MSD packaging standards are strict because moisture can devastate your electronic components and lead to costly failures. When moisture infiltrates devices, it causes delamination between the die and packaging, accelerates oxidation, and compromises solder joint reliability. You'll need to keep internal humidity levels below 10% RH to prevent the dreaded "popcorn effect" and other damage that often goes unnoticed until it's too late. Industry standards like J-STD-033 and IPC-1605 exist to protect your components through proper storage, handling, and packaging protocols. Understanding these requirements can save you from substantial warranty claims and reputation damage.
The Reality of Moisture Damage
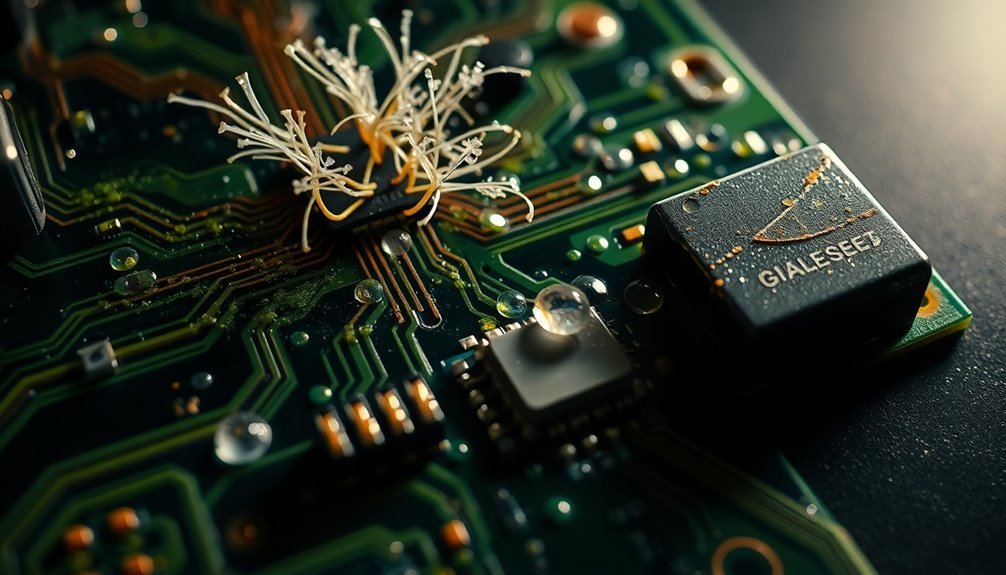
In electronic device manufacturing, moisture poses a severe and persistent threat to component integrity. When moisture infiltrates your devices, it triggers a cascade of destructive effects that can compromise their functionality and reliability.
You'll find that moisture causes delamination between the die and packaging, while also leading to the dangerous "popcorn effect" where trapped moisture becomes steam, creating cracks in the plastic package.
You're facing multiple risks when moisture enters your components. It accelerates oxidation, promotes the formation of intermetallic compounds, and greatly degrades solder joint reliability. Internal humidity levels should be kept below 10% RH in storage to prevent these issues.
These issues don't just affect the immediate assembly process – they can cause long-term reliability problems that may not become apparent until after your products are in the field. Manual tracking errors frequently lead to unknown exposure levels, forcing additional baking that can further compromise component integrity.
What's particularly challenging is that moisture can infiltrate at any stage between circuit card fabrication and final assembly.
You can't afford to be casual about moisture control because once it's introduced, eliminating it becomes vital for preventing issues in subsequent processing steps.
That's why you'll need to implement strict storage protocols using dry bags or cabinets, and carefully manage exposure times between processing steps to maintain component integrity.
Meeting Industry Compliance Requirements
Steering through industry compliance requirements demands a thorough understanding of multiple standards that govern moisture-sensitive device handling.
You'll need to familiarize yourself with key standards like J-STD-033 and IPC-1605, which provide essential guidelines for packaging, storage, and handling of moisture-sensitive devices.
To meet these requirements, you must implement proper packaging protocols using moisture barrier bags, desiccants, and humidity indicator cards. Workers must maintain relative humidity between 5-10% RH in storage environments. Effective packaging is crucial as it ensures product safety and integrity throughout the supply chain.
It's vital that you guarantee all packaging materials meet specifications and that sealing techniques follow standardized methods. You'll also need to manage exposure times meticulously, tracking floor life and implementing appropriate bake cycles when necessary.
Your compliance strategy should include extensive training programs for operators and integration of automated tracking systems.
You'll want to establish clear communication channels with suppliers to maintain consistency throughout the supply chain.
Regular monitoring of your MSD handling procedures is essential to verify ongoing compliance.
Remember that these standards aren't static – they're regularly updated, so you'll need to stay current with revisions and adjust your processes accordingly.
Proper implementation of these requirements helps prevent costly moisture-related defects and guarantees product reliability.
Critical Storage and Handling Protocols
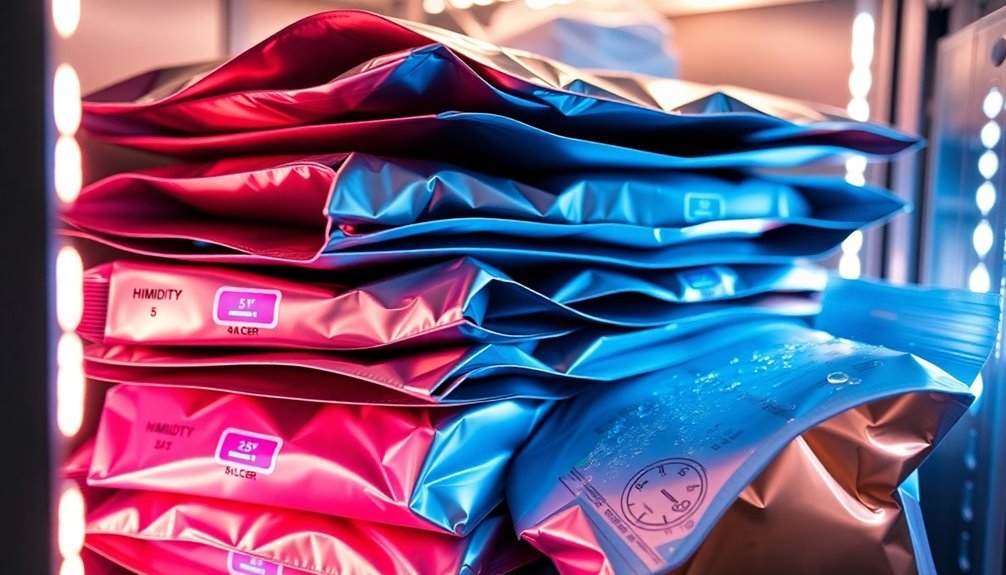
You'll need to maintain strict control over your dry cabinet conditions, ensuring humidity levels remain below 10% RH and temperature stays consistent with manufacturer specifications.
When you're accessing MSDs from dry storage, it's essential to minimize the exposure time and promptly return unused components to their protective environment.
You must properly reseal any opened moisture barrier bags using appropriate heat-sealing techniques and include fresh desiccants with humidity indicator cards to maintain the integrity of stored components.
Dry Cabinet Control Requirements
Maintaining precise control over dry cabinet conditions stands as a cornerstone of proper MSD handling. You'll need to guarantee your dry cabinets maintain relative humidity at 10% or less, with an ideal target of 5% RH for critical components. The temperature shouldn't exceed 30°C to prevent moisture-related damage to your sensitive electronic components.
When you're working with MSDs, you must transfer them to dry storage within 30 minutes of opening moisture barrier bags (MBBs) if your environment exceeds 30°C/60% RH. For Level 5 and 5a components, you'll need to implement re-drying procedures if exposure extends beyond 8 hours. Your desiccant cabinets should maintain humidity below 5% RH during this process.
You'll want to monitor and record MBB opening times meticulously while conducting swift visual inspections to minimize exposure. Remember to implement proper ESD protection during handling and baking procedures.
When baking is necessary, maintain 125°C for high-temperature trays, but don't exceed 40°C for low-temperature trays. After baking, use dry cabinets for cooling to prevent moisture re-absorption and maintain component integrity.
Proper Resealing After Opening
Building on proper dry cabinet control, proper resealing of moisture-sensitive devices demands immediate attention once packages are opened. You'll need to verify original desiccant reuse if exposure time hasn't exceeded 30 minutes for Level 2-4 MSDs. When resealing, inspect your HICs for any signs of moisture exposure and confirm the integrity of your MBB seals.
Action | Requirement | Critical Check |
---|---|---|
Timing | Immediate resealing | Monitor exposure clock |
Desiccant | Use original if <30 min | Calculate sufficient amount |
HIC | Place inside MBB | Check for moisture indicators |
Seal Integrity | Verify complete seal | Inspect for damage |
Your resealing process must follow J-STD-033B.1 standards precisely, verifying you've calculated the correct desiccant amount to maintain proper humidity levels. You can't afford to skip any steps, as moisture absorption happens quickly. Remember to track your exposure times accurately and document each resealing event. If you're unsure about the package's integrity or exposure duration, you'll need to follow re-baking procedures before resealing to prevent potential component damage.
Cost Impact of Poor Management
Poor MSD management can rack up substantial costs across multiple areas of electronics manufacturing. When you don't properly handle moisture-sensitive devices, you'll face immediate expenses from damaged components that crack or delaminate during the reflow process. These failures often require complete replacement of parts, driving up both material and labor costs.
You'll encounter operational inefficiencies that drain your resources when you rely on manual tracking systems prone to human error. Without standardized procedures and proper training, your staff's inconsistent handling practices can create production delays and supply chain disruptions. Each time you need to repeat bake cycles due to incorrect exposure tracking, you're not only wasting energy but also potentially compromising the integrity of your components.
The long-term financial impact can be even more severe. If you deliver defective products due to moisture-related failures, you'll face warranty claims and potential damage to your brand reputation.
Non-compliance with industry standards might result in regulatory penalties, while systematic failures in your MSD management can lead to lost revenue and decreased customer trust. These consequences make proper MSD handling essential for maintaining both product quality and your bottom line.
Prevention Through Proper Packaging
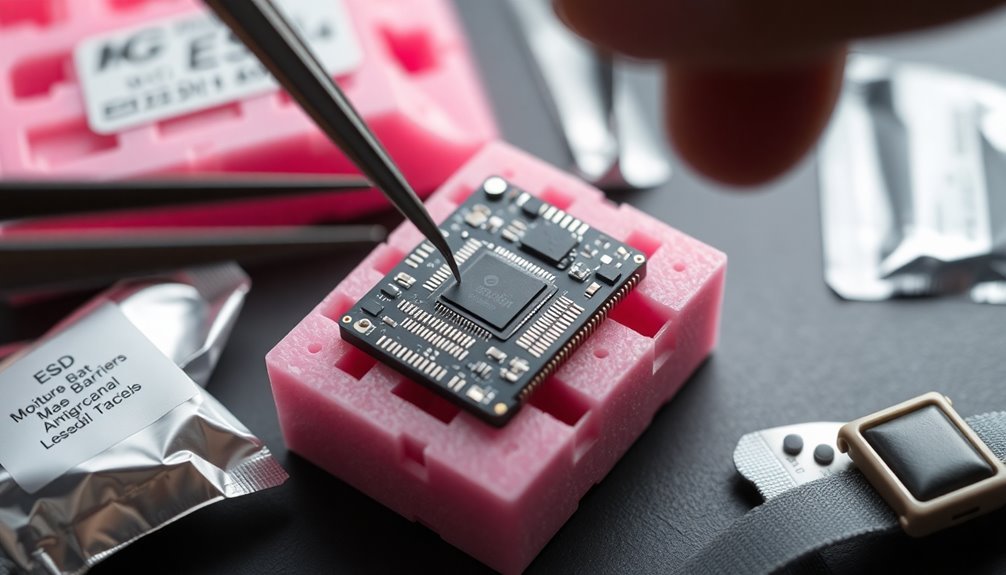
Effective packaging serves as your first line of defense against moisture damage in electronic components.
You'll need to guarantee your Moisture Barrier Bags (MBBs) maintain humidity levels below 10% RH through proper sealing and desiccant use. These bags, coupled with Humidity Indicator Cards (HICs), create a controlled environment that protects your sensitive devices.
When you're handling MSDs, you must keep ambient conditions below 30°C and 60% RH.
You'll want to store components in dry cabinets between processing steps and maintain detailed records of exposure times. If you need to bake devices, don't exceed 125°C for high-temperature trays or 40°C for low-temperature trays, and always maintain ESD protection throughout the process.
Your packaging must comply with J-STD-033 and IPC-1605 standards.
You'll need to use appropriate MBB materials, include sufficient desiccant quantities, and implement proper sealing techniques. Remember that your storage conditions directly affect shelf life, so you should minimize handling times and maintain strict humidity control.
When reusing MBBs, you must replace desiccants and verify proper sealing to guarantee continued protection.
Supply Chain Quality Control
You'll need to establish rigorous supplier certification requirements that align with GMP principles and maintain detailed documentation of quality standards throughout your supply chain network.
Independent quality assurance audits must be regularly conducted to verify compliance with established quality control systems and GMP requirements.
Your real-time tracking systems must integrate with quality control checkpoints to monitor product integrity and enable swift responses to any deviations from established standards. Dedicated teams of detail-oriented personnel perform comprehensive inspections to identify potential quality issues.
When handling cross-border shipments, you're required to implement additional verification protocols that guarantee consistent quality control measures across different regulatory jurisdictions while maintaining complete traceability of your products.
Supplier Certification Requirements
Supply chain integrity in MSD packaging hinges on rigorous supplier certification requirements. You'll find that suppliers must demonstrate thorough compliance with J-STD-033B.1 and IPC-1605 standards, which govern everything from dry packaging to storage protocols. It's not just about following rules – it's about proving consistent adherence through ongoing audits and detailed documentation. Similar to how Type II MSD systems produce effluent with consistently low contaminant levels, packaging suppliers must maintain reliable quality standards.
Certification Focus | Requirements | Verification Method |
---|---|---|
Material Quality | MBBs, Desiccants, HICs | Physical Testing |
Storage Controls | Temperature, Humidity | Environmental Monitoring |
Handling Procedures | ESD Protection, Exposure Limits | Process Audits |
When you're working with certified suppliers, you can expect them to maintain precise records of MSD handling and provide evidence of proper dehumidification processes. They'll need to show they're using appropriate materials for each MSD level (2a to 5a) and following specific drying procedures, typically at temperatures up to 125°C. Your suppliers must also demonstrate they've implemented robust communication systems to stay current with industry standards and maintain clear documentation trails from component entry to final packaging.
Real-Time Tracking Systems
Integrating seamlessly with modern supply chains, real-time tracking systems form the backbone of MSD quality control.
You'll find these systems monitoring components from the moment supplier packaging is opened until the final reflow process, markedly reducing the risks associated with manual tracking errors.
When you implement real-time tracking, you're getting strategic placement of monitoring units throughout your facility – from stockrooms to SMT assembly lines.
These systems automatically track exposure times, log bake cycles, and monitor storage conditions, ensuring you're always compliant with J-STD-033 standards.
You won't just improve your current operations; you'll also set yourself up for future expansion.
The networked software can be upgraded to track all SMT components, not just MSDs, while advanced algorithms help you predict and prevent moisture-related issues before they occur.
Cross-Border Quality Verification
From the initial supplier handoff to final assembly, cross-border quality verification demands rigorous oversight of moisture-sensitive devices. You'll need to guarantee that suppliers properly package components in Moisture Barrier Bags (MBBs) with appropriate desiccants and humidity indicator cards. These bags must maintain their seal integrity throughout the entire supply chain journey.
When you're handling MSDs across borders, you must verify that suppliers follow J-STD-033 standards for packaging and storage. It's critical to maintain strict temperature and humidity controls, especially when devices travel through different climate zones. If you discover that devices have been previously exposed to moisture, they'll need proper baking before being resealed in MBBs.
You'll want to implement a robust storage system that keeps devices in environments not exceeding 30°C/60% RH for more than one hour. You must track exposure times meticulously and guarantee quick returns to dry packaging when devices aren't used immediately.
Frequently Asked Questions
How Long Can MSDS Survive Accidental Exposure to High Humidity Environments?
You shouldn't expose MSDs to high humidity for more than 8 hours. If you exceed this limit, you'll need to perform immediate drying procedures to prevent damage like delamination and the popcorn effect.
Can Damaged MSD Packaging Be Repaired Without Compromising Component Integrity?
You can repair damaged MSD packaging, but you'll need to follow strict protocols including re-drying components and proper re-sealing. It's safer to re-package components entirely to guarantee their integrity remains intact.
What Alternatives Exist for Companies That Cannot Afford Dry Storage Facilities?
You can use moisture barrier bags with desiccants and humidity indicator cards as cost-effective alternatives. Dry bags near production lines, combined with proper tracking systems, offer reliable temporary storage for your moisture-sensitive devices.
Do Different Geographical Climates Require Adjustments to Standard MSD Packaging Requirements?
Yes, you'll need to adjust your MSD packaging based on your location's climate. In humid regions, you should use stronger moisture barriers and more desiccants, while dry climates may require less stringent measures.
How Often Should MSD Handling Training Be Updated for Facility Personnel?
You'll need to update your MSD handling training at least annually and whenever standards change. It's important to schedule additional sessions if you're implementing new procedures or receiving feedback about handling issues.
In Summary
You'll find that strict MSD packaging standards are your first line of defense against costly component failures and manufacturing delays. By following these rigorous protocols, you're not just meeting compliance requirements – you're protecting your investment and ensuring product reliability. Don't underestimate moisture's destructive power; proper MSD packaging practices will save you money and maintain your reputation for quality throughout the supply chain.
Leave a Reply