You'll need to maintain relative humidity levels above 55% RH to completely eliminate static electricity in manufacturing environments. However, most facilities target 40-50% RH as the ideal range to balance static prevention with protecting moisture-sensitive equipment and materials. Lower humidity (below 30% RH) substantially increases static risks, while higher levels can cause corrosion or other moisture-related issues. For electronics and semiconductor manufacturing, staying between 35-45% RH offers the best compromise. To fully protect your facility, you'll want to take into account additional factors beyond just humidity control.
Optimal Humidity Ranges
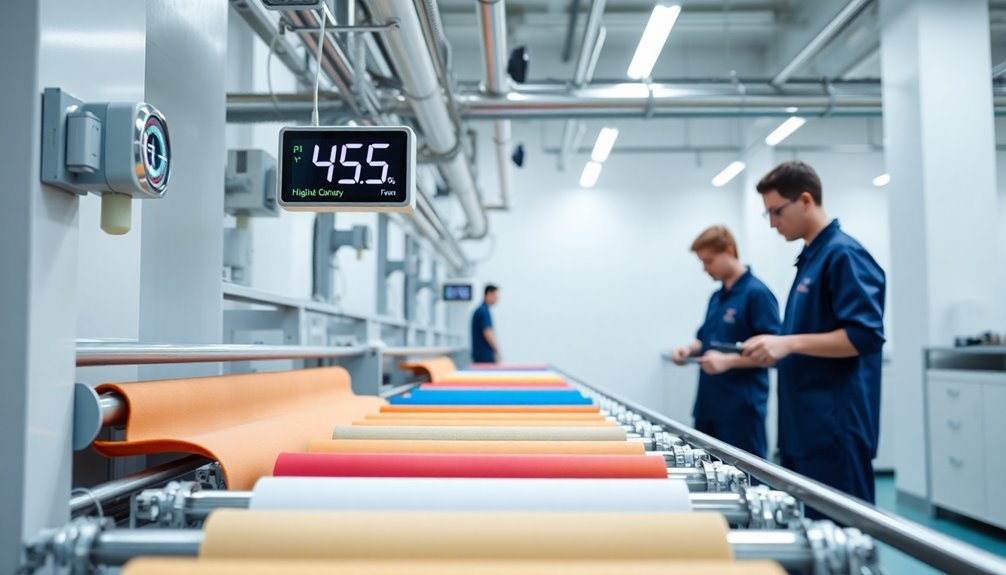
While manufacturing environments can tolerate a broad range of humidity levels, maintaining relative humidity (RH) between 30-70% is essential for static prevention.
You'll find that the ideal range narrows depending on your specific manufacturing needs, with 40-45% RH being particularly effective for semiconductor manufacturing. This range helps you balance moisture control with static prevention. Research by industry leaders like Intel and MIT confirms this range delivers optimal results.
For the best static control, you'll want to keep humidity levels above 55% RH, as this can eliminate static electricity altogether. However, if you're working with electronics or semiconductors, you'll need to be more precise.
In semiconductor assembly and wafer transportation, target 35-45% RH to prevent damage while maintaining adequate static control. For general electronics manufacturing, you can aim for 30-60% RH, though 40-50% RH provides the best balance.
Be aware that humidity below 30% RH substantially increases your risk of electrostatic discharge (ESD). You'll need to pay special attention to areas near heat-generating machines, where localized dry air pockets can create static problems.
If you're dealing with moisture-sensitive processes, like wafer fabrication, you might need to maintain lower humidity levels in specific areas.
Manufacturing Environment Controls
Now that you understand ideal humidity ranges, implementing effective control systems becomes the next priority. You'll need to focus on both facility-wide solutions and localized controls to maintain consistent humidity levels that prevent static electricity.
Start by installing a continuous air barrier throughout your facility, which will minimize uncontrolled air leakage and reduce condensation issues. Regular monitoring of relative humidity levels between 40-60% is essential for maintaining optimal conditions.
You'll want to integrate state-of-the-art air handling systems that include both humidifiers and dehumidifiers. For large spaces, consider using direct room humidifiers that can release fine sprays to quickly adjust humidity levels, particularly around heat-generating equipment that creates dry air pockets.
Don't overlook the importance of proper sealing and insulation – they're vital for maintaining stable humidity levels.
You should also implement modular installations where possible, as they offer flexibility in adjusting humidity levels and easier maintenance access.
For best results, integrate your humidity control system with existing environmental controls and install monitoring equipment to track performance.
Regular inspections and maintenance checks will guarantee your system continues to perform effectively, keeping static electricity at bay and your manufacturing processes running smoothly.
Static Electricity Impact
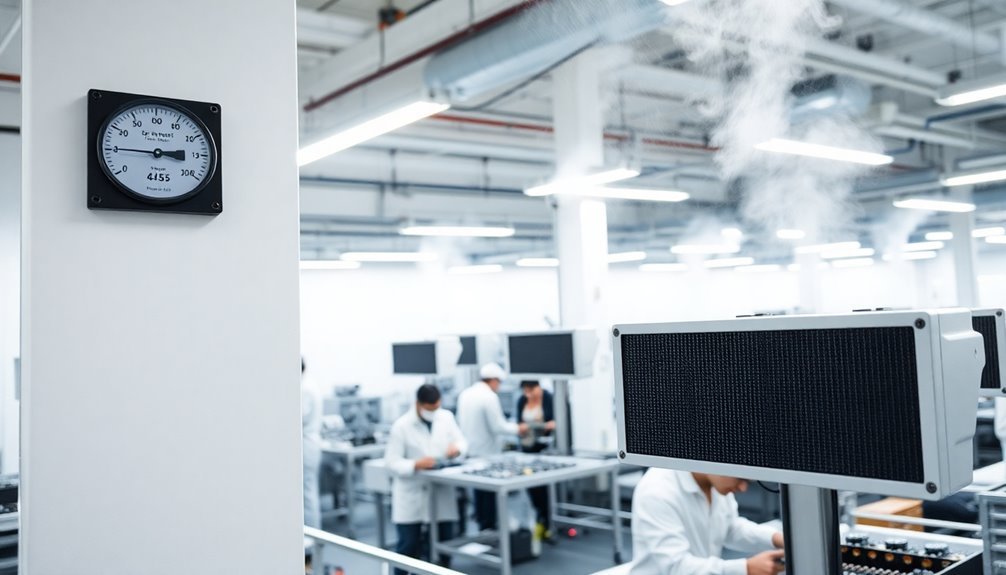
Static electricity poses substantial threats to manufacturing operations across multiple fronts. You'll find it disrupting production quality by causing manufacturing defects, compromising food product sealing, and creating printing issues on DTF machines. Impurities and dust tend to accumulate on surfaces, making cleaning procedures more challenging.
These problems lead to increased scrap rates and considerable product losses that directly impact your bottom line.
Your machinery and equipment aren't immune either. You're likely to experience frequent stoppages and breakdowns due to static charge buildup, particularly in textile operations where fibers stick together and jam machines.
This downtime markedly reduces your production efficiency and overall productivity.
The safety implications can't be ignored. Your workers face shock hazards, especially in areas with high humidity or low conductivity.
There's also the risk of fire from electrostatic discharge, which can trigger dust explosions if proper grounding isn't maintained. These risks require you to implement thorough safety measures and protective equipment.
Your employees' well-being is also at stake. They may experience minor injuries and discomfort from static shocks, affecting their productivity and job satisfaction.
You'll need to address these concerns through proper static control measures to maintain a safe, comfortable working environment.
Humidity Control Methods
Controlling static electricity effectively requires precise management of your facility's humidity levels, and you'll find several proven methods to achieve this control. Each method offers distinct advantages depending on your facility's size and requirements.
The dry fog humidification system stands out as a cost-efficient solution, cutting operating expenses by up to 80% compared to traditional steam systems while maintaining the essential 55% relative humidity needed for static prevention. For precise calibration needs, you'll find the two-pressure method delivers high accuracy, though it's better suited for smaller applications. Installing proper humidity control helps prevent particle adhesion issues that can compromise product quality.
Method | Best Application | Key Advantage |
---|---|---|
Dry Fog | Large spaces | Cost-effective, 80% savings |
Two-Pressure | Small-scale | High accuracy |
Two-Temperature | Medium volumes | Stable (±0.2-0.5%) |
Steam Injection | Industrial | Widespread compatibility |
DX Dehumidification | Large facilities | Precise control |
When you're dealing with larger volume requirements, the two-temperature method provides reliable stability within ±0.5%. For industrial applications, steam injection and DX dehumidification systems offer robust solutions, though they'll require more energy. Consider your facility's size, accuracy requirements, and energy constraints when selecting your humidity control method.
Critical Risk Management
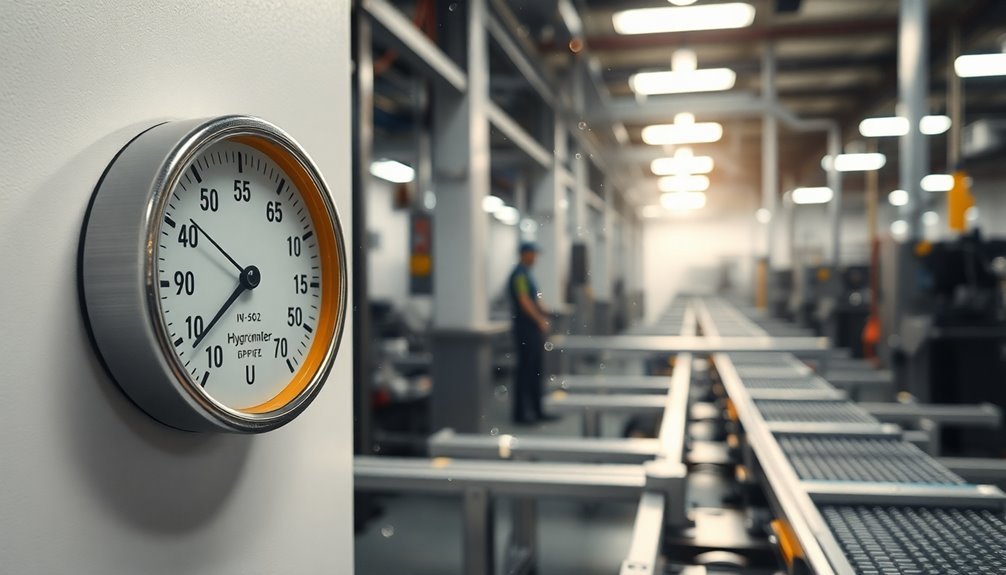
Through effective humidity management, you'll protect your manufacturing process from critical static-related risks that can severely impact productivity and safety.
You'll need to maintain humidity levels between 45-55%RH to minimize static buildup, as levels below 45%RH can generate dangerous static charges through friction.
Be especially vigilant of dry micro-climates created by heat-generating machines, which can form localized pockets of low humidity. The abrasion and peeling between materials in these areas significantly increases static generation. You'll want to monitor these areas closely, as they can compromise your static control efforts even when general facility humidity appears adequate.
Follow industry standards like ESDA's TR20.20-2008 and MIL-STD-1695, which recommend maintaining 30-70%RH for handling electronic components.
You'll need to adjust your humidity control strategy based on your specific industry requirements. For electronics manufacturing, maintain 30-70%RH, while general manufacturing typically requires 40-60%RH.
Remember that your ESD protective materials won't perform effectively in low humidity conditions, so you should test their performance at your facility's lowest expected humidity levels. This testing guarantees your static prevention measures remain reliable throughout your operations.
Frequently Asked Questions
How Quickly Does Static Electricity Dissipate When Humidity Levels Are Increased?
You'll notice static electricity dissipates faster as humidity rises, especially above 40% relative humidity. When you increase moisture levels, the scattering time decreases exponentially, allowing charges to disperse more quickly through conductive surfaces.
Can Different Materials in Manufacturing Require Different Optimal Humidity Levels?
Yes, you'll need different humidity levels for various materials – electronics require 45-60% RH, composites need 40-60% RH, wood processing needs 25-35% RH, and chemical labs function best at 30-45% RH.
What Seasonal Adjustments Should Be Made to Maintain Consistent Humidity Control?
You'll need to adjust your dehumidification strategy between seasons, using rental units during humid months and possibly adding localized spray systems in dry periods. Monitor and maintain 45-55%RH consistently throughout the year.
Does Facility Altitude Affect Recommended Humidity Ranges for Static Prevention?
No, your facility's altitude doesn't directly impact recommended humidity ranges for static prevention. You'll still need to maintain humidity above 45%RH, ideally above 55%RH, regardless of your location's elevation.
How Do Airflow Patterns Influence Static Buildup in Manufacturing Zones?
You'll find that proper airflow patterns reduce static buildup by maintaining consistent air movement. When you optimize flow patterns and minimize impedance, you'll decrease static pressure and prevent charge accumulation in manufacturing areas.
In Summary
You'll need to maintain relative humidity levels between 40-60% to effectively control static electricity in your manufacturing facility. If you're working with sensitive electronics or materials, don't let humidity drop below 30%, as static charges become more prevalent. Keep monitoring your environment and adjust your humidification systems accordingly to protect your products and equipment from static-related damage.
Leave a Reply