for Maintaining ESD Containers?
You should use ESD-specific cleaning solutions and soft microfiber cloths. Don't apply regular cleaners or IPA wipes. Avoid abrasive tools and harsh chemicals that'll damage protective properties. Let surfaces dry completely after cleaning.
How Does Temperature Fluctuation Affect ESD Container Performance?
You'll notice temperature changes can weaken your ESD container's protective properties, reducing its static dissipative qualities. Extreme heat or cold may alter the material's conductivity and compromise its ability to shield components.
Are There Special Storage Requirements for Unused ESD Containers?
You'll need to store unused ESD containers in clean areas with temperatures between 5-35°C and humidity of 45-75%. Keep them away from chemicals, ground them properly, and protect them from physical damage.
In Summary
You'll need to guarantee your ESD containers meet all technical requirements and testing protocols outlined in this guide. Stay current with evolving standards, as they're vital for protecting sensitive electronics. Remember to verify your containers' surface resistivity, static decay performance, and grounding specifications regularly. By following these thorough requirements, you're safeguarding your components while maintaining regulatory compliance and environmental responsibility.
Leave a Reply