To get certified in semiconductor handling safety, you'll need to complete several key training programs. Start with OSHA's 10-Hour Semiconductor General Training to learn fundamental worker rights and hazard identification. Next, pursue SESHA's Safety Bootcamp Suite for specialized chemical and toxic gas handling certifications. You'll also need to master GHS protocols and complete the two-part Semiconductor Process Chemical Safety Training. Make sure to document all training and obtain third-party assessments for each certification. The path to proper semiconductor safety certification involves multiple layers of expertise that build upon each other.
Understanding Semiconductor Safety Basics

Safeguarding semiconductor manufacturing starts with understanding fundamental safety principles. You'll need to master proper ventilation systems, personal protective equipment (PPE), and chemical handling protocols before working with semiconductors.
Understanding how to monitor air quality and implement protective barriers is vital for your safety and those around you. Trained personnel must complete comprehensive safety courses to handle energetic materials properly.
You'll learn to identify and prevent hazards associated with energetic materials, radiation, and toxic metals. Recognizing potential dangers and knowing how to handle water-reactive and pyrophoric chemicals safely is imperative.
You must become familiar with fire prevention strategies and emergency response procedures to handle unexpected situations effectively.
Your training will cover proper chemical storage techniques, including correct labeling and ventilation requirements. You'll discover how to handle semiconductor materials without causing damage or dangerous material release.
Regular equipment maintenance and proper ventilation system operation are skills you'll need to master.
The SEMI-S2 standard and OSHA regulations will guide your understanding of safety requirements. You must learn to conduct material characterization according to industry standards and participate in regular safety audits to maintain compliance with established protocols.
Essential Certification Programs
Today's semiconductor industry's certification requirements guarantee you're properly qualified to handle hazardous materials and complex processes safely.
To get started, you'll need to complete the OSHA 10 Hour Semiconductor General Training, which UL and SESHA developed specifically for the high-tech industry. This online program covers worker rights, employer responsibilities, and hazard identification. The program provides 24/7 online access to accommodate various work schedules.
If you're aiming for advanced credentials, you can pursue Texas A&M University's Online Safety in Semiconductor Processing Certificate. You'll need a bachelor's degree in engineering with a 3.0 GPA minimum. This program requires 12 semester credit hours covering microelectronics processing and nanomaterials.
For specialized training, you'll want to complete SESHA's Safety Bootcamp Suite, which includes courses on chemical safety, toxic gases, and hazardous energy procedures.
If you're working in automotive semiconductors, you'll need ISO 26262 certification, which focuses on product development safety and vendor qualifications.
Each certification program includes mandatory documentation of safety processes and requires third-party assessments. You'll learn detailed fabrication safety protocols and gain thorough knowledge of semiconductor-specific hazard controls.
Required Training Components
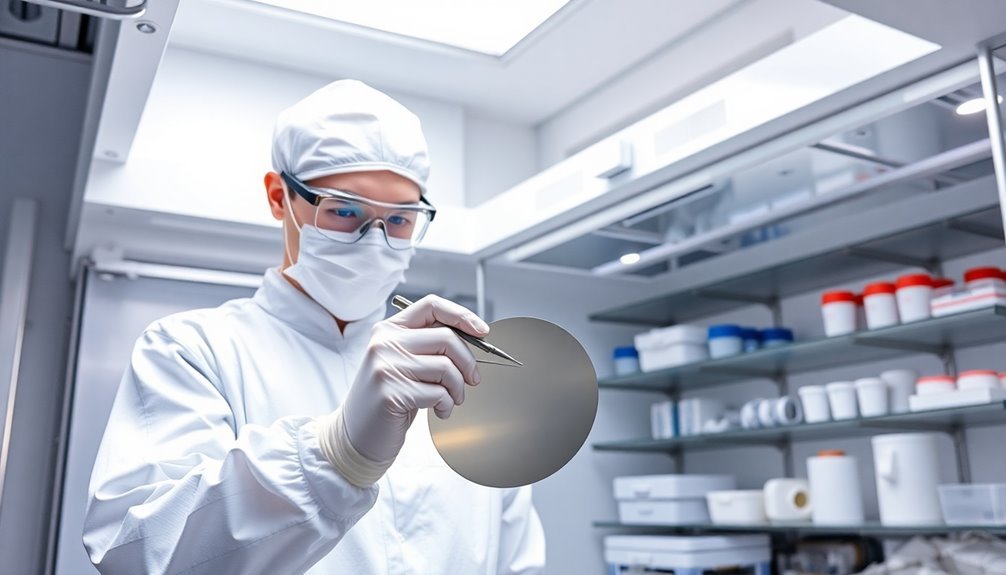
Your core chemical safety training must cover essential GHS protocols, hazard communication, and emergency procedures for handling semiconductor materials.
You'll need to master the proper controls and responses for extremely hazardous chemicals, with special attention to gases and their containment systems. The comprehensive curriculum requires 373 minutes of training to complete all safety modules.
Equipment protection requirements include thorough knowledge of SEMI guidelines S1 through S10, focusing on safety labels, evaluations, and risk assessment procedures.
Core Chemical Safety Training
Core chemical safety training forms the foundation of semiconductor handling certification, aligning with OSHA standards 29 CFR 1910.1200 and 1910.1450. You'll need to master chemical hazard identification, safe handling procedures, and proper storage guidelines specific to semiconductor manufacturing environments.
During your training, you'll learn to interpret the Globally Harmonized System (GHS) for chemical classification and labeling. This includes understanding Safety Data Sheets (SDS) and recognizing various hazard pictograms.
You'll also become proficient in identifying chemical by-products and special hazards unique to compound semiconductor operations. A designated Chemical Hygiene Officer must oversee all laboratory safety protocols and procedures.
Your training will cover essential emergency response procedures for chemical spills and releases. You'll learn proper PPE selection and usage to protect yourself from hazardous exposures.
The program emphasizes practical applications, including chemical segregation techniques and proper labeling protocols.
While OSHA doesn't mandate specific retraining intervals, you'll need to stay current with regulatory updates and participate in refresher courses as required by state and local laws.
Upon completing your core chemical safety training, you'll receive certification documenting your competency in semiconductor chemical handling.
Remember to maintain accurate records of your training and certifications for compliance purposes.
Equipment Protection Requirements
Building upon your chemical safety foundation, equipment protection training introduces specific requirements aligned with the SEMI S2 Standard. You'll need to understand the 22 EHS categories and comply with specific safety protocols designed to protect both personnel and equipment in semiconductor manufacturing environments.
The training guarantees you're prepared to handle emergency shutdowns and maintain proper ventilation specifications while working with sensitive semiconductor equipment. Safe fabrication procedures involving hazardous chemicals and gases require specialized handling knowledge.
To meet equipment protection requirements, you'll need to master these essential components:
- Personal protective equipment usage, including proper fitting and maintenance of gloves, safety glasses, face shields, and respirators to prevent chemical exposure and injuries.
- Regular equipment inspection protocols and preventive maintenance procedures, including lockout/tagout implementation during servicing.
- Proper handling and storage techniques in controlled environments, maintaining specific temperature and cleanliness standards.
- Emergency response procedures and shutdown protocols aligned with SEMI S2 guidelines.
You'll need to demonstrate proficiency in these areas through practical assessments and receive certification from authorized organizations like DEKRA. This certification verifies your ability to maintain safety standards while protecting valuable semiconductor equipment and materials.
OSHA Compliance Standards
The Occupational Safety and Health Administration (OSHA) has established rigorous compliance standards for semiconductor handling that align with industry-specific guidelines like SEMI-S2 and ANSI Z244.1.
To maintain compliance, you need to focus on several key areas, including proper lockout/tagout procedures using control circuit type devices and implementing thorough ventilation systems to minimize exposure to harmful particles and chemicals. The extensive EHS hazard categories outlined in SEMI standards must be carefully addressed during safety implementations.
To meet OSHA requirements, you must provide appropriate PPE and verify workers use it correctly. This includes gloves, goggles, and protective aprons when handling hazardous materials.
You'll also need to implement a regular equipment maintenance schedule and document all inspections to prevent mechanical failures.
Employee training is vital for OSHA compliance. You'll need to provide detailed instruction on hazardous materials handling, equipment operation, and emergency protocols.
Make sure you're following the SEMI Standards "S" series guidelines and maintaining proper chemical labeling and storage practices. Don't forget to regularly monitor air quality and maintain gas detection systems.
To stay compliant, you should also participate in OSHCON's free consultation program, which can help identify potential safety issues before they become problems.
Chemical Safety Training Requirements

Safety training extends beyond basic OSHA compliance into specific chemical handling requirements for semiconductor operations. You'll need to complete a two-part training course that covers thorough chemical safety protocols, hazard communication, and emergency procedures.
The certification process typically takes 2-4 hours total, with each part requiring 1-2 hours of focused study. Course access is available 24/7 for up to a year after enrollment.
Your chemical safety training must align with both the OSHA Hazard Communication Standard and Laboratory Safety Standard while incorporating semiconductor-specific hazards. The curriculum emphasizes the Globally Harmonized System (GHS) and SEMI standards for energetic materials.
- You'll learn to identify and handle various categories of semiconductor chemicals, understanding their unique hazards and proper storage requirements.
- The training covers engineering controls, administrative measures, and proper use of personal protective equipment.
- You must master emergency response procedures specific to semiconductor operations.
- You'll study process-specific hazards, including those associated with compound semiconductor manufacturing.
While federal OSHA doesn't mandate specific retraining intervals, your local regulations may require periodic recertification. Upon completing both parts and making payment, you'll receive your certification demonstrating your competency in semiconductor chemical safety.
Equipment Handling Procedures
Proper equipment handling in semiconductor facilities requires multiple layers of static control and damage prevention. You'll need to guarantee all equipment and tools are properly grounded, and work surfaces must be equipped with anti-static mats that are correctly grounded to prevent electrostatic buildup.
When handling semiconductor products, you'll need to use anti-static containers and specialized transport equipment with conductive castors. Your tools should include anti-static tweezers or vacuum tweezers with conductive chucking pads. Storage in a clean, dry atmosphere with nitrogen is essential for preventing oxidation and contamination.
You must inspect all equipment regularly for wear that could potentially damage semiconductor products.
You'll need to maintain strict static control measures throughout the facility. This includes using grounding straps, ionizing air blowers, and guaranteeing work chairs have conductive covers grounded to the floor.
During transportation, you must minimize mechanical vibration and protect products from moisture.
For storage, you'll need to use containers made of static-free materials and avoid stacking products directly on top of each other. It's crucial to separate boards with mounted semiconductors and store them in anti-static board containers.
Remember to periodically measure the charged potential of products and systems in your work area.
Hands-On Training Protocols

Establishing effective hands-on training requires completion of thorough OSHA-approved programs and industry-specific certification courses. You'll need to participate in extensive training sessions that combine theoretical knowledge with practical applications in state-of-the-art facilities.
These programs typically include nanofabrication labs and materials characterization labs where you'll develop essential skills through immersive learning experiences.
During your hands-on training, you'll engage in module-based learning that covers essential semiconductor handling procedures while emphasizing safety protocols. The training includes both synchronous and asynchronous components, with up to 60 hours of practical lab work where you'll perform actual semiconductor manufacturing tasks.
- Complete OSHA 10 Hour Semiconductor General Training to understand worker rights and hazard identification
- Participate in industry-specific demonstrations focusing on safe handling, storage, and fabrication processes
- Engage in collaborative projects to apply your skills in thin-film deposition and etching techniques
- Document your practical experience through site-specific training activities and portfolio building
Your hands-on training culminates in receiving recognized certifications that verify your competency in semiconductor handling safety, preparing you for entry-level positions in the industry.
Industry-Specific Safety Guidelines
The semiconductor industry requires stringent adherence to thorough safety guidelines that protect both personnel and equipment. You'll need to master proper ventilation protocols, including the use of fume hoods and exhaust systems to remove harmful airborne particles and gases. It's critical to implement gas detection systems and maintain regular air quality checks.
Safety Area | Key Requirements | Essential Equipment |
---|---|---|
Chemical Handling | Proper labeling and storage | PPE, automated systems |
Radiation Safety | Barrier implementation | Shields, warning systems |
Machine Safety | Regular maintenance | Lockout/tagout devices |
When working with chemicals, you'll need to follow strict protocols for handling, storing, and disposing of hazardous materials. Always use automated systems when possible and verify you're wearing appropriate PPE. Machine and radiation safety requires proper guards, shields, and lockout/tagout procedures during maintenance.
You must comply with SEMI and OSHA standards, participating in regular inspections and safety design reviews. These guidelines aren't just recommendations – they're mandatory requirements that protect you and your colleagues. Stay current with certification requirements and maintain thorough documentation of all safety procedures and training completed.
Certification Assessment Process

Successfully completing semiconductor safety certification requires mastering multiple assessment components and standards. You'll need to demonstrate proficiency in SEMI guidelines S2, S8, and S10, which cover environmental health, ergonomics, and risk assessment processes.
Texas A&M University's Graduate Certificate program requires a bachelor's degree in engineering and completion of 12 semester credit hours through specific courses like CHEN 675 and SENG 689.
The certification assessment evaluates your knowledge and skills across four critical areas:
- Fire protection systems and electrical safety protocols, including emergency shutdown procedures and hazard warning implementations
- Chemical handling competencies, radiation safety measures, and noise control strategies following SEMI S2-0821 guidelines
- Ventilation and exhaust specifications, including proper documentation of safety procedures and maintenance requirements
- Risk assessment methodologies aligned with SEMI S10-0423E standards and ISO 26262 functional safety requirements
You'll need to demonstrate practical understanding of hazard mitigation techniques and the ability to implement safety principles in real-world scenarios. The certification guarantees you're equipped to maintain compliance with regulatory requirements while fostering a safety-conscious culture within semiconductor manufacturing environments.
Professional Development Pathways
Beyond mastering certification requirements, you'll find numerous pathways to advance your semiconductor safety expertise. You can pursue university programs like Texas A&M's Safety in Semiconductor Processing or engage in industry-specific training such as OSHA's 10 Hour Semiconductor General Training. Many employers offer tuition reimbursement and career development planning to support your growth.
Development Path | What You'll Gain |
---|---|
University Programs | Extensive understanding of microelectronics processes and material safety protocols |
Industry Training | Practical knowledge of hazard identification and ISO 26262 implementation |
Professional Workshops | Hands-on experience with equipment operation and lean production methods |
To enhance your expertise, you'll need to develop technical proficiency in circuit theory, power electronics, and statistical process control. Consider pursuing UL-Certified Functional Safety Professional Training or participating in professional development workshops offered by organizations like Festo. Stay current by engaging with industry publications and joining semiconductor manufacturing communities. Your career options span various positions, from manufacturing management to engineering fundamentals, all emphasizing critical thinking and continuous learning.
Frequently Asked Questions
How Long Does Semiconductor Safety Certification Remain Valid Before Requiring Renewal?
Your semiconductor safety certification typically remains valid for three years. After that, you'll need to renew it through recertification processes, which may include completing continuing education requirements and passing updated assessments.
Can Previous Workplace Safety Certifications Count Toward Semiconductor Handling Requirements?
While your general workplace safety certifications can provide useful foundational knowledge, they won't fully satisfy semiconductor handling requirements. You'll need additional specialized training to meet industry-specific safety standards and compliance regulations.
Are There Physical Health Requirements to Qualify for Semiconductor Safety Certification?
You won't face specific physical health requirements for semiconductor safety certification. While employers must guarantee you can work safely, certification programs focus on your knowledge of safety procedures rather than your physical condition.
What Percentage of Certified Professionals Successfully Transition Into Semiconductor Manufacturing Roles?
You won't find exact changeover rates since they're not publicly reported. While certification programs aim to prepare you for semiconductor manufacturing roles, success rates vary based on your skills, experience, and local industry demand.
Does Certification Cost Vary by Location or Training Provider?
Yes, you'll find significant cost variations based on your location and chosen provider. Regional regulations, testing standards, and provider-specific fees can impact your certification costs, with ranges from $4,400 to $19,000 for different certifications.
In Summary
Getting certified in semiconductor handling safety isn't just about meeting requirements – it's about protecting yourself and others while working with sensitive materials. Once you've completed your training, certifications, and assessments, you'll need to stay current with evolving industry standards. Remember to maintain your credentials through continuing education and regular safety updates. Your commitment to safety certification is an investment in your professional future.
Leave a Reply