Your warehouse needs multiple layers of static control to prevent fires and explosions. Start with ionizers placed strategically in high-traffic areas and workstations to neutralize static charges. You'll need proper grounding systems, static dissipative surfaces, and monitoring equipment like handheld electrostatic meters to track static levels. Guarantee your team wears anti-static clothing and follows safety protocols, while maintaining well-ventilated spaces to reduce static buildup. Don't forget to implement real-time monitoring systems with IoT devices and sensors. Understanding the full scope of warehouse static protection can make the difference between safety and disaster.
Understanding Warehouse Static Risks
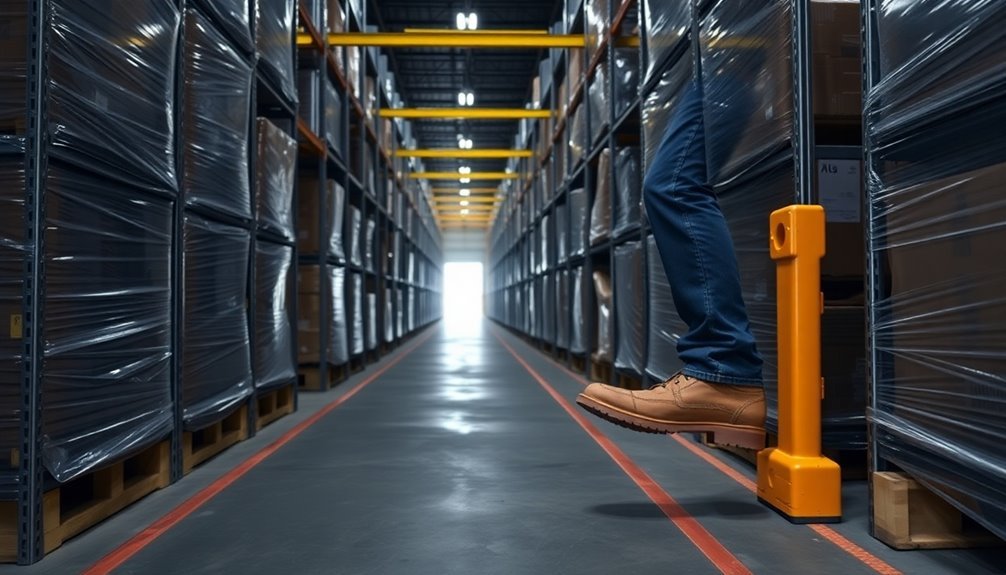
Most critically, you need to recognize that static electricity isn't just an operational nuisance – it's a safety hazard.
Static discharge can ignite flammable materials in your warehouse, creating a serious fire risk that endangers both your facility and personnel.
Regular movement and handling of non-conductive materials in warehouses can generate harmful static charges that build up over time.
Essential Static Control Equipment
Equipping your warehouse with proper static control devices forms the foundation of a thorough ESD protection strategy.
You'll need several key types of equipment to create a thorough static control system.
Start with ionizers, which neutralize static charges by generating both positive and negative ions. Bar-type ionizers work well for wide areas like entrances, while nozzle ionizers are perfect for confined spaces. Modern ionizers can achieve energy savings of 60% through efficient designs.
For monitoring purposes, you'll want to install static sensors like the IZH10 handheld electrostatic meter to diagnose and track static levels throughout your facility.
Don't forget to implement proper grounding systems, which should connect all ESD control materials to your equipment grounding conductor.
Your workstations need static dissipative surfaces with resistance to ground between 1.0 x 10^6 and 1.0 x 10^9 ohms.
For rapid static elimination, consider installing compact fan static eliminators like the SJ-LF Series, which can remove static in as little as 0.5 seconds.
To maintain effectiveness, you'll need to regularly check and maintain your equipment.
Install continuous monitoring devices like wrist strap testers and guarantee all components maintain the same electrical potential through a common point ground system.
Strategic Placement of Ionizers
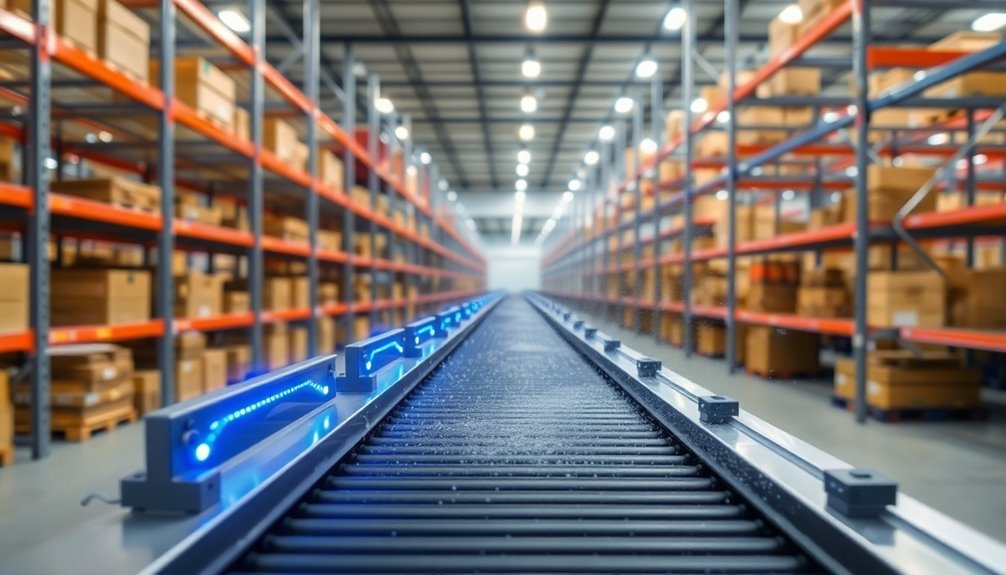
With meticulous planning, the strategic placement of ionizers can dramatically enhance your warehouse's static control efficacy. You'll want to position ionizers in high-traffic areas and near entrances to prevent static charges from spreading. For large spaces, think about installing overhead ionizing blowers and pods in a grid pattern to guarantee thorough coverage. Static attraction forces make simple air blowers ineffective on their own for removing particles.
Location | Recommended Solution |
---|---|
Entrances & Exits | Bar-type eliminators |
Workstations | Localized ionizers |
Large Open Areas | Overhead blower systems |
While room ionization was once the go-to solution, you'll achieve better results with localized workstation ionization. These units provide faster decay times and can be easily adjusted as your layout changes. For peak performance, place your ionizers just below ceiling height in fixed installations, and guarantee they're within 6" to 42" of target areas for workstation units.
Don't forget to ponder both pulse AC and lower frequency systems – they're particularly effective in larger spaces as they allow ions to travel further. When selecting your ionization equipment, make sure it meets ANSI/ESD S20.20 standards and factor in the total life cycle costs, including maintenance and operation expenses.
Personnel and Safety Measures
Safety protocols form the backbone of an effective static control program in your warehouse. You'll need to implement thorough safety measures that protect both your personnel and equipment from static-related hazards while maintaining general warehouse safety standards.
Start by confirming your employees wear proper protective gear, including anti-static clothing, gloves, and appropriate footwear.
You'll want to provide regular training sessions on static control procedures alongside general safety protocols. Make certain your staff understands the importance of reporting any static-related incidents or hazards they observe.
Keep your warehouse well-ventilated to reduce static buildup, and maintain clear aisles and workspaces to prevent accidents. Always ensure Material Safety Data Sheets are readily available and up-to-date for any chemicals or hazardous materials in your facility. Install proper guardrails and safety equipment in elevated areas where static discharge risks are higher.
You should also establish ergonomic workstations that consider both static control and employee comfort.
Implement a regular maintenance schedule for all static control equipment, including ionizers and grounding systems. Use detailed checklists during inspections to verify that all safety measures are functioning correctly.
Don't forget to clearly mark hazardous zones where static electricity poses a particular risk, and confirm emergency exits are easily accessible and well-marked.
Monitoring and Maintenance Systems
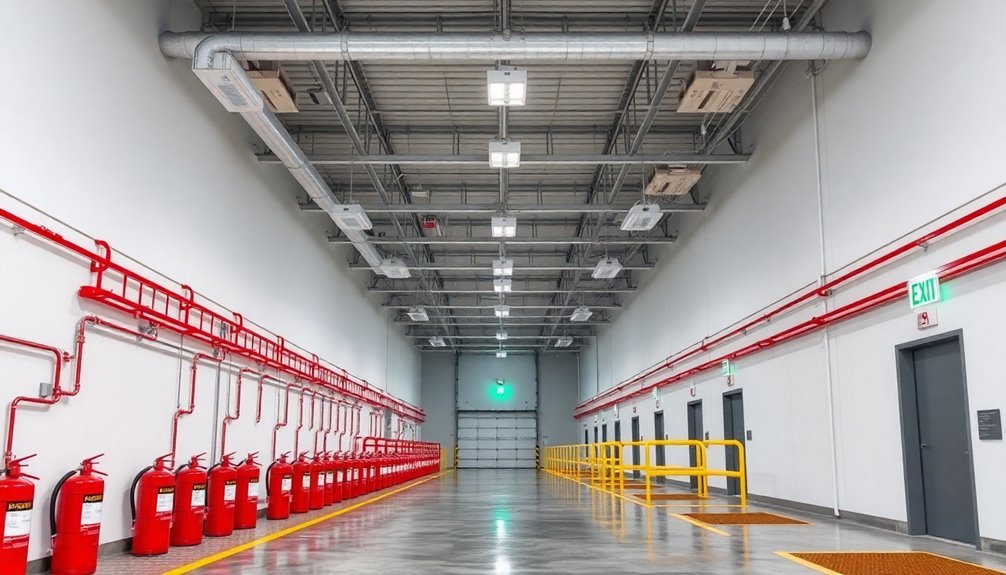
Modern monitoring and maintenance systems serve as your warehouse's central nervous system for static control management. By integrating IoT devices, RFID tags, and advanced sensors, you'll get real-time data about your facility's static conditions. These systems connect seamlessly with your existing warehouse management software, providing instant alerts and automated responses to potential static threats. Predictive analytics help optimize static control by forecasting potential issues before they occur.
Component | Function | Benefit |
---|---|---|
RFID Tags | Track inventory movement | Prevents static buildup in high-traffic areas |
IoT Sensors | Monitor humidity levels | Maintains ideal static-safe conditions |
UWB Technology | Precise location tracking | Identifies static-prone zones |
Temperature Sensors | Environmental monitoring | Controls static-generating conditions |
Data Analytics | Pattern recognition | Predicts potential static issues |
You'll need to implement scalable monitoring solutions that can grow with your warehouse operations. Your system should include centralized software that consolidates data from multiple sources, giving you a thorough view of static control effectiveness. Through customizable dashboards, you can track key metrics and make data-driven decisions about your static control measures. The integration of these technologies delivers improved ROI by reducing static-related incidents and maintaining consistent protection across your facility.
Frequently Asked Questions
How Long Do Static Control Ionizers Typically Last Before Needing Replacement?
You'll need to replace your ionizers every 1-2 years, though lifespan varies by type. With proper maintenance, including regular cleaning and testing, you can extend their life, but radioactive ionizers require yearly replacement.
Can Warehouse Static Control Equipment Operate Effectively in Extreme Temperatures?
Your static control equipment can operate in extreme temperatures, but you'll need specialized ionizers rated for -40°C to 180°C. Maintain proper humidity levels and use climate control systems for peak performance.
What Certifications Should I Look for When Purchasing Static Control Equipment?
You'll want equipment certified to ANSI/ESD S20.20 standards. Look for vendors with ESDA certification and verify that testing equipment meets international compliance standards. These certifications guarantee reliable performance and industry-accepted quality levels.
How Does Humidity Affect the Performance of Static Elimination Systems?
Higher humidity improves your static elimination systems' performance since moisture acts as a natural conductor. You'll get ideal results when you maintain 55% relative humidity alongside ionizers or other static control equipment.
Are There Specific Static Control Requirements for Handling Different Types of Materials?
Yes, you'll need different controls based on material properties. Use static-dissipative surfaces for electronics, conductive materials for grounding, and anti-static packaging for sensitive components. Follow industry-specific ESD protection standards.
In Summary
You'll need to regularly assess and update your warehouse's static control measures to maintain a safe working environment. Remember to test your ionizers, ESD mats, and grounding systems monthly, train your staff on proper static safety protocols, and keep detailed maintenance logs. By staying proactive with your static control program, you'll protect both your sensitive inventory and your workforce from potentially costly static discharge incidents.
Leave a Reply