To protect circuit boards with foam packaging, you'll need specialized foam materials like polyethylene, polyurethane, or conductive foam designed for electronics. Choose anti-static foam with proper ESD protection – conductive foam offers full shielding while static dissipative foam provides controlled discharge. Make sure to measure your circuit board's dimensions carefully, including any protruding components, and create a snug-fitting custom insert that cradles the board securely. Cut the foam using appropriate methods like CNC routing or laser cutting for precision. Store boards in controlled temperatures between 15-30°C with 40-65% humidity. Understanding the specific needs of your circuit boards will help you implement the most effective protection strategy.
Understanding Foam Packaging Materials
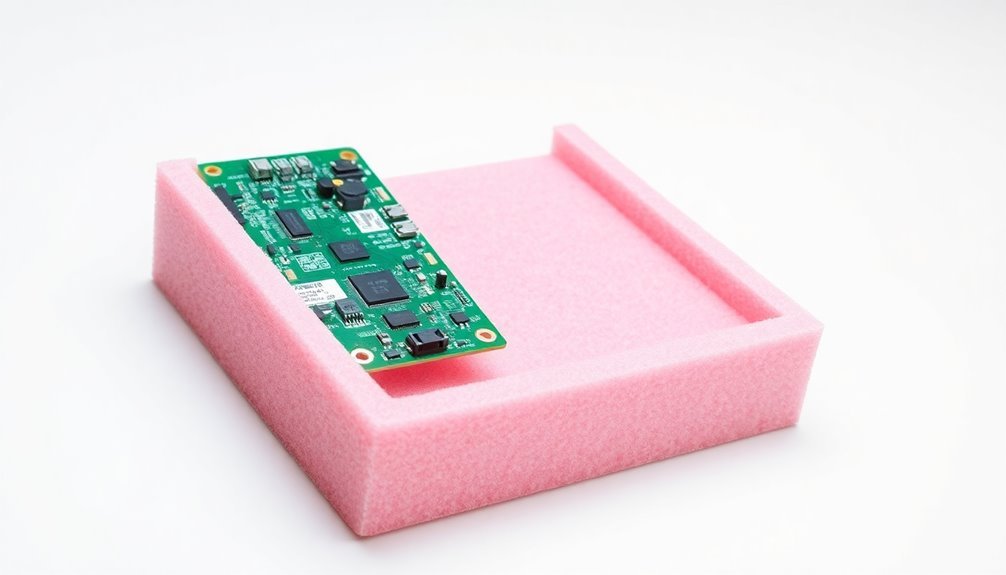
Manufacturers widely rely on foam packaging materials to protect sensitive circuit boards during shipping and handling. When selecting foam materials, you'll need to understand the key types available and their specific properties to guarantee maximum protection for your electronic components.
Polyethylene foam offers excellent shock absorption and durability, making it ideal for heavy electronics or high-impact scenarios. Special foam inserts can be designed with robust protective qualities to guard against both mechanical and electrical risks.
If you're packaging delicate components, polyurethane foam's open-cell structure provides gentle cushioning that's perfect for sensitive circuit boards.
For components that require static protection, you'll want to use anti-static foam, which comes in both polyethylene and polyurethane variants.
Expanded Polyethylene (EPE) foam provides a lightweight, non-abrasive solution that's particularly effective for consumer electronics, offering both shock absorption and moisture resistance.
If you need superior impact absorption and chemical resistance, consider Zotefoams, which also feature static dissipative properties.
Each foam type can be customized to fit your specific requirements, allowing you to create tailored packaging solutions that guarantee your circuit boards remain secure and protected throughout the shipping process.
Selecting The Right Foam Type
Now that you understand the range of foam packaging materials available, selecting the right foam type for your circuit board protection requires careful consideration of static protection levels.
If you're handling highly sensitive electronics that need thorough static protection, choose conductive foam, which creates a Faraday cage around your components and offers a low resistance range of 10^3-10^5.
For components that need protection against static build-up but don't require full shielding, opt for pink anti-static foam. It's suitable for most circuit boards and computer chips, with a resistance range of 10^6-10^9.
When you need a middle-ground solution, static dissipative foam provides controlled discharge with resistance values between 10^8-10^11. Expert consultation can help determine the most appropriate foam type for your specific requirements.
Your selection should factor in shipping conditions and environmental hazards. Consider the distance your circuit boards will travel and potential exposure to shock or vibration.
Don't forget to evaluate cost-efficiency – while conductive foam offers superior protection, it's more expensive and may not be necessary for all applications.
Remember to inspect your foam regularly if you're reusing it, ensuring it maintains its protective properties for reliable circuit board safety.
Custom Foam Insert Design
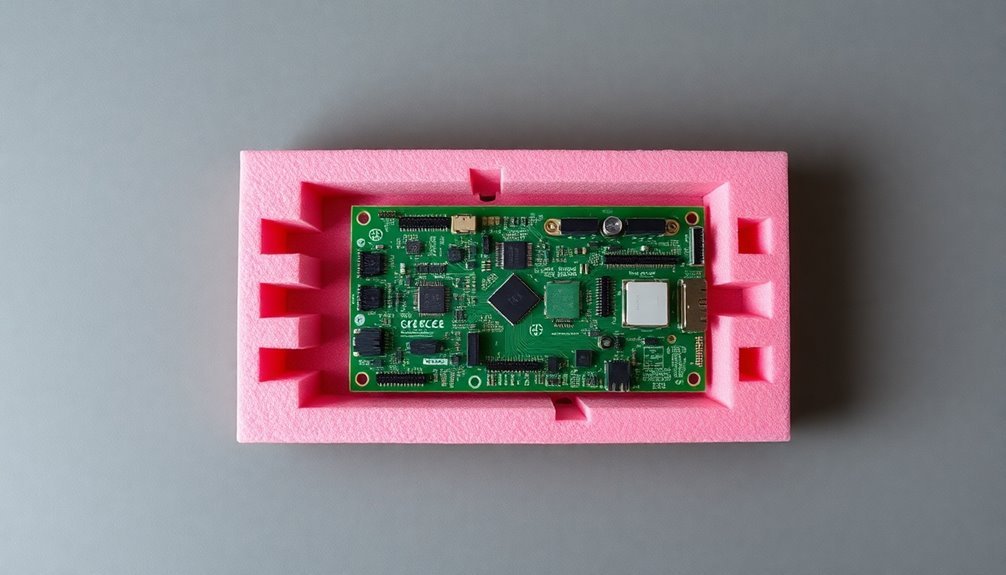
You'll need to start by taking detailed measurements of your circuit board's length, width, height, and any protruding components to guarantee a precise fit for your foam insert.
When selecting your foam material, consider whether you need antistatic properties for sensitive electronics and choose between options like PE, PU, or XLPE based on your protection requirements. State-of-the-art equipment ensures precise cutting for optimal circuit board protection.
Create your cut pattern by mapping out the board's exact outline and any necessary supports, leaving appropriate clearance for easy insertion and removal while maintaining snug protection.
Measuring Board Dimensions Precisely
Accurate measurement of circuit board dimensions forms the foundation of effective custom foam packaging design. You'll need to measure three key dimensions: length (top to bottom), width (left to right), and thickness (depth between dividing cells). It's essential to provide these measurements in the correct order to verify your custom foam insert fits perfectly.
When measuring your circuit boards, you'll want to account for any protrusions or extending components. Modern measurement solutions like automated optical inspection can help detect and measure these features with high precision. If your board has significant protrusions, you might need to reverse the length and width dimensions to achieve the best fit.
Using precise tools like calipers will give you authoritative measurements, which are far more reliable than traditional methods like imagers or projectors.
Your measurements will directly influence the design of your custom foam insert, including the selection of appropriate materials and the incorporation of necessary protection features. You'll need to think about the board's weight and fragility when determining foam density and thickness.
Don't forget to factor in buffer space between components and ESD protection requirements. By taking accurate measurements, you're verifying your circuit boards will be properly protected during transport and storage, preventing costly damage to sensitive components.
Selecting Foam Material Types
Selecting the right foam material type is critical for protecting circuit boards during transport and storage. You'll need to choose anti-static foam that meets EIA-541 standards to prevent damage from static charges, while ensuring the material is non-abrasive to protect delicate surfaces.
For circuit boards, polyurethane (PU) foam is your best choice as it's an open-cell material ideal for smaller, sensitive components. Pink anti-static foam with a surface resistance range of 10^4 to 10^9 ohms provides optimal static dissipation properties.
If you're packaging larger electronic items, think about cross-linked polyethylene (XLPE) for its structural rigidity. You can also use polyethylene (PE) foam for additional cushioning and vibration dampening.
When designing your foam packaging, you'll want to think about custom inserts that precisely fit your circuit board's dimensions. These can be cut from various foam materials and combined to provide the best protection.
Remember to assess your board's fragility and anticipated handling conditions when making your selection. If you're dealing with high-value electronics that have sensitive surface finishes, it's crucial to choose non-abrasive foam materials.
For the best results, work with a packaging specialist who can help you select the right combination of foam materials and design custom inserts for your specific needs.
Creating Precise Cut Patterns
When designing custom foam inserts for circuit boards, precise cut patterns serve as the foundation for reliable protection. You'll need to start by evaluating your circuit board's fragility and calculating the required cushioning to absorb shocks and vibrations effectively. Anti-static formulations are essential when selecting polyurethane or polyethylene foams for electronics packaging.
To create accurate cut patterns, you'll want to leverage CAD files for detailed designs that match your circuit board's exact dimensions. You can then choose from several cutting methods: die-cutting for precise shapes, laser cutting for intricate designs, or CNC machining for complex configurations. For smaller projects, manual cutting might suffice.
Before moving to full production, create prototypes and conduct thorough testing to validate your design.
You can use foam injection molding for large-scale production runs or CNC routing for more specialized requirements. If you need detailed markings or specific identifiers, consider incorporating laser engraving into your process.
Throughout production, maintain strict quality control measures and regularly check that your foam inserts meet protection requirements.
Don't forget to manage your supply chain effectively to guarantee consistent material availability and timely delivery of your finished protective packaging.
Static Protection Requirements
You'll find three primary ESD foam options for circuit board protection: non-crosslinked polyethylene, cross-linked polyethylene, and PUR-Polyurethane, each offering distinct static-dissipative properties.
Your foam packaging must meet standardized discharge testing requirements, including surface resistivity measurements and charge decay assessments that conform to industry specifications. Since device-level ESD damage can be particularly harmful to semiconductor components, proper foam protection is critical.
To guarantee complete ESD protection, you need multiple protective layers, including antistatic foam inserts, conductive outer packaging, and proper grounding mechanisms that work together to prevent static buildup.
ESD Foam Types Available
Because circuit boards require reliable protection against electrostatic discharge, manufacturers offer several specialized ESD foam varieties to meet different static protection requirements.
PE foam provides versatile ESD protection with adjustable surface resistance levels, while EVA foam offers single-layer thickness up to 70mm and excellent moldability. The higher density of EVA foam at 85kg/m³ ensures permanent anti-static properties.
EPE foam features an eco-friendly closed-cell structure with surface resistance of 10^8-10^11 ohms, and PU foam provides an open-cell structure that you can customize to your size requirements.
You'll find these foams available in different colors that indicate their static protection levels. Black conductive foam offers resistance of 10^3-10^5 ohms, while pink static dissipative foam provides 10^8-10^11 ohms. Black anti-static foam falls in the middle range at 10^6-10^9 ohms.
When selecting your foam type, you'll need to think about the protection duration, as some varieties like EPE and PU foam provide effective static protection for about six months. Each foam type can be precisely cut to match your circuit board's dimensions, providing thorough protection.
You'll want to choose your foam based on your specific component requirements and verify it complies with ANSI/ESD S20 standards for the best protection.
Discharge Testing Standards
The rigorous testing of ESD protection goes far beyond selecting the right foam type. You'll need to understand both device-level and system-level testing standards to guarantee your circuit boards are adequately protected.
At the device level, you're required to perform six total discharges per pin – three positive and three negative pulses – while monitoring the ground connection to verify protection effectiveness.
For system-level testing, you must follow the IEC 61000-4-2 standard, which specifies contact discharge tests at 2 kV, 4 kV, 6 kV, and 8 kV, with air discharge tests reaching up to 15 kV. If you're working in specific industries, you'll need to meet additional standards like EN 60601-1-2 for medical devices or ISO 10605 for automotive products.
You'll want to conduct all testing in an ESD Protected Area (EPA) with proper controls in place. This means using grounding wrist straps, dissipative gloves, and anti-static mats.
Don't forget to regularly test your grounding accessories and verify your working environment with a ground/polarity tester. Remember, ESD control principles should be implemented throughout your entire facility wherever sensitive electronic components are handled.
Protective Layer Requirements
Proper static protection requires multiple layers of defense to shield circuit boards from electrostatic discharge. When designing your protective packaging, you'll need to guarantee that static charges have a clear path to ground while maintaining complete coverage around sensitive components.
The most effective approach combines proper grounding techniques with specialized foam materials that prevent static buildup.
To implement effective protective layers, you should:
- Design your packaging with low-impedance ground planes and incorporate vias to efficiently drain static charges, keeping protection circuits as close to IC pins as possible.
- Select conductive foam materials with surface resistivity less than 10^12 Ohms/square to create a Faraday cage effect around your boards.
- Use custom foam inserts and dividers that conform to your PCB's shape while maintaining consistent static protection under varying environmental conditions.
The combination of proper grounding and appropriate foam materials creates a thorough protective system. You'll want to guarantee your foam packaging provides both physical cushioning and static dissipation.
For maximum protection, consider using all-in-one ESD containers with custom-fitted foam inserts that offer complete static shielding without requiring additional protective bags.
Proper PCB Handling Techniques
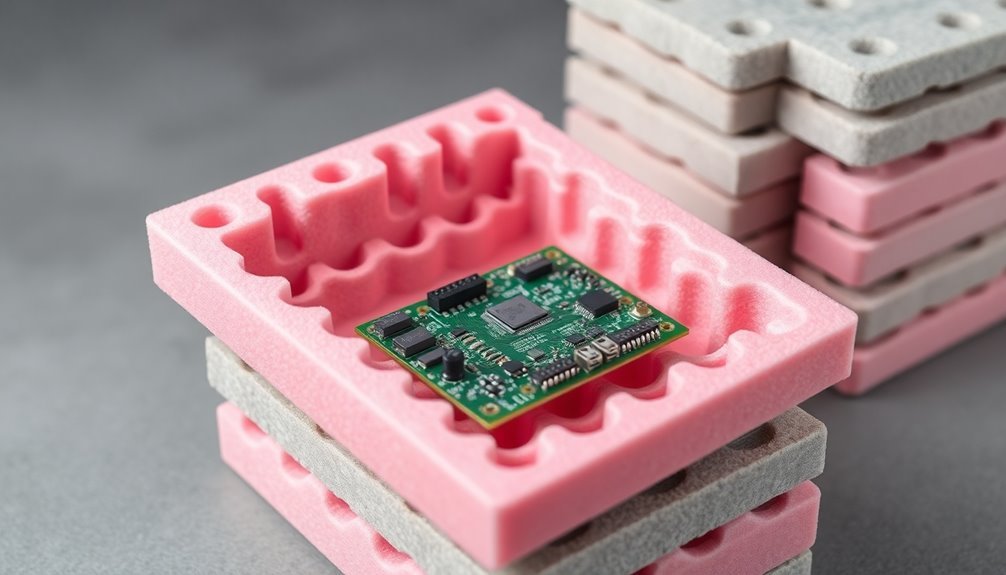
Careful handling of printed circuit boards requires strict adherence to established safety protocols and techniques. You'll need to minimize direct contact by using transportation racks and trays whenever possible, and always wear protective gear including gloves and safety glasses to prevent contamination and personal injury.
When handling PCBs, use both hands to prevent bending or flexing, and avoid unnecessary movements that could cause damage.
You'll want to connect yourself to an ESD-safe workstation using a grounded wrist strap before touching any boards. Keep your workspace clean and organized, using only ESD-safe tools and equipment that are free from contamination.
Don't forget to inspect your work carefully using magnifying glasses or loupes.
Store your PCBs in dry, cool environments using high-quality packaging materials like anti-static bags and foam inserts. If you're working with boards containing hazardous materials like lead, take extra precautions and follow proper safety guidelines.
Remember to use shock-absorbing materials and rigid mounting systems during transportation to protect against mechanical stress and vibration.
When storing multiple boards, use dividers or compartments to prevent movement and contact between components.
Storage and Transportation Guidelines
During PCB storage and transportation, maintaining strict environmental controls becomes critical for preserving board quality.
You'll need to store PCBs at temperatures between 15°C and 30°C, while keeping relative humidity between 40% and 65%. Use desiccants or humidity control equipment to prevent moisture damage, and consider vacuum-sealing boards with desiccants to extend their shelf life up to a year for gold-plated FPCs.
When preparing PCBs for transport, follow these essential steps:
- Place boards in antistatic bags and wrap them with bubble wrap or foam inserts, ensuring protection against both physical damage and electrostatic discharge.
- Seal wrapped PCBs in moisture barrier bags, then place them in sturdy boxes with packing materials to prevent movement.
- Label packages clearly with handling instructions, supplier information, and relevant identification numbers including CAGE Code, purchase order, and date code.
For long-term storage, you'll need to monitor environmental conditions regularly. If boards have been out of dry storage for more than five days, bake them according to IPC-1601A standards before packaging. Choose packaging materials that adapt to your PCBs' shape, such as conductive foam inserts, for ideal protection during both storage and shipping.
Foam Packaging Best Practices
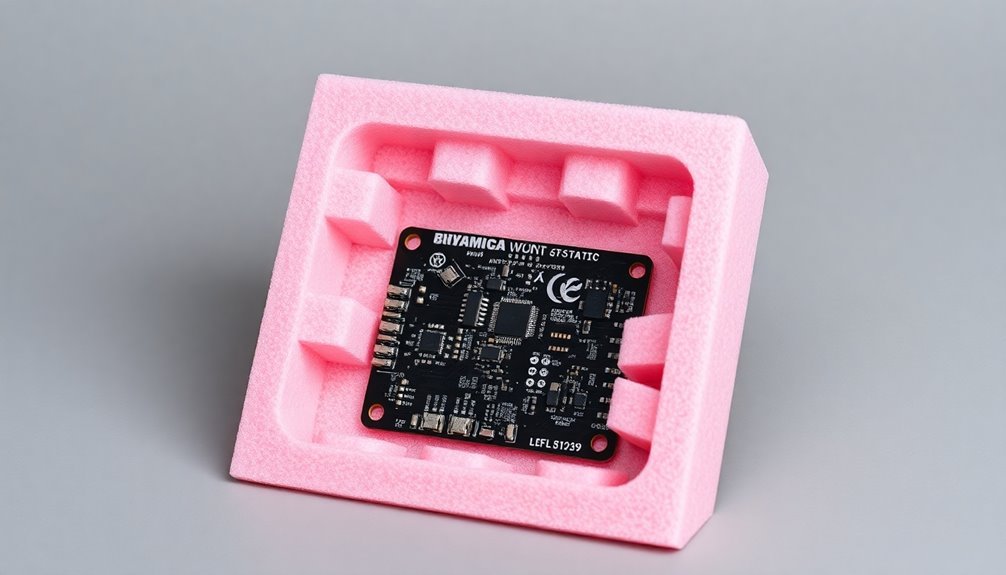
Foam packaging serves as a critical defense system for protecting circuit boards against physical damage and electrostatic discharge. You'll need to select the right type of foam based on your specific protection requirements: anti-static foam for dissipating charges, conductive foam for electromagnetic shielding, or ESD foam that meets EIA-541 standards.
To maximize protection, you should incorporate foam inserts and dividers that conform to your PCB's shape. Custom-designed die-cut foam inserts offer the most precise fit, while foam tote partitions can be used in either antistatic or electrically conductive versions.
When selecting materials, opt for non-crosslinked polyethylene or PUR-Polyurethane foams for customized solutions.
Combine your foam packaging with complementary protective elements. Use ESD plastic containers with foam interiors for complete protection against both mechanical risks and electrostatic discharge.
You'll find various foam options available, including pink anti-static, black conductive, and dissipative varieties. For additional security, pair your foam packaging with static shielding bags and corrugated polypropylene sheets, especially for long-term shipping and storage needs.
Frequently Asked Questions
How Long Can PCBS Safely Remain Stored in Foam Packaging?
You'll need to monitor your PCB's coating type: gold-plated ones last 6 months (up to 1 year with vacuum sealing), while those with silver, tin, or OSP coatings should be stored for just 3 months.
Can Foam Packaging Be Recycled After Its End-Of-Life Use?
Yes, you can recycle foam packaging, but only about 6-12% actually gets recycled. You'll need to remove labels and contaminants first, then take it to local recycling centers that accept EPS foam materials.
What Cleaning Solutions Are Safe to Use on Reusable Foam Packaging?
You can safely clean reusable foam packaging with mild detergents, diluted isopropyl alcohol, or antistatic cleaners. Always test on a small area first and avoid harsh chemicals that'll damage the foam material.
How Many Times Can Foam Packaging Typically Be Reused Before Replacement?
You'll typically get 5-10 reuses from high-quality foam packaging with proper handling. Though it varies based on material type, usage conditions, and storage practices, durable foam can last even longer with careful maintenance.
Does Extreme Temperature Affect the Protective Properties of Foam Packaging?
Yes, extreme temperatures will substantially affect your foam packaging's protective properties. You'll notice reduced cushioning ability, compromised structural integrity, and possible material degradation. It's best to avoid exposing foam to temperature extremes.
In Summary
You'll find proper foam packaging is essential for protecting your circuit boards throughout their lifecycle. Remember to choose anti-static foam materials, design custom inserts that fit your PCBs perfectly, and follow proper handling protocols. Don't skimp on quality packaging – it's your best insurance against costly damage. By implementing these foam packaging best practices, you're ensuring your circuit boards arrive safely and remain protected in storage.
Leave a Reply