When working on electronics repairs, you'll need proper grounding to prevent static damage. Start with an ESD wrist strap connected to a verified ground point, and pair it with an anti-static floor mat. Keep your workspace equipped with a grounded metal surface and ESD-safe workbench. Don't forget to wear static control garments and gloves while handling components. Maintain humidity levels between 40-60%, and regularly test all grounding equipment. Use proper computer case discharge methods, implement multiple grounding points when needed, and always verify surface conductivity first. These foundational steps will guide you toward mastering safe electronics repair techniques.
ESD Wrist Straps
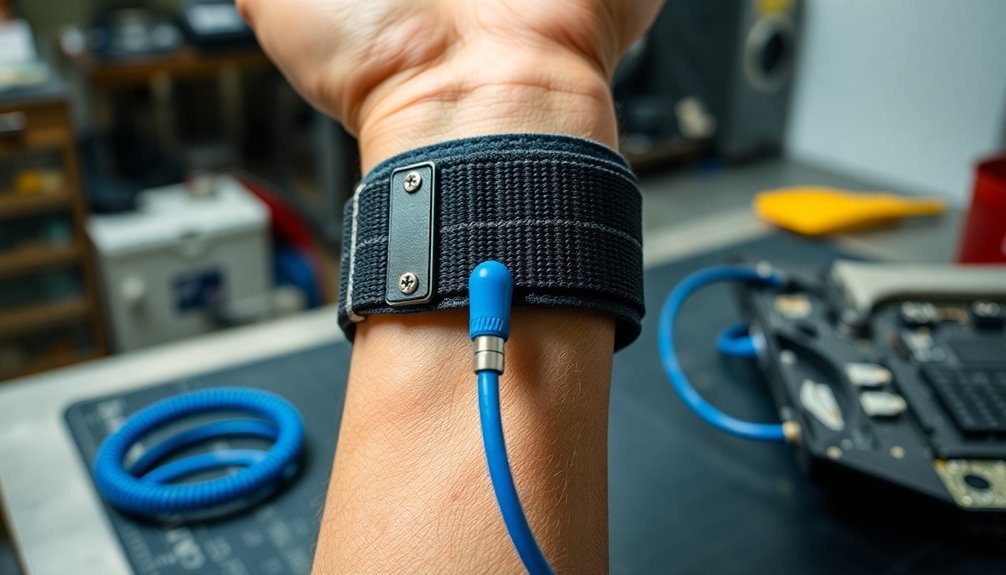
A reliable ESD wrist strap serves as your first line of defense against static electricity when working with sensitive electronics. When you're handling delicate components during repairs, the strap's anti-static properties prevent static buildup that could potentially damage your devices. With 4.7 out of 5 stars from customers, these straps prove highly reliable for electronics repair work.
The design features an adjustable elastic band with a secure buckle, ensuring a comfortable fit while maintaining consistent contact with your skin for effective grounding. Like many products on AliExpress, these straps come with buyer protection to ensure your purchase is secure.
You'll find these essential safety tools at electronics retailers like Best Buy or through various online marketplaces that offer international shipping options. Before starting any repair work, you'll need to connect the strap's grounding point properly and inspect it for any signs of wear or damage.
The cordless design allows you greater mobility while working, but don't forget to maintain regular contact with your grounding point.
To keep your ESD wrist strap in ideal condition, clean it regularly and store it properly when not in use. If you notice any damage or deterioration, take advantage of the 30-day return policy offered by most retailers to replace it.
Anti-Static Floor Mats
While ESD wrist straps protect your hands and arms, anti-static floor mats complete your thorough grounding setup. These mats, available in sizes from 12 x 18 inches to 23 x 47 inches, create a safe work surface that prevents static electricity damage to your electronic components. The non-slip surface provides essential stability during delicate repair work. The molded domed surface of some models offers superior static dissipation capabilities.
When selecting an anti-static floor mat, you'll want to focus on three key features. First, make sure it's made of durable thermoplastic or rubber material that can withstand regular use. Second, verify it has a reliable grounding wire system that you can easily connect. Third, confirm it meets ANSI/ESD S 4.1 compliance standards for guaranteed ESD protection.
To maximize your mat's effectiveness, you'll need proper installation and maintenance. Start by placing it on a clean, flat surface and connecting the grounding wire securely. Clean it regularly with mild detergent and water, and inspect both the mat and grounding wire for wear.
Some mats offer additional features like heat resistance for soldering work and convenient screw slots for organizing small parts during repairs. If you notice significant wear or damage to the grounding wire, don't hesitate to replace the mat to maintain peak protection.
Computer Case Discharge Method
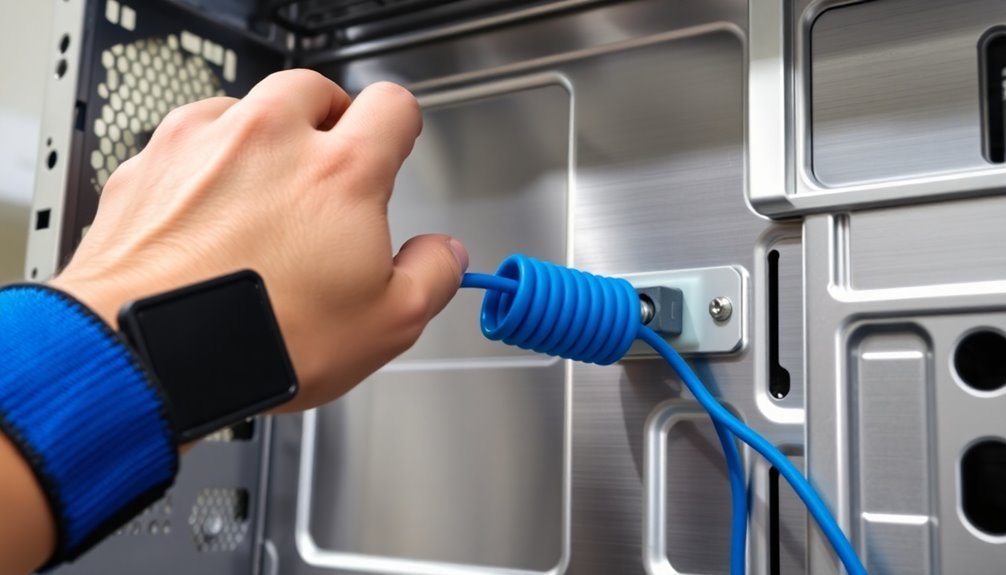
Before you start working on your computer, you'll need to identify the bare metal contact points on your case that provide the best grounding connection.
When touching these metal areas, make sure they're not painted or coated, as these surfaces won't effectively discharge static electricity from your body.
You should perform a quick ground wire safety check by ensuring your power supply is properly connected to a grounded outlet, even though the computer remains powered off during repairs.
It's critical to remove all watches and jewelry from your hands before beginning any repair work to reduce static risks.
Working in an environment with 45-55% humidity provides optimal conditions for preventing ESD damage while working on electronics.
Metal Case Contact Points
Metal case contact points serve as vital discharge pathways in computer repair and maintenance. You'll need to guarantee these points are clean and free from oxidation to maintain effective grounding. Use a brass or steel brush for regular cleaning, or opt for a nylon brush on more sensitive contacts. If you're dealing with stubborn buildup, you can apply vinegar or baking soda as mild cleaning agents. Regular inspection of contact points will help identify white crusty residue that indicates potential corrosion issues. Keep one hand away while working on metal cases to reduce the risk of shock through your chest cavity.
Before you begin any cleaning process, always disconnect the power to prevent electrical hazards. When selecting cleaning materials, avoid harsh solvents that might damage surrounding plastic or rubber components. It's important to test your chosen cleaner on a small area first to prevent unexpected damage.
You'll want to focus on materials like copper, aluminum, or tinned copper for your grounding connections, as they offer superior conductivity. Install spring-loaded connectors where possible to maintain consistent contact, especially in areas prone to vibration.
Remember to check for potential galvanic corrosion between different metals and use appropriate washers or coatings when necessary. Your grounding points must be both mechanically secure and electrically solid to guarantee effective protection against static discharge and electromagnetic interference.
Ground Wire Safety Check
Every ground wire safety check begins with a detailed inspection of your computer case's discharge system.
You'll need to carefully examine the ground wire for any visible damage, wear, or corrosion that could compromise its effectiveness. Check both ends of the wire to verify they're properly connected and secure.
Using a digital multimeter, you'll want to test the ground wire's continuity and resistance. Set your meter to AC volts and measure between the ground wire and known ground points. If you detect any breaks or poor connections, repair them immediately.
Don't forget to test all ground wires in the circuit for extensive safety coverage.
Watch out for common issues that can create hazards. These include corroded connections that increase resistance, improper grounding techniques, and open grounds that don't provide a low-resistance path for fault current.
If you're working with older equipment, be especially vigilant about bootleg connections and improper ground-to-neutral connections.
Remember that unprotected outlets can create serious electrocution risks. While GFCI protection can serve as a temporary solution for open grounds, you'll need to verify all grounding systems meet NFPA and IEEE safety standards for long-term protection.
Proper Static-Free Clothing Selection
Electronics technicians must select appropriate static-free clothing to create a safe working environment when handling sensitive components. When choosing your protective wear, focus on garments that blend conductive and artificial fibers, which automatically discharge static buildup. You'll need to guarantee your clothing reduces charge surface density to less than 7 microcoulombs per square meter for effective protection.
Start with an ESD lab coat or coveralls that feature ultrasonically sealed edges to minimize particle generation. These garments should include static dissipative fibers in their polyester knit construction.
Don't forget to complete your protection with anti-static gloves, as they're essential for direct contact with sensitive electronics.
You'll want to inspect your static-free clothing regularly for signs of wear and tear, as damaged garments won't provide adequate protection. Make certain your chosen attire meets ISO Class 4 cleanroom production standards and maintains low ion and extractable levels.
Grounded Metal Surface Contact
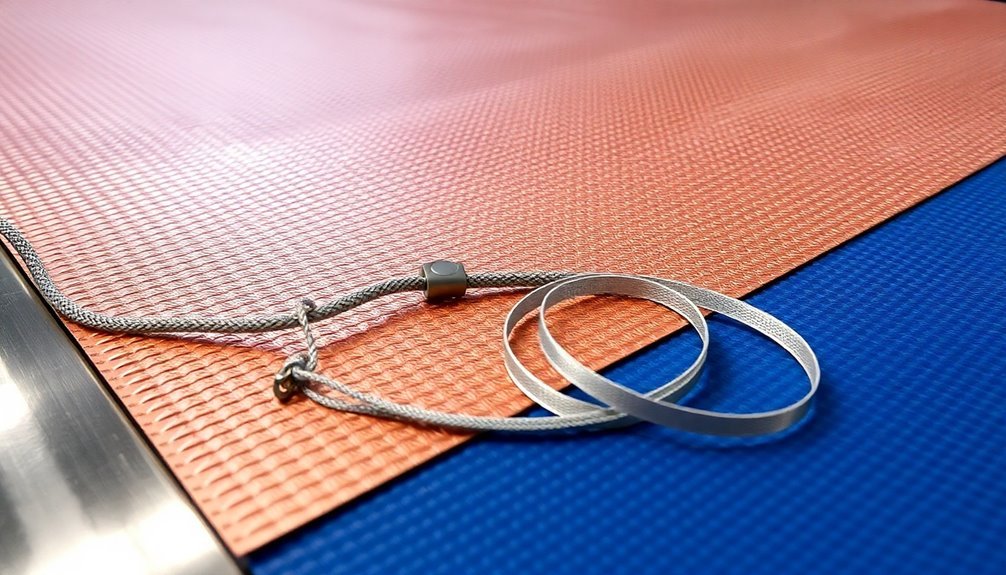
When working on electronics repair, you'll need to identify proper contact points on your grounded metal surface that are free from paint, oxide layers, or other insulating materials.
You should maintain consistent electrical connection by using robust fastening methods like screws or bolts rather than unreliable clips or adhesives.
Before starting any repair work, test the surface's conductivity using a multimeter to ascertain it provides effective grounding protection.
Proper Contact Points Location
Establishing contact points for proper grounding depends heavily on identifying and connecting to designated metal surfaces throughout your workspace.
You'll need to guarantee all conductive surfaces, including your workbench and tools, are properly bonded to clearly marked grounding points that provide the same electrical potential across your work area.
When setting up your contact points, you must connect to designated grounding points, grounding rods, or equipment grounding conductors.
If you're using auxiliary grounding points, connect them to your main grounding system to prevent potential differences.
Install anti-static mats at your workstation to create a safe, static-dissipative surface.
You'll want to implement a thorough grounding strategy that includes proper use of wrist straps and ESD-safe footwear.
Your flooring and footwear system should create a reliable ground path while minimizing triboelectric charging.
Don't forget to regularly test all grounding accessories and inspect your entire grounding system to maintain its effectiveness.
Pay special attention to keeping your contact points easily accessible and maintaining low resistance in your connections.
Remember that improper grounding can lead to costly ESD damage to electronic components.
Maintaining Consistent Metal Connection
Following proper contact point setup, maintaining consistent metal connections forms the backbone of a reliable grounding system. You'll need to guarantee all metallic components, workbenches, and tools are properly bonded to your common ground point, creating an equipotential environment that prevents static buildup. This means connecting all conductive surfaces to eliminate potential differences between items in your work area.
You must regularly test and maintain your grounding accessories, including anti-static mats, wrist straps, and ESD-safe footwear, to verify they're functioning correctly. When you're moving equipment, use dissipative or conductive casters to maintain electrical contact with the floor. Remember that your total resistance to ground, including yourself, footwear, and floor, shouldn't exceed 1.0 x 10^9 ohms.
To maintain effective ground continuity, you'll want to connect all your ESD control materials to the equipment grounding conductor. Keep in mind that insulators can't be controlled through grounding, so you'll need to either eliminate them or manage them separately.
Your accumulated body voltage should stay below 100 volts during standard walking voltage tests to guarantee proper grounding effectiveness.
Testing Surface Conductivity First
Surface conductivity testing serves as your first line of defense in establishing reliable grounding connections. You'll need to use a conductivity meter to measure the surface's electrical properties, guaranteeing it meets the necessary standards for safe grounding. Test multiple points across the surface to verify consistent conductivity, as variations could indicate potential problem areas.
Before conducting your tests, make sure you've properly cleaned the surface by removing any non-conductive films, paint, or oxide layers. Use appropriate conductive cleaners to enhance surface conductivity, but be careful not to leave behind chemical residues that could compromise the connection.
After cleaning, perform another round of conductivity tests to confirm improvement. Compare your conductivity readings against standard benchmarks to guarantee they're within acceptable ranges. If you find areas with poor conductivity, you'll need to address these issues through additional cleaning or surface preparation.
Don't forget to visually inspect the surface for signs of oxidation or contamination that might affect your readings. When you're satisfied with the conductivity test results, you can proceed with establishing your grounding connection, knowing you've verified the surface's ability to conduct electricity effectively.
ESD-Safe Workbench Setup
Creating a proper ESD-safe workbench setup requires careful attention to both materials and grounding methods.
You'll need to start with a static-dissipative or static-conductive surface, preferably using an ESD mat that covers your entire work area. Choose ESD vinyl mats for general electronics assembly or ESD rubber mats if you're doing soldering work.
Connect your workbench directly to a verified ground point, avoiding daisy chain connections. You'll want to establish a common point ground with less than 1 ohm resistance to your electrical outlet. If you need an auxiliary ground, guarantee it maintains less than 25 ohms resistance.
Place all your equipment on the ESD-safe surface and verify it's properly grounded. Use only ESD-safe tools designed for static-sensitive environments, and manage your cords carefully to prevent accidental ground disconnections.
Don't forget to install ESD warning signs and regularly test your wrist straps and heel grounders. If you're working with insulative materials, consider adding an ESD air ionizer to neutralize static charges.
Keep your workspace clean using ESD-safe cleaners, and store sensitive components in ESD-safe bags and foam.
Component Handling Best Practices
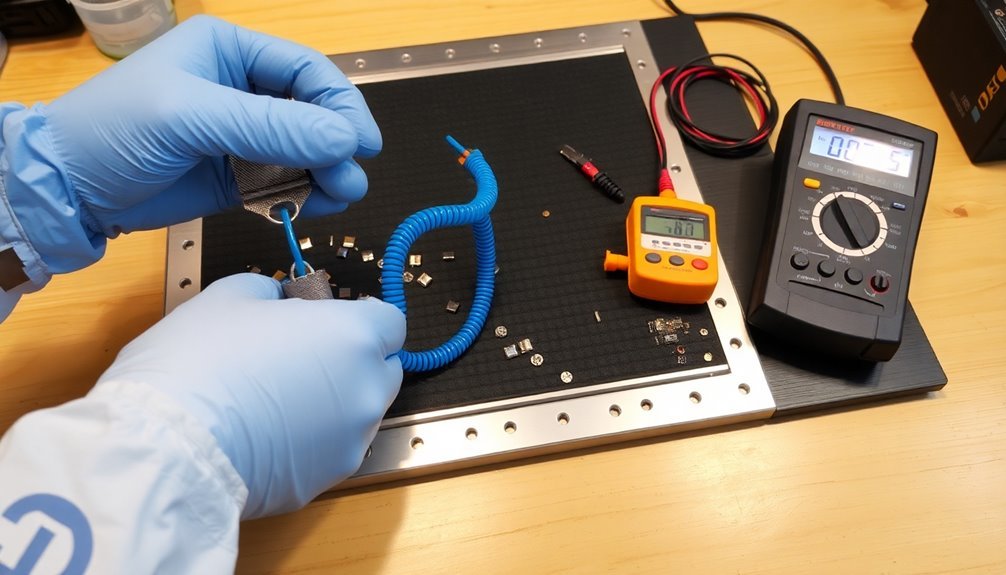
Proper component handling forms the foundation of safe electronics repair. You'll need to handle components by their edges whenever possible, avoiding contact with sensitive areas and leads that can be damaged by static electricity or contamination. For smaller components, use tweezers to guarantee precise and safe manipulation.
When working with circuit boards, you'll want to use specialized racks and trays to prevent physical damage. Never stack boards or assemblies on top of each other, as this can lead to component damage.
Before starting any repair work, you must discharge capacitors to prevent electrical shock and wear an anti-static wrist strap to guard against static discharge.
Store your components and circuit boards in shielded bags or boxes when they're not in use. These materials provide essential protection through static shielding, antistatic cushioning, and static dissipation properties.
Before beginning repairs, conduct a thorough visual inspection using magnifying tools to identify potential issues like cracks, burns, or loose connections. You'll need to avoid using hand creams containing silicone, as these can interfere with soldering and adhesion.
For desoldering tasks, use proper tools like desoldering pumps or wicks to safely remove excess solder.
Humidity Control For Static
Beyond safe handling practices, humidity control plays a major role in protecting electronic components from static damage. You'll need to maintain relative humidity (RH) between 40% and 60% to create a favorable environment for electronics repair. When humidity drops below 30%, you're facing increased risks of electrostatic discharge that can destroy sensitive components.
Humidity Level | Effects | Required Action |
---|---|---|
Below 30% RH | High ESD risk, brittle materials | Use humidifier |
40-60% RH | Ideal conditions, reduced static | Monitor levels |
Above 60% RH | Corrosion risk, condensation | Use dehumidifier |
You'll want to implement proper air circulation to prevent moisture buildup and maintain consistent humidity throughout your workspace. Install humidity monitoring systems and check them regularly to maintain ideal conditions. If you're in a naturally dry environment, you'll need a humidifier to increase moisture levels. Conversely, use dehumidifiers in high-moisture areas to prevent corrosion and condensation issues. Remember that maintaining proper humidity isn't just about static control – it also protects your components from moisture damage and maintains consistent product quality in your repair work.
Professional Grounding Equipment Testing
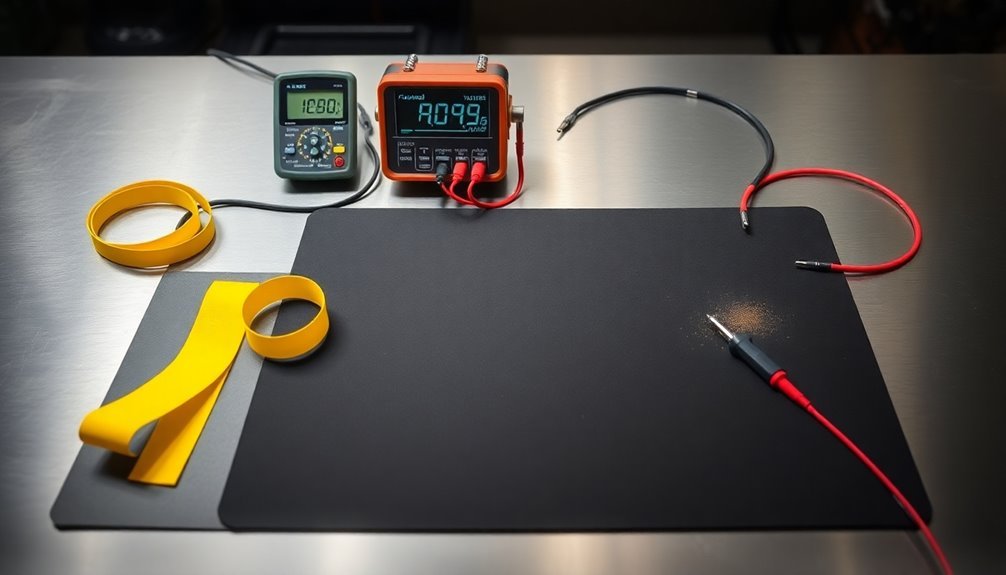
Three critical aspects define professional grounding equipment testing: standards compliance, reliability verification, and proper calibration protocols.
When you're working with electronic repairs, you'll need equipment that meets UL-listed requirements and adheres to strict safety regulations to protect against electrical hazards.
You'll want to confirm your grounding clusters and assemblies undergo thorough testing using factory-approved standards. Your equipment should be precision-engineered with industrial-strength components, tested under the most demanding conditions to guarantee peak conductivity and protection.
In-shop testing provides quick turnaround while maintaining accuracy in validation.
To maintain professional standards, you'll need to implement regular calibration and maintenance schedules for your grounding equipment. Professional-grade solutions require specific testing tools and protocols to verify their performance.
When you're setting up your grounding system, seek expert advice to confirm proper implementation. Remember that high-quality grounding clusters are designed for various applications, so you'll need to choose equipment that matches your specific needs.
Multiple Grounding Points System
Building on professional testing practices, understanding multiple grounding points systems represents the next step in electronics repair safety. While multi-point grounding can be beneficial in high-frequency environments, you'll need to carefully consider the risks and requirements before implementing this approach.
When you're working with multiple grounding points, you must verify proper installation to avoid creating parallel paths for current, which can lead to overheating and fire hazards. You'll find that connecting neutral to ground at more than one point can cause dangerous current division in signal ground wires. That's why many experts recommend single-point grounding as a safer alternative for most electronics repair situations.
If you decide to implement a multi-point system, you'll need to focus on proper conductor sizing and cross bonding. You must comply with local electrical codes and verify your ground grid meets safety requirements.
While multi-point grounding can maintain better reference ground potential across various frequencies, you'll face higher installation and maintenance costs. For electronics repair work, you'll want to carefully evaluate whether the benefits of multi-point grounding outweigh the potential risks and complexity of implementation.
Frequently Asked Questions
Can Extreme Cold Temperatures Affect the Effectiveness of ESD Protection Methods?
Yes, extreme cold can affect your ESD protection's effectiveness by altering material conductivity and increasing component leakage current. You'll notice reduced static dissipation capabilities and potentially compromised protection in very cold environments.
How Often Should Grounding Equipment Be Replaced Versus Just Inspected?
You should inspect grounding equipment semi-annually and replace it if you find damage, corrosion, or high resistance readings. Follow your manufacturer's guidelines, but don't wait longer than 5 years for full replacement.
Does Radiofrequency Interference Impact the Reliability of Grounding Systems?
Yes, radiofrequency interference can seriously impact your grounding system's reliability. You'll find it induces unwanted currents, increases ground impedance, and creates electromagnetic compatibility issues if you don't implement proper RFI mitigation measures.
What Emergency Backup Grounding Methods Work During Power Outages?
You'll need backup grounding systems like portable MPGUs with internal batteries, ground rods, and mobile grounding units. They'll maintain protection during outages while ensuring your equipment stays safely grounded for repairs.
Can Magnetic Fields From Nearby Equipment Compromise ESD Protection Measures?
Yes, magnetic fields can compromise your ESD protection. They'll induce unwanted currents in conductive paths and create ground loops. You'll need proper shielding, star grounding configurations, and strategic placement to protect your equipment.
In Summary
Following proper grounding methods isn't optional when working with electronics – it's vital for both your safety and protecting valuable components. You'll find that combining multiple approaches, from wearing ESD straps to maintaining proper humidity levels, creates the most effective protection system. Keep testing your grounding equipment regularly and never skip these critical safety steps during repairs or maintenance work.
Leave a Reply