When you need reliable magnetic warning labels, choose from these top 7 options: MagnaGuard Pro with UltraTuff coating, SafetyFirst UV-resistant labels, DuraMag chemical-resistant series, FlexiMag repositionable warnings, ToughGuard high-temperature labels, MRI-Safe magnetic notices, and Universal ANSI-compliant warnings. Each features standardized headers like "DANGER" or "WARNING," clear graphics, and durable materials that resist fading and wear. You'll find options rated from -40°F to 160°F, with fade-resistant inks and protective lamination for long-term use. Understanding the specific features of each label type will help you make the safest choice for your facility.
Essential Safety Features
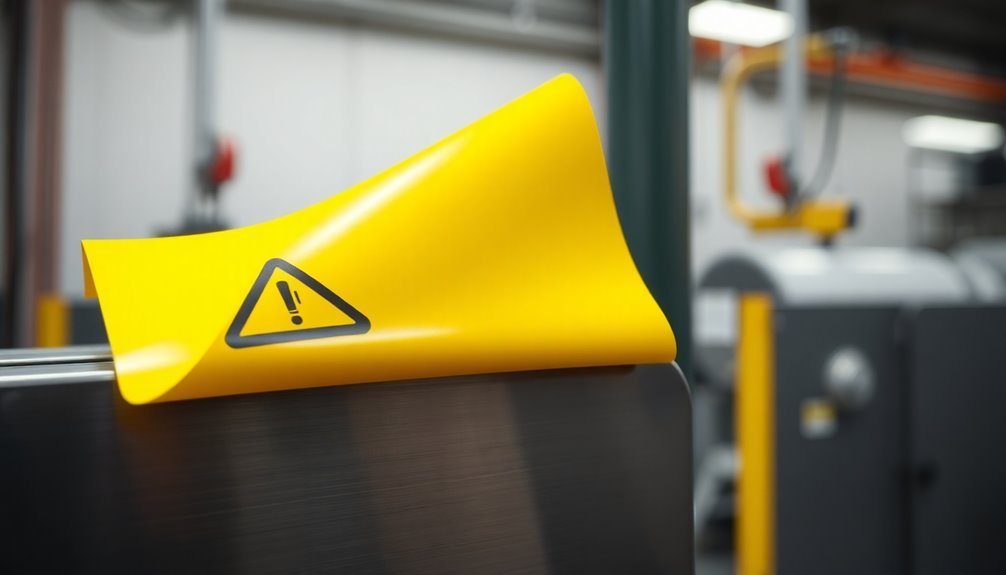
Safety stands at the forefront of magnetic warning label design, incorporating multiple critical features that protect lives and prevent accidents. ANSI-compliant warning labels use standardized headers like "DANGER," "WARNING," and "CAUTION" to clearly communicate the severity of potential hazards you might encounter.
These labels feature durable materials with UltraTuff overlaminate protection, guaranteeing they won't fade or smear in harsh weather conditions. You can rely on their clear graphics and text to detail specific hazards and access restrictions. ISO 7010 standards ensure consistent symbol recognition across different facilities.
Standardized safety symbols make them easily understandable regardless of your language background. When you're working with equipment that generates strong magnetic fields, you'll notice these labels are designed specifically to alert individuals with pacemakers and other implanted devices about potential risks.
The labels' high-quality construction guarantees they'll remain visible and effective throughout long-term industrial use. You'll see that they're available in various sizes to suit different applications, and their pictograms enable quick recognition of hazards.
Types of Magnetic Warning Labels
Throughout industrial and medical facilities, magnetic warning labels come in several distinct categories to address specific safety concerns.
You'll encounter standard warning and caution labels that alert personnel to the presence of strong magnetic fields, while specialized labels like "No Pacemakers" provide critical warnings for individuals with medical devices.
For MRI facilities, you'll need specific warning labels that comply with strict safety protocols. These labels clearly mark restricted areas and remind staff about the dangers of bringing metal objects near the equipment. These signs commonly specify a safe distance of 36" for individuals with medical implants.
Each label features universally recognized symbols and standardized colors that make hazard identification immediate and clear.
You can choose from various materials, including durable vinyl and polyester options that won't deteriorate in demanding environments. The labels come in different sizes to suit your specific application, and they're equipped with high-strength adhesives to secure them firmly in place.
All labels meet ANSI standards and incorporate ISO 7010 symbols for international recognition.
For enclosed areas with static magnetic fields, you'll want to use specialized labels that specifically warn about these conditions. They're particularly important in research facilities and industrial settings where magnetic equipment operates continuously.
Proper Surface Application Methods
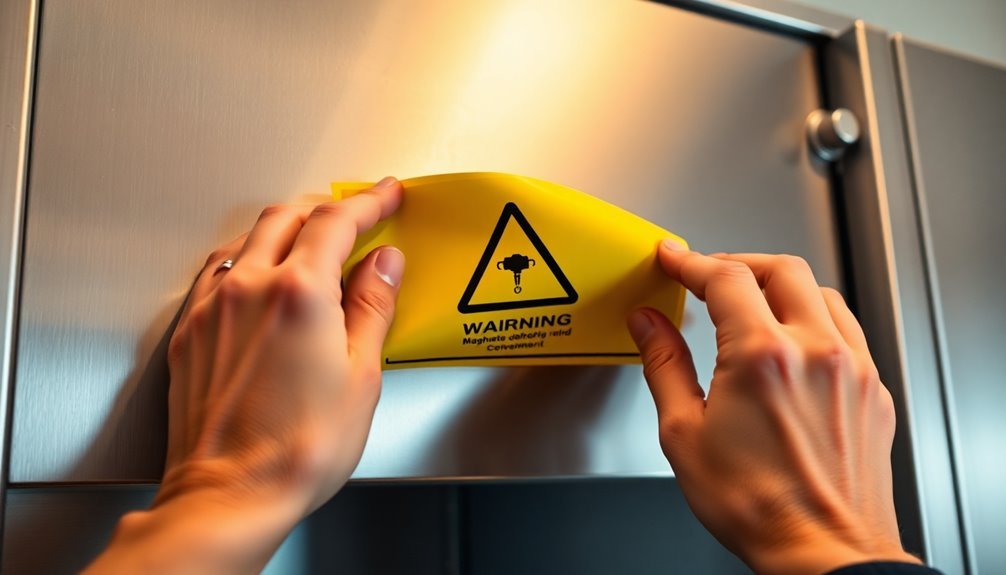
A successful magnetic warning label installation begins with proper surface preparation and application techniques. You'll need to guarantee the surface is clean, dry, and free from any contaminants that could affect adhesion. Before applying your magnetic warning label, check that the surface is both flat and made of ferromagnetic material like steel. These labels are designed to meet OSHA safety standards while providing clear hazard communication on metal surfaces.
When applying the label, carefully peel back the protective backing and align it properly before making contact. Apply firm, even pressure across the entire surface to prevent air bubbles or wrinkles. Don't stretch the label during application, as this can compromise its adhesive properties.
Surface Prep Steps | Application Tips |
---|---|
Clean thoroughly | Align before contact |
Guarantee complete dryness | Press firmly and evenly |
Check surface flatness | Avoid stretching |
Verify material compatibility | Remove air bubbles |
Control temperature | Inspect final result |
For enhanced adhesion, you can lightly sand the surface or use adhesion promoters for challenging surfaces. If you need to remove and reuse the label later, pull it off slowly and evenly to maintain its integrity. Store any removed labels in a clean, dry place and inspect them for damage before reapplication.
Weather Resistance Properties
Once you've properly applied your magnetic warning labels, understanding their weather resistance capabilities helps guarantee long-term performance. These labels are engineered to withstand multiple environmental challenges, protecting your safety messages in various conditions.
You'll find that quality magnetic warning labels offer extensive chemical resistance, preventing degradation when exposed to harsh substances. They won't discolor or peel off when they come into contact with industrial chemicals, and they'll maintain their adhesive properties throughout exposure. The labels can be easily cleaned with water or mild detergent to maintain their appearance and readability.
The labels' water-resistant properties confirm they'll stay firmly in place even in wet conditions. You won't need to worry about water penetrating the adhesive layer or compromising the label's integrity during long-term moisture exposure.
They're also designed to handle UV radiation, so you won't experience fading or deterioration when using them outdoors.
Temperature resistance is another vital feature you can count on. Your magnetic warning labels will perform effectively across a wide temperature range, resisting both high and low extremes without becoming brittle or losing their magnetic properties.
This thorough weather resistance confirms your safety messages remain clear and effective, regardless of environmental conditions.
Durability and Material Quality
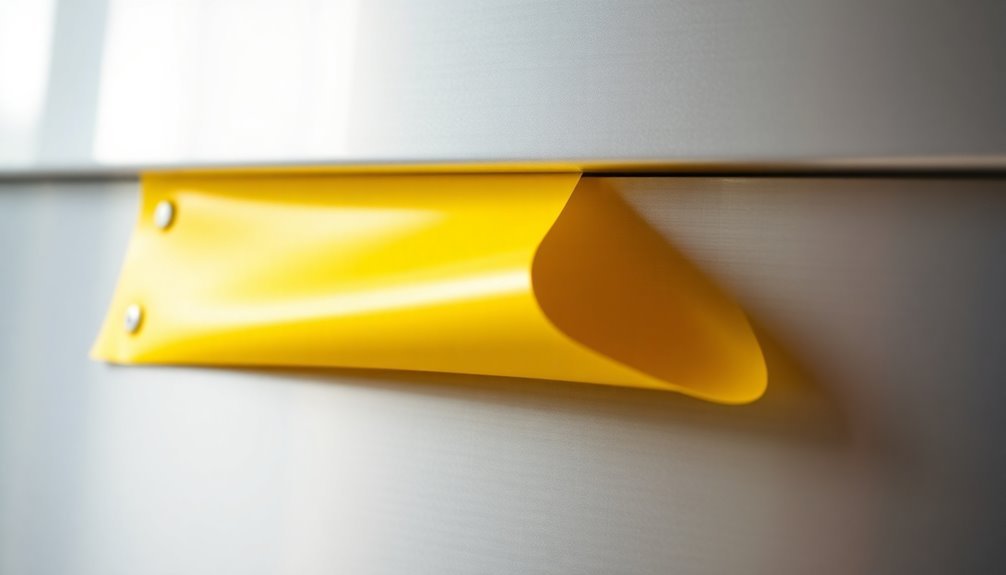
Every component of magnetic warning labels is engineered for maximum durability and longevity. You'll find that these labels utilize high-grade magnetic vinyl and polyester materials that remain stable in temperatures ranging from -40°F to 160°F. Regular cleaning and inspection helps maintain the magnetic warning labels' effectiveness and extends their usable life.
The lead-free composition guarantees both safety compliance and environmental responsibility, while the absence of plasticizers prevents cracking and deterioration over time.
With proper maintenance, you can expect your magnetic warning labels to last up to 5 years. The labels' durability stems from multiple quality features: fade-resistant inks that maintain visibility, protective lamination that guards against scratches and abrasions, and a strong magnetization of +/- 0.002 that guarantees secure adhesion to metal surfaces.
You'll notice that manufacturers prioritize quality control by adhering to strict regulatory standards, including ROHS, CROHS, and REACH compliance.
The materials used don't just meet basic requirements – they're specifically chosen for industrial applications where reliability is vital. You can trust that each label's construction incorporates expert design principles, guaranteeing that your safety messages remain clear and effective throughout the product's lifecycle.
The combination of premium materials and manufacturing standards delivers consistent performance in demanding environments.
ANSI Compliance Requirements
Strong magnetic warning labels must also meet rigorous ANSI compliance requirements to be legally usable in workplaces. You'll need to guarantee your labels follow specific color-coding standards: red (PMS485) for danger, orange (PMS144) for warning, yellow (PMS109) for caution, and blue (PMS2935) for notice or information.
Your magnetic labels must incorporate standard signal words like "DANGER," "WARNING," or "CAUTION" based on the hazard level. Each label should feature three key components: a safety header with the appropriate signal word, clear safety symbols or pictograms, and a message panel that identifies the hazard, its consequences, and how to avoid it. The materials used for these labels must be UV and chemical resistant to ensure longevity in various industrial environments.
When designing your magnetic warning labels, you'll need to follow ANSI Z535.4 standards for text formatting. Use headline-style text, active voice statements, and left justification to maximize readability.
Don't forget that your labels must maintain their compliance even after repeated removal and reattachment. The text, symbols, and colors should remain clear and legible despite regular handling, and the magnetic material shouldn't compromise any of these ANSI-mandated design elements.
Best Placement Practices
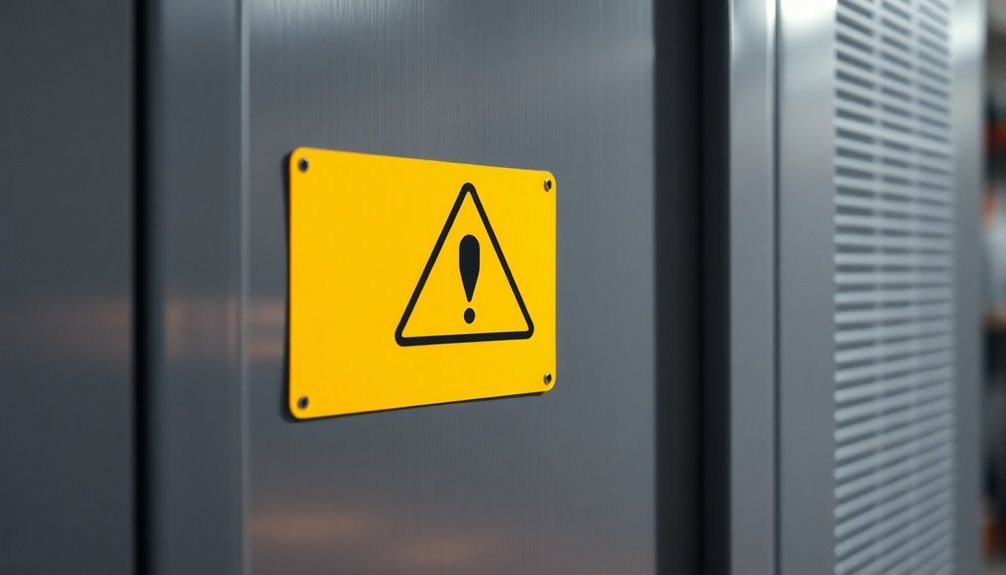
Proper placement of magnetic warning labels can make the difference between safety and potential accidents. You'll need to think about strategic locations, visual clarity, and environmental factors when installing these essential safety markers.
Start by identifying all access points where magnetic fields exceed 5 G and mark them clearly. You'll want to position labels where they're visible before anyone approaches the hazard zone. Don't forget to include a field strength map in a prominent location. Signal words like "DANGER" should be included on labels to quickly convey the risk level.
Placement Factor | Key Consideration |
---|---|
Distance | Must be readable from intended viewing range |
Surface | Clean and obstruction-free area |
Environment | Protected from damage and weathering |
Height | Eye-level placement when possible |
Lighting | Adequate illumination for visibility |
Choose labels with internationally recognized symbols and make certain they're made from durable materials that can withstand your specific environment. You'll need to incorporate specific warnings for those with pacemakers and other medical devices.
Remember to regularly inspect your warning labels for damage or wear. If you're working in a diverse workplace, think about using multilingual options to make certain everyone understands the hazard warnings.
Storage and Handling Guidelines
Taking care of your magnetic warning labels extends beyond placement – you'll need to implement specific storage and handling practices to maintain their effectiveness.
Store your labels in a controlled environment that protects them from extreme temperatures, humidity, and direct sunlight. When you're not using them, keep them in a clean, dry area to prevent moisture damage and maintain their adhesive properties.
During installation, guarantee the surface is completely clean and dry before applying the labels. Don't overload magnetic labels with excessive weight, as this can cause them to detach and create safety hazards. You'll want to follow the manufacturer's guidelines precisely for proper installation and maximum longevity.
Make it a routine to inspect your labels regularly for signs of wear, fading, or detachment. If you're working in harsh industrial environments, pay special attention to chemical exposure and temperature fluctuations that might affect label performance.
When handling the labels, avoid bending or creasing them, as this can compromise their magnetic properties. If you notice any damage or deterioration, replace the labels immediately to maintain safety compliance and effective hazard communication.
Removal and Reuse Tips
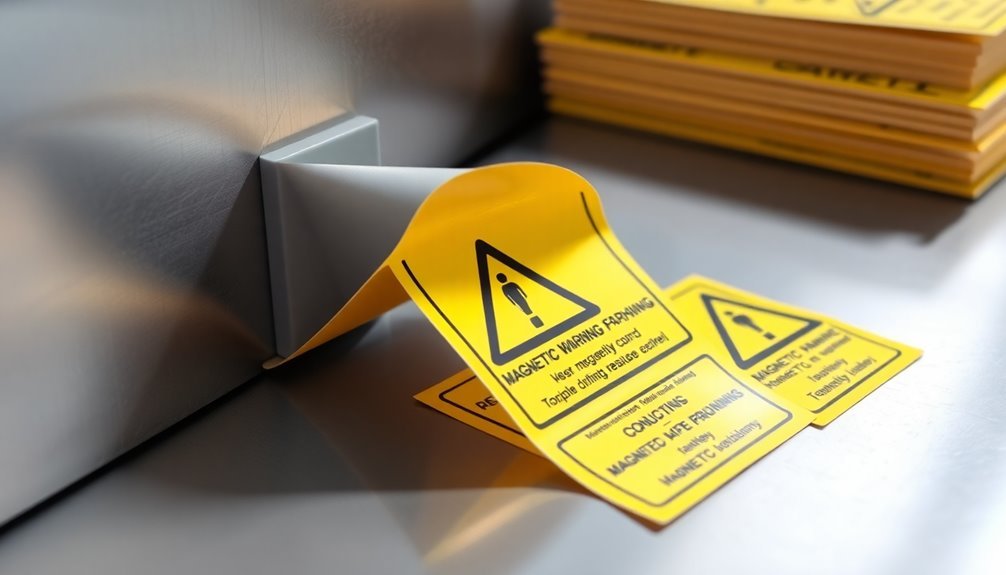
Safe removal and reuse of magnetic warning labels requires careful attention to detail and the right techniques.
When you're ready to remove a magnetic label, work on a clean, flat surface to prevent damage to both the label and the surface it's attached to. You'll want to start at one corner, gently lifting the magnet while keeping it parallel to the surface to avoid bending or warping.
To guarantee your magnetic labels remain reusable, don't pull them off abruptly, as this can strain the magnetic material. Instead, peel them away slowly and steadily.
Once removed, store your magnetic labels by placing them on a metal surface or keeping them flat in a dry location away from electronics. If you're dealing with multiple labels, don't stack them directly on top of each other, as this can weaken their magnetic properties.
Before reapplying your magnetic labels, clean both the label and the intended surface thoroughly. Check for any damage or wear that might affect adhesion.
When reapplying, align the label carefully and press it down gradually from one end to the other to prevent air bubbles and guarantee proper attachment.
Common Field Strength Indicators
Magnetic field strength indicators allow you to verify the effectiveness of warning labels and guarantee proper magnetization levels. You'll find several tools to measure magnetic field strength, each serving specific purposes in quality control.
Gauss meters and Hall effect gages help you measure tangential field strength on your test object's surface. These devices assess field intensity in the air adjacent to components and guarantee balanced field strength in multiple-direction magnetization. You'll need them to confirm if your magnetic field meets required specifications.
When you need to demonstrate both field strength and direction, QQIs serve as artificial flaw standards. These thin steel shims come with etched patterns and work best with wet testing methods, activating when magnetization reaches at least 30 gauss.
For basic field strength assessment, you can use slotted strips. They'll give you a general indication of field strength in specific areas and work with both wet and dry methods. Keep in mind they're limited to single-direction testing.
Understanding measurement units is vital. You'll encounter magnetic field strength (H) in amperes/meter, flux density (B) in teslas or gauss, and magnetic flux (f) in webers or maxwells.
Customization and Size Options
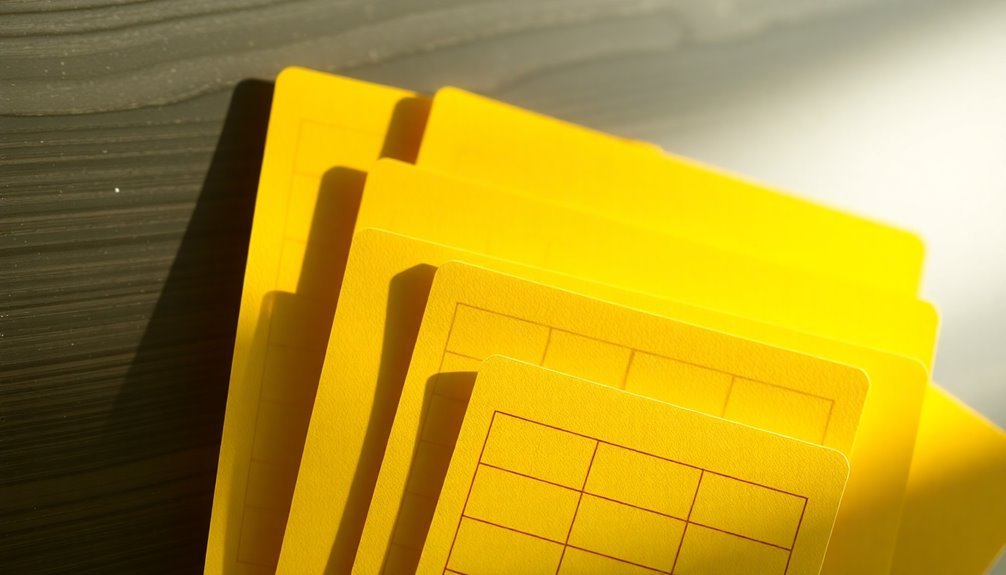
When it comes to warning labels, you'll find extensive customization possibilities to match your specific requirements. You can select from multiple label materials and create custom signs without incurring additional charges.
If you need multilingual warnings, you can opt for translations in French (Canadian) or Spanish (Mexican), ensuring clear communication across diverse workforces.
The magnetic hazard labels come in three standard sizes: 1-1/2", 2-1/2", and 4-1/2", with a minimum size requirement of 4.00" x 4.00" for specific warning labels. You can also request custom sizes based on your viewing distance and legibility needs.
For material options, you'll have access to durable, self-adhesive vinyl with either standard or Super-Stik adhesive, depending on your surface requirements.
These industrial-grade materials resist UV rays, water, and chemicals, making them suitable for indoor, industrial, and outdoor environments. You won't struggle with application – the peel-and-stick design allows for quick setup on various surfaces like metal, wood, and concrete.
When you need to remove the labels, they'll come off cleanly without leaving behind messy residue.
Regulatory Standards
The regulatory landscape for removable magnetic warning labels encompasses several critical standards and guidelines. You'll need to verify your labels comply with CPSC safety standards, ASTM F963-17 requirements, and ANSI Z535 specifications for safety signs.
When selecting magnetic warning labels, you must verify they meet the CPSC's flux index requirements of less than 50 kG² mm² for any separable magnets that fit within a small parts cylinder. You're also required to follow specific testing procedures outlined in ASTM F963 sections 8.25.1 through 8.25.3.
Your warning labels should clearly indicate magnetic field strengths, particularly when they exceed 5 G, and include access restrictions for areas with strong magnetic fields. It's essential that you use durable materials that can withstand environmental conditions while maintaining legibility.
If you're planning to sell internationally, you'll need to take into account additional requirements, such as Canada's CCPSA regulations.
Don't forget to maintain proper documentation, including certificates of compliance (CPC or GCC), unless your products fall under educational, research, professional, or industrial exclusions. Stay current with regulatory updates to maintain continued compliance.
Frequently Asked Questions
Can Magnetic Warning Labels Interfere With Electronic Equipment Nearby?
You shouldn't worry about warning labels themselves causing interference. While they're only mildly magnetic, they serve to warn you about stronger magnetic fields nearby that could actually affect your electronic equipment.
How Often Should Magnetic Warning Labels Be Inspected and Replaced?
You'll need to inspect magnetic warning labels monthly for physical damage and every 6 months near high-intensity fields. Replace them immediately if they're worn, faded, or damaged to maintain safety compliance.
Are Magnetic Warning Labels Effective Through Protective Coverings or Paint?
You'll find magnetic warning labels lose effectiveness through protective coverings or paint. They'll work through thin layers, but thick coatings substantially reduce their magnetic strength and visibility, making them less reliable for safety purposes.
Do Magnetic Warning Labels Lose Strength When Repeatedly Removed and Reapplied?
Yes, you'll notice magnetic warning labels gradually lose strength with repeated removal and reapplication. The constant handling causes material fatigue, physical wear, and adhesive degradation, weakening their magnetic properties over time.
Can Magnetic Warning Labels Be Safely Used on Curved or Irregular Surfaces?
Yes, you can safely use magnetic warning labels on curved surfaces. They're made with flexible materials that conform to irregular shapes while maintaining strong adhesion. You'll get reliable performance as long as the surface is ferrous metal.
In Summary
Magnetic warning labels provide essential safety messaging that you'll need for various workplace and industrial settings. Choose labels with strong field strength, weather-resistant materials, and clear visibility to guarantee maximum protection. When you're selecting from these top seven options, consider your specific surface requirements and environmental conditions. Remember, you can easily reposition these labels while maintaining their effectiveness in protecting workers and equipment.
Leave a Reply