Select the right static dissipative foam by evaluating your component's size, shape, and sensitivity requirements. You'll need to maintain proper environmental conditions, keeping humidity between 30-70% and temperature at 68-72°F for peak performance. Store your foam in sealed ESD-safe containers away from direct sunlight and contaminants. When handling, always use clean, dry gloves to prevent oil transfer. Consider customizing foam cavities for precise component fit, and implement regular testing using ASTM standards. Don't forget to monitor costs through efficient design and automated processes. The deeper you explore these fundamentals, the better you'll protect your sensitive electronics.
Selecting the Right Foam Type
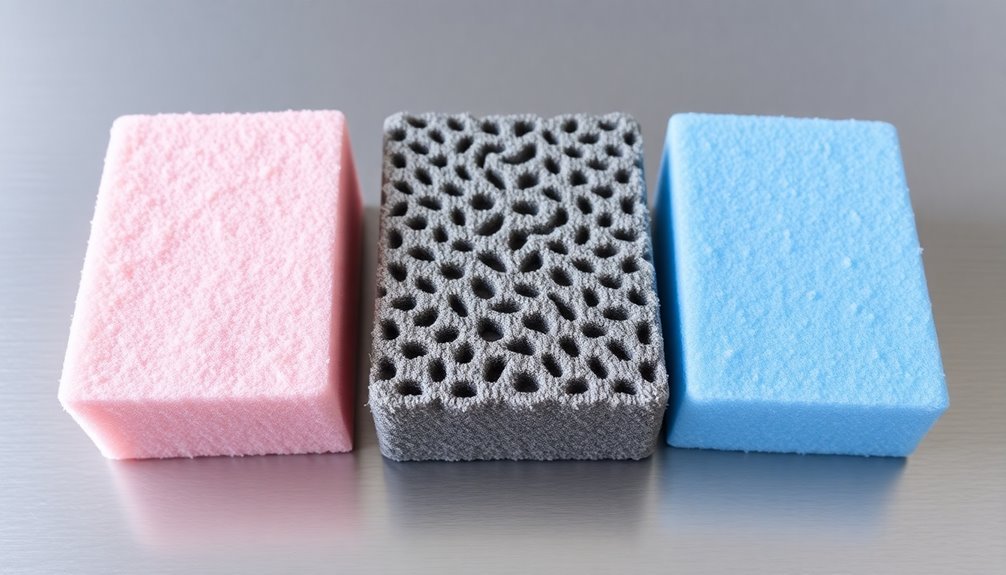
When choosing static protection foam for your sensitive electronics, understanding the key differences between conductive, anti-static, and static dissipative options is essential.
Conductive foam creates a Faraday cage around your products, making it ideal for highly sensitive components that need complete protection. You'll find it's particularly effective for reusable packaging solutions and in-plant handling.
Anti-static foam, typically pink in color, prevents static buildup but doesn't offer full protection against static transfer. If you're using this type, you'll need additional static shielding bags for complete safety. It's best suited for work-in-progress applications where gradual discharge isn't necessary.
For a balanced solution, take into account static dissipative foam. It combines the benefits of both conductive and anti-static properties, allowing charges to dissipate slowly while preventing sudden static shocks. Expert consultation is recommended when selecting foam type for specialized applications. The closed-cell structure of PE and EVA foams provides superior protection against moisture and physical damage.
When selecting your foam type, evaluate your components' sensitivity to static discharge, intended application, and environmental conditions.
Don't forget to take into account material properties like density and surface resistance. You'll also want to assess the foam's durability and reusability, especially if you're planning long-term storage or frequent handling of components.
Environmental Impact on Performance
Environmental conditions play a critical role in your static dissipative foam's performance, with humidity levels directly affecting its ability to safely discharge static electricity.
You'll find that lower humidity can reduce the foam's dissipative properties, while higher temperatures may compromise its protective capabilities and structural integrity.
When selecting static dissipative foam packaging, you'll need to take into account both your storage environment and shipping conditions to guarantee consistent performance throughout the product's journey. The foam's design allows for customized protection options to meet specific environmental requirements. Sustainable alternatives like Stratocell R provide excellent cushioning while maintaining static dissipative properties.
Humidity Effects on Dissipation
Humidity levels in and around packaging environments play an important role in static dissipation performance. You'll find that higher relative humidity (RH) notably improves static dissipation rates, while dry conditions increase static build-up risks. For ideal ESD protection, you should maintain RH levels between 30% and 70%, with 50-60% being perfect.
When you're working with static dissipative foam packaging, remember that humidity directly affects its performance. At 20% RH, you could generate up to 6,000V at a workbench, compared to just 100V at 60% RH. This dramatic difference shows why proper humidity control is vital for protecting sensitive electronics. Ionization systems are especially important in low humidity environments to neutralize charges. Regular testing is crucial since surfactant molecules deteriorate over time, affecting the foam's anti-static properties.
You'll need to test your packaging materials at the lowest expected operating humidity to guarantee reliable performance. Some static dissipative foams can lose effectiveness in dry conditions, so choose materials like ETHAFOAM AS that maintain their properties across varying humidity levels.
Consider installing humidification systems in your packaging area – they can reduce static build-up by up to 98%. During autumn and winter, when indoor air tends to be drier, you'll need to pay extra attention to maintaining appropriate humidity levels.
Temperature Impact on Protection
Temperature plays an essential role in determining how effectively static dissipative foam protects your sensitive electronics. You'll need to guarantee your storage conditions stay within specific temperature ranges: -30 to 80 degrees Celsius for conductive foam and -10 to 85 degrees Celsius for anti-static foam. When you maintain these temperature limits, your foam packaging will retain its key protective properties.
You can rely on high-quality static dissipative foams to maintain their performance across various temperatures within their specified ranges. They're engineered for thermal stability, which means they'll consistently protect your components from static discharge throughout storage and transportation. The rigid closed cell structure ensures reliable protection even under varying environmental conditions. Anti Static PE Foam provides superior cushioning protection with its specialized closed-cell design.
However, if you expose the foam to temperatures beyond its recommended range, you'll risk compromising its protective capabilities.
When you're choosing foam packaging, consider both the environmental impact and performance reliability. Today's static dissipative foams are designed to be eco-friendly and recyclable while maintaining their protective properties.
You'll want to select materials that comply with environmental standards without sacrificing their ability to protect your electronics. Remember that proper disposal of these materials is important for environmental sustainability.
Storage and Handling Guidelines

You'll need to store your static dissipative foam in a temperature-controlled environment between 68-72°F (20-22°C) to maintain its ideal performance.
Keep your foam away from dust, oils, and moisture by storing it in sealed ESD-safe containers when not in use.
It's crucial to handle the foam with clean, grounded equipment and avoid contact with bare hands to prevent contamination that could compromise its static dissipative properties.
Proper Temperature Control Methods
Maintaining precise temperature control is essential for preserving static dissipative foam's protective qualities and performance. You'll need to keep storage and handling temperatures between -10 and 85 °C while avoiding rapid fluctuations that can compromise the foam's effectiveness.
Temperature Aspect | Impact | Action Required |
---|---|---|
High Temperature | Accelerates foam degradation | Monitor and maintain cooling systems |
Low Temperature | Reduces foam pliability | Verify heating systems are functional |
Fluctuations | Affects conductivity | Install climate control systems |
Ideal Range | Maintains properties | Keep temperature logs and alerts |
To protect your foam packaging, you'll want to implement climate-controlled storage areas and verify your transportation vehicles have proper temperature regulation. Don't skip regular monitoring and temperature logging – these practices help you identify and address issues before they affect the foam's performance. Train your staff to recognize temperature-related problems and respond appropriately to maintain ideal conditions.
Remember that both extreme temperatures and rapid changes can impact the foam's static dissipative properties and cushioning effectiveness. You'll need to maintain stable conditions to verify your electronic components remain protected throughout storage and handling processes.
Avoiding Contamination Risks
To guarantee peak performance of static dissipative foam packaging, proper contamination control measures are vital during storage and handling.
You'll need to store your packaging away from direct sunlight and keep it sealed to prevent degradation and particulate entry. Always use clean, dry gloves when handling materials to avoid transferring skin oils that could compromise the packaging's integrity.
For best protection, you should handle your packaging in cleanroom environments equipped with HEPA filtration or laminar flow systems.
It's essential to maintain clean surfaces and use anti-static tools during component handling. You'll want to regularly inspect your packaging for any signs of damage or contamination that could compromise its effectiveness.
When selecting materials, choose options with low outgassing properties and intrinsic anti-static characteristics.
Don't use materials that release VOCs or generate particles through abrasion. You must ground yourself and your equipment properly by wearing anti-static wrist straps and using conductive tools.
Remember to handle all packaging gently to minimize particulate generation, and always follow established protocols for consistent contamination control.
Regular cleanroom maintenance and proper material storage will help guarantee your packaging remains contamination-free.
Customization for Specific Components
Three key factors drive the customization of static dissipative foam packaging: component size, shape, and sensitivity level. You'll need to evaluate these elements when selecting the appropriate foam material and design for your electronic components.
For permanent ESD protection, you'll want to choose black conductive foam, which maintains its protective properties regardless of environmental conditions. If you're only packaging components for short-term storage, pink anti-static foam can work, but remember that its effectiveness depends on humidity levels.
You can customize your foam packaging with specific cavity sizes and shapes to match your components precisely. The material options include EPE foam for anti-static solutions and high-density conductive polyethylene foam for component leads.
When you're dealing with Class A painted surfaces, EPE foam trays offer excellent abrasion resistance.
For small and medium-sized electronics or circuit boards, you'll find that custom foam inserts can be manufactured without tooling costs. You can request samples to test the effectiveness of different materials and designs through vibration assessments.
Remember that reusability is an advantage – these custom solutions remain durable through multiple uses in plant handling and storage applications.
Cost Optimization Strategies
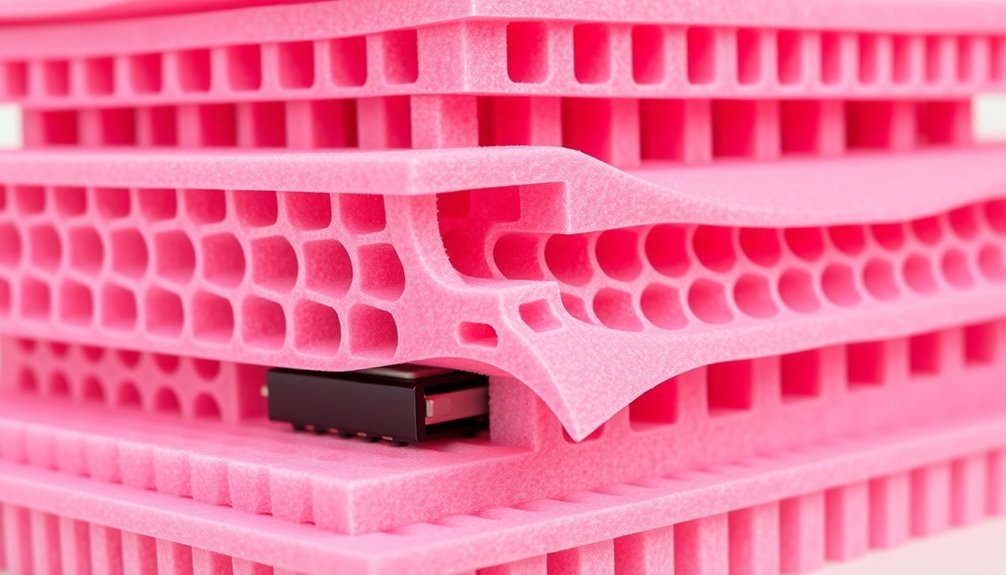
While customizing static dissipative foam packaging enhances protection, managing costs effectively guarantees long-term sustainability. You'll find significant savings by implementing material optimization strategies, starting with right-sized packaging design and regular reviews to minimize waste.
Focus on streamlining your packaging operations through supply chain optimization. You can reduce costs by consolidating suppliers, implementing vendor-managed inventory, and adopting just-in-time delivery systems.
Consider automating your packing processes to minimize labor costs and increase efficiency. You'll benefit from conducting thorough cost analyses to identify areas for improvement.
Evaluate your material usage, assess packaging performance, and run transit trials to guarantee cost reductions don't compromise protection. Use value engineering techniques to optimize specifications while maintaining effectiveness.
To maximize efficiency, train your staff on proper packing techniques and implement easier-to-assemble designs. You can further reduce expenses by optimizing warehouse operations and streamlining packaging lines.
Remember to regularly review your packaging costs and assess new industry innovations that could lead to additional savings while maintaining the static dissipative properties your components require.
Testing and Quality Assurance
Rigorous testing and quality assurance protocols guarantee your static dissipative foam packaging maintains its protective properties.
You'll need to conduct both surface and volume resistivity testing using ASTM D257 standards to confirm your materials meet specifications. Apply electrodes under proper load conditions and measure resistance with an ohm meter to classify your foam's static dissipative properties accurately.
For thorough quality assurance, you'll want to perform ESD shielding tests following ANSI/ESD STM11.31-2012 standards.
Test your packaging materials at both 12% and 50% relative humidity levels, using a 1kV Human Body Model discharge to verify protection levels. Monitor peak current and energy measurements inside the packaging to confirm adequate shielding.
Don't forget to evaluate your foam's cushioning performance through dynamic testing methods like ASTM D4168 and ASTM D1596.
You'll need to use either free-fall drop tests or shock test machines to measure shock-absorbing characteristics. While these tests provide valuable data for developing cushioning curves, remember they're examining the material in isolation, not as part of a complete packaging system.
Reuse and Disposal Best Practices
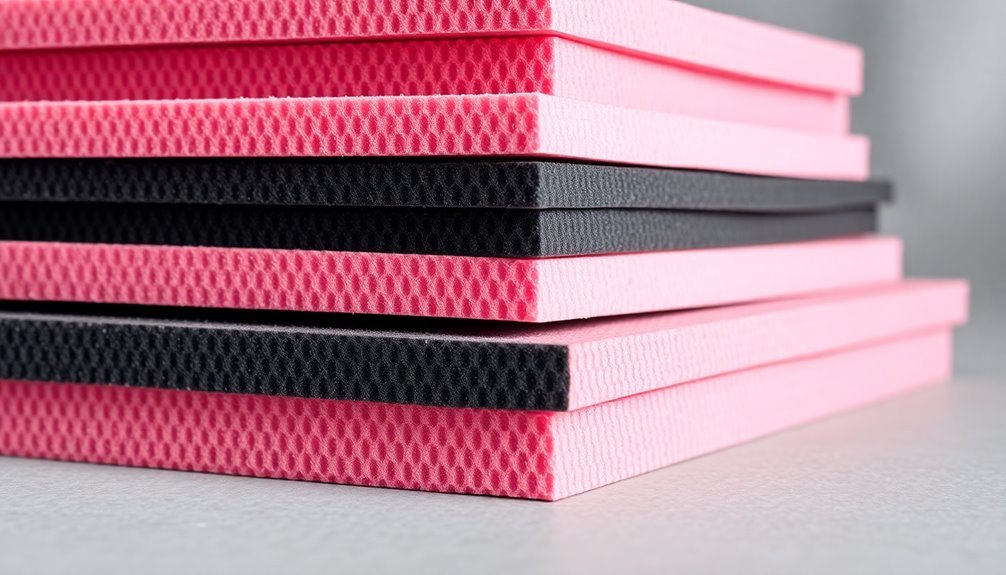
Proper reuse and disposal practices guarantee you maximize the value of your static dissipative foam packaging while minimizing environmental impact. When reusing foam packaging, make certain you thoroughly clean it without harsh chemicals and dry it completely to maintain its protective properties.
Store your cleaned foam in a dry environment away from direct sunlight, and always handle it with care to prevent physical damage.
- Before reusing static dissipative foam, inspect it carefully for signs of wear or degradation, as reuse can compromise its protective properties.
- Consider cross-industry reuse opportunities for non-ESD sensitive products to extend the foam's lifecycle.
- Look for specialized recycling programs that accept static dissipative foam rather than disposing of it in standard recycling bins.
- Document your disposal processes and make certain compliance with local regulations for proper waste management.
When disposing of foam that's no longer suitable for reuse, partner with environmentally responsible disposal services.
You'll want to explore closed-loop recycling programs where available and support companies that offer sustainable packaging solutions.
Remember that while static dissipative foam is typically designed for single use, proper handling and storage can extend its useful life while maintaining its protective qualities.
Frequently Asked Questions
Can Static Dissipative Foam Be Used With Food-Grade Electronic Packaging?
Yes, you can use static dissipative foam with food-grade electronic packaging when it's made from certified materials like EPP foam that meets FDA and EU food safety standards and won't contaminate your components.
How Quickly Does Static Dissipative Foam Lose Effectiveness After Initial Exposure?
You'll notice static dissipative foam begins losing effectiveness immediately after exposure, typically degrading considerably within 6-12 months depending on humidity levels and handling. It's best to monitor its performance through regular testing.
Does Cutting or Shaping the Foam Affect Its Static Dissipative Properties?
You don't need to worry about cutting or shaping static dissipative foam. It won't affect its protective properties since the antistatic agents are distributed throughout the material, not just on the surface.
Are There Specific Cleaning Solutions Safe for Static Dissipative Foam?
You'll need specialized ESD cleaners like StaticCARE or ACL Staticide for static dissipative foam. Don't use regular household cleaners, as they can damage the foam's electrical properties and compromise its static protection.
Can Static Dissipative Foam Be Used Alongside Regular Bubble Wrap?
Yes, you can use static dissipative foam with regular bubble wrap, but you'll need to guarantee the foam directly contacts your electronic components. The bubble wrap provides impact protection while the foam handles static protection.
In Summary
Static dissipative foam packaging isn't just about protecting your components – it's an investment in your product's safety and reliability. You'll maximize your packaging's effectiveness by choosing the right foam type, maintaining proper storage conditions, and following quality testing protocols. Whether you're shipping sensitive electronics or storing valuable components, these seven tips will help you optimize your static control packaging strategy and reduce costly damage.
Leave a Reply