You'll need to maintain humidity levels between 40-60% RH to protect circuit boards during manufacturing, with 50% being ideal. Use moisture barrier bags with desiccants and humidity indicator cards for storage, and implement proper moisture detection systems like ceramic sensors or MLIs to monitor conditions. Steam humidifiers and desiccant dryers can help control moisture levels, while ESD-free racks provide additional protection. Follow MSL standards for handling sensitive components – some require use within specific timeframes after opening moisture barrier bags. Understanding these controls and standards will help you prevent costly moisture-related defects in your PCB production.
Understanding Humidity Control Fundamentals
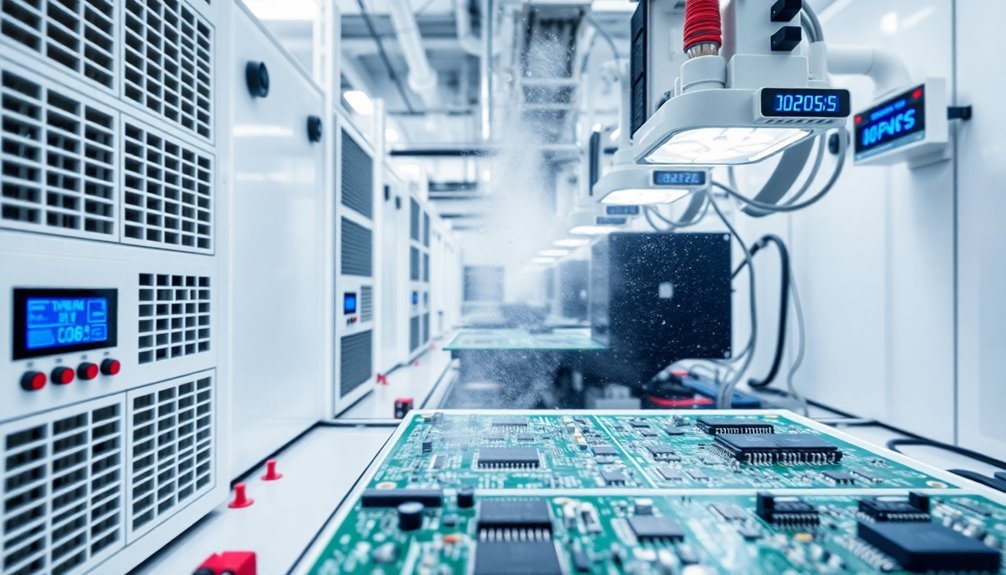
Most electronics manufacturing environments require precise humidity control to protect sensitive components and guarantee ideal production conditions. You'll need to maintain relative humidity levels between 30% and 70%, though a consistent 50% RH is often the sweet spot for best stability in your manufacturing processes.
Understanding the fundamentals of humidity control helps you prevent costly damage and production issues. When humidity drops below 45% RH, you're at increased risk of electrostatic discharges that can destroy sensitive components. Dielectric properties change when humidity fluctuates, affecting the overall performance of electronic components.
Conversely, keeping humidity above 55% RH protects sensitive materials from deterioration. You'll find that proper humidity levels also reduce dust accumulation and help prevent corrosion on your circuit boards.
To achieve effective humidity control, you'll want to implement adiabatic air humidifying systems that offer precise moisture management. These systems don't just maintain ideal humidity; they also provide beneficial cooling effects that help offset heat generated during manufacturing.
You should regularly conduct site assessments to determine your facility's specific humidity requirements and integrate real-time monitoring systems for continuous oversight. This proactive approach guarantees compliance with industry regulations while maximizing production yields and operational efficiency.
Moisture Sensitivity Level Standards
Circuit board manufacturers rely on Moisture Sensitivity Level (MSL) standards to protect sensitive electronic components during assembly. You'll find MSL ratings ranging from 1 to 6, with each level indicating how susceptible a component is to moisture-induced damage during storage and reflow soldering.
When you're working with components rated MSL 1, you don't need to worry about floor life – these parts can handle unlimited exposure. However, if you're dealing with more sensitive components like MSL 3, you'll need to use them within 168 hours of opening their moisture barrier bags. These standards were established by the IPC/JEDEC J-STD-020 specification to ensure consistent handling practices across the industry.
The most sensitive components, rated MSL 5 and 5A, give you just 48 and 24 hours respectively.
If you exceed a component's floor life, you'll need to bake it at 125°C for 24 hours to remove excess moisture. Without proper handling, you risk serious damage like package cracking, delamination, and the "popcorn" effect.
To protect your components, you should store them in moisture barrier bags with desiccants and moisture indicator cards. Once you've assembled the board and applied conformal coating, you won't need to worry about moisture sensitivity anymore.
Common Humidity Control Methods
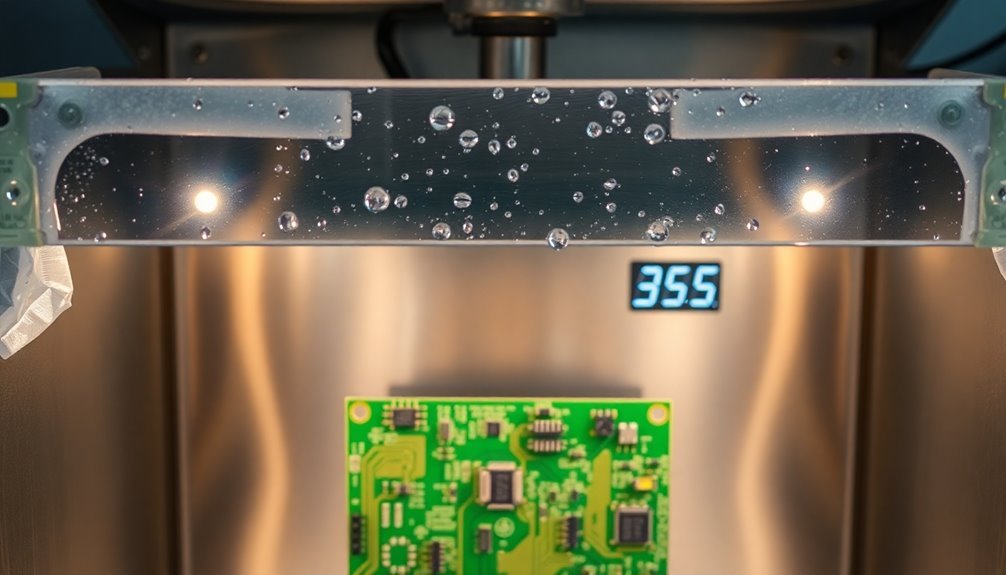
The key to protecting circuit boards lies in maintaining precise humidity control through multiple proven methods. You'll need to maintain relative humidity between 40% and 55% to prevent electrostatic discharge while ensuring ideal manufacturing conditions. Steam humidifier systems provide customized moisture control for sensitive manufacturing areas.
Adiabatic humidification systems offer an efficient solution, adding moisture to the air while helping stabilize indoor temperatures and reducing operational costs.
For dehumidification, you'll want to implement desiccant dryers combined with aftercoolers to remove excess moisture and adjust air temperature. Sorption rotor systems provide continuous moisture removal through their regeneration process, which is essential for maintaining consistent humidity levels in your facility.
You can further protect your circuit boards using specialized storage and packaging solutions. Consider using drying enclosures that maintain humidity levels below 0.05g/m³, and implement protective measures like conformal coating or thermoplastic overmolding.
During fabrication, you'll need to work in temperature-controlled environments with desiccant drying agents. Don't forget to use meshed copper planes in your PCB design to reduce moisture accumulation, and always apply low-pressure vacuum during lamination to prevent moisture-trapping voids.
Preventing ESD Through Humidity
Understanding how humidity affects electrostatic discharge (ESD) is essential for protecting your sensitive electronic components. When humidity levels drop below 30%, you'll face markedly increased risks of static electricity buildup and discharge. This occurs because dry air can't effectively dissipate static charges, leaving your circuit boards vulnerable to damage. Complex miniature circuits in modern electronics are particularly susceptible to ESD damage.
You'll achieve the best ESD prevention by maintaining relative humidity between 40% and 60%. At these levels, water vapor in the air acts as a natural conductor, helping dissipate static charges before they can accumulate to dangerous levels.
While humidity above 60% provides excellent ESD protection, you'll want to avoid such high levels as they can lead to corrosion issues.
To maintain proper humidity levels in your manufacturing environment, you can implement evaporative humidifiers or integrated cooling systems. You'll also want to minimize factors that create dry conditions, such as heat-generating equipment and carpeted areas.
If you can't maintain ideal humidity levels, consider using ionized air systems to help dissipate static charges. Remember that consistent humidity control is vital – even brief periods of low humidity can create conditions where damaging ESD events become likely.
Moisture Detection Systems
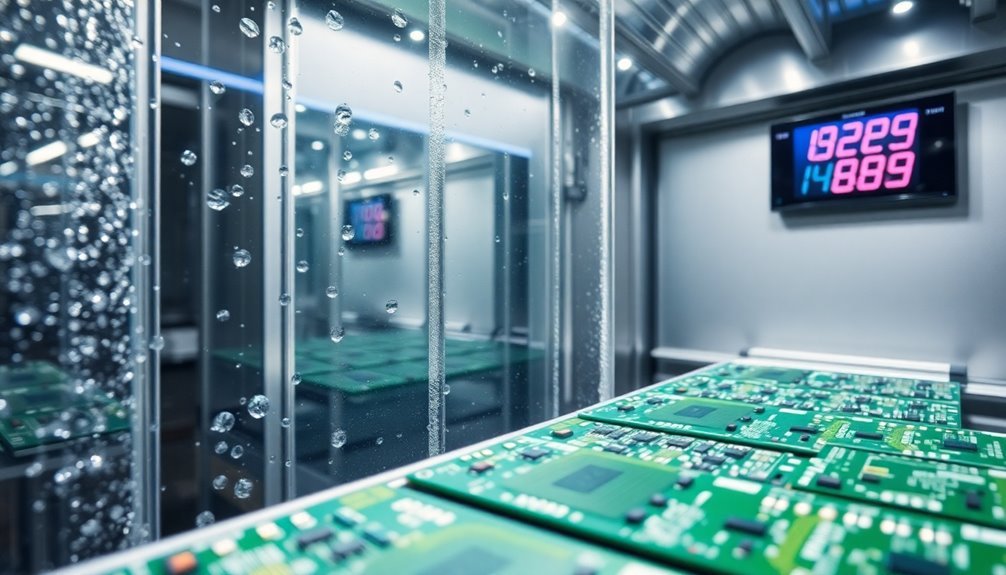
You'll find numerous advanced moisture detection technologies available for monitoring circuit board environments, including ceramic metal-oxide sensors and RF measurement systems.
Your facility can benefit from capacitive measurement applications that provide real-time data on humidity levels, allowing for immediate process adjustments when moisture levels fall outside acceptable ranges. Ceramic sensors operate effectively in extremely dry conditions of up to -120 °Cfp while maintaining accuracy.
These monitoring solutions integrate with your existing control systems to maintain ideal humidity conditions for circuit board manufacturing and storage.
Advanced Monitoring Technologies
Modern moisture detection systems have revolutionized how we monitor and protect circuit boards from humidity-related damage. You'll find several advanced technologies that work together to provide a thorough moisture detection and prevention. The sensor technology shows 14% to 29% increases in capacitance measurements when exposed to moisture over time.
Technology | Detection Method | Application |
---|---|---|
Fringing Field Capacitors | Capacitance Changes | PCB Moisture Detection |
Ceramic Metal-Oxide | Dielectric Properties | Dew Point Measurement |
MLIs | Saturation Level | PCB Quality Control |
RF Sensors | Radio Frequency | Industrial Profiling |
Real-Time Monitoring | Continuous Data | Process Control |
You can implement these technologies throughout your manufacturing process to detect moisture before it causes damage. Fringing field capacitors integrate directly into your PCB design, while ceramic metal-oxide sensors offer cost-effective dew point monitoring. For rapid response times, you'll want to think about MLIs, which can detect changes in less than 24 hours at room temperature.
The D-MET system with dynamic background gas compensation guarantees you're getting consistent, accurate readings. When you're dealing with sensitive electronics, these non-contact measurement solutions help you maintain quality without risking contamination, making them ideal for modern manufacturing environments.
Capacitive Measurement Applications
Capacitive moisture detection systems form the backbone of today's PCB protection strategies, relying on the unique dielectric properties of water molecules to measure humidity levels.
When you're protecting PCBs during manufacturing, you'll benefit from capacitive sensors' ability to detect moisture sensitivity levels through their hygroscopic dielectric material positioned between electrodes. The 555 Timer IC generates the necessary signals for precise moisture measurements. The sensors respond to humidity changes as water vapor alters the dielectric constant, creating measurable capacitance variations that correlate directly with moisture content.
These systems convert moisture-related capacitance changes into precise voltage measurements using square wave signals, providing accurate readings without the corrosion risks associated with resistive sensors.
You can trust these systems in your manufacturing environment because they're designed with protective layers for chemical resistance and robust operation. They're particularly effective when managing moisture sensitivity levels (MSL) in PCB production, where precise humidity control is vital.
The technology's integration with RF dielectric measurement capabilities allows you to obtain complete moisture profiles, while dynamic background compensation systems guarantee your readings remain accurate regardless of surrounding environmental conditions.
Optimal Humidity Storage Guidelines
The proper storage of circuit boards requires careful attention to both temperature and humidity levels, with ideal conditions ranging between 15-30°C and 40-65% relative humidity. You'll need to implement several protective measures to safeguard your PCBs in top condition during storage.
Storage Element | Implementation Method |
---|---|
Moisture Control | Use moisture barrier bags with desiccants and humidity indicator cards |
Environmental Protection | Store in ESD-free racks away from direct sunlight |
Packaging Security | Apply vacuum packaging with tight seals |
Surface Protection | Use conformal coating and anti-oxidation varnish |
Monitoring System | Conduct regular inspections and track humidity levels |
To maximize your PCBs' storage life, you'll want to maintain a stable, dry environment while implementing proper packaging techniques. Don't forget to label each unit with essential details like model numbers and storage dates. You should seal unused components in moisture barrier bags and include humidity indicator cards to monitor internal moisture levels. For long-term storage up to 9 months, you'll need to apply additional protective measures such as conformal coating and anti-oxidation varnish to prevent degradation and extend shelf life.
Manufacturing Environment Best Practices
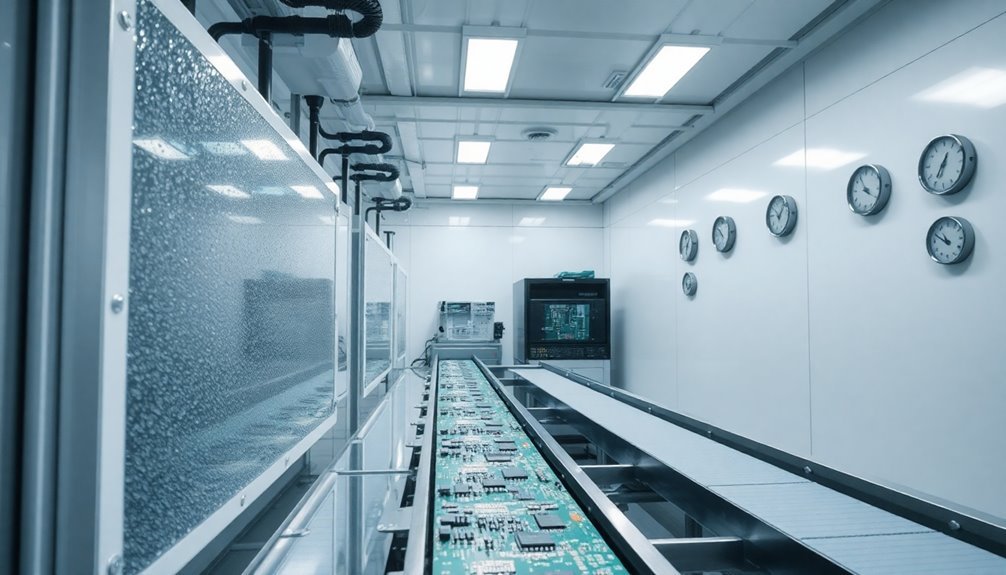
While proper storage practices protect circuit boards after production, maintaining ideal manufacturing conditions directly affects PCB quality from the start.
You'll need to establish controlled environments with humidifiers to regulate moisture levels during the lamination process, while also implementing desiccant drying agents to absorb excess moisture from the air.
To strengthen your manufacturing process, you'll want to incorporate meshed copper planes during PCB fabrication. This technique improves the bond between layers while reducing moisture-related issues.
Don't forget to thoroughly clean all components before assembly and apply conformal coating to protect against moisture and contaminants.
You should implement thorough quality management practices, including Total Quality Management and lean manufacturing principles. These approaches will help you maintain consistent production standards while minimizing defects.
It's crucial to establish statistical process control measures to monitor your manufacturing processes and conduct regular audits to guarantee compliance with quality standards.
Remember to focus on supplier quality management to guarantee you're receiving high-quality materials. By combining these manufacturing best practices with proper environmental controls, you'll substantially reduce moisture-related issues in your PCB production.
Humidity Impact on PCB Quality
Understanding humidity's impact on PCB quality requires careful attention to multiple critical factors. When humidity drops below 30%, you're facing increased risks of electrostatic discharge that can damage sensitive components.
Conversely, excessive humidity above 60% can lead to serious soldering defects and long-term reliability issues.
You'll need to monitor your manufacturing environment closely, as humidity affects several essential aspects of PCB production. Your solder paste application works best between 40% and 50% humidity at 65-75°F.
If you're dealing with high humidity, you'll encounter problems like solder paste infiltration, incomplete soldering, and potential delamination in solder joints.
You must also consider your components' Moisture Sensitivity Level ratings, which determine safe exposure times to humid conditions.
Watch out for condensation, as it's particularly dangerous on powered PCBs. It can trigger short circuits and initiate corrosion processes, especially on exposed surface pads.
To protect your PCBs, you'll want to implement proper storage solutions, including desiccants, and maintain strict environmental controls throughout your manufacturing process.
Cost-Effective Moisture Prevention Strategies
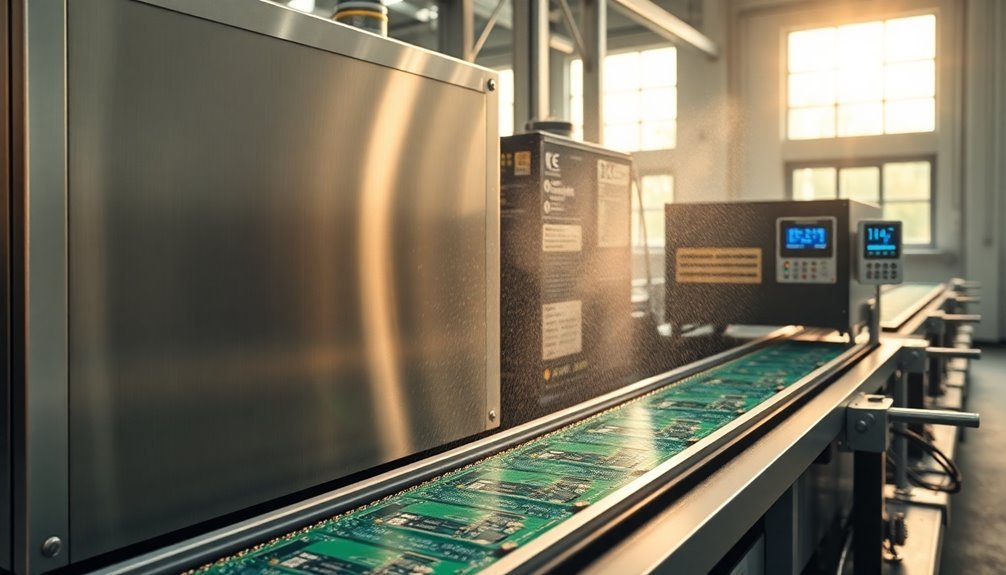
You'll find that desiccant packaging solutions offer a low initial investment compared to automated humidity control systems, with industrial-grade desiccant packs costing roughly $0.50-$2 per unit.
While automated humidity control systems require a higher upfront cost of $2,000-$5,000, they provide long-term savings through reduced PCB failure rates and minimal maintenance requirements.
The choice between these solutions depends on your production volume, as desiccant packages prove more cost-effective for small batches, while automated systems become economical for large-scale manufacturing operations.
Desiccant Packaging Cost Analysis
The cost analysis of desiccant packaging reveals a complex balance between initial investment and long-term savings. While you'll notice steady price increases across packaging formats like clamshells, jars, and pouches from 2012 to 2027, the benefits often outweigh these rising costs.
Your investment in desiccant solutions directly contributes to reduced spoilage and waste, making it a financially sound decision for protecting circuit boards.
You can see the industry's robust growth reflected in specialty packaging figures, which have jumped from $243.9 billion in 2019 to $325.7 billion in 2023. With specialty packaging now representing 51% of sales, you're part of a significant market shift toward quality moisture control solutions.
The U.S. market's expansion to $183.65 billion in 2023, with projections reaching $218.23 billion by 2027, demonstrates the increasing value placed on effective moisture prevention.
When you're considering packaging costs, factor in that the global desiccant market, valued at $1.05 billion in 2023, is growing at a 5.24% CAGR. While initial equipment costs and pharmaceutical packaging regulations pose challenges, the long-term benefits of reduced product failure and extended shelf life justify the investment.
Automated Humidity Control Investment
Moving beyond packaged desiccant solutions, automated humidity control systems offer a more thoroughgoing approach to protecting circuit boards. By maintaining relative humidity between 30-60%, you'll substantially reduce the risk of electrostatic discharge and moisture-related damage during manufacturing.
These systems integrate seamlessly with temperature controls, providing an extensive environmental management that's essential for SMT and wave soldering processes.
Your investment in automated humidity control delivers measurable returns through:
- Reduced repair costs and fewer warranty claims due to moisture-related failures
- Enhanced production efficiency with real-time monitoring and adjustment capabilities
- Consistent product quality across manufacturing batches
- Lower long-term maintenance expenses and improved yield rates
When implementing automated humidity control, you'll need to focus on both immediate and long-term strategies. Start by integrating anti-static measures and grounding equipment, then establish real-time monitoring protocols.
Consider moisture-resistant materials and conformal coatings for additional protection. The initial investment might seem substantial, but the long-term benefits of improved product reliability, reduced defects, and enhanced production efficiency make automated humidity control a cost-effective solution for circuit board manufacturing.
Design Solutions for Humidity Control
Protection against moisture stands as a critical consideration in circuit board design. You'll need to implement multiple design strategies to maintain ideal humidity levels between 40% and 50% during the assembly process.
Start by selecting components with appropriate Moisture Sensitivity Levels (MSL) that can withstand exposure to relative humidity between 40% and 60%.
You can protect your PCBs from moisture damage by applying conformal coatings, which create a protective barrier against electrochemical processes. Consider using thermoplastic overmolding or potting techniques for additional protection, but make certain your board is completely dry before application. When selecting materials, opt for moisture-resistant options and guarantee proper adhesion of solder paste and coatings.
Don't forget to implement ESD protection measures by maintaining humidity levels above 30%. You'll want to use ESD wrist straps, heel straps, and grounded equipment during assembly.
For long-term protection, pack your assembled PCBs with desiccants and store them in moisture-controlled environments. Remember to train your personnel on proper humidity control procedures and regularly maintain your environmental control systems to guarantee consistent protection throughout the manufacturing process.
Climate Considerations for PCB Protection
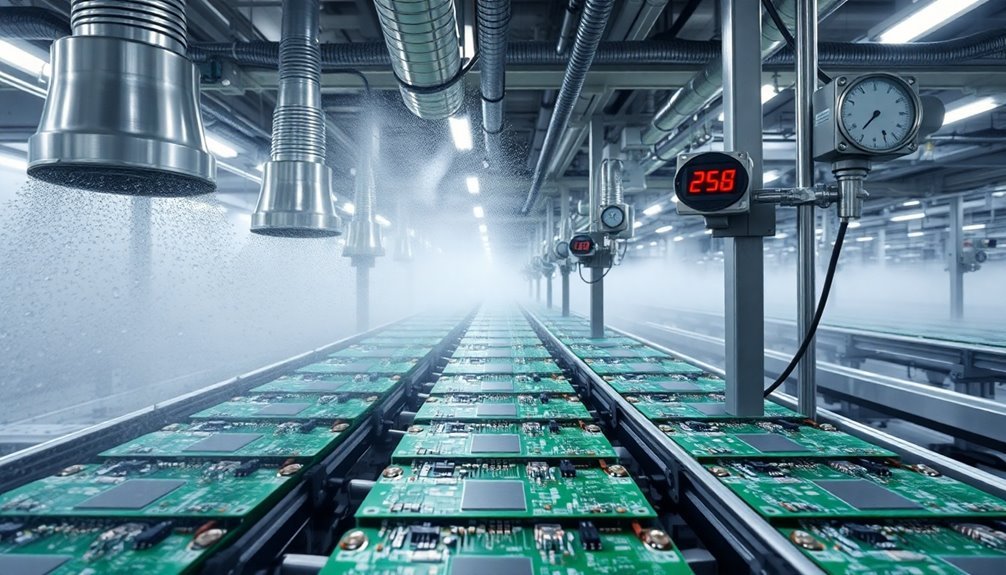
When you're manufacturing PCBs in different climate zones, you'll need to adapt your humidity control strategies to match the specific challenges of each region.
In tropical environments, you'll want to focus on dehumidification systems that can maintain 30-60% relative humidity despite the naturally high moisture levels. This range is crucial for preventing moisture-related issues such as corrosion and ensuring the stability of electronic components, while also mitigating the risk of electrostatic discharge (ESD).
In desert climates, you'll need to add moisture to prevent dangerous static buildup. Lower humidity environments pose a higher risk of ESD, so maintaining a humidity level at or above 30% is essential to mitigate this risk.
Your climate control solutions must account for seasonal variations and extreme weather events that could impact your facility's ability to maintain ideal PCB manufacturing conditions. This includes ensuring that the temperature and humidity are evenly distributed throughout the manufacturing area and that the environment is free from dust and other impurities to prevent any adverse effects on the PCBs.
Regional Humidity Control Challenges
Understanding regional climate variations plays a crucial role in PCB manufacturing and protection. You'll face distinct challenges when managing PCB production in arid versus temperate climates, each requiring specific control measures to maintain quality.
In arid regions, you must combat low humidity levels that increase ESD risks and affect component integrity. You'll need humidifiers and anti-static equipment while maintaining humidity above 30%.
For temperate climates, you're working within ideal conditions of 30-60% RH and 20-25°C, but you'll still need consistent monitoring and control systems.
Key challenges you'll encounter across different regions include:
- Maintaining precise humidity levels despite external weather fluctuations
- Protecting moisture-sensitive components during storage and assembly
- Managing ESD risks through proper grounding and anti-static measures
- Optimizing soldering processes for specific climate conditions
Whether you're operating in arid or temperate environments, you'll need to implement appropriate moisture control strategies. This includes using desiccants, protective coatings, and nitrogen-filled ovens during soldering.
You should also regularly calibrate your humidity sensors and maintain detailed environmental records to guarantee consistent manufacturing conditions regardless of regional climate challenges.
Tropical Manufacturing Environment Adaptations
Tropical environments present unique challenges that surpass those found in arid or temperate regions. You'll need to maintain strict temperature control between 20-25°C and keep humidity levels between 30-60% RH to protect your circuit boards. It's vital to implement real-time monitoring systems that track and adjust these conditions continuously.
You can combat moisture-related issues by incorporating multiple protective measures. Start by using desiccant drying agents and making certain of thorough cleaning of components before assembly.
You'll want to select materials specifically designed for moisture resistance, such as PTFE-based substrates or boards with acrylic and silicone coatings. Adding meshed copper planes will strengthen layer bonds and help prevent moisture penetration.
After assembly, you'll need to apply additional protection methods. Consider using conformal coatings to shield your PCBs from moisture and contaminants. For more robust protection, you can opt for thermoplastic overmolding or microencapsulation with epoxy.
If your application demands maximum protection, potting can completely enclose the PCB – just make certain the board is moisture-free before applying this method. Whatever protection you choose, proper storage and packing remain critical to maintaining board integrity.
Desert Climate Protection Methods
Scorching desert climates expose circuit boards to extreme challenges that demand specialized protection methods. You'll need to implement robust protection strategies to shield your PCBs from temperature extremes, humidity fluctuations, and dust contamination.
Start by selecting materials with low moisture absorption properties and increase component spacing to minimize moisture-related damage.
You'll want to incorporate effective thermal management systems and choose conformal coatings specifically designed for high-temperature environments.
Key desert climate protection measures include:
- Maintaining strict temperature control (20-25°C) during manufacturing
- Using sealing technologies like gaskets and silicone seals
- Implementing pre-baking procedures to remove excess moisture
- Conducting regular thermal and moisture testing
Your manufacturing environment must maintain relative humidity between 30% and 60% while ensuring a dust-free cleanroom setting.
Don't forget to establish proper storage conditions with controlled temperature and humidity levels.
Package your PCBs using moisture-resistant materials during storage and transportation.
Remember to select components with low moisture sensitivity and perform reliability testing to simulate long-term desert climate exposure for maximum protection.
Frequently Asked Questions
How Quickly Can Moisture Damage Occur in an Unprotected Circuit Board?
You'll find moisture damage can occur within hours in unprotected PCBs, as rapid absorption leads to immediate ionic corrosion. Even brief exposure to high humidity can trigger delamination and electrical performance issues.
Can UV Exposure Affect Moisture Sensitivity Levels in PCB Components?
While UV exposure won't directly affect your components' MSL ratings, it can degrade certain materials over time. You'll want to focus primarily on controlling humidity levels, as that's what determines moisture sensitivity in PCBs.
What Emergency Measures Exist if Humidity Control Systems Suddenly Fail?
You'll need to immediately implement bake-out procedures, seal boards with desiccants, halt production, and use portable dehumidifiers. Meanwhile, move sensitive components to climate-controlled areas and document all actions taken.
Do Different Solder Types Require Different Humidity Control Specifications?
Yes, you'll find that different solder types have varying humidity requirements. Lead-free solders typically need tighter humidity control (35-55% RH) than traditional lead-based solders (30-60% RH) for ideal performance and reliability.
How Do Vibrations Impact Moisture Absorption Rates in Circuit Boards?
You'll find limited direct research on vibration's effect on moisture absorption rates. However, vibrations can cause physical stress and cracking in PCBs, which may create new pathways for moisture to enter the board.
In Summary
You'll find that proper humidity control is essential for protecting your circuit boards throughout the manufacturing process. By implementing appropriate moisture prevention strategies, following MSL standards, and utilizing effective detection systems, you're safeguarding your PCBs from damage and ensuring top-notch quality. Don't overlook climate-specific considerations and ESD prevention – they're vital factors in maintaining reliable board production and reducing costly failures.
Leave a Reply