You'll want to maintain relative humidity levels between 35-65% for successful electronics assembly, with 40% RH being the ideal sweet spot. This range prevents both moisture-related damage and static electricity issues. For specific processes, keep humidity at 40-50% RH for solder paste application and 35-45% RH for semiconductor assembly, while maintaining temperatures between 65-77°F. Too much humidity leads to corrosion and short circuits, while too little causes ESD risks and brittle components. Proper humidity control maximizes production quality and device longevity. Understanding the full scope of moisture control can transform your assembly outcomes.
Understanding Moisture Control Fundamentals
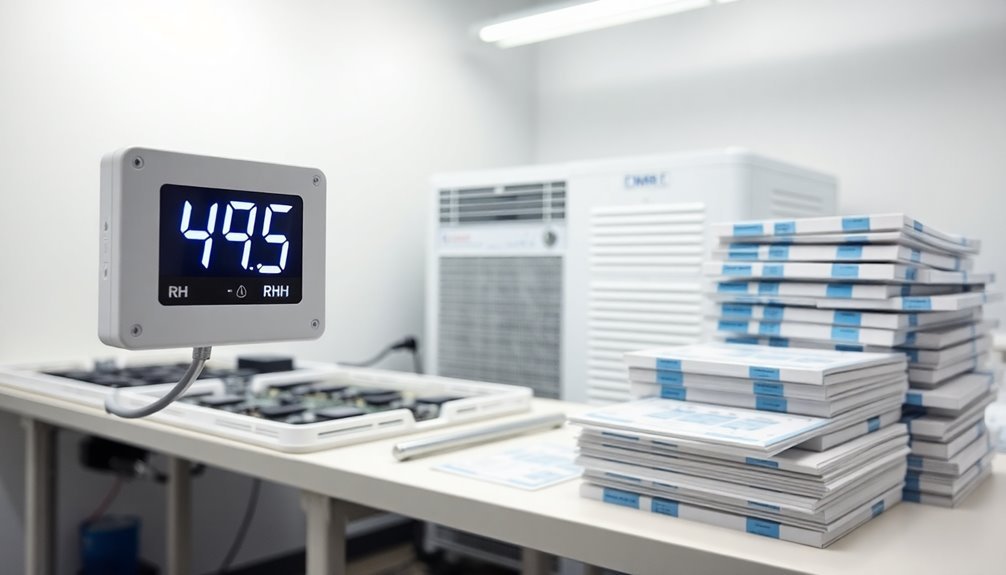
Confronting the challenges of moisture control in electronics assembly begins with understanding how water vapor can compromise your components and assemblies. You'll need to recognize that moisture infiltration occurs through multiple pathways, from environmental conditions to manufacturing processes, and even through human contact during handling.
When moisture infiltrates your electronics, it triggers several destructive mechanisms. You'll find that oxidation attacks metal contacts, reducing their conductivity, while electrochemical migration accelerates corrosion across your assembly. The presence of moisture can lead to signal distortion due to its effects on insulation materials.
These issues don't just affect performance – they can lead to complete system failures and shortened product lifespans.
You'll want to focus on both prevention and management strategies. Start by controlling your production environment's humidity levels and implementing proper sealing techniques. Don't overlook the importance of pre-baking boards before soldering, especially in humid conditions.
You should also consider strategic component placement on your PCBs to minimize moisture exposure.
Remember that effective moisture control isn't just about preventing water vapor entry – it's about creating thorough protection through multiple layers of defense. This includes selecting moisture-resistant materials, applying protective coatings, and ensuring proper ventilation throughout your assembly's lifecycle.
Ideal Humidity Range Guidelines
Having established the fundamentals of moisture control, let's focus on the specific humidity ranges that protect your electronics during assembly. You'll want to maintain relative humidity between 35-65% for general electronics assembly, with an ideal target of 40% RH for best ESD protection and corrosion prevention.
Process Type | Humidity Range | Temperature Range |
---|---|---|
Solder Paste | 40-50% RH | 65-75°F |
Semiconductor | 35-45% RH | 70-77°F |
General Assembly | 35-65% RH | 70-77°F |
Your facility's humidity control directly impacts product quality and manufacturing success. When humidity drops too low, you'll face increased ESD risks and rapid solder paste drying. If it rises too high, you'll encounter condensation issues and potential corrosion, especially in areas with closely spaced pads. Using proper desiccants during storage helps maintain these optimal conditions.
For sensitive processes and wafer transportation, you should maintain humidity between 40-45% RH. This range offers the best protection against both static electricity and moisture-related defects. You'll find that maintaining these levels not only protects your components but also extends the shelf life of your assembled PCBs and creates consistent manufacturing conditions throughout your facility.
Static Prevention Through Humidity
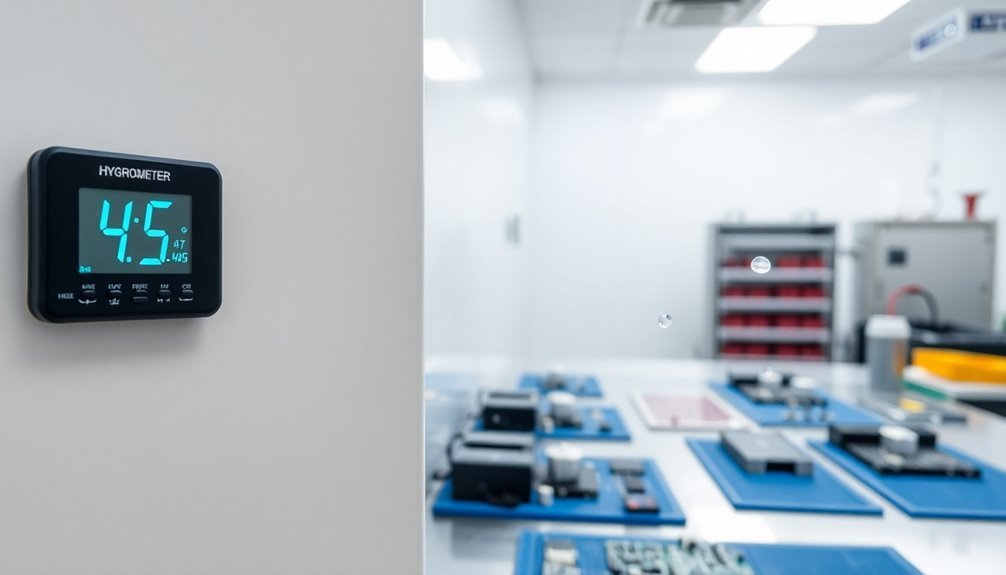
Maintaining proper humidity levels in your electronics assembly environment creates a moisture barrier that naturally prevents static buildup and ESD damage.
You'll find that air moisture molecules attach themselves to surfaces, forming a protective layer that allows static charges to dissipate safely rather than accumulate. The ideal relative humidity range 40-60% provides optimal static control while avoiding excess moisture.
To guarantee consistent static prevention, you should implement regular humidity monitoring with calibrated sensors and maintain detailed logs of your facility's moisture levels.
Moisture's Role Against ESD
While electronic components are sensitive to many environmental factors, humidity plays a crucial role in preventing electrostatic discharge (ESD) during assembly operations.
When moisture levels in the air rise above 30% RH, you'll notice a significant reduction in static electricity buildup, as water molecules create a natural conductive layer on surfaces that helps dissipate charges.
To effectively protect your electronic assemblies, you'll want to maintain humidity levels between 45% and 55% RH. This range provides the best protection against ESD while avoiding the corrosive effects that can occur at higher humidity levels above 70% RH. Implementing advanced humidity control systems ensures consistent environmental conditions throughout the manufacturing process.
You should pay special attention to areas near hot machinery, where localized dry air pockets can create unexpected static buildup risks.
- Moisture acts as a natural conductor, helping to dissipate static charges before they can cause damage
- Humidity levels above 40% RH create a protective film on surfaces that prevents charge accumulation
- Areas with humidity below 30% RH are at high risk for tribocharging and electrostatic induction
- Proper moisture control helps eliminate invisible ESD events that can damage components without visible signs
The key is maintaining consistent humidity levels throughout your assembly area to guarantee reliable ESD protection.
#
Humidity Monitoring Best Practices
By maintaining these best practices, you'll create a reliable humidity control system that protects your electronic components and guarantees manufacturing success.
Remember that proper monitoring isn't just about meeting standards – it's about creating a consistently safe environment for your sensitive electronic components.
Proper Humidity Levels
Maintaining optimal humidity levels is crucial. When humidity levels are too low, static electricity builds up and discharges unexpectedly, potentially destroying delicate electronic components. This discharge can cause immediate failures or latent defects, leading to product recalls and customer dissatisfaction. Research by leading institutions has shown that a 35-45% RH range provides the best protection against humidity-related issues.
Minimizing ESD
Humidity control minimizes the buildup and discharge of static electricity, reducing the risk of ESD-related failures during manufacturing processes. With a humidity level of 40% RH, surface resistance is lowered on floors, carpets, table mats, and other areas, which helps to dissipate electric charges and prevent ESD events.
Balancing Humidity
Finding the perfect humidity level in manufacturing is like walking a tightrope. On one side, low humidity can lead to ESD, where static electricity builds up and suddenly discharges, damaging sensitive electronic components. On the other, high humidity can cause condensation and corrosion, leading to short circuits and long-term reliability issues. Advanced humidity control systems can help maintain this delicate balance, ensuring the environment remains within the optimal range.
Additional Protection Measures
In addition to maintaining optimal humidity levels, other protection measures can be employed. For example, using a conformal coating on PCBs provides significant protection against humidity and water uptake. These materials prevent the electrochemical growth of conductive salts or filaments between exposed metals on surface layers and protect the components themselves by providing a complete shield against moisture uptake.
Comprehensive Humidity Control
Effective humidity management is not just about preventing damage; it's about optimizing the entire production process. With the right humidity levels, electronic components are easier to handle, soldering processes become more reliable, and the overall assembly line runs more smoothly. It also reduces the risk of contamination, as stable humidity levels prevent the buildup of dust and other particulates that can interfere with manufacturing.
Dehumidification and Advanced Strategies
Dehumidification is a crucial ally in the battle against excess moisture in electronics manufacturing. Modern dehumidification systems are highly efficient and can be customized to suit specific manufacturing environments. They ensure that the air remains at optimal humidity levels, protecting delicate electronic parts from moisture damage. Advanced humidity control strategies involve a holistic approach to managing the manufacturing environment, including integrating climate control systems with real-time monitoring and data analytics.
Moisture Effects On Component Reliability
Through constant exposure to environmental conditions, moisture poses significant threats to electronic component reliability. When moisture infiltrates assemblies, it can trigger a cascade of destructive processes that compromise both performance and longevity.
Maintaining humidity levels between 30% and 70% RH helps prevent these issues from developing. Moisture combined with conductive contaminants creates paths for short circuits, while also promoting electrochemical migration and corrosion of essential connections.
Component reliability faces particular challenges when moisture absorption occurs, as it can lead to material degradation and altered electrical properties. Hygroscopic materials are especially susceptible, often experiencing swelling and dimensional changes that affect their functionality.
The presence of moisture also increases the risk of oxidation on metal contacts and can foster the growth of mold or fungi on PCBs.
- Short circuits and electrochemical migration can cause immediate component failure
- Corrosion of electrical connections leads to intermittent faults and system instability
- Material swelling and misalignment compromise mechanical integrity
- Degradation of insulating materials alters critical dielectric properties
Understanding these effects is vital as they often develop gradually and may not be apparent until significant damage has occurred. You'll need to implement proper humidity control measures to protect your components from these reliability threats.
Maintaining Optimal Assembly Conditions
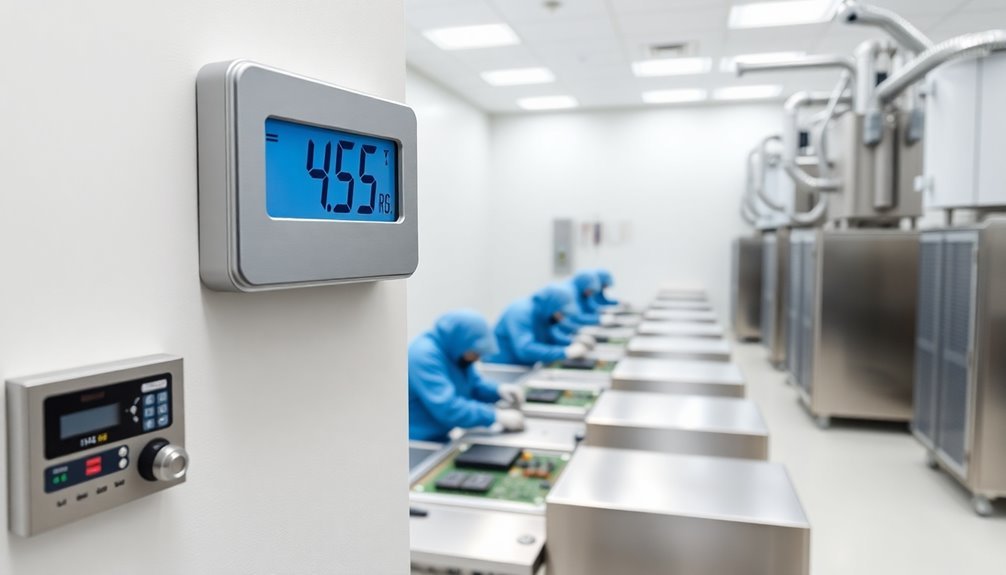
In accordance with industry standards, maintaining ideal assembly conditions requires precise control over relative humidity levels, typically between 40% and 50% RH.
You'll need to design your facility with high-quality humidity control systems that can consistently maintain these levels, especially in cleanroom environments where requirements are even stricter (35% to 45% RH).
When you're working with electronics assembly, you must consider that different components have varying moisture sensitivity levels (MSL).
You'll want to monitor your solder paste application conditions carefully, keeping the environment between 65°F to 75°F with 40% to 50% RH to achieve optimal results.
It's vital to prevent both extremes – too low humidity can increase ESD risks, while excessive moisture can lead to condensation and incomplete soldering. The use of automated 3D inspection helps detect any moisture-related soldering defects immediately.
You'll need to account for your geographical location and external environmental factors when setting up your humidity control systems.
If you're in an arid or tropical climate, you may need additional equipment to maintain stable conditions.
Remember to implement proper storage and packaging procedures, including the use of desiccants, to protect your assembled PCBs from humidity infiltration during non-production periods.
## Humidity Monitoring Best Practices
You'll need to implement real-time data collection through a network of calibrated humidity sensors that continuously monitor your assembly environment and feed information to a centralized system.
Set up automated alerts that trigger when humidity levels approach your predetermined thresholds, typically between 30-50% RH for electronics assembly.
Configure your monitoring system to log historical data, which enables you to track trends and make proactive adjustments before humidity issues affect production quality.
Real-Time Data Collection Methods
Effective real-time humidity monitoring relies heavily on selecting the right combination of sensors and data collection methods. You'll find that capacitive sensors offer superior accuracy and rapid response times, while being resistant to contamination in dusty environments.
For your electronics assembly needs, optical sensors provide exceptional sensitivity without electromagnetic interference concerns.
Your data collection system should incorporate high-quality data loggers with stainless steel construction and integrated modules for real-time reporting. When you're monitoring sensitive electronics, Remote Telemetry Units (RTUs) become essential for processing data and generating immediate alerts if humidity levels deviate from acceptable ranges.
- Choose sensors based on your specific environment – capacitive for dusty conditions, optical for areas with electromagnetic interference
- Implement data loggers with sufficient memory capacity (120,000+ data points) for continuous monitoring
- Use RTUs with thresholding capabilities to enable instant alert generation
- Verify proper sensor calibration within the 10-90% RH range for accuracy
You'll need to evaluate environmental factors and customize your setup based on location-specific requirements. Regular calibration and system flexibility will help maintain precise humidity control throughout your electronics assembly process.
Alert Systems Setup Guidelines
Building upon your data collection framework, a robust alert system serves as your primary defense against humidity-related issues in electronics assembly. You'll need to select appropriate sensors that match your specific environment, integrating them with Remote Telemetry Units (RTUs) for thorough monitoring and real-time notifications.
When setting up your alert system, choose from various sensor types based on your specific needs. Capacitive sensors offer high accuracy but consider EMI sensitivity, while optical sensors provide EMI immunity. For harsh environments, opt for resistive sensors, and when real-time monitoring is vital, electrochemical or semiconductor IC sensors deliver reliable performance.
To maintain system effectiveness, you'll need to calibrate your sensors every 6-12 months and implement multiple threshold values that trigger alerts when humidity levels fall outside the acceptable range of 30-70% RH.
Configure your RTUs to continuously monitor conditions and immediately notify equipment when thresholds are crossed. Remember to account for seasonal variations and specific component sensitivity in your threshold settings.
Your alert system should integrate with your facility's existing infrastructure and include battery backup to guarantee uninterrupted monitoring during power failures.
Frequently Asked Questions
How Quickly Can Humidity Changes Damage Electronic Components During Assembly?
You'll see damage to electronics within minutes of exposure to high humidity, as moisture can instantly trigger short circuits, while rapid humidity changes can immediately affect sensitive components through condensation and material stress.
What Emergency Procedures Should Facilities Follow During Sudden Humidity Control Failures?
You'll need to immediately alert staff, halt production, and activate ESD protocols. Deploy temporary dehumidifiers, protect sensitive components, and isolate affected areas while your maintenance team repairs the humidity control system.
Do Different Geographical Regions Require Different Humidity Control Equipment Specifications?
Yes, you'll need different equipment specs for each region. Your coastal areas require higher-capacity dehumidifiers, while arid regions need less robust systems. Climate patterns and local humidity levels determine your specific equipment needs.
How Does Seasonal Variation Affect Humidity Control System Maintenance Requirements?
You'll need more frequent system maintenance during extreme seasons. You must adjust filters, calibrate sensors, and clean components more often when dealing with summer's high humidity and winter's dry conditions.
Can Temporary Portable Humidifiers Effectively Supplement Main Systems During Peak Production?
Yes, you'll find portable humidifiers can effectively supplement main systems during peak production when they're properly sized and positioned. However, you must monitor their output closely and maintain them regularly for top-notch performance.
In Summary
You'll find maintaining proper humidity control essential for electronics assembly success. Keep your facility's relative humidity between 30-60%, implementing monitoring systems and environmental controls. Don't risk component damage or ESD issues – regular humidity checks and swift corrective actions protect your investment. Remember, ideal moisture levels guarantee reliable bonds, prevent static discharge, and maximize production quality.
Leave a Reply