To maintain proper static control in your cleanroom, you'll need to follow key standards: ground all personnel with ESD wrist straps and conductive flooring, use ESD-safe materials for workstations and packaging, maintain humidity between 30-40% RH, install static-dissipative flooring with resistance of 1×10⁶ to 1×10⁹ ohms, implement continuous static monitoring systems, deploy air ionization equipment, design ESD-protected workspaces, establish proper handling procedures for sensitive components, and maintain rigorous testing protocols. Following these standards helps prevent costly product failures and contamination issues. Discover how these requirements work together to create your ideal controlled environment.
Personnel Grounding Requirements
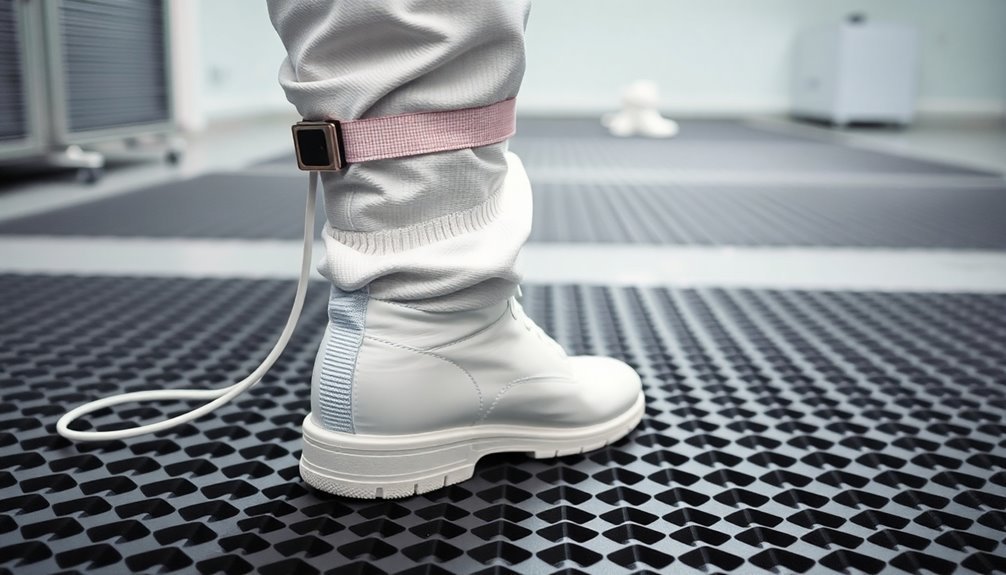
In accordance with industry standards, personnel grounding forms the cornerstone of static control in cleanroom environments. You'll need to implement thorough ESD protection measures to safeguard both your staff and sensitive equipment.
Your primary focus should be on connecting all personnel and equipment to a common ground point, which then links to a main grounding conductor. Continuous monitoring systems should be utilized to verify proper grounding connections at all times.
You must equip your team with ESD wrist straps that bond individuals to their workstations, paired with antistatic mats for complete workstation protection. When working at standing stations, you'll need to provide heel, toe, or boot straps to eliminate insulative barriers between feet and facility surfaces.
For enhanced protection, install conductive flooring combined with appropriate shoe grounders.
In high-sensitivity areas, you'll need to enforce strict gowning protocols, including full-body anti-static suits. You should limit personnel access and implement pre-planned work schedules to minimize entry and exit frequency.
Remember to maintain your grounding equipment regularly and verify its effectiveness through consistent testing. These measures aren't just recommendations – they're essential steps to prevent costly product failures and guarantee personnel safety in your cleanroom operation.
ESD-Safe Material Selection
Building upon proper personnel grounding practices, selecting the right ESD-safe materials forms the foundation of your cleanroom's static control strategy.
You'll need to focus on four key areas: flooring, workstations, packaging and storage, and clothing.
Your flooring should incorporate either conductive materials for rapid static dissipation or dissipative materials for gradual drainage. Both options must comply with ANSI/ESD S20.20 and IEC 61340 standards. Walking across untreated flooring can generate up to 35,000 volts of static electricity.
Similarly, your workstations require conductive or dissipative materials that integrate seamlessly with your overall ESD control system.
Don't overlook the importance of proper packaging and storage solutions. You'll want to use anti-static, conductive, or dissipative materials that meet both ESD control standards and cleanroom cleanliness requirements.
For clothing, select static-dissipative fabrics with continuous conducting threads that effectively minimize charge accumulation while maintaining cleanroom compatibility.
When selecting these materials, you must guarantee they work together as an all-encompassing system.
Each component should complement the others while meeting both ESD control standards and cleanroom specifications.
Environmental Humidity Control Standards
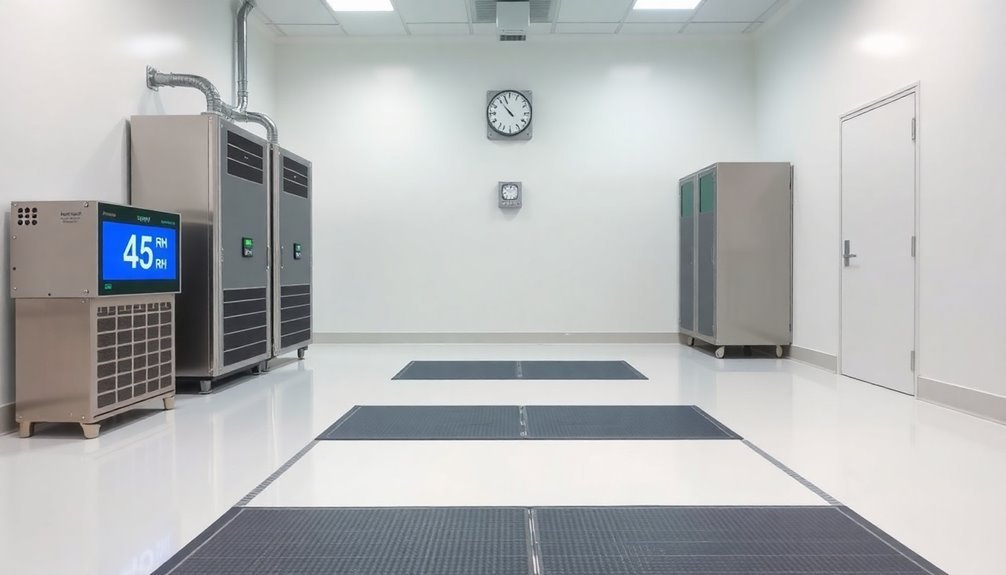
You'll need to maintain your cleanroom's relative humidity between 30% and 40% RH to effectively control static electricity and guarantee ideal operating conditions.
Your daily humidity monitoring should include regular checks throughout different zones of the cleanroom, particularly during shift changes and periods of high activity.
When working with sensitive electronic components or pharmaceuticals, you must guarantee your humidity control systems can consistently maintain these levels despite external weather changes and frequent personnel entries. Using double airlocks for entry helps minimize humidity fluctuations from frequent worker movement in and out of the cleanroom.
Optimal Humidity Range Requirements
Maintaining precise humidity control stands as one of the most critical requirements for cleanroom operations, with recommended ranges typically falling between 30-60% Relative Humidity (RH).
You'll need to keep your cleanroom's humidity levels carefully regulated, as excessive moisture can trigger bacteria growth and product degradation. High humidity also creates static electricity issues that can interfere with particle movement, while uncontrolled levels may cause powder feed clogging and tablet die inconsistencies in pharmaceutical manufacturing. Industry standards emphasize maintaining a narrow tolerance of ±2% RH when operating at temperatures below 70°F.
To achieve ideal control, you should implement specific strategies based on your cleanroom's classification. For ISO 5/Grade A spaces and CNC areas, you'll want to maintain 30-60% RH, while plant utilities rooms can operate at up to 80% RH. Raw materials warehouses offer more flexibility with a 20-80% RH range.
You can manage humidity through various methods, including desiccant systems capable of producing dew points below 0°F (-18°C) or air conditioning systems that dehumidify by lowering temperatures below the dew point.
Whatever system you choose, it's crucial to design it with minimal sensitivity to external environmental variables to maintain consistent control.
Daily Moisture Level Monitoring
Effective monitoring of daily moisture levels depends heavily on up-to-date sensor systems and automated controls that track humidity fluctuations in real time. You'll need to guarantee your cleanroom's HVAC system includes calibrated humidity sensors that communicate with automatic controls to maintain specific setpoints through dehumidification or steam injection processes. In semiconductor fabrication facilities, maintaining proper moisture levels is especially critical since variable humidity levels directly impact photolithography yield.
Monitoring Component | Required Action |
---|---|
Humidity Sensors | Daily calibration checks and response testing |
Control Systems | Regular maintenance and setpoint verification |
HVAC Equipment | Inspection of cooling coils and steam injectors |
You'll want to pay special attention to external factors that can impact your moisture control. These include the number of personnel entries and exits, which introduce additional humidity, and any potential leaks in the cleanroom envelope. It's essential to implement double airlocks and maintain a proper differential pressure to minimize moisture infiltration from outside sources.
To comply with regulatory standards like CGMP and ISO requirements, you must document all daily monitoring activities. Your moisture control strategy should integrate both air conditioning and desiccant systems when necessary, especially in facilities that require stringent ESD control measures or handle moisture-sensitive products.
Cleanroom Flooring Specifications
When you select cleanroom flooring, you'll need to meet specific material resistivity requirements of 1×10⁶ to 1×10⁹ ohms for effective static control.
Your installation must include proper grounding strips and conductive adhesives to maintain continuous electrical conductivity throughout the floor surface. The Gerfix TPS+ adhesive provides optimal conductivity for cleanroom installations.
You'll need to perform quarterly resistance testing and maintain certification records to guarantee your flooring system continues to meet ESD control standards.
Material Resistivity Requirements
Strict material resistivity requirements govern cleanroom flooring to prevent electrostatic discharge (ESD) and maintain contamination control.
You'll need to guarantee your flooring materials meet specific electrical resistance measurements, typically ranging between 1.0 x 10E6 and 1.0 x 10E9 ohms when tested using ANSI/ESD STM7.1 standards.
Understanding your flooring's resistance classification is vital:
- Conductive floors measure less than 1.0 x 10E6 ohms
- Static dissipative floors range from 1.0 x 10E6 to 1.0 x 10E9 ohms
- Resistance values above 1.0 x 10E9 ohms aren't recommended, despite ATIS 0600321 allowing up to 10E10 ohms
You'll need to account for environmental factors that can affect your flooring's electrical performance.
Temperature changes and relative humidity fluctuations can considerably impact resistance values, as can material aging over time. Proper installation requires copper grounding straps at a rate of one per 1000 square feet for effective static dissipation.
When selecting materials, focus on ESD rubber, vinyl, or epoxy options that consistently maintain their electrical properties while minimizing particle transfer and out-gassing.
Regular testing is essential to verify your flooring maintains its required resistance levels, guaranteeing continuous protection against static discharge in your cleanroom environment.
Installation Best Practices
Proper installation of cleanroom flooring demands meticulous attention to several critical factors.
You'll need to start with thorough floor preparation, guaranteeing the existing concrete is in good condition and all cracks or depressions are filled and leveled. Before applying your chosen ESD flooring material, you must spread a thin layer of adhesive uniformly across the sub-floor. The ideal electrical resistance range should measure between 1 x 10E5 and 1 x 10E8 ohms for optimal static control.
When installing your cleanroom flooring, you'll need to select materials that meet strict out-gassing requirements and particle control standards. Whether you're working with rubber, vinyl, or epoxy flooring, make certain it's compatible with your facility's ISO classification and electrical performance requirements.
Don't forget to verify that your chosen material works well with your cleanroom's footwear and humidity control systems.
After installation, you must seal all gaps and cracks thoroughly, applying a glossy finish that facilitates easy cleaning and contamination prevention.
You'll need to conduct post-installation ESD audits to confirm compliance with industry standards like ANSI/ESD S20.20 and IEC 61340.
Remember to document all installation procedures and maintain records of electrical performance testing for quality assurance purposes.
Testing and Certification
Before your cleanroom can become operational, you'll need to conduct thorough testing and certification of the flooring system to assure compliance with industry standards. Your flooring must meet specific ISO classifications and GMP requirements, particularly if you're working in pharmaceutical or medical manufacturing environments.
The testing process involves multiple critical evaluations to assure your flooring meets all necessary standards:
- ESD performance testing to verify proper static dissipation levels according to ANSI/ESD S20.20 and IEC 61340 guidelines
- Chemical resistance assessment to confirm the flooring can withstand regular exposure to cleaning agents and disinfectants
- FloorScore certification testing to validate indoor air quality and environmental sustainability metrics
You'll need to document all test results and maintain certification records for compliance purposes.
During testing, pay special attention to the flooring's particle generation rates, which must align with your cleanroom's ISO classification requirements.
Don't forget to verify that your flooring system's electrostatic dissipative properties remain consistent across the entire installation, as any gaps in performance could compromise your cleanroom's integrity and put sensitive electronics at risk.
Static Monitoring Equipment Protocols
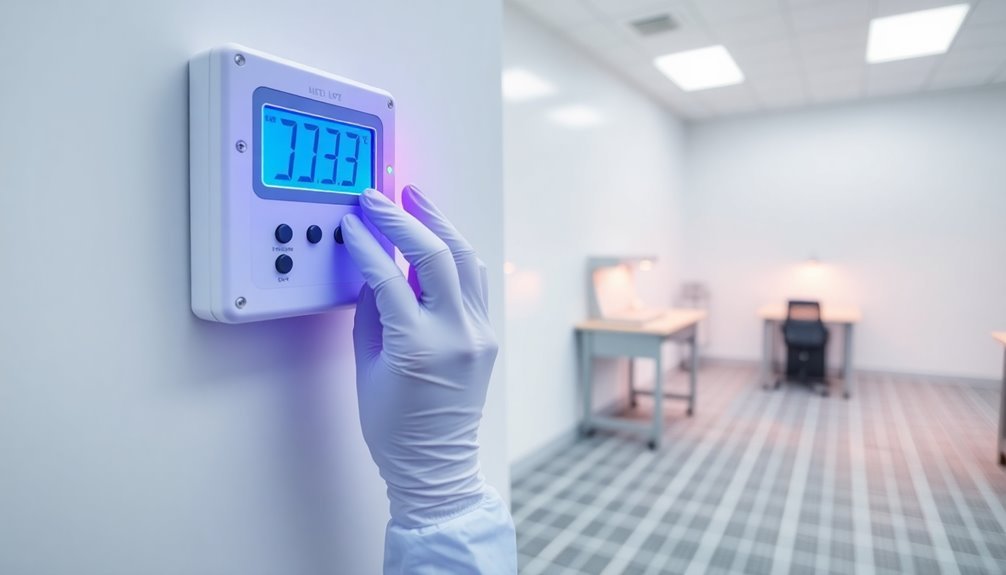
Regular monitoring protocols form the foundation of effective static control in cleanrooms.
You'll need to implement thorough static monitoring equipment to prevent electrostatic discharge that can damage sensitive devices and corrupt microprocessor-controlled applications. Start with anti-static flooring that's properly grounded, choosing between dissipative and conductive options based on your specific discharge risks.
You must ascertain your cleanroom's infrastructure includes grounded electrical conductors while eliminating insulators wherever possible.
When you can't avoid insulators, replace them with dissipative plastics and ascertain proper grounding. Don't use materials like Teflon, glass, or standard plastics that can hold static charges. Instead, install cleanroom-specific anti-static wall materials that control both static and particle shedding.
Your monitoring equipment should constantly assess static levels, particularly in areas with low relative humidity and HEPA filters, as these conditions can increase static-related contamination risks.
While you'll need to ground mobile objects and personnel, don't rely solely on wrist straps, as they're not practical for all mobile elements.
Design your airflow systems to transport potential contamination away from products before settling occurs.
Gowning and Clothing Regulations
Through strict adherence to gowning protocols, you'll protect the integrity of your cleanroom environment and prevent contamination.
Before entering the gowning room, you must remove all personal items, including jewelry, phones, and cosmetics. Your cleanroom attire should meet ISO 14644-5:2016 standards, using breathable, non-fragmentable materials that won't compromise the controlled environment.
Follow your facility's documented SOPs for proper gowning order, typically starting with shoe covers and progressing upward. You'll need to maintain strict separation between sterile and non-sterile surfaces throughout the process.
When donning your cleanroom garments, pay special attention to these critical steps:
- Use the no-touch hand-washing station and thoroughly dry your hands before handling any sterile items
- Apply shoe covers completely over your cleaned footwear, using two pairs in hazardous areas
- Don your cleanroom hood first, ensuring it's tucked properly into your coveralls
Remember to use the full-length mirror with visual instructions to verify proper gowning.
You'll need to regularly inspect your garments for wear and replace them according to your facility's maintenance schedule. Always document your compliance with gowning procedures as part of your quality control process.
Air Ionization System Requirements
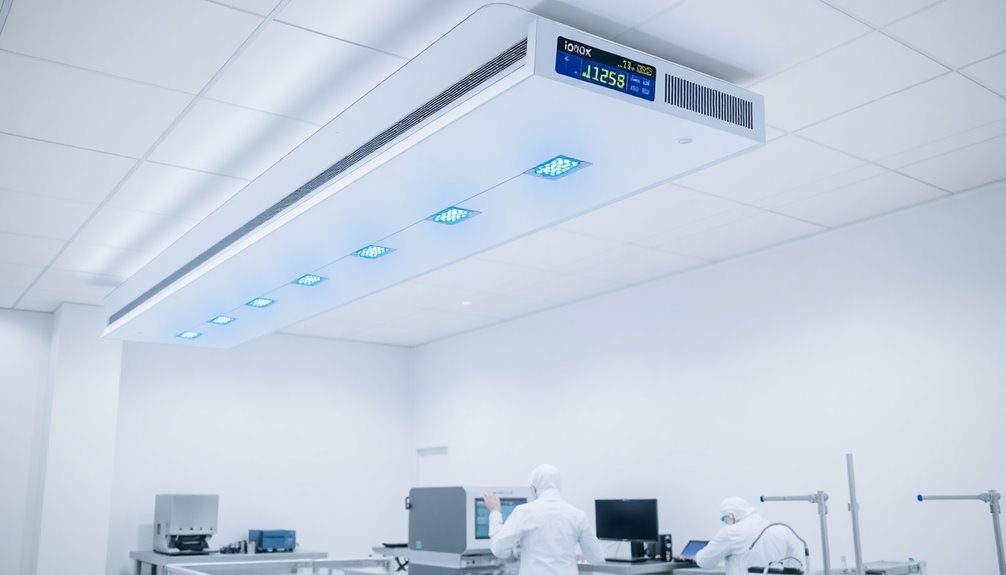
Maintaining effective static control in cleanrooms requires properly installed air ionization systems at critical points throughout your facility. You'll need to position ionizing blowers at street entrances to gown-up rooms and before clean room entrances. The systems should use pulsed DC technology to minimize ion recombination and maintain an ion balance of 0 ±5V.
System Component | Key Requirements | Benefits |
---|---|---|
Ceiling Emitters | Strategic placement | Uniform coverage |
Digital Controls | Modular design | Easy management |
Ion Shields | Fan output protection | Enhanced stability |
Your ionization system must deliver consistent performance through features like high ion density and fast neutralization capabilities. Modern systems like the CoreStat and Simco-Ion Guardian CR2000 offer digital control interfaces and advanced alarm notifications to help you maintain peak performance. You'll find that these systems require minimal maintenance, with some models offering up to 10-year warranties.
To guarantee GMP compliance and minimize contamination risks, you should regularly monitor system performance and maintain proper calibration schedules. The system you choose must be compatible with your cleanroom's cleaning agents and support your facility's ISO classification requirements.
ESD Workspace Design Guidelines
You'll need to start your ESD workspace design by establishing a proper grounding layout that connects all conductive elements to a single common ground point.
Position your equipment strategically to maintain unobstructed paths for personnel movement while ensuring all ESD-sensitive components remain within designated protected zones.
When selecting materials for your workspace, opt for static-dissipative surfaces, conductive flooring, and ESD-safe furniture that meets cleanroom standards and maintains effective static control.
Grounding Layout Best Practices
Effective ESD workspace design starts with an extensive grounding layout that connects all components to a common point ground.
You'll need to verify your worksurfaces maintain a resistance to ground between 1.0 x 10^6 and 1.0 x 10^9 for controlled static dissipation. Remember to clearly mark and separate ESD-sensitive areas from non-ESD activities to prevent accidental discharge events.
Your grounding layout must incorporate these critical elements:
- A common point ground that connects all workstation components and personnel equipment through properly rated conductors
- Continuous monitoring systems that provide real-time alerts for any grounding failures or disconnections
- ESD-safe materials throughout the workspace, including antistatic mats and appropriate static control products
When setting up your grounding system, you'll need to optimize the workspace layout for efficient workflow while maintaining proper static control.
Install clear signage to identify grounding points and static-controlled areas. Don't forget to implement ionization systems where necessary, especially when dealing with insulating materials.
Your grounding layout should support continuous monitoring capabilities, allowing you to quickly identify and address any potential grounding issues before they cause damage to sensitive components.
Equipment Positioning For Safety
Proper equipment positioning in an ESD workspace builds upon a solid grounding foundation to maximize both safety and efficiency. You'll need to arrange your components and tools in a logical sequence that minimizes unnecessary movement while maintaining easy access to frequently used items. Position your ESD-safe tools within arm's reach and guarantee they're connected to your common point ground.
Install air ionizers strategically around your workspace, particularly in areas where grounding isn't practical or when working with insulating materials. You'll want to place these devices so they effectively neutralize static charges without interfering with your work process. Position continuous monitoring devices where you can easily see their displays and respond quickly to any alerts.
Your workstation should incorporate static-dissipative flooring and include properly placed heel grounders for mobile staff.
Don't forget to set up your monitoring equipment to regularly test wrist straps and other grounding devices. You'll need to maintain clear paths for static dissipation and guarantee all equipment connections lead to your common ground point.
Remember to position your ionization systems to cover your entire work area effectively while keeping them clear of any obstacles that might reduce their effectiveness.
Material Selection Guidelines
Selecting appropriate materials for an ESD workspace requires careful consideration of every surface and component that might contact sensitive electronics. You'll need to guarantee your flooring, work surfaces, and storage solutions meet specific conductivity requirements to safely discharge static electricity.
Start with your workspace foundations by installing ESD-compliant flooring or mats with proper grounding snaps every 10 feet. Your work surfaces should maintain a resistance to ground between 1.0 x 10^6 and 1.0 x 10^9 ohms, using materials like static-dissipative rubber, vinyl, or laminate.
Key material requirements for your ESD workspace include:
- Protective clothing made from static-free materials that prevent contamination and static buildup
- Work surfaces with proper grounding connections to a common point ground
- Storage containers and packaging designed with conductive or dissipative materials
Don't forget to implement regular inspection routines for all ESD materials. Your flooring, work surfaces, clothing, and storage solutions need consistent maintenance to remain effective.
Guarantee all materials are properly grounded and connected to prevent static buildup that could damage sensitive components. When selecting materials, prioritize those that resist chemical and physical damage while maintaining their static-dissipative properties.
Static-Sensitive Component Handling Procedures
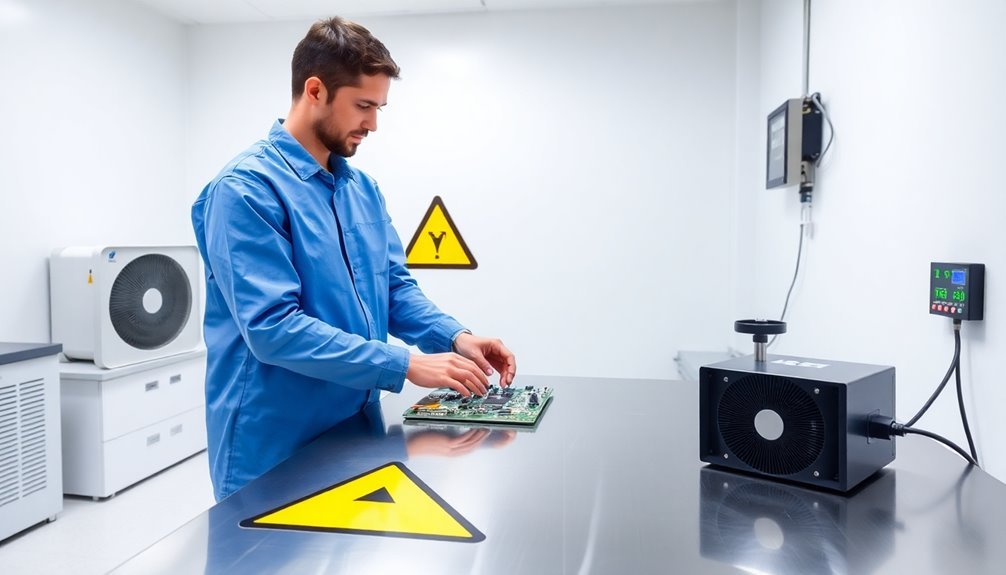
Carefully handling static-sensitive components requires an extensive set of procedures to prevent electrostatic discharge (ESD) damage.
You'll need to wear anti-static gloves and garments to prevent static transfer from your body to sensitive components. Always use a properly connected wrist strap to maintain grounding while handling components.
You must transport components in static-safe containers and use grounded carts when moving materials between locations.
Don't place components on standard surfaces – only use static-controlled surfaces that won't generate or transfer static charges. Keep your handling of sensitive components to a minimum, as each touch presents an opportunity for ESD damage.
Ensure your workstation meets ESD-safe requirements with proper grounding and ionization.
You'll need to work in an environment with controlled humidity levels and anti-static flooring. Use only ESD-safe tools designed for static-sensitive environments, and store components in static-controlled storage areas when not in use.
Remember that only personnel with proper ESD training should handle sensitive components. If you're entering a static-controlled area, you may need to use an air shower to remove any static charges from your person.
Documentation and Testing Standards
For cleanroom documentation, you'll need specialized paper products that meet strict quality and cleanliness standards. The paper must be made from high-quality cellulose that's been through a calendaring process to reduce fiber size and improve stability.
You'll find that coated papers with latex or synthetic materials help encapsulate particulates, while blue-colored paper makes it easy to identify compliant materials.
Your documentation must comply with ISO 14644-1 standards, which specify cleanliness levels based on particle counts per cubic meter of air.
When managing your cleanroom documentation, pay attention to these critical requirements:
- Package all materials in polybags with carton liners to prevent contamination from corrugated materials
- Test and certify products according to ISO 14644-3:2005 standards for as-built, at rest, and operational conditions
- Maintain regular cleaning procedures and monitoring protocols
You'll need to implement strict control measures, including proper gowning protocols and restrictions on static-prone clothing.
Using anti-static materials and equipment prevents electrostatic discharge, while controlling temperature, humidity, and airflow helps maintain ideal cleanroom conditions.
Remember to continuously monitor and document these parameters to guarantee compliance with cleanliness standards.
Frequently Asked Questions
How Often Should Ionizing Blowers Be Recalibrated for Optimal Static Control Performance?
You'll need to recalibrate your ionizing blowers every 6-12 months, but check performance monthly after installation. For critical cleanroom use, calibrate every 3 months to maintain ideal static control performance.
What Emergency Procedures Should Be Followed During an Esd-Related Equipment Malfunction?
You should immediately shut down the malfunctioning equipment, notify your team, evacuate the area, disconnect power if possible, and wear proper ESD-safe gear before attempting any repairs or assessments of the situation.
Can Wireless Devices Be Safely Used in Static-Controlled Cleanroom Areas?
You can safely use wireless devices in static-controlled cleanrooms if they're properly certified, have anti-static casings, and you follow strict guidelines like maintaining distance from sensitive equipment and using proper ESD protection.
How Do Seasonal Changes Affect Static Control Measures in Cleanroom Environments?
You'll need to adapt your static control measures as seasons change. In winter, you'll face increased static risks due to low humidity, while summer's air conditioning can create similar dry conditions requiring enhanced prevention.
What Are the Disposal Protocols for Contaminated Esd-Protective Equipment?
You'll need to segregate contaminated ESD equipment, store it in sealed containers with hazard labels, and follow OSHA guidelines. Document your disposal procedures and use certified hazmat teams when handling dangerous substances.
In Summary
You'll need to consistently monitor and maintain all these static control measures to keep your cleanroom operating safely and effectively. Make sure you're regularly testing your ESD equipment, training your personnel, and documenting all procedures. Don't forget to stay up-to-date with the latest industry standards, as static control requirements often evolve with new technologies and manufacturing processes.
Leave a Reply