The three most reliable ESD monitoring systems you'll find in manufacturing are Simco-Ion's Novx Series 7000, DescoEMIT's Continuous Monitors, and Static Clean's Guardian System. The Novx Series 7000 stands out with its thorough real-time monitoring and heat mapping capabilities. DescoEMIT's solution excels in continuous wrist strap and work surface testing, while Static Clean's Guardian System offers superior integration with existing factory systems. Each platform provides essential features like early detection, data logging, and compliance with international standards. Understanding the unique strengths of each system will help you make the best choice for your facility's needs.
Continuous ESD Monitoring Platforms
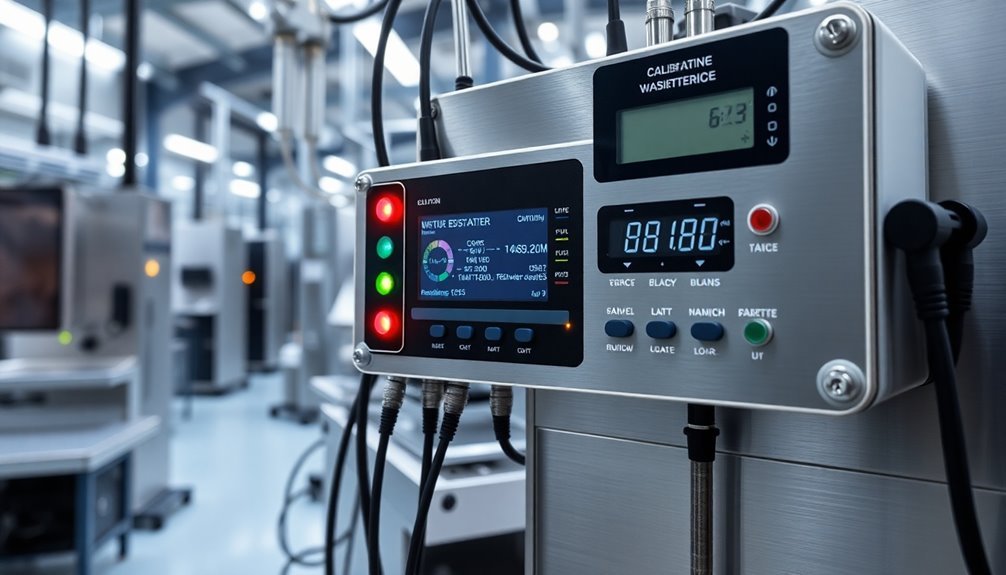
Modern continuous ESD monitoring platforms integrate sophisticated components to safeguard your manufacturing process against electrostatic discharge threats.
You'll find these systems equipped with ESD fieldmeters, analog-to-digital converters, and Ethernet interfaces that work together to provide real-time monitoring of static charge buildup.
The platforms utilize non-contact fieldmeters to track E-field data from ESD-susceptible items, converting this information into digital data that's uploaded to local servers. A combination of single and dual wire monitors ensures comprehensive coverage for various sensitivity levels. You can monitor your assembly line's static charge levels through detailed heat maps, helping you identify problematic areas immediately.
These systems don't just detect issues – they'll help you prevent them through early detection capabilities.
You can easily integrate these monitoring platforms with your existing manufacturing lines using off-the-shelf components and standard mounting methods.
The systems offer continuous testing of wrist straps and ESD protective worksurfaces while employing specific antenna configurations to detect pulse electromagnetic energy from ESD events.
With multiple power options, including battery operation, you'll maintain flexibility in your monitoring setup.
Plus, the platforms comply with ISO certification requirements and integrate seamlessly with your factory monitoring systems.
Embedded Static Detection Systems
While continuous monitoring platforms offer facility-wide protection, embedded static detection systems take ESD protection directly to the chip level.
You'll need to carefully select the right technology – whether it's on-chip, discrete, or software-based detection – to match your specific design requirements. Early functional validation samples are often scarce due to competing development needs. When implementing these systems, you'll want to focus on noise management and strategic sensor placement to guarantee reliable detection in EMI-heavy environments.
Testing your embedded detection system is vital before deployment. You can use mock-ups and evaluation boards to validate your design without risking damage to expensive equipment.
Don't forget to test under various temperature and voltage conditions to guarantee consistent performance across all operating environments.
- Use ESD generators to simulate events and verify detector response
- Implement real-time protection features to reduce soft errors and system upsets
- Integrate response mechanisms that trigger immediately upon ESD detection
- Document detector levels and ranges for different strike scenarios
- Consider collecting ESD event telemetry to optimize protection levels
Ionization Management Solutions
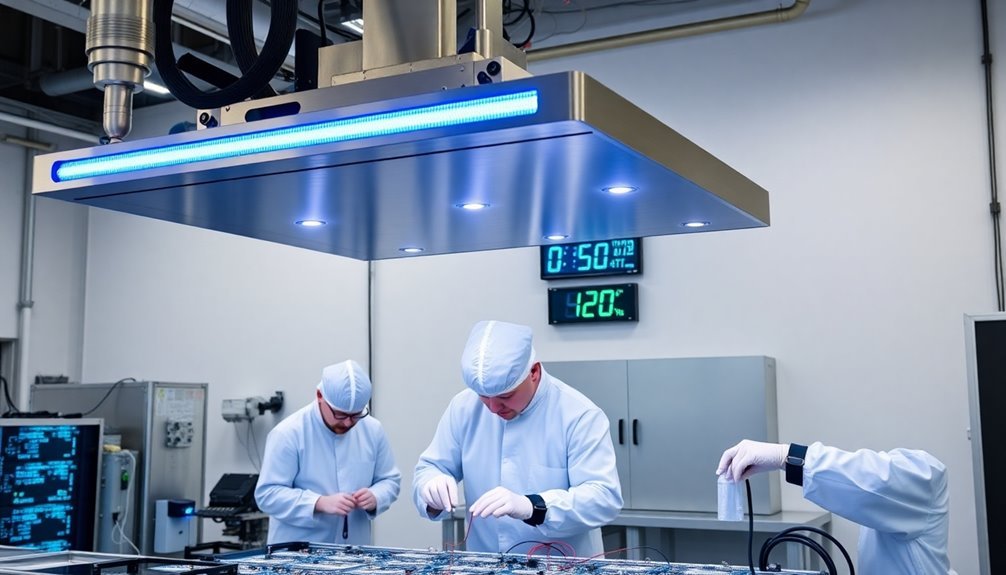
Through effective ionization management, you'll greatly reduce ESD risks in your manufacturing environment. To achieve ideal results, you'll need to follow key standards like ANSI/ESD S20.20 and IEC 61340-5-1 while implementing ionizers in your ESD protected areas (EPAs).
You'll want to start by identifying ESD-sensitive areas and determining the most effective ionizer placement. Choose between floor and overhead models based on your specific manufacturing needs and production area size. The Simco-Ion Novx Series 7000 Process Monitoring System can help you track electrostatic parameters and manage your ionizers effectively. Daily testing procedures are essential to ensure reliable ESD control and protection.
Remember that ionizer effectiveness depends heavily on proper grounding and regular maintenance. You'll need to calibrate your systems regularly and conduct facility surveys to verify they're working at peak performance.
Consider factors like airflow and humidity, as these can impact ionization performance.
For thorough protection, combine your ionization solutions with other ESD control methods. While ionizers are excellent at neutralizing charges on insulative materials, they work best as part of a complete ESD control strategy that includes grounding and dissipative materials.
Don't forget to implement continuous monitoring to track system performance and identify areas needing improvement.
Frequently Asked Questions
How Frequently Should ESD Monitoring Systems Be Recalibrated for Optimal Performance?
You'll need to recalibrate your ESD monitoring systems annually at minimum, but consider more frequent checks based on your equipment's usage, sensitivity of items handled, and specific production risks. Continuous monitoring requires periodic verification.
What Are the Power Backup Requirements for Continuous ESD Monitoring Systems?
You'll need stable 120 VAC power with battery backup systems to maintain continuous operation. Make certain your ESD monitoring system includes uninterruptible power supplies and emergency batteries to prevent monitoring gaps during outages.
Can Multiple ESD Monitoring Systems Interfere With Each Other's Readings?
Yes, your ESD monitoring systems can interfere with each other. You'll need proper isolation techniques, standardized configurations, and compatible equipment to prevent false readings and guarantee accurate monitoring across multiple systems.
What Environmental Factors Affect the Accuracy of ESD Monitoring Measurements?
Your ESD monitoring measurements are considerably affected by temperature changes, humidity levels, lighting conditions, and air quality. You'll need to control these factors to guarantee your measurements stay accurate and reliable.
How Long Do ESD Monitoring System Sensors Typically Last Before Replacement?
You'll need to replace your ESD monitoring sensors every 1.5 to 2 years under normal conditions. If you're using them for critical applications or certification purposes, plan on annual replacements to maintain accurate measurements.
In Summary
You'll find today's ESD monitoring solutions have evolved dramatically to protect your manufacturing operations. Whether you choose continuous monitoring platforms, embedded detection systems, or ionization management solutions, they all offer robust protection against static discharge threats. Consider your facility's specific needs and budget when selecting from these top options to maintain the integrity of your sensitive electronic components and production processes.
Leave a Reply