Your factory needs static control audits to protect workers, equipment, and products from the damaging effects of electrostatic discharge (ESD). Regular audits help you identify high-risk areas, verify the effectiveness of protection measures, and guarantee compliance with OSHA and industry standards. Without proper monitoring, static buildup can cause immediate or latent damage to electronic components, disrupt machinery alignment, and contaminate products – leading to significant financial losses. In fact, companies lose an average of 6.5% in revenue due to ESD-related issues. Understanding your facility's static control needs will help you implement the right protective measures to safeguard your operations.
Understanding Static Control Risks
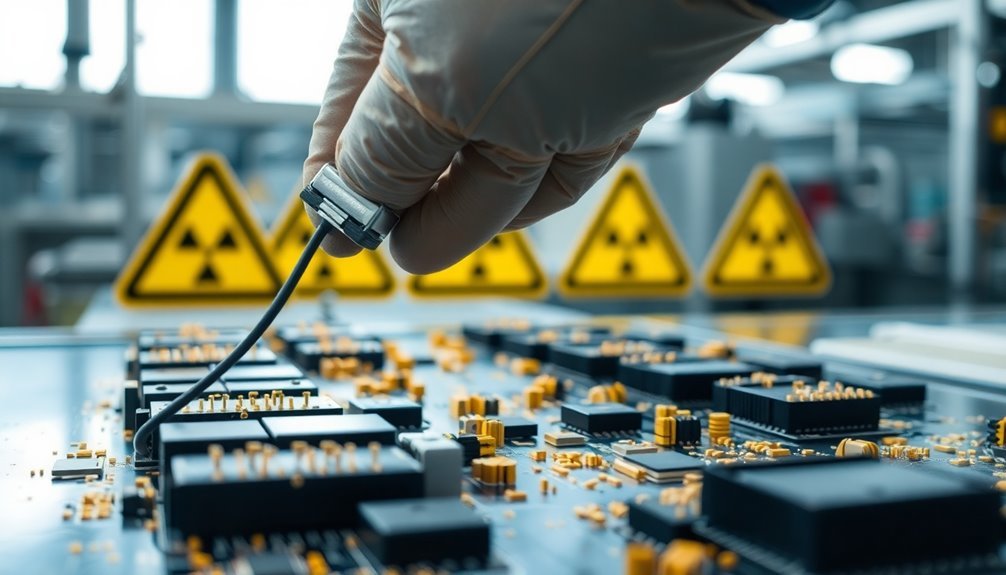
In accordance with industry standards, static control risks pose significant challenges for manufacturing facilities. You'll find that static electricity accumulates through regular factory operations, particularly when your personnel move around and handle materials.
These charges build up more rapidly in environments with low relative humidity, and the use of non-conductive tools only compounds the problem. Friction between surfaces can generate harmful static charges during routine operations.
Your electronic components face serious threats from electrostatic discharge (ESD) events. These incidents can cause immediate damage or, more insidiously, create latent issues that emerge later in your products' lifecycle.
You'll notice that static buildup doesn't just affect electronics – it can also disrupt machinery alignment and contaminate your products.
You need to pay special attention to areas where sensitive components are handled, particularly production lines with insulative surfaces. Your workstations must maintain proper grounding, and you should establish clearly defined Electrostatic Protected Areas (EPAs).
Without these measures, you're risking product quality, reliability, and potentially expensive equipment failures. The key to preventing these issues lies in understanding how static charges develop in your specific operating environment and implementing appropriate control measures.
Workplace Safety Compliance
A thorough workplace safety compliance strategy forms the foundation of your static control program. You'll need to confirm your facility meets OSHA and industry standards to protect against ESD-related incidents and avoid potential liability issues. Remember, you're responsible not just for meeting minimum requirements but exceeding them to maintain a truly safe environment.
Your compliance strategy must include proper identification of ESD-sensitive areas and implementation of essential safety measures. Creating and maintaining high static awareness through posters and regular reminders helps reinforce your safety protocols. You'll need to equip your staff with appropriate anti-static PPE, including conductive clothing, gloves, and boots that meet global standards.
It's essential to verify that all protective equipment effectively dissipates static electricity and prevents charge buildup.
Training plays a critical role in your compliance efforts. You must provide detailed, job-specific education to confirm your personnel understand ESD risks and proper handling procedures.
Your training program should include regular updates and visual reminders throughout your facility. Don't forget to establish protocols for visitors entering your EPAs – they'll need basic ESD awareness and proper instruction on using protective equipment like wrist straps and footwear correctly.
Protecting Electronic Components
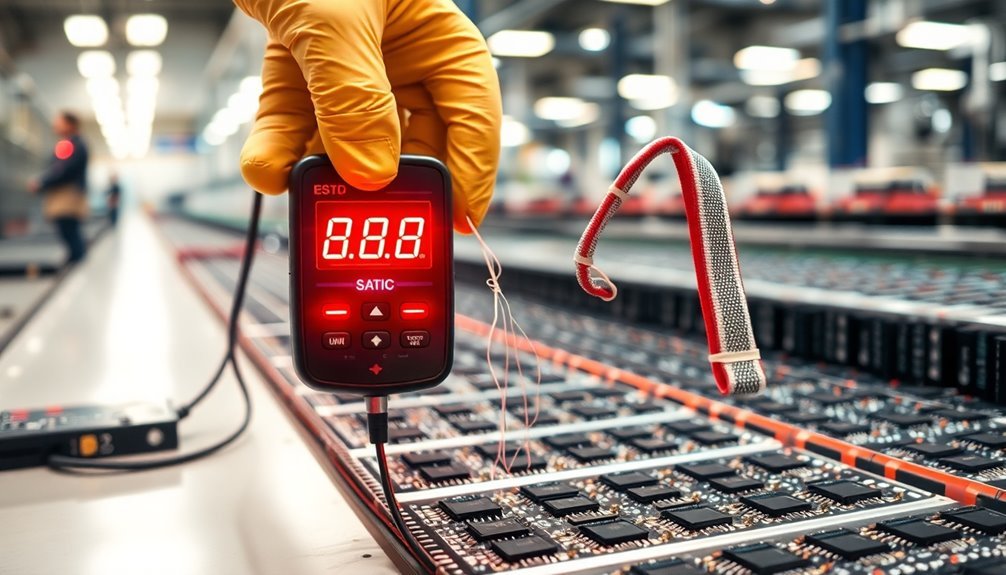
Your factory's electronic components need robust ESD protection measures to prevent both immediate and long-term device failures that can impact your bottom line.
Regular site evaluations help ensure that your ESD control systems remain effective over time through proper measurement and testing.
You'll see significant cost savings by implementing proper grounding systems, using ESD-safe materials, and maintaining controlled environments with appropriate humidity levels.
Given that ESD damage accounts for up to 33% of product losses in the electronics industry, your investment in thorough static control measures will quickly pay for itself through reduced component failures and warranty claims.
Device Failure Prevention Strategies
Protecting electronic components from device failure requires a thorough, multi-layered approach that combines proper handling, design considerations, and preventive controls.
You'll need to start by identifying sensitive components through HBM and CDM ratings, then establish protected areas (EPAs) where these components will be handled. It's vital to implement extensive ESD control measures, including proper grounding systems, antistatic materials, and humidity control. Regular auditing is essential for evaluating the effectiveness of your ESD control program.
Your design strategy should incorporate ESD protection through careful circuit design, proper use of decoupling capacitors, and effective shielding of critical components. You'll also want to guarantee compliance with international standards like ANSI/ESD S20.20 and IEC 61340-5-1 while maintaining strict quality control protocols.
Here are key preventive measures you should implement:
- Use wrist straps and static control garments to bond personnel to ground
- Install continuous monitoring systems for testing wrist straps and work surfaces
- Maintain appropriate humidity levels in your facility
- Conduct regular employee training on ESD handling techniques
Remember to employ thorough failure analysis methodologies and component testing procedures to identify and address potential issues before they cause significant damage to your electronic components.
Cost-Saving Through Protection
Effective ESD protection measures can save you substantial money by preventing costly device failures and warranty claims. Industry data shows that companies lose an average of 6.5% in revenue due to ESD-related issues, making protection not just a technical necessity but a vital business strategy.
You'll find that the cost of implementing ESD safeguards is relatively minimal compared to the potential losses from product recalls and damaged reputation. Electronic manufacturing facilities often rely on ioniser technology to neutralize static charges in sensitive areas.
By establishing ESD-controlled workstations and maintaining proper grounding systems, you're creating a shield against costly electronic component damage. Regular audits help you verify that your protection measures remain effective and compliant with legal requirements.
You'll need specialized equipment like wristband checkers and resistivity meters to guarantee your control measures are working as intended.
Don't overlook the importance of employee training and humidity control in your ESD protection strategy. Your staff needs to understand proper handling techniques, while maintaining appropriate humidity levels helps reduce static electricity in your manufacturing environment.
When you combine these measures with regular testing of electro-conductive components, you'll create a thorough ESD protection system that safeguards both your products and your bottom line.
Daily Monitoring Best Practices
A successful static control program hinges on robust daily monitoring practices that combine various techniques and tools. You'll need to integrate automated systems with real-time data analysis to verify your factory's static control measures remain effective. Regular inspections should be documented and reviewed to highlight any deficiencies requiring immediate attention.
By implementing a risk-based approach, you can prioritize monitoring activities in areas where static discharge poses the greatest threat to your operations and products.
Your daily monitoring strategy should incorporate both static monitoring tools and thorough data logging systems. These tools, such as the FMX for portable monitoring and IQ Power Sensor Bars for continuous line monitoring, will help you maintain ideal static control levels throughout your facility.
Key elements to include in your daily monitoring routine:
- Real-time alerts through integrated control stations to notify you of potential static control failures
- Regular sampling and observation using portable monitoring devices in high-risk areas
- Data analysis of trends to anticipate and prevent static-related issues
- Automated testing schedules that align with your production cycles and risk assessments
Remember to continuously adjust your static neutralizing equipment based on the monitoring data you collect, maintaining optimal performance and protection for your facility.
Equipment Verification Requirements
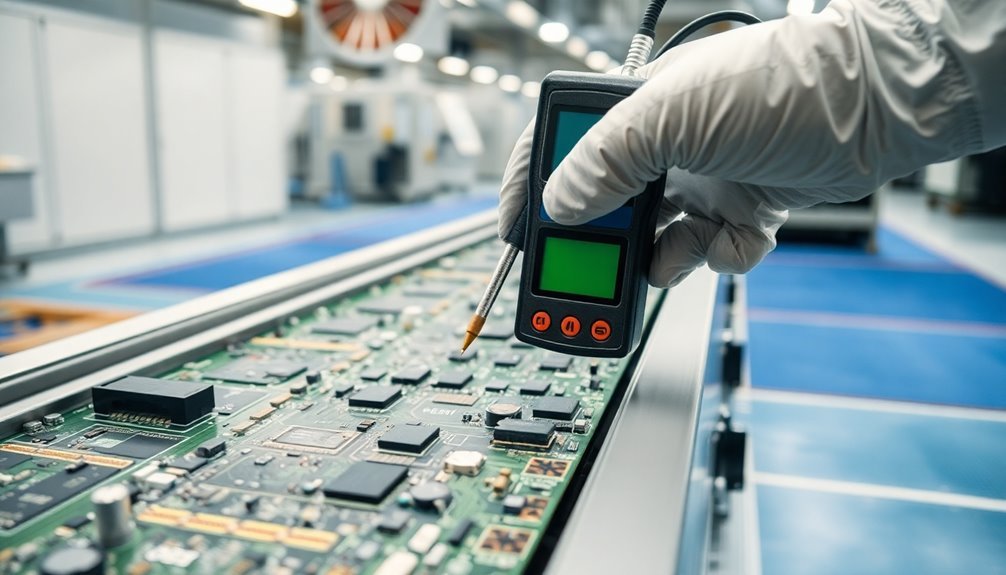
Your static control program requires rigorous equipment verification to maintain its effectiveness and compliance with ANSI/ESD S20.20 and IEC 61340-5-1 standards. You'll need essential instruments like electrostatic field meters, wide-range resistance meters, and ground circuit testers to perform accurate measurements. Don't forget to include charged plate monitors and specialized testers for footwear and wrist straps.
To guarantee reliable results, you should conduct monthly audits using consistent sampling techniques and statistical analysis. It's vital to use detailed checklists and assign a single auditor who'll maintain consistency throughout the verification process. These audits help strengthen management commitment to your ESD control program.
Your audit must cover all areas where ESD-sensitive devices are present. Focus your verification on workplace processes, grounding systems, and ESD control measures. You'll need to check antistatic mats, wrist straps, and footwear while reviewing material flow for potential charge accumulation points.
When you discover deficiencies, implement immediate corrective actions and provide necessary training to your personnel. Make sure you're documenting all audit details – you'll need these records for ISO 9000 or ANSI/ESD S20.20 certification. Track trends in your data to establish effective preventive measures.
Personnel Training and Certification
Training personnel to handle ESD-sensitive components demands a thorough curriculum that meets ANSI/ESD S20.20 and IEC 61340-5-1 standards. Your training program should cover the physics of static electricity, specific organizational ESD control procedures, and each employee's role in maintaining compliance.
You'll need to use diverse training methods, including live instruction, videos, and specialized modules tailored to different job functions.
To guarantee your training program's effectiveness, you'll want to implement continuous assessment and improvement strategies. Track retraining needs, share performance data, and conduct regular evaluations to maintain high standards across all facilities. Don't forget to take into account cultural differences when implementing global training programs.
Here's what your training program should deliver:
- In-depth understanding of static electricity fundamentals and ESD control
- Hands-on experience with measurement tools and compliance verification
- Clear knowledge of individual responsibilities within the ESD Control Program
- Practical skills for using continuous monitoring systems and wrist strap testing
Remember to integrate your ESD certification process with existing quality management systems and maintain regular updates as standards evolve. You'll need to enforce retraining for any non-compliance issues to guarantee ongoing program effectiveness.
Cost Benefits of Regular Audits
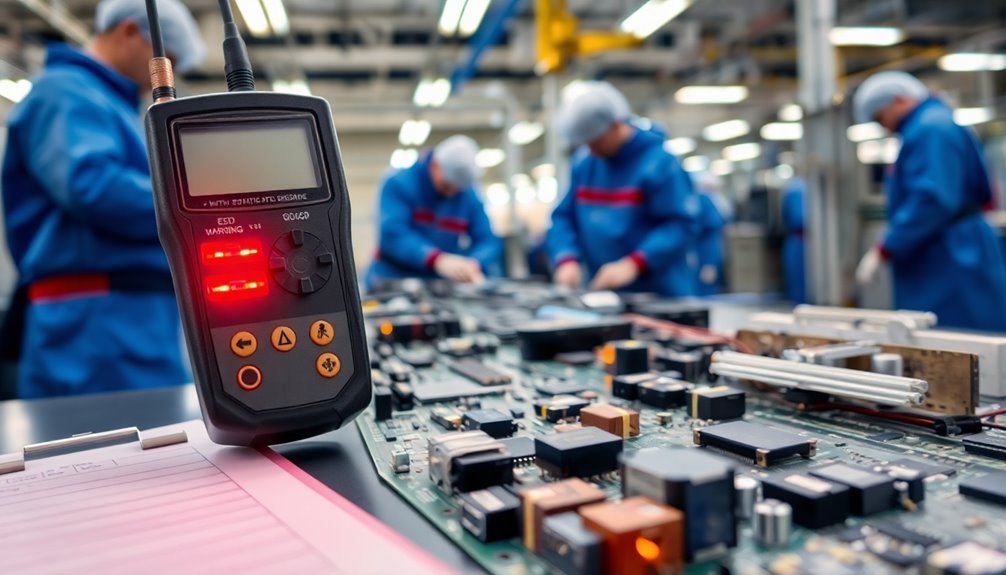
While proper training sets the foundation for ESD control, regular audits deliver substantial financial returns that justify the investment. You'll find that implementing ESD control programs can yield an impressive ROI of up to 1,000%, with every dollar invested potentially saving you $95 in return.
Companies typically report over 50% savings in return and repair costs after initiating these programs.
Your factory's bottom line will benefit considerably from regular audits, as they help identify operational inefficiencies and prevent costly disruptions. By reducing ESD-related costs by 80%, you can add approximately 5% to your profit margin without increasing sales.
Regular audits also guarantee you're complying with ISO 9000 requirements and maintaining customer satisfaction through improved product quality.
The financial impact becomes clear when you consider that ESD damage can lead to quality and reliability failures costing up to $10 million. Through continuous monitoring and analysis, you'll see improved yields, productivity, and capacity.
Your audit program will help identify cost-saving strategies, determine when staff needs retraining, and guarantee your ESD control measures remain effective, leading to decreased scrap rates and increased throughput.
Common Static Control Violations
When you conduct static control audits in factories, you'll often find improper grounding techniques as a major violation, including unbonded equipment and inadequate connections to ground points.
Your inspection will likely reveal missing or incorrectly used ESD protection equipment, such as wrist straps without proper monitoring systems and non-compliant ESD flooring materials.
These fundamental violations can put sensitive electronic components at risk of damage and lead to costly production failures if not addressed promptly.
Improper Grounding Techniques
Improper grounding techniques consistently rank among the most serious static control violations in factory environments. Your facility's grounding systems require grounding resistance of 1 megaohm or less for effective static dissipation, while resistance exceeding 10 ohms in metal systems often indicates a problematic path to ground.
You'll need to guarantee continuous maintenance and inspection of your grounding connections, as dirt, system fatigue, and loose connections can compromise their effectiveness.
You might think that simply connecting conductive equipment pieces or letting containers touch is enough for proper bonding, but that's not the case. Surface coatings and contamination can reduce conductivity, making intentional bonding connections necessary to equalize static charges and prevent dangerous sparking.
Here are critical grounding issues you need to address:
- Non-continuous paths to ground due to deteriorated connections or corrosion
- Insufficient bonding between conductive equipment pieces, even when they're touching
- Lack of regular maintenance checks on grounding and bonding systems
- Improper auxiliary ground connections that aren't properly bonded to equipment grounding conductors
Missing ESD Protection Equipment
Beyond faulty grounding systems, the absence of proper ESD protection equipment represents another major static control violation in manufacturing facilities. You'll find that thorough ESD protection isn't just about having a few wristbands – it requires a complete ecosystem of specialized equipment throughout your product's lifecycle.
From antistatic workbenches to ionizing blowers, each piece plays a vital role in maintaining a static-safe environment.
When you're missing essential ESD equipment, you're exposing your operation to significant risks. Your sensitive electronic components become vulnerable to damage, and you'll likely face increased repair costs and productivity losses.
Without proper ESD-safe packaging, your products remain at risk during transport and storage. The absence of continuous monitors means you can't verify if your existing protection measures are working effectively.
To meet industry standards like JESD625B and IEC-61340-5-1, you'll need to invest in appropriate ESD equipment based on your facility's specific needs. This includes antistatic attire, specialized cleaning chemicals, floor mats, and ionizers.
Implementing Effective Control Measures
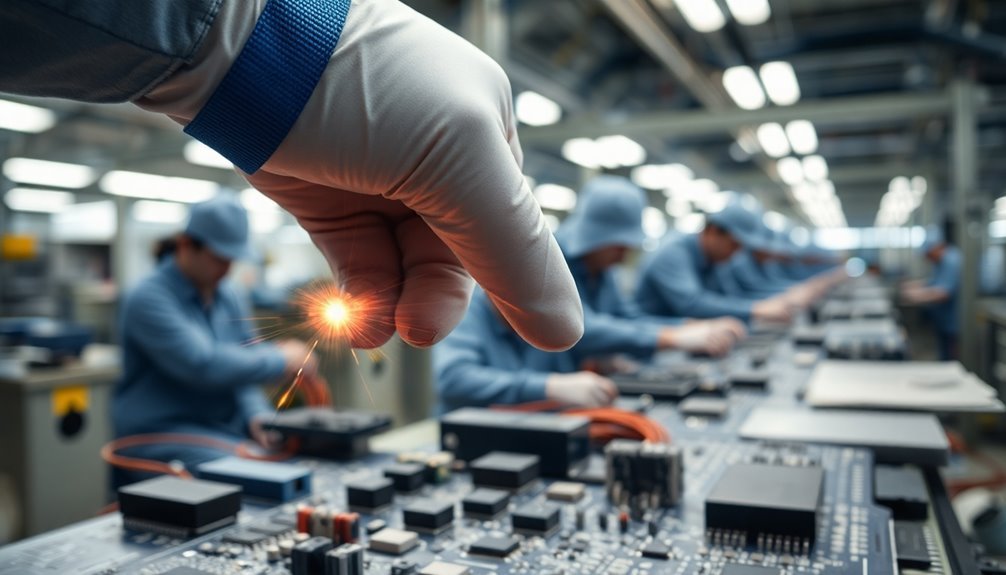
Several critical steps must be taken to implement effective static control measures in factory environments. You'll need to establish thorough grounding systems, integrate ionization technology, and guarantee all employees receive proper ESD safety training. It's crucial to verify that your control measures comply with industry standards like ANSI/ESD S20.20 through regular inspections and testing.
To maintain an effective static control program, you'll want to focus on these key elements:
- Install properly grounded workstations and guarantee all equipment connects to a common ground point
- Set up ionizers in critical areas where static charges pose the highest risk
- Use only ESD-approved materials and equipment throughout your facility
- Document and regularly update all static control procedures and practices
Your implementation strategy should include continuous monitoring and improvement processes. Make sure you're conducting thorough assessments of high-risk areas and designate ESD coordinators to oversee control measures.
Don't forget to leverage technology for data analysis and control testing. Regular audits – whether daily, weekly, or monthly – will help you identify and address potential issues before they become problems.
Consider bringing in third-party auditors annually to guarantee complete compliance with industry standards.
Frequently Asked Questions
How Often Should Static Control Audit Teams Rotate to Maintain Objectivity?
You should rotate your static control audit teams every 2-3 years to maintain objectivity. For lead auditors, consider a 5-year rotation cycle, aligned with common regulatory requirements and best practices in audit management.
Can Remote Auditing Technologies Effectively Replace In-Person Static Control Inspections?
While remote auditing tech can supplement your static control inspections, you'll need a hybrid approach. Remote tools offer cost savings and flexibility, but can't fully replace hands-on physical inspections and interpersonal interactions.
What Weather Conditions Most Significantly Impact Static Control Audit Readings?
You'll find dry, cold weather conditions most substantially affect your static control audit readings, as low humidity and cold temperatures increase static electricity buildup. Winter months typically present the greatest challenges for accurate measurements.
How Do Different Flooring Materials Affect Static Control Audit Requirements?
You'll need to adjust your audit requirements based on each material's conductivity range. Epoxy, rubber, vinyl, and carpet require different testing frequencies and methods to verify their specific static control performance levels.
Should Static Control Audits Be Conducted During Peak Production Hours?
Yes, you should conduct static control audits during peak hours to get accurate assessments of your ESD control practices. It'll reveal real-world compliance and potential issues when production stress is highest.
In Summary
Regular static control audits aren't just about compliance—they're essential for protecting your workers, equipment, and products. You'll minimize costly component damage, prevent workplace accidents, and maintain quality standards by staying proactive. Don't wait for problems to surface; implement thorough static control measures now. With proper training, monitoring, and verification processes, you're safeguarding your factory's operations and bottom line.
Leave a Reply