Military static shielding goes far beyond standard anti-static measures through its sophisticated multi-layer design. You'll find advanced metallic barriers using materials like copper and aluminum, combined with specialized conductive coatings and thermoplastic polymers. These military-grade shields must meet rigorous MIL-PRF-81705 standards, requiring precise specifications for thickness, tensile strength, and EMI attenuation. The construction includes static-dissipative outer layers, conductive middle layers, and protective inner layers – all carefully sealed and grounded. When you're protecting defense equipment worth millions, you'll discover why these enhanced specifications and testing protocols make all the difference.
The Faraday Cage Construction
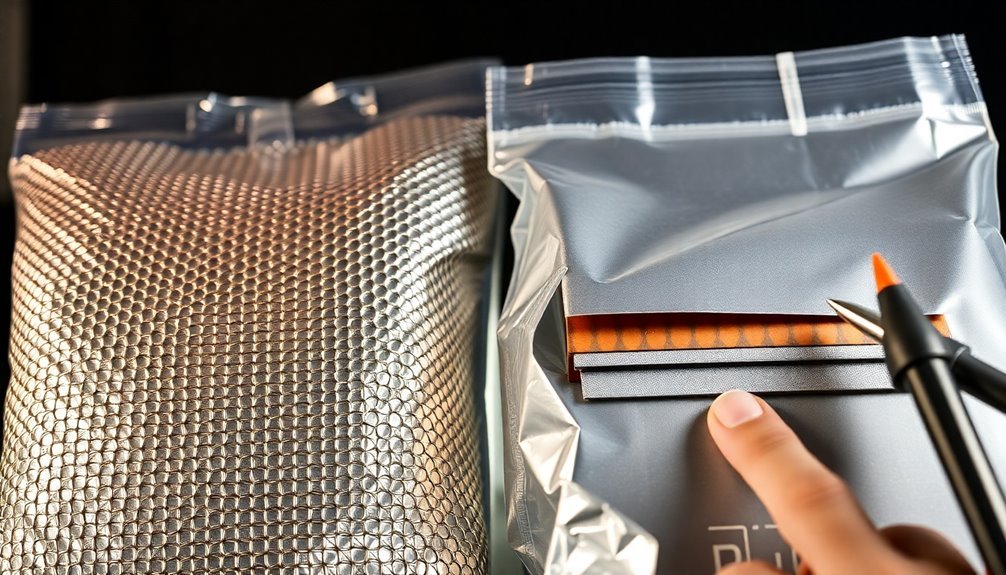
When constructing a Faraday cage for military static shielding, you'll need to focus on three critical elements: conductive material selection, structure type, and proper sealing.
You'll want to choose highly conductive materials like copper or aluminum, as they provide superior shielding effectiveness. The thickness of your material matters substantially – thicker materials will give you better protection against electromagnetic interference. Conducting charges redistribute on the surface to cancel external fields effectively.
You can build your cage as either a solid metal enclosure or a mesh structure, but you'll need to carefully consider the size of any holes in relation to the wavelengths you're blocking. Remember, the holes must be smaller than the electromagnetic wavelength you're trying to shield against. For military applications, you'll typically need extremely small holes to protect against high-frequency threats.
Don't forget to pay special attention to sealing any gaps in your construction. Even tiny openings can compromise your shield's effectiveness.
You'll also want to implement proper grounding to dissipate charge buildup and enhance shielding performance. For military-grade protection, you'll need to guarantee every connection point and seam is tightly sealed and properly conductive.
Military Grade Material Layers
You'll find military-grade static shielding bags employ a sophisticated three-layer design that works in perfect harmony to protect sensitive electronics.
Each specialized layer, from the static-dissipative outer polyester to the conductive middle aluminum and the dissipative inner polyethylene, creates an impenetrable defense system against electrostatic discharge.
The metallic middle layer is particularly essential, as it forms a continuous conductive barrier that channels harmful charges safely away from protected components. This advanced construction achieves Faraday cage protection through its meticulously engineered layers.
Multi-Layer Protection Design
The sophistication of military static shielding lies in its multi-layer protection design, where various materials work in concert to create a thorough defense system. Each layer serves a specific protective function, from electromagnetic interference (EMI) shielding to thermal and optical protection, all while meeting strict military standards.
You'll find that the EMI and RFI shielding layers use conductive materials like copper, aluminum, and stainless steel, with special attention paid to seam closure. The Faraday cage principle is implemented through continuous conductive layers, while plastic components receive specialized conductive coatings to maintain effectiveness without adding excessive weight. Near-infrared protection is achieved through NIR-absorbing materials that enhance concealment in low-light conditions.
When it comes to thermal and optical protection, you're looking at materials specifically chosen to cover both visual (400-750 nm) and thermal (3000-15000 nm) spectral ranges. These layers incorporate camouflage patterns to reduce visual contrast while reflecting thermal radiation to minimize heat signatures.
Military certification guarantees you're getting materials that won't just perform well initially but will maintain their stability under various environmental conditions. Every layer must comply with specific MIL-specs and undergo rigorous testing to guarantee reliability and interchangeability across military applications.
Advanced Metallic Barrier Construction
Military static shielding relies heavily on advanced metallic barrier construction, where specialized material layers work synergistically to create impenetrable defenses.
You'll find that these barriers incorporate military-grade metal plating with exceptional corrosion resistance and thermal protection properties. The construction combines zinc-aluminum coated steel with polypropylene geotextile to guarantee maximum durability and protection against harsh environmental conditions. These protective layers maintain their effectiveness even during extreme temperature fluctuations, from scorching deserts to arctic environments.
The modular design of these metallic barriers allows for quick deployment and versatile configurations, adapting to your specific operational requirements. You're getting thorough protection across multiple spectrums, including EMI, RFI, and EMF interference, thanks to the integration of specialized military-grade fabrics and thermoplastic polymers.
- Zinc-aluminum coating provides superior corrosion resistance and structural integrity
- Electroplating and chemical deposition create robust protective layers
- Military-grade fabrics offer multi-spectral electromagnetic shielding
- Modular components enable rapid assembly and reconfiguration
- Thermoplastic polymers guarantee flame retardancy and heavy-duty performance
The combination of these advanced materials and construction techniques guarantees your equipment remains protected against environmental threats while maintaining top operational efficiency. You're getting defense-standard quality control at every layer, guaranteeing the highest level of protection for critical military applications.
ESD Protection Beyond Standard Measures
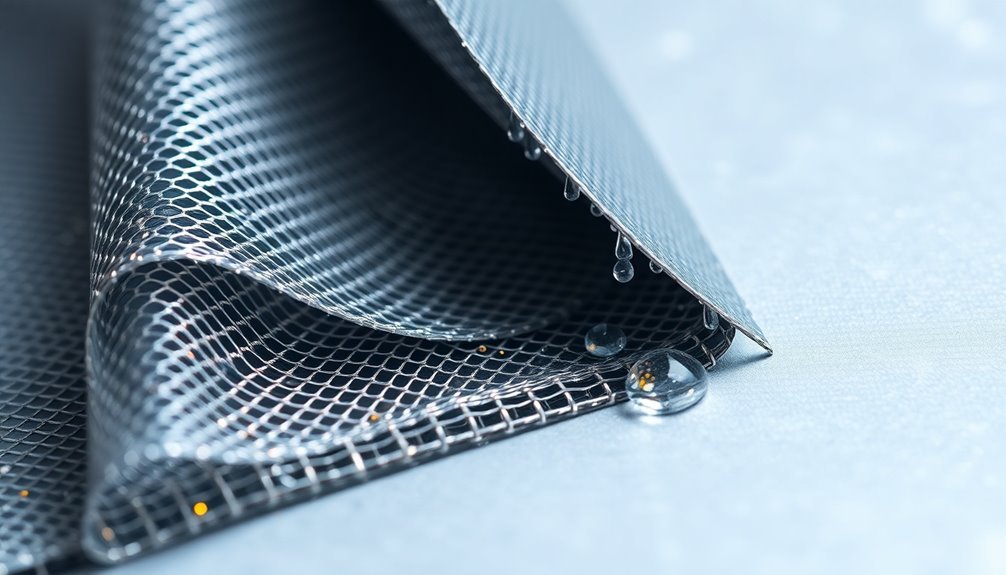
You'll find military-grade ESD protection extends far beyond basic anti-static measures through its sophisticated multi-layer defense system, incorporating specialized materials like MIL-PRF-81705E and MIL-DTL-117H in strategic combinations.
Your testing protocols must meet rigorous military standards, including ASTM F1812 for contact and air-gap discharge evaluation, while maintaining documented compliance with MIL-STD-1686. These standards help ensure reduced damage rates during shipping and handling of sensitive electronic components.
To guarantee mission-critical components remain protected, you're required to implement and verify multiple protective layers working in concert, from moisture barriers to Faraday Cage shielding.
Multi-Layer Defense System
Modern military static shielding relies heavily on multi-layer defense systems that combine diverse protective measures to create a thorough shield against threats. You'll find these systems incorporate multiple overlapping layers of protection, much like the proven success of missile defense systems such as Israel's Iron Dome.
The geographical dispersion of protective elements provides extensive coverage, while the defense-in-depth approach offers multiple opportunities to neutralize static threats before they can cause damage. These systems employ static dissipative polyethylene as a crucial inner layer component.
Each layer in the system serves a specific purpose, working together to create a robust defense against ESD. You'll benefit from increased reliability, as the failure of one layer won't compromise the entire system.
These adaptable solutions continue to evolve with technological advancements, safeguarding protection against future threats.
- Overlapping protective layers increase system reliability and effectiveness
- Geographically dispersed sensors monitor static buildup at multiple points
- Multiple interception opportunities enhance the system's overall success rate
- Varied protective measures address different types of static threats
- Continuous system updates incorporate new technologies and countermeasures
The multi-layered approach has proven particularly effective in military applications, where equipment protection is vital for mission success.
Advanced Testing Requirements
Building upon the multi-layer defense concept, advanced testing requirements for military static shielding go well beyond standard commercial measures. You'll find that military standards like MIL-STD-1686 establish exceptionally rigorous testing protocols that guarantee maximum protection against electrostatic discharge. The AS6171 test methods are crucial for detecting any counterfeit or substandard components that could compromise static shielding integrity.
Testing Aspect | Military Requirement |
---|---|
Environmental Control | 12%±3%RH at 73°F±5°F for 48 hours |
Certification Standards | MIL-STD-750, MIL-STD-883, MIL-STD-202 |
Quality Assurance | DFARS Part 252.246-7007 compliance |
When you're dealing with military applications, you must comply with specialized testing methods outlined in ANSI/ESD STM11.11 and STM11.12 for formal ESD qualification. These standards require thorough protection plans and continuous performance monitoring. You'll need to conduct risk assessments across all functions, from quality assurance to material handling.
For spaceflight and potential spaceflight applications, you're required to implement even more stringent control measures. This includes advanced instrumentation to measure surface and volume resistance of static shielding bags, guaranteeing they meet the strict requirements of ANSI/ESD STM11.31. The Defense Logistics Agency (DLA) regularly audits these testing procedures to maintain MIL-SPEC compliance.
Static Shielding Vs Anti-Static
The fundamental difference between static shielding and anti-static protection lies in their defensive capabilities. While static shielding bags provide extensive protection through multiple layers and Faraday cage properties, anti-static bags only prevent the buildup of static electricity.
You'll need to understand that static shielding is essential for sensitive electronic components, especially in military applications where MIL-PRF-81705 specifications must be met.
When you're choosing between the two types, consider these critical distinctions:
- Static shielding bags must be completely sealed to maintain their ESD protection
- Anti-static bags are suitable only for non-sensitive items like manuals or hardware
- Static shielding incorporates metallic layers for complete ESD protection
- Anti-static materials won't generate triboelectric charges but can't shield from external ESD
- Static shielding offers moisture vapor barrier properties in addition to ESD protection
If you're working with military electronics, you'll always need static shielding bags, not just anti-static ones. The multi-layer construction and Faraday cage effect of static shielding bags provide the thorough protection required for sensitive military components, while anti-static bags simply won't meet these stringent requirements.
Meeting Military Specifications
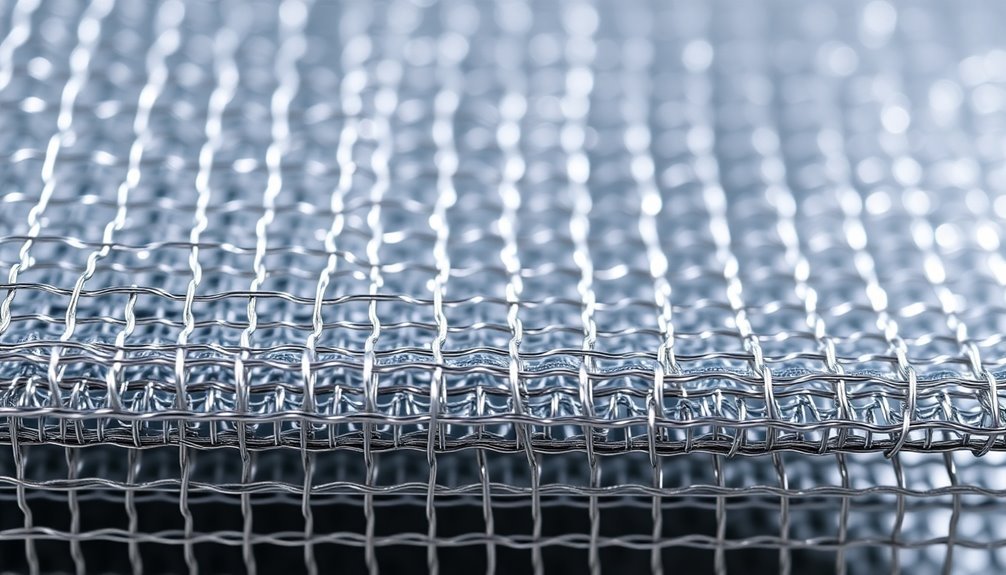
Rigorous military specifications govern every aspect of static shielding materials used in defense applications. To meet MIL-PRF-81705 standards, these materials must undergo extensive testing for physical strength, electrical properties, and EMI protection capabilities.
Property | Requirement |
---|---|
Thickness | 4.5 mils |
Tensile Strength MD | 4,100 psi minimum |
Puncture Resistance | 19 lbs minimum |
EMI Attenuation | >35 dB before flex |
You'll need to guarantee your materials meet strict sealing conditions, operating at 375°F with 40psi pressure for peak performance. The grounding system must maintain a maximum resistance of 10,000 ohms, requiring proper installation of ground grab bars and adherence to NFPA 77 guidelines.
The most critical specifications focus on EMI and static protection. Your shielding materials must demonstrate EMI attenuation above 35 dB before flexing and maintain at least 30 dB after flexing. Static decay requirements are equally demanding, with the inner layer needing less than 1.0 second decay time and the outer layer performing at under 0.02 seconds. These specifications guarantee consistent protection for sensitive military electronics and components.
Critical Defense Applications
Meeting strict military specifications paves the way for protecting vital defense electronics that can't afford to fail. You'll find antistatic UHMW-PE materials integrated into mission-critical systems where electrostatic discharge poses a serious threat to operational reliability.
These specialized materials protect sensitive components in military equipment, from missile guidance systems to radar installations.
When you're dealing with defense applications, you need materials that can dissipate static charges effectively while maintaining their structural integrity. That's why antistatic UHMW-PE has become essential in protecting:
- Circuit boards and connectors in aerospace systems
- Avionic components in military aircraft
- Communication equipment in ground vehicles
- Missile guidance system housings
- Radar system components and casings
You'll see these materials at work in both stationary and mobile defense systems, where they prevent static buildup through human contact and environmental factors.
The combination of wear resistance and static dissipation makes antistatic UHMW-PE ideal for bushings and bearings in defense equipment.
As technology advances, these materials continue to evolve, ensuring your defense electronics remain protected from ESD-related failures that could compromise mission success.
Rigorous Testing and Standards
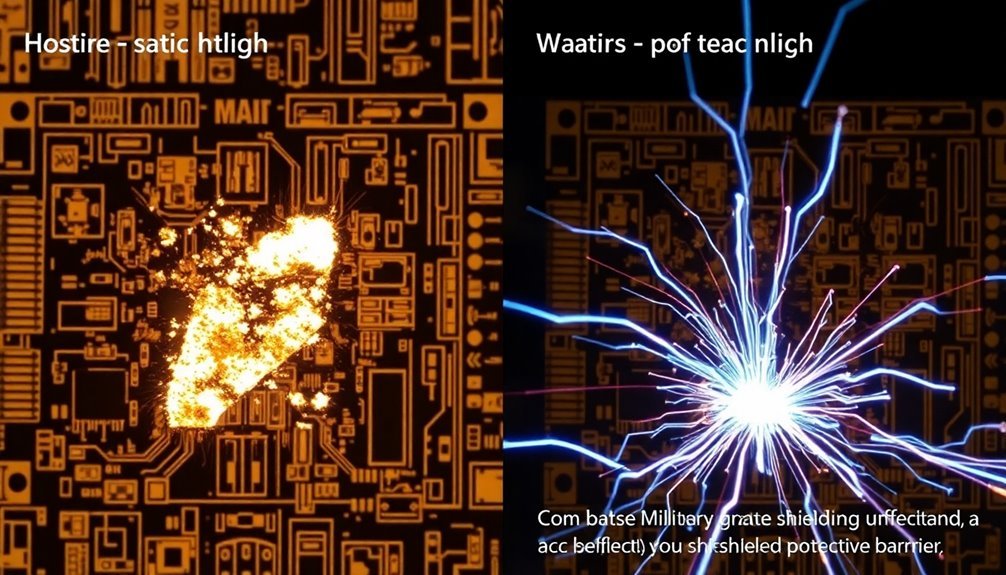
Quality assurance for military static shielding demands extensive testing across frequencies from 30 MHz to 1 GHz. You'll find that testing procedures require specialized environments like anechoic chambers and shielded rooms, where spectrum and network analyzers measure precise dynamic ranges and actual signals.
The process often involves removing internal components to guarantee accurate readings.
Military standards like MIL-STD-188-125-1 and MIL-STD-188-125-2 govern these rigorous requirements. You're looking at thorough frameworks that address both fixed facilities and transportable ground-based systems, particularly focusing on HEMP hardening and EMI protection.
The testing verifies the effectiveness of electromagnetic barriers and HEMP shields, which must form a continuous conductive housing to reduce field coupling into protected volumes.
You'll need certified compliance labs with specific expertise to conduct these tests. Organizations like Keystone Compliance offer testing capabilities for various enclosure sizes, from small components to entire buildings.
These labs must strictly adhere to military standards while using specialized equipment to measure shielding effectiveness. They're guaranteeing your static shielding can effectively block electromagnetic energy and prevent system degradation or failure under real-world conditions.
Frequently Asked Questions
What Is the Average Lifespan of Military-Grade Static Shielding Bags?
You can expect military-grade static shielding bags to last 5-20 years when properly stored at 68°F in a dry environment. Remember to test them annually and follow FIFO inventory practices for best results.
Can Military Static Shielding Bags Be Safely Reused Multiple Times?
Yes, you can safely reuse military static shielding bags multiple times, but you'll need to inspect them carefully before each use. Discard bags if you find any holes, tears, or damage to the shielding layer.
How Do Extreme Temperatures Affect the Performance of Military Static Shielding?
Extreme temperatures can degrade your military static shielding's protective properties. High heat weakens the material's conductive layers, while extreme cold can make it brittle and compromise its static-dissipative capabilities.
Are There Special Disposal Requirements for Military-Grade Static Shielding Materials?
You'll need to follow strict DoD disposal regulations for military-grade static shielding. You must comply with DEMIL codes, handle hazardous materials properly, and coordinate with your Program Manager for proper disposal procedures.
What Happens if Military Static Shielding Bags Get Wet During Storage?
If your military static shielding bags get wet, they'll lose their ESD protection, risk material degradation, and compromise their moisture barrier. You'll need to replace them as they won't effectively protect sensitive electronic components anymore.
In Summary
You'll find military static shielding is a complex defense against electromagnetic threats that goes far beyond standard commercial solutions. Through its multi-layered construction, specialized materials, and rigorous testing protocols, it meets the strictest military specifications. When you're protecting sensitive defense equipment, you can't settle for basic anti-static measures – you need the superior protection that only military-grade static shielding delivers.
Leave a Reply