When packaging computer components, you'll need to prioritize both physical and electrostatic protection. Start by selecting anti-static foam with proper surface resistance (10^6 to 10^9 ohms) and use double-boxing techniques for extra security. Layer different foam types strategically, with polyurethane for sensitive parts and polyethylene for heavier items. Pack each component individually using custom-cut foam inserts, and consider the specific weight and size requirements. Don't forget to fill empty spaces with supplemental cushioning, and always secure corners with foam inserts. Before shipping, test your package thoroughly to confirm it can withstand typical transit conditions. These fundamentals are just the beginning of mastering safe component packaging.
Choose Anti-Static Foam Materials
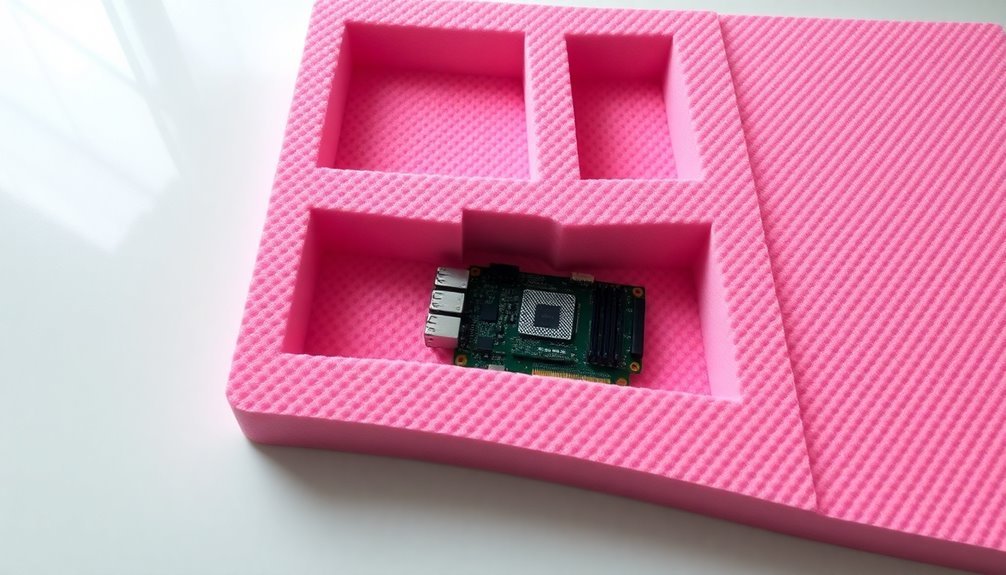
Protecting your computer components starts with selecting the right anti-static foam materials. You'll need to understand the different types available to make an informed choice for your specific needs.
Conductive foam offers the highest level of protection by creating a Faraday cage around your components, while standard anti-static foam prevents static build-up but doesn't provide complete protection against static transfer. Anti-static PE foam provides excellent protection with its closed-cell structure and optimal density range.
When selecting foam materials, you'll want to check the surface resistance values. Conductive foam typically ranges from 10^3 to 10^5 ohms, while black anti-static foam measures between 10^6 and 10^9 ohms.
For delicate components, consider using eggcrate foam or custom-cut foam inserts that provide additional cushioning while maintaining anti-static properties.
Don't reuse anti-static foam, as it can lose its protective qualities over time. You'll find various custom options available, including convoluted foam and foam pouches that can be tailored to fit specific component shapes.
When sourcing your materials, work with reputable suppliers who use high-quality raw materials and can provide professional guidance for your particular packaging needs. This guarantees you're getting reliable protection for your valuable computer components.
Master Double-Boxing Protection Methods
When double-boxing your computer components, you'll need to maintain a consistent space cushion between your inner and outer boxes using foam materials.
Start by securing your components in the inner box with foam padding, ensuring it's completely sealed before placing it inside the larger container.
Fill all empty gaps between the boxes with proper foam inserts to prevent shifting during transit, paying special attention to corners and edges where impact often occurs. Similar to how KVM switches allow secure connections between multiple computers, using proper double-boxing methods ensures safe transport of sensitive hardware.
Space Cushion Between Boxes
Through proper double-boxing techniques, you'll need to create adequate space cushioning between your inner and outer boxes to safeguard computer components during transit. Place an outer box that's large enough to accommodate your inner box while leaving sufficient room for protective cushioning on all sides.
The custom expanding foam machine can fill bags precisely to create perfect cushioning around components. Place anti-static polyurethane, polyethylene, or expanded polystyrene foam inserts strategically between the boxes. You'll want to guarantee even distribution of these cushioning materials to maintain consistent protection throughout.
Install foam corner inserts in the outer box to prevent shifting and protect against corner damage during handling.
When selecting your foam materials, consider using convoluted (egg crate) foam inserts to better control product movement and absorb impacts. You'll need to customize your foam thickness based on your components' specific needs and fragility. Remember to perform vibration assessments to determine the best foam thickness and placement between boxes.
Always seal your outer box tightly to keep the foam cushions firmly in place. Document your packaging process with photographs from multiple angles, and maintain consistent temperature conditions while packing to guarantee proper foam expansion and performance.
Secure Inner Box First
Building on proper space cushioning principles, your inner box serves as the first line of defense for computer components. You'll need to carefully position foam packaging pieces on both ends of the computer chassis, ensuring the thicker side aligns with the vent/filter unit. Make sure the foam's notch lines up perfectly with the side panel vent. The packaging's vibration dampening properties help protect sensitive electronic components during transit.
When securing your components, use custom die-cut foam inserts for essential protection. These inserts eliminate gaps and prevent movement during transit. Slide the inner box over your system, checking that it fits squarely on both chassis ends before sealing it securely with tape.
Component | Protection Method | Key Consideration |
---|---|---|
Chassis | Anti-static foam | Thicker side at vent |
Side Panel | Notched foam | Align with vent |
Overall System | Custom inserts | Fill all gaps |
Before proceeding to the outer box, verify that your inner packaging is tight and secure. Don't forget to place your computer in a plastic shipping bag first to prevent scratches. This initial layer of protection is vital for maintaining your component's integrity throughout the shipping process, making the subsequent double-boxing steps even more effective.
Fill Empty Gaps Properly
To master double-boxing protection, you'll need to eliminate all empty spaces between your computer components and packaging materials. Empty gaps allow components to shift during transit, potentially causing severe damage to your valuable hardware.
Using appropriate materials like polyurethane expanding foam, convoluted foam inserts, and anti-static bubble wrap guarantees maximum protection while preventing static electricity damage. The specialized cellular structure of polyurethane foam delivers superior cushioning while maintaining firmness.
- Choose polyurethane expanding foam to secure heavy components like GPUs and coolers, creating a custom-fit barrier that prevents movement.
- Wrap individual components with anti-static materials before placing them in custom die-cut foam inserts that match your box dimensions.
- Fill remaining gaps with convoluted foam, which quickly recovers its shape after impact and provides consistent protection.
- Add towels or packing paper as supplemental cushioning to eliminate any remaining void spaces.
For the best protection, combine these gap-filling techniques with double-boxing methods. Place your properly packed inner box inside a larger outer box with additional cushioning material between them.
This creates an effective shock zone that absorbs impacts and vibrations during shipping, substantially reducing the risk of damage to your computer components.
Layer Different Foam Types
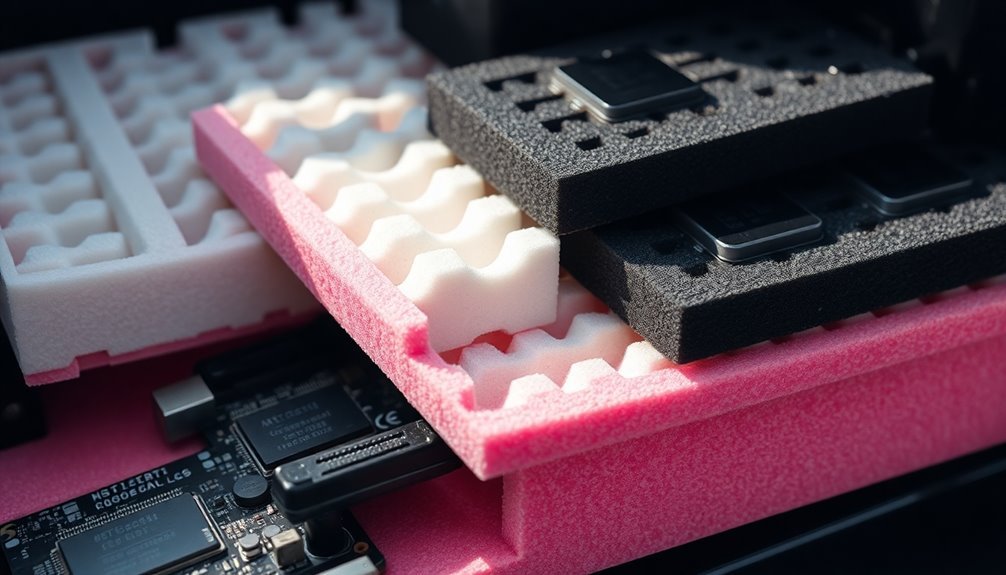
Layering multiple foam types sets up a robust defense system for your computer components. You'll want to start with a base layer of polyurethane foam for sensitive parts, as it's soft and lightweight.
For heavier components, opt for cross-linked polyethylene foam, which won't deform under pressure and offers superior durability. The non-abrasive properties ensure your components remain scratch-free during transit.
When you're dealing with static-sensitive parts, always incorporate ESD foam that meets EIA-541 standards. Place this anti-static layer directly against your components to dissipate any harmful electrostatic charges.
You should combine open-cell and closed-cell foams to achieve balanced protection against both impacts and vibrations.
Choose your foam densities carefully – use lower density polyurethane (2 lb./ft3) for smaller parts and higher density polyethylene (4 lb./ft3) for larger components.
Don't forget to think about each foam's cushioning curve when layering. For maximum protection, you'll want to custom mold or precisely cut the foam to match your component's exact shape.
Remember that proper PSI matching between the foam and your component's weight is vital for the best protection.
If moisture's a concern, include a layer of expanded polyethylene foam, which offers excellent water resistance.
Pack Components Individually
You'll want to wrap each computer component separately using anti-static materials and secure any loose parts before placing them in foam enclosures.
Maintaining adequate space between components prevents friction and potential damage during transit, while ensuring each part has its own cushioned compartment.
For maximum protection, customize your foam packaging by cutting precise slots that match the exact dimensions of your specific hardware components.
Static electricity can be minimized by avoiding carpeted work surfaces when packing components.
Proper Component Wrapping Techniques
Three essential steps form the foundation of protecting computer components during packaging: wrapping the tower, securing the monitor, and organizing accessories. When packing your computer, you'll want to follow these critical steps to guarantee maximum protection during transport.
- Start by wrapping your computer tower in a soft towel or packing paper, followed by anti-static bubble wrap to prevent static buildup. Place it upright in a sturdy box and fill empty spaces with crumpled paper. Line the box bottom with additional bubble wrap for enhanced protection.
- Protect your monitor by focusing on the screen's safety. Wrap it in a towel, then add anti-static bubble wrap before placing it in a separate box.
- Carefully detach all cables, unscrewing connectors where necessary. Label them with masking tape for easy identification.
- Package peripherals individually using paper and bubble wrap.
When wrapping each component, make sure you're using proper materials like anti-static bubble wrap and sturdy boxes. Don't allow direct contact between components and box walls – always use padding as a buffer.
Secure all box seams with packing tape, and label each package clearly. This systematic approach will help prevent damage during transit and make reassembly much easier at your destination.
Space Between Parts Essential
Maintaining proper spacing between computer components during packaging consistently proves critical for preventing damage during transit. You'll need to guarantee each part has adequate clearance from others, with a minimum of 10mm between through-hole components and transmission edges, and 5mm from non-transmission edges.
When designing your foam inserts, follow the standard clearance guidelines of 125 mil spacing for top-side PCB components and 300 mil for secondary-side components. Don't forget to maintain at least 8 mil between parts and hole walls, along with 7 mil spacing from annular rings to guarantee proper soldering and assembly quality.
For maximum protection, you'll want to use foam-in-place packaging or precisely cut foam inserts that maintain uniform spacing. Work with structural engineers to design inserts that perfectly match your box dimensions and component configurations.
Secure each component individually within its designated space, using foam corners in outer boxes to prevent movement. Always verify your spacing measurements against component-specific guidelines, and maintain consistent orientation throughout the packaging process.
This attention to proper spacing will substantially reduce the risk of damage during handling and shipping.
Customize Foam For Each
Every computer component requires individualized foam packaging to guarantee maximum protection during transit. When you're designing custom foam inserts for computer parts, you'll need to evaluate the specific shape, weight, and sensitivity of each component.
Using materials like anti-static polyethylene or ESD foam prevents damage from static electricity, while ensuring each part stays firmly in place during shipping.
- Select polyurethane foam for lighter components like RAM sticks and SSDs, as it provides excellent cushioning while remaining lightweight
- Choose ESD foam for sensitive electronic components to protect against static discharge that could damage circuitry
- Use closed-cell polyethylene foam for heavier items like power supplies and graphics cards to prevent moisture damage
- Implement convoluted foam designs for items with irregular shapes, ensuring complete surface contact
Start by evaluating each component's requirements and create precise cutouts using CAD software for accuracy. You'll want to test your prototype designs for shock absorption and compression resistance before finalizing the packaging.
Remember that proper spacing between components is vital, so design your foam inserts with adequate separation to prevent contact during transit.
Consider Component Size and Weight
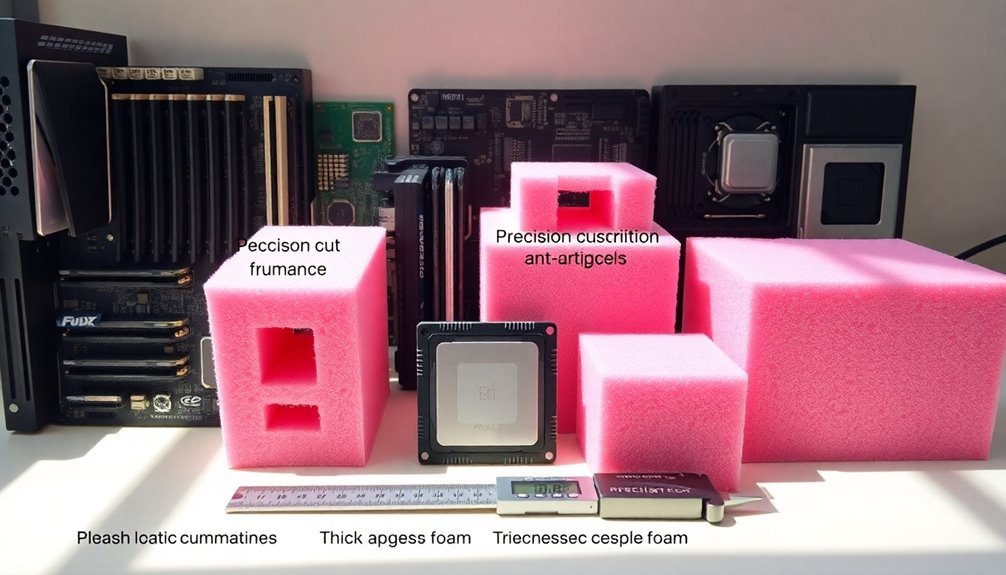
Determining your computer component's size and weight is crucial for selecting the right foam packaging. You'll need to calculate the volume by multiplying length, width, and height, then dividing by 1728 to get cubic feet. Remember to account for any cavities in your components and multiply by the number of parts you're packaging.
When considering PSI (pounds per square inch), position your components on their largest, flattest sides to distribute weight evenly. This reduces the risk of damage during drops and makes handling safer. Calculate PSI by dividing the weight by the surface area of each side to help you choose appropriate foam density.
You'll want to select foam thickness and density based on cushioning curves specific to your components. Don't assume that thicker or denser foam is always better – it could actually damage delicate parts. Instead, use at least three inches of appropriate cushioning material around your items.
Consider foam-in-place, corner pads, or custom foam inserts that precisely fit your components. Avoid using paper-based materials for cushioning, and make certain all empty spaces are properly filled to prevent movement during transit.
Secure Empty Spaces Properly
Properly securing empty spaces in computer component packaging requires a strategic approach using versatile foam solutions. You'll need to focus on eliminating void spaces that could allow components to shift during transit, potentially causing damage to sensitive parts.
- Start with convoluted foam inserts that you can die-cut to create custom fits for your components, ensuring they stay firmly in place.
- Use anti-static foam materials to protect against electrical damage, particularly when packaging circuit boards or memory modules.
- Implement interlocking foam pieces to create a solid protection system that absorbs shocks effectively.
- Apply the box-in-box method for extra-sensitive items like monitors and hard drives.
Fill any remaining spaces with anti-static packing peanuts or bubble cushion wrap, pressing components firmly into place.
You'll want to perform a gentle shake test to identify areas that need additional void fill.
For maximum protection, consider using expanding foam solutions like FOAMplus® that mold directly to your components' contours. These systems expand up to 250 times their liquid volume, providing precise protection while eliminating the need for excessive storage space.
Remember to choose foam materials with appropriate strength ratings based on your components' weight and fragility.
Test Package Before Shipping
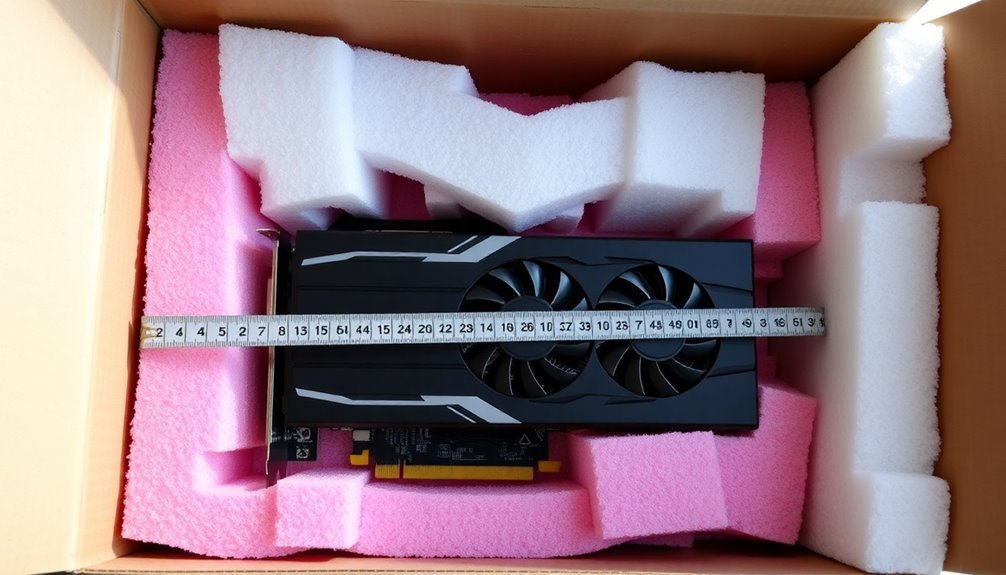
Testing your packaged computer components before shipping is a critical step that can save you from costly returns and damage claims. You'll want to send your test package to the FedEx Packaging Lab, where they'll conduct thorough distribution testing at no charge except for shipping costs to their facility.
Start by selecting the appropriate test based on your shipping method: ISTA-6-FEDEX-A for FedEx Express or Ground, ISTA-6-FEDEX-B for Express Freight, or ISTA 3B for Freight LTL shipments.
Mark your test package clearly, then place it in a sturdy outer container with protective materials like foam or air-cellular cushioning between layers. Don't forget to label the outer container as "Overpacked/Test Pkg. Inside."
Email your completed test application to packagingservices@fedex.com and attach a copy to the outside of your package.
You can submit up to four packages per two-week cycle, and you'll typically receive results within 4-6 business days for parcels or 5-8 days for freight.
If you're shipping components that would normally contain hazardous materials, use sand, water, or dummy products to simulate the weight during testing.
Frequently Asked Questions
How Long Can Computer Components Safely Remain Stored in Foam Packaging?
You'll find most components stay safe in high-quality foam for 1-2 years. Don't store them longer than necessary, and check your foam regularly for signs of degradation to protect your valuable parts.
Can Foam Packaging Materials Be Reused for Multiple Shipments?
Yes, you can reuse foam packaging for multiple shipments, especially cross-linked polyethylene foam. It's durable and maintains its protective properties, but you'll need to inspect it regularly for wear and damage between uses.
What Temperature Ranges Can Different Types of Foam Packaging Withstand?
You'll find foam packaging has varied temperature ranges: PBO foam handles -260°C to 600°C, PU foam works from -40°C to 80°C, PE foam tolerates -50°C to 70°C, and anti-static foam functions between -10°C to 85°C.
Does Colored Foam Affect the Anti-Static Properties of Packaging Materials?
No, the color doesn't affect anti-static properties. You'll find that anti-static protection comes from special additives in the foam, not its color, though pink is commonly used to indicate anti-static properties.
How Often Should Foam Packaging Materials Be Replaced in Long-Term Storage?
You'll need to replace your foam packaging materials every 1-2 years, especially if they're anti-static. Check regularly for signs of degradation, and don't wait until your foam loses its protective properties.
In Summary
Following these foam packaging tips will guarantee your computer components arrive safely at their destination. You'll protect sensitive electronics from both static damage and physical impact when you carefully select materials and implement proper double-boxing techniques. Whether you're shipping a single graphics card or an entire system, don't skip any steps. Your attention to proper foam packaging will preserve your valuable hardware investments.
Leave a Reply