You'll find these 3 proven maintenance schedules effective for protecting your workstations. Start with daily ESD checks – verify wrist straps, test continuous monitors, and remove non-essential insulators like coffee cups. Next, implement weekly surface testing using a megohmmeter to measure resistance and document findings. Finally, conduct monthly grounding system maintenance by inspecting connections, verifying continuity, and checking bonding points. These schedules work together to maintain ESD protection and prevent costly damage to sensitive equipment. The details of each schedule reveal even more ways to safeguard your workspace.
Daily ESD Workstation Checks
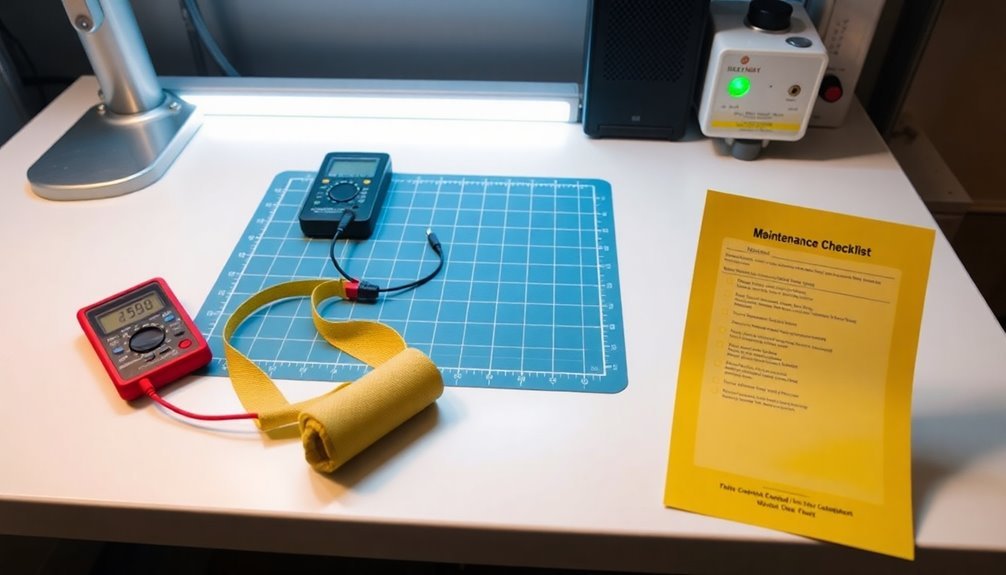
A workstation's daily ESD checks form the foundation of effective static control in electronic manufacturing environments.
You'll need to verify your wrist strap and footwear using a combo tester when entering the EPA, and document these results.
At your workstation, check that continuous monitors are functioning and grounding terminals are properly marked and operational.
Make sure your ionizers are correctly positioned and working, and verify that your floor maintains its dissipative properties.
You'll want to remove any non-essential insulators like coffee cups or radios that could generate static charges.
Your workbench should have a dissipative-grounded surface with common point grounds for wrist straps.
Don't forget to check that you're using ESD-compliant tools and that they're properly grounded.
All protective equipment, including worksurfaces, shelves, and chairs, must be dissipative and grounded.
You'll need to guarantee your ESD-sensitive components are stored in properly labeled, ESD-compliant packaging.
Remember to use your daily check forms to verify compliance and maintain documentation of all checks performed.
If you're working with untrained personnel, they must be escorted within the EPA at all times.
Clean all surfaces with approved ESD cleaners to maintain proper dissipative properties and prevent static buildup.
Weekly Surface Testing Protocol
Regular surface testing forms a crucial component of your ESD workstation maintenance routine. You'll need to conduct weekly inspections using a surface resistance megohmmeter to maintain your workstations' proper resistance to ground, preventing costly ESD damage to sensitive components.
To perform the test, connect your megohmmeter's sensing lead to equipment ground through a properly wired three-wire extension cord. Place a 5# electrode on the worksurface and measure the resistance to ground. Surface cleanliness is essential since surface finish conditions can significantly affect measurements. Your readings should fall below 10^7 ohms for general use, or below 10^6 ohms for high-risk applications.
If you encounter high resistance measurements, you'll need to troubleshoot each component separately. Check the surface material, ground cord, and snap connections individually by measuring both RTT and RTG values.
Document your findings and any corrective actions you take.
You should integrate these weekly tests into your overall maintenance schedule using a tracking tool. Don't forget to record all test results and adjust your testing frequency based on historical data and asset criticality. This systematic approach maintains that you'll catch potential issues before they impact your operations.
Monthly Grounding System Maintenance
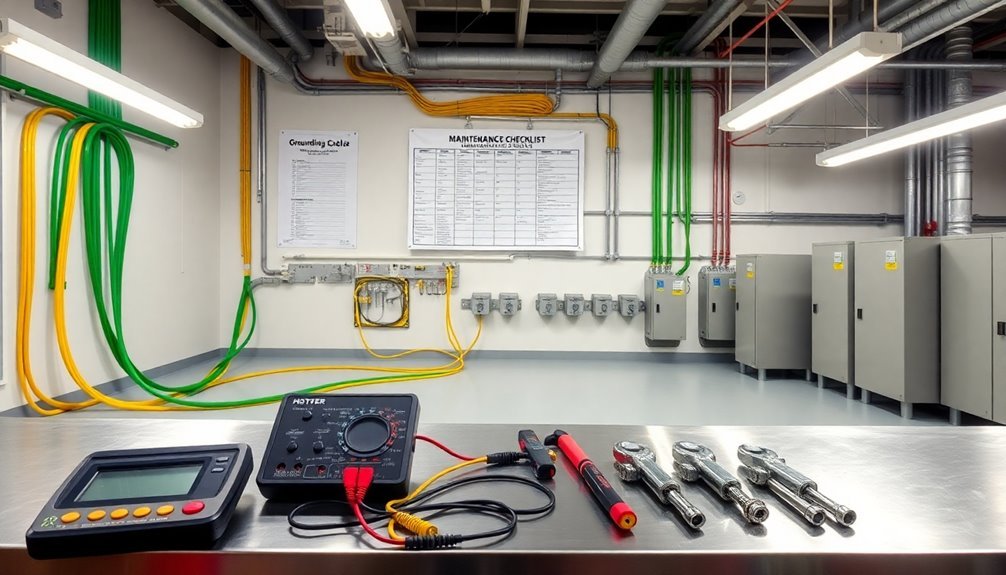
While daily ESD precautions protect your equipment, monthly grounding system maintenance guarantees long-term reliability of your workstation's protective measures. You'll need to perform visual inspections of all ground connections, checking for signs of corrosion, loose connections, or physical damage to conductors. Use a multimeter to verify continuity between your workstation's components and the main ground point. After major electrical storms or failures, make sure to conduct additional inspections to maintain safety standards.
Inspection Area | What to Check | Action Required |
---|---|---|
Ground Connections | Corrosion, damage | Clean or replace |
Conductor Lines | Continuity, wear | Test and repair |
Bonding Points | Tightness, oxidation | Retighten, clean |
Don't forget to measure resistance-to-ground using a 2-point test method, ensuring readings remain below 25 ohms. If you discover any values exceeding this threshold, you'll need immediate corrective action. Pay special attention to permanent bonds between metal masses and support structures, as these are essential for maintaining proper grounding integrity. Document all measurements and observations in your maintenance log, noting any repairs or replacements made. If you're not confident in performing these checks, it's best to schedule a qualified electrician for this monthly maintenance.
Frequently Asked Questions
How Often Should Maintenance Software Be Updated for Optimal Workstation Performance?
You'll need to update your maintenance software weekly, with critical patches applied immediately. Schedule automated updates on Sundays, and don't skip regular OS updates to maintain top-notch workstation security and performance.
What Temperature Range Is Ideal for Maintaining Esd-Sensitive Workstation Equipment?
You'll want to keep your ESD-sensitive workstation between 68° to 75°F (20° to 24°C) for maximum reliability. This range guarantees proper equipment function while minimizing the risk of electrostatic discharge events.
Can Multiple Maintenance Schedules Be Integrated Into a Single Tracking System?
Yes, you can integrate multiple maintenance schedules into a single tracking system using either centralized integration for unified control or decentralized integration with shared calendars to coordinate activities while maintaining team autonomy.
When Should Workstation Maintenance Schedules Be Reviewed for Potential Adjustments?
You should review your workstation maintenance schedules quarterly and after significant changes, like new equipment installations or recurring issues. Don't forget to analyze performance data and maintenance logs during reviews.
How Do Seasonal Changes Affect Workstation Maintenance Requirements and Scheduling?
You'll need to adjust your workstation maintenance based on seasonal humidity, temperature, and dust levels. You should increase cleaning frequency in summer and winter when HVAC usage peaks.
In Summary
By implementing these three maintenance schedules, you'll keep your ESD workstation running safely and efficiently. Make daily checks part of your routine, stick to weekly surface testing, and don't skip those monthly grounding inspections. Not only will you protect sensitive components from damage, but you'll also extend the life of your equipment and maintain compliance with safety standards.
Leave a Reply