You'll need specific warning labels for electrical equipment operating at 50 volts or higher when workers perform maintenance while energized. For static protection signs, you must display the ESD Susceptibility Symbol and guarantee labels are readable from three feet away with clear contrast between text and background. Place these signs in ESD-protected areas that meet ANSI/ESD S20.20 specifications for resistance measurements. Your labels should comply with NFPA 70E standards and use ANSI Z535 compliant headers, with proper voltage levels clearly marked. Understanding the complete requirements for ESD protection will help guarantee your facility's safety and compliance.
Voltage Thresholds for Warning Labels
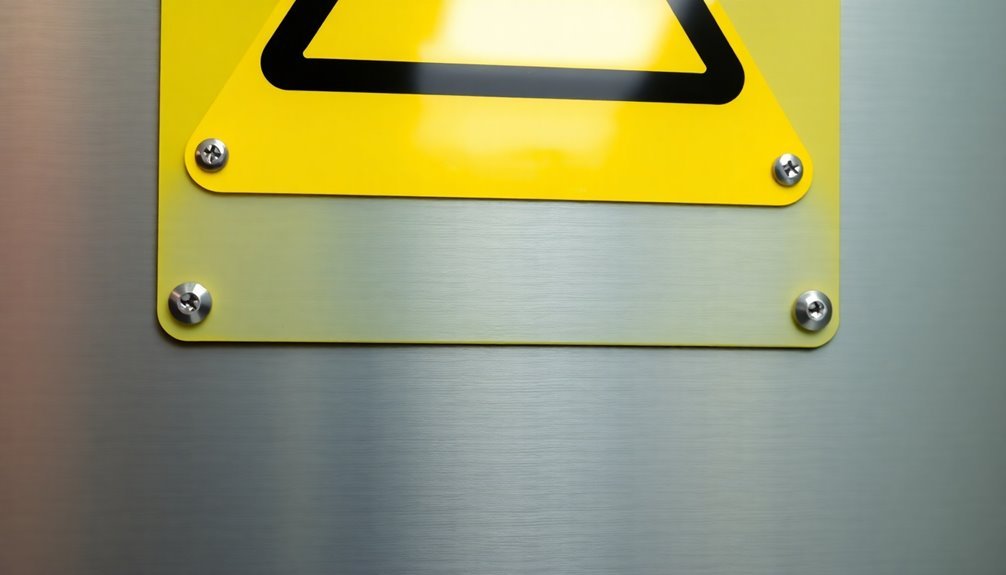
Warning labels must be applied to electrical equipment operating at 50 volts or higher when workers need to examine, adjust, service, or maintain it while energized. You'll find these labels on switchboards, transformers, and industrial control panels that remain powered during maintenance work.
The labels provide critical safety information to prevent electrical accidents and electrocution. For equipment handling sensitive electronic components, ESD Protected Areas must be clearly marked to prevent static discharge damage.
When you're working with electrical equipment, you'll notice that arc flash warning labels include specific details about incident energy, arc flash boundary, available fault current, and nominal voltage. This information helps you select the proper test instruments and personal protective equipment (PPE) for the job.
You'll need to pay attention to these labels to determine the level of PPE required for safe work.
You can use custom voltage labels for equipment operating at specific voltage levels above standard thresholds. These labels must clearly communicate hazardous voltage warnings to prevent electrical shock.
Whether you're dealing with standard or custom installations, the warning labels serve as your first line of defense against electrical hazards, ensuring you're aware of potential dangers before beginning any work.
ESD Protection Current Limits
In accordance with industry standards, ESD protection devices must handle specific current limits to safeguard sensitive electronic components. These devices are designed to manage current surges during electrostatic discharge events, with absolute maximum ratings defining the stress levels that can't be exceeded without causing permanent damage.
When you're designing ESD protection circuits, you'll need to focus on critical parameters like breakdown voltage and reverse stand-off voltage (VRWM). You should use reverse-biased diodes as shunt elements towards ground, ensuring proper current flow through protection circuits rather than sensitive components. TVS diodes act as short circuits during ESD surges while remaining open in normal operation.
To achieve this, you'll want to minimize impedance between protected IC pins and surge sources. Your ESD verification process must include checking maximum current density and point-to-point resistance along discharge paths.
Remember that ESD events typically induce currents ranging from 0.1 to 10 amps, lasting between 10^-6 to 10^-3 seconds. You'll need to place protection circuits close to IC pins and incorporate vias near inputs to efficiently drain current to ground.
Make sure your ground design maintains low impedance to effectively dissipate ESD energy throughout the system.
Static Protection Sign Requirements
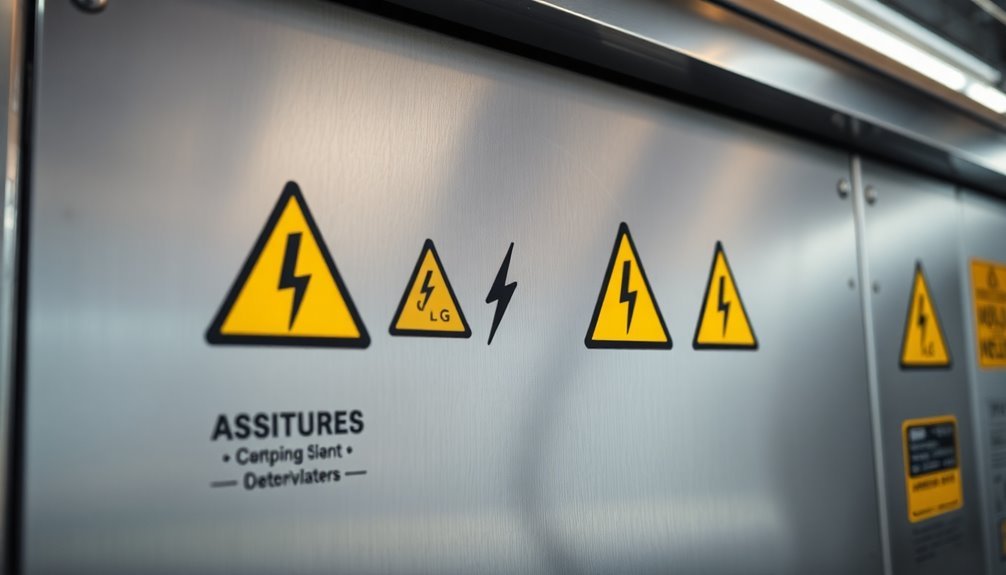
Protection Type | Symbol | Usage | Visibility | Standard |
---|---|---|---|---|
Shielding | S | Bags, containers | 3ft readable | ANSI/ESD S8.1 |
Field Protection | F | Equipment covers | Clear contrast | IEC 60417 6202 |
Conductive | C | Smocks, garments | High contrast | EN 61340-5-3 |
Dissipative | D | Sheet protectors | Bold marking | ANSI/ESD S20.20 |
General ESD | ESD Symbol | Warning signs | Yellow/Black | ANSI/ESD S8.1 |
When working with high voltages over 250 VAC, you'll need additional safety considerations. Your wrist straps must incorporate proper resistance values (1 Megohm) to limit current to less than 0.5 mA, and ionization may be necessary to neutralize electrostatic charges in these environments. The ESD Susceptibility Symbol must be clearly displayed on all sensitive devices and assemblies to ensure proper handling procedures are followed.
Arc Flash Boundary Standards
Safety standards for arc flash boundaries establish critical protection zones around electrical equipment. You'll need to understand that these boundaries mark the distance where incident energy equals 1.2 cal/cm², which can cause second-degree burns. Setting up temporary warning barricades is essential for restricting access to unqualified persons.
The National Fire Protection Association's 70E standard defines these requirements, which OSHA recognizes as a consensus standard.
You can calculate arc flash boundaries using several methods, including the NFPA 70E formula, IEEE 1584 empirical calculations, or specialized software programs. When you're determining these boundaries, you'll need to take into account voltage levels, fault current, and protective device clearing times.
Environmental factors like humidity, temperature, and altitude will also impact your calculations.
You must clearly mark these boundaries with appropriate signage that includes specific information: nominal system voltage, available incident energy, working distance, and required PPE category.
You'll need to implement barricades to alert workers of safe distances and safeguard that they're wearing proper PPE when working within the boundary.
Remember to recalculate these boundaries whenever you make system changes, as modifications can affect the arc flash risk zone.
High Voltage Safety Guidelines
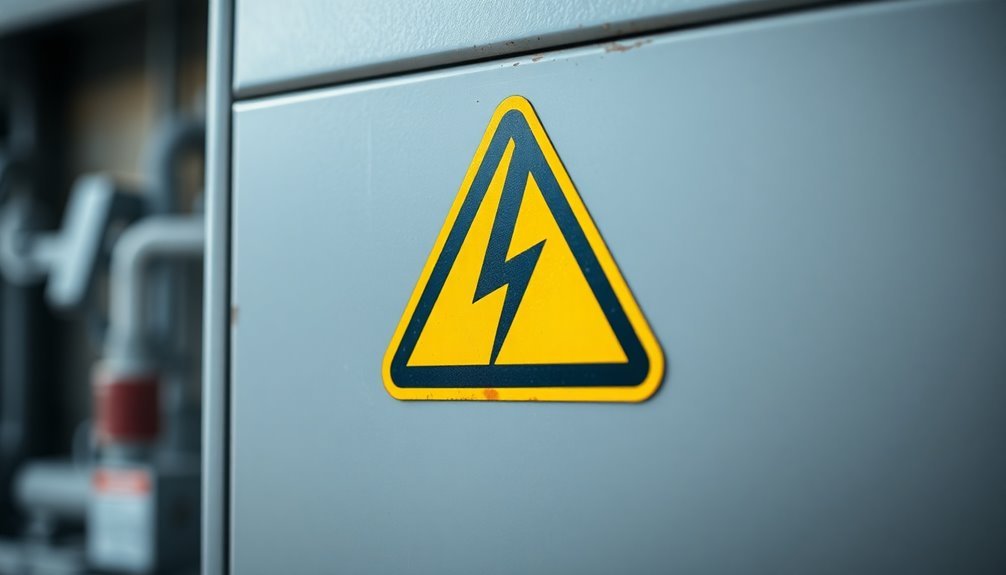
Building upon arc flash protection requirements, high voltage safety guidelines form a thorough framework for protecting workers from electrical hazards.
You'll need to follow strict protocols including proper training, use of PPE, and implementation of lockout/tagout procedures to guarantee your safety when working with high voltage equipment. Workers should never work alone and must maintain safe working distances at all times.
You must comply with OSHA regulations 29 CFR 1910.137 and NFPA 70E standards, which outline essential safety practices. Before starting any work, you're required to conduct electrical hazard analysis and establish emergency procedures.
When handling high voltage equipment, you'll need to use voltage testing equipment, checking it both before and after use.
Your workspace must display clear warning labels that meet standardized requirements. These labels should be heat-resistant, visible, and include hazard information in multiple languages.
You'll need to guarantee they're properly placed near high voltage equipment and in areas where workers might encounter electrical hazards.
ESD Control Equipment Specifications
ESD control equipment must meet strict current-limiting safety standards to protect both personnel and sensitive electronics.
Your resistance testing requirements for ESD control items should follow ANSI/ESD S20.20 specifications, including wrist strap systems under 3.5 x 10^7 ohms and footwear systems under 1.0 x 10^9 ohms.
When you're implementing these standards, regular verification of resistance measurements becomes essential for maintaining compliant ESD protection systems. Compliance verification plans need to be documented and followed according to established testing frequencies and procedures.
Current-Limiting Safety Standards
Current-limiting standards for ESD control equipment establish specific resistance and voltage requirements to protect sensitive electronic devices.
Safety signage with proper warning labels must be clearly displayed near all electrostatic discharge control equipment to prevent accidents and injuries.
You'll need to guarantee your wrist strap systems and static control garments maintain resistance levels below 3.5 x 10^7 ohms, while your flooring systems, seating, and mobile equipment shouldn't exceed 1.0 x 10^9 ohms.
For your soldering equipment, you must maintain tip-to-ground resistance of less than 10 ohms.
When using ionization equipment, you'll need to keep the offset voltage between -35 and 35 volts, with discharge times that meet your specific requirements. You should guarantee your air ionizers provide complete coverage of work surfaces where devices are exposed.
Your ESD control measures must account for device sensitivity levels, with Human Body Model (HBM) at 100 volts and Charged Device Model (CDM) at 200 volts as standard thresholds. If you're working with more sensitive devices, you'll need to implement stricter controls to meet reduced target levels of 1000 volts for HBM and 250 volts for CDM.
Remember to properly ground all conductive and dissipative materials in your Electrostatic Protected Areas through a common ground point.
Resistance Testing Requirements
When testing ESD control equipment, you'll need to follow specific resistance requirements that vary by component type.
For wrist straps, you must verify that the interior resistance measures 1.0 x 10^5 ohms and exterior resistance reaches 1.0 x 10^7 ohms, with the total system resistance not exceeding 3.5 x 10^7 ohms.
Footwear and seating share similar requirements, with both needing system resistance below 1.0 x 10^9 ohms.
For worksurfaces, you'll need to test both point-to-point and point-to-groundable point measurements, confirming they don't exceed 1.0 x 10^9 ohms.
When measuring metal parts, you'll need to verify resistance to ground is less than 2 ohms, while surfaces in contact with ESD-sensitive items should maintain resistance between 10^6 and 10^9 ohms.
For ionization testing, you'll need to check that the offset voltage stays within -35 to +35 volts, with discharge times meeting your facility's specific requirements.
All testing must comply with ANSI/ESD standards, including S1.1 for wrist straps and STM97.1 for footwear. You'll need to use appropriate meters and probes to guarantee accurate measurements of both resistance and potential.
Warning Label Placement Regulations
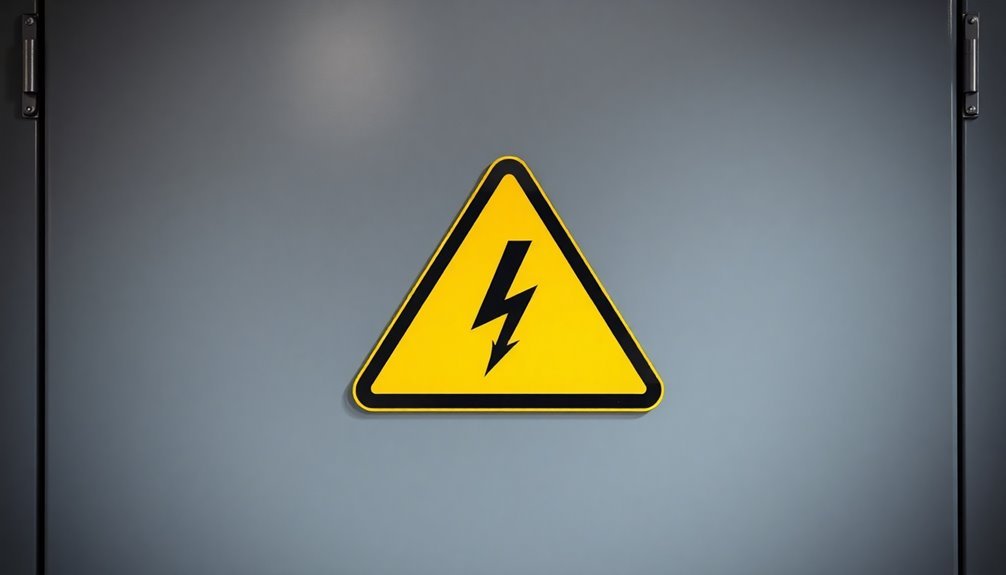
Warning label placement on packages follows strict regulatory guidelines to guarantee safety information is clearly visible and properly communicated. You'll need to verify all cautionary labeling appears in lines parallel to the package's base, except for specific containers like collapsible tubes or F-type containers.
When placing warning labels, you must position them within reasonable proximity to usage directions and group them in the same general area.
The principal display panel requires specific elements blocked together, including the signal word and hazard statements in capital letters.
For proper static protection labeling, follow these critical placement requirements:
- Position ESD caution labels so they're readable from three feet away
- Maintain clear contrast between lettering/symbols and the background
- Use black symbols on yellow backgrounds for maximum visibility
- Group cautionary statements together, separated by border lines or spaces
If you're placing cautionary material on panels other than the principal display, you must include a statement directing users to read these cautions carefully.
Remember that all warning text must be conspicuous and legible, with type size reasonably proportional to other printed content on the package or accompanying literature.
Frequently Asked Questions
How Often Should Warning Labels Be Inspected and Replaced?
You'll need to inspect warning labels annually and before each use. Replace them immediately if they're damaged or illegible. For equipment in harsh environments or with heavy usage, increase your inspection frequency accordingly.
Can Warning Labels Be Customized With Company Logos While Maintaining Compliance?
Yes, you can customize warning labels with your company's logo while maintaining compliance. Just make certain your logo doesn't interfere with required safety symbols, text, or color schemes specified by OSHA and ANSI standards.
What Temperature Ranges Can Warning Labels Withstand Before Deteriorating?
You'll find most warning labels can withstand temperatures from -80°C to +100°C (-112°F to 212°F), while specialized electrical labels endure up to 150°C (302°F). Weather-resistant versions handle -50°F to 250°F conditions.
Are Multilingual Warning Labels Required in International Manufacturing Facilities?
You'll find that multilingual warning labels aren't universally required, but they're strongly recommended for international facilities. EU regulations mandate local language labels, while U.S. standards like ANSI Z535 make them voluntary.
What Cleaning Solutions Are Safe to Use on Warning Labels?
You'll want to use mild soap and water or isopropyl alcohol for cleaning warning labels. Don't apply harsh solvents, abrasives, or acetone as they'll damage the label material and compromise readability.
In Summary
You'll need to stay compliant with voltage warning label requirements while implementing your static protection signage. Make sure you're following current ESD thresholds, maintaining proper arc flash boundaries, and placing warning labels at all required locations. Don't forget to regularly inspect your ESD control equipment and verify it meets safety specifications. Your facility's safety depends on strict adherence to these high voltage guidelines.
Leave a Reply