To protect circuit boards during storage and shipping, you'll need multiple layers of defense. Start with anti-static bags or metallized shielding bags to prevent ESD damage, then add moisture barrier protection with desiccant packets. Use high-quality foam inserts with custom cutouts to immobilize your PCBs and prevent physical damage. Wrap boards in anti-static bubble wrap or specialized foam sheets for impact resistance. Don't forget proper labeling and humidity control in your storage area. Maintain temperatures between 50-75°F during transport. The key to complete PCB protection lies in understanding how these methods work together.
Static Protection Fundamentals
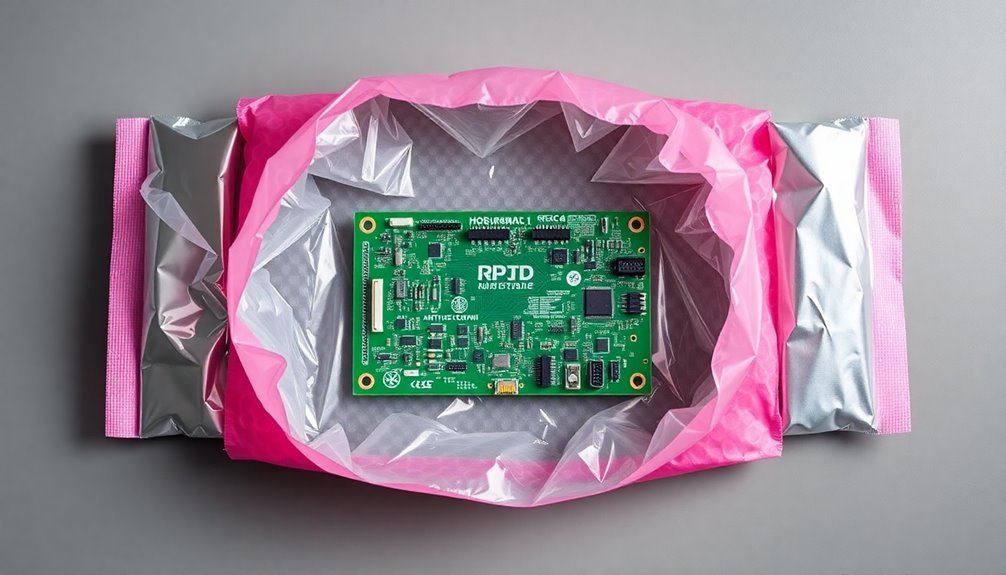
Every electronic circuit board requires robust static protection to prevent damage from electrostatic discharge (ESD). You'll need to implement proper grounding schemes by using a chassis ground separated from digital and analog grounds, ensuring a low impedance path for ESD protection components. ESD events can generate high current pulses that quickly dissipate heat into PCB components.
If you can't use chassis earth ground, utilize tightly coupled multiple layer ground planes instead.
When selecting and placing components, you'll want to position TVS diodes close to ESD sources and steer current away from protected ICs. Make sure you're creating direct paths from ESD sources to TVS without unnecessary vias or stubs, and connect TVS ground pins to same-layer ground planes. Use stitching vias for multi-layer ground planes to minimize inductance.
You must also incorporate specific circuit design elements, including ESD protection circuits and low-pass RL circuits with inductors and TVS diodes.
For storage and handling, you'll need to use antistatic bags and foam inserts while maintaining proper humidity control. Don't forget to store PCBs in electrostatically shielded containers and regularly inspect grounding connections to prevent static buildup.
Choosing Anti-Static Packaging Materials
When you're selecting anti-static packaging for circuit boards, you'll need to understand four key material types: anti-static bags, conductive packaging, shielding materials, and dissipative solutions.
You'll want to match the shielding layer to your specific needs – using metallized barriers for maximum protection or dissipative materials for basic handling. Smaller electronic components require extra attention since they are more vulnerable to ESD.
Anti-Static Bags
Anti-static bags are designed to prevent the creation of static charges when sensitive devices are in contact with the material. These bags are typically pink or light blue to signify that the material is non-static generating. However, they do not protect the contents from external static charges. For instance, if an operator with a static charge picks up a circuit board in an anti-static bag, the bag does not protect the contents from that external charge.
Conductive Packaging
Conductive packaging conducts any potential static charges away from sensitive parts, keeping any flow of electricity under control. It does not accumulate static charges. This type of packaging is often made from materials like conductive crosslink black polyethylene foam or conductive extruded high-impact polypropylene plastic.
Shielding Materials
Shielding packaging provides a barrier that reduces electrostatic discharge. This type of packaging comes in bags and boxes that fully protect the contents from static damage by creating a Faraday cage around the contents. Shielded bags are often metallized with a thin coating of polyester and aluminum to ensure that a static charge can be drained to any ground. Shielded boxes are typically black and made from conductive materials like conductive corrugated or conductive fluted plastic.
Dissipative Solutions
Dissipative packaging slows down the flow of any static charges, rather than directing it like conductive packaging. This type of packaging is useful for basic handling where maximum protection is not required but some level of static control is necessary.
Testing your chosen packaging's ESD protection level with a surface resistivity meter will confirm you've picked the right material for your circuit board's sensitivity requirements.
Types of Static-Control Materials
The selection of proper static-control materials plays a crucial role in protecting circuit boards during storage and transit.
There are four main types of static-control materials, each serving distinct protective functions for your sensitive electronics. As few as 10 volts can damage sensitive printed circuit boards during handling.
Anti-static packaging prevents electrostatic charges from forming when products rub against surfaces, making it ideal for general protection of microchips and motherboards.
Conductive packaging takes protection a step further by actively conducting potential static charges away from sensitive components, offering superior durability for repeated use.
Shielding packaging creates a protective barrier against electrostatic fields,
while dissipative packaging slows down static charge flow for balanced protection.
When selecting static-control materials, consider these key factors:
- Anti-static materials work best for basic handling and short-term storage
- Conductive options excel in reusable shipping scenarios
- Shielding materials provide the highest level of protection through multi-layer barriers
- Dissipative packaging offers cost-effective protection for moderately sensitive components
- Metal-in and metal-out bags provide varying levels of protection based on your specific needs
Each type complements specific handling requirements, so you'll want to match your selection to your circuit board's sensitivity level and shipping conditions.
Proper Shielding Layer Selection
Building on your understanding of static-control materials, selecting the right shielding layer demands careful consideration of your circuit board's specific protection needs. You'll need to choose between static-shielding bags and antistatic bags based on your protection requirements. Static-shielding bags with metal-in or metal-out construction provide Faraday Cage protection, while antistatic bags offer basic ESD protection for less sensitive components.
For critical electronics, you'll want to use metal-out bags due to their lower resistance properties. When packaging your PCBs, make certain you're using proper ESD procedures, including grounding operators and maintaining appropriate handling protocols. Following MIL-B-81705C standards ensures optimal static decay and surface resistivity for your packaging solutions.
Package Type | Protection Level | Construction | Best Use | Thickness |
---|---|---|---|---|
Metal-In Bags | High | Multi-layer metallic | General electronics | 2-8 mil |
Metal-Out Bags | Highest | Metal exterior | Critical components | 2-8 mil |
Antistatic Bags | Basic | Polyethylene | Low-risk items | 2-8 mil |
Black Conductive Tubing | Moderate | Conductive polymer | Bulk storage | Variable |
Anti-static Foam | Supplementary | ESD-safe foam | Cushioning | Variable |
Consider vacuum sealing for additional protection against moisture and contamination. You can enhance cushioning through controlled vacuum speeds or by adding ESD-safe foam materials when needed.
Testing Material ESD Protection
Selecting appropriate anti-static packaging requires systematic testing to verify ESD protection levels. You'll need to evaluate materials that can protect circuit boards from static charges up to 20 kV, using an IEC ESD simulator to confirm their effectiveness.
When testing packaging materials, consider both their immediate and long-term protection capabilities, keeping in mind that anti-static properties typically degrade after one year. The most effective approach involves implementing multiple packaging layers for maximum protection during transport.
Choose your materials based on these proven protection layers:
- Anti-static transparent materials for basic protection against static buildup
- Static-shielding metallic or semi-transparent materials to block electrostatic fields
- Black conductive tubing for single-layer static charge protection
- Treated plastic films with static-dissipative properties
- Vacuum-sealed antistatic materials for thorough ESD protection
You'll want to test your packaging materials considering the Charge Device Model rating of your components. Remember to verify that your chosen materials prevent tribocharging and minimize the use of insulators.
For semiconductor devices, it's essential to test protection levels using standard packing methods like trays, tape and reel, or magazines. Consider both intimate and proximity packaging layers when conducting your tests to guarantee complete protection during handling and shipping.
Moisture Barrier Solutions

Effective moisture barrier solutions play a vital role in protecting circuit boards throughout their lifecycle. You'll find several proven methods to safeguard your PCBs from moisture-related damage, each offering unique advantages for different scenarios.
Moisture-adsorbing solutions act as physical barriers that you can customize to your specific needs. These solutions prevent condensation while reducing the risk of desiccant dust contamination, making them ideal for high-humidity environments where traditional desiccant bags aren't effective.
When you need thorough protection, conformal coatings create a protective film using materials like acrylic, polyurethane, or silicone. While you'll need to remove and reapply these coatings during rework, they provide reliable environmental protection when properly cured. Including moisture indicator cards helps monitor exposure levels during storage and shipping.
For shipping and storage, you can rely on moisture barrier packaging with puncture-resistant materials and desiccant packets. You'll find options including vacuum sealing for moisture-sensitive applications and ESD-protective variants for complete protection.
If moisture has already affected your PCBs, you can implement various removal techniques. These include controlled baking, low-level heating elements, dry nitrogen gas displacement, or vacuum drying for severe cases.
Remember to maintain controlled humidity and temperature in your production and storage areas.
Impact Prevention Techniques
Protecting circuit boards from physical damage calls for thorough impact prevention strategies. You'll need to implement multiple layers of protection to shield your PCBs from shocks, vibrations, and physical contact that could compromise their integrity. Regular inspection helps identify potential temperature fluctuation damage early on.
Start by using high-quality foam inserts and specialized packaging materials designed specifically for electronic components.
Your impact prevention strategy should include these essential elements:
- Use static shielding bags combined with anti-static bubble wrap to provide both impact and ESD protection
- Install rigid mounting systems and secure transportation carriers to minimize movement during transit
- Place desiccant packets inside air-tight packaging to control moisture while providing cushioning
- Employ compartmentalized trays and dividers to prevent boards from colliding during storage
- Handle boards only by their edges and utilize automated processes whenever possible
Remember to maintain clean workstations and wear appropriate protective clothing when handling PCBs.
Store your circuit boards in sealed containers with proper shock-absorbing materials, and confirm your storage shelving can adequately support the weight without risk of collapse.
PCB Immobilization Methods

The provided facts about environmental PCB remediation don't align with writing about protective packaging for circuit boards. However, if you're looking for a paragraph about immobilizing printed circuit boards (PCBs) during transit using custom foam inserts,
You'll find custom foam inserts are essential for properly immobilizing printed circuit boards during shipping and handling. Since circuit boards should be protected from potential taste or odor contamination, specialized foam materials are selected that remain inert and neutral. The foam can be precisely cut to match your board's exact dimensions, creating snug cavities that prevent lateral and vertical movement. These custom solutions often feature anti-static properties and strategic compression points to protect sensitive components while maintaining the board's position throughout transit.
Custom Foam Insert Solutions
Custom foam insert solutions represent a sophisticated approach to PCB immobilization, combining advanced materials with precision manufacturing techniques. You'll find various foam types specifically designed for electronics protection, including EPE, EVA, PE, PU, and XLPE foams, each offering unique protective properties for your circuit boards.
When you're selecting a custom foam insert solution, consider these essential benefits that protect your PCBs:
- Anti-static properties that prevent electrical damage during handling and transport
- Superior shock absorption capabilities through specialized foam structures
- Precise fit through CNC cutting and die-cutting manufacturing processes
- Complete product immobilization that prevents shifting and movement
- Long-lasting durability for repeated use and consistent protection
You can customize these foam inserts using various manufacturing methods to match your specific PCB dimensions and requirements. Whether you're using Pelican™ cases or other specialized containers, you'll achieve top-notch protection through precise engineering.
The combination of advanced materials and manufacturing techniques guarantees your circuit boards remain secure during shipping, storage, and handling, while maintaining their integrity through static protection and impact absorption.
Securing PCB During Transit
Successful PCB transit requires a thorough approach to immobilization that combines multiple protective elements.
You'll need to start with proper ESD protection by placing your PCBs in anti-static bags or pink poly wrapping to prevent static discharge damage. For sensitive boards, consider using vacuum-sealed packaging with moisture barrier protection and desiccant packs.
To prevent mechanical damage during shipping, you'll want to secure your PCBs in rigid boxes with custom-fitted foam inserts. Make sure you're using shock-absorbing materials at critical points and eliminating any void space that could allow movement. Anti-static foam inserts work best as they provide both cushioning and ESD protection.
Don't forget to clearly label your packages with handling instructions and "fragile" warnings. You should also consider environmental factors by including thermal insulation if your boards will face extreme temperatures.
When selecting a shipping method, choose carriers that offer climate-controlled transport options and tracking capabilities. Remember to seal your boxes securely and reinforce them if needed, especially for heavier PCB assemblies or long-distance shipping routes.
Handling Sensitive Electronic Components
Static electricity poses a significant threat to electronic components, requiring strict handling protocols to prevent damage. You'll need to ground yourself properly using wrist straps and mats before handling any ESD-sensitive devices.
Always maintain relative humidity levels between 20% and 80% non-condensing to minimize static buildup in your work area.
When working with circuit boards, you must use proper protective measures and follow these essential handling guidelines:
- Don't remove boards from their protective packaging unless you're in a static-controlled location with properly grounded equipment.
- Use the provided handles when removing or replacing circuit boards, and avoid unnecessary movement or contact with clothing.
- Never stack circuit boards directly on top of each other – use foam inserts or antistatic mats as separators.
- Keep boards in static shielding bags or clamshells when transporting them between work locations.
- Work only on dissipative surfaces with an impedance of at least 10,000 ohms per square.
If you notice torn or damaged static-shielding bags, replace them immediately as they can attract static charges. Remember to maintain proper environmental controls in your storage facilities using dehumidifiers and guarantee all handling equipment remains properly grounded.
Essential Cushioning Materials
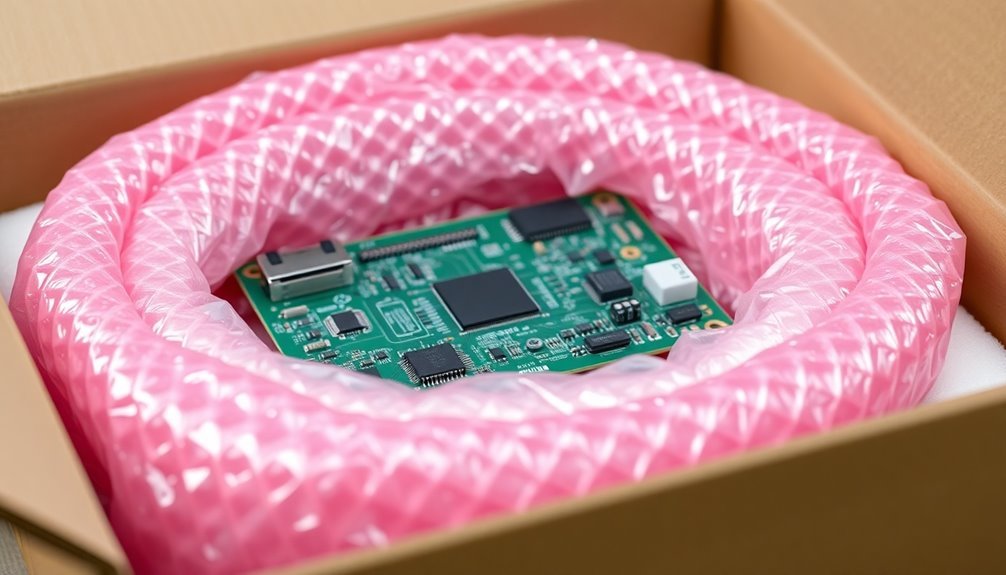
Beyond static protection, your circuit boards need reliable physical safeguards during storage and transport. When choosing cushioning materials, you'll find bubble wrap is a top performer, especially with its varying bubble sizes for different PCB types. For delicate boards, opt for smaller bubbles, and consider metallized versions that offer static shielding while protecting the top and bottom of your containers.
Foam sheets provide another excellent option, particularly closed-cell anti-static varieties that effectively absorb shock. You can create custom cutouts to match specific PCB shapes, ensuring your boards remain immobile during transit.
Air pillows offer similar benefits, molding around your PCBs to prevent movement while providing consistent protection against impacts and vibrations.
If you're looking for an eco-friendly alternative, paper cushioning materials can work well, especially for less sensitive boards. You'll find accordion-style sheets or crumpled paper particularly useful as supplementary protection.
While paper doesn't offer static protection like specialized materials, you can combine it with anti-static options to create a thorough protective solution that's both effective and environmentally conscious.
Shipping Container Requirements
Selecting the right containers for your circuit boards calls for careful attention to sizing and material specifications. You'll need to choose from various container dimensions, such as 797 x 598 x 240 mm or 1195 x 397 x 170 mm, to properly accommodate your PCBs.
For sensitive components, opt for ESD-injected plastic boxes with modular internal separators that can secure multiple boards.
Consider these essential shipping container requirements:
- Use containers that can accommodate board thickness up to 7 mm while providing adequate protection
- Select ESD-protected boxes with special foam inserts for sensitive electronic components
- Choose moisture barrier packaging with desiccant packets for ocean freight or humid environments
- Implement modular systems that allow efficient storage and shipping of multiple boards
- Install proper labeling with ESD warning stickers for clear handling instructions
When selecting your shipping containers, you'll want to verify manufacturer packaging standards and review specific requirements for your PCBs.
Don't forget to factor in whether you'll need vacuum-sealed packaging for high-level moisture protection or custom solutions for boards with unique specifications like temperature sensitivity.
Safe Transport Guidelines
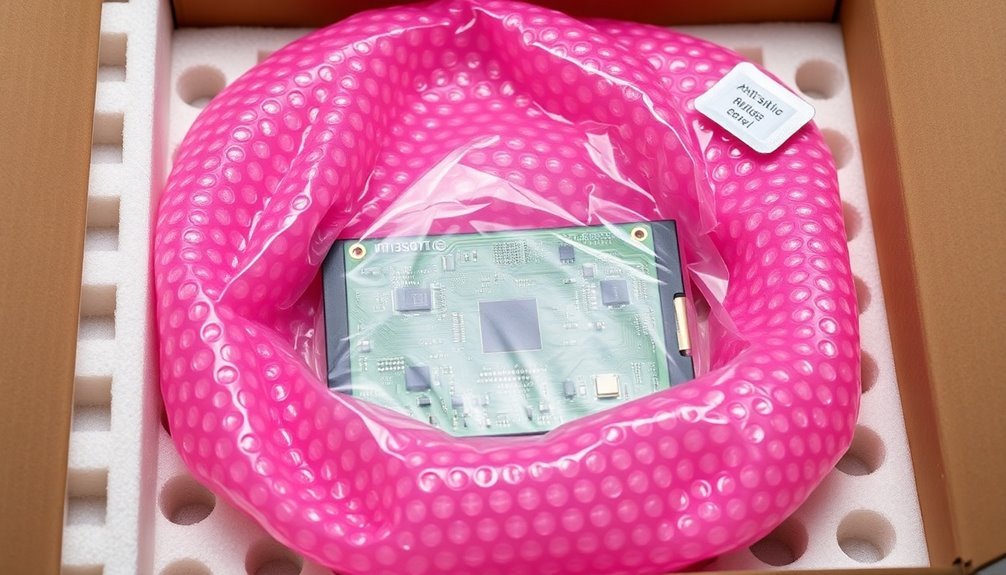
Professional transport of circuit boards demands a thorough set of safety protocols to prevent damage during handling and shipping. You'll need to guarantee all transport tools are in good working condition, with special attention to wheels and frames. Always inspect your equipment regularly and remove damaged tools from service immediately.
When handling PCBs, you'll want to avoid rough movements and direct stacking. Maintain a balanced speed during transport to prevent unnecessary turbulence. Don't forget to implement moisture and static protection measures, including moisture barrier bags and desiccant packets for sensitive components.
Transport Phase | Key Actions | Safety Measures |
---|---|---|
Pre-Transport | Inspect tools | Check wheels/frames |
Loading | Handle gently | Use anti-static materials |
In-Transit | Maintain stability | Prevent stacking |
Storage | Control environment | Add moisture protection |
Unloading | Move carefully | Follow safety protocols |
You'll need to protect boards from environmental factors like dust, direct sunlight, and temperature extremes. Consider using anti-static bubble wrap for cushioning and vacuum sealing for highly sensitive components. It's vital to maintain a clean, stable storage environment and implement proper fall prevention measures throughout the transport process.
Storage Best Practices
You'll need to maintain strict control over humidity and temperature in your PCB storage environment using dehumidification systems and consistent climate settings.
Your storage system should incorporate ESD-safe containers and modular bins that protect components while keeping them organized and easily accessible.
For long-term protection, you should implement moisture barrier bags with desiccant packets and proper handling protocols that minimize direct contact with circuit boards.
Controlling Humidity and Temperature
Maintaining proper humidity and temperature control stands as a critical requirement for PCB storage. You'll need to keep relative humidity between 20% and 60%, with 50% being ideal for bare PCBs.
To achieve this, use desiccants like silica gel and consider investing in specialized dry cabinets that can maintain ultra-low humidity levels below 3% RH.
Temperature stability plays an equally important role in protecting your PCBs. While storing them at room temperature, you'll want to implement monitoring systems that alert you to any concerning changes in environmental conditions.
Don't forget to include moisture indicator cards in your storage containers.
Here's what you'll need for effective humidity and temperature control:
- Desiccant packets or containers filled with silica gel
- Moisture-resistant packaging materials that comply with industry standards
- Dry cabinets or storage units with automatic humidity control
- Environmental monitoring systems with alarm capabilities
- Dehumidifiers for larger storage areas
Remember to follow standards like JEDEC-STD-033 for moisture-sensitive components.
If your PCBs have been exposed to excessive moisture, you can use high-temperature baking to remove it, but prevention through proper storage is always the better approach.
Organized Storage Systems
While protecting PCBs from environmental damage is crucial, implementing an organized storage system forms the backbone of proper circuit board protection. You'll need to set up dedicated storage racks that keep your PCBs properly organized and easily accessible while preventing any potential damage from improper stacking or handling.
Make sure you're using clear, detailed labels on all stored PCBs, including essential information like contents and storage dates. This labeling system helps you maintain a strict first-in, first-out (FIFO) policy, ensuring you'll use older boards before newer ones and prevent any PCBs from exceeding their maximum storage times.
Don't forget to maintain ESD compliance throughout your storage area. You'll need to regularly inspect and clean your storage spaces to prevent contamination that could compromise board integrity.
When handling boards, always use clean gloves and change them frequently to avoid transferring contaminants. Consider using protective bags when moving PCBs between stations, and rely on racks and tray carts to minimize direct handling.
Long-term Protection Solutions
For long-term PCB protection, implementing thorough storage solutions substantially reduces the risk of damage and deterioration. You'll need to focus on both environmental controls and specialized protective measures to safeguard your circuit boards in top condition during extended storage periods.
Store your PCBs in temperature-controlled rooms with low humidity, and always use moisture barrier bags (MBBs) to prevent moisture exposure. When handling boards, wear clean gloves and use antistatic equipment to protect against electrostatic discharge.
For enhanced protection, consider applying conformal coatings or encapsulation methods that shield against environmental factors.
Here's what you'll need for extensive long-term protection:
- Moisture barrier bags combined with dry storage cabinets to maintain ideal humidity levels
- Antistatic packaging materials, including bags, bubble wrap, and foam inserts
- Conformal coatings or varnish applications to guard against moisture and corrosion
- ESD protection systems, including proper grounding equipment and ESD diodes
- EMI shielding solutions for sensitive components
Remember to regularly inspect your storage conditions and packaging materials to maintain their protective properties over time.
If you're shipping PCBs, use vacuum-sealed antistatic bags with appropriate cushioning materials to prevent damage during transit.
Quality Control Measures

Quality control measures safeguard circuit boards through multiple inspection points during design, manufacturing, and shipping phases. You'll need to implement thorough verification processes starting with design validation and component inspection before assembly begins.
During manufacturing, guarantee your team conducts detailed microscopic inspections of solder joints and performs extensive electrical testing.
Your quality control shouldn't stop at assembly. You'll want to verify protective packaging materials, including antistatic bags, foam inserts, and moisture barriers. Make sure you're using proper ESD protection throughout the handling process to prevent static damage.
It's essential that you validate shipping marks and packaging integrity before dispatch.
After manufacturing, you'll need to perform functional testing to confirm the PCB's performance meets specifications. Don't forget to check voltage levels and verify barcodes for accurate tracking. You should examine carton weights and quantities against your specifications, and train your staff to IPC standards for consistent quality assurance.
Watch for unusual odors that might indicate production issues. By maintaining strict quality control at each stage, you'll substantially reduce the risk of PCB damage and guarantee reliable delivery to your customers.
Frequently Asked Questions
How Long Can Circuit Boards Safely Remain in Temporary Anti-Static Packaging?
You can safely store your circuit boards in temporary anti-static packaging for about one year. After that, you'll need to replace the packaging since its anti-static properties will start to degrade.
Can PCBS Be Stacked Directly on Top of Each Other During Shipping?
No, you shouldn't stack PCBs directly on top of each other. You'll risk damage from friction, trapped moisture, electrostatic discharge, and potential shock damage. Always use non-static dividers between boards during shipping.
What Temperature Ranges Are Safe for Storing Packaged Circuit Boards?
You'll want to store your packaged circuit boards between 12°C to 40°C (54°F to 104°F). This temperature range helps prevent moisture damage and component deterioration while maintaining the board's overall reliability and performance.
How Often Should Packaging Materials Be Inspected for Wear and Degradation?
You'll need to inspect your packaging materials daily for high-volume operations, weekly for moderate volumes, and monthly for low volumes. Don't forget to conduct special checks after any material changes or incidents.
Are Biodegradable Alternatives Available for Traditional Circuit Board Packaging Materials?
Yes, you'll find several biodegradable options like Soluboard for PCB substrates, starch-based packing peanuts, cornstarch packaging, and mushroom-based materials. These alternatives can reduce your environmental impact while protecting components effectively.
In Summary
You'll find that proper PCB packaging requires a multi-layered approach. Implement anti-static materials, moisture barriers, and impact protection while ensuring boards stay immobilized during transit. Don't forget to maintain quality control throughout the process and follow shipping regulations carefully. By combining these protective methods with proper storage practices, you'll successfully safeguard your circuit boards from manufacturing to final destination.
Leave a Reply