When stacking conductive containers, you'll need to follow seven key methods for safe storage: Start with a properly grounded foundation using metal plates or grounding rods. Install twist locks between containers to maintain electrical continuity. Use corner guards made from Type 5052 or 5005 aluminum to protect connection points. Maintain 10-20mm gaps between units for ventilation while preserving conductivity. Connect bonding cables between containers to equalize static charges. Keep humidity levels between 50-75°F using environmental controls. Stack uniformly sized containers with heavier units at the bottom, never exceeding nine containers high. These foundational steps will help you master the complete system of conductive storage safety.
Grounding Methods for Container Stacks
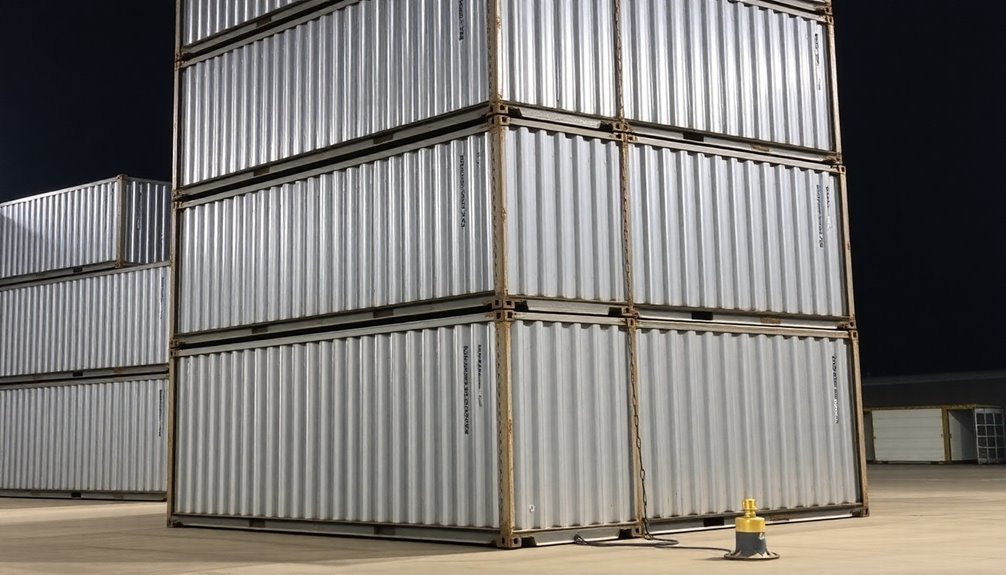
Ground safety protocols for container stacking begin with a thorough assessment of your base surface and soil conditions. You'll need to verify that the ground is level and firm enough to support your containers, and for larger yards, conduct soil tests to confirm the land can handle multiple stacked units. Having a level foundation base prevents misalignment issues that can compromise the entire stack's structural integrity.
To secure your containers properly, you'll want to implement either concrete footings with anchors or steel plates with welded connections pressed into wet concrete. Twist locks bolted to the foundation offer a quick and reliable solution for securing containers while maintaining flexibility in your setup.
Don't forget to check the corner castings on each container to confirm they're in good condition for proper alignment and stacking.
When handling containers with flammable materials, you must establish proper electrical grounding. Connect bonding cables between dispensing and receiving vessels, or use metallic floorplates for both bonding and containment during liquid transfers.
If you're working with non-conductive containers, install metal grounding rods or wires to create a safe electrical pathway. Always verify that your grounding system is compatible with existing yard infrastructure and meets safety requirements for static electricity dissipation.
Vertical Static-Free Stacking Techniques
When implementing vertical static-free stacking techniques, you'll need to start with a level, reinforced foundation that can support multiple container loads. You'll want to guarantee proper weight distribution by placing heavier containers at the bottom and maintaining uniform sizing throughout the stack.
To achieve maximum stability, you must align the corner posts precisely, as they're designed to bear the weight of containers above. The containers' unique hinged-lid design ensures secure closure during stacking operations. Use twist locks or lashing rods to secure each container to prevent shifting or separation.
Don't exceed the recommended stack height of nine containers, and always consider wind loading factors in your planning.
Your containers should be made of durable, conductive materials with rapid static decay rates to prevent charge buildup. You'll need to conduct regular inspections to identify any damage that could compromise the stack's integrity.
Make sure you're following OSHA regulations throughout the stacking process to maintain workplace safety and avoid penalties.
For air-sensitive or moisture-sensitive items, you'll want to verify that your containers provide adequate protection.
Professional planning is essential – create a detailed stacking strategy that accounts for load distribution, stability requirements, and safety considerations before beginning the stacking process.
Cross-Stack Discharge Prevention
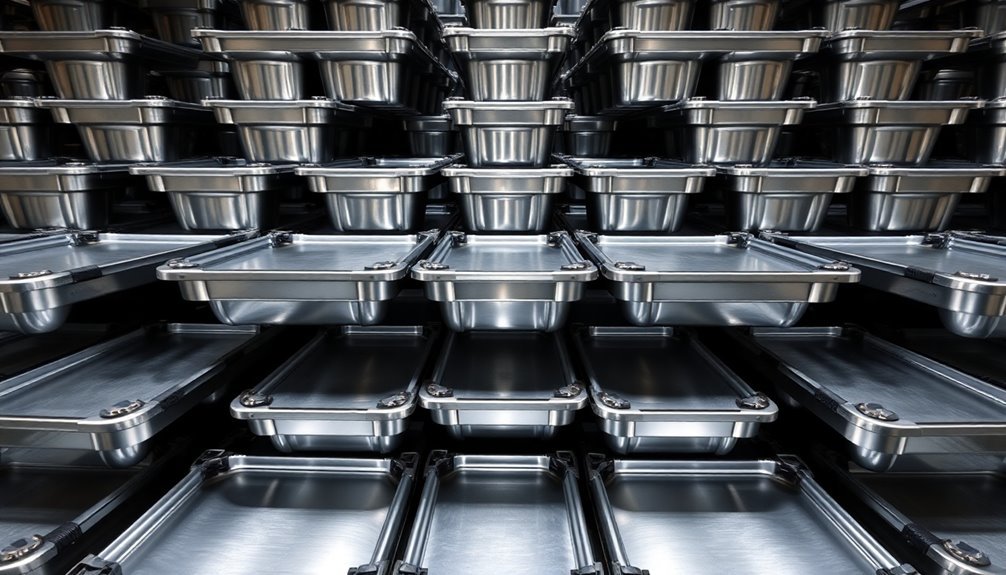
Three critical factors determine effective cross-stack discharge prevention: proper container shielding, secure stacking techniques, and environmental controls.
To protect your electronics, you'll need to implement static shielding bags and anti-static materials while guaranteeing containers are properly secured with lashing rods and twist-locks.
When you're stacking containers, align corner posts precisely to maximize stability and reduce vibration-induced static. You should inspect each container before stacking and verify it's free from defects that could compromise ESD protection. Following containment level requirements for hazardous materials storage helps ensure proper handling and safety protocols are maintained.
Make sure you're using ESD-safe materials and maintaining proper humidity levels in your storage area to minimize static buildup.
You'll need to follow OSHA regulations and ISO standards for container stacking heights and spacing. Don't exceed recommended stacking limits, as this increases ESD risk.
Apply anti-static coatings to your containers and regularly maintain your equipment to prevent discharge incidents. Remember to properly label all containers with handling requirements and guarantee your staff is trained in ESD-prevention techniques.
For maximum protection, ground your equipment and personnel, and keep static-inducing materials away from sensitive electronics. This thorough approach will substantially reduce the risk of cross-stack discharge damage.
Metal Corner Protection Systems
You'll find that 304 stainless steel corner brackets offer the strongest protection for conductive container stacking, with a standard 16-gauge thickness that can handle up to 2,000 pounds of direct impact force.
To properly install these protective edges, you need to first clean the surface area, align the bracket against the corner ensuring it's level, and secure it using either the pre-drilled #8 screws or industrial-grade adhesive tape. The corrosion-resistant alloy composition ensures long-lasting protection even in harsh chemical environments.
Your reinforced corners can substantially extend container life by preventing metal fatigue at critical stress points while maintaining the stack's conductive properties.
Corner Bracket Material Types
Various material options exist for corner bracket protection systems, each offering distinct advantages in conductive container applications. You'll find stainless steel brackets provide superior corrosion resistance and durability, making them ideal for environments with high moisture or chemical exposure. Aluminum brackets offer an excellent strength-to-weight ratio, which can reduce overall container weight while maintaining structural integrity.
For specialized applications, you'll want to evaluate carbon steel brackets when maximum load-bearing capacity is essential, particularly in heavy-duty industrial storage. Galvanized steel options provide enhanced protection against rust and corrosion, extending the life of your storage system. Coated materials offer additional protection while maintaining the material's core properties.
Material Type | Key Benefit | Best Application |
---|---|---|
Stainless Steel | Corrosion Resistant | Chemical Storage |
Aluminum | Lightweight | General Purpose |
Carbon Steel | High Load Capacity | Heavy Industry |
When selecting corner bracket materials, you'll need to assess several factors: the weight of your containers, environmental conditions, and frequency of use. For conductive applications, verify the material you choose maintains proper electrical conductivity to prevent static buildup. Evaluate maintenance requirements and long-term cost implications, as some materials may require periodic treatments or replacements.
Edge Protection Installation Steps
Installing edge protection systems properly begins with thorough preparation and equipment inspection. Before you start, inspect all components for defects, check welds for cracking, and verify you've selected appropriate brackets for your surface type. Like using aluminum corner guards, this system provides excellent protection and durability in high-traffic areas.
You'll need industrial-grade ladders rated for at least 120kg and a clean, debris-free work area.
Begin bracket installation by attaching them to roof rafters or wall studs using tightening bolts and self-tapping screws. Space your gable brackets no more than 2.4 meters apart, using at least two brackets on each side. Adjust your J-Bar or S-Bar to extend no more than 100mm beyond the roof's leading edge.
Install the rails systematically, starting with the mid or top rail. Don't tighten them until you've positioned all rails in the section. Use corner connectors at gable tops and external corners.
You'll need additional rails if the gap between the roof surface and bottom rail exceeds regulatory limits of 275mm or 250mm.
Complete the installation by securing all hand bolts on rail posts and fitting ladder access brackets with double couplers. Perform a final check to verify all universal brackets and posts are secure, with no sliding guard rails.
Reinforcement Load Bearing Capacity
For ideal load-bearing capacity, metal corner protection systems require precise installation and careful consideration of weight distribution. You'll need to install steel corner protectors to maintain structural integrity and prevent damage during stacking operations. These high-quality steel components not only protect against scratches and dents but also enhance overall weight distribution. The galvanized metal finish ensures maximum durability and corrosion resistance in various environments.
When you're modifying containers, remember that structural changes will decrease their load capacity. You'll need to reinforce removed sections with new steel, and it's crucial to weld strong steel bars along the roof and periphery.
Consider using I-beams or square tubes as reinforcements, but always consult a structural engineer for specific requirements.
You must account for load calculations when planning your stacking system. Standard containers can handle 330 psf when unmodified, but interior floor loads typically shouldn't exceed 40 psf for live loads and 70 psf for dead loads.
If you're adding roof modifications, factor in an additional 60-75 psf. When stacking, place smaller containers under larger ones and guarantee vertical alignment.
Don't use offset stacking, as it increases collapse risk. Always secure containers properly to prevent shifting.
Conductive Base Layer Requirements
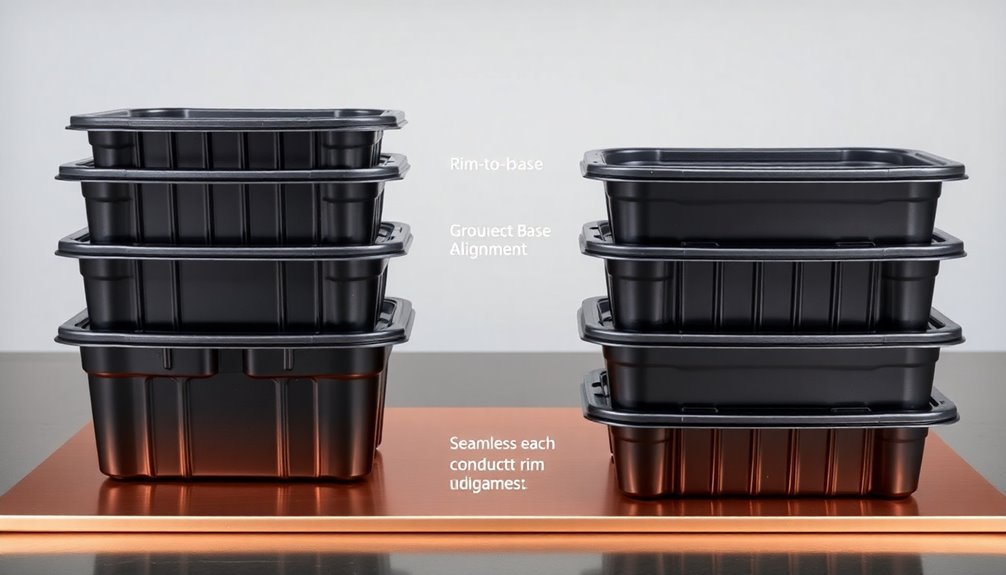
Proper conductive base layers serve as the foundation for safe container stacking operations. You'll need to guarantee your base layer material can withstand various environmental conditions while maintaining consistent electrical conductivity throughout its service life.
When selecting your conductive base layer, you must focus on materials that offer reliable protection against moisture and temperature fluctuations. The material's thickness should be sufficient to maintain structural integrity, preventing damage during container stacking operations. Well-ventilated storage conditions are essential to prevent equipment damage.
You'll want to pay special attention to the installation process, making sure the conductive side faces the ground for peak performance.
You must regularly test your base layer's resistance to verify it maintains proper conductivity levels. It's crucial to conduct environmental testing, including freeze-thaw cycles and water immersion tests, to guarantee long-term durability.
Don't forget to verify compatibility with other materials in your stacking system and comply with ASTM D7240-18 standards.
You'll need to properly store your conductive base layers in a dry, well-ventilated area away from high-traffic zones. Keep the storage temperature between 32°F and 104°F, and maintain humidity levels below 80% to preserve material integrity.
Static Control Stacking Hardware
Building on your conductive base layer foundation, static control stacking hardware provides the next level of protection against electrical discharge risks. You'll need to integrate multiple components to create a thorough static control system for your container stacking operations.
Bar and nozzle ionizers work together to neutralize static electricity in both open and confined spaces, while static sensors continuously monitor charge levels to guarantee effective neutralization.
For secure stacking, you'll want to combine anti-static materials with proper securing hardware:
- Install twist locks at container corners to prevent lateral movement and guarantee stable stacking
- Use anti-static fittings made from conductive resin for all connection points
- Implement lashing rods with conductive materials to secure container stacks
- Add lashing bridges for additional structural support in high-stack configurations
- Select container handling equipment with anti-static urethane components
When handling static-sensitive items, incorporate ion boxes for simultaneous static neutralization and dust removal. These units are particularly effective for small to medium parts that require careful handling.
Remember to regularly check your static sensors and maintain proper grounding connections throughout your stacking system to guarantee consistent protection against static discharge.
Environmental Humidity Control Measures
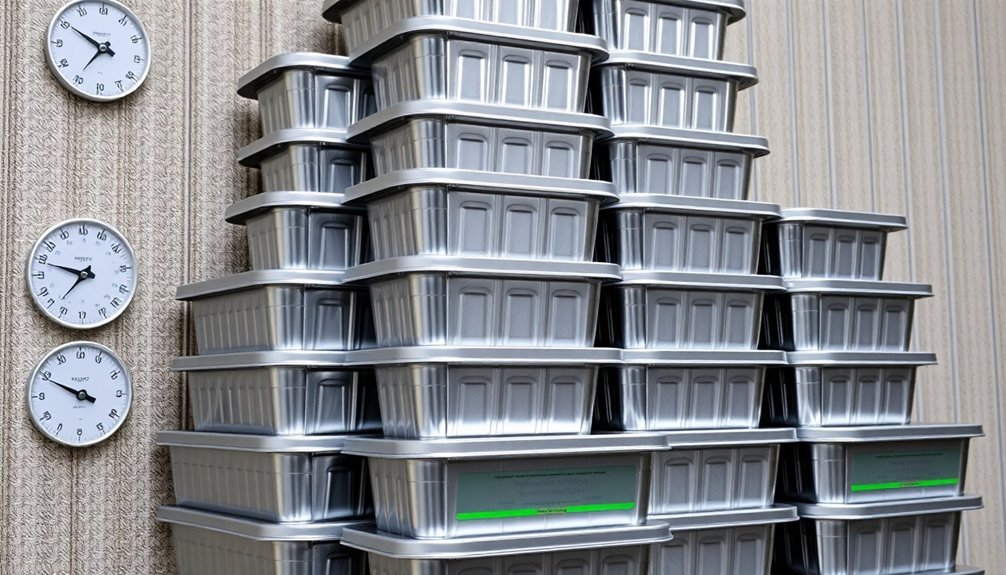
Install moisture sensors at strategic points throughout your conductive container stacking system to monitor humidity levels and prevent static buildup.
You'll need to place sensors both at ground level and at elevated positions to track moisture variations that could affect your container's conductivity performance.
Implement airflow management systems with automated controls to maintain ideal humidity ranges between 50-75°F, ensuring consistent environmental conditions across your stacked containers.
Moisture Sensors Installation Guide
Moisture sensors serve as critical components in environmental humidity control systems, requiring careful preparation and precise installation techniques. To guarantee peak performance, you'll need to soak the sensors overnight in water and mark each cable with distinct patterns to identify their designated depths.
Before installation, prepare moist soil balls by adding just enough water to maintain shape without crumbling.
When you're ready to install, follow these essential steps:
- Auger holes to precise depths (10 cm, 30 cm, 60 cm, 90 cm)
- Place prepared soil balls at the bottom of each hole
- Guide sensors using PVC tubes while maintaining wire tension
- Backfill holes with soil, tamping firmly for secure placement
- Route wires through protective tubing to prevent damage
You'll need to connect each sensor to the corresponding channel on your Soil Moisture and Temperature Station based on depth. Don't rush to collect data – these sensors require a full week to equilibrate with the surrounding soil conditions. During this settling period, avoid taking measurements to guarantee data accuracy.
Handle the wire leads with extra care, as the connection points are particularly vulnerable to damage.
Airflow Management Control Systems
Beyond sensor installation, effective airflow management control systems form the backbone of any reliable humidity control setup. You'll need to integrate key components including humidifiers, dehumidifiers, and ventilation systems to maintain ideal conditions within your stacked containers. These systems work together to prevent moisture damage while guaranteeing your stored items remain protected.
To implement effective airflow management, you'll want to focus on both mechanical and passive ventilation strategies. Install small fans in your containment chambers, adjusting their RPM to maintain proper air pressure.
Place vents strategically to maximize cross-ventilation, and use containment panels to prevent hot air recirculation. You'll find that separating hot and cold air streams markedly improves temperature control and reduces energy consumption.
Don't forget to assess your ventilation needs based on container size and local climate conditions. You should insulate your containers properly to regulate temperature and minimize condensation risks.
Regular maintenance is vital – clean and inspect your ventilation components frequently. For additional moisture control, you can incorporate dehumidifiers or moisture-absorbing materials into your setup.
This thorough approach guarantees the best environmental conditions for your conductive container storage system.
Container Material Compatibility Guidelines
Selecting appropriate container materials requires careful evaluation of multiple chemical and physical factors to guarantee safe, reliable storage. When choosing materials for your conductive containers, you'll need to take into account both chemical compatibility and environmental conditions to prevent degradation and guarantee long-term performance.
Start your material selection process by consulting chemical compatibility charts, which use rating systems to indicate how different materials interact with specific chemicals. You'll want to pay special attention to temperature ranges and chemical concentrations, as these factors substantially impact material performance.
- Check the material's corrosion resistance against your stored chemicals
- Evaluate thermal stability across your facility's temperature range
- Verify chemical resistance ratings for both primary and secondary exposures
- Take into account regulatory requirements for your specific industry
- Test materials under your actual operating conditions before full implementation
Remember to document your material selection process and maintain records of compatibility testing. You'll need to regularly assess container performance and watch for signs of material degradation.
If you're storing multiple chemicals, guarantee your chosen material is compatible with all substances it might contact, including cleaning agents and environmental factors.
Stack Height Safety Limits
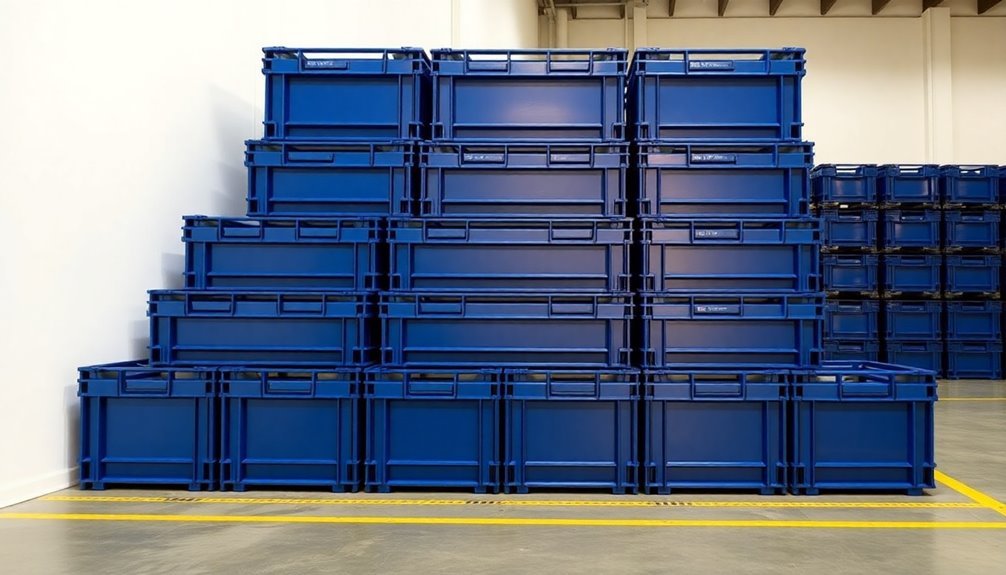
Safe container stacking consistently requires adherence to established height limits and weight distribution guidelines. You'll need to take into account both the physical limitations of your containers and local regulations when determining maximum stack heights.
Standard containers can typically be stacked five to six levels high, but you must account for environmental conditions that might require lower heights.
Your stacking decisions should factor in the corner post load capacity of 192 metric tons for ISO containers. Remember that as you add layers, the center of gravity rises, increasing instability risks. You'll want to guarantee even weight distribution across the entire stack to prevent structural failures or collapses.
When determining stack heights, evaluate your containers' material strength and condition. Steel containers offer superior stacking capability, but you must still inspect them regularly for damage.
Don't forget to account for dynamic loads if you're planning to transport stacked containers by sea or rail. You're required to use proper locking mechanisms, such as twist locks, to prevent shifting.
Failure to follow these height safety limits can result in OSHA penalties, worker injuries, and significant operational disruptions.
Ventilation Between Stacked Units
Proper airflow management between stacked conductive containers plays a vital role in protecting your stored components. You'll need to maintain gaps of 10-20mm between units to guarantee adequate ventilation, which prevents moisture buildup and helps dissipate heat from sensitive electronics.
When stacking your containers, consider alternating their orientation to create natural air channels that promote circulation.
To maximize ventilation effectiveness in your storage setup, implement these key practices:
- Keep containers clean and free from dust accumulation, as debris can interfere with proper airflow and create static electricity risks
- Choose cushioning materials that don't obstruct air movement while still providing necessary protection
- Inspect your stacked containers regularly for signs of condensation or inadequate ventilation
- Maintain a climate-controlled environment to minimize the impact of external temperature and humidity fluctuations
- Consider using containers with built-in ventilation features like mesh panels or strategic perforations
Remember that different container materials require specific ventilation approaches. If you're using conductive polypropylene or corrugated materials like Corstat, you'll need to pay extra attention to moisture prevention.
Don't compromise ventilation when implementing offset stacking patterns, as proper airflow remains essential for ESD safety.
Frequently Asked Questions
How Often Should Conductive Stacking Equipment Be Recalibrated for Optimal Performance?
You'll need to conduct regular inspections, but there's no standardized recalibration frequency. It's best to check your conductive stacking equipment monthly for wear, damage, and conductivity to maintain ideal performance.
What Alternative Materials Can Replace Damaged Conductive Corner Castings?
You can replace damaged conductive corner castings with high thermal conductivity steels like DHA-THERMO. It'll provide better thermal performance and durability while maintaining structural integrity, serving as a cost-effective alternative to traditional materials.
Can Different Container Brands Be Mixed in Conductive Stacking Arrangements?
You can mix different container brands if they meet the same ESD standards and have compatible dimensions. Just guarantee their corner posts align properly and they maintain uniform surface resistance for effective protection.
How Do Seasonal Temperature Changes Affect Conductive Stacking System Maintenance?
You don't need to modify your conductive stacking maintenance for seasonal changes, as temperature variations don't affect conductivity. Just maintain regular inspections and guarantee proper alignment of corner posts year-round.
What Emergency Procedures Apply When Static Discharge Occurs During Stacking Operations?
If you encounter static discharge, immediately stop operations, evacuate the area, and activate emergency protocols. You'll need to ground affected equipment, document the incident, and contact your safety supervisor for guidance.
In Summary
You'll find these container stacking methods essential for maintaining proper conductivity and safety in your storage facility. Remember to inspect your grounding systems regularly, monitor humidity levels, and never exceed recommended stack heights. By following these guidelines for conductive stacking, you're protecting both your stored materials and workforce from static discharge risks. Don't forget to document your stacking procedures for consistent implementation.
Leave a Reply