You'll need to follow specific testing protocols to evaluate static control packaging materials properly. Start by calibrating your testing equipment, including surface resistance meters and static decay testers, to guarantee accurate measurements. Maintain strict environmental conditions (23°C ± 3°C, 12% RH ± 3% RH) and condition materials for 48 hours before testing. Conduct surface resistance tests using appropriate voltage levels: 10V for conductive materials and 100V for dissipative materials. Document all results systematically to maintain compliance with ANSI/ESD S541 standards. The following guide will equip you with thorough testing methods to guarantee your packaging meets industry requirements.
Understanding Static Control Testing Standards
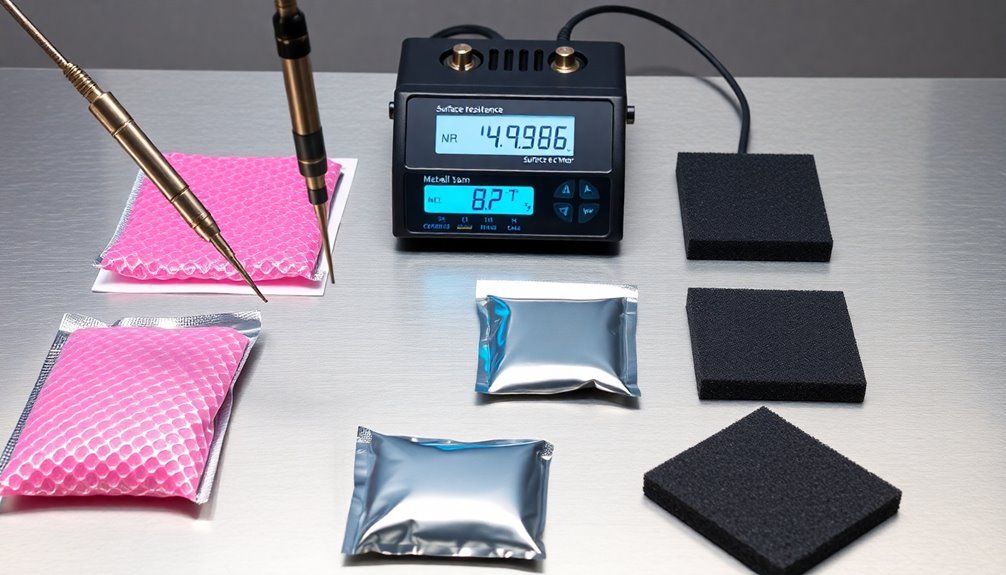
Several vital standards govern the testing of static control packaging materials, with ANSI/ESD S541 serving as the primary framework. To guarantee reliable results, you'll need to conduct all tests under specific conditions: 12%±3% relative humidity and 73±5°F (23°C±3°C), maintaining these conditions for at least 48 hours.
When you're working with static control packaging, you'll find materials classified into three categories: conductive, static dissipative, or insulative, based on their electrical resistance properties. You'll need to verify that all packaging materials carry proper traceability markings, including manufacturer information and date or lot codes. Regular audits enhance the effectiveness of your ESD control program by ensuring continuous compliance with established standards.
It's imperative that you rely on accredited laboratories for your testing needs, as they'll follow standardized procedures that guarantee consistent, reliable results. Advanced instrumentation helps ensure testing accuracy and repeatability across different lab facilities.
If you're operating globally, you'll also need to take into account international standards like IEC 61340. You must verify that your packaging meets the requirements for ESD Protected Areas (EPAs) and maintains compliance with all relevant standards.
Regular verification testing isn't optional – it's vital for maintaining the integrity of your ESD control program and preventing the use of counterfeit materials.
Surface Resistance Measurement Techniques
You'll need specific testing equipment, including a surface resistance meter and properly sized electrodes, to accurately measure static control properties of packaging materials.
The setup must include careful placement of the electrode assembly on specimen samples that are at least 3" x 5" in size, with consistent pressure and proper contact. For optimal measurement accuracy, use equipment with ASTM parallel bar sensing technology.
Testing methods typically follow standardized procedures outlined in ANSI/ESDA and ASTM specifications.
Your measurements will be greatly influenced by environmental conditions, so you must maintain controlled temperature and humidity levels (23° C ± 3° C and 12% RH ± 3% RH) throughout testing to guarantee reliable results.
Testing Equipment Setup Steps
Proper equipment setup stands as the foundation for accurate surface resistance measurements of static control packaging materials. You'll need to start by selecting the appropriate testing equipment, such as ESD audit kits, handheld two-point resistance testers, or resistive meters, depending on your specific testing requirements. Similar to friction and peel testers, precise calibration and setup are essential for reliable data collection.
Before beginning any measurements, you must prepare your testing environment. First, eliminate potential sources of static electricity that could interfere with your readings. Clean your test surface thoroughly to remove any contaminants that might affect the results. Consider using Staticide solutions to ensure your testing surface remains free of static buildup.
Next, calibrate your measurement device according to the manufacturer's specifications, ensuring you've selected the correct probes and fixtures for your material type.
Once you've prepared your equipment, conduct a pre-test to verify that everything's functioning correctly. You'll want to position your probes at the specified distances according to ANSI/ESD S20.20 standards. Remember to check that all connections are secure and that your voltage settings match the testing requirements.
Don't forget to prepare your documentation system for recording measurements, as you'll need to track both resistance to ground and point-to-point resistance values for detailed analysis.
Environmental Impact on Readings
While conducting surface resistance measurements, environmental conditions play a critical role in obtaining accurate and repeatable results. You'll need to maintain temperature between 5-50°C and relative humidity between 0-90%, guaranteeing non-condensing conditions throughout your testing process. High accuracy meters provide the most reliable results for quality assurance.
It's essential that you select the appropriate voltage for your materials: 10V for conductive, 100V for dissipative, and higher voltages for insulative materials.
When taking measurements, you'll need to account for electrification time, particularly with high-resistance materials that require longer stabilization periods. Your meter's accuracy tolerances, typically ±10% with ±5% repeatability, will affect your final readings.
You should maintain constant voltage during testing, as voltage drops can lead to inaccurate results. Remember to regularly clean your probes and calibrate your equipment against known standards to guarantee measurement reliability.
Following these environmental controls will help you comply with ASTM and ANSI/ESD STM11.11-2015 standards while achieving consistent, reliable measurements.
Volume Resistance Testing Protocols
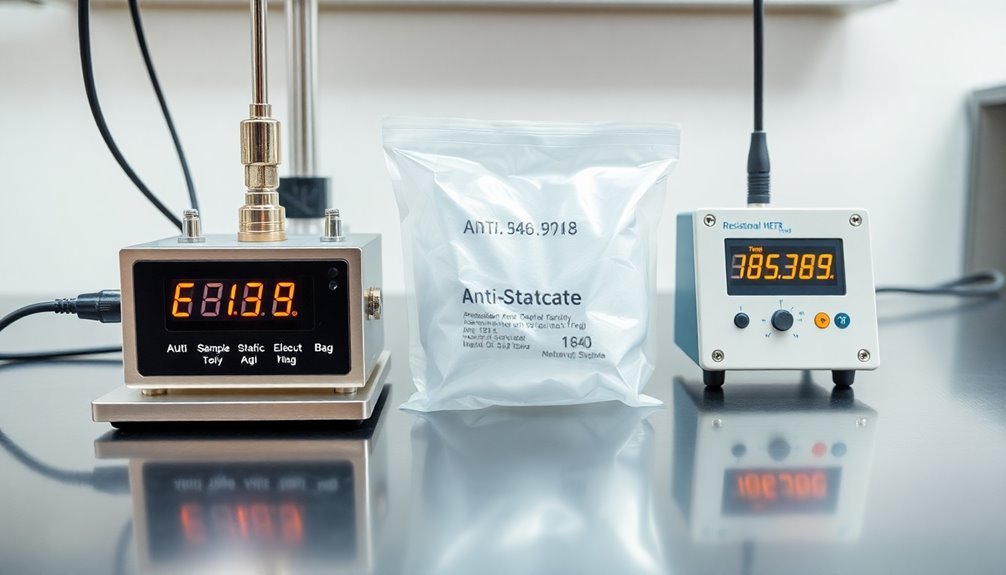
Before you begin volume resistance testing, you'll need to properly set up and calibrate your electrometer and concentric ring fixture according to ANSI/ESD STM11.12 standards.
You must then condition your test specimens in a controlled environment of 12%±3% RH and 73°F±5°F for a minimum of 48 hours. Implementing a systematic quality control checklist helps ensure consistent and reliable test results.
Periodic verification of incoming materials is essential to prevent counterfeit packaging from entering your testing process. Your measurements and data recording should follow strict protocols, using the calibrated equipment to measure resistance from the inside of the material to the test plate, ensuring all results fall within the compliance threshold of <1.0 x 10^11Ω.
Equipment Setup and Calibration
Through rigorous standardization, volume resistance testing demands precise equipment setup and calibration procedures as outlined in ANSI/ESD STM11.12. You'll need to properly configure your concentric ring fixtures and electrometers according to these standards to guarantee accurate measurements of static control materials.
Before beginning any tests, you must calibrate your equipment using a reference measurement of 1.0 x 10^12 Ω. This calibration step is vital for maintaining compliance and guaranteeing reproducible results. You'll need to verify that both your electrometers and concentric rings meet the calibration requirements specified in the standard.
Your testing environment requires strict control, with conditions maintained at 12%±3% relative humidity and 73°F±5°F. You must precondition your samples in this environment for a minimum of 48 hours, and it's essential that you don't remove them from the chamber during evaluation.
When setting up your equipment, guarantee that all components are properly connected and functioning within specified parameters. Your measurement accuracy depends heavily on proper equipment setup and calibration, which directly impacts your ability to classify materials based on their volume resistance properties and guarantee effective ESD protection.
Conditioning Test Specimens
For accurate volume resistance testing, proper specimen conditioning stands as a critical foundation. You'll need to maintain specimens at 12%±3% relative humidity and 73°F±5°F for a minimum of 48 hours before testing. These specific conditions guarantee your materials reach stability, leading to consistent and reliable test results.
When you're conducting volume resistance tests according to ANSI/ESD STM11.12, you must keep specimens in the controlled environment throughout the testing process. Moving them to different conditions can compromise the accuracy of your measurements. The test will determine how effectively your materials can dissipate static charges when used in an ESD Protected Area.
You'll measure volume resistance through the material's thickness using appropriate test fixtures. To maintain compliance, you must follow the standard testing protocols precisely, as any deviations can produce unreliable results.
Remember that your testing should ideally be performed at accredited laboratories to guarantee integrity and accuracy. By maintaining strict adherence to these conditioning requirements and testing procedures, you'll generate reproducible results that accurately reflect your static dissipative materials' performance against ANSI/ESD STM11.12 standards.
Measurement and Data Recording
The measurement and recording of volume resistance data demands meticulous attention to protocol compliance. You'll need to conduct your testing in strict accordance with ANSI/ESD STM11.12 standards, using a calibrated concentric ring fixture to measure the volume resistance from the inside of the bag to the plate.
During testing, you must maintain environmental conditions at 12%±3% relative humidity and 73±5°F. To guarantee accurate results, you'll want to keep your specimens in the test chamber throughout the measurement process.
When you're taking measurements, focus on achieving a volume resistance reading below 1.0 x 10^11 Ω, as this is the defined acceptance criterion. You should record each measurement systematically for your compliance assessment.
Your test report needs to include detailed data analysis and clear conclusions about the material's performance. You'll want to document all relevant measurements, environmental conditions, and any deviations from standard protocols.
Remember that these results directly impact material qualification and selection decisions, so maintaining precision in your measurement and recording procedures is essential for guaranteeing reliable static control packaging performance in EPA environments.
Electrostatic Decay Test Methods
While protecting sensitive electronic components remains vital in modern manufacturing, electrostatic decay testing serves as an important method for evaluating packaging materials' ability to dissipate static charges. You'll need to follow specific standards like MIL-STD-3010C and IEC-61340-4-4 to guarantee accurate results.
To perform the test, you must first condition your material at 12% relative humidity and 73°F for at least 48 hours. Then, charge the material with 5000V using corona or triboelectrification methods. Using high-impedance voltmeters or electrometers, you'll measure how quickly the charge dissipates.
Material Type | Decay Time | Classification |
---|---|---|
Conductive | <0.5s | Fastest |
Dissipative | 0.5-5s | Moderate |
Insulative | >5s | Slowest |
Your material must dissipate 99% of the charge within the specified time limit – typically 2 seconds according to MIL-STD-3010C. You'll classify materials based on their charge relaxation time, which directly influences proper grounding and handling procedures. This testing method's particularly vital in electronics manufacturing and packaging industries where static control is essential for product protection.
Static Shielding Performance Assessment
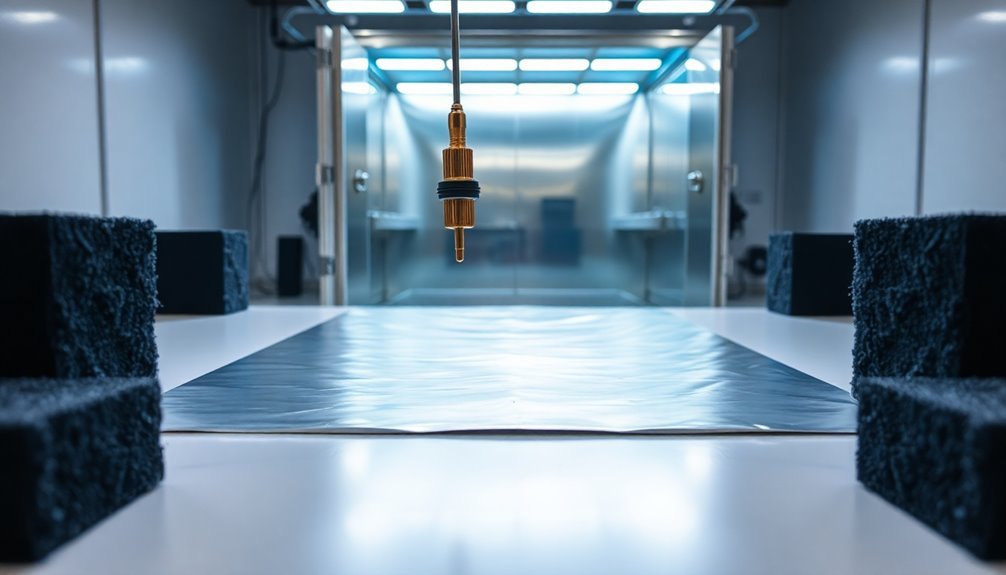
Static shielding performance evaluation represents a vital process in appraising protective packaging materials for electronic components.
You'll need to conduct several standardized tests following ANSI/ESD guidelines to guarantee materials meet industry requirements and provide effective protection through the Faraday cage effect.
When you're evaluating static shielding performance, you'll need to perform volume resistance and surface resistance tests to measure the material's ability to dissipate static charges.
You should also conduct charge retention tests and static shielding evaluations under controlled environmental conditions. The materials you're testing must demonstrate surface resistance within the static dissipative range of 1×10^4 Ω/sq to 1×10^11 Ω/sq.
You'll want to examine the material's layered construction, confirming it includes essential components like static dissipative coatings, metal layers, and polyethylene.
Don't forget to take into account environmental factors and material variability in your evaluation.
While balancing cost with performance, you must verify that materials meet application-specific requirements and maintain consistent quality.
Remember that supplier reliability plays a vital role in guaranteeing the materials you're testing will provide dependable static protection.
Environmental Conditioning Requirements
Building upon proper static shielding evaluation practices, environmental conditioning stands as a foundational element of accurate material testing.
You'll need to follow ANSI/ESD S541's specifications of 12% ± 3% relative humidity and 23°C ± 3°C when qualifying your static control packaging materials. This standardization guarantees consistent results across different testing laboratories and helps identify materials that might fail in low-humidity conditions.
To maintain effective ESD control in your facility, you must:
- Test materials at your facility's lowest experienced humidity level, particularly if it's below the standard requirement.
- Document and track humidity variations throughout the year to assess potential risks.
- Verify material performance regularly, especially for topically coated antistatic materials that may fail in low-humidity environments.
You'll need to integrate these environmental conditioning requirements into your overall ESD control program.
When selecting packaging materials, consider your specific facility conditions and EPA requirements.
Remember that continuous monitoring of both environmental conditions and material performance is vital for maintaining compliance with ANSI/ESD standards and guaranteeing consistent protection of your ESD-sensitive items.
Testing Equipment and Calibration
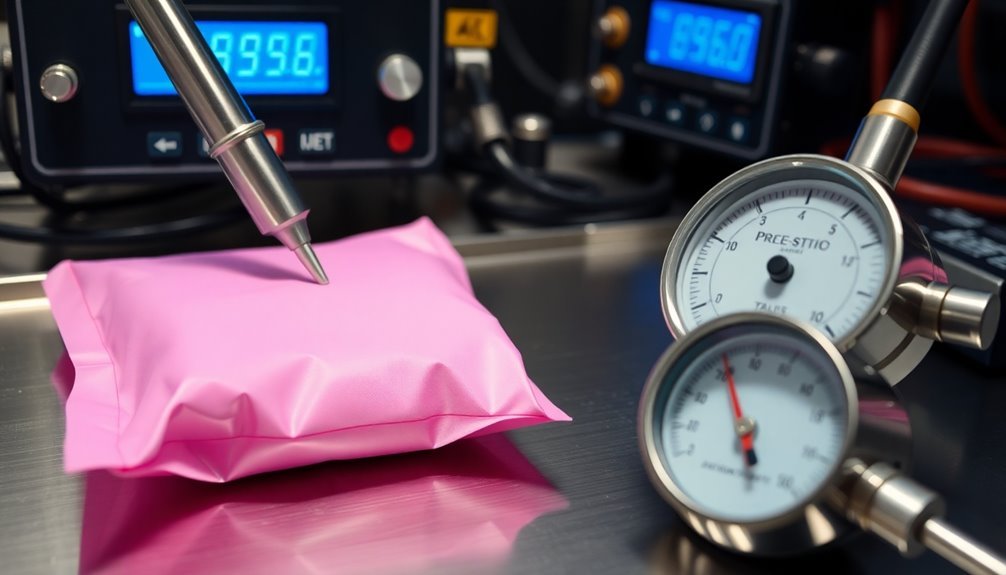
You'll need specific test equipment, including properly calibrated ESD testers, surface resistance meters, and static decay testers, to accurately evaluate static control packaging materials.
To maintain testing accuracy, you must follow a regular maintenance schedule for your equipment and keep detailed records of all calibration activities in accordance with ANSI/ESD S20.20 standards.
Your calibration checklist should include verification of equipment accuracy against certified standards, documentation of calibration dates, and confirmation that all devices meet the requirements specified by manufacturers like Desco Industries or SCS Static Control Solutions.
Essential Test Equipment Setup
Proper testing of ESD packaging materials requires a thorough suite of specialized equipment and rigorous calibration protocols.
You'll need to verify your testing environment includes essential tools like two-point resistance testers, static field meters, and shielding effectiveness testers to validate packaging compliance with ANSI/ESD standards.
Before beginning any testing procedures, you must verify that all equipment is properly calibrated and traceable to national standards.
Your documentation should clearly show calibration records for audit purposes, and you'll want to maintain ISO 9001 certification requirements throughout your testing process.
To set up your testing station effectively, follow these critical steps:
- Position your static field meters and resistance testers on a clean, grounded surface, verifying they're properly connected to power sources and calibrated according to manufacturer specifications.
- Install thickness and tear resistance testers in designated areas where they won't be affected by environmental interference.
- Set up your static decay and friction testers in temperature-controlled spaces to maintain consistent testing conditions.
Remember to validate your equipment setup regularly and maintain detailed records of all calibration checks and testing procedures to verify ongoing compliance with ESD standards.
Maintenance Of Testing Devices
Regular maintenance of your testing devices forms the backbone of accurate ESD packaging material validation.
You'll need to follow strict calibration schedules and maintain detailed records that comply with ANSI/ESD S541 standards. Confirm you're documenting all environmental conditions during calibration and keeping certificates on file for audit purposes.
You must store your equipment in a controlled environment where temperature stays at 73±5°F and relative humidity at 12%±3%.
Don't remove test samples from these conditions, as this can compromise your results. Before testing, precondition your samples for at least 48 hours under these specific parameters.
Handle your testing equipment with appropriate care and inspect it regularly for signs of wear.
You'll need to clean and maintain devices according to manufacturer specifications, using them only for their intended purposes. Make sure you're following proper storage protocols to prevent degradation and maintain calibration accuracy.
Train your personnel thoroughly on equipment use, maintenance procedures, and calibration protocols.
Keep detailed records of all training sessions and confirm your team stays updated on new standards and equipment updates. This thorough approach to maintenance will help guarantee reliable test results.
Calibration Standards Checklist
Before beginning any testing procedures, a thorough calibration standards checklist guarantees your equipment meets all required specifications.
You'll need to verify your testing devices comply with ANSI/ESD S541 requirements and maintain proper documentation of all calibration activities for traceability to national standards.
To maintain accuracy in your static control packaging tests, follow these essential calibration requirements:
- Verify environmental conditions meet the specified parameters of 12%±3% relative humidity and 73±5°F using calibrated environmental chambers before conducting any tests.
- Calibrate your electrometers and concentric ring fixtures according to ANSI/ESD STM11.11 and STM11.12 standards for surface and volume resistance testing.
- Confirm your electrostatic decay testing equipment follows Mil-STD-3010C, Method 4046 specifications and uses appropriate calibration standards.
Remember to maintain detailed records of each calibration, including dates, environmental conditions, and reference standard values used.
Your calibration software should track all measurements and store results for future reference.
Don't forget to schedule regular calibration intervals as specified by your equipment manufacturer, and always recalibrate after significant use or environmental changes.
Material Classification and Selection
Understanding static control packaging materials requires a systematic approach to classification and selection based on their electrical properties and intended applications.
You'll encounter four main categories: conductive materials with surface resistance between 10^2 and 10^5 ohms that conduct charges away, dissipative materials with resistance between 10^5 and 10^11 ohms that slow charge flow, anti-static materials that prevent tribocharging, and shielding materials that create protective barriers.
When selecting materials, you'll need to examine several critical factors. Start by evaluating environmental conditions, including humidity and temperature exposure risks.
Consider your device's ESD sensitivity level to determine the required protection threshold. You must also factor in cost-effectiveness and handling requirements, ensuring the material offers adequate protection while remaining practical for your operations.
Don't forget to verify compliance with industry standards, particularly ANSI/ESD S541 guidelines. You'll want to maintain proper documentation of material certifications and testing results.
For high-sensitivity applications, you should choose conductive or shielding materials, while less critical components may be adequately protected with dissipative or anti-static options.
Always test materials under your specific operating conditions before implementation.
Quality Control Test Procedures
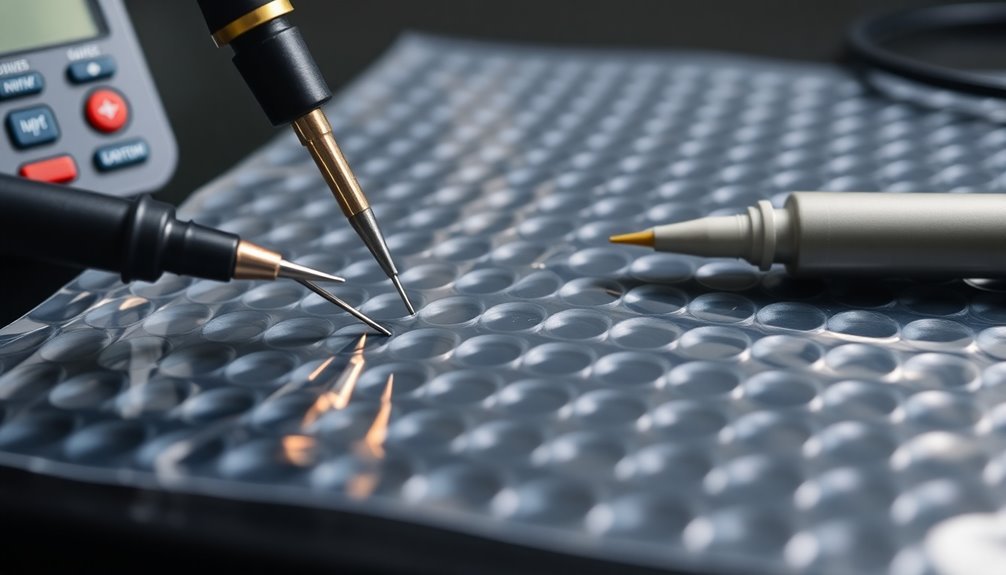
Quality control test procedures for static control packaging call for rigorous evaluation across multiple parameters.
You'll need to conduct surface and volume resistance testing according to ANSI/ESD standards to guarantee proper charge dissipation properties. These tests determine how effectively your packaging materials can protect sensitive electronic components from damaging static discharge.
When testing static control packaging, you should focus on these vital measurements:
- Static shielding capabilities at varying humidity levels using ANSI/ESD STM11.31-2012, which helps verify the material's protective performance under different environmental conditions.
- Electrostatic decay rates that must meet Mil-STD-3010C Method 4046 requirements, guaranteeing rapid dissipation of static charges.
- Charge retention properties using the Faraday Cup method, which measures how well the material prevents static buildup.
Don't forget to complement these specific ESD tests with standard packaging quality control procedures.
You'll want to check seal integrity, barrier properties, and conduct drop testing to guarantee complete protection.
Remember that proper documentation of test results is essential for maintaining quality standards and meeting regulatory requirements in static control packaging manufacturing.
Packaging Compliance and Certification
Compliance with ESD packaging standards requires strict adherence to ANSI/ESD S541 specifications and rigorous certification processes.
You'll need to guarantee your packaging materials meet specific resistance requirements: conductive materials should measure between 10^2 and 10^5 ohms, while dissipative materials should range from 10^5 to 10^11 ohms.
For certification, you'll need to implement regular testing protocols following ANSI/ESD S541 guidelines and ESD TR53-01-06 requirements. Your verification process must include surface resistance, volume resistance, electrostatic decay, and charge retention tests.
Third-party certification may be necessary to demonstrate compliance with ANSI/ESD S20.20 standards.
When packaging ESD-sensitive items, you must guarantee different requirements are met for inside and outside EPA use. Inside EPA packaging should be low charge generating and dissipative, while outside EPA packaging requires additional electrostatic discharge shielding.
Don't forget to include proper marking and traceability information on all packaging, including manufacturer details and date/lot codes.
Your packaging system design should account for environmental conditions and device sensitivity while maintaining continuous grounding and equipotential bonding throughout the EPA.
Frequently Asked Questions
How Long Does ESD Packaging Maintain Its Protective Properties During Actual Use?
You'll find that ESD packaging maintains its protective properties for 2-5 years when properly stored and handled, but you should regularly test it for surface resistivity and static decay to guarantee ongoing protection.
Can Static Control Packaging Materials Be Safely Reused Multiple Times?
You can reuse static control packaging if it's undamaged and meets surface resistance standards. However, you'll need to inspect for wear, follow cleaning protocols, and guarantee compliance with manufacturer guidelines before each reuse.
What Causes Sudden Failures in ESD Packaging That Passed Initial Testing?
You'll find sudden ESD packaging failures often occur from improper handling, material degradation over time, environmental stress, compromised seals, and incorrect storage conditions – even when packaging initially passed quality tests.
How Do Extreme Shipping Temperatures Affect ESD Packaging Performance Over Time?
You'll notice your ESD packaging's performance degrades as extreme temperatures cause material expansion, contraction, and moisture changes. This compromises protective properties and can weaken static-dissipative coatings over repeated exposure cycles.
Are There Alternatives to Traditional ESD Testing Methods for Small Businesses?
You can use portable ESD testing devices, collaborate with testing labs, or share equipment with other businesses. While there's no perfect substitute for traditional methods, these alternatives can help manage your testing needs.
In Summary
You'll find that proper testing of static control packaging is essential for protecting sensitive electronic components. By following standardized test methods and maintaining calibrated equipment, you're ensuring reliable results for surface resistance, volume resistance, decay rates, and shielding effectiveness. Regular quality control testing lets you verify ongoing compliance and make informed decisions about packaging materials that meet your specific ESD protection requirements.
Leave a Reply