Static control tools help you maintain a safe ESD-protected workspace through several key measurements. You'll need ESD meters to detect static voltage levels and polarity, plus humidity monitors to guarantee levels stay above 45% RH. Grounding testers verify your surfaces and equipment using methods like the 3-point fall-of-potential test, while surface resistivity meters check if materials meet safety standards. Don't forget ionizer performance monitors and charge decay analyzers to assess how quickly static dissipates. Understanding these essential tools and their proper use will strengthen your workspace's ESD protection strategy.
Understanding ESD Meter Functions
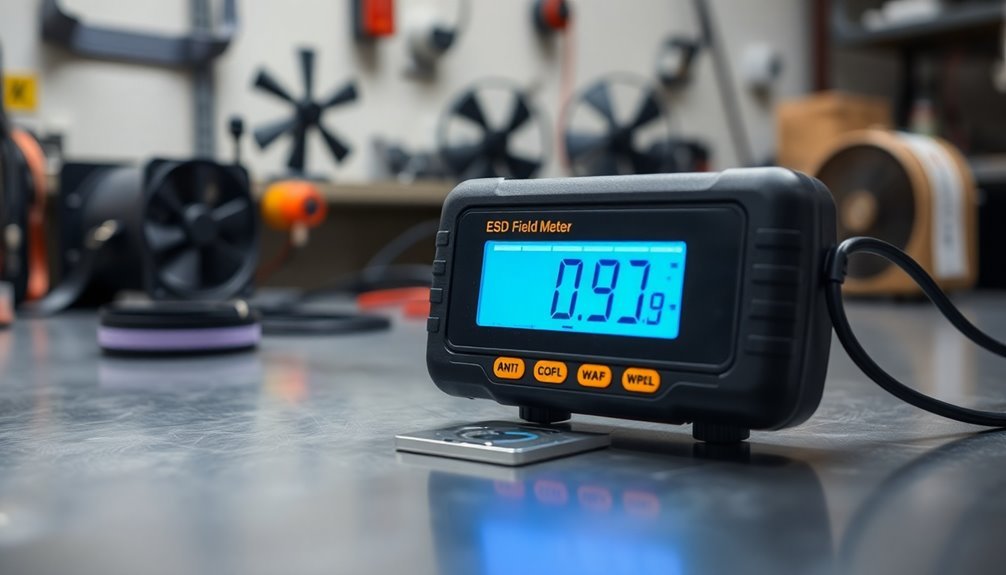
When working with sensitive electronic equipment, understanding how ESD meters function is essential for maintaining a safe workspace. These devices measure static voltage without transferring the charge to the instrument, allowing you to detect potential risks before they cause damage.
You'll be able to determine both the presence and polarity of static charges in your work environment. Annual calibration is necessary to ensure accurate testing results.
Your ESD meter can measure voltages ranging from 0 to ±19.99 kV with ±5% accuracy, but you'll need to verify proper grounding for reliable measurements.
Different types of meters serve various purposes: you can use handheld meters for portable testing, fieldmeters for measuring electric fields, or charge plate monitors to evaluate ionization systems.
When you're using an ESD meter, remember that environmental factors like humidity and temperature can affect your readings. You'll need to maintain proper distance between the meter and the object being measured, and always verify both you and the meter are correctly grounded.
Regular calibration of your meter is vital to maintain its accuracy and reliability. By understanding these fundamental functions, you'll be better equipped to protect sensitive components and maintain a safe workspace.
Common Static Detection Tools
Building on your knowledge of ESD meters, you'll need several other static detection tools to maintain a thorough workspace safety system. Similar to static code analysis, these tools help identify issues before they become problems. You'll find bar ionizers particularly effective at neutralizing static electricity, with their quick 0.3-second response time and replaceable needle cartridges that minimize downtime.
For monitoring purposes, you can use the IZH10 handheld meter to diagnose electrostatic fields or install the IZD10 sensor for fixed-location monitoring. The IZE11 monitor will translate these readings into LED displays and provide necessary outputs for your safety systems.
Device Type | Function | Key Feature |
---|---|---|
Bar Ionizers | Static Neutralization | 0.3s response time |
IZH10 Meter | Field Detection | Portable diagnosis |
IZD10 Sensor | Fixed Monitoring | Continuous tracking |
Anti-static Fittings | Static Prevention | Copper-free vacuum use |
Ion Box | Complete Treatment | Auto-sensing operation |
You'll also want to incorporate anti-static equipment like Series KA fittings and TAS/TAU tubing in your air pressure systems. For specialized applications, consider using the ZVB Ion Box, which combines neutralization with dust removal for sensitive components like optical glass and medical devices.
Humidity Monitoring Equipment
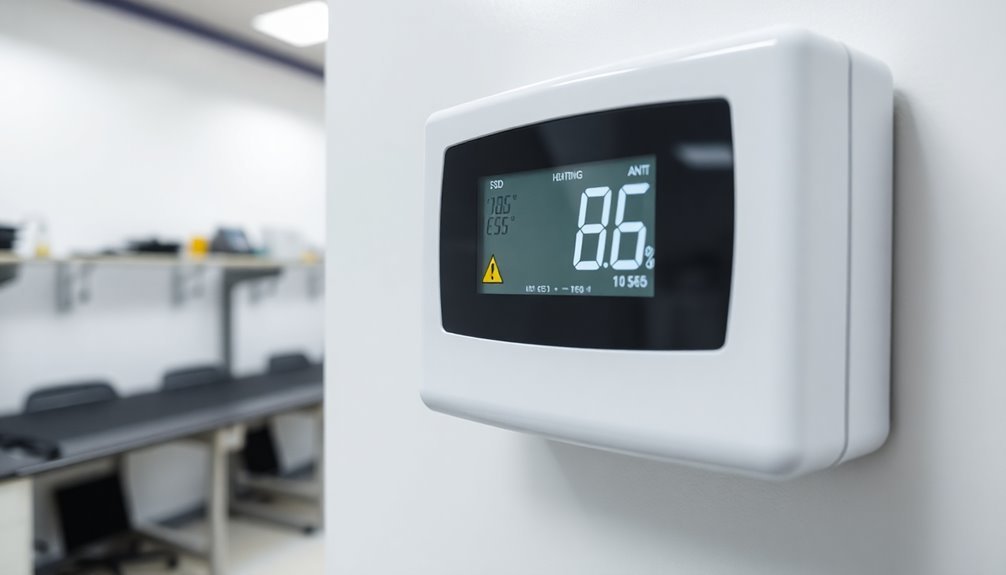
Since humidity levels directly affect static build-up in workspaces, you'll need reliable monitoring equipment to maintain ideal conditions. Your facility should maintain humidity above 45% RH, with 55% RH being ideal for eliminating static build-up completely.
To achieve this, you'll want to employ specialized measurement tools like the SK Series that can simultaneously track both humidity and static charge levels. Steam and fog systems are popular choices for maintaining consistent humidity control.
Monitoring becomes especially critical near heat-generating machinery, where localized dry air pockets can form even in otherwise humid environments. To combat these issues, you can use handheld devices like the IZH10 electrostatic meter to spot-check problem areas throughout your workspace. These tools help you identify where you might need additional humidity control measures.
For thorough monitoring, you should install permanent sensors that continuously track humidity levels, particularly in areas prone to static problems. When combined with precision humidity control systems like MicroCool FOCUS, these monitoring tools enable you to maintain ideal conditions.
Grounding Cord Test Methods
Testing the integrity of your grounding cords requires selecting from among several proven methods, each with distinct advantages.
The 2-point method offers quick testing of connections and conductors but isn't as accurate as other methods. You'll connect P1 and C1 terminals to the ground electrode under test, and P2 and C2 to a separate metallic grounding point. The electrode must be outside spheres of influence of secondary grounding points for accurate readings.
For more reliable results, you'll want to use the 3-point (fall-of-potential) method. This approach requires you to drive a probe into the earth at ten times the diagonal length of your grounding system, with a second probe placed at the diagonal length.
You'll need to isolate the system from power utilities and remove external connections, but you'll get the most thorough resistance measurements.
If you're working with live systems, the clamp-on method is your best option. It uses a transformer to induce oscillating voltage while the system remains connected to utilities.
Remember that all methods require proper spacing between test points to avoid interference. When accuracy is vital, follow IEEE Standard 81 guidelines for fall-of-potential testing to guarantee reliable results.
Ionizer Performance Measurements
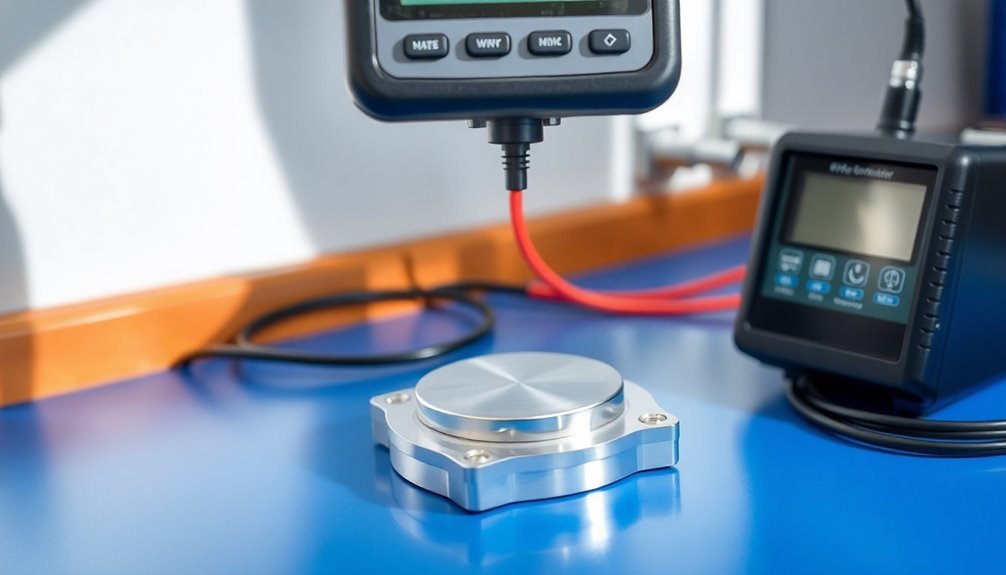
A reliable ionizer performance measurement system centers on the Charged Plate Monitor (CPM), which serves as the industry standard for evaluating static control effectiveness.
When you're measuring ionizer performance, you'll need to focus on two critical parameters. The balance (offset voltage) shows you how close the ionization gets to neutral zero volts, while the discharge time tells you how quickly your ionizer can reduce a ±1000V charge to 10% of its starting value. Similar to medical facilities that place sharps containers at optimal heights, proper positioning of measurement equipment is crucial for accurate readings.
You'll want to verify your measurements comply with ANSI/EOS/ESD S3.1 standards.
For quick diagnostic work, you can use handheld static meters like TAKK's Model 5740, which measures charges up to 200kV. These tools help you position static control equipment and troubleshoot issues effectively.
Remember that accurate measurements depend on proper calibration of your testing equipment, and you'll need to evaluate potential limitations when testing AC ionizers with traditional CPM methods. For the most precise results, you should use properly calibrated electrostatic voltmeters.
Wrist Strap Testing Devices
You'll need to test your wrist strap daily using either an offline tester for quick checks or a continuous monitoring system for real-time protection.
Watch for warning signs of wrist strap failure, including inconsistent readings, loose connections, or visible wear on the band or cord.
Regular testing should include both resistance measurements and visual inspections of all components to guarantee your ESD protection remains reliable. Advanced testing stations allow you to log test data for improved quality control tracking.
Testing Methods and Frequency
Proper wrist strap testing combines three essential components: reliable testing devices, standardized methods, and consistent frequency checks. Your testing protocol should align with EN 61340-5-1 Annex A Test method A.1, which establishes the standard measurement approach using voltages between 9 V d.c. to 100 V d.c. The best approach is to conduct the tests while the wrist strap is worn, including checking the band, ground cord, and skin contact.
You'll need to maintain a strict testing schedule based on your workspace's ESD risk exposure and product value. For daily-use wrist straps, you should conduct tests at the start of each shift.
If you're handling high-value components, you'll want to implement continuous monitoring systems.
Key testing requirements you must follow:
- Test your wrist strap daily if you use it every day
- Verify both the strap's resistance and proper ground connection
- Document test results unless using continuous monitoring systems
- Respond immediately to any test failures before handling sensitive components
If you're working with particularly sensitive or valuable products, you'll benefit from continuous monitoring systems like the CM400 series. These devices provide instant alerts for grounding issues and eliminate the need for manual testing records, ensuring uninterrupted protection throughout your work session.
Common Failure Warning Signs
Testing protocols help identify problems, but recognizing warning signs early can prevent ESD risks before formal testing.
When using testing devices, you'll notice several clear indicators of wrist strap failure. A high fail alarm signals resistance above 35 megohms, while a low fail alarm indicates resistance below 750K ohms, often due to a shorted resistor. Watch for yellow LEDs that suggest poor skin contact, and red LEDs that warn of safety hazard conditions like lost resistivity.
High skin resistance from dry conditions or wearing the strap over clothing can disrupt conductivity. If you notice intermittent failures, check for a soiled wristband or damaged coil cord. Daily wrist strap testing is essential unless continuous monitoring systems are in place.
Environmental factors like humidity and temperature changes can affect your strap's performance, so monitor these conditions closely.
Don't ignore audio signals from your testing device – they're designed to alert you to pass/fail status immediately. When you spot physical damage like cuts or frays in the strap or cord, replace the equipment immediately.
ESD Mat Resistance Checks
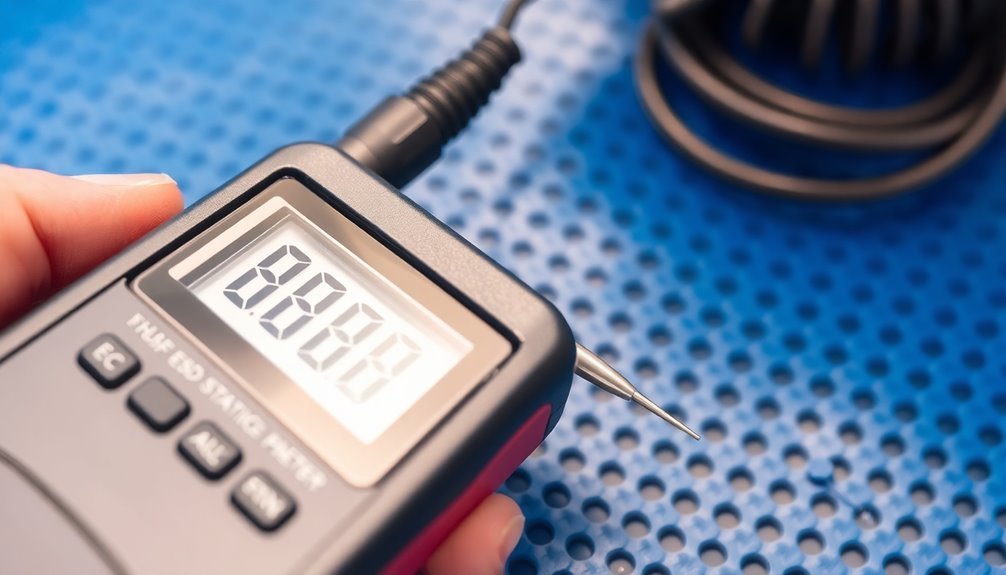
Your ESD mat's resistance check should include both resistance-to-ground (RTG) and point-to-point (RTT) measurements using the 5-pound electrodes placed according to ANSI/ESD S4.1 standards.
You'll need to verify that your mat's resistance falls between 1 x 10^6 and 1 x 10^12 ohms to guarantee proper static dissipation.
Regular surface conductivity tests will help maintain your workspace's ESD protection and prevent potential damage to sensitive electronic components.
Point-to-Ground Testing Methods
To verify ESD mats function effectively, point-to-ground resistance checks must be performed using specific equipment and procedures outlined in ANSI/ESD S4.1 standards. You'll need a surface resistivity meter and five-pound electrodes to conduct accurate resistance-to-ground (RTG) measurements. These tests guarantee your mat maintains proper static dissipative properties within the required range of 1 x 10^6 to 1 x 10^9 ohms.
When performing point-to-ground testing, follow these essential steps:
- Remove all ESD-sensitive devices from the mat's surface before beginning your measurements
- Connect one five-pound electrode to your resistance meter and another lead from the meter to the mat's ground snap
- Place the electrode 2 inches away from any edge, targeting the most frequently used area of the mat
- Start testing with 10 volts, then switch to 100 volts if the resistance reading is ≥1.0 x 10^6 ohms
You'll want to record the resistance measurements displayed on your meter for documentation purposes. If you're unsure where to test on the mat's surface, choose two points near the center for consistent results.
This verification process helps maintain workspace safety and guarantees your ESD protection measures remain effective.
Routine Resistance Value Checks
Regular monitoring of ESD mat resistance values guarantees your workspace maintains essential static protection standards. You'll need to perform both RTT (Resistance Top-to-Top) and RTG (Resistance to Groundable Point) measurements using a Surface Resistivity Meter to comply with ANSI/ESD S4.1 standards.
When conducting RTT tests, place two 5-pound electrodes 10 inches apart on your mat's most used area. Keep them 2 inches from edges and 3 inches from grounding points.
For RTG testing, connect one lead to a ground point and place the other electrode at the mat's furthest convenient point. Start your testing at 10 volts, but switch to 100 volts if resistance exceeds 1.0 x 10^6 ohms.
Your mat's resistance should fall between 1 x 10^6 and 1 x 10^9 ohms to pass inspection. Remember to remove ESD-sensitive devices before testing and verify proper grounding connections.
You'll want to conduct these checks periodically to maintain effectiveness. If your readings fall outside the acceptable range, you'll need to replace your mat to maintain workplace safety standards.
Surface Conductivity Verification
To guarantee your ESD mat functions properly requires routine surface conductivity verification through resistance checks. You'll need to perform both resistance-top-to-top (RTT) and resistance-to-groundable point (RTG) tests using an ESD meter kit and following ANSI/ESD S4.1 standards.
To verify surface conductivity effectively, you'll want to understand these essential measurements:
- For RTT testing, place two 5-pound electrodes 10 inches apart and 2 inches from any edge of your mat, then measure the resistance between these points.
- When conducting RTG tests, clip the black test lead to your ground point and position one electrode at the furthest convenient point on the mat's surface.
- Check that your readings fall within the dissipative range of 1 x 10^6 to 1 x 10^9 ohms, which confirms proper static charge dissipation.
- Verify that your mat isn't exhibiting insulative properties (above 1 x 10^12 ohms/square) or overly conductive characteristics (below 1 x 10^5 ohms/square).
If your measurements fall outside these ranges, you'll need to replace your mat to maintain workplace safety and protect sensitive electronic components from ESD damage.
Surface Resistivity Testing Equipment
Safety in electrical workspaces relies heavily on surface resistivity testing equipment – specialized tools that measure how effectively materials conduct or resist electrical current. You'll find these devices available in several formats, from handheld meters to extensive digital test kits, each designed to provide measurements in ohms per square.
When you're testing workspace surfaces, you can choose from equipment with different features to match your needs. Most models offer selectable test voltages of 10V and 100V, while some include automatic zeroing and power shut-off functions. You'll also find units that monitor ambient temperature and humidity, giving you a complete picture of your testing environment.
To maintain ESD control programs effectively, you'll need to use these tools to test various surfaces, from flooring to workbenches. The equipment helps you verify compliance with standards like ASTM D257 and IEC 61340-4-1.
You can use handheld meters like the ACL 395 for quick checks or opt for complete test kits like the SRM500K for more detailed analysis. Whether you're selecting materials for electronics manufacturing or conducting routine safety checks, surface resistivity testing equipment guarantees your workspace meets essential safety requirements.
Air Ionization Balance Meters
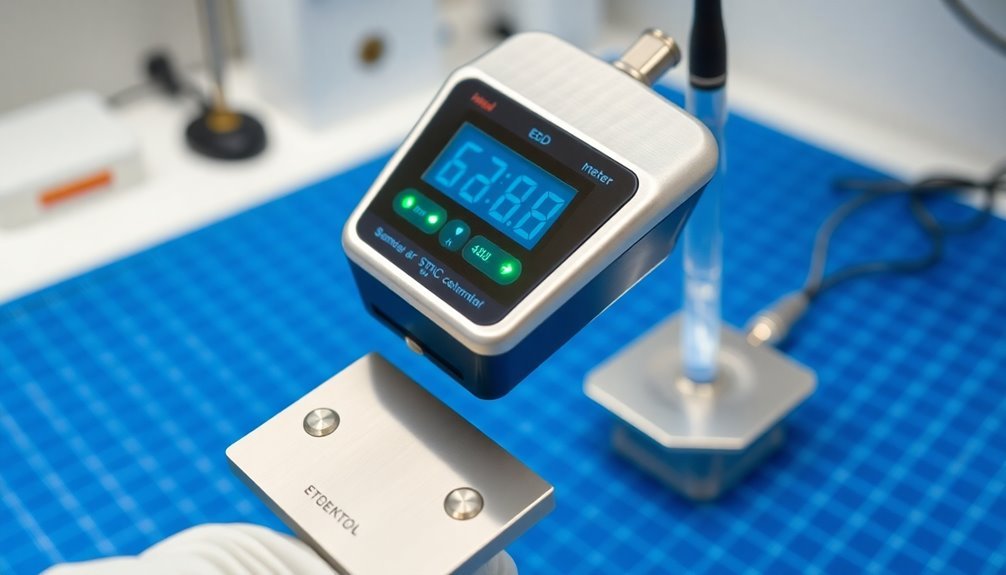
Beyond surface testing, effective ESD control demands precise monitoring of air ionization levels in your workspace. Air ionization balance meters help you detect electrostatic threats and measure deviations from electrical ground in volts.
You'll find these devices available in various configurations, from ceiling-mounted systems to portable charge plate monitors (CPMs), all designed to maintain your workspace's proper static control.
These essential tools support ISO S20.20 ESD compliance and offer continuous monitoring through dual-purpose sensors. When you're setting up your static control program, you'll want to think about these critical features:
- Real-time LCD displays that show instant measurements of ion balance
- Adjustable sensitivity levels with passcode protection for secure operation
- 20 picoFarad capacitance in CPMs for precise measurements
- Built-in data logging capabilities for compliance documentation
You can choose between localized workstation ionizers for targeted protection or room-wide systems depending on your needs. Whether you're working in a cleanroom or managing production areas with sensitive electronics, these meters maintain the right balance of positive and negative ions to prevent costly ESD damage.
Footwear Resistance Testing Systems
In accordance with international safety standards, static dissipative footwear plays a critical role in controlling electrostatic discharge risks. International standards like EN ISO 20345:2011 and ASTM F2413 specify resistance ranges between 100 KΩ to 1000 MΩ, while NFPA 77 and IEC TS 60079-32-1 recommend a narrower range of 1-100 MΩ.
You'll find two primary testing methods for verifying footwear compliance. The first involves using testers like Sole-Mate II, which measures resistance between a handheld metal bar and a floor plate while you're wearing the shoes.
The second method uses metal shot pellets inside the footwear placed on an electrode plate, commonly used in QIMA labs.
To maintain accurate readings, you'll need to take into account several factors. Environmental conditions can markedly affect electrical resistance measurements, and proper footwear maintenance is essential.
You should implement regular testing procedures and verify that your staff receives proper training on tester usage.
For enhanced workplace safety, you can integrate systems like Sole-Mate II with access control systems. This integration verifies that only personnel wearing compliant footwear can enter sensitive areas, helping you maintain consistent ESD protection throughout your facility.
Charge Decay Time Analyzers

You'll find charge decay time analyzers essential for monitoring how quickly static charges dissipate from workplace materials in real-time.
Your analyzer's display will show discharge curves as they happen, letting you track the rate at which potentially harmful charges diminish from various surfaces.
These tools also enable you to assess surface resistivity, ensuring your workplace materials meet safety standards and maintain proper static-dissipative properties.
Real-Time Decay Monitoring
Real-time decay monitoring represents a critical aspect of workspace safety through specialized charge decay time analyzers. You'll need to understand how these tools continuously track the dissipation of static charges in your workspace to maintain proper ESD protection.
Using devices like the JCI155 Charge Decay Time Meter or SCS 711 Charge Analyzer, you can effectively monitor static decay in real-time.
To guarantee accurate measurements, you'll need to follow these essential steps:
- Condition your materials at 50% relative humidity for at least 12 hours before testing.
- Apply a 5000V charge using corona discharge units to the material surface.
- Use high-impedance voltmeters to record the decay curve.
- Monitor field strength with electrostatic field meters at fixed distances.
You'll find these measurements essential for maintaining compliance with standards like MIL-STD-3010 and EIA-541. By implementing real-time monitoring, you're actively protecting sensitive electronic components and guaranteeing your workspace meets industry requirements.
The continuous data from these analyzers helps you identify potential ESD risks before they cause damage, making them an invaluable tool in electronics manufacturing and handling environments.
Surface Resistivity Assessment
Through precise measurement of static charge dissipation, surface resistivity evaluation forms a cornerstone of workplace ESD protection.
You'll find tools like the JCI 155v6 and SCS 711 Charge Analyzers that measure how quickly static charges dissipate from material surfaces, helping you evaluate if your workspace materials meet safety standards.
When you're using these analyzers, you'll be able to set specific start voltages (600-1100V) and stop voltages (1-500V) to test material performance. The instruments provide graphical displays of decay curves, and you can use specialized software like JCI Graph to analyze your results more thoroughly.
You'll need to maintain these tools properly, including annual calibration, to guarantee accurate measurements. When conducting tests, you must follow proper setup procedures and condition materials at specific humidity levels.
These analyzers don't just help you comply with standards like MIL-STD-3010; they're essential for quality control in manufacturing, packaging, and electronics industries. By regularly evaluating surface resistivity, you're actively preventing ESD-related damage to products and guaranteeing workplace safety measures remain effective.
Static Voltage Field Meters
Static voltage field meters serve as essential guardians in modern workspaces, using non-contact sensors to measure electrostatic fields and surface voltages. These portable devices offer reliable measurements that aren't affected by probe-to-surface distances, making them invaluable for protecting sensitive equipment and ensuring personnel safety.
You'll find these meters equipped with user-friendly features like digital displays and data logging capabilities, allowing you to monitor static levels effectively. When you're working in manufacturing, cleanrooms, or hospitals, these tools help you maintain strict ESD compliance and prevent costly damage to electronic components.
Here's what makes static voltage field meters vital for your workspace safety:
- They provide real-time measurements of both initial peak voltage and decay rates
- They include alarm systems that alert you when static levels become dangerous
- They work across diverse industries, from electronics to pharmaceuticals
- They help you create and maintain static-safe work areas that protect both equipment and personnel
Whether you're managing a production line or overseeing a cleanroom, these meters form an essential part of your static control strategy, helping you maintain operational efficiency while meeting safety standards.
Frequently Asked Questions
How Often Should Static Control Tools Be Calibrated for Optimal Performance?
You'll need to calibrate your static control tools daily to yearly, depending on usage frequency and environment risks. For high-use settings, calibrate weekly, while less demanding environments may require monthly or annual checks.
Can Static Control Tools Be Shared Between Different Workstations Safely?
You shouldn't share static control tools between workstations, as it risks cross-contamination and compromises ESD safety. If you must share, guarantee proper grounding and cleaning between uses to maintain protection.
What Temperature Conditions Affect the Accuracy of Static Control Measurements?
Your static control measurements' accuracy can be affected by temperature fluctuations, strain gauge errors, thermoelectric voltages, and material limitations. You'll need proper compensation techniques like Wheatstone bridges for reliable readings.
Do Wireless Static Control Monitoring Systems Provide Reliable Workplace Safety Data?
Yes, you'll find wireless static control systems provide reliable workplace safety data through real-time monitoring, self-organizing networks, and thorough failure detection. They're especially effective when integrated with WirelessHART networks for continuous monitoring.
Which Static Control Tools Require Specialized Training Beyond Basic ESD Certification?
You'll need specialized training for continuous monitoring systems, ESD event detectors, and ionization equipment. These advanced tools require expertise in calibration, data analysis, and troubleshooting beyond basic ESD certification requirements.
In Summary
You'll need a thorough array of static control measurement tools to maintain a safe workspace. Rely on ESD meters, field detectors, and humidity monitors for daily checks. Don't forget to regularly test your grounding equipment, ionizers, and footwear using specialized meters. By consistently measuring and monitoring these elements, you're protecting sensitive components and ensuring your workspace meets necessary ESD safety standards.
Leave a Reply