High-frequency ionizers serve seven essential industrial functions. You'll find them protecting sensitive electronics during manufacturing, safeguarding medical device assembly in cleanrooms, and preventing static-related issues in printing processes. They're critical for precision semiconductor fabrication, where they reduce particle contamination by up to 90%. In textile processing, they enhance surface properties and dye adhesion without chemical treatments. They're also important for film production to prevent dust attraction and static buildup. Finally, they maintain cleanroom operations by neutralizing charges that could compromise sterile environments. Exploring each application reveals their remarkable impact on modern manufacturing.
Protecting Sensitive Electronics Components
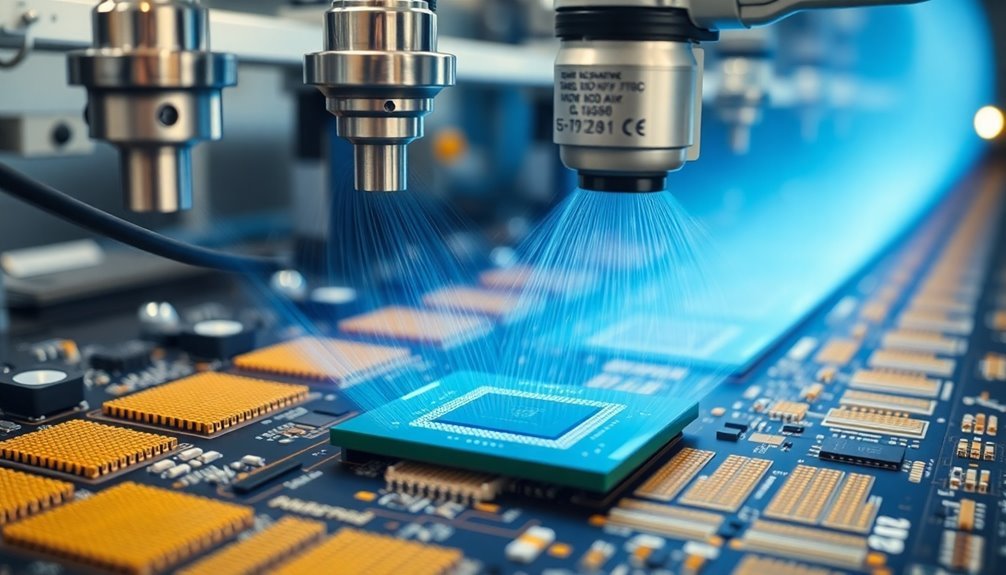
High-frequency ionizers step up to provide essential protection for sensitive electronics components during manufacturing and assembly processes.
You'll find these advanced systems use cutting-edge technology to neutralize static electricity quickly and efficiently, preventing costly damage to delicate parts. With De Laval nozzles in their electrode probes, they achieve supersonic air speeds that dramatically enhance ion attachment rates. The SJ-H Series also eliminates static five times faster than conventional ionizers. Self-diagnosis functions ensure optimal performance at all times.
You can precisely target static elimination where it's needed most, even in hard-to-reach areas inside devices. The compact design allows you to install ionizers in confined spaces where traditional models won't fit, while adjustable fan speeds let you customize your static elimination strategy.
With a range of up to 10 feet, you'll get thorough coverage throughout your assembly area.
You won't need to worry about frequent maintenance, thanks to I.C.C. technology that minimizes probe degradation. The systems include automatic cleaning features and maintenance alerts that guarantee consistent performance.
When you're operating these ionizers, you'll benefit from their energy-efficient design, which uses minimal air volume while maintaining ideal static elimination. This efficiency can reduce your running costs by up to 60%, making them a cost-effective solution for electronics protection.
Medical Device Assembly Protection
When you're manufacturing medical devices, you'll need highly precise ionization control to protect sensitive electronic components during assembly in cleanroom environments.
Your cleanroom static control solutions must meet strict ANSI/ESD S20.20 compliance standards while preventing potential ESD damage that could compromise device reliability.
High-frequency ionizers integrated into your assembly line provide continuous protection against static charges, ensuring both product quality and regulatory compliance. Regular maintenance with isopropyl alcohol cleaning helps maintain optimal ionizer performance during medical device production. The D3I Defender model offers balanced ionization systems specifically designed for 4-5 foot medical device workstations.
Cleanroom Static Control Solutions
Static discharge poses a vital threat in medical device assembly cleanrooms, where even minor electrical disturbances can compromise product integrity and safety.
You'll need extensive static control solutions to maintain an ideal cleanroom environment and protect sensitive medical devices during assembly.
Air ionization systems form your first line of defense, introducing balanced positive and negative ions to neutralize static charges on surfaces and in the air. clean booths have proven especially effective for protecting delicate electronics from charged surfaces.
You can enhance this protection by installing ionizing blowers at strategic points, particularly near entry zones and essential production areas. ESD safe furniture provides additional protection against static buildup during assembly operations.
When you combine these with anti-static wall panels, you'll greatly reduce particle shedding and maintain better static control throughout your facility.
To guarantee your static control measures remain effective, you'll want to implement regular ESD monitoring.
This includes installing measurement equipment to track static levels and maintaining proper documentation.
Don't forget to integrate static removal capabilities in your air showers – they're vital for removing contaminants and neutralizing charges on personnel entering the cleanroom.
Remember to train your staff on proper static control procedures and maintain your equipment regularly to guarantee consistent protection of your medical device assembly process.
Precise Ionization For Components
Building upon cleanroom-wide static control, precise component-level ionization requires specialized high-frequency equipment for medical device assembly.
You'll find these advanced ionizers incorporate de Laval nozzles and internal ground plates to deliver supersonic ion flow directly to sensitive components while maintaining cleanroom integrity.
When you're working with medical devices, you'll need to verify your ionization system meets ANSI/ESD S20.20 standards and ISO 14644 Class 4 ratings.
The latest high-frequency ionizers offer adjustable airflow settings and modular designs that you can easily integrate into your assembly line, providing consistent protection for each component.
You'll benefit from the systems' self-diagnostic capabilities and auto-clean features, which minimize maintenance downtime and verify continuous operation. Regular updates through manufacturer newsletters help maintain optimal performance and authenticity verification.
The pulse AC methods deliver high-speed ionization that you can precisely control, while silicone-free construction prevents contamination of sensitive medical components.
For real-time monitoring, you can connect these ionizers to your facility monitoring systems (FMS).
This integration lets you track ionization performance and maintain documentation for quality control.
The high-voltage circuit technology ensures stable ion output, while advanced insulation protects both operators and components throughout the assembly process.
Controlling Static During Printing
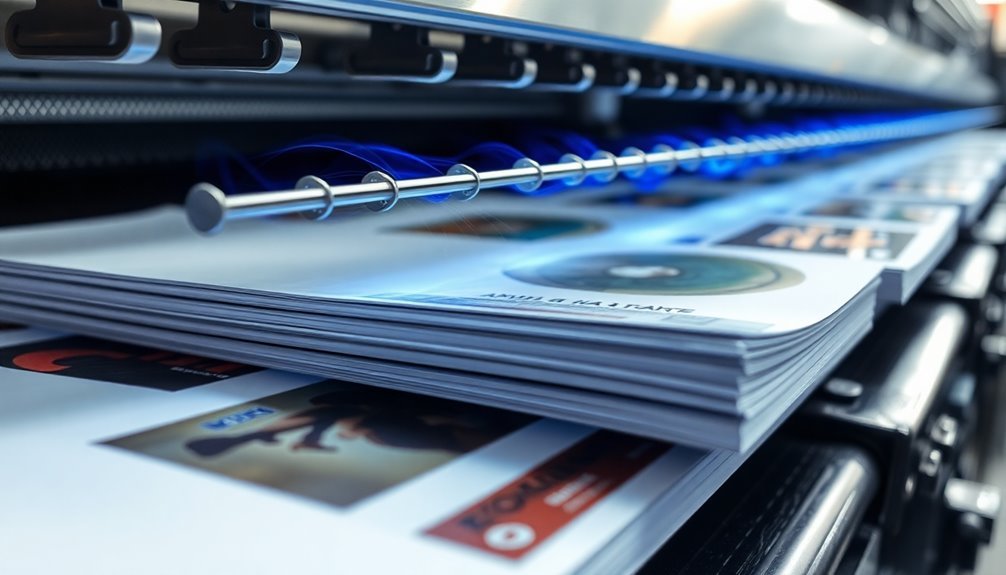
You'll find that high frequency ionizers are essential for preventing paper sheets from sticking together during the printing process, ensuring smooth material flow through your production line.
By neutralizing static charges, you're able to minimize print quality issues like misalignment and unwanted particle attraction that can mar your finished products.
Continuous operation models with integrated fans, like the ER-F series, provide consistent charge elimination throughout extended print runs.
Your production line can maintain higher speeds when static-related disruptions are eliminated, leading to improved efficiency and reduced downtime.
Prevent Paper Sheet Sticking
Numerous printing operations face challenges with paper sheets sticking together due to static electricity buildup. You'll find that high-frequency ionizers offer effective solutions to combat this common issue by neutralizing static charges and guaranteeing smooth paper movement through your printing machinery.
When you're dealing with paper sheet sticking, you can implement various ionizer technologies to improve your printing process. Using air-assisted ionization systems with De Laval nozzles, you'll achieve superior ion attachment rates and faster static elimination. You can adjust the airflow settings to match your specific printing speed requirements while maintaining ideal static control.
- Picture sheets of paper flowing smoothly through your printer without clinging or jamming
- Visualize a continuous production line where papers separate effortlessly
- Imagine dust-free printed materials with perfect print quality
You'll find multiple ionizer options to suit your needs, from overhead blowers for large printing areas to compact bar-type ionizers for restricted spaces. The I.R.G. structure and pulse AC method guarantee balanced ionization, while high-frequency AC technology maintains consistent performance.
For best results, you can position ionizers at strategic points throughout your printing line to create static-free zones.
Reduce Print Quality Issues
Print quality depends heavily on effective static control during your printing operations. When you implement proper static elimination systems, you'll prevent numerous print defects and guarantee consistent output quality.
Static eliminators effectively neutralize charges that cause overspray and registration problems, which directly impact your final print results.
You'll notice significant improvements in digital printing processes when you install static control devices. These systems prevent print head clogging failures and guarantee smooth operation of your equipment.
For best results, you'll want to position static eliminators at both the entrance and exit points of your press, particularly where the drying process generates static charges at high speeds.
Advanced ionizers like the SJ-H Series provide excellent static elimination without using air, making them ideal when airflow might compromise print quality.
You'll achieve the finest results by incorporating high-speed ionizers that feature I.C.C. technology, which maintains consistent performance even as electrodes age.
When you're dealing with photographic processes or pre-press operations, static eliminators become particularly essential as they prevent dust particles from compromising your image quality through unwanted contamination.
Boost Production Line Speed
Several cutting-edge ionizer technologies now enable dramatic increases in production line speeds.
You'll achieve faster throughput by leveraging supersonic ion delivery systems that operate at speeds exceeding sound barriers, eliminating static in less than one second. The combination of de Laval nozzles and I.R.G. structure guarantees ions reach their targets efficiently, even at distances up to 1500mm from your production line.
You can maintain peak speeds while guaranteeing quality by implementing pulse AC methods that deliver balanced ionization. The I.C.C. technology extends operational lifetime threefold, reducing maintenance downtime that could slow your production. With 60% lower running costs, you won't need to compromise between speed and efficiency.
- Watch as paper sheets flow smoothly through your printing press without static-induced clinging or misalignment
- See your packaging materials move seamlessly through high-speed conveyor systems without attracting dust
- Experience consistent product flow with automated cleaning systems maintaining peak performance
Variable airspeed control lets you fine-tune the static elimination process to match your specific production speeds, while the ultra-compact design integrates seamlessly into existing line configurations without requiring extensive modifications.
Semiconductor Manufacturing Precision
Through advanced high frequency AC technology, semiconductor manufacturing has achieved unprecedented precision in static control and contamination prevention. You'll find that modern ionizers, like the 4214 In-line Ultra-clean Nitrogen Ionizer, use silicon-containing emitters combined with high-frequency AC voltage to maintain pristine manufacturing conditions. This technology's effectiveness is evident in wafer fab operations, where users report 50-90% reductions in particle contamination on semiconductor wafers.
Component | Function | Benefit |
---|---|---|
Silicon Emitters | Particle Control | Class 1 Manufacturing Compatible |
High Frequency AC | Plasma Generation | Precise Material Removal |
Ionized Nitrogen | Static Control | Reduced ESD Events |
You'll need to understand that these systems operate at frequencies between 1-100 kHz, with a mean voltage of approximately zero (±500 volts). The technology's implementation in cleanroom environments has revolutionized semiconductor production by preventing ESD events during cassette transfers and minimizing contamination during web fabrication processes. When you're working with these systems, you'll notice they comply with ANSI/ESDA SP3.4-2016 standards, ensuring consistent performance verification through standardized testing procedures.
Textile Processing Applications
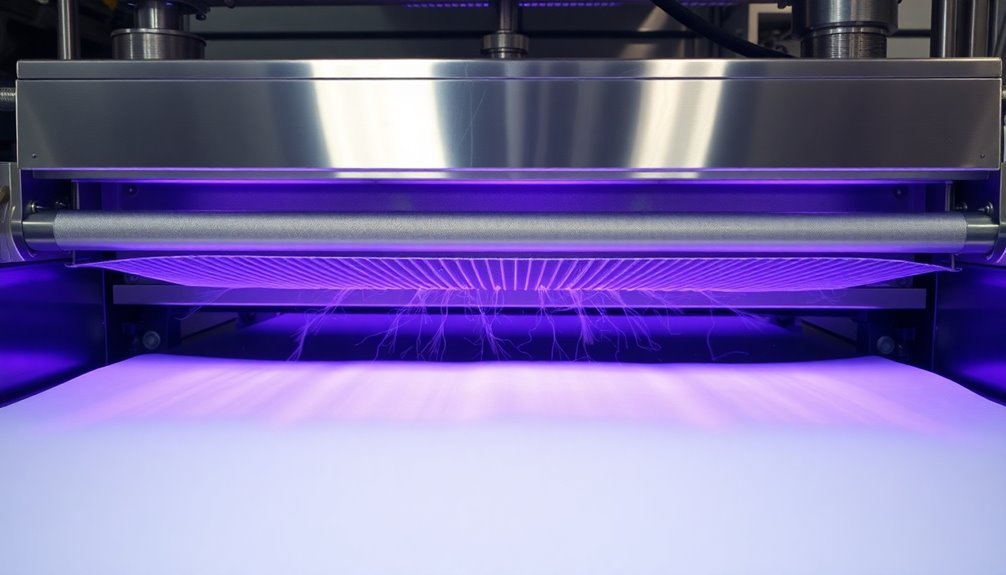
High frequency ionizers have revolutionized textile processing by enabling precise surface modifications across a wide range of fabrics. You'll find that the 13.56MHz frequency plasma cleaning technology offers exceptional control over fabric surface properties, allowing you to enhance wettability, improve dye adhesion, and create specialized functional coatings without damaging the base material.
When you're working with plasma treatment in textile processing, you'll notice these distinct advantages:
- The ionized gas particles dancing across the fabric surface, creating microscopic changes that enhance the material's properties
- The subtle blue glow of the plasma field as it uniformly treats large fabric rolls
- The clean, efficient process that leaves no chemical residue or waste behind
You can achieve multiple surface modifications through this technology, from making fabrics water-repellent with HMDSO treatment to adding antibacterial properties or UV protection.
It's particularly effective when you're treating synthetic fibers like polyester and polypropylene. The process is environmentally friendly, eliminating the need for wet chemical treatments and reducing your facility's environmental footprint.
You'll also find that plasma-treated textiles offer superior performance characteristics while maintaining their original feel and comfort.
Film Production Static Management
The management of static charges in film production presents unique challenges that high-frequency ionizers effectively solve. You'll find these devices particularly valuable in both inline and local applications, where they efficiently neutralize static charges that could otherwise cause defects in your film products.
When you're selecting an ionizer for film production, you'll want to focus on units featuring high-frequency AC voltage profiles operating between 1 to 100 kiloHertz. It's crucial to choose models with silicon-containing emitters (at least 47% silicon by weight) to guarantee clean performance. You'll notice these modern designs don't require low-frequency voltage pulses, making them more efficient for inline operations.
For plastic film and lamination processes, you'll achieve the best results using overhead or bar ionizers. They're especially effective for wider products and can be scaled up as needed.
You'll need to maintain your ionizers regularly by cleaning the emitter pins to prevent contamination and guarantee balanced ion production. Consider models with replaceable needle cartridges and remote-control capabilities – they'll make your maintenance tasks easier while keeping your production line running smoothly.
Cleanroom Operations
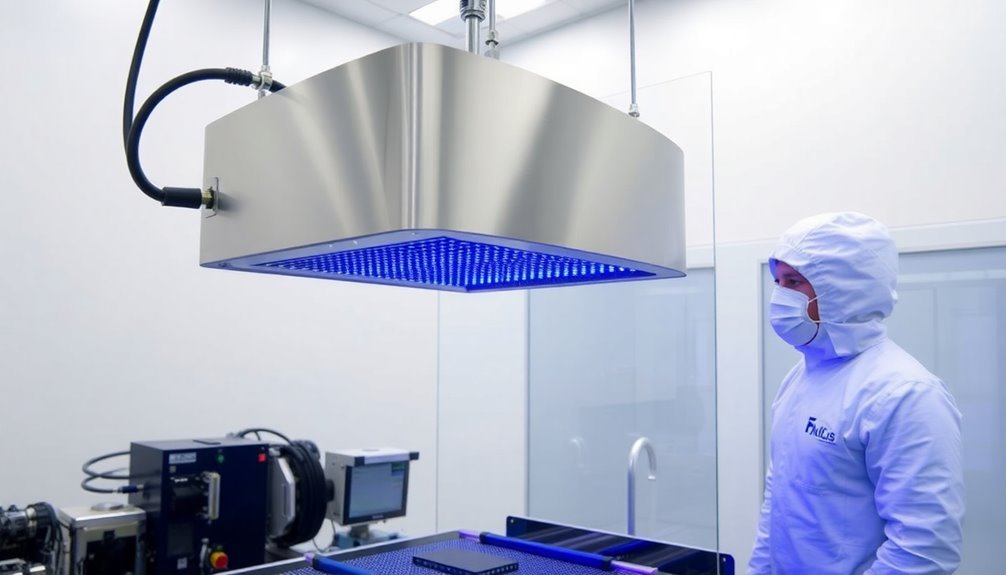
Cleanroom environments demand specialized ionization solutions to protect sensitive components from static-related defects.
You'll need to implement ceiling-mounted ionizers that work with laminar airflow systems and pulsed DC ionizing bars for minienvironments to effectively neutralize static charges. These systems can reduce particle addition by up to 80% during web processes and markedly improve cleaning efficiency.
When setting up your cleanroom ionization system, you'll want to focus on proper placement for unobstructed airflow and maximum neutralization efficiency.
Regular maintenance, including cleaning emitter points with isopropyl alcohol and conducting performance checks, is essential for maintaining system effectiveness.
- Picture a photolithography area where invisible ions flow down from ceiling units, creating a protective shield around sensitive wafers
- Visualize technicians in gowning rooms passing through curtains of ionized air that strip away contaminating particles
- Imagine robotic arms moving smoothly through minienvironments, protected by precisely positioned ionizing bars
You'll find that properly maintained ionization systems improve product yields, reduce downtime from robot lockups, and enhance cleaning processes.
They're particularly valuable when traditional static control methods like wrist straps aren't practical in cleanroom operations.
Frequently Asked Questions
How Often Should Ionizer Electrodes Be Cleaned for Optimal Performance?
You'll need to clean your ionizer electrodes daily to weekly, depending on your environment's dust levels. Make sure to monitor performance and inspect for buildup – adjust your cleaning schedule based on these factors.
What Safety Certifications Are Required for Ionizers in Food Processing Facilities?
You'll need UL certification for electrical safety, CE marking for EU compliance, FDA approval for food contact, and ISO 9001 for quality management. Your local health department may require additional certifications.
Can Ionizers Be Safely Used Around Water-Based Manufacturing Processes?
You'll need waterproof ionizers with proper IP ratings for water-based processes. Choose alpha ionizers or specially designed electrical models that are intrinsically safe, and always position them away from direct water exposure.
What Is the Typical Lifespan of a High-Frequency Ionizer?
You'll typically get 5+ years from your high-frequency ionizer if it's well-maintained. With regular cleaning and proper care, your ionizer's tungsten electrodes will last longer, especially if you've got self-cleaning features.
How Do Temperature and Humidity Affect Ionizer Performance?
Your ionizer works best at 20-30°C and 40-60% humidity. High temps can wear electrodes and cause malfunctions, while extreme humidity affects ion mobility and can corrode components. Keep conditions moderate for ideal performance.
In Summary
You've now seen how high frequency ionizers serve as essential tools across multiple industrial applications. From safeguarding delicate electronics to ensuring precision in semiconductor production, these devices have become indispensable. Whether you're managing a cleanroom or overseeing textile processing, you'll find that proper ionization control is vital for quality, safety, and efficiency in your industrial operations.
Leave a Reply