Ion decay testing requires strict adherence to industry standards like EIA/JEDEC EIA/JESD 57A and MIL-STD 883J Method 1019.9. You'll need to maintain precise environmental conditions of 23°C ± 2°C and 12% ± 3% RH while ensuring proper equipment calibration every six months per JESDD625-A guidelines. Your testing setup must include field meters and CPM tools for evaluating ionizer performance, with decay measurements from 1000V to 100V. Quality control measures include daily background checks, voltage consistency monitoring, and detailed record keeping. The complex interplay of standards, equipment, and procedures forms just the foundation of effective ion decay testing practices.
Understanding Ion Decay Test Standards
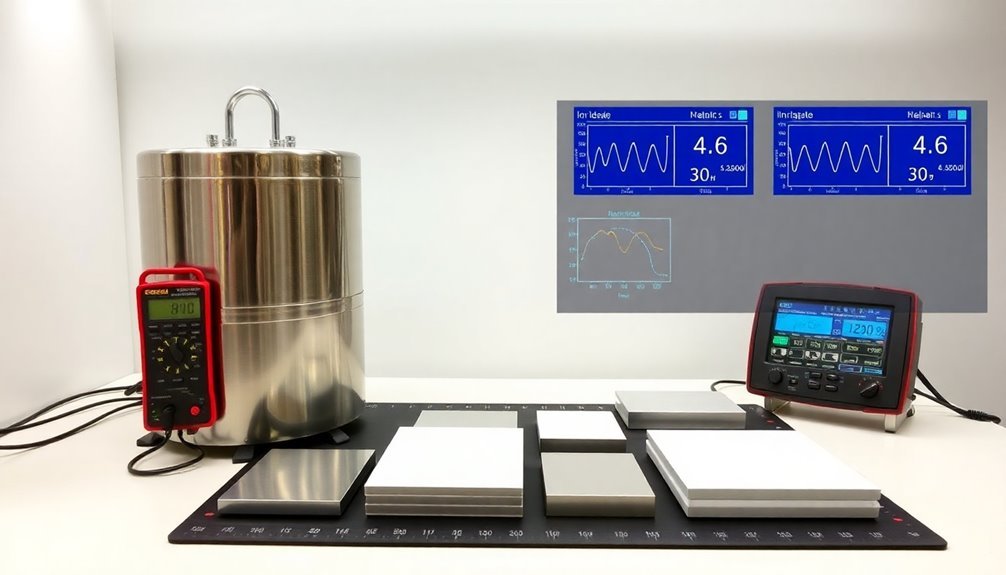
Ion decay testing's standardization relies on several established protocols, with EIA/JEDEC EIA/JESD 57A serving as the primary framework for measuring single-event effects in semiconductor devices.
When you're conducting these tests, you'll need to follow strict guidelines for heavy ion irradiation procedures and measurement techniques. Similar to ion chromatography methods used in fluoride analysis, precise calibration and monitoring are essential. MIL-STD 883J Method 1019.9 complements this framework by providing essential guidelines for steady-state total dose irradiation testing.
Modern ion traps can collect data from 1,000 to 1 million ions for highly accurate measurements. You'll find that test conditions must meet specific requirements to guarantee accuracy. These include maintaining dose rate calibration within 5% variation and field uniformity within 10%.
The testing environment can be either a vacuum chamber or air-based, depending on your device configuration. You'll need to monitor temperature conditions carefully, typically maintaining them at 20°C ± 10°C.
While standards like ASTM D6908-03 exist for pressure decay testing in water filtration systems, they're not directly applicable to ion decay testing.
Instead, you'll want to focus on the specific requirements for semiconductor testing, which include proper sample preparation techniques like delidding or decapsulation.
These standards guarantee your test results are reliable, reproducible, and recognized within the industry.
Equipment Calibration and Setup
Equipment Type | Key Advantages | Regular Checks | Calibration Frequency |
---|---|---|---|
Field Meter | Portable, field-friendly | Clean sensors weekly | Semi-annually |
CPM | High precision, built-in timer | Verify plate isolation | Semi-annually |
Test Kit | Cost-effective testing | Check charging unit | Semi-annually |
Verification Tools | Compliance assurance | Inspect connections | Before each use |
To maintain accuracy, you must calibrate your equipment semi-annually following JESDD625-A and ANSI/ESD STM3.1 guidelines. When setting up for measurements, position your ionizer and CPM as specified in the standards, then set the CPM to Decay/Offset mode. Don't forget to record all calibration data to justify your maintenance schedules. If your measurements fall outside the ±35 volts offset voltage limit specified by ANSI/ESD S20.20, you'll need to service your equipment immediately.
Testing Environment Requirements
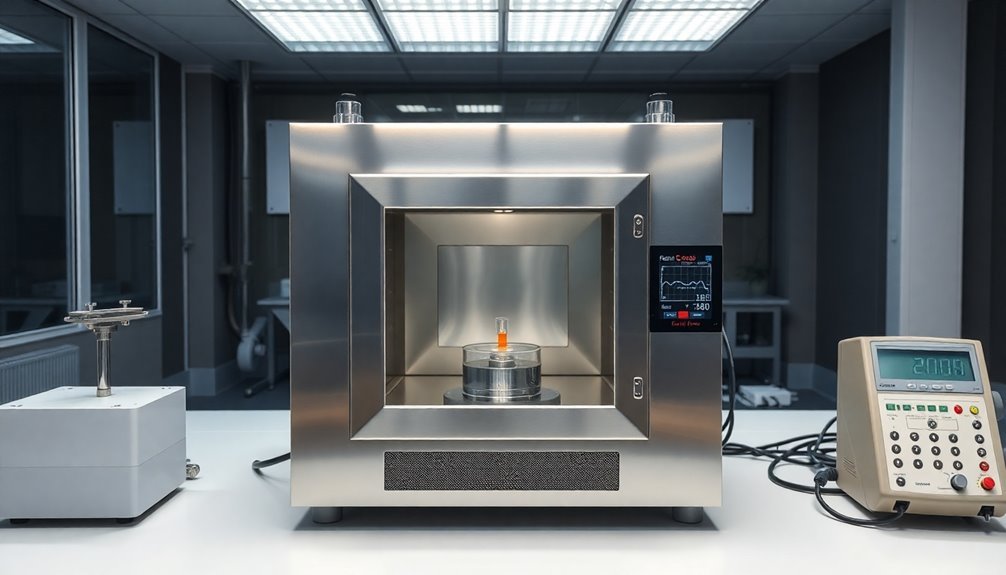
Testing demands precise environmental control to guarantee accurate and repeatable results.
You'll need to maintain a temperature of 23°C ± 2°C and humidity levels of 12% ± 3% RH throughout your qualification tests. These conditions must remain stable to secure measurement consistency. Studies show that decay rate variations can occur under different ionization conditions, similar to effects seen in highly charged ions.
Airflow plays an essential role in your testing environment, as it affects ion distribution and measurement accuracy. Regular offset voltage verification helps ensure ionizer performance remains within acceptable limits of ±35V.
You'll want to establish laminar airflow while avoiding drafts that could disrupt readings. If you're testing in a cleanroom setting, remember that air ionization might be your primary ESD control method due to limited grounding options.
You must carefully consider proximity and interference factors.
Keep metal objects away from the test area, as they can alter electric fields and skew results. Position your testing equipment away from external sources of static and electrical interference to maintain measurement integrity.
To guarantee compliance, you'll need to follow industry standards like IEC 61340-4-7 and ANSI/ESD STM3.1.
Document all test conditions and results thoroughly for future reference and regulatory requirements. Your testing area should be free from significant temperature gradients and maintain consistent environmental controls throughout the testing process.
Quality Control Measures
With your testing environment properly configured, implementing rigorous quality control measures safeguards the reliability of your ion decay results. You'll need to perform daily background reading checks and evaluate voltage supply consistency, flagging any variations exceeding 5%. It's essential to conduct constancy tests using standard check sources like Co-57 or Cs-137 to verify calibration settings and chamber stability. Following established gamma camera uniformity protocols helps maintain measurement consistency across testing sessions. Modern Geiger-Müller counters provide precise detection capabilities for these measurements.
Your annual accuracy tests shouldn't deviate more than ±5% from certified activity values, while quarterly precision tests help identify any issues with background changes or power fluctuations. You'll want to use long-lived radioisotopes for reproducibility tests, maintaining variations within ±1%.
Test Type | Frequency | Acceptable Variation |
---|---|---|
Accuracy | Annual | ±5% |
Precision | Quarterly | ±5% |
Linearity | Annual | ±10% |
For linearity testing, you'll use Tc-99m sources and measure activities over 36 hours at 1-hour intervals. Document all test results and corrective actions in your quality assurance records. Remember to include various professionals in your QA committee reviews, making quality control a collaborative effort rather than an individual responsibility.
Advanced Testing Applications
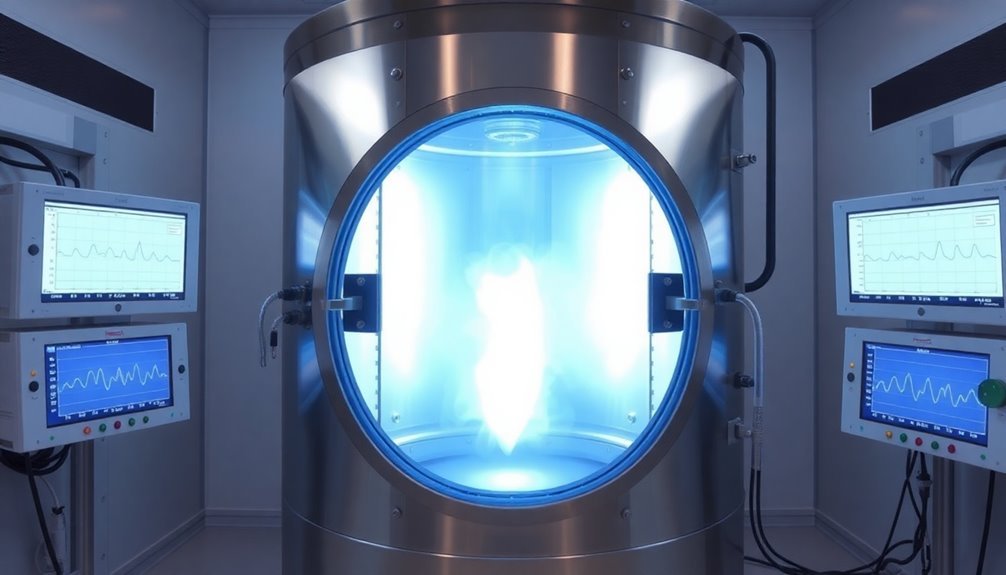
Advanced ion decay applications leverage sophisticated techniques that combine ion trapping with precision detection systems. You'll find that these systems suspend radioactive isotopes in a vacuum while using alternating electric fields to confine them, allowing for precise measurements of beta particles and gamma rays during decay events.
When you're working with highly charged ions, you'll need specialized equipment like storage rings and electron-ion beam traps. These setups let you control ion temperatures through various cooling methods, including electron, stochastic, and laser cooling, while studying how electron density influences decay processes.
You can apply these techniques to investigate specific decay phenomena, such as beta decay and beta-delayed neutron emission. For example, you'll see this in experiments using xenon-137 and lithium-8 ions, where you can determine neutrino ejection angles and track all decay particles.
For practical applications in ionization system testing, you'll use decay testers to evaluate system performance. These instruments measure charge dissipation time and perform essential tests for ion balance and humidity levels.
You'll find this particularly useful when determining maintenance schedules and gauging system effectiveness.
Frequently Asked Questions
How Long Does Operator Training Typically Take to Achieve Testing Certification?
You'll need between several hours to multiple days for operator testing certification, depending on your prior experience, equipment complexity, and specific requirements. Training includes both hands-on practice and theoretical knowledge.
What Are the Average Maintenance Costs for Ion Decay Testing Equipment?
You'll typically spend 5-15% of your equipment's purchase price on annual maintenance. For a $10,000 system, that's $500-$1,500 per year, including calibration, repairs, and replacement parts.
Can Ion Decay Testing Be Performed Simultaneously on Multiple Components?
You can test multiple components simultaneously, but you'll need to carefully control cross-contamination and guarantee separate detection systems for each sample. It's technically possible but requires precise planning and monitoring.
How Often Do False Positives Occur in Automated Ion Decay Testing?
You'll typically encounter false positives in 2-5% of automated tests, but your rates can vary based on instrument calibration, sample complexity, and chosen monitoring parameters. Regular validation helps minimize these occurrences.
What Backup Procedures Exist if Equipment Fails During Critical Testing Cycles?
You'll need to immediately switch to calibrated backup equipment or an approved external facility. Confirm you've validated the alternate system, run quality controls, and duplicate recent results before continuing critical testing cycles.
In Summary
You'll find ion decay testing essential for maintaining quality control in static-sensitive environments. By following industry standards, calibrating your equipment regularly, and maintaining proper testing conditions, you're ensuring accurate and reliable results. Remember to document your procedures, stay updated on the latest testing protocols, and implement rigorous quality control measures. When you're consistent with these practices, you'll achieve ideal testing outcomes.
Leave a Reply