Choosing the right static control ionizer depends on your specific workspace and needs. For small areas or targeted protection, consider benchtop or point-of-use ionizers that offer direct coverage. Larger workspaces benefit from overhead units, which provide uniform air distribution when mounted 17-24 inches above the work surface. Your environment's humidity levels and static sensitivity requirements will determine whether you need corona discharge or alpha radiation technology. You'll also want to factor in maintenance requirements, discharge time metrics, and budget constraints. Understanding these key factors will guide you toward the most effective static control solution for your situation.
Understanding Static Control Basics
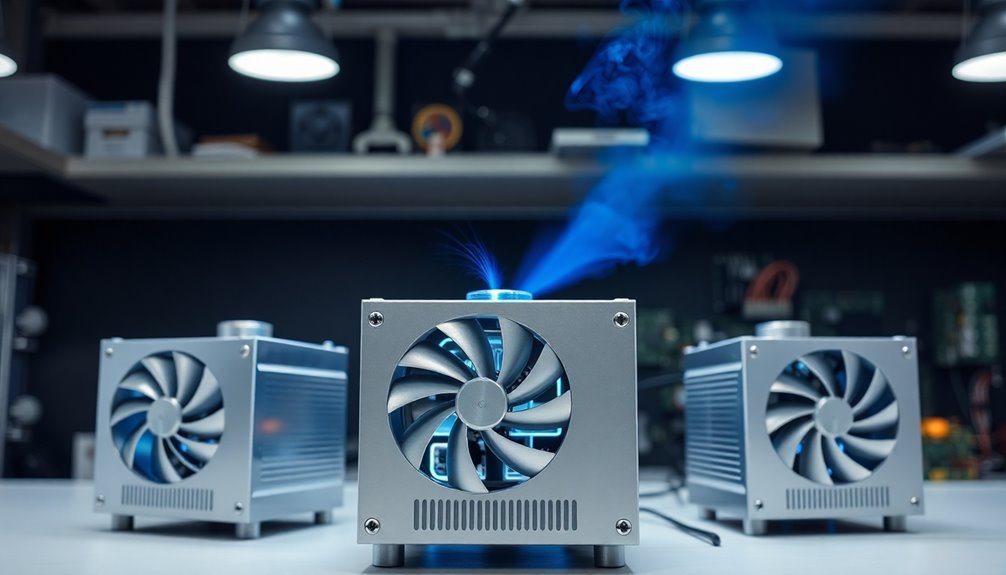
Static electricity poses significant risks in manufacturing and handling of sensitive electronic components. To protect your products and equipment, you'll need to understand the six basic principles of ESD control that focus on eliminating, reducing, dissipating, and neutralizing electrostatic charges.
Your ESD control program must include proper grounding as its foundation. You'll need to guarantee all conductive and dissipative materials connect to a known ground, while personnel should wear properly connected wrist straps to maintain ground potential. The resistance to ground for personnel and footwear must match wrist strap specifications of 35 x 10^6 ohms. Continuous monitoring systems provide real-time verification of wrist strap functionality.
Your equipment, including electrical tools, must connect to the equipment ground for both fault current protection and ESD control.
The materials you choose play an important role in static control. You'll want to use conductive materials (which need grounding) and static dissipative materials for handling sensitive devices. It's vital to avoid insulators in ESD-sensitive areas since they can't discharge through grounding.
Your workstation should feature ESD-safe surfaces and appropriate humidity levels, while your staff should wear ESD-safe clothing to suppress electric fields. Following standards like ANSI/ESD S20.20 and implementing proper workstation configurations will help guarantee thorough static control.
Types of Static Control Ionizers
You'll find two main technologies dominating static control ionization: corona discharge and alpha radiation, with corona being more common in everyday applications.
When choosing between DC and AC corona systems, you'll notice DC offers better ion balance and longer maintenance intervals, while AC provides faster neutralization speeds and simpler electronics. Notably, modern systems can achieve rapid neutralization times of 0.3 seconds.
These fundamental differences in ionizing technologies will shape your choice based on specific application needs, such as neutralization speed, maintenance requirements, and safety considerations. Modern soft X-ray systems provide another effective option for specialized applications where traditional methods may be unsuitable.
Comparing Corona Vs Alpha
When choosing between static control methods, corona and alpha ionizers represent two distinct approaches to neutralizing electrostatic charges.
Corona ionizers use high voltage applied to metal emitters, while alpha ionizers utilize polonium-210's natural radiation to generate ions through air molecule collisions.
You'll find corona ionizers are more common in standard manufacturing environments, particularly in semiconductor packaging and textile applications. Maintaining proper humidity levels between 20-60% non-condensing ensures optimal ionizer performance.
They require fans or compressed air to distribute ions and need regular maintenance to guarantee proper ion balance.
While they're cost-effective initially, you'll need to factor in ongoing maintenance expenses. Alpha ionization provides superior performance by creating zero voltage neutralization through the ionization of oxygen and nitrogen.
If you're working with extreme temperatures (-40°C to 180°C), explosive environments, or tight spaces, alpha ionizers might be your better choice.
They naturally produce balanced ions and don't require balance adjustments.
However, you'll need to take into account regulatory compliance due to their radioactive nature and plan for yearly source replacement as their effectiveness diminishes over time.
Your decision should ultimately depend on your specific needs: environmental conditions, space constraints, maintenance capabilities, and regulatory requirements.
Reflect on whether you need precise ion balance for sensitive components and if you can accommodate the necessary air distribution systems.
DC Vs AC Technologies
Beyond comparing ionization sources, understanding the fundamental differences between AC and DC technologies shapes your choice of static control ionizer. While AC ionizers use transformers to generate both positive and negative ions from the same emitters, DC ionizers employ separate power supplies for each polarity, offering distinct advantages and limitations.
You'll find AC ionizers require higher fan speeds due to significant ion recombination, as they alternate 60 times per second. Their main benefit lies in even emitter wear, reducing replacement frequency. Dirty emitters affect performance but rarely cause complete system failure.
DC technology, available in both steady-state and pulsed variations, delivers superior performance with lower fan speeds and higher ion density. Nuclear ionizers provide an alternative solution for explosive environments where electrical systems pose risks.
When evaluating DC vs AC technologies, consider these key factors:
- Air Flow Requirements – DC units operate effectively at lower fan speeds, while AC needs stronger airflow for peak performance.
- Maintenance Needs – AC emitters wear evenly but DC units require regular monitoring to prevent polarity imbalance.
- Environmental Sensitivity – DC ionizers suit clean rooms and quiet spaces due to lower fan requirements.
- Ion Density – DC technology provides higher ion density and more consistent balance voltage, particularly in steady-state configurations.
The pulsed DC option offers an excellent balance, combining reduced recombination with comfortable airflow levels.
Workspace Size and Layout
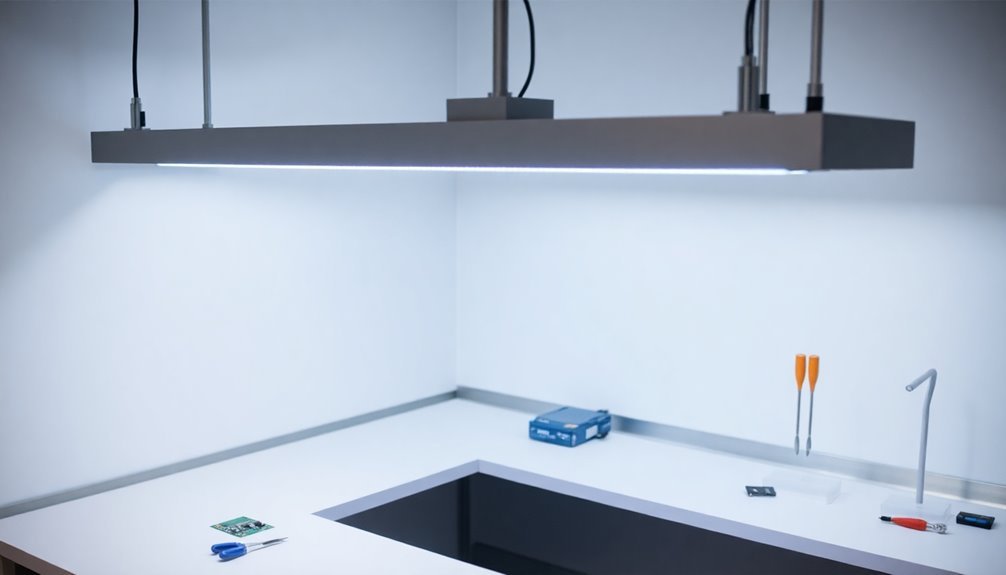
When planning your static control system, you'll need to carefully assess your workspace dimensions to select the right ionizer type and coverage area.
Your space requirements will determine whether you're better served by compact benchtop units for small areas or overhead ionizers for broader coverage.
You can maximize protection by matching the ionizer's effective range to your workspace layout, ensuring critical areas receive appropriate ionization levels.
Space Requirements For Ionizers
Since workspace configurations vary greatly in manufacturing environments, choosing the right ionizer setup requires careful consideration of space requirements and layout options.
You'll find that localized ionizers offer more efficiency than full-room systems, delivering ions directly where you need them with up to 10 times faster performance.
When planning your ionizer installation, consider these key space requirements:
- Overhead ionizers need 17-24 inches of clearance above workbenches to guarantee unobstructed ion flow and ideal coverage.
- Bar ionizers can treat areas up to 2500mm wide and work well in confined spaces, as their controls and power supply can be mounted separately.
- Room ionization systems require emitter placement just below ceiling height and depend on air movement, making them less efficient for targeted static control.
- Point-of-use ionizers provide flexibility for changing production layouts while maintaining effective static elimination in specific areas.
Your maintenance needs will vary based on placement choice. Localized systems are easier to maintain and relocate compared to full-room installations.
Remember that all ionizers require periodic emitter cleaning to prevent contamination and maintain ideal performance.
Optimal Coverage Planning
Planning ideal ionizer coverage requires a thorough assessment of your workspace dimensions and layout configurations. You'll need to evaluate whether you're protecting a single workstation or an entire room, as this directly impacts your ionizer selection and placement strategy.
Coverage Type | Specifications | Benefits | Best Application |
---|---|---|---|
Localized Workstation | 16" x 24" for ion guns | 10x faster performance | Precise area protection |
Benchtop Systems | Workspace-specific | Direct protection | Unobstructed workbenches |
Overhead Units | Full bench coverage | Uniform air distribution | Space-limited stations |
Room Systems | Large area coverage | Wide-range protection | Laminar flow environments |
When mapping out your coverage plan, you'll want to prioritize localized ionization for critical areas, as it delivers more effective static control compared to room-wide solutions. If you're working with limited bench space, overhead ionizers provide consistent coverage without consuming valuable work surface area. For specialized tasks like PCB assembly, point-of-use options like ion guns give you the flexibility to target specific areas while maintaining ideal performance. Remember to account for any obstacles or equipment that might interfere with airflow paths when planning your ionizer placement.
Static Sensitivity Requirements
Static sensitivity's demanding nature requires specific ionization solutions across various industries and applications.
When you're working with semiconductors, plastics, or textiles, you'll need to carefully evaluate your static control requirements, especially in environments with relative humidity below 30%.
Your choice of ionizer type directly impacts its effectiveness in controlling static charges.
Corona ionizers work well for most standard applications, while alpha ionizers excel in extreme conditions or when handling highly sensitive components.
You'll find that AC ionizers provide balanced ion generation, though pulsed DC systems often deliver better performance by reducing ion recombination.
Consider these critical factors when selecting your static control solution:
- Workspace configuration – Choose overhead ionizers for limited spaces and benchtop units for flexibility
- Environmental conditions – Select alpha ionizers for extreme temperatures or specialized environments
- Product sensitivity level – Opt for precision ionizers when handling highly sensitive components
- Maintenance requirements – Factor in regular balancing and cleaning needs, especially for corona-based systems
Your specific application's requirements, including dust presence, temperature variations, and workspace constraints, will ultimately determine the most suitable ionizer configuration for your static control needs.
Performance Metrics That Matter
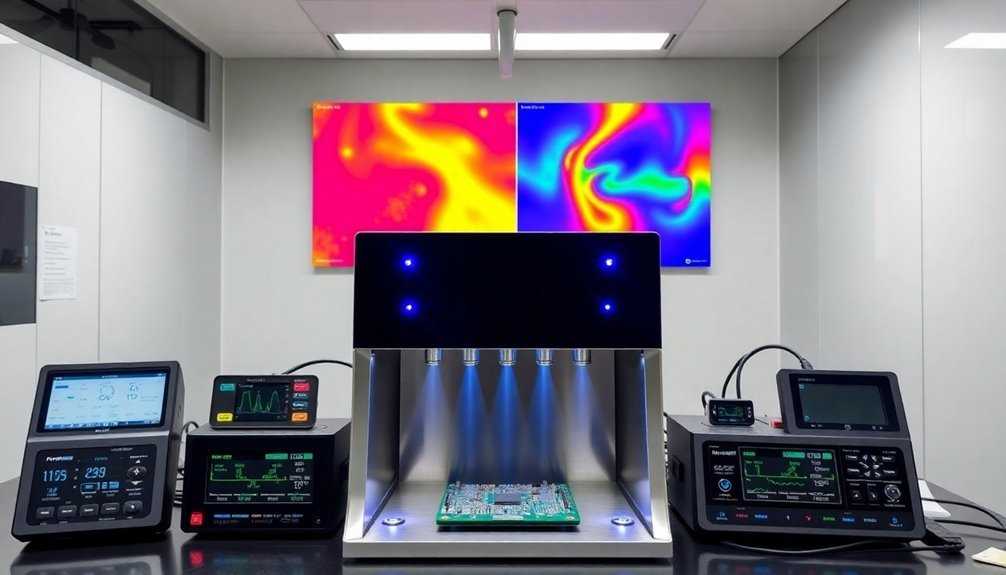
Performance evaluation of ionizers hinges on two critical metrics: discharge time and offset voltage. You'll need to measure how quickly your ionizer can neutralize static charges and how well it maintains ion balance to guarantee effective static control in your application.
To measure these metrics, you'll want to use a Charged Plate Monitor (CPM) that complies with ANSI EOS/ESD S3.1 standards. The CPM uses a 6" x 6" plate to measure discharge time from 1000V to 100V and monitors offset voltage, which should typically stay within ±35V.
When testing, you'll charge the plate to 1000V and measure the time it takes to discharge to 10% of the initial voltage.
Be aware that your testing equipment has limitations. CPMs aren't designed for low voltage measurements below 5V, and fieldmeter sensor bandwidth can affect accuracy. You'll need to take into account specific test conditions, including proper distances and air volume.
For critical applications like MR head production, you might want to explore high-performance options like Polonium 210 alpha ionizers, which provide inherently balanced ion output and reliable zero balance verification.
Maintenance and Operating Costs
Smart manufacturers know that maintaining ionizers doesn't have to break the bank. With advanced features like self-cleaning technology and automatic emitter point cleaners, you'll find that modern ionizers can greatly reduce your maintenance burden and operating costs.
Models like the Ptec IN5500 and those with CoreStat technology offer long-term stability and programmable cleaning cycles that minimize downtime.
When selecting an ionizer, consider these critical cost factors:
- Initial investment vs. life cycle costs – Look for energy-efficient models that offer maintenance-free operation
- Automated cleaning features – Self-cleaning systems can save thousands in labor costs and reduce production interruptions
- Maintenance intervals – Choose models that align with EIA-625 standards but offer flexibility for your specific needs
- Performance monitoring – Opt for units with built-in notification systems that alert you when maintenance is required
You'll want to focus on ionizers that combine automated maintenance features with long service life, like the KEYENCE SJ-F700 series.
These units protect your ESD-sensitive components while keeping your maintenance costs low.
Remember that proper maintenance isn't just about cost – it's about ensuring consistent performance and protecting your production process.
Safety and Compliance Standards
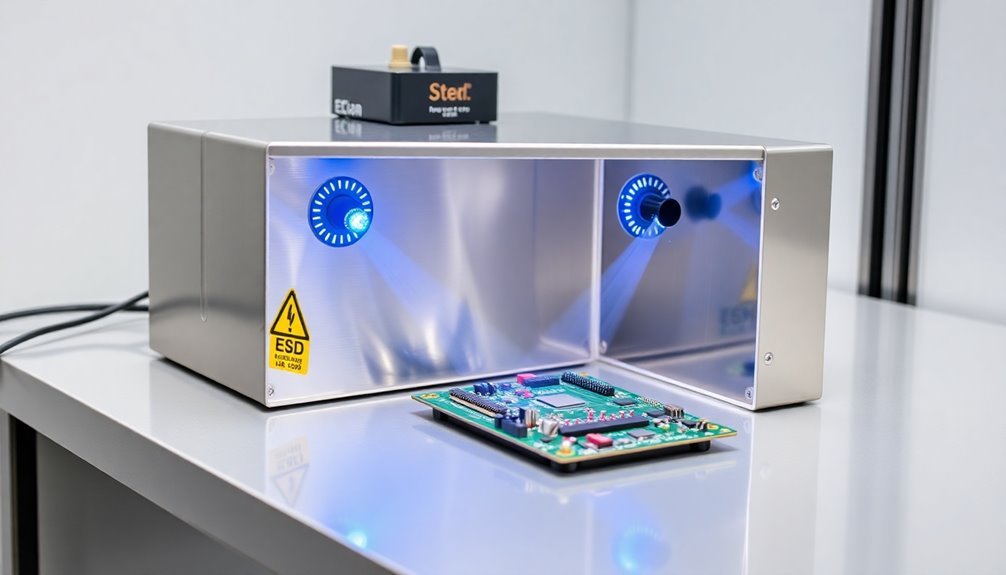
With workplace safety becoming increasingly regulated, understanding ionizer compliance standards is vital for protecting both personnel and sensitive electronics.
You'll need to verify your ionizers meet key standards like ANSI/ESD S20.20, NFPA 77, and IEC 60079, which provide essential guidelines for ESD control programs and static electricity management.
Your ionizers must maintain an offset voltage below +/-35 volts and achieve specified discharge times to comply with ANSI/ESD STM3.1. This means you'll need to implement regular testing and maintenance schedules to verify performance.
Don't rely solely on room ionization, as it may not provide adequate protection for all applications.
You'll also need to take into account proper placement of your ionizers within ESD safety zones and verify they're compatible with your specific environment, especially in cleanrooms.
Remember to establish thorough grounding and bonding procedures alongside your ionization system.
To maintain compliance, you must regularly clean and test your ionizers, document their performance, and address any failures immediately.
Environmental Factors to Consider
You'll find that environmental humidity greatly impacts your ionizer's performance, with levels below 30% requiring particular attention to maintain effective static control.
Your facility's temperature and humidity conditions directly affect ion generation and distribution, making it essential to monitor and maintain appropriate environmental parameters.
The physical layout of your workspace also matters, as you'll need adequate clearance for proper ion distribution and sufficient space to accommodate either room ionization systems or localized workstation units based on your specific requirements.
Temperature and Humidity Impact
Environmental conditions play a vital role in static control ionizers' performance and effectiveness. Temperature and humidity variations can notably impact your ionizer's ability to neutralize static charges effectively.
When selecting an ionizer, you'll need to take into account both your facility's typical environmental conditions and any extreme scenarios your equipment might face.
Your operating environment's temperature range is particularly important for proper ionizer selection. While standard ionizers work well in typical conditions (23°C ± 2°C), some applications require more robust solutions. The 4612 Ionizer, for instance, can handle temperatures from -50°C to +150°C, making it suitable for extreme environments.
Take into account these vital environmental factors when choosing your ionizer:
- Operating temperature range – Verify your ionizer can handle your facility's temperature extremes, especially if you're working with high-temperature processes.
- Humidity levels – Low humidity environments increase static generation, so you'll need more effective ionization.
- Environmental adaptability – Look for closed-loop control systems that can adjust to changing conditions.
- Compliance requirements – Your ionizer must meet industry standards like IEC 61340-4-7 for your specific environment.
For peak performance, consider ionizers with external sensors and self-balancing technology to maintain consistent operation despite environmental fluctuations.
Space and Layout Requirements
Determining your facility's space and layout requirements stands as a vital first step in implementing an effective static control system. You'll need to evaluate whether a full-room or localized ionization solution best suits your needs based on your workspace configuration.
Space Type | Best Ionizer Choice | Key Benefits | Factors to Ponder |
---|---|---|---|
Large Production Areas | Full-Room Systems | Complete coverage, uniform protection | Higher costs, slower decay times |
Workstations | Benchtop/Overhead | Targeted protection, flexibility | Must maintain clear ion path |
Assembly Lines | Ion Bars | Fits confined spaces, customizable lengths | Regular emitter cleaning needed |
Mini-Environments | Localized Units | Cost-efficient, precise control | Limited coverage area |
When planning your layout, you'll want to contemplate overhead ionizers for space-restricted workstations where maintaining an unobstructed ion flow is vital. If you're working with multiple stations, benchtop ionizers offer mobility and adaptability. For confined spaces, ion bars provide an effective solution that won't interfere with your operations. Remember that proper placement is essential – keep the path in front of your ionizers clear and maintain regular cleaning schedules for ideal performance.
Power Source Options
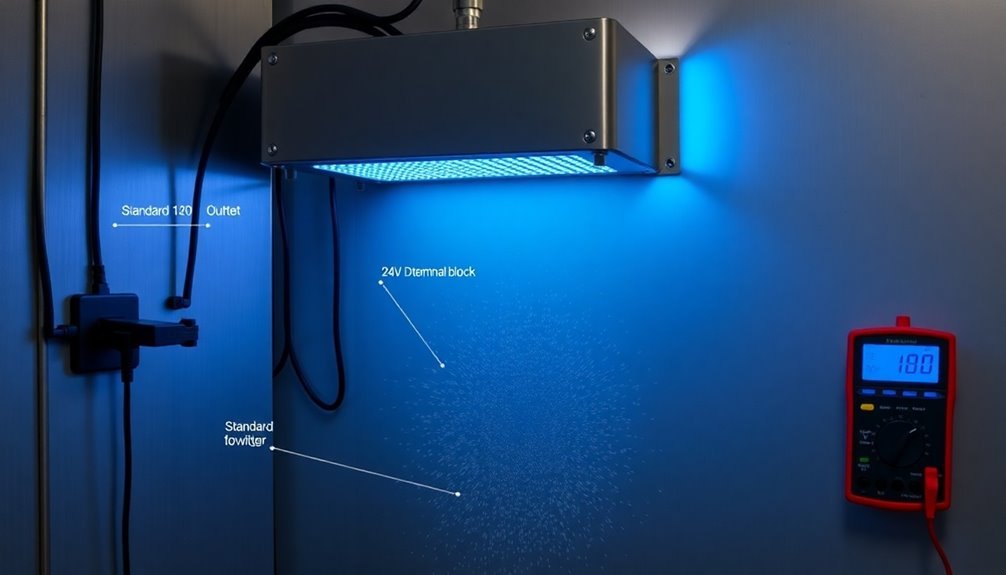
In accordance with static control requirements, ionizers can be powered through several distinct methods: AC power, DC power, non-electrical sources like alpha ionization, or integrated/external power supplies. Your choice depends on your specific application needs and environmental constraints.
You'll find each power source offers unique advantages. AC ionizers use alternating current that cycles 60 times per second, providing evenly worn emitter points but requiring additional airflow for effectiveness.
DC ionizers come in steady-state and pulsed versions, delivering higher ion density and reduced recombination rates – perfect for controlled static environments.
- Choose AC power when you've got consistent airflow available and need low maintenance emitter points.
- Select DC power if you're working with sensitive electronics and require minimal ion recombination.
- Consider alpha ionization when you need balanced ionization without electrical interference.
- Opt for integrated or external power supplies based on your installation flexibility requirements.
For specialized applications, you can use solutions like the IZN Nozzle Ionizer with DC power or fan ionizers with AC adapters.
If you're working with sensitive electronics, alpha ionization sources like polonium 210 provide balanced ionization without voltage swings.
Air Movement Requirements
Air movement plays an essential role in effective static control ionization. You'll need adequate airflow to distribute ions from the ionizer to your target area, regardless of which type of ionizer you choose.
When selecting an ionizer, consider how you'll achieve this necessary air movement – either through integrated fans or existing environmental airflow systems.
If you're working in a general workspace, you might opt for ionizers with built-in fans. However, if you're operating in a cleanroom or laminar flow hood, you'll need to guarantee your ionizer works compatibly with existing air handling systems while maintaining required cleanliness standards.
The type of ionizer you select will influence your air movement requirements. Steady-state DC ionizers need consistent airflow to distribute ions effectively, while pulsed DC systems can operate with reduced airflow.
If you're using compressed gas or alpha ionizers, you'll need to plan for directed air movement to carry ions to their targets.
Remember that humidity levels and airflow speed can impact your ionizer's performance. You'll want to maintain proper air movement to guarantee balanced ion distribution and effective static charge neutralization throughout your work area.
Installation and Setup Process
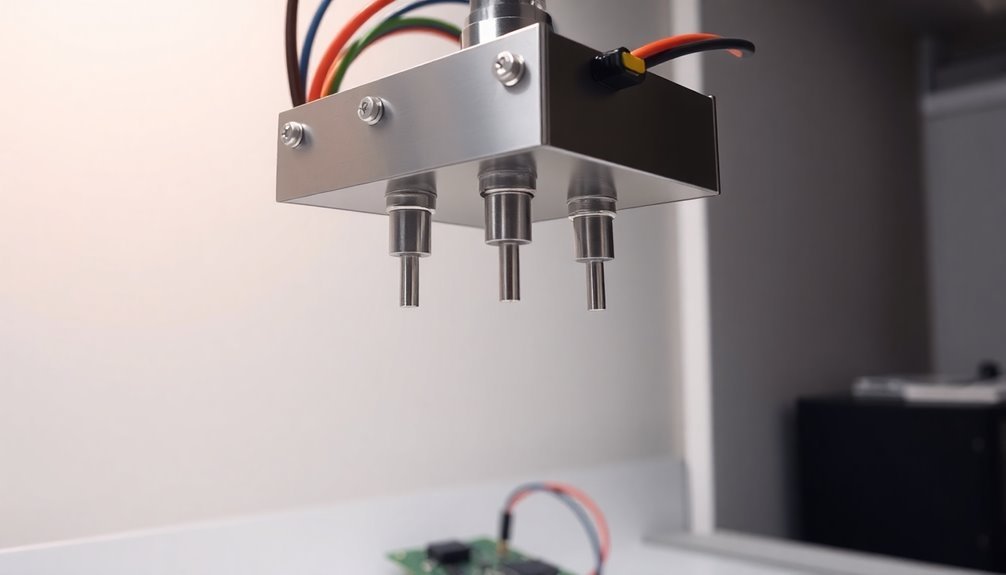
Proper installation and setup lay the foundation for effective static control ionization. You'll need to carefully position your ionizer where airflow isn't restricted and guarantee it's properly grounded using the included wire.
Before plugging the power cord into an AC source, verify that the ON/OFF switch is in the OFF position and confirm the power source matches your unit's voltage requirements.
For peak performance, direct the airflow towards your target neutralization areas using the tilt lock knobs. Once positioned, you'll need to complete these essential setup steps:
- Execute a cleaning cycle to guarantee your emitter points are free from debris.
- Check for any potential blockages that could impair airflow.
- Set the fan speed according to your neutralization requirements.
- Use a charge plate monitor to verify performance and offset voltage.
Remember to maintain proper grounding of all conductors and static dissipative materials throughout the setup process.
You should only proceed with internal adjustments if you're qualified to do so. Regular monitoring for alarms is critical, as they'll indicate issues like abnormal high voltage or fan obstruction that require immediate attention.
Budget and Long Term Value
Making a smart investment in static control ionizers requires careful consideration of both immediate costs and long-term value. With initial prices ranging from $558.58 to $808.00, you'll need to weigh these upfront costs against potential savings from preventing static damage and improving production efficiency.
When evaluating long-term value, focus on the ionizer's durability and performance consistency. Look for units with proven track records of 10+ years and guarantee they comply with ANSI ESD S20.20-2021 standards.
Consider maintenance requirements, including emitter point cleaners and replaceable parts, as these affect your total ownership cost.
You'll want to calculate your return on investment by factoring in static damage prevention, increased productivity, and quality improvements. Don't forget to include ongoing expenses like maintenance, replacement parts, and energy consumption in your calculations.
Compare different types of ionizers – overhead, benchtop, and handheld – to find the most cost-effective solution for your needs.
Consider your budget's flexibility for future upgrades and whether the ionizer can be easily relocated as your production needs change. A thorough warranty and reliable manufacturer support can greatly enhance your investment's value.
Frequently Asked Questions
Can Ionizers Be Used Alongside Humidity Control Systems Without Interference?
Yes, you can use ionizers alongside humidity control systems without any interference. They work independently of each other, with ionizers neutralizing static charges while humidity systems manage moisture levels in your environment.
How Do Ionizers Perform When Exposed to Electromagnetic Fields From Nearby Equipment?
You'll find AC ionizers are more susceptible to electromagnetic interference than DC or Alpha types. For best performance near equipment generating electromagnetic fields, choose DC ionizers and use proper shielding and grounding methods.
What Happens if an Ionizer's Emitter Points Become Contaminated During Operation?
When your ionizer's emitter points get contaminated, you'll notice reduced ion production, decreased static elimination effectiveness, and potential system failure. You'll need regular cleaning to maintain peak performance and prevent further issues.
Do Different Cleaning Chemicals Affect the Performance of Ionizer Components?
Yes, cleaning chemicals can greatly impact your ionizer's performance. You'll need to avoid conductive chemicals and harsh solvents that can damage emitter tips, transformers, and other components. Use non-ionic detergents for safe cleaning.
Can Multiple Ionizer Technologies Be Combined for Enhanced Static Control Effectiveness?
Yes, you can combine multiple ionizer technologies to achieve better static control. By integrating different systems like corona and compressed air ionizers, you'll get enhanced coverage, flexibility, and improved effectiveness in your workspace.
In Summary
Choose your static control ionizer by carefully evaluating your workspace dimensions, ESD sensitivity levels, and air delivery needs. You'll want to match the ionizer's performance specs to your specific requirements while staying within budget. Don't forget to factor in installation complexity and long-term maintenance costs. Whether you select benchtop, overhead, or in-tool ionizers, prioritize reliable static elimination that protects your sensitive components.
Leave a Reply