You'll need static control ionizers in your printing operations because static electricity causes major production headaches and quality issues. As materials move at high speeds through printers, they generate static charges that attract dust, cause paper jams, and lead to misaligned prints. This is especially problematic in low-humidity conditions, where over 70% of printer issues stem from static buildup. Static control ionizers neutralize these charges, preventing costly reprints, equipment damage, and material waste. They're particularly vital when working with synthetic substrates. Understanding how these devices protect your printing investment can transform your production outcomes.
Static Electricity Basics in Printing
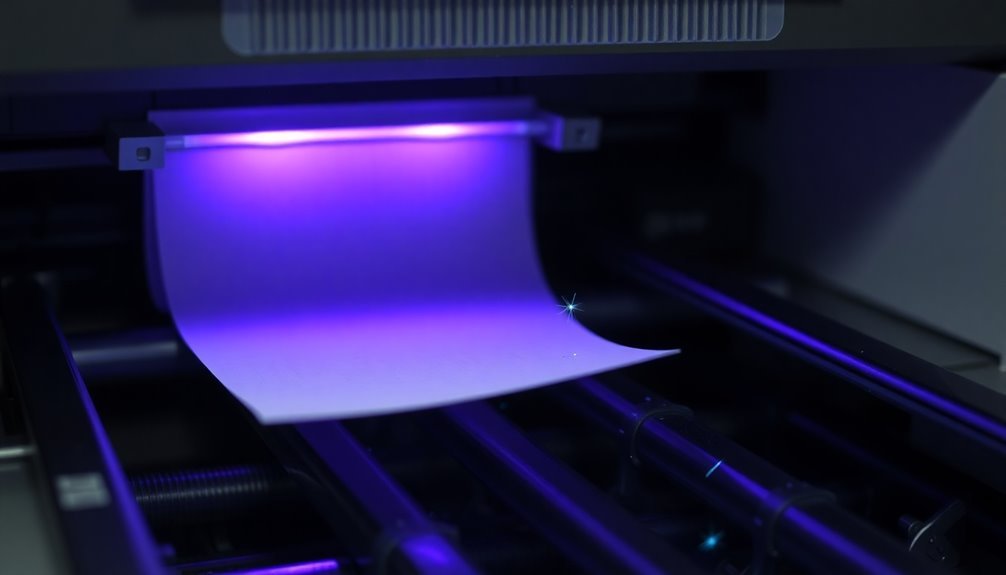
How does static electricity impact the printing process? In your printing facility, static charges build up naturally through the movement and friction of materials, particularly during high-speed operations.
When you're working with synthetic substrates, plastics, paper, or textiles, the static generation becomes even more pronounced, especially if there's slippage or misalignment in your equipment. Your materials can build up significant electrostatic charges as they move through the printing equipment.
Low humidity levels in winter cause over 70% of printer issues related to static electricity problems. You'll notice several problems when static electricity isn't properly controlled. It can cause misregistration of prints, resulting in wasted materials and decreased productivity.
You might also encounter ghosting issues, where faint duplicate images appear on your prints, compromising their quality. More significantly, static electricity creates serious safety hazards – it can trigger fires, explosions, and deliver uncomfortable shocks to your operators.
Beyond these immediate concerns, you'll find that static charges attract dust and debris to your substrates and equipment. This accumulation not only affects print quality but can also damage your machinery over time.
Understanding these basics helps you recognize why static control is essential – it's not just about print quality, but also about maintaining a safe, efficient, and productive printing environment.
Common Printing Production Problems
While managing static electricity is fundamental to printing success, you'll encounter various other production challenges that can affect your print quality and efficiency.
You're likely to face issues like paper jams, which often occur due to improper loading or paper dust buildup. Mismatched paper sizes and improper roller pressurization can lead to recurring paper jams. Poor print quality and streaky outputs can result from clogged print heads or incompatible printer settings. HP printers are especially susceptible to print smears that can compromise document quality.
If you're seeing wrinkled pages, check your feed and exit rollers, as wear and tear or humidity issues could be the culprits. When you notice lines appearing on your prints, examine your scanner glass and mirrors for foreign substances, or investigate potential drum unit malfunctions.
Blank pages and slow printing speeds might indicate low toner levels or outdated printer drivers.
To maintain peak printing performance, you'll need to implement preventive measures. Make sure you're using high-quality paper and loading it correctly in your trays.
Don't skip regular maintenance tasks like cleaning printer parts and updating drivers. You should also monitor your printer settings to verify they match your paper type and quality requirements.
Types of Printing Ionizers
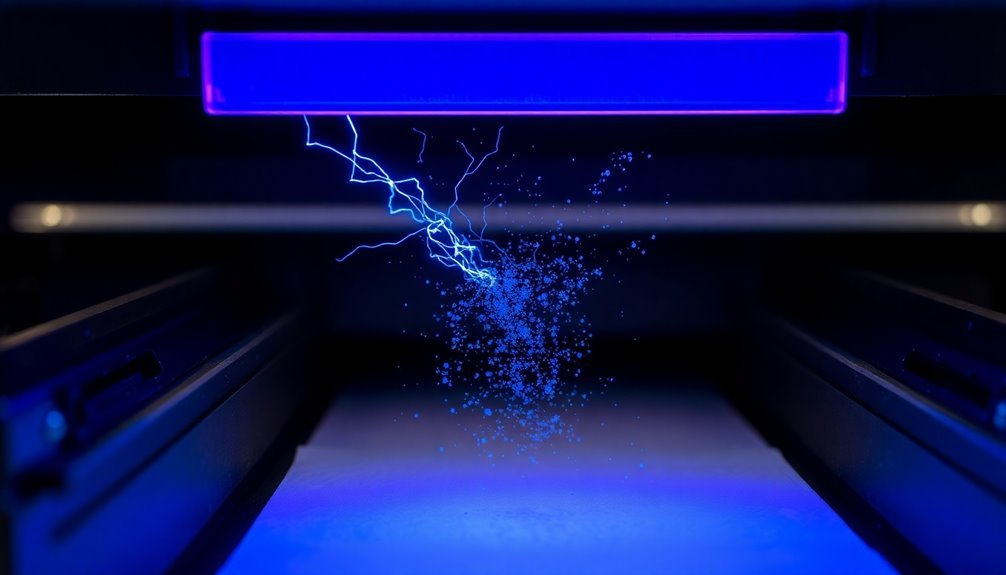
Printing's static control needs are addressed by four main types of ionizers: bar, blower, spot, and specialized units. Each type serves specific applications in your printing environment and offers unique advantages for static elimination. Electrostatic discharge protection is crucial for maintaining print quality and equipment longevity.
Type | Primary Use | Key Feature |
---|---|---|
Bar | Workstation Coverage | Mounted 17-24" overhead |
Blower | Surface Treatment | Motorized air delivery |
Spot | Precision Control | Hand-held targeting |
Bar ionizers mount above your workstation, providing thorough static elimination through multiple emitter points. They're particularly effective when you need consistent coverage across your printing workspace. You'll find them ideal for mini-environments and workbench applications.
Blower-type units use compressed air or nitrogen to actively push ionized air toward your target surface. These systems are essential for preventing paper clinging during high-speed printing operations. You can choose between hand-held guns or mounted units with foot pedal operation, making them versatile for treating contamination and visual defects.
When you need precise static control, spot ionizers offer targeted solutions through hand-held guns or mounted units. They're perfect for detailed work in specific areas. For specialized printing operations like tampon printing, you'll find custom ionizing systems designed to match your specific machine requirements and printing processes.
Benefits of Static Control
Static control delivers four essential benefits that transform your printing operations: preventing static-related issues, improving safety, optimizing production processes, and enhancing quality.
When you implement static control, you'll prevent common issues like dust attraction and contamination that can compromise your print quality. You'll also minimize printing defects such as clogged nozzles and ink manipulation while protecting operators from unexpected shocks. The use of ion-generating technology effectively neutralizes static charges by balancing positive and negative ions. Increased production speeds demand proper static management for optimal performance.
Safety improvements are significant, as static control reduces the risk of fires and sparks in your facility. It also protects your electronic components and sensitive materials from ESD damage, ensuring your equipment remains reliable and operational.
Your production processes will run more smoothly with neutralized static charges on substrates. You'll notice better ink transfer, improved color consistency, and fewer paper jams. This means you can handle static-sensitive materials more effectively and maintain consistent workflow.
Quality and productivity gains become evident through reduced reject rates and fewer costly reprints. You'll achieve higher production speeds while maintaining print quality, and your static-sensitive materials will process more reliably.
These improvements directly impact your bottom line by increasing operational efficiency and reducing waste.
Cost Impact on Print Operations

At the heart of print operations, uncontrolled static electricity creates a considerable financial burden through multiple cost centers.
You'll face direct costs through increased material waste, as static attracts dust and debris to your printing surfaces, leading to poor print quality and rejected outputs. Your production efficiency suffers when you're forced to stop operations frequently for cleaning and adjustments.
The financial impact extends beyond immediate production issues. You're likely to encounter higher maintenance costs from static-damaged equipment, while your energy bills can spike due to inefficient static control methods.
When static disrupts your print quality, you'll also risk damaging your brand's reputation, potentially losing future business opportunities.
However, you can achieve substantial long-term savings by implementing effective static control systems.
You'll reduce maintenance requirements, especially with self-balance technology, while minimizing material waste and extending equipment lifespan. Systems without blowers can lower your energy consumption considerably.
Most importantly, you'll protect yourself from potentially catastrophic costs associated with static-related accidents, injuries, and fire risks that could otherwise result in OSHA reports and costly lawsuits.
Safety Concerns and Solutions
You'll need to implement robust shock prevention measures, such as properly grounded ionization systems, to protect your personnel from potentially dangerous static discharges during printing operations.
Managing fire risks requires you to maintain effective static control devices and monitor humidity levels, particularly in areas where flammable materials and vapors are present.
Your facility must strictly follow personnel protection standards, including regular safety training and the proper use of static control equipment, to create a secure working environment.
Shock Prevention Measures
The prevention of electrostatic shock in printer environments requires an all-encompassing approach to safety and control measures. You'll need to implement multiple static control solutions to guarantee your printing operations remain safe and efficient.
Start by installing ionizers near your printers, positioning them close to static-prone areas for ideal effectiveness. You'll find that both AC and DC ionizers work well, though DC models offer extended range and higher control capabilities.
Make certain you're maintaining proper humidity levels in your printing facility, as dry conditions can notably increase static buildup.
To maximize your static control efforts, you'll want to focus on ionizer balance. Unbalanced ionizers can create unwanted charges on ungrounded objects, so it's essential to use systems with sensor feedback and self-balancing technology.
You should also implement regular maintenance schedules, including cleaning emitter points and checking ionizer performance.
These measures won't just protect your equipment; they'll also enhance your productivity. You'll experience fewer static-related defects, reduced equipment damage, and improved worker safety.
Fire Risk Management
Managing fire risks in printing environments demands careful attention to static electricity control, especially when working with flammable materials like inks, solvents, and paper dust. You'll need to be particularly vigilant about static charges that can build up on rapidly moving substrates, as they're capable of igniting dangerous vapor-air mixtures or suspended particles.
Risk Factor | Control Measure |
---|---|
Flammable Solvents | Install anti-static bars and ionizers near solvent handling areas |
Moving Materials | Implement static neutralization systems at key friction points |
Paper Dust | Use ionizing blowers to prevent dust accumulation |
To protect your printing operation, you'll need to follow NFPA 77 guidelines for static electricity control. Start by conducting a thorough hazard assessment to identify all potential ignition sources and flammable substances in your facility. Then, implement appropriate static control solutions, such as strategically placed ionizers and anti-static bars. Don't forget to regularly test and maintain your static elimination equipment to guarantee it's working effectively. Remember, compliance with regulatory standards isn't just about following rules – it's about preventing potentially catastrophic fires and explosions that could harm your staff and damage your facility.
Personnel Protection Standards
Beyond fire prevention, protecting personnel from static-related hazards requires thorough safety protocols in printing environments.
Static electricity can cause unexpected shocks, attract harmful contaminants, and create unsafe working conditions around printing equipment. You'll need to implement extensive protection measures to safeguard your staff and maintain efficient operations.
To establish effective personnel protection standards, you must focus on these essential components:
- Train your staff in proper ESD (Electrostatic Discharge) procedures, including the correct use of grounding equipment and static-control devices specific to printing operations.
- Install and maintain ionizers with balanced ion output and automatic adjustment features to neutralize static charges effectively.
- Create designated static-controlled zones around sensitive printing equipment, complete with proper grounding systems and anti-static flooring.
- Equip your team with appropriate static-reducing clothing and accessories, particularly when handling sensitive printing components.
Regular maintenance and inspection of these protective measures are vital.
You'll need to monitor humidity levels, verify the effectiveness of static control devices, and confirm all grounding systems remain functional.
These standards not only protect your personnel but also help maintain consistent print quality and equipment longevity.
Choosing the Right Ionizer
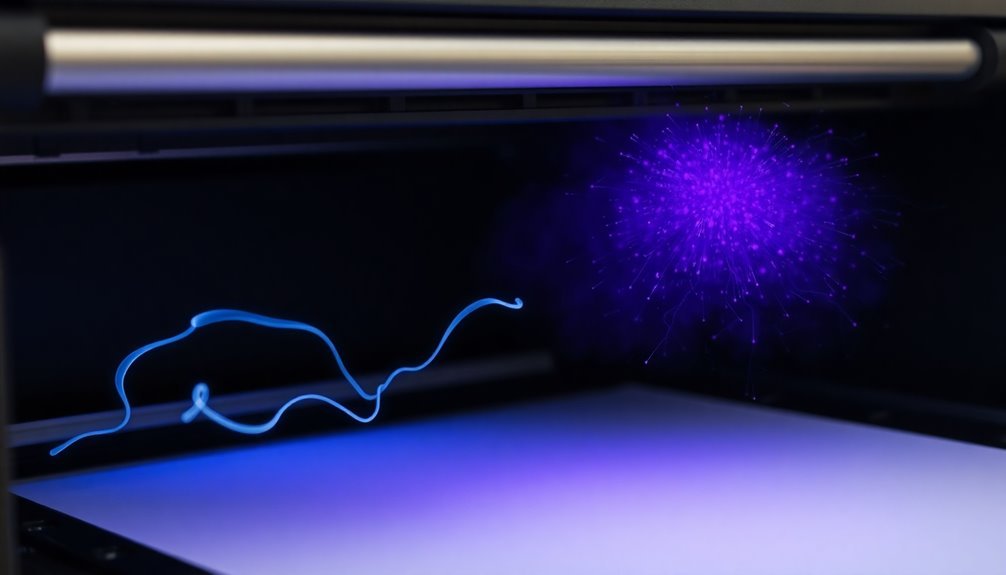
Selecting an appropriate ionizer requires careful consideration of your specific printing environment and requirements. You'll need to evaluate factors like space constraints, air movement sensitivity, and the type of static control needed for your printing operations.
Ionizer Type | Best For | Key Features |
---|---|---|
Air Ionizers | Large Areas | Compressed air delivery, effective cleaning |
Bar Ionizers | Wide Coverage | Self-diagnosis, versatile mounting |
Non-Blower | Delicate Work | No air movement, spot elimination |
For printing operations where paper movement is critical, you'll want to avoid systems that create excessive air disturbance. Non-blower ionizers might be your best choice for delicate paper handling, while bar ionizers work well for wider printing surfaces. If you're dealing with high-speed operations, consider bipolar ionizers with self-balancing technology to maintain consistent static elimination.
Look for features that'll reduce your maintenance needs, such as self-diagnosis and alarm outputs. You should also consider the long-term cost benefits – while premium ionizers might cost more initially, they often pay for themselves through improved efficiency and reduced static-related defects. Remember to check if the ionizer can be integrated with your existing printing equipment to maximize its effectiveness.
Proper Installation and Placement
You'll get the best performance from your static control ionizer by mounting it within 2 inches of the print path where static charges are most problematic.
For sheet-fed presses, position the ionizing bar near the feeder area to neutralize charges before sheets enter the press.
In web printing applications, you can install multiple ionizing bars strategically along the paper path to maintain consistent static control throughout the printing process.
Optimal Mounting Locations
Proper mounting location of static control ionizers represents three critical factors: height, obstruction, and distance to target.
When installing ionizers for your printer setup, you'll want to position them 17-24 inches above the work area while ensuring unobstructed airflow to effectively neutralize static charges.
For peak performance, you'll need to take into account whether to use ceiling-mounted or localized installations. While both options work, localized mounting often delivers better results due to faster response times and greater flexibility.
You can use L-brackets or DIN rail mounting systems with adjustable angles to achieve precise airflow direction.
Consider these key mounting principles for your printer's static control:
- Distance matters most – position ionizers as close as possible to target areas while maintaining recommended minimum distances.
- Keep the airflow path clear – avoid any obstructions between the ionizer and the target surface.
- Use angle-adjustable mounts to direct ionized air precisely where it's needed.
- Take into account the material properties of your printing substrates when determining peak mounting locations.
For complex setups, remember that DC ionization offers longer operational life than AC, though both require strategic positioning for maximum effectiveness.
Distance From Print Path
Critical distances between ionizer bars and print paths directly impact static elimination effectiveness. You'll need to position your ionizer bar extremely close to the media surface, ideally within 1/4-inch for induction ionizers. This proximity guarantees the ions can effectively neutralize static charges while minimizing environmental interference.
When you're installing your ionizer, remember that effectiveness diminishes as distance increases. You must place the bar precisely where static is most problematic, such as near feeding points or after dryers. For digital printing, mount your ionizer above the print path for continuous neutralization, while pad printing requires placement between the pad plate and substrate.
If you don't maintain proper distance, you'll face several problems. Your static elimination will become inadequate, leading to printing defects, dust attraction, and clogged nozzles.
You'll also risk ink manipulation issues and potential operator safety hazards from electrostatic discharge. To avoid costly reprints and production delays, confirm your ionizer bar maintains consistent proximity to the media surface.
Remember that both sides of the substrate may need neutralization, so position your equipment accordingly for complete coverage.
Maintenance and Performance Monitoring
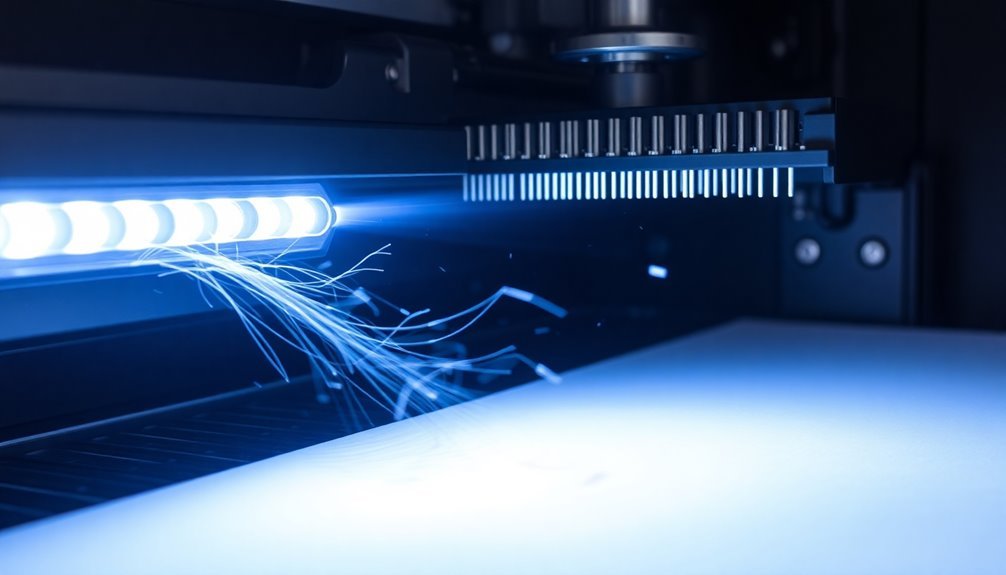
Regular maintenance and monitoring form the backbone of effective static control ionizer performance in printing environments. You'll need to clean emitter points periodically and watch for dust or ink buildup that can compromise your ionizer's effectiveness. As these devices age, their performance naturally degrades, making routine maintenance vital for maintaining ideal static control.
To guarantee your printer's static control system operates at peak efficiency, you'll want to implement these key monitoring practices:
- Use handheld static meters regularly to measure voltage levels and check for any emerging static issues.
- Monitor the balance between positive and negative ions, as this equilibrium is essential for proper neutralization.
- Pay attention to performance alarms and sensor feedback that indicate when maintenance is needed.
- Track ion output levels to determine when cleaning or replacement of components becomes necessary.
Your ionizer's technology type will influence its maintenance requirements. While CoreStat technology offers self-balancing and auto-cleaning features, traditional induction ionizers need more frequent attention.
Consider implementing sensor feedback systems that automatically adjust ionizer balance, as they'll help reduce your manual maintenance burden while maintaining consistent performance.
Environmental Factors and Considerations
Environmental conditions fundamentally shape the effectiveness of static control systems in printing operations.
You'll find that low humidity is particularly challenging, as it greatly increases static build-up in your printing environment. When humidity drops below 30-50%, you're likely to experience more static-related issues, especially when working with thermoplastic materials that require humidity levels above 40% for ideal static control.
Your printing materials themselves play a vital role in static generation. PVC, acrylic, and other thermoplastic materials are notorious static generators, and they'll require special attention in your static control strategy. When these materials experience friction during the printing process, they can accumulate substantial static charges.
You'll need to pay close attention to airflow around your ionizers, as it directly affects their performance. Air disturbances can disrupt the ionization process, potentially reducing its effectiveness.
That's why you'll benefit from using external sensors that help adjust your ionizers to compensate for environmental changes. For larger printing areas, you might want to take into account air-assisted ionizers, which can effectively neutralize static across broader surfaces while maintaining consistent performance despite environmental variations.
Print Quality Enhancement Methods
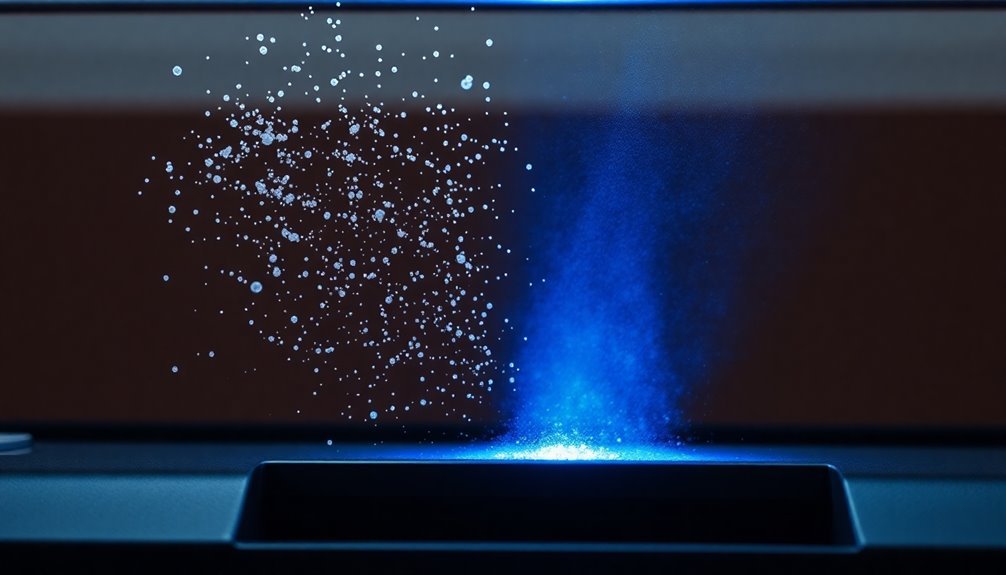
You'll find that proper ink distribution control starts with effective static elimination through strategically placed ionizers at key printing stages.
To enhance paper surface treatment, you can combine ionization methods with specialized air nozzles that simultaneously neutralize static and clean the substrate.
Your dust elimination efforts will work best when you implement both active static control devices and proper air filtration systems to prevent particle accumulation on print materials.
Ink Distribution Control Methods
Precise control of ink distribution plays an essential role in achieving ideal print quality across various printing technologies. In web-offset printing, you'll find that ink key distribution functions correct lateral ink spread, while ink key openings work together with distribution functions to regulate ink supply to the plate cylinder. The process maintains a linear relationship between ink film thickness on the fountain roller and ductor roller.
For best ink distribution control across different printing methods, you'll need to understand these fundamental aspects:
- Web-offset systems use equally-spaced ink flow adjustment devices with threaded ink keys that push against blade segments, allowing precise local control of ink feed.
- Inkjet systems rely on precisely positioned nozzles ejecting ink at 5-10 meters per second, with optical encoders controlling dot placement.
- Rotogravure printing utilizes coating layers with kaolin clay particles to enhance ink retention and achieve higher color density.
- Automatic ink supply systems with closed pump mechanisms guarantee consistent ink flow while reducing waste and contamination risks.
The rotation control unit works with ratchet settings to manage fountain roller rotation, while ink saturation blocks connect ink thickness to density values for consistent output.
Paper Surface Treatment
Effective paper surface treatment consistently relies on static control ionizers to enhance print quality and prevent costly production issues. You'll find that proper static control prevents paper jams, misfeeds, and dangerous operator shocks while ensuring ideal ink distribution across surfaces.
Treatment Method | Purpose | Benefits |
---|---|---|
Humidification | Moisture Control | Reduces static in dry environments |
Electric Ionization | Charge Neutralization | Breaks down air molecules into balanced ions |
Chemical Treatment | Surface Conditioning | Improves print adhesion and quality |
Modern ionizers like KEYENCE's SJ-H Series offer high-speed static elimination with minimal airflow, making them perfect for precise printing applications. You'll want to position static eliminators near feeding points or over printing press feeder piles for maximum effectiveness. For thorough coverage, you can install static bars between the pad plate and substrate, flooding the area with neutralizing ions.
Today's advanced technologies include maintenance-free options like the SJ-F700 Series, which features automatic probe cleaning. You'll also find ultra-small static elimination heads that work in tight spaces, ensuring you can implement effective static control regardless of your printer configuration.
Dust Elimination Techniques
Through extensive dust elimination techniques, static control ionizers serve as the frontline defense against print quality issues. You'll find that these devices effectively neutralize static charges that typically attract dust particles to your printing surfaces.
By increasing air conductivity, ionizers create an environment where dust particles are less likely to settle on your substrates, leading to cleaner prints and fewer quality defects.
To maximize dust elimination in your printing operations, you'll want to implement these proven techniques:
- Position ionizers strategically near feeding points and between substrates and printing plates to neutralize charges before dust can accumulate.
- Maintain ideal humidity levels alongside ionization to create a thorough dust control system.
- Choose the right type of ionizer (electric, induction, or corona discharge) based on your specific printing process and materials.
- Regularly clean and maintain your ionizers to guarantee consistent performance and effectiveness.
You'll notice significant improvements in print quality when you combine proper ionizer placement with consistent maintenance.
This approach not only reduces dust-related defects but also minimizes production delays and costly reprints, ultimately improving your overall printing efficiency.
Future of Static Control Technology
Innovation in static control technology continues to reshape the printing industry's future, with several key developments on the horizon.
You'll see more sophisticated ionization systems integrating seamlessly with your existing production equipment through PLCs and HMI interfaces, allowing for automated static management throughout your printing process.
You can expect to encounter more efficient DC ionizers with extended ranges and improved air amplification ratios, making static elimination more effective across larger areas.
These systems will incorporate advanced humidity control features, especially vital if you're operating in low-humidity environments.
The future of static control will bring you maintenance-free solutions that reduce downtime and boost productivity.
You'll benefit from specialized ionizers designed specifically for printing applications, featuring enhanced durability and longer service life.
The integration of static control with other production processes will become more streamlined, offering you extensive solutions rather than standalone devices.
Watch for developments in air-assisted technologies that combine static elimination with contaminant control, helping you maintain both static-free environments and cleaner printing surfaces.
These advancements will make static control more cost-effective and efficient for your printing operations.
Frequently Asked Questions
Can Ionizers Interfere With Wireless Networks or Electronic Devices Near Printing Equipment?
You shouldn't worry much about interference since modern ionizers are designed to minimize EMI and RFI. However, it's best to follow manufacturer guidelines for placement to avoid any potential impact on nearby electronics.
How Long Does It Typically Take to See Results After Installing Ionizers?
You'll notice immediate results after powering on ionizers, with significant static reduction within seconds. For ideal printing quality improvements, you'll see clear benefits during your first few print runs after installation.
Do Different Colored Papers or Specialty Stocks Require Different Ionizer Settings?
Yes, you'll need different ionizer settings for colored and specialty papers because they have varying static properties. Adjust your ionizer's power and range based on the paper's composition and surface characteristics.
What Happens if an Ionizer Malfunctions During a Critical Print Run?
You'll notice immediate quality issues like cloudy prints and paper jams. Your production will slow down or stop completely, and you'll need to implement backup static control measures or fix the ionizer quickly.
Are There Specific Cleaning Solutions Recommended for Maintaining Ionizer Effectiveness?
You'll want to use distilled water as your primary cleaning solution for ionizers. You can also safely use specialized anti-static cleaners or isopropyl alcohol, but always avoid tap water and harsh chemical cleaners.
In Summary
You'll find that static control ionizers are essential investments for maintaining print quality and operational efficiency. They'll reduce costly production delays, minimize waste, and protect your equipment from static-related damage. By implementing proper static control measures, you're ensuring consistent print quality while extending the life of your printing equipment. As printing technology advances, static control solutions will continue to evolve alongside these developments.
Leave a Reply