You'll need five key tests to verify your static dissipative storage materials meet safety standards. Start with surface resistivity measurements using a meter and electrodes to check resistance levels between 1×10^6 and 1×10^12 ohms. Conduct static decay time tests to confirm charge drops from 5000V to 50V within acceptable limits. Run triboelectric response analysis to evaluate charge transfer characteristics. Perform voltage discharge rate checks using the RC circuit model for accurate measurements. Finally, verify material composition falls within proper static dissipative ranges. These fundamental checks will help protect your sensitive components – and there's much more to understand about each test.
Surface Resistivity Measurement Test
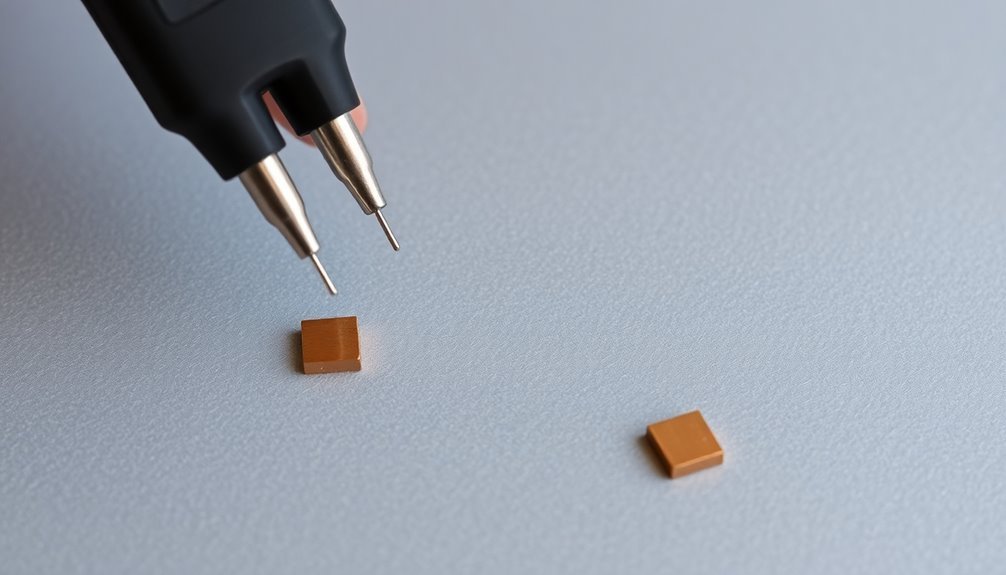
Measuring surface resistivity accurately determines whether your storage materials provide adequate static dissipation protection. You'll need a surface resistivity meter equipped with an area-to-area probe or ring tester to conduct proper measurements under controlled conditions of 12% ± 3% relative humidity and 73° ± 5°F. Regular testing of ESD materials helps maintain ANSI/ESD compliance.
To perform the test, you'll conduct both RTT (Resistance Top to Top) and RTG (Resistance to Groundable Point) measurements.
For RTT testing, place two 5-pound electrodes 10 inches apart on the surface, keeping them 2 inches from any edge.
For RTG testing, use one electrode and connect a black test lead to ground, maintaining 3 inches distance from grounded points.
Your material meets static dissipative requirements if it falls between 1 x 10^6 and 1 x 10^12 ohms. Specifically, RTT measurements should be greater than or equal to 1 x 10^6 ohms, while RTG measurements should range between 1 x 10^6 and 1 x 10^9 ohms.
Static Decay Time Test
The Static Decay Time Test provides a critical method to evaluate how quickly static charges dissipate from storage materials to ground. You'll need to follow specific standards like MIL-STD-3010C or EIA-541 to guarantee your testing meets industry requirements.
During the test, you'll precondition your materials at controlled humidity levels before charging them to a high voltage, typically 5000V. Materials like PET and PVC tend to retain 100% of charge over extended periods.
To perform the test, you'll use specialized equipment like static decay analyzers or charge decay testers equipped with Faraday cages. You'll watch as the voltage drops from its initial charge to less than 50 volts, measuring the time it takes. For materials to be considered static dissipative, they must reduce their charge to 10% within 5 seconds.
You'll want to maintain consistent environmental conditions throughout your testing using an environmental chamber. The test equipment's automatic functions will help you reduce errors and guarantee reliable results.
Modern testing software will display and analyze your data in real-time. This test is essential if you're working with electronics, packaging, or manufacturing applications where static charges could compromise product quality.
Triboelectric Response Analysis
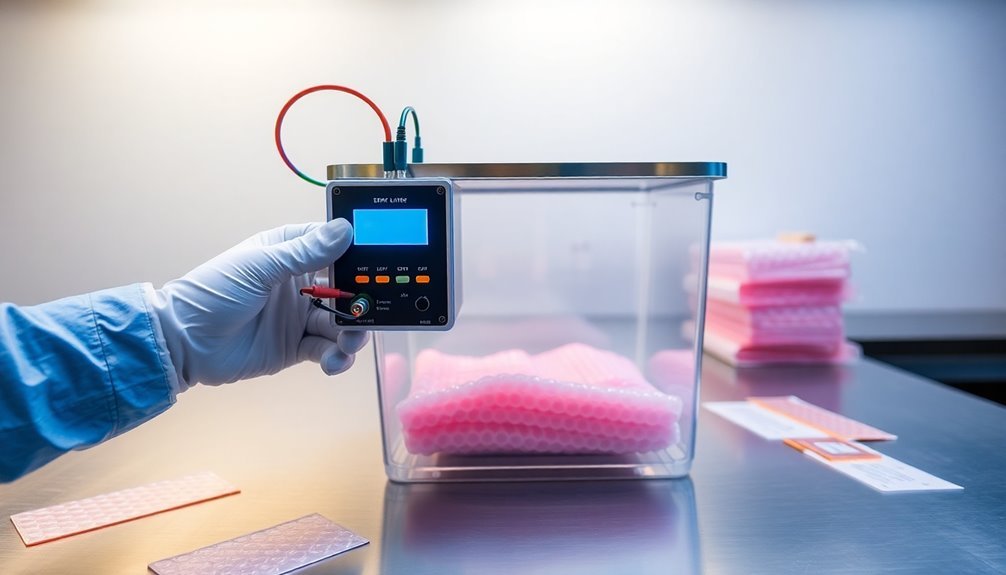
A reliable triboelectric response analysis helps you understand how different materials generate and transfer static charges through contact and separation.
You'll need to take into account several key factors when analyzing triboelectric responses in storage materials, including the contact area, separation speed, and ambient humidity levels, as these directly affect charge generation.
When you're testing materials, refer to the triboelectric series to predict charge polarity and magnitude. Materials positioned higher in the series will typically acquire a positive charge, while those lower in the series become negatively charged. You'll notice stronger charge generation between materials that are further apart in the series. Surface engineering techniques can enhance the material's electron transfer capabilities through improved tribolayer properties.
You should examine the specific charge transfer mechanisms at work in your storage materials. While electron transfer is the primary mechanism, you'll also need to account for ion transfer and surface irregularities that can affect charge generation.
Don't forget that mechanical factors like strain and bending can contribute to charge buildup through additional mechanisms such as piezoelectricity.
For accurate results, you'll want to conduct your analysis under controlled humidity conditions, as moisture substantially impacts charge generation and retention in storage materials.
Voltage Discharge Rate Check
Building on your triboelectric analysis findings, you'll need to verify how quickly static charges dissipate from your storage materials. You can measure discharge rates using the RC circuit model, where t = R*C*ln(V/V0). For accurate testing, you'll want to follow MIL-STD-3010C standards, which specify a maximum discharge time of 2 seconds for a 5 kV charge at 50% relative humidity. Testing must account for relative humidity variations since surface resistance changes significantly with environmental conditions.
Test Parameter | Acceptable Range | Test Method |
---|---|---|
Surface Resistance | <1.0 x 10^11 O | ANSI/ESD STM11.11 |
Volume Resistance | <1.0 x 10^11 O | ANSI/ESD STM11.12 |
Decay Time | <2.0 seconds | MIL-STD-3010C |
To conduct your voltage discharge test, you'll need to measure both surface and volume resistance. Your storage materials should fall within the dissipative range of 1 x 10^5 to 1 x 10^12 Ω/square for surface resistivity. Use the Human Body Model parameters (200 pF capacitance, 10 KΩ resistance) as your baseline for calculations. Remember that discharge currents can vary substantially, from 24,900 A to 249 nA, depending on your circuit's resistance and discharge time.
Material Composition Verification
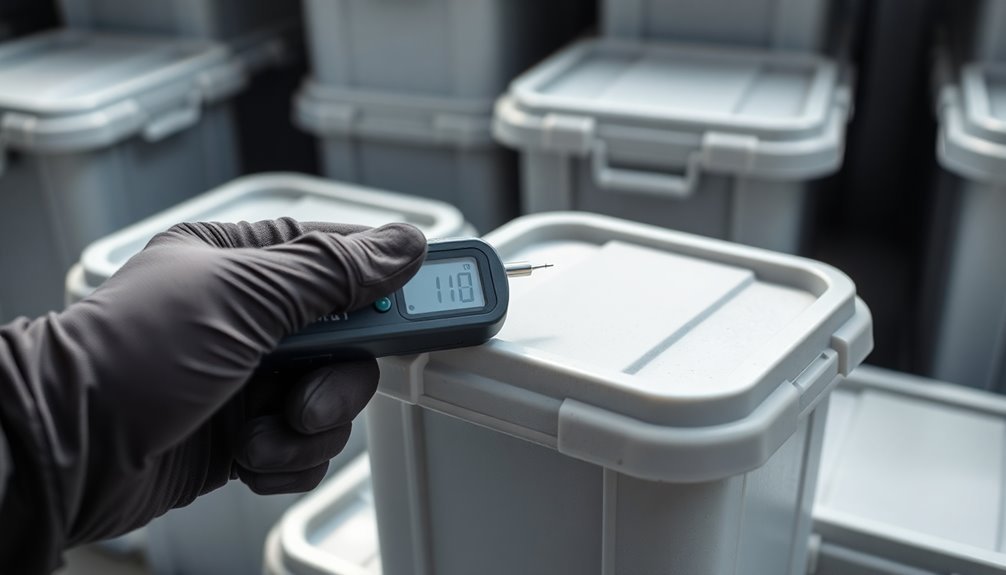
Verifying material composition starts with understanding four distinct categories of ESD-protective materials: static dissipative, conductive, antistatic, and insulative.
You'll need to know that static dissipative materials have surface resistance between 1.0 x 10^4 and 1.0 x 10^11 ohms, while conductive materials measure less than 1.0 x 10^4 ohms. Antistatic materials typically range between 10^10 and 10^12 ohms, and insulative materials exceed 1.0 x 10^11 ohms. Even minor static discharge events can generate voltages above 30,000 volts, making proper material verification crucial.
To verify your storage material's composition, you'll need to conduct surface resistance testing following ANSI/ESD STM11.11-2015 or ASTM D257 standards. You must perform these tests in a controlled environment at 73±5°F and 12±3% relative humidity.
The process involves using electrodes to measure the material's surface resistance while accounting for electrical path length and dimensional specifics.
Remember that ESD protective materials must be either antistatic or static dissipative to meet compliance standards. Your material should demonstrate high electrical resistivity and effectively prevent triboelectric charging.
You'll need to maintain traceable test data to comply with ANSI/ESD S20.20-2014, ensuring your storage solution meets all necessary safety requirements.
Frequently Asked Questions
How Often Should Static Dissipative Storage Containers Be Replaced?
You should replace your static dissipative containers every 12 months, unless they're permanent materials or have a 3-year guarantee. However, always test them regularly and replace immediately if they fail performance tests.
Can Static Dissipative Materials Be Damaged by Cleaning Solutions?
Yes, you'll damage static dissipative materials if you use standard cleaning solutions. You should only use ESD-safe cleaners, as regular products containing alkali or ammonia can harm the material's anti-static properties.
What Temperature Ranges Are Safe for Static Dissipative Storage Materials?
You'll want to keep your static dissipative materials between 40°F and 170°F for ideal performance. Don't exceed 225°F even for intermittent use, and you'll get the best results at room temperature storage.
Do Humidity Levels Affect the Performance of Static Dissipative Storage?
Yes, humidity levels strongly affect your static dissipative storage. You'll want to maintain 40-60% relative humidity, as levels below 40% increase static build-up risk, while higher humidity helps dissipate electric charges effectively.
Can Static Dissipative Containers Be Stacked Without Compromising Their Protective Properties?
Yes, you can safely stack static dissipative containers if they're made with proper materials. Verify they meet required ohm/square resistance ranges and use double-thick wall designs to maintain their protective properties while stacked.
In Summary
You've now learned the five essential tests to verify your static dissipative storage solutions. By regularly performing surface resistivity measurements, decay time tests, triboelectric analysis, voltage discharge checks, and material composition verification, you'll guarantee your storage systems maintain proper ESD protection. Don't skip these simple yet vital tests – they're your best defense against costly static damage to sensitive electronic components.
Leave a Reply