To control static in semiconductor plants, you'll need to establish Electrostatic Protected Areas (EPAs) and maintain consistent electrostatic potential throughout your facility. Install proper grounding systems, air ionization units, and conductive flooring that meets semiconductor industry standards. You must manage the triboelectric effect by eliminating static-generating processes and using static-dissipative materials. Train your personnel on ESD fundamentals, anti-static tools, and cleanroom protocols. Regular testing and verification are essential – conduct daily personal grounding checks, monthly surface resistivity measurements, and quarterly ionizer performance tests. The deeper you explore these guidelines, the more protected your sensitive components will be.
Understanding Static Control Fundamentals
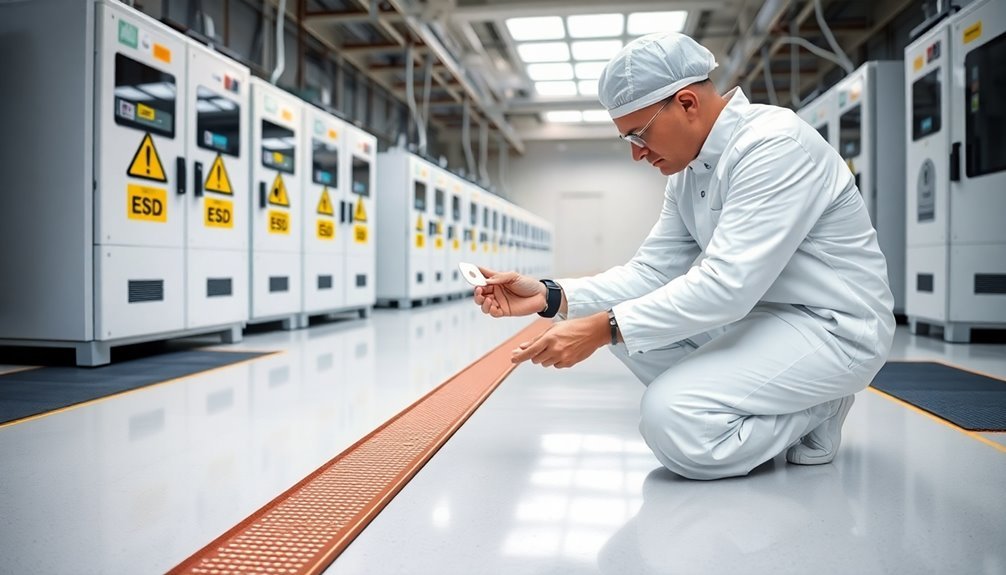
Getting to grips with static control in semiconductor plants starts with mastering the fundamental principles. You'll need to design your products and processes with built-in protection against electrostatic discharge (ESD) effects, while clearly defining the required level of static control for your specific environment.
You must identify and establish electrostatic protected areas (EPAs) where you'll handle sensitive components. Within these areas, you'll want to focus on keeping all processes and materials at the same electrostatic potential to prevent charge generation.
When charges do occur, you'll need to implement proper grounding, ionization, and conductive materials to neutralize them effectively. The implementation of effective ESD controls is crucial since ESD-related damage can cost manufacturers up to 33% in losses.
To maintain robust static control, you'll need to pay special attention to the triboelectric effect, which can generate unwanted charges when materials like glass, silica, plastics, and elastomers interact. These charges can lead to ESD damage, electromagnetic interference, and unwanted particle attraction.
You'll find that establishing proper grounding procedures is essential – all conductors and dissipative materials must connect to a common ground point, and you should regularly test these connections to verify they're maintaining equipotential balance.
Facility Design Best Practices
Now that you understand static control fundamentals, implementing them through proper facility design creates the foundation for effective ESD protection. Your facility's construction materials, layout, and infrastructure must work together to minimize static risks while maintaining operational efficiency.
When designing your semiconductor facility, you'll need to prioritize static-resistant materials throughout the building. This includes installing conductive or static-dissipative flooring, selecting appropriate furniture, and ensuring all equipment is properly grounded. Continuous monitoring of these control methods ensures static charge is managed effectively before causing issues.
Your layout should create clear separation between static-sensitive areas and potential static generators.
Here are the critical elements you must incorporate into your facility design:
- Fire barriers with minimum one-hour ratings between cleanrooms and HC-2 occupancies
- Earthquake restraints designed for specific horizontal force requirements
- Power conditioning systems to maintain clean power supply
- Integrated static control devices like air ionizers in key areas
Remember to design your automated material handling systems with static control in mind, following SEMI E78 standards. You'll also want to implement continuous monitoring systems to verify the effectiveness of your static control measures and maintain compliance with industry standards like SEMI E129 and ANSI/ESD S20.20.
Air Ionization Systems
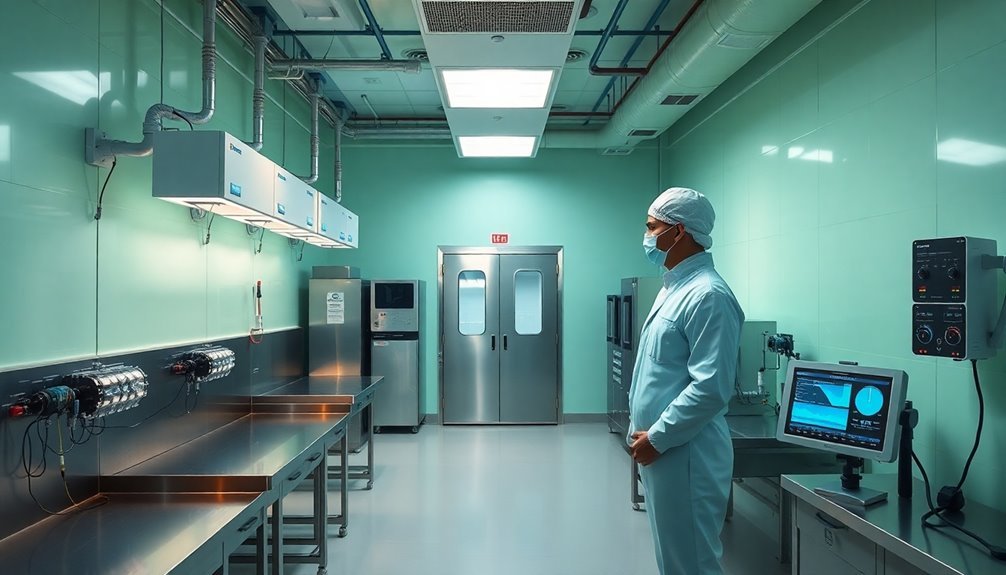
Understanding how air ionization systems work is crucial for effective static control in semiconductor facilities. These systems can reduce static charges by 50% to 90%, substantially decreasing particle contamination on semiconductor wafers and improving overall production yields. Cleanroom emitters should be placed at 6-foot intervals for optimal coverage.
You'll need to implement ionization systems strategically throughout your facility, particularly in cleanroom environments where insulators are present. Focus on critical areas like cassette transfer tools, temperature chambers, and stepper minienvironments.
When properly deployed, you'll see improved IC testing results and reduced microprocessor downtime.
To maintain peak performance, you must select appropriate emitter point materials and regularly verify system balance. Don't overlook the importance of routine maintenance and inspection to prevent particle generation.
You'll want to integrate your ionization systems with other static control methods for maximum effectiveness.
Monitor your system's output current levels continuously and adjust as needed to minimize particle generation. You'll find that well-maintained ionization systems increase machine uptime and enhance cleaning efficiency in both manual and liquid processes.
Remember to implement thorough verification procedures to guarantee your systems maintain proper balance and performance over time.
Equipment Grounding Requirements
While air ionization addresses airborne static concerns, proper equipment grounding forms the backbone of your semiconductor facility's static control system. You'll need to guarantee all equipment meets ANSI/ESD S20.20 standards and maintains a resistance path to ground of less than 1 ohm for explicit grounding connections. Ground bus bars on equipment must be mounted using insulated standoffs to maintain proper isolation.
It's vital to connect equipment through proper equipment grounding conductors rather than directly to grounding electrodes, as this practice isn't allowed by the NEC.
Your facility's grounding system should incorporate these essential requirements:
- Establish a minimum of two grounding electrodes unless you can achieve less than 25 ohms resistance with one
- Space electrodes at twice their length to prevent overlapping zones of influence
- Maintain less than 1.0 x 10^9 ohms resistance between ESD control items and common connection points
- Connect all exposed metal parts to guarantee they're at earth potential
You'll need to verify that your auxiliary grounding maintains less than 25 ohms resistance to the equipment grounding conductor. Remember that while the NEC only requires 25 ohms ground resistance, you should aim for 5 ohms or less in your industrial semiconductor setting to achieve ideal static control protection.
Material Selection Guidelines
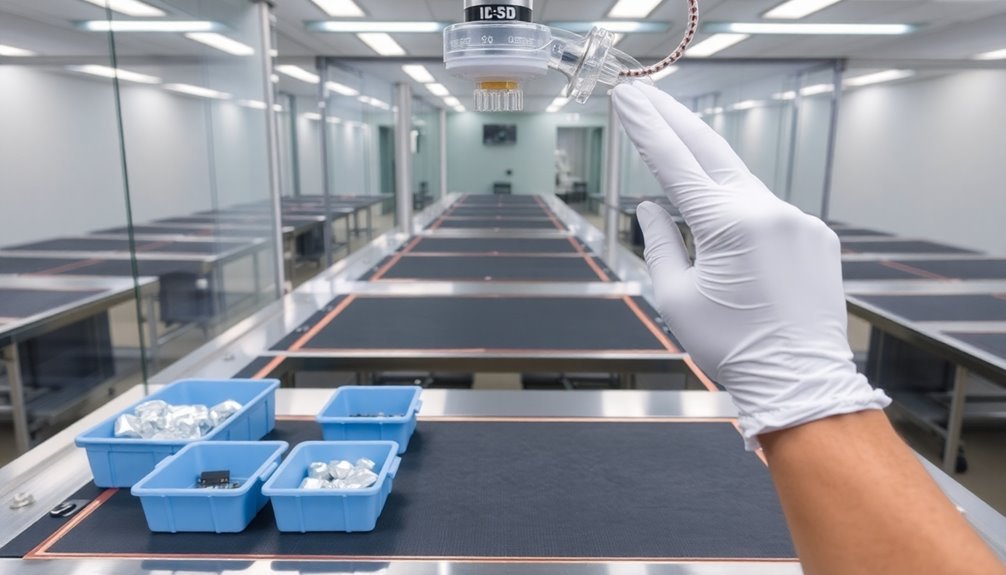
You'll need to install conductive flooring and wall materials that meet semiconductor industry ESD standards to establish a proper static-controlled environment.
Make sure you don't use highly insulative materials in critical areas, as they can accumulate dangerous static charges that may damage sensitive components. Consider implementing triboelectric nanogenerators as an advanced method for controlling static buildup from human movement.
Your equipment must incorporate static-dissipative components, including properly grounded work surfaces, storage containers, and handling tools, to maintain an effective static control system throughout the facility.
Conductive Floor and Walls
Semiconductor plants' static control relies heavily on proper material selection for conductive floors and walls. You'll need to guarantee your flooring has a resistance of less than 1 million ohms to meet ANSI standards and provide ideal charge dissipation.
For floors, you can choose from conductive vinyl sheets, seamless ESD tiles, or epoxy floors with conductive materials. Your walls should use conductive coatings or materials with similar resistance levels. Movement within the facility significantly increases static discharge risks, making proper static control measures essential.
When installing conductive flooring and walls, you'll need to follow these critical requirements:
- Install copper grounding strips for every 1,000 sq. ft. of ESD flooring
- Connect all surfaces to a proper grounding system
- Prepare surfaces with conductive underlayment
- Test regularly to maintain ANSI/ESD S20.20 compliance
You'll need to maintain these surfaces regularly to preserve their conductivity. This includes using appropriate cleaning methods and conducting periodic resistance testing. For flooring, you can apply conductive floor finishes to help maintain effectiveness.
Remember that both floors and walls must work together in your static control system to protect sensitive semiconductor equipment and maintain a safe manufacturing environment.
Insulative Material Restrictions
In semiconductor manufacturing, proper material selection plays a critical role in static control, particularly regarding insulative materials. You'll need to carefully assess all non-conductive materials for static charge accumulation and guarantee they're treated or modified to reduce static risks. Due to the extensive use of silicon-based wafers, precise material selection is especially critical during wafer fabrication processes.
When you're selecting materials for your semiconductor facility, opt for conductive or static-dissipative alternatives whenever possible. If you must use insulative materials, you'll need to apply conductive coatings or films and implement proper grounding systems. Don't forget to install and regularly verify ionization systems as an additional control measure.
You must guarantee your material choices comply with ISO/TS-16949 and ISO 15494:2015 standards for plastic components. Your selected materials should withstand harsh chemicals while maintaining their static control properties.
When designing tools and components, you'll need to think about precise dimensional requirements and optimize for both cost and quality.
For cleanroom environments, you're required to follow specific static charge control regulations. Remember to regularly qualify your tools and verify that all insulative materials meet thermal and chemical resistance standards.
This thorough approach to material selection will help minimize static-related defects in your semiconductor manufacturing process.
Dissipative Equipment Components
Building on proper insulative material control, selecting the right dissipative equipment components requires careful consideration of specific material properties. You'll need to focus on materials that effectively dissipate static charges while meeting stringent semiconductor manufacturing requirements.
Electrostatic dissipative coatings, electrically dissipating elastomers, and EMI shielding materials form the core components of your ESD protection strategy. Cleanroom conditions are critical for maintaining the effectiveness of these dissipative materials.
When selecting dissipative materials for your semiconductor manufacturing equipment, you'll want to prioritize these essential characteristics:
- Low moisture absorption rates to maintain consistent electrical properties
- Tight substrate weave for reliable performance
- Strong CAF (Conductive Anodic Filament) resistance
- Appropriate dissipation factors for your specific application
Your material choices should align with ESD Association guidelines while providing effective protection against static damage.
You'll find that properly selected dissipative components not only protect semiconductor materials from ESD damage but also help minimize dust attraction and extend equipment lifespan.
Remember to verify that your chosen materials meet the required standards for dielectric constants and dissipation factors specific to your manufacturing process.
Personnel Training Programs
Through thorough personnel training, manufacturing facilities can establish effective static control practices that protect sensitive semiconductor devices. You'll need to master fundamental concepts like electrostatic charge behavior, proper grounding techniques, and the use of air ionization systems. Your training must cover both theoretical knowledge and practical applications, guaranteeing you're equipped to handle static-sensitive components safely.
Training Component | Key Focus Areas | Verification Methods |
---|---|---|
Basic Theory | ESD principles, charge generation, device sensitivity | Written assessments |
Equipment Handling | Anti-static tools, grounding procedures, ionizer operation | Practical demonstrations |
Cleanroom Protocol | Proper attire, material handling, workspace maintenance | Observation checklists |
Compliance Standards | SEMI E129, ANSI/ESD S20.20, ITRS guidelines | Certification tests |
You'll learn to implement industry-standard practices aligned with SEMI E129 and ANSI/ESD S20.20 guidelines. The training emphasizes proper use of static-dissipative surfaces, antistatic materials, and specialized tools. You must understand cleanroom attire requirements and maintain strict protocols for handling sensitive devices. Regular assessments and documentation of your training guarantee ongoing compliance with industry standards and help maintain the integrity of static control measures throughout the facility.
Testing and Verification Methods
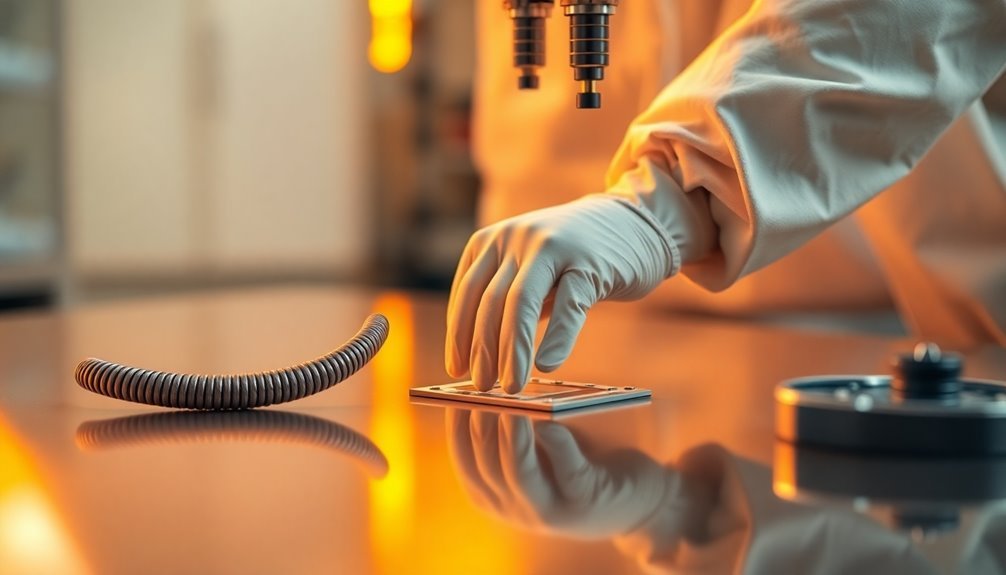
Proper training must be supported by robust testing and verification methods to guarantee static control measures remain effective. You'll need to implement thorough testing protocols based on established standards like SEMI E129 and ANSI/ESD S20.20. These frameworks provide structured approaches to assess and maintain your facility's static control effectiveness.
Regular performance verification is vital through systematic testing of all static control components. You should conduct periodic measurements of semiconductor products' charged potential and verify the resistance values of anti-static mats, which should fall between 7.5 x 10^5 and 1 x 10^9 ohms.
Here are the essential verification steps you must follow:
- Perform daily checks of personal grounding equipment, including wrist straps and conductive footwear.
- Measure and record surface resistivity of work surfaces and flooring monthly.
- Test ionizer performance and balance at least quarterly.
- Conduct extensive ESD audits semi-annually to verify system-wide compliance.
Remember to document all test results and maintain detailed records of verification activities. When tests reveal any deviations from established parameters, you'll need to implement immediate corrective actions to maintain the integrity of your static control program.
Industry Standards Implementation
To implement effective static control in your semiconductor facility, you'll need to follow key standards like SEMI E129 and ISO 14644-1, which establish critical benchmarks for electrostatic charge management.
Your static control program must integrate continuous verification protocols through regular testing and monitoring to maintain compliance with these industry requirements.
You'll find that systematic implementation of these standards, combined with ongoing verification, helps prevent costly product losses from ESD and contamination while meeting regulatory demands.
Key Standards For Compliance
Several critical industry standards govern static control compliance in semiconductor manufacturing facilities. You'll need to focus primarily on SEMI E78-1102 and E129-1103 standards, which provide thorough guidelines for evaluating and controlling electrostatic discharge and attraction.
These standards are especially vital as device sizes continue to shrink, making static control an increasingly significant technology barrier.
To guarantee effective implementation, you should utilize the ANSI/ESD S20.20 standard, which offers flexibility in defining your static control program based on your specific product sensitivities. The ITRS 2003 recommendations reinforce these standards while emphasizing their cost-effectiveness in preventing static-related problems.
When implementing these standards, you'll need to:
- Incorporate static control methods into your initial facility design
- Conduct regular verification testing using SEMI E129 methods
- Maintain ongoing compliance through documented maintenance procedures
- Adjust acceptable static charge levels based on your product feature sizes
Verification isn't a one-time event. You must continuously monitor and adjust your static control measures as part of your factory maintenance routine, guaranteeing protection for both current and future technology nodes.
Continuous Verification Protocols
Effective continuous verification protocols serve as the backbone of any semiconductor facility's static control program. You'll need to implement a multi-layered approach that combines formal verification methods with assertion-based techniques to guarantee thorough static control protection.
By utilizing GapFreeVerification analysis and digital twin integration, you're able to detect potential vulnerabilities before they impact production.
You'll want to align your protocols with key industry standards like SEMI E187 and E188, which provide frameworks for cybersecurity in semiconductor manufacturing equipment and facilities. Implement regular risk assessments and vulnerability scanning to maintain the integrity of your static control measures.
Through high-level automation and real-time data analysis, you can monitor and verify your static control systems without requiring deep hardware expertise.
Make sure you're leveraging digital twin technology to simulate and predict the impact of new security weaknesses on your static control infrastructure. This approach allows you to conduct pre-fabrication verification and identify corner-case issues that traditional testing might miss.
Remember to maintain continuous support through commercial-grade technology to guarantee your verification protocols remain effective and up-to-date.
Frequently Asked Questions
How Often Should Air Ionizer Emitter Points Be Cleaned and Maintained?
You'll need to clean your air ionizer emitter points every 3-6 months, but check them more frequently if you're in advanced cleanroom environments. Don't forget to verify performance after each cleaning.
What Humidity Levels Are Optimal for Effective Static Control?
You'll want to maintain relative humidity between 30% and 60% for effective static control. For ideal ESD protection, aim closer to 60%, but don't exceed 70% to avoid corrosion and particle adhesion issues.
Can Wireless Devices Interfere With Static Control Monitoring Systems?
Yes, your wireless devices can substantially interfere with static control monitoring systems. You'll notice they can disrupt accuracy and reliability, especially when multiple devices overlap channels, potentially compromising your static hazard detection capabilities.
How Do Seasonal Changes Affect Static Control Effectiveness in Semiconductor Facilities?
You'll notice lower humidity in winter increases ESD risks, while peak production seasons reduce static issues. You must adjust your humidity controls and static measures seasonally to maintain effective semiconductor facility protection.
What Is the Typical Lifespan of Static Dissipative Flooring Materials?
You'll find vinyl floors maintain ESD properties for 20+ years, while epoxy floors need recoating after just a few years. Despite physical durability lasting longer, ESD effectiveness varies substantially between different flooring materials.
In Summary
You'll find that implementing thorough static control measures is vital for protecting your semiconductor manufacturing operations. By following these essential guidelines for facility design, air ionization, grounding, materials, and personnel training, you're establishing a robust ESD protection system. Don't forget to regularly test and verify your controls while staying compliant with industry standards. Your diligence in static control directly impacts product quality and yield rates.
Leave a Reply