Non-metallic static protection packaging solutions give you powerful ESD defense while cutting costs. Though initial investments may be higher, you'll save considerably through reduced product damage, fewer returns, and lower shipping expenses. You can choose from anti-static, dissipative, conductive, or static shielding materials – each offering specific protection levels for your electronics, medical devices, or aerospace components. These recyclable solutions are lighter and more versatile than metallic alternatives, adapting easily to your unique packaging needs. With the electronics industry facing $5 billion in annual ESD losses, exploring these innovative solutions could transform your bottom line.
Cost Benefits and Market Value
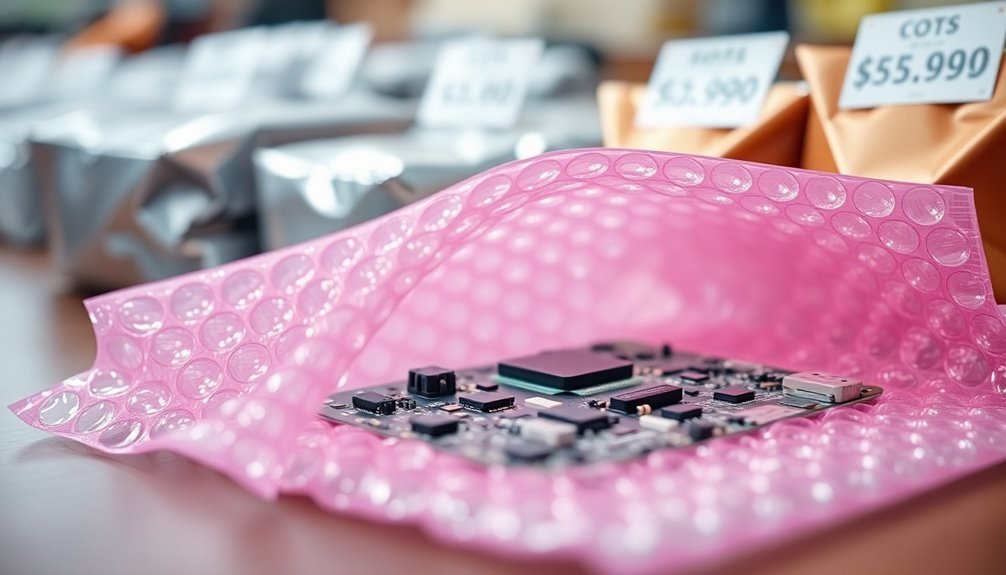
Non-metallic static protection packaging breaks down into a compelling cost-benefit equation for businesses.
While you'll face higher initial costs, the long-term savings greatly outweigh this investment, particularly when you consider that electrostatic discharge damage costs the electronics industry up to $5 billion annually.
You're looking at reduced damages, lower packaging expenses, and fewer product returns that can cut losses by up to 33%.
You'll see immediate benefits in your operational efficiency as you won't need to handle as many returned goods or process replacement orders. Using proper anti-static solutions can protect against static charge transfer that commonly occurs through friction and contact. An estimated 25% of failures in electronic parts can be directly attributed to electrostatic discharge damage.
The packaging's reusability adds another layer of cost advantage, helping you maximize your return on investment while meeting essential industry standards for automotive, aerospace, and medical sectors.
Your customers will also be more satisfied when they receive undamaged products, which directly impacts your bottom line through repeat business and reduced reverse logistics costs.
Types of Non-Metallic Protection Materials
While cost considerations play a key role in packaging decisions, selecting the right type of static protection material determines your success in safeguarding sensitive components. You'll find four main categories of non-metallic static protection materials, each serving specific protection needs and applications. Non-metallic materials like amine-free polyethylene provide excellent protection without causing corrosion or outgassing issues. These materials have seen continuous technological advancements to improve their protective capabilities.
Material Type | Key Features |
---|---|
Anti-Static | Prevents static buildup; pink/black colored; humidity independent; suitable for non-critical applications |
Dissipative | Slows electricity flow; pink colored; uses humectant additives; ideal for ESD-safe environments |
Conductive | Channels charges away; black colored; excellent durability; perfect for static-sensitive electronics |
Static Shielding | Provides Faraday Cage protection; metallic appearance; low MVTR; best for highly sensitive devices |
When choosing your packaging solution, you'll need to match the protection level with your product's sensitivity. Anti-static materials work well for basic protection, while dissipative options offer controlled charge flow. For more sensitive components, you'll want to use conductive materials that actively channel away charges. If you're handling highly sensitive electronics, static shielding materials with their multi-layer construction provide the ultimate protection through Faraday Cage shielding.
Essential Applications Across Industries
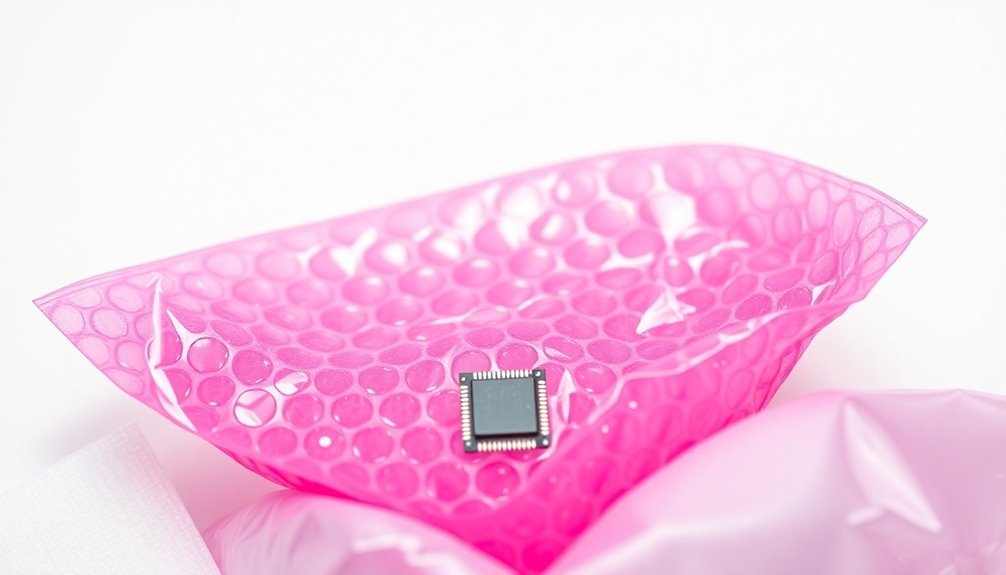
Static protection packaging solutions reach far beyond basic storage needs, serving vital functions across multiple industries. In electronics manufacturing, you'll find these solutions preventing costly damage to circuit boards and microchips while ensuring product reliability throughout assembly and transportation processes. A charge of 30 volts can be enough to cause significant damage to sensitive electronic components.
When you're dealing with aerospace and defense applications, non-metallic static protection becomes essential for safeguarding high-cost, precision equipment operating in harsh environments. These solutions help you maintain compliance with strict regulatory requirements while protecting safety-critical systems. Using hermetic packages ensures reliable sealing and protection in extreme conditions.
In healthcare, you're protecting sensitive medical devices and components from static damage while preventing contamination through reduced static buildup. You'll meet industry safety standards while ensuring the integrity of vital medical equipment that patients rely on.
For automotive and telecommunications sectors, you're securing essential electronic components that power modern vehicles and communication systems. You'll reduce costs associated with static-related damage while maintaining compliance with industry standards.
These solutions protect everything from vehicle safety systems to telecommunications equipment, ensuring reliable performance and reducing the need for costly repairs.
Material Construction and Components
The foundation of effective static protection lies in specialized material construction and innovative components. When you're selecting non-metallic static protection packaging, you'll encounter various material types designed for specific needs. Single-layer solutions like carbon-loaded polyethylene provide basic static control, while more advanced options feature multiple layers for extensive protection. These materials are commonly available in a pink color tone. Intimate packaging provides essential protection as the first layer in direct contact with sensitive components.
Most high-performance static-shielding bags employ a three-layer structure: an outer low-charging layer, a conductive middle layer, and an inner polyester layer for durability. You'll find these materials enhanced with specialized additives – humectants in LDPE pull moisture from the air to create static shields, while amine-free and N-Octonoic acid-free compositions prevent corrosion.
The physical properties of these materials are equally important. You can choose from transparent or semi-transparent options for easy content identification, with thicknesses ranging from 3.6 to 8 mil.
For specialized applications, you'll find anti-static foam sheets in various densities. The construction method matters too – some solutions use buried metal layers for cost efficiency, while others feature laminated metallized polyester to create a Faraday cage effect around your products.
Advantages Over Metallic Alternatives
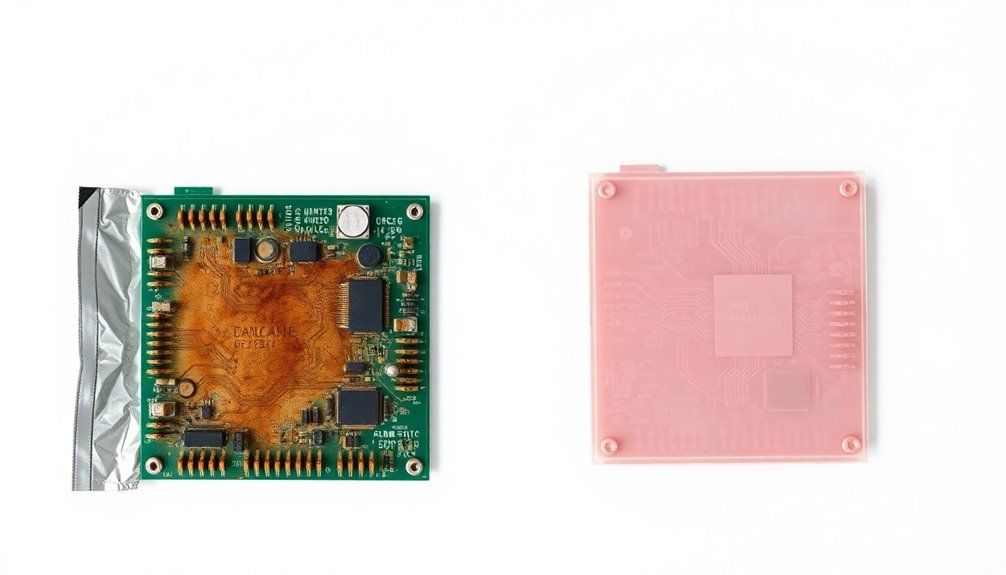
Building upon the advanced material constructions, non-metallic packaging solutions offer distinct advantages over their metallic counterparts. You'll find these solutions are considerably more cost-effective, particularly in large-scale operations where the savings can substantially impact your bottom line. The use of materials like polyethylene and polyester helps reduce production costs while maintaining protective qualities. These materials provide ESD protection for sensitive electronic components during handling and transport. The materials are often topically treated with an expected useful life of about one year.
You'll appreciate the environmental benefits of choosing non-metallic options. These materials are often recyclable, with PET and HDPE being widely accepted in recycling programs. This sustainability factor helps you comply with environmental regulations while reducing your reliance on non-renewable resources.
When it comes to versatility, you'll discover that non-metallic solutions offer exceptional flexibility. They're available in various forms, including bags, tubing, and bubble wrap, and can be customized to fit your specific product dimensions.
The handling advantages are clear – these materials are lighter, easier to manipulate, and generally more resistant to tears and punctures than their metallic alternatives. You'll also benefit from reduced shipping costs due to their lightweight nature, and you'll find them easier to seal and open during your packaging processes.
Performance in ESD Protection
When you're selecting non-metallic static protection packaging, you'll find various solutions offering different levels of charge control, from anti-static materials that prevent charge generation to static shielding that creates a complete barrier against external charges.
You can achieve ideal protection by matching the packaging type to your specific needs, considering that dissipative packaging (10^5 – 10^11 ohms) provides gradual discharge for sensitive components, while conductive packaging (10^2 – 10^5 ohms) offers rapid charge dissipation.
The durability of modern non-metallic ESD solutions during transport, combined with their cost-effectiveness, makes them a practical choice for protecting electronic components throughout the supply chain.
Effective Static Charge Control
Over the past decade, effective static charge control has become paramount in protecting sensitive electronic components from electrostatic discharge damage. You'll find that non-metallic static protection packaging employs various materials specifically designed to prevent and control static charges throughout your supply chain.
When you're handling sensitive electronics, you'll want to utilize anti-static packaging that prevents charge creation during product movement and contact. These materials incorporate anti-static polymers that won't generate static when they interact with other surfaces.
You can choose between static-dissipative materials that prevent charge build-up or conductive packaging that actively channels potential static charges away from your sensitive components.
For your most demanding applications, such as aerospace or semiconductor manufacturing, you'll need packaging that meets strict technical specifications. The surface resistivity of these materials ranges from 1×10^12 to 10^4-6 Ohms/sq, ensuring consistent protection.
You can also customize your packaging solutions with different materials like anti-static nylon, polythene, or PET films. Whether you're working in cleanroom environments or managing electronic inventory, you'll find color-coded options that make identification easier while maintaining ideal ESD protection.
Cost Vs Protection Balance
Because the selection of ESD protection materials directly impacts both your bottom line and product safety, striking the right balance between cost and protection becomes essential.
You'll find that non-metallic solutions like anti-static polythene and PET films offer cost-effective protection while meeting industry standards for static dissipation and shielding effectiveness.
When you're evaluating packaging options, consider how different materials provide varying levels of protection. While metallized polyester might be necessary for highly sensitive components, you can often achieve adequate protection with more affordable alternatives.
Conductive materials with surface resistance of 10^4-6 Ω effectively dissipate static charges without breaking your budget.
You can optimize your costs further through customization. By tailoring packaging solutions to your specific needs, you'll minimize material waste and improve efficiency.
Consider durable options like anti-static nylon, which reduces long-term costs by lasting longer. Additionally, you'll benefit from reduced shipping expenses with lightweight, non-metallic solutions.
When you invest in the right ESD protection, you're not just preventing damage – you're extending product life and reducing replacement costs while maintaining necessary protection levels.
Durability During Transport
The durability of non-metallic ESD packaging faces constant challenges during transport, making performance reliability critical for protecting sensitive components.
You'll find that layered construction using polyester and static dissipative polyethylene creates a robust barrier that resists tears and punctures while maintaining consistent ESD protection.
When you're selecting non-metallic packaging solutions, you'll need to evaluate their performance across varying environmental conditions.
These materials must maintain their protective properties regardless of humidity levels and temperature fluctuations.
While they don't incorporate metal shielding, they rely on advanced anti-static coatings and specialized polymers to achieve reliable static dissipation.
You'll want to implement regular testing protocols to verify your packaging's ongoing effectiveness.
Check for surface resistance degradation and physical integrity, especially if you're storing materials for extended periods.
Remember that proper storage in controlled environments greatly extends the functional life of your non-metallic ESD packaging.
By following industry standards like ANSI/ESD S541-2018, you're ensuring that your non-metallic solutions provide adequate protection during transit.
Always train your team on proper handling procedures to prevent accidental damage that could compromise the packaging's protective qualities.
Environmental Impact and Sustainability
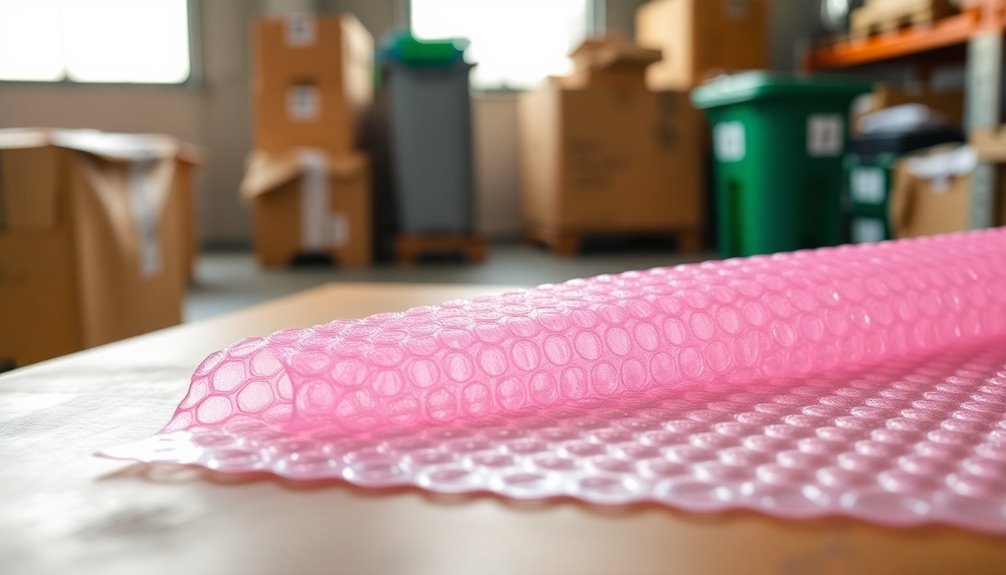
Modern industry's reliance on non-environmentally friendly packaging has created severe environmental challenges that demand immediate attention.
Traditional ESD packaging materials, particularly non-biodegradable plastics and synthetic rubbers, contribute considerably to landfill waste and marine pollution, threatening ecosystems and wildlife for centuries to come.
You'll find that standard ESD bags pose a particular challenge due to their mixed-material composition, making them difficult to recycle through municipal systems.
Additionally, these materials often end up as microplastics in the food chain, creating potential health risks for humans and marine life alike.
However, you can now choose from innovative sustainable alternatives that maintain effective static protection while reducing environmental impact.
Biodegradable ESD bags made from natural fibers like cellulose and recyclable Corstat packaging products offer practical solutions.
You'll discover that these eco-friendly options not only help preserve natural resources but also minimize disposal costs for your business.
Frequently Asked Questions
How Long Does Non-Metallic Static Protection Packaging Maintain Its Protective Properties?
Your non-metallic static protection packaging can last for years when you store it properly. You'll maintain its effectiveness by controlling humidity, temperature, and handling carefully, while regularly checking for any damage.
Can Non-Metallic Packaging Be Reused Without Compromising Its Static Protection Effectiveness?
You can reuse non-metallic packaging several times, but you'll need to inspect it carefully for damage and wear. The static protection properties will gradually decline, so it's best to monitor effectiveness between uses.
What Temperature Ranges Can Non-Metallic Static Protection Materials Safely Withstand?
You'll find most non-metallic static protection materials work safely between -40°C to 80°C. For storage, keep them at 15°C to 30°C, and some specialized materials can handle up to 100°C without losing effectiveness.
Are There Specific Storage Requirements for Unused Non-Metallic Static Protection Packaging?
You'll need to store your unused non-metallic static protection packaging in controlled humidity (30-70%), away from sunlight and heat sources. Keep it in closed containers, separate from other materials, and inspect regularly for damage.
How Can You Test if Non-Metallic Packaging Is Still Providing Adequate Protection?
You can test your non-metallic packaging's effectiveness using static decay rate measurements, triboelectric testing, and surface resistivity checks. Monitor results under different humidity levels to guarantee it's still meeting ESD protection standards.
In Summary
You'll find that non-metallic static protection packaging offers compelling advantages for your business needs. From cost savings and versatile material options to proven ESD protection performance, these solutions deliver exceptional value. They're environmentally sustainable, adaptable across industries, and often outperform metallic alternatives. When you're choosing packaging solutions, non-metallic options provide the perfect balance of protection, practicality, and environmental responsibility.
Leave a Reply