To properly protect circuit boards, you'll need multiple layers of specialized packaging. Start with anti-static bags to prevent ESD damage, then wrap boards in ESD-safe bubble wrap or foam inserts for impact protection. You'll want to maintain humidity levels between 40-65% using desiccants and moisture barrier bags. Place wrapped boards in rigid boxes with cushioning materials like foam or packing peanuts to prevent movement. Don't forget to clearly label packages as "Fragile" and "Handle with Care." While these basics will get you started, there's much more to ensuring your PCBs arrive safely at their destination.
Understanding PCB Packaging Requirements
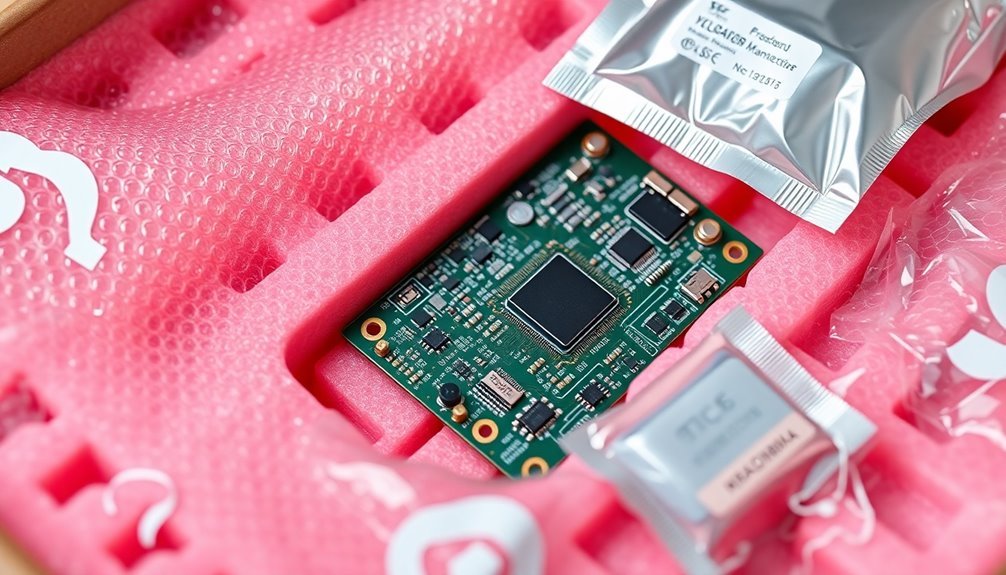
Don't forget about proper labeling—it's vital for handling and tracking. Include your supplier's CAGE Code, purchase order number, and clear handling instructions like "Fragile" on the package.
If you're storing PCBs before shipment, keep them in dry conditions and consider baking them if moisture exposure is a concern. The use of moisture barrier bags during storage provides an additional layer of protection against humidity damage.
Store your boards in a stable and dry environment with controlled temperature (range 15°C to 30°C) and with relative humidity levels of 40% to 65% to prevent damage from fluctuations. Avoid storing in damp areas as they are sensitive to humidity. Utilize desiccants or humidity control devices to maintain optimal moisture levels.
Use covers or packaging to prevent dust accumulation and ensure a clean storage environment. Protect from extended exposure to direct sunlight, as this can lead to material aging and degradation.
Stock unused boards in anti-static bags, foam sheets, or similar materials to safeguard them from mechanical and environmental damage. Store PCBs in ESD-free racks to shield against electrostatic discharge.
Label each unit with details such as model, batch number, and storage date for easier tracking and management. Conduct regular inspections of stored boards to ensure their packaging remains intact.
Essential Static Protection Materials
To safeguard your circuit boards from static damage, you'll want to start with anti-static bags made from specialized dissipative polyethylene that prevents harmful charge buildup.
Staff should maintain appropriate humidity levels in storage areas to minimize static electricity risks. You can enhance your protection by using metalized shielding bags that create a Faraday cage effect through their multi-layered construction of aluminum, carbon, and static-dissipative coatings.
When transporting circuit boards, you'll need conductive materials like properly grounded containers and static-controlled carts with specialized casters to maintain complete protection throughout transit.
Antistatic Bags And Applications
Protection against static electricity stands as a critical requirement in electronic component handling. When you're working with PCBs and sensitive electronic components, you'll need antistatic bags as your first line of defense. These bags, typically colored pink or blue, are made from specially formulated resins that prevent static buildup during handling.
You'll find that antistatic bags are single-layered and amine-free, guaranteeing they won't contaminate circuit boards or uncorroded solder points. While they're excellent for short-term storage and handling within ESD-protected areas, they don't shield against external static charges. These materials have a limited shelf life of approximately one year due to their topical treatment.
For complete protection, you'll need to combine them with static shielding bags when transporting components outside protected environments.
When using antistatic bags, you must follow proper ESD procedures and guarantee you're properly grounded. Look for bags that meet industry standards like MIL-PRF-81705D Type II and EIA-541. You'll recognize them by their ESD caution logos and anti-static notations.
Remember that these bags offer puncture resistance and basic ESD protection, but for highly sensitive components, you'll want to upgrade to multilayered static shielding bags that provide Faraday cage protection.
Metalized Wrap Protection Features
A reliable barrier against static damage, metalized wrap provides essential protection for your circuit boards through multiple specialized layers. The metallized coating prevents static buildup while efficiently dissipating charges away from your PCB, creating a robust shield against ESD, radio frequency, and electromagnetic interference.
You'll find the material composition consists of metallized plastic films with conductive properties that guarantee proper grounding and static discharge. Edge plating techniques enhance this protective capability by providing additional shielding across circuit board edges.
The wrap's thickness offers durability while maintaining effective shielding, and its adhesive properties keep it securely in place during transport and handling.
When you're packaging PCBs, place the metalized wrap between your board and external packaging materials, safeguarding a tight seal. You'll want to integrate cushioning materials for thorough protection while maintaining proper grounding procedures during the packaging process.
Conductive Materials In Transit
The selection of conductive materials plays a crucial role in safeguarding circuit boards during transit. You'll find these materials are specifically designed to provide rapid discharge of static electricity, with their low electrical resistance of less than 1 x 10^4 ohms ensuring quick and safe transfer of charges to the ground.
When you're shipping circuit boards, you'll want to use conductive packaging materials like bags and boxes that actively conduct static charges away from your sensitive components. Carbon-loaded materials are commonly used in these packaging solutions due to their excellent conductivity.
These materials provide a controlled path for electricity, substantially reducing the risk of ESD-related damage during transportation and handling.
You'll need to take into account that conductive materials work differently from static dissipative ones. While both protect against ESD, conductive materials offer faster discharge rates, making them ideal for scenarios where rapid grounding is essential.
You'll often find them used alongside static dissipative materials for thorough protection.
For the best protection, you should select conductive packaging based on your circuit boards' sensitivity levels and specific transit requirements.
Shock Prevention During Transit
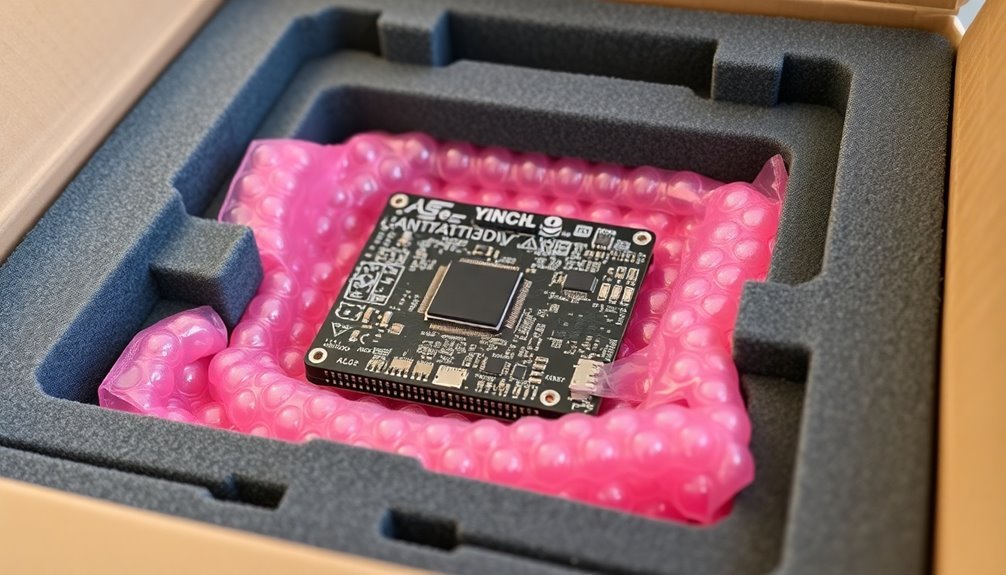
You'll need to implement multiple layers of protection to safeguard circuit boards during shipping, starting with impact-absorbing foam that cradles the board from all angles.
A well-designed cushioning system combines soft foam inserts with rigid outer materials to create suspension-like protection that absorbs both minor vibrations and major impacts. Implementing proper lifting procedures during packaging helps prevent component damage and ESD risks.
Your packaging should incorporate specialized foam solutions that match the exact dimensions of your circuit boards, preventing any movement that could lead to damage.
Multi-Layer Cushioning Systems
Protecting sensitive circuit boards during transit requires implementing thorough multi-layer cushioning systems that work together to prevent shock damage.
You'll need to start with double-walled bubble wrap and ESD-specific materials that prevent static buildup while cushioning your components. Add custom-cut ESD foam inserts to cradle specific parts and prevent movement during shipping. The inclusion of solder mask layers helps protect exposed copper traces from potential oxidation during transportation.
Your outer packaging should include rigid boxes reinforced with puncture-resistant materials. Use moisture barrier bags and sealed ESD bags for individual component protection, especially when shipping through humid environments.
Don't forget to incorporate void fill materials to eliminate empty spaces where components might shift and sustain damage.
You can enhance protection by implementing advanced technologies like vacuum sealing and anti-static coatings. Custom-designed inserts tailored to your circuit boards' dimensions will provide maximum stability.
Combine multiple materials strategically – use vibration-damping materials alongside moisture-control packaging with desiccants. Secure everything with proper fastening methods to prevent movement.
This integrated approach guarantees your circuit boards receive extensive protection against shock, static, moisture, and vibration throughout their journey.
Impact-Absorbing Foam Solutions
Selecting the right impact-absorbing foam solution is essential for safeguarding circuit boards during transit. You'll find various materials available, including non-crosslinked and cross-linked polyethylene, as well as PUR-Polyurethane, each offering unique protective properties for your PCBs.
When you're handling ESD-sensitive components, you'll want to choose antistatic or electrically conductive foam versions that prevent electrostatic discharges. These specialized foams don't just protect against physical damage; they guarantee your circuit boards remain electrically safe throughout transport and storage. The foam materials adapt to the shape of the boards, providing superior protection against impacts and vibrations.
You can customize your foam solutions to match specific PCB dimensions, creating a snug fit that prevents movement and maximizes protection. Whether you're using polyurethane foam for its lightweight properties or cross-linked polyethylene for superior cushioning, you'll benefit from excellent shock absorption capabilities.
These foams can be tailored to fit the exact shape and size of your circuit boards, ensuring they are securely held in place and protected from both mechanical and electrical risks. This customization is crucial for optimal protection during the entire process, from production to assembly.
Suspension Packaging Techniques
Circuit boards demand robust protection during transit, and suspension packaging techniques offer an innovative solution for shock prevention. You'll find that suspension systems create elastic and dissipative mechanical joints that substantially reduce vibration and shock damage to critical components.
When you're choosing a suspension packaging method, you've got several effective options. Film suspension uses stretch film inserts to suspend your boards, while 2-in-1 suspension and retention systems offer versatile protection in a single unit.
For PCBs specifically, you'll want to use antistatic stretch film combined with ESD-protected corrugated board to guard against both physical damage and electrostatic discharge.
You can easily adjust these suspension systems to match your circuit board's specific weight and vulnerabilities. The materials you select should provide ideal elasticity and shock absorption while maintaining ESD protection.
You'll appreciate that these systems are quick to set up and don't require specialized tools or expensive cushioning materials. For moisture-sensitive boards, you can integrate moisture barrier materials with your suspension packaging.
Remember to verify your packaging method through testing to confirm it meets your protection requirements.
Environmental Safeguards for PCBs
The global environmental impact of PCBs has led to strict international safeguards through the Stockholm Convention, which came into force in 2004. You'll need to comply with regulations that mandate the elimination of PCB use in equipment by 2025 and guarantee environmentally sound management of contaminated materials by 2028. The Convention prohibits new PCB production and strictly controls the import and export of PCB-containing equipment.
These regulations exist because PCBs pose significant environmental risks. They persist in the environment, travel through various mediums, and accumulate in fatty tissues throughout the food chain, affecting everything from marine life to humans.
Environmental Concern | Impact | Required Action |
---|---|---|
Persistence | Remains in environment long-term | Phase out by 2025 |
Bioaccumulation | Builds up in fatty tissues | Proper waste management |
Global Transport | Spreads via air and water | Export/import controls |
Food Chain Effects | Affects all species | Sound disposal methods |
Human Exposure | Present in most humans | Strict handling protocols |
To maintain compliance, you'll need to implement proper storage, handling, and disposal procedures for any PCB-containing equipment or materials. This includes using appropriate containment methods and working with certified disposal facilities.
Custom Packaging Solutions
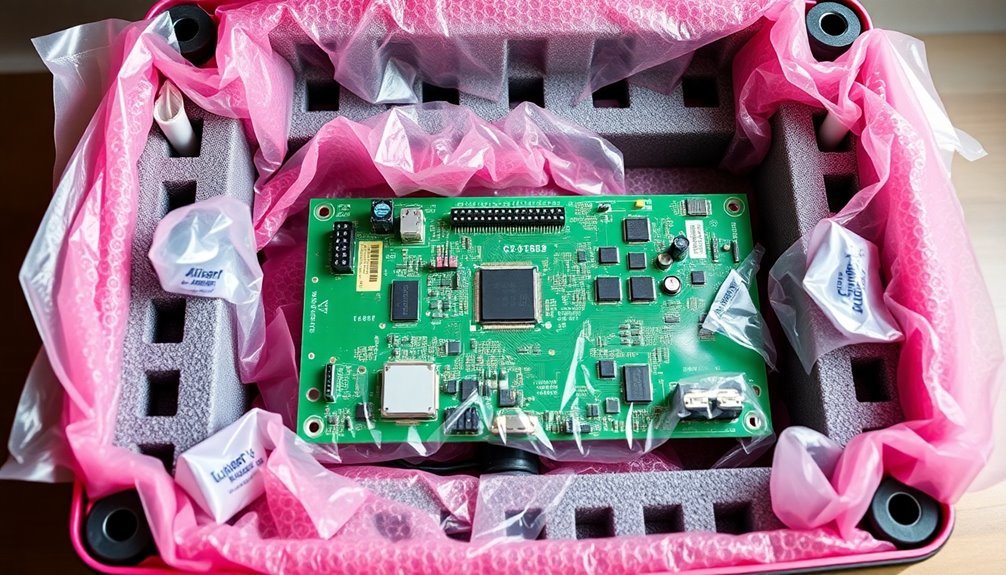
While environmental regulations govern PCB disposal and handling, proper protective packaging guarantees these valuable components reach their destination safely and remain compliant throughout their lifecycle.
You'll find that custom packaging solutions offer thorough protection through various materials like static protective containers, Corstat, CFP, and specialized foams designed for sensitive electronic components.
When you're looking to protect your circuit boards, custom solutions provide these essential benefits:
- Static discharge protection through antistatic and electrically conductive materials
- Precise fit packaging that's engineered to your exact specifications
- Moisture barrier options for sensitive PCBs requiring maximum protection
- Shock-absorbing materials that guard against vibration and physical damage
- Cost-efficient designs that reduce waste and long-term expenses
You can choose from thermoformed plastic containers, conductive fluted plastic with permanent ESD foam inserts, or vacuum-sealed packaging for extreme moisture protection. These solutions aren't just about protection – they're designed to streamline your handling processes and reduce labor costs.
Whether you're shipping bulk quantities or individual boards, custom packaging certifies your PCBs arrive intact while maintaining their integrity throughout storage and transportation.
Quality Testing and Standards
To guarantee your PCBs meet industry standards, quality testing must follow rigorous IPC guidelines and certification requirements. You'll need to comply with IPC-A-600 standards while paying special attention to critical inspection zones like solder lands, plated through-holes, and board edges.
Your quality testing protocol should include detailed measurements of conformal coating thickness and proper documentation through Certificates of Conformance. You'll want to include specific treatment types and test results in your C of C documentation.
When handling sensitive components, you must implement ESD protective measures throughout the testing process.
For moisture-sensitive components, particularly those with silver immersion finishes, you'll need to verify that your moisture barrier bags meet the required water vapor transmission rate of 0.002 gm/100 in²/24 hrs. Testing should confirm proper heat sealing with light air evacuation.
Don't forget to check that all packaging materials meet anti-static requirements and environmental durability standards.
Remember to maintain clean, dry conditions during testing and limit package quantities to one PCA or ten PCBs per moisture barrier bag.
Your quality control process should align with both IPC standards and ECIA guidelines to maintain consistent practices across manufacturing and distribution.
Shipping Best Practices
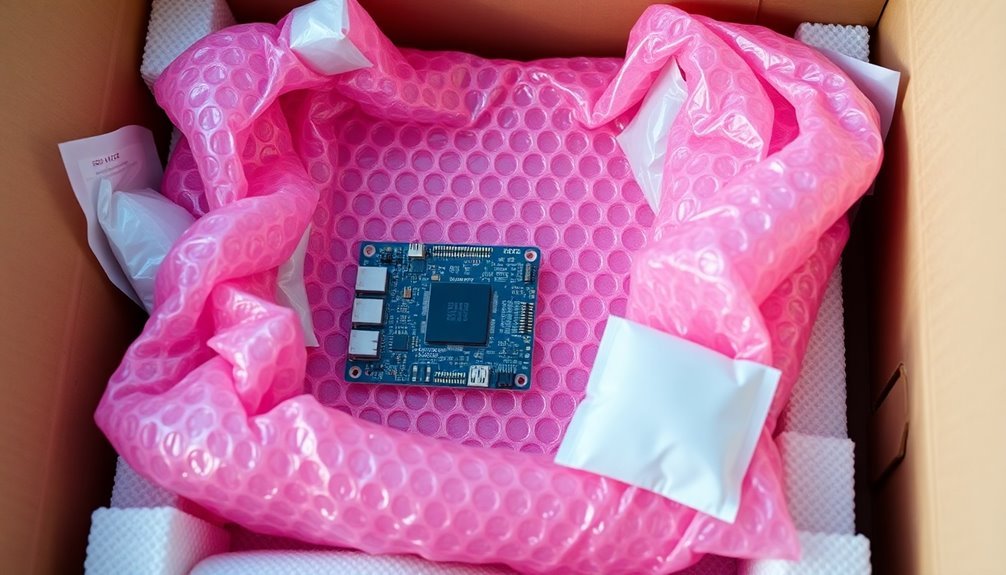
Successful PCB shipping requires careful attention to both packaging materials and handling procedures. You'll need to focus on protecting your circuit boards from static electricity, physical damage, and environmental factors during transit.
Start by cleaning each PCB thoroughly and placing it in an anti-static bag to prevent ESD damage.
Choose your packaging materials carefully, selecting options that provide multiple layers of protection. Your PCBs should be immobilized within the shipping container using foam inserts or cardboard partitions, and wrapped in appropriate cushioning materials like bubble wrap or foam sheets.
Essential shipping best practices include:
- Using moisture barrier bags to protect against corrosion and humidity
- Implementing proper labeling with clear handling instructions
- Selecting tracking-enabled courier services for shipment monitoring
- Installing non-static dividers between multiple PCBs
- Insuring valuable shipments against loss or damage
When shipping in bulk, consider using reusable packaging solutions like conductive fluted plastic containers or custom-designed foam inserts. You'll save money in the long run while ensuring consistent protection for your PCBs.
Remember to document all shipments thoroughly and maintain clear communication with both shipping providers and recipients throughout the process.
Frequently Asked Questions
Can PCBS Be Stacked During Shipping if Proper Cushioning Is Used?
You shouldn't stack PCBs during shipping, even with cushioning, as it risks damage and electrostatic discharge. If you absolutely must stack them, you'll need proper anti-static materials and cushioning between each board.
How Long Can PCBS Safely Remain in Temporary Packaging Materials?
You shouldn't keep PCBs in temporary packaging for more than 72 hours. If you're storing them longer, transfer them to proper moisture barrier bags with desiccants to maintain their surface finish quality.
What's the Maximum Temperature PCB Packaging Materials Can Withstand During Transit?
You'll want packaging that withstands up to 60-70°C during transit. Standard anti-static bags and foam can handle these temperatures, but don't expose them to higher heat as it may compromise protection.
Should Different-Sized PCBS Be Packaged Together in the Same Container?
You shouldn't package different-sized PCBs together. It's best to separate them to prevent damage, as larger boards can harm smaller ones. Use size-specific packaging to guarantee proper protection and immobilization.
How Often Should Packaging Materials for PCBS Be Replaced in Storage?
You'll need to inspect your PCB packaging materials every 30 days and replace them when you notice signs of degradation. Don't wait longer than recommended, as compromised materials won't protect your boards adequately.
In Summary
Protect your circuit boards effectively by combining anti-static packaging, shock-absorbing materials, and proper moisture barriers. You'll need to guarantee your packaging meets industry standards and undergoes thorough testing before implementation. Don't forget to clearly label packages with handling instructions and ESD warnings. When you're following these protective measures consistently, you'll substantially reduce damage risks during storage and shipping.
Leave a Reply