You'll find basic footwear testing machines starting around $850-$1,200 for essential equipment like outsole flexing and abrasion testers. Premium testing solutions can range from $3,000 to $5,000, offering computerized controls and real-time monitoring. Specific machines vary widely in cost – from $350 for manual surface testers to $36,000 for advanced slip resistance equipment. Don't forget to factor in maintenance costs of $2,000-$20,000 monthly, plus energy expenses and staff training. Understanding the complete cost picture can help you make smarter investment decisions for your testing needs.
ESD Testing Equipment Price Overview
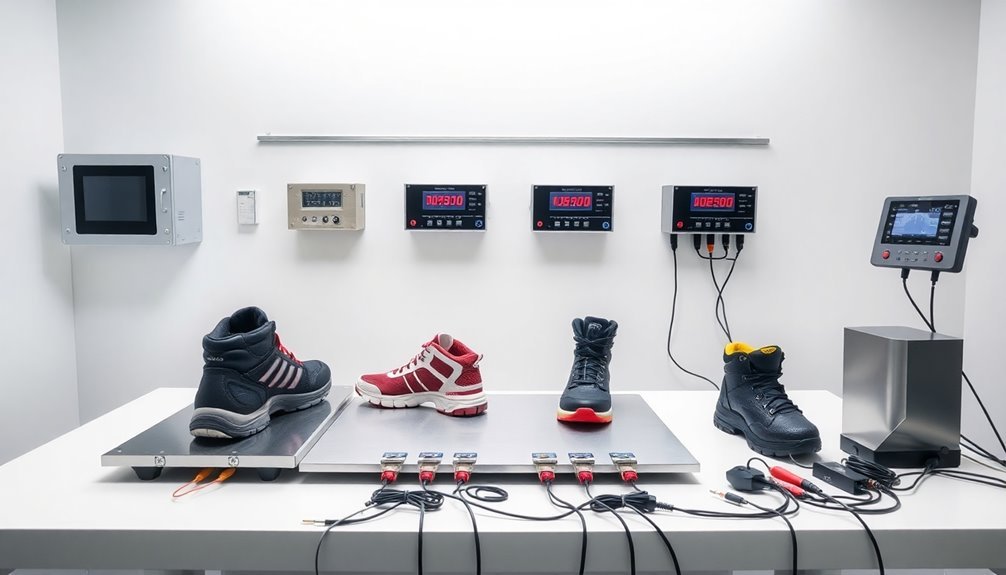
While ESD footwear testing equipment varies substantially in price, you'll find basic testers starting around $200 and professional testing kits exceeding $3,000.
High-end models like the Warmbier PDT800K Deluxe "Near-Fail" Combo Tester will cost you around $2,108, offering thorough testing capabilities for both wrist straps and footwear. Advanced testers often include two floor weights that comply with industry standards.
If you're looking for surface resistance testing equipment to complement your footwear tester, you'll need to budget accordingly. Basic meters like the SCS Surface Resistance Meter cost about $428, while advanced options like the SCS Resistance Pro Meter run around $1,780.
Desktop models can exceed $5,000 for premium features and accuracy.
You'll also need to take into account accessories for your testing equipment. Test leads, electrodes, and carrying cases range from $15 to $226, with items like the Warmbier Test Leads being on the higher end.
For a complete testing solution, thorough kits like the SCS Eos/ESD Assessment Kit cost around $8,465, though most facilities won't require such extensive equipment.
Your specific testing needs and facility requirements will ultimately determine which price range best suits your situation.
Basic Resistance Testing Machine Costs
You'll find basic resistance testing machines for footwear starting at $200 for entry-level models, while general-purpose testers can be found for as low as $100.
Many testers offer voltage up to 600V for comprehensive safety verification of footwear resistance levels.
Premium electronic systems with advanced features can reach $3,500, offering enhanced precision and automated testing capabilities.
When choosing between models, you'll need to weigh whether specialized footwear testing requirements justify the higher cost of industry-specific machines that typically range from $1,300 to $1,600.
Entry-Level Price Ranges
For entry-level footwear testing equipment, basic resistance machines typically range from Rs 70,000 to Rs 100,000 ($850-$1,200 USD).
You'll find essential machines like the Outsole Flexing Tester and Veslic Abrasion Tester priced at around Rs 90,000, while the Heel Fatigue Tester comes in slightly lower at Rs 77,800. These prices reflect basic configurations with digital displays and semi-automatic operations. Many of these machines are equipped with touch screen controls to ensure precise testing parameters.
When you're looking at specific testing equipment, you'll notice that manufacturers like Ramp Impex Private Limited and Asian Test Equipment dominate the entry-level market. Their machines typically feature mild steel construction and comply with multiple international standards, including ISO, SATRA, and ASTM specifications.
The Rub Fastness Tester, for instance, costs Rs 90,000 and meets industrial testing requirements.
Most entry-level machines offer essential testing capabilities while maintaining compliance with relevant standards. You'll find that these basic units often include digital displays and semi-automatic features, making them suitable for fundamental quality control operations.
While more advanced machines can cost substantially more, these entry-level options provide a practical starting point for basic footwear testing needs.
Premium Models and Features
Premium resistance testing machines command prices between $3,000 and $5,000, offering sophisticated features like computerized controls and real-time data monitoring.
You'll find these high-end machines equipped with mechanical pull force capabilities and universal testing functions for materials like rubber and steel. These machines comply with industry testing standards like ASTM, ISO, and TAPPI.
For advanced footwear testing, you'll need to invest in systems that provide real-time closed-loop control and integrated test center software. These premium machines can apply maximum torque up to 1,600 Nm and achieve rotational speeds of 300 degrees per second.
They're particularly valuable for thorough footwear analysis and quality assurance.
The specialized testing equipment segment offers options ranging from $198 to $3,800. You can choose from electronic universal testing machines with 5 KN capacity, digital display adhesive peeling testers, and heel impact fatigue testing devices.
For specific testing needs, you'll find portable options like the MARK II Slip Resistance Tester and the Portable Inclineable Articulated Strut Slip Tester (PIAST). These portable units feature premium steel construction and are designed for easy operation and maintenance while meeting ASTM-F1677 standards.
Ground Conductivity Analyzers Investment Range
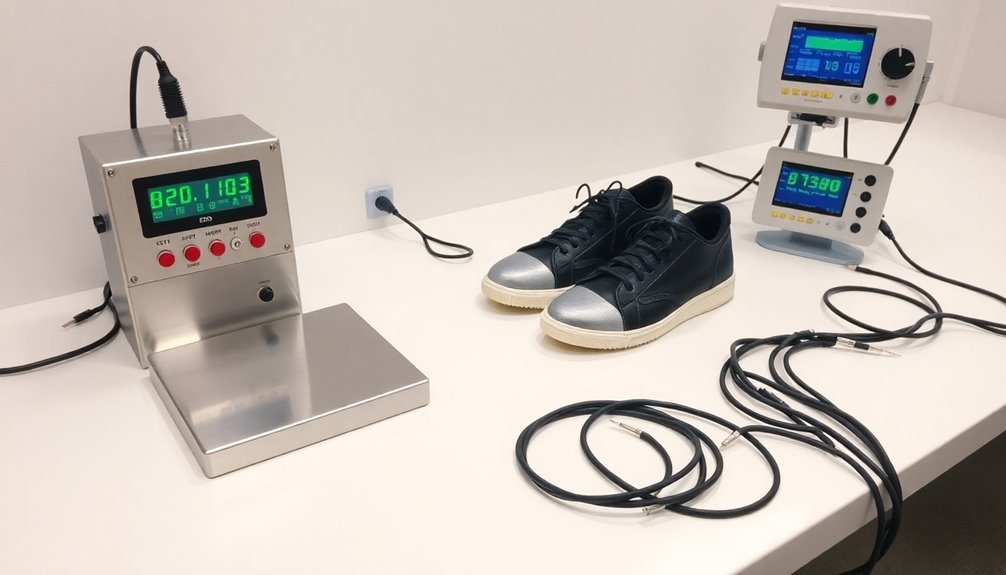
When you're exploring ground conductivity analyzers like the Geonics EM38-4, you'll find various pricing tiers that align with different measurement capabilities and precision levels.
Your investment will directly impact testing accuracy, with high-end models offering superior precision of +/- 0.1% full scale and conductivity ranges up to 1,000 mS/m.
While specific pricing isn't publicly listed, you can expect the cost to reflect the analyzer's advanced features, such as multiple intercoil spacings and versatile data communication options through RS-232, Bluetooth, and USB connections. The instrument's ability to operate in extreme temperature conditions from -40°C to +50°C demonstrates its durability and value for various testing environments.
Pricing Tiers For Analyzers
The investment landscape for ground conductivity analyzers spans across four distinct pricing tiers, ranging from basic portable meters to sophisticated industrial equipment. You'll find entry-level portable meters in Tier 1, priced from $42.41 to $659.00, offering basic functionality like NPK, EC, and pH measurements for field testing. Many units incorporate conductive nitrile rubber to enhance grounding capabilities and measurement accuracy.
Moving up to Tier 2, mid-range analyzers cost between $130.00 and $170.00, providing specialized features for water treatment and agricultural applications. Tier 3 equipment, priced from $499.00 to $699.00, delivers higher precision for laboratory and detailed field studies. At the top end, Tier 4 professional meters range from $1,249 to $50,940.00, offering industrial-grade accuracy and durability.
Tier Level | Price Range | Key Features |
---|---|---|
Tier 1 | $42-659 | Multi-parameter sensing, portable design |
Tier 2 | $130-170 | Water treatment, agricultural use |
Tier 3 | $499-699 | High precision, laboratory grade |
Each tier represents a significant jump in capabilities and precision, with higher tiers offering enhanced features like temperature compensation, digital outputs, and robust construction for harsh environments. Your choice should align with your specific testing requirements and operational environment.
Testing Accuracy Vs Cost
Striking a balance between testing accuracy and cost presents a critical decision point when investing in ground conductivity analyzers. You'll find that entry-level models starting at $130-$145 offer basic conductivity measurements, while professional-grade equipment like the Geonics EM39 delivers superior precision and depth capabilities at a higher price point. The system's 39.2 kHz frequency ensures optimal performance for most geological applications.
When evaluating accuracy versus investment, consider these critical factors:
- Environmental conditions impact field accuracy, requiring more sophisticated equipment for consistent results
- Higher-end models provide better noise reduction and sensitivity adjustments
- Regular calibration capabilities directly affect long-term measurement reliability
Your testing requirements should drive your investment decision. Mid-range options like the BOQU MPG-6099 ($659-$759) offer multi-parameter analysis, suitable for water quality monitoring and basic agricultural assessments.
However, if you're conducting geological surveys or archaeological exploration, you'll need advanced models like the EM38-4, which provide both conductivity and magnetic susceptibility measurements at multiple depths.
Keep in mind that professional-grade analyzers often include dedicated calibration services and technical support, adding value beyond mere accuracy specifications.
Static Dissipative Footwear Test Methods
Modern static dissipative footwear testing relies on three primary international standards: IEC TS 60079-32-1, EN ISO 20345, and NFPA 77 Section 8.2.2.2. Each standard specifies different resistance ranges, with IEC requiring 1-100 Meg-Ohm and EN ISO allowing 100 Kilo-Ohm to 1000 Meg-Ohm for antistatic footwear.
You'll need specific equipment to conduct proper testing. The SATRA STM 470 conductivity tester is your primary tool, requiring steel balls to fill the shoe and create contact with the connection plate. You'll apply 100±2V dc for one minute to measure resistance.
For simpler testing, you can use the Sole-Mate II device, which measures resistance between a hand-held metal bar and plate.
To verify accurate results, you'll need to test footwear in both dry and wet conditions. When performing wet testing, you must apply conductive lacquer to guarantee proper contact between the sole and copper plate.
While these methods vary in complexity and cost, they're all essential for maintaining safety standards. Remember, you're responsible for following manufacturer's instructions and relevant standards during testing, as proper verification of static dissipative properties is vital for workplace safety.
Premium ESD Testing Solutions
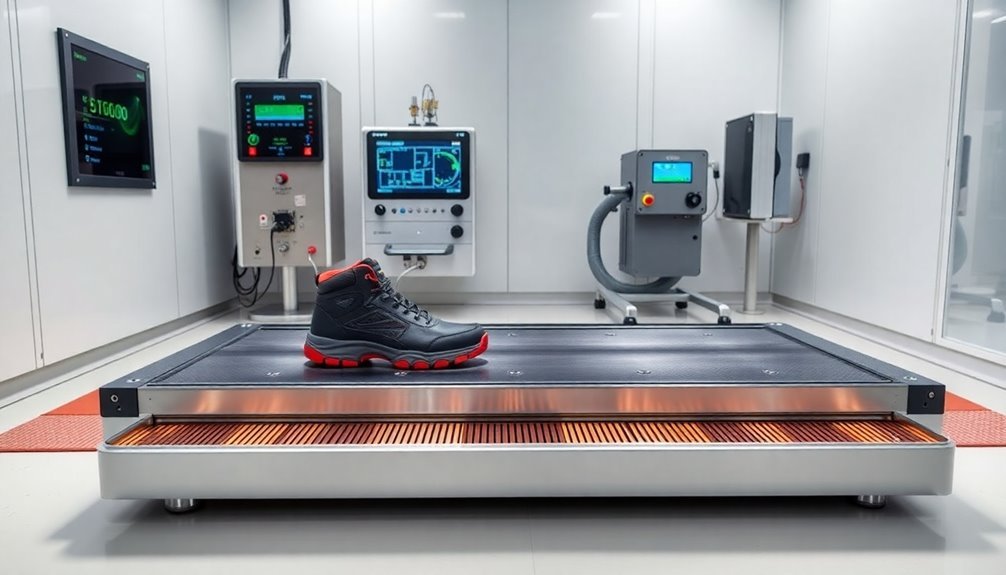
Professional ESD testing equipment represents a significant investment in workplace safety, with high-end solutions ranging from $1,500 to $2,000 for complete testing kits. When you're looking at premium options like the AEMC Electrostatic Discharge Floor Test Kit at $1,640, you'll also need to think about additional accessories that can impact your total investment.
These include adapters ($20), continuity probes ($121), and test leads ($114-$189).
Premium ESD testers offer several advantages that justify their cost:
- Extended battery life supporting up to 6,000 IR tests or 3,000 R tests
- Robust IP 54 rating for environmental protection
- Compliance with strict safety standards like IEC/EN 61010-1 and 600V CAT IV
You'll find these high-end units provide thorough testing capabilities while meeting international standards for static dissipative footwear testing. When you're selecting equipment, remember that proper testing guarantees your workplace's safety through accurate resistance measurements (typically 750 Kiloohms to 35 megohms).
While the initial investment might seem substantial, it's vital for maintaining consistent ESD protection and compliance with safety regulations in your facility.
Testing Machine Maintenance Expenses
Maintenance expenditures for footwear testing machines require careful financial planning, with costs typically ranging from 5-10% of your total operating budget. You'll need to account for both routine maintenance tasks and potential major component replacements throughout your equipment's lifecycle.
For servo-hydraulic machines, you're looking at power unit replacement costs between $35,000 and $45,000, while electromechanical systems might require motor drive replacements ranging from $17,000 to $25,000.
Regular maintenance includes essential tasks like lubricating moving parts, replacing extensometer knife edges, and cleaning grip faces to guarantee accurate testing results.
You can optimize your maintenance expenses by implementing a preventive maintenance program. This approach helps you identify potential issues before they become serious problems, reducing unexpected downtime and costly emergency repairs.
Consider investing in service contracts, which often provide discounted maintenance rates and priority service.
Don't forget to factor in technician labor costs and specialized tools required for maintenance procedures. While energy-efficient machinery may cost more upfront, it can substantially reduce your long-term operating expenses.
Regular inspections and timely replacement of worn parts will help maintain your equipment's efficiency and extend its lifespan.
Installation and Setup Requirements
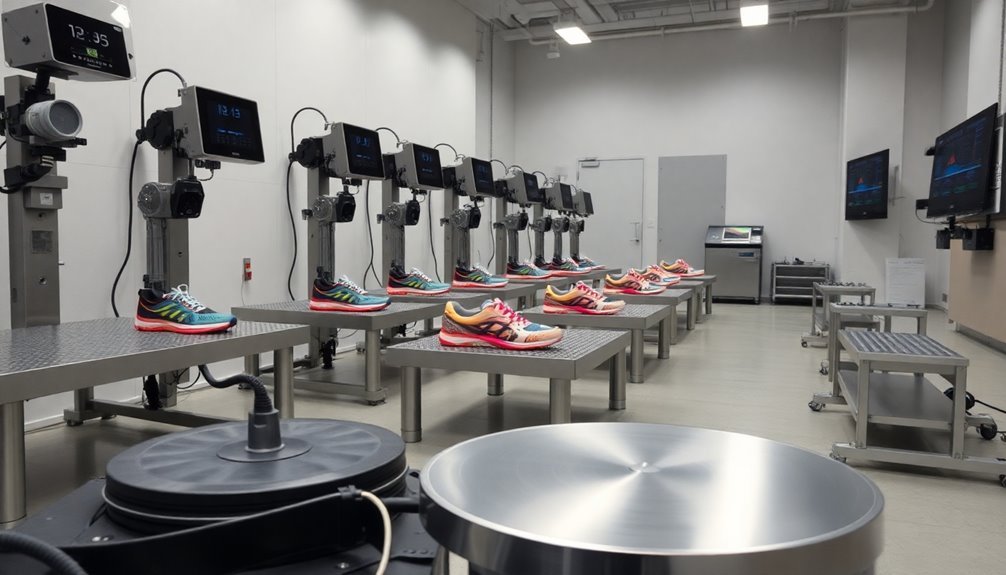
Proper installation of footwear testing equipment demands careful attention to mounting specifications and power requirements. You'll need to mount the equipment approximately 1.5 meters above floor level using the Dual Lock Fastening Discs for secure wall attachment.
Don't forget to establish a proper earth ground connection, as it's vital for accurate testing results.
The power setup requires specific considerations depending on your model. You'll need either:
- An AC/DC transformer for the SCS 740 model
- A 24-30VDC power adapter
- A 9V battery for certain combo testers
When installing the foot plate component, you'll need to connect it using the appropriate banana plug to jack connection and secure it properly to the pedestal using the provided screws and Allen wrench. Make sure to route all cables through the designated guides to prevent tripping hazards and guarantee efficient operation.
Don't overlook the importance of proper DIP switch configuration for setting resistance limits and audio adjustments if your model includes these features.
Remember to verify that your calibration certificate is included and keep it accessible for future reference.
Careful attention to these installation requirements will guarantee accurate testing results and extended equipment life.
Compliance Testing Equipment Breakdown
Through rigorous industrial standards, footwear compliance testing requires four essential equipment categories.
Universal Tensile Testing Machines form the first category, featuring PC-controlled systems like STm 566 and STm 766. These machines are equipped with double-column structures for enhanced stability and precision load cells for reliable testing of tensile, peeling, and tear characteristics.
The second category includes Slip Resistance and Abrasion Testers, where you'll encounter equipment like STm 603 and the SATRA Pedatron. These machines test the coefficient of friction and simulate walking actions to evaluate soling wear on various flooring surfaces.
Impact and Penetration Testers make up the third category, with equipment like STm 609 testing safety footwear's protective capabilities. You'll need to test four areas of each shoe's outsole, applying at least 1,100 newtons of force for non-metallic inserts.
The fourth category encompasses Electrical Safety Testers, which must achieve 2.5% accuracy at 100 V DC. You'll use these machines with stainless steel balls and copper contact base plates to measure electrical resistance between the sole and conductive surfaces.
Annual Operating Cost Analysis
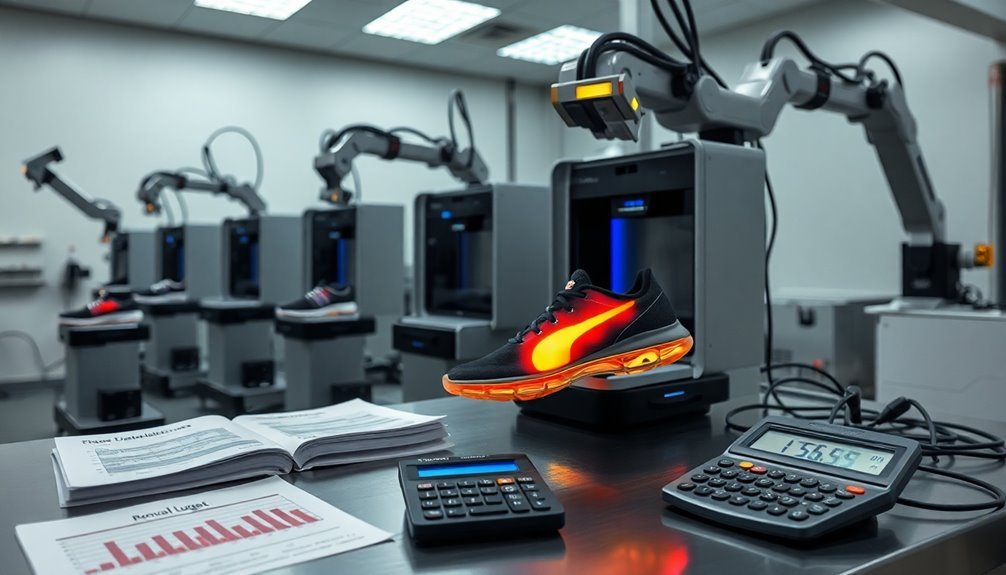
When you're planning your footwear testing facility's budget, you'll need to balance machinery maintenance costs (5-10% of your operating budget) against monthly energy expenses ranging from $1,000 to $10,000.
Your staff training investments will directly impact maintenance efficiency, as skilled technicians can better prevent and address equipment issues that could otherwise lead to costly downtime.
Based on the equipment maintenance data, you should schedule major replacements annually, allocating between $5,000 and $10,000 for 3D printing equipment maintenance alone.
Maintenance vs. Energy Costs
The bottom line of footwear testing operations hinges on two major cost factors: maintenance and energy consumption. When you're comparing these expenses, you'll find that maintenance costs typically range from $2,000 to $20,000 annually, while energy costs can run between $1,000 to $10,000 monthly.
Your maintenance expenses will primarily stem from:
- Regular equipment inspections and repairs
- Replacement of worn components like knife edges and grip faces
- Periodic lubrication and cleaning of moving parts
Energy costs tend to fluctuate based on your operational scale and testing volume. You'll notice that per-pair testing costs average between $0.50 to $2, with similar rates applying to 3D printing operations.
While maintenance costs might appear substantial upfront, they're often lower than cumulative energy expenses, especially in smaller operations.
You can enhance both cost categories through strategic planning. Modern, efficient equipment might cost more initially but can substantially reduce your energy consumption over time.
Similarly, implementing a robust maintenance schedule, typically allocating 5-10% of the equipment's purchase price annually, helps prevent costly breakdowns and maintains peak energy efficiency.
Staff Training Requirements
Beyond equipment maintenance and energy costs, staff training represents a significant annual operating expense in footwear testing facilities. You'll need to budget between $1,000 and $10,000 per training program, depending on its depth and scope. This investment covers everything from basic shoemaking courses to advanced footwear technologist accreditation programs.
Your technicians will require ongoing training to keep pace with the evolving global footwear market. Organizations like SATRA offer specialized courses that enhance your team's technical expertise and guarantee compliance with industry standards.
While in-house training can help reduce external costs, you'll still need to allocate funds for annual skills assessments and certification processes.
The return on your training investment manifests through improved productivity, enhanced quality control, and better regulatory compliance. Your trained technicians will operate testing equipment more efficiently and maintain higher safety standards. They'll also develop a broader understanding of different production environments, which is vital for thorough testing procedures.
Consider that while training costs may seem substantial, they're essential for maintaining competitiveness and fostering innovation in your testing facility. Plus, investing in your staff's development often leads to better employee retention and job satisfaction.
Equipment Replacement Scheduling
Footwear testing equipment's replacement schedule demands careful financial planning and strategic timing. You'll need to take into account that most testing equipment has a lifespan of 5-10 years before requiring major upgrades, while factoring in your maintenance costs that typically run between $2,000 to $20,000 monthly.
When planning your replacement schedule, take into account these key cost factors:
- Servo-hydraulic testing machine retrofits range from $15,000 to $25,000, while new machines can cost up to $500,000
- Electromechanical testing equipment retrofits cost $10,000 to $25,000, depending on motor reusability
- Specific shoe testing equipment sets vary from $1,380 to $15,000
You'll want to track your maintenance expenses, which typically account for 5-10% of your total operating budget. If you're running a smaller operation, purchasing new equipment might actually be more cost-effective than continuing maintenance on older machines.
Preventive maintenance can substantially extend your equipment's lifespan and reduce emergency repair costs. Your replacement schedule should balance these ongoing maintenance costs against the substantial investment required for new equipment, while considering your operation's size and testing volume.
Calibration Service Pricing Details
When evaluating calibration services for footwear testing equipment, you'll encounter a range of pricing structures that depend on equipment complexity and service requirements. Basic calibration services for standard testing equipment typically start at CHF 125, while more complex devices may cost up to CHF 325 for calibration.
Service Type | Standard Price | Express Option (+25%) |
---|---|---|
Basic Calibration | CHF 125 | CHF 156.25 |
Complex Equipment | CHF 325 | CHF 406.25 |
Hourly Adjustment | CHF 130 | CHF 162.50 |
Out-of-Tolerance Check | 90% of base price | N/A |
Additional Cleaning | Varies by device | +25% if expedited |
You'll need to factor in potential additional costs for adjustments, cleaning, or express services. If you require urgent calibration, you can opt for express service at a 25% premium. Be aware that if your equipment is found to be out of tolerance and can't be adjusted, you'll still be charged 90% of the calibration fee. For any additional work needed, expect to pay around CHF 130 per hour. Always get consent for extra services to avoid unexpected charges.
Volume Testing Equipment Selection
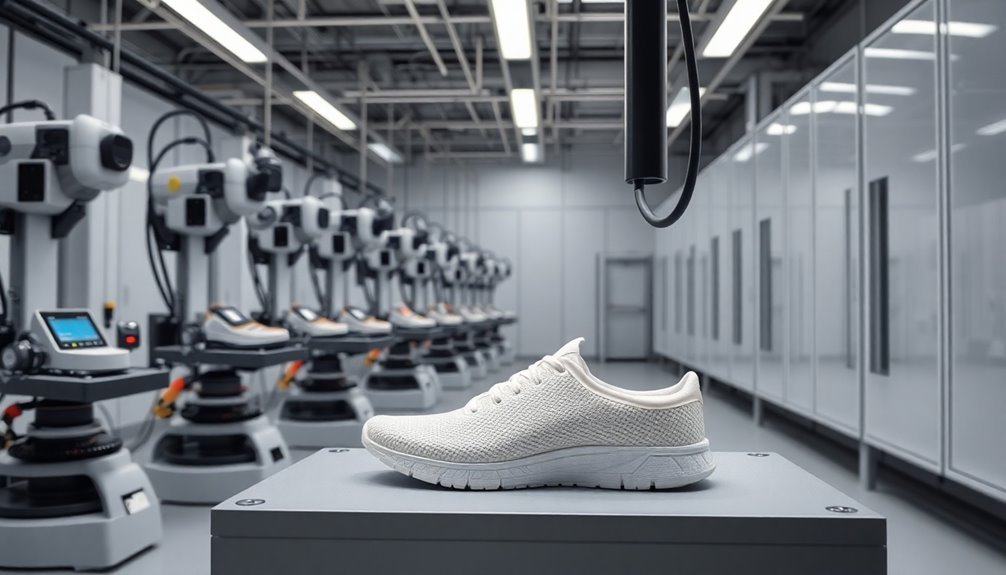
Selecting the right testing equipment requires careful consideration of both your testing needs and budget constraints. The investment range varies substantially, from around $2,000 for basic adhesion testing machines to $38,000 for advanced slip resistance and abrasion testing equipment.
When planning your equipment selection, you'll need to prioritize based on your most critical testing requirements. For essential footwear testing capabilities, consider these core testing categories:
- Tensile strength testing equipment ($1,800-$3,800) for material strength evaluation
- Sole adhesion testing machines ($2,000-$4,000) for bond strength assessment
- Slip resistance testers ($3,600-$38,000) for safety compliance verification
Your choice should align with industry standards relevant to your product lines. For instance, if you're primarily testing polymer-based soles, you'll need equipment that can verify the minimum 70 N/cm adhesion strength requirement.
Abrasion resistance testing equipment, while expensive ($15,000-$38,000), is vital for durability assessment and compliance with standards like SATRA TM362. Remember that each piece of equipment must meet specific testing parameters and industry standards, so don't compromise on quality just to save on initial costs.
Frequently Asked Questions
How Long Does It Typically Take to Train Staff on Footwear Testing Equipment?
You'll need about 2 days per training module, with thorough footwear testing programs typically requiring completion of 5-7 modules within two years. Hands-on equipment training is included in each module session.
Can Testing Equipment Be Rented Instead of Purchased for Short-Term Needs?
Yes, you can rent footwear testing equipment for short-term projects. It's cost-effective, offers well-maintained machinery, and includes calibration services. You'll also get technical support and flexible rental periods to match your needs.
What Warranty Coverage Is Standard for Most Footwear Testing Machines?
You'll typically get a 1-2 year standard warranty that covers parts and labor. Most manufacturers include technical support, calibration services, and repairs, but won't cover damage from misuse or unauthorized modifications.
Are There Government Incentives Available for Purchasing Footwear Testing Equipment?
Yes, you'll find tax credits, grants, and subsidies for testing equipment purchases, especially for R&D investments. You can claim deductions, access SME-specific funding, and benefit from reduced import duties when buying footwear testing machines.
How Often Should Testing Equipment Be Replaced to Maintain Optimal Performance?
You'll need to replace testing equipment based on usage intensity and type. Generally, plan for tensile machines every 1-2 years, slip testers every 500-1,000 tests, and impact/friction testers every 5-10 years.
In Summary
You'll find footwear testing equipment costs vary substantially based on your needs. Basic resistance testers start around $500, while extensive ESD testing systems can reach $15,000+. Don't forget to factor in annual calibration fees ($200-800) and maintenance costs. For most small to medium operations, you can expect to invest $2,000-5,000 in quality testing equipment that'll meet compliance standards.
Leave a Reply