You'll need both static and moisture protection to properly safeguard your electronic components during storage and shipping. Use specialized materials like anti-static pink poly or metallized polyester bags that create a Faraday cage effect while maintaining humidity control. These packages should comply with ANSI/ESD S541-2018 standards and maintain a vapor barrier rating suitable for your components' sensitivity levels. Keep storage areas between 60-70°F with humidity under 60%, and always handle items with ESD-safe gloves or wrist straps. Understanding the complete spectrum of protection options will help you make the most cost-effective choice for your specific needs.
Understanding Static-Safe Packaging Fundamentals
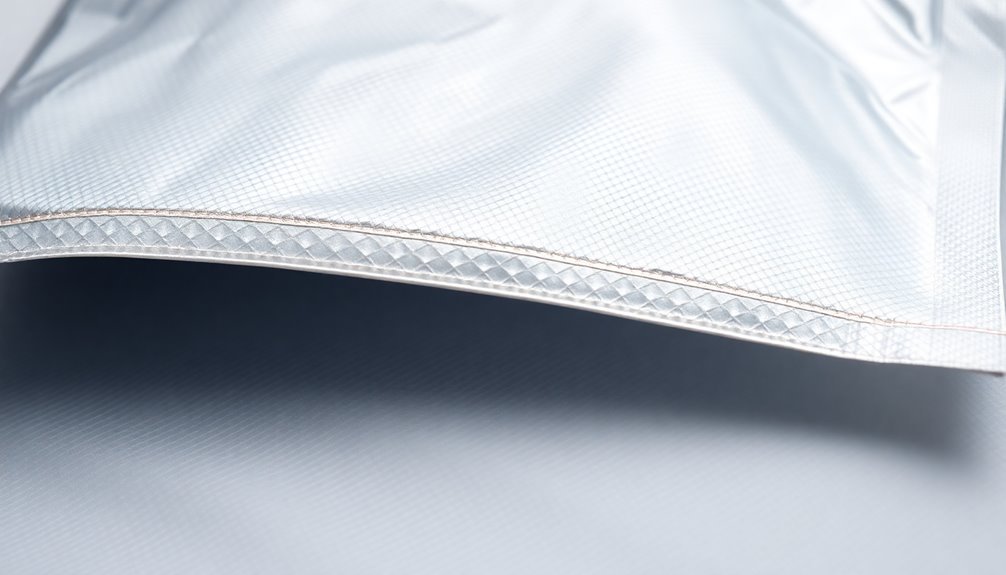
Static-safe packaging boils down to protecting sensitive electronic components from electrostatic discharge (ESD) damage during handling, shipping, and storage.
You'll need to understand that static charges can build up during routine operations, potentially causing severe damage to your electronic components if not properly managed.
To effectively protect your components, you'll want to focus on two key aspects: anti-static materials and static shielding.
Anti-static packaging resists the buildup of static charges, while shielding materials create a Faraday cage effect that disperses electromagnetic charges along the exterior surfaces.
The most effective bags incorporate multiple protective layers including polyethylene, aluminum, and polyester for maximum protection.
You'll find that static shielding bags and films offer superior protection compared to basic anti-static packaging.
When implementing static-safe packaging, you must select materials based on your specific component requirements and testing conditions.
Following standards like ANSI/ESD S541-2018 will help you determine the most appropriate packaging solutions.
Remember that proper grounding is essential – all conductors and dissipative materials should maintain the same electrical potential.
Maintaining humidity above 40% in storage areas helps reduce static voltage potential and minimize ESD risks.
You'll also need to guarantee your team receives proper training on ESD protection protocols and regularly monitors the effectiveness of your packaging solutions to maintain component integrity.
Common ESD Packaging Materials
You'll encounter several vital types of ESD packaging materials when protecting sensitive electronics, each serving a distinct purpose. Anti-static materials prevent tribocharging, while conductive materials actively transport charges away from stored components.
Dissipative materials work by slowing electrical flow, and shielding materials create protective Faraday Cage barriers against electrostatic charges. According to industry data, the ESD packaging market is expected to reach $5,773.1 million by 2027. Compliance standards across 55 countries ensure these materials meet rigorous safety specifications.
When selecting your ESD packaging, you'll need to take into account surface resistance properties. Conductive materials typically range between 10^2 and 10^5 ohms, while dissipative materials span from 10^5 to 10^11 ohms. For maximum protection, you can opt for metal-in and metal-out constructions, which provide superior ESD shielding.
You'll find these materials extensively used across multiple industries. They're essential in electronics manufacturing, medical device production, aerospace applications, automotive components, and telecommunications equipment.
Moisture Barrier Technology Explained
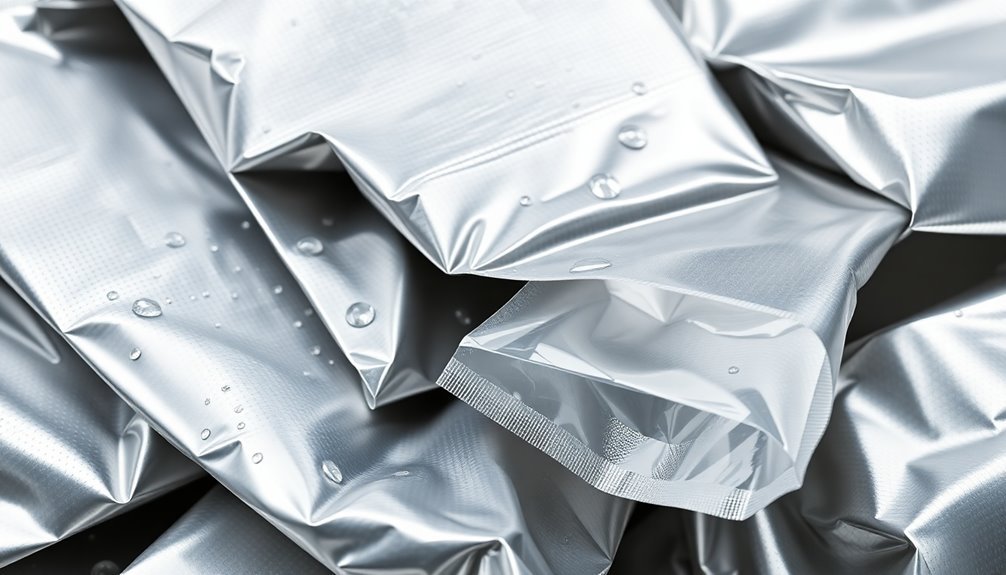
You'll find that moisture barriers in static-safe packaging rely on precise vapor transmission rates to protect sensitive electronics from humidity damage.
Multi-layer protection systems combine different materials, like metallized films and specialized polymers, to create a robust barrier against both moisture and static electricity. Class I vapor barriers are often incorporated into these systems based on their extremely low permeability ratings.
Testing the seal integrity of these barriers guarantees consistent performance and helps maintain the required moisture protection levels throughout the packaging's service life. The installation process must include continuous sealing to prevent any moisture infiltration through gaps or breaks.
Vapor Transmission Rate Basics
When protecting sensitive electronic components, understanding vapor transmission rate (WVTR) is fundamental for effective packaging design.
You'll need to know that WVTR measures how quickly water vapor passes through a material over time under specific conditions, typically measured in g/100 in^2/24 hr or g/m^2/24 hr. Lower WVTR values indicate better moisture barrier properties, which is essential for protecting your electronics. Active and passive barrier solutions are widely used in pharmaceutical packaging for optimal moisture protection.
You'll find that material selection greatly impacts WVTR performance. Different polymers offer varying levels of protection, with specialized materials like HDPE and OPP providing better moisture barriers than standard LDPE. Hydrophobic materials can significantly enhance moisture protection capabilities.
The thickness of your packaging material also plays a critical role – thicker materials generally offer improved barrier properties.
To guarantee reliable protection, you'll want to take into account standardized testing methods like ASTM D7709, which measures WVTR under controlled conditions (typically at 100°F and 90% RH).
These tests help you compare different materials' performance accurately. Remember that additives and copolymer layers can affect WVTR by up to 30%, while processing conditions may cause variations of about 5%.
When selecting packaging materials, you'll need to factor in these aspects to achieve the most effective moisture protection for your electronic components.
Multi-Layer Protection Systems
Most modern static-safe packaging relies on multi-layer barrier technology that combines different materials to achieve superior moisture protection. When you're working with sensitive electronics, you'll need packaging that prevents both static discharge and moisture damage.
Multi-layer barriers incorporate specialized materials like nano-fibrillated cellulose and hydrophobic biowax to create robust protection against water vapor and gases. These advanced systems demonstrate air permeability ratings exceeding 15,000 seconds, ensuring exceptional gas barrier performance. With a permeance rating of 0.0071 perms, these barriers provide exceptional protection against moisture infiltration.
You'll find these protection systems particularly effective because they deliver low water vapor transmission rates while maintaining the package's static-safe properties. The technology has evolved to include plasma-based coatings and specialized barrier layers that integrate seamlessly into high-density polyethylene, ensuring your products remain protected without compromising recyclability.
- Picture a microscopic sandwich of materials, each layer performing a specific protective function
- Visualize an invisible shield that repels water molecules while letting static charges dissipate safely
- Think of a transparent force field that maintains consistent internal conditions
- Imagine a flexible yet impenetrable barrier that moves with your product without breaking down
These multi-layer systems don't just protect – they extend product shelf life and maintain the integrity of your sensitive components throughout storage and shipping.
Seal Integrity Testing
Through rigorous testing protocols, seal integrity testing forms the backbone of moisture barrier verification in static-safe packaging. You'll need to employ multiple testing methods to guarantee your packaging meets regulatory standards and maintains product protection.
Start with visual inspection under controlled lighting conditions, examining seal edges and corners for any visible defects. You can enhance this process using dye penetration tests, where you'll apply compatible dye solutions along seal edges to identify potential breaches.
For more thorough analysis, you'll want to use bubble emission tests by submerging packages in water and checking for escaping bubbles under pressure. Non-destructive testing methods like VeriPac vacuum decay technology offer you reliable results without compromising package integrity.
When working with Tyvek or other porous materials, you'll need to pay special attention to their unique properties, as they provide superior microbial barrier protection through HDPE filaments. You can utilize advanced seal-scan technologies that employ airborne ultrasound to detect defects in visually acceptable seals.
Types of Static Protection
Static-safe packaging breaks down into four distinct categories, each offering unique protective properties for sensitive electronic components.
When you're selecting packaging materials, you'll need to understand how each type functions to protect your products effectively.
Anti-static materials prevent static buildup through specialized additives and are typically pink in color, making them easily identifiable.
Conductive materials work like lightning rods, channeling electric charges away from stored items through carbon-loaded materials.
Dissipative options slow down static charges rather than directing them, offering a balanced approach for non-critical applications.
Shielding materials create a Faraday cage effect, blocking both electrostatic discharge and electromagnetic interference.
- Pink anti-static bags nestled inside shipping boxes, protecting delicate circuit boards
- Black conductive tubing wrapped securely around sensitive cable assemblies
- Metallic-looking shielding bags reflecting light while safeguarding microprocessors
- Clear dissipative bubble wrap cushioning electronic components during transit
You'll find each type serves specific needs in your packaging strategy.
Anti-static materials work well for basic shipping, while shielding materials offer maximum protection for highly sensitive components.
Conductive and dissipative materials provide intermediate levels of protection based on your specific requirements.
Essential ESD Safety Measures
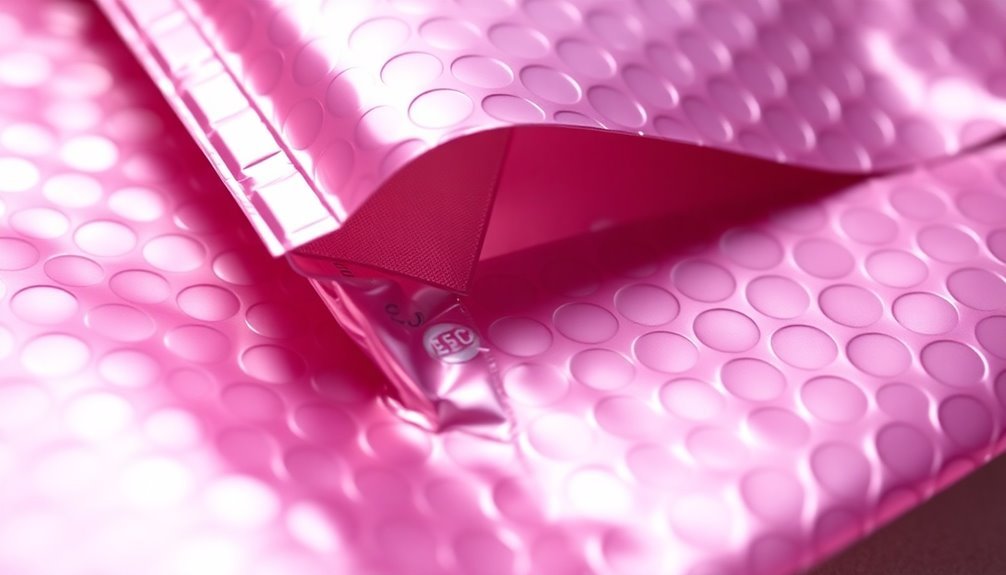
You'll need to establish proper grounding equipment with reliable testing protocols to maintain effective ESD safety measures in your packaging facility.
Regular testing of your ESD control methods, including wrist straps, ionizers, and floor mats, guarantees consistent protection against static discharge throughout your operations.
Your daily protection procedures should include monitoring humidity levels, verifying grounding connections, and conducting spot checks on packaging materials before use.
Proper Grounding Equipment Setup
A reliable grounding equipment setup forms the foundation of any effective ESD safety system.
You'll need to start with a properly grounded workstation that includes a static dissipative mat connected to a common point ground. Install an Earth Bonding Point at your workstation and connect it directly to a verified electrical ground to guarantee safety.
Your essential grounding components should include a wrist strap system with current-limiting resistors, connected to the same grounding point as your work surface.
If you're working at a standing station, you'll want to implement a flooring/footwear system using ESD control flooring and appropriate footwear.
- Picture a clean workstation with a dark blue static dissipative mat firmly secured and connected to ground via a metallic crimp connector
- Visualize a comfortable wrist strap with a secure, snug fit around your wrist, connected to the Earth Bonding Point
- See yourself working on a clear surface free from insulators, with all components properly grounded
- Imagine a complete floor mat system with heel grounders providing consistent contact with the grounded surface
Remember to verify your grounding connections regularly and maintain single-point grounding to prevent potential electrical loops.
This setup guarantees consistent static discharge protection for your sensitive components.
Testing ESD Control Methods
Building on your established grounding system, regular testing guarantees your ESD control methods meet industry standards.
You'll need to follow IEC 61000-4-2 testing procedures using ESD simulators to verify your packaging's protective capabilities. Start by testing multiple voltage levels, typically between 2 kV and 15 kV, to ascertain thorough protection across different discharge scenarios.
Implement testing using all three ESD models: Human Body Model, Machine Model, and Charged Device Model. These simulations will help you identify potential vulnerabilities in your packaging design.
Don't forget to assess your protection mechanisms against both direct and indirect discharge events, as products can fail from either type.
When you're testing your packaging solutions, watch for common issues like insufficient protection layers or poor material selection. If you detect failures, you'll need to implement appropriate mitigation techniques, such as enhancing your grounding systems or upgrading protective materials.
Remember to document all test results for compliance purposes, especially if you're shipping to North American markets.
Keep your testing equipment calibrated and maintain consistent testing procedures to ascertain reliable, repeatable results that meet your industry's specific standards.
Daily Protection Procedures
Three core elements form the foundation of daily ESD protection: proper grounding equipment, controlled workspaces, and consistent personal protection measures. You'll need to implement these protective measures every time you handle static-sensitive components.
Start by wearing an anti-static wrist strap connected to a common ground point, and guarantee you're using ESD-safe footwear on conductive flooring.
Keep your workspace static-safe by maintaining proper humidity levels and using ionizers to neutralize charges in the air. You'll want to clearly mark your ESD Protected Area (EPA) and equip it with grounding cables and static dissipative mats. Don't bring non-essential personal items into the EPA.
- Picture a workspace where every surface gleams with properly installed dissipative materials
- Envision organized workstations with visible ground points and neatly coiled grounding cords
- See yourself wearing complete ESD gear: wrist strap, lab coat, and heel straps
- Imagine a clean, controlled environment with prominent EPA signage and markings
Remember to regularly inspect your ESD control equipment and maintain cleanliness in your work area.
Use ESD-safe tools and store components in appropriate shielding materials to guarantee consistent protection throughout your daily operations.
Moisture Control in Electronics Storage
Inside the world of electronics storage, moisture poses one of the greatest threats to component integrity.
You'll need to maintain strict humidity control between 40% to 60% relative humidity to protect your electronic components from damage. When humidity levels rise too high, your components can absorb moisture, leading to short circuits and corrosion. Conversely, if humidity drops too low, you risk static electricity buildup that can harm sensitive parts.
To protect moisture-sensitive devices (MSDs), you'll want to invest in dry cabinets that maintain humidity levels below 5%. If you don't have access to dry cabinets, use moisture barrier bags (MBBs) combined with desiccants and humidity indicator cards.
It's vital to track the cumulative exposure time of your MSDs to guarantee they don't exceed their specified floor life.
You can further protect your components by implementing these important practices:
- Store electronics in cool, dry environments (20-25°C).
- Conduct regular inspections for signs of moisture damage.
- Use airtight containers with desiccants.
Remember to avoid sudden temperature changes that can cause condensation.
Selecting Appropriate Packaging Solutions
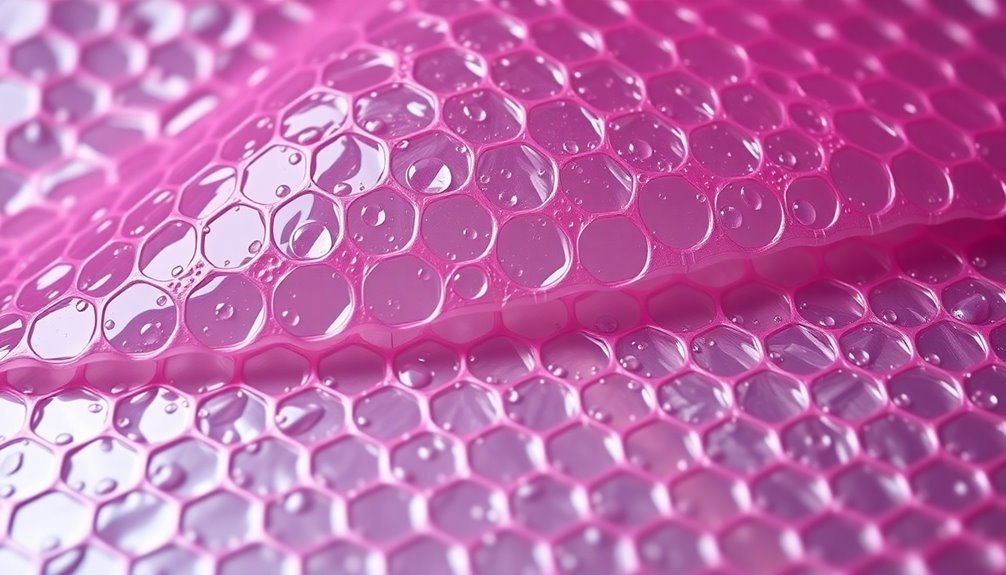
When you're choosing static-safe packaging, you'll need to assess the level of protection your electronic components require based on their sensitivity to ESD and environmental conditions.
You should examine the material composition of potential packaging solutions, focusing on features like MVTR ratings, puncture resistance, and static dissipative properties that match your specific needs.
Weighing the cost against performance benefits will help you determine the most effective packaging solution, considering factors such as reusability, durability, and compliance with industry standards.
Evaluating Protection Level Requirements
Selecting the right level of static-safe packaging requires a careful evaluation of both your components' sensitivity and environmental risks.
You'll need to assess whether basic static protection is sufficient or if you need extensive moisture barrier solutions. Consider your storage conditions, transportation methods, and the value of your components when making this decision.
For sensitive electronic components, you'll want to evaluate protection levels based on industry standards like ANSI/ESD S20.20.
Test your chosen packaging solution's performance in real-world conditions, including its ability to prevent static discharge and maintain moisture barriers. Don't forget to verify the packaging material's compatibility with your specific components.
- A basic static shield bag floating in the air, crackling with visible static electricity being blocked at its surface
- A moisture barrier bag with water droplets beading up and rolling off its metallic surface
- A combo bag undergoing a seal integrity test with visible pressure indicators
- A specialized vacuum-sealed ESD bag protecting a circuit board, with a clear view of the protective layers
Choose your protection level based on measurable criteria, including puncture resistance, moisture barrier efficiency, and temperature stability.
If you're handling highly sensitive components, opt for enhanced protection solutions like CALDRY 1500 or specialized vacuum-sealed ESD bags.
Material Composition Analysis
Three primary material compositions form the backbone of static-safe packaging solutions: metallized polyester for Faraday cage protection, static dissipative polyethylene for charge control, and specialized moisture barrier layers for humidity defense.
When you're selecting materials, you'll need to take into account how these elements work together to create thorough protection.
For moisture protection, you'll want to focus on polyethylene and nylon films combined with desiccants. These materials work together to create an impermeable barrier against water vapor, while desiccants absorb any residual moisture that might penetrate the packaging.
You'll find advanced options like CALDRY VF 125 and metalized MVB that offer dual protection against both static and moisture.
To guarantee ideal protection, you'll need to evaluate the material's ESD shielding efficiency and humidity-independent performance.
Look for packaging that maintains its anti-static properties over time and offers strong puncture resistance.
The most effective solutions will incorporate multiple layers, such as nylon/PE laminates or composite materials, giving you thorough protection for your sensitive electronic components.
Cost-Benefit Performance Assessment
Building on your understanding of material compositions, let's examine the cost-benefit dynamics of static-safe packaging solutions. When you're evaluating static-safe packaging options, you'll need to balance initial costs against long-term performance benefits.
While larger purchases offer better per-unit pricing, it's crucial to take into account your specific protection requirements and storage conditions.
Your cost-benefit analysis should focus on these key performance indicators:
- A high-quality moisture barrier bag with low MVTR protecting valuable circuit boards from humidity damage
- Multiple layers of metallized polyester creating an impenetrable shield against static discharge
- Durable puncture-resistant materials safeguarding components during shipping and handling
- Clear humidity indicator cards monitoring moisture levels in real-time
You'll find that investing in premium moisture barrier bags with superior ESD protection often proves more economical than risking component damage.
Factor in volume discounts and customization needs when calculating total costs. Keep in mind that while basic bags might seem cost-effective initially, they may not provide adequate protection for sensitive electronics.
Your choice should align with both industry compliance standards and your specific application requirements, ensuring maximum protection within your budget constraints.
Industry Standards for Protection
Due to the critical nature of protecting electronic components, industry standards have evolved to establish extensive guidelines for static-safe packaging. You'll need to comply with ANSI/ESD S20.20 for ESD protection and IPC/JEDEC J-STD-033 for moisture-sensitive device handling to guarantee your components remain safe throughout manufacturing and shipping processes.
When selecting packaging materials, you must make certain they meet specific requirements for both static and moisture protection. Your materials should incorporate effective ESD shielding through metallized layers while maintaining low moisture vapor transmission rates.
Don't overlook the significance of static dissipative properties and puncture resistance in your packaging choices.
You'll face several challenges in implementing these standards effectively. You must balance cost considerations with protection requirements while making sure your entire supply chain adheres to these guidelines.
It's crucial to maintain proper storage conditions and conduct regular compliance audits.
To enhance your protection measures, you can utilize advanced packaging technologies. Consider incorporating vacuum sealing, desiccants, and humidity indicators into your packaging solutions.
These innovations, combined with custom packaging options, will help you maintain compliance while providing maximum protection for your sensitive components.
Testing ESD Package Effectiveness
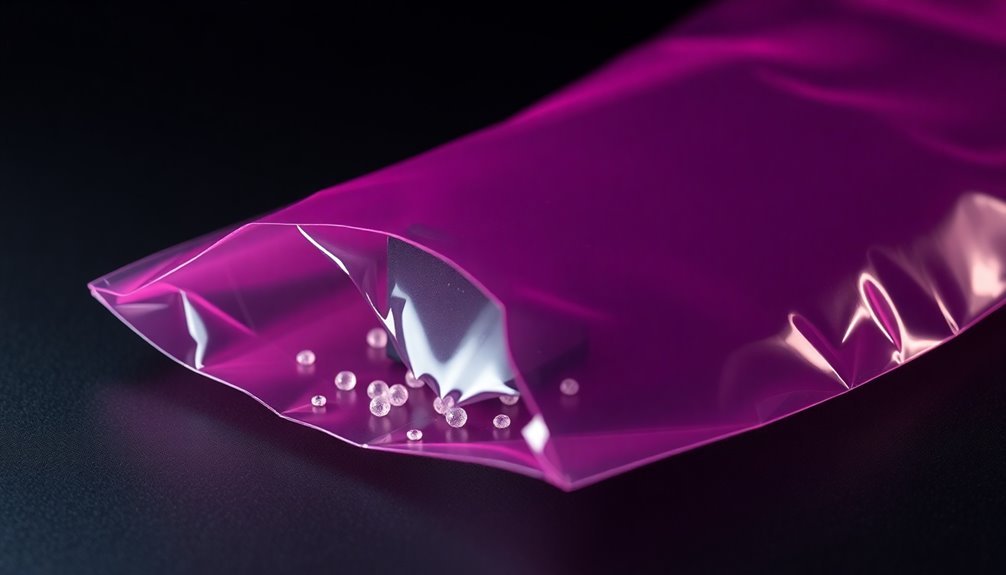
After implementing thorough packaging standards, you'll need to verify their effectiveness through rigorous testing protocols. Your testing program should combine surface and volume resistance measurements with static shielding evaluations to guarantee extensive protection.
You'll want to use specialized ESD meters and simulators while maintaining strict environmental controls during testing.
When conducting your tests, you'll need to pay close attention to temperature and humidity conditions, as these factors greatly impact ESD behavior. Follow established standards like IEC 61000-4-2 and ANSI/ESD S541-2008 to confirm your testing procedures meet industry requirements.
- Picture yourself using an ESD simulator to create controlled discharges, watching the energy dissipate safely through your packaging material.
- Envision your test samples properly conditioned in environmental chambers, awaiting precise measurements.
- Visualize the resistance testing setup with its ground planes and measurement electrodes precisely positioned.
- See yourself documenting waveform readings as your ESD meter validates your package's protective capabilities.
Remember to maintain consistent test conditions and regularly verify your equipment's calibration. Your testing process should include both contact and air discharge methods to simulate real-world scenarios your packages might encounter.
Best Storage Practices
To maintain the integrity of ESD-sensitive components, proper storage practices must combine climate control, container selection, and handling protocols.
Keep your storage area temperature between 60°F and 70°F, with relative humidity below 60%. You'll need to store components in ESD-safe containers with moisture barrier properties and secure seals.
Select storage containers made of static-dissipative or conductive materials with proper ESD shielding. You should guarantee they're clearly labeled with ESD and moisture-sensitive warnings.
Don't forget to include desiccants inside moisture barrier bags to maintain a dry environment.
When handling components, always use ESD-safe tools and wear anti-static gloves. You'll want to avoid wearing clothing that generates static electricity.
Make sure your storage area has proper grounding, ESD-safe flooring, and anti-static workstations. Keep static-generating materials like polystyrene away from storage areas.
Implement a first-in, first-out inventory system to minimize storage time, and regularly inspect both components and moisture barrier bags for signs of damage.
You should clean storage areas frequently to prevent dust buildup, which can compromise component integrity and create additional handling risks.
Handling and Shipping Guidelines
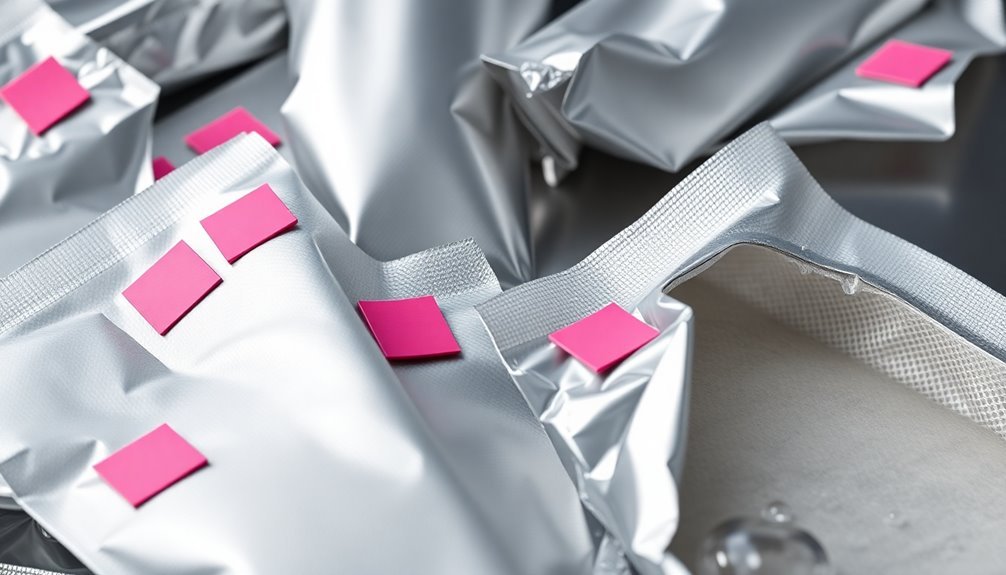
Successful component shipping begins with proper handling procedures and protective packaging methods.
You'll need to use static-safe gloves or wrist straps while handling components and verify your work surface meets ANSI/ESD S20.20 standards.
When preparing items for shipping, use bags that provide both static and moisture barrier protection, along with appropriate desiccants to control humidity levels.
Always maintain a controlled environment with 40-60% relative humidity and handle components by their edges to prevent static discharge.
During transport, protect your items from extreme temperatures and physical shocks by using proper shock-absorbing materials and secure containers.
- Picture yourself carefully lifting a delicate microchip using static-safe tweezers, holding it only by its edges
- Visualize sealing a component in a metallic Faraday cage bag that reflects light with its protective coating
- Imagine placing foam inserts around your packaged component, creating a cushioned nest for safe transit
- See yourself applying bright warning labels that clearly mark the package as ESD-sensitive
Upon receipt, inspect packages thoroughly for any signs of damage or moisture intrusion before opening them in a static-safe environment.
Document any issues immediately and maintain proper handling procedures throughout the inspection process.
Cost Benefits of Protection
Three compelling reasons make investing in proper ESD protection a smart financial decision.
First, you'll considerably reduce damage costs, as the expense of replacing damaged electronic components far exceeds the cost of protective packaging. ESD bags and moisture barriers prevent both immediate and long-term damage, protecting your investment from costly repairs.
Second, you're extending the lifespan of your components when you use high-quality protective packaging. Moisture barrier bags keep components dry, while proper ESD protection shields them from static electricity that can degrade performance over time.
By combining static and moisture protection, you'll prevent corrosion and contamination that could otherwise shorten your components' life expectancy.
Third, you're getting extensive protection against multiple environmental threats. When you use ESD bags with moisture barriers and add features like desiccants and humidity indicator cards, you're creating a complete protective system.
You can enhance this protection further by vacuum sealing the bags. While basic static dissipative bags aren't sufficient, investing in quality packaging that includes Faraday cage protection will save you money by preventing damage throughout the storage and shipping process.
Frequently Asked Questions
Can Static-Safe Bags Be Reused, and How Many Times Safely?
You can reuse static shielding bags if they're undamaged, but you'll need to inspect them carefully before each use. It's best to limit reuse to 3-5 times and discard bags with tears or wrinkles.
What Happens if You Accidentally Touch Components Without ESD Protection?
If you touch components without ESD protection, you can damage or destroy them instantly. You won't always see visible damage, but the static discharge from your body can silently degrade or kill sensitive electronics.
How Long Do Anti-Static Treatments Typically Last on Packaging Materials?
You'll typically find anti-static treatments last 1-2 years, but their effectiveness can vary based on storage conditions, handling frequency, and material type. It's best to check manufacturer specifications for specific durations.
Does Extreme Cold Affect the Performance of Moisture Barrier Bags?
While your moisture barrier bags will maintain their vapor protection in extreme cold, you'll need to watch for reduced flexibility and potential seal issues. The aluminum layer and desiccants continue working, just less efficiently.
Can Regular Plastic Bags Be Converted Into Static-Safe Packaging?
You can't convert regular plastic bags into static-safe packaging. It's not feasible or safe for your electronics. You should always use properly manufactured static-safe bags that meet industry standards for ESD protection.
In Summary
You'll save significant costs and protect sensitive components by implementing proper static-safe packaging with moisture barriers. Don't underestimate the importance of regular testing and careful handling procedures. Make sure you're following the storage guidelines and using appropriate ESD materials. When you invest in quality protection measures now, you'll prevent costly damage and extend the life of your electronic products later.
Leave a Reply