Solid grounding systems provide the most reliable solution for your cleanroom's static control and equipment protection needs. You'll want to maintain a resistance of five ohms or less throughout your system, with copper straps placed every 1,000 square feet. Connect all conductive surfaces, including stainless steel components and ESD flooring, to a common ground point for ideal performance. Regular testing and monitoring guarantee your system stays compliant with industry standards like IEC 61340-5-1 and ANSI/ESD S20.20. While high-resistance grounding offers benefits in specific scenarios, solid grounding's simplicity and effectiveness make it the top choice for most cleanroom applications. Exploring the various installation methods and maintenance protocols will help you maximize your grounding system's performance.
Understanding Cleanroom Grounding Requirements
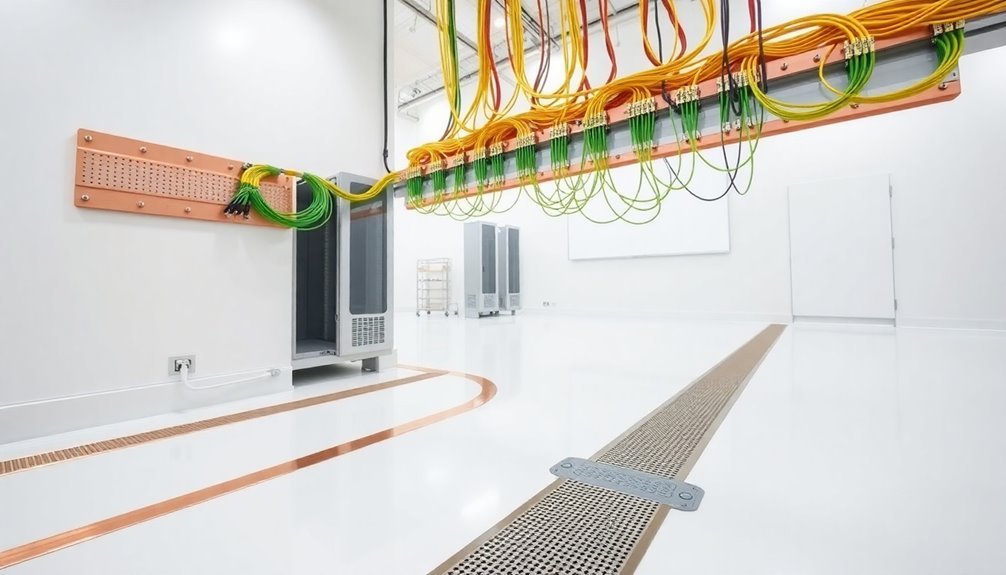
Three critical aspects define cleanroom grounding requirements: static charge prevention, personnel safety, and equipment protection.
You'll need to implement a thorough grounding system that addresses all these elements through a common ground point, which serves as the foundation for your cleanroom's safety infrastructure. Ground plug testers should be used to verify outlet integrity before installation.
To meet these requirements, you'll want to focus on establishing proper ESD (Electrostatic Discharge) flooring combined with conductive footwear. This combination creates an effective path for static discharge, protecting both personnel and sensitive equipment.
Your grounding system must maintain a resistance of five ohms or less to guarantee peak performance.
You'll need to ground all conductive surfaces, including stainless steel components, through copper grounding straps or rods. For every 1,000 square feet of ESD flooring, install at least one grounding strap, making sure each room has a minimum of one connection.
When setting up your grounding system, consider both personnel and equipment needs. This includes implementing wrist straps, ESD chairs, and conductive carts with ESD wheels.
Regular resistance measurements will help you verify your grounding system's effectiveness and maintain compliance with safety standards.
ESD Flooring Material Options
The selection of proper ESD flooring materials plays an essential role in maintaining cleanroom integrity and static control. You'll find three main options: conductive rubber, epoxy, and vinyl flooring, each with distinct characteristics.
Conductive rubber flooring stands out as the only Class-0 Qualified option, offering superior low body voltage generation. You'll appreciate its ergonomic benefits, including slip resistance and comfort underfoot. It's also easier to maintain and can be installed over existing surfaces. These installations must maintain system resistance below 3.5 X 10^7 ohms for optimal performance.
Conductive epoxy flooring excels in durability and chemical resistance, making it ideal for labs and manufacturing facilities. While it creates a seamless surface when installed, you'll need to take into account its challenging repair process and less ergonomic nature.
You'll want to approach conductive vinyl flooring with caution. Despite its lower cost, it generates more static than rubber or epoxy and can emit particles that compromise cleanroom environments.
When installing any ESD flooring, you must guarantee proper grounding. Connect the floor to an AC electrical outlet, earth ground, or steel columns using copper straps, with one strap required per 1000 square feet of flooring.
Ground System Types
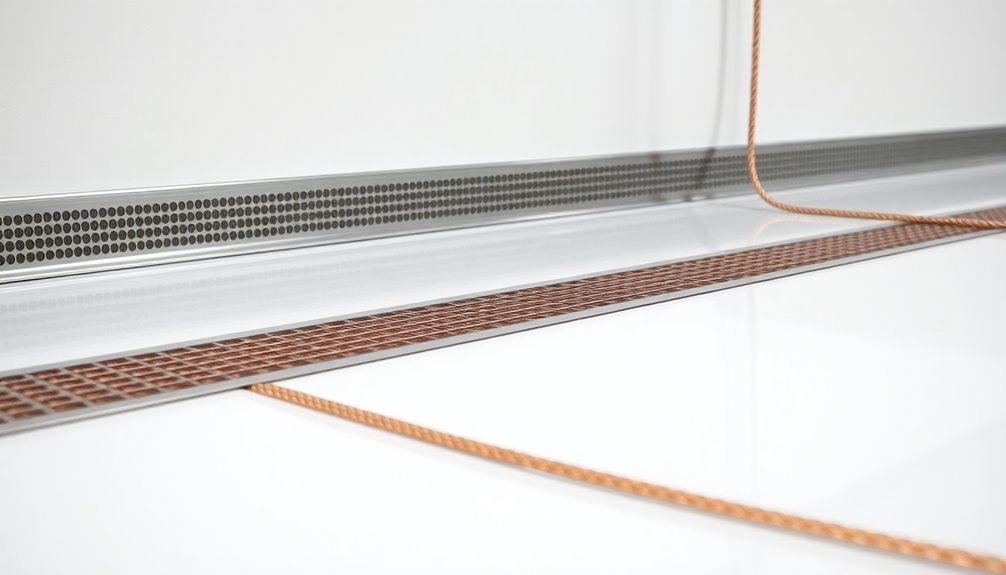
When you're selecting a grounding system for your cleanroom, you'll need to choose between solidly grounded systems that provide direct earth connections and high-resistance grounding (HRG) systems that limit fault currents.
Your choice affects both safety and equipment protection, as solid grounding offers better fault clearing while HRG systems reduce the risk of arc flash events.
Equipotential bonding further enhances safety by connecting all conductive surfaces to maintain equal electrical potential, preventing dangerous voltage differences between equipment and surfaces. Effective performance requires resistance to ground measurements to stay below 1.0 x 10^6 ohms.
Solid Vs HRG Systems
Selecting between solid and high resistance grounding (HRG) systems represents a critical decision for cleanroom facilities. While solid grounding provides a direct path to earth and maximizes safety through immediate fault current dissipation, HRG systems incorporate a resistor that limits fault currents to controlled levels. Each system offers distinct advantages for cleanroom environments.
1. Solid grounding excels in simplicity and maintenance, making it easier to implement and troubleshoot. The stick-built construction approach typically requires more robust grounding systems due to its metal-stud framing and integrated components.
You'll find it's particularly effective for ESD protection, meeting IEC 61340-5-1 and ANSI/ESD S20.20 standards while providing consistent voltage stability for sensitive equipment.
2. HRG systems shine in applications where you need to minimize downtime and control fault energy.
They're especially valuable in high-voltage distribution scenarios, reducing the risk of arc flashes and electrical discharges that could compromise cleanroom integrity.
3. Your choice between these systems often depends on your specific operational needs.
Solid grounding works best when you prioritize straightforward implementation and ESD compliance, while HRG systems prove superior when you're dealing with critical processes where fault current limitation is essential for continuous operation.
Equipotential Bonding Applications
Effective equipotential bonding applications serve as critical safeguards in cleanroom environments by eliminating voltage differences between conductive elements.
Current regulations require solid metal bonding in a radial configuration between all EBS elements.
You'll need to guarantee all metal components are connected to the protective PE conductor using properly sized conductors: 6 mm² for copper, 16 mm² for aluminum, or 50 mm² for steel. These connections must be accessible for inspection and should use bolted assemblies rather than soldering.
In your cleanroom's high-risk areas, you'll want to implement Additional Equipotential Bonding Systems (AEBS).
These systems require copper conductors with a minimum cross-sectional area of 10 mm² and must connect at least six components. When installing AEBS, you don't need to run protective conductors from every component to the distribution switchboard, but you must guarantee all external conductive parts are properly bonded.
Watch out for potential challenges, especially if you're replacing metal pipes with plastic ones, as this can disrupt existing electrical connections.
You'll need to verify your building has a suitable grounding system with separate PE and N conductors, or alternatively, implement a TN-C-S system where PEN splits into PE and N conductors at the main grounding bus.
Installation Best Practices
When you're installing cleanroom grounding systems, you'll need to place copper straps strategically at one strap per 1,000 square feet while ensuring proper contact with the building's ground points.
You must connect all equipment to these grounding points using approved connectors and maintain resistance levels below 5 ohms throughout the system. Regular monitoring helps maintain body voltage at 100V as per safety requirements.
After completing the installation, you'll need to verify the entire system through thorough testing, including resistance measurements and continuity checks at all connection points.
Copper Strap Placement Guidelines
In accordance with industry standards, proper installation of copper grounding straps requires careful attention to spacing and placement requirements.
You'll need to install one copper strap for every 1,000 square feet of ESD flooring, guaranteeing each room has at least one grounding point. When placing these straps, you'll want to create a 90-degree angle at the wall-floor junction, with at least 6 inches of the strap making direct contact with the floor surface.
For ideal grounding performance, follow these essential placement guidelines:
- Attach straps to approved connection points such as electrical outlets, building steel, or dedicated grounding bars – remember to remove the center screw and grounding screw when connecting to outlets.
- Cover the strap with conductive adhesive and new flooring material to maintain electrical continuity while protecting the installation.
- Test the connection using a volt-ohm meter to verify proper grounding before completing the installation.
When selecting attachment points, you'll find several viable options, including structural I-beams, aluminum studs, and copper bus bars. The conductive pressure-sensitive adhesive creates a reliable electrical pathway between the flooring tiles and grounding system.
Remember to clean all connection surfaces thoroughly and remove any non-conductive coatings to guarantee reliable electrical contact.
Equipment Connection Standards
Proper equipment connection standards serve as the foundation for a reliable cleanroom grounding system. You'll need to verify all your equipment meets the resistance specification of less than 1.0 x 10^9 ohms when measured from the equipment through personnel and flooring. It's crucial to implement common point grounding, connecting all your ESD protective materials to the same electrical potential. Additionally, surge protection devices require proper grounding for effective operation against electrical spikes and transients.
Connection Type | Method | Purpose |
---|---|---|
Primary Ground | Equipment grounding conductor | Creates main path for static dissipation |
Auxiliary Ground | Bonding to water pipes/building frame | Minimizes potential differences |
Structural Ground | Copper straps to support columns | Provides direct building connection |
Equipment Ground | Direct connection to ground point | Maintains equipotential balance |
Common Point Ground | Copper bus bars | Centralizes grounding connections |
When installing your equipment connections, you'll need to follow ANSI/ESD S6.1 and ESD TR20.20 standards. Connect your instruments' DC sides to the electrical safety ground, and implement a two-step grounding solution that links equipment to a common ground point before connecting to the main grounding conductor. Don't forget to regularly test these connections using the fall of potential method to maintain compliance.
Testing After Setup
Testing your cleanroom grounding system after installation guarantees long-term reliability and safety.
You'll need to conduct extensive testing procedures using a volt ohm meter (VOM) to verify that all connections meet industry standards, particularly the 5-ohm threshold for industrial systems.
It's essential to perform continuity checks between grounding straps and electrical grounds while documenting all results for future reference.
1. Start by testing all copper grounding straps connected to structural elements, ensuring they're properly secured to beams and columns.
You'll want to verify that each connection point maintains consistent electrical continuity.
2. Next, examine your earth bonding plugs and copper bus bars, confirming they're providing secure ground connections.
These components serve as significant junction points in your cleanroom's grounding network.
3. Finally, establish a regular testing schedule to monitor your grounding system's performance over time.
You should conduct periodic resistance measurements and maintain detailed records of all testing activities.
Remember to train your personnel on proper testing procedures and system maintenance.
They'll need to understand how to identify potential issues and when to schedule necessary upgrades or repairs to maintain ideal grounding system performance.
Performance Testing and Verification
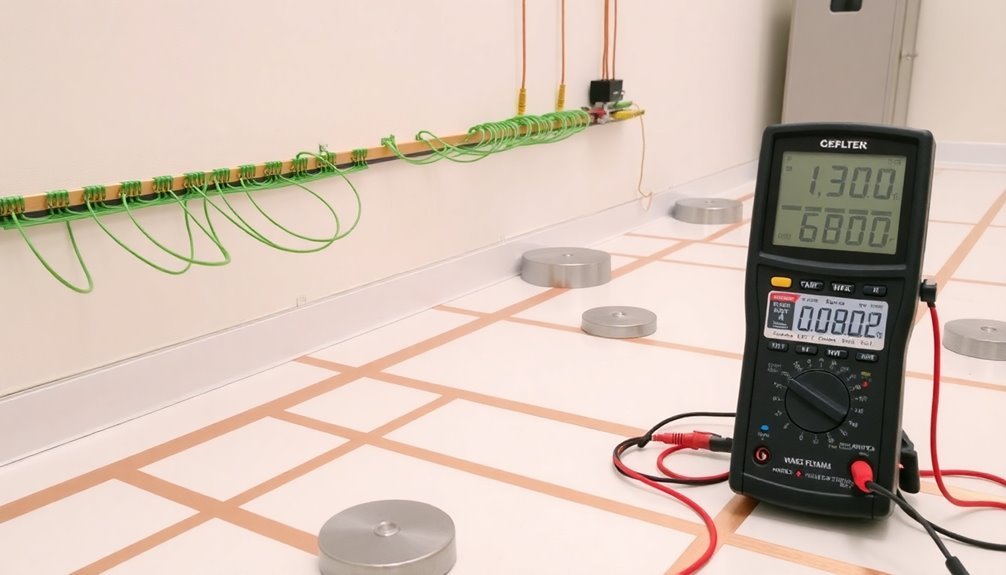
Through thorough testing and verification, cleanroom grounding systems maintain their vital performance standards. You'll need to conduct initial resistance measurements when you first install the electrode and continue testing at regular intervals to guarantee the resistance-to-ground doesn't increase over time.
You can employ two primary testing methods for your cleanroom's grounding system. The 3-Point Fall-of-Potential Method requires complete isolation from power and involves placing probes at specific distances based on your system's diagonal length.
If you need to test while power's running, you'll want to use the Induced Frequency Testing method, which utilizes a special transformer to measure both system resistance and utility neutral grounding impedance.
To maintain peak performance, you'll want to implement continuous monitoring with high-input noise filtration and remote communications capabilities. Your monitoring system should focus on key metrics like resistance and conductivity, which are essential indicators of your system's effectiveness.
Don't forget that environmental factors such as temperature, humidity, and soil conditions can affect your grounding system's performance, so you'll need to account for these variables in your testing protocols.
Maintenance and Safety Protocols
While testing validates your grounding system's performance, maintaining it requires a well-structured set of protocols. You'll need to implement regular inspections of all electrical systems and equipment, guaranteeing they remain properly certified and grounded. This includes checking your Master Ground Bar connections and verifying that all indoor cabinets housing radio and microwave equipment maintain direct ground connectivity.
Your maintenance protocol should focus on three critical areas:
- Regular calibration and maintenance of all grounding equipment, including wrist straps, antistatic work mats, and earth bonding plugs, following manufacturer guidelines strictly.
- Continuous monitoring of environmental conditions through real-time assessment systems that track particle counts, temperature, humidity, and pressure differentials.
- Systematic inspection of static-dissipative flooring and ionization systems to confirm they're functioning effectively for static charge dissipation.
You must also maintain thorough contamination control plans that outline specific maintenance procedures and schedules.
Keep detailed records of all inspections, calibrations, and maintenance activities. When you detect any irregularities in your grounding system's performance, address them immediately to prevent potential ESD risks and maintain cleanroom integrity.
Frequently Asked Questions
How Often Should Copper Grounding Straps Be Replaced in Cleanroom Environments?
You should replace copper grounding straps annually during visual inspections, or immediately if you notice damage or corrosion. Don't wait longer than 5 years, even if they appear fine during regular checks.
Can Multiple Cleanroom Grounding Systems Be Integrated Into One Facility?
Yes, you can integrate multiple grounding systems in one facility. You'll need to verify they're all connected to the same electrical ground and establish a Common Point Ground for effective equipotential bonding.
What Happens if Cleanroom Grounding Systems Fail During Critical Operations?
If your cleanroom's grounding system fails during critical operations, you'll face immediate risks of ESD damage to products, equipment malfunctions, potential safety hazards to personnel, and serious compliance violations that could halt operations.
Do Different Cleanroom Classifications Require Different Grounding System Configurations?
Yes, you'll need different grounding configurations based on your cleanroom class. ISO 5 and higher require stricter ESD controls like dissipative flooring and walls, while ISO 7 and lower can use basic grounding techniques.
How Do Seasonal Temperature Changes Affect Cleanroom Grounding System Performance?
Seasonal temperature changes can affect your cleanroom's grounding performance by altering humidity levels and material conductivity. You'll need to monitor and adjust your system regularly to maintain consistent grounding effectiveness throughout the year.
In Summary
You'll find that proper grounding systems are essential for your cleanroom's effectiveness and safety. Choose ESD flooring materials that match your specific needs, implement an extensive grounding network, and maintain regular testing protocols. Don't forget to train your staff on safety procedures and conduct periodic system evaluations. When you follow these guidelines, you'll guarantee ideal static control and protect your sensitive operations.
Leave a Reply