You'll want to prioritize three key types of ESD storage materials to protect your sensitive electronics effectively. Static shielding bags with Faraday Cage protection offer the highest level of defense, while anti-static foam trays provide both physical and static protection during handling. For long-term storage, consider ESD-safe storage cabinets and totes made from conductive or static dissipative materials with surface resistance ratings between 10^5 and 10^11 ohms/square. Don't forget moisture barrier bags for components that need additional environmental protection. Understanding the specific properties of each material type will help you create the ideal ESD-safe storage solution.
Understanding ESD Storage Fundamentals
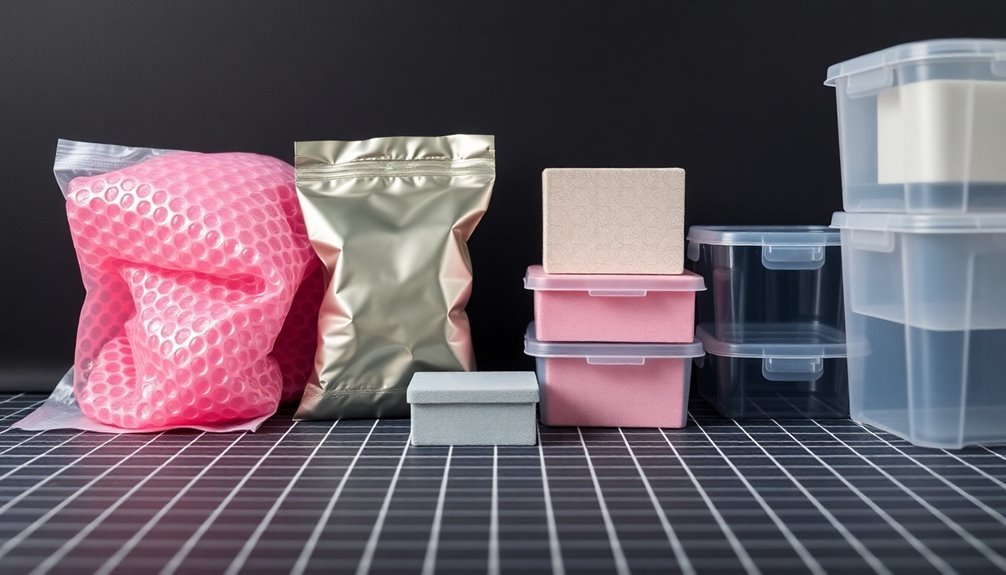
Nearly every electronic component today requires protection from electrostatic discharge (ESD), a phenomenon where static electricity rapidly transfers between objects. As electronic devices become increasingly sensitive due to their smaller circuitry and faster speeds, proper ESD protection is vital for maintaining product reliability and productivity in the electronics industry.
To protect your sensitive components, you'll need to understand three main categories of ESD storage materials. Conductive materials, with resistance between 10^-5 to 10^6 ohms per square, allow electrons to flow easily and include metals and carbon-based materials. Proper storage requires grounded shelving units with specialized conductive materials to safely house components.
Dissipative materials, ranging from 10^7 to 10^9 ohms per square, provide a controlled discharge path that's safer for your components. Anti-static materials, with resistivity between 10^10 to 10^12 ohms per square, help prevent triboelectric charging.
You'll find these materials implemented in various storage solutions, including shielding bags that use the Faraday Cage effect to keep charges on the outer surface. When selecting storage materials, you should prioritize those that offer appropriate resistance levels and shielding capabilities for your specific components' sensitivity levels.
Essential ESD Storage Materials
When you need specialized solutions, consider ESD foam trays for fragile items or blister trays with individual compartments. These options combine physical protection with static dissipation properties. Storage facilities provide secure spaces for long-term component protection against static build-up.
For packaging needs, you'll want to select from various bag types. Static shielding bags provide Faraday Cage protection, while antistatic poly bags offer basic ESD protection.
For moisture-sensitive components, use ESD moisture barrier bags that protect against multiple threats, including corrosion and physical damage. Metal-out bags are your best choice for critical electronics requiring lower resistance readings.
Choosing Anti-Static Storage Solutions
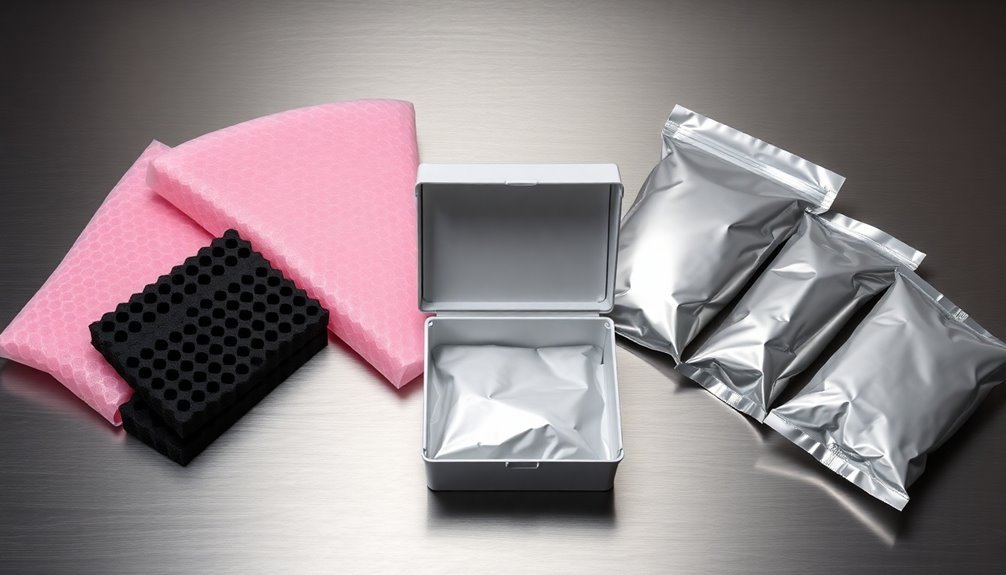
When selecting anti-static storage solutions, you need to evaluate different ESD storage grades based on your specific protection requirements and industry standards.
You should verify that the materials meet established quality benchmarks, including surface resistivity measurements and decay time specifications.
Cost-effective protection can be achieved by matching the right ESD materials to your components' sensitivity levels, whether through static-dissipative containers, conductive packaging, or shielding materials. Stainless steel components provide superior durability and conductivity for long-term storage needs.
Key Considerations
- Material Selection: Choose the correct material for your ESD storage needs. For example, conductive fiberboard, antistatic polypropylene, and static-dissipative materials are commonly used.
- ESD Standards: Ensure compliance with relevant ESD standards such as ANSI/ESD S6.1 for grounding and ANSI/ESD S541 for packaging materials.
- Environmental Factors: Consider whether moisture is an issue and if the items inside the ESD storage are sensitive to physical damage or sharp objects.
- Storage and Transportation: Determine if the ESD storage solutions will be used within an Electrostatic Protected Area (EPA) or if they will be transported outside of an EPA.
- Functionality: Choose storage solutions that are robust, easy to clean, and suitable for both heavyweight and lightweight supplies. Options include ESD bins, cabinets, drawers, and PCB holders.
Compliance and Quality
- Ensure the ESD storage solutions comply with international standards such as EN 61340-5-1 and other relevant requirements.
- Verify that the anti-static properties of the materials are durable and long-lasting.
Application-Specific Solutions
- For storage, consider collapsible conductive totes that provide excellent ESD protection and reduce storage and shipping costs.
- For sensitive components, use ESD storage counters, cabinets, and PCB holders that offer effective anti-static protection.
Selecting ESD Storage Grade
Proper selection of ESD storage grade requires a thorough understanding of your components' ESD sensitivity levels. You'll need to review manufacturer data sheets for HBM and CDM ratings, which are tested according to ANSI/ESDA/JEDEC standards JS-001 and JS-002. While these qualification voltages don't strongly correlate with field static voltages, they're essential for determining appropriate protection levels.
When selecting storage materials, you'll encounter various options including conductive polypropylene boxes, static shielding containers, and fiberboard solutions. To ensure maximum protection, all components should be stored in low charging materials to minimize triboelectric charge generation. You can choose between high-conductive or low-conductive packing foam for additional protection inside these containers.
Your selection should align with your ESD control plan, which must comply with EN 61340 Part 5-1 standards.
Consider the material's surface resistance and resistivity properties when making your choice. You'll find three main categories: static-dissipative, static-shielding, and conductive materials. Each offers different protection levels suited to specific component needs.
Remember that proper ESD storage solutions don't just protect your components – they'll improve productivity and reduce replacement costs by preventing static-induced damage during storage and transportation.
ESD Material Quality Standards
Building on your storage grade selection, you'll need to verify that your chosen ESD materials meet established quality standards.
Four primary standards govern ESD storage materials: ANSI/ESD S20.20, IEC 61340-5-1, JEDEC JESD625B, and MIL-STD-1686. Each standard serves specific industries and applications, guaranteeing proper protection of sensitive electronic components.
For general electronics manufacturing, you'll want to focus on ANSI/ESD S20.20, which provides detailed guidelines for creating electrostatic protective areas and specifies requirements for packaging materials. Regular compliance audits and testing help maintain ESD control effectiveness over time.
If you're working with European markets, make certain your materials comply with IEC 61340-5-1.
For semiconductor manufacturing, JEDEC JESD625B offers stringent specifications tailored to protect semiconductor devices.
Military suppliers must adhere to MIL-STD-1686 requirements.
When evaluating materials against these standards, check for specific resistance limits, test method compliance, and proper documentation. Your materials should demonstrate appropriate static dissipation properties and meet the required specifications for your application.
Don't forget to verify that your supplier can provide certification documentation proving compliance with the relevant standards.
Cost-Effective Protection Solutions
Several cost-effective ESD storage solutions exist that don't require breaking your budget while maintaining essential protection for sensitive electronic components. You'll find that conductive materials like stainless steel and static-dissipative plastics offer reliable protection while remaining cost-efficient over time. When you're selecting storage options, focus on materials that provide both ESD protection and space efficiency. The automated storage systems deliver 99.9% picking accuracy while maintaining robust ESD protection standards.
Solution Type | Cost-Saving Feature | Protection Level |
---|---|---|
Conductive Bins | Reusable & Durable | High Protection |
Adjustable Shelving | Space Optimization | Medium Protection |
Divider Systems | Customizable Sizing | Medium-High Protection |
Storage Cabinets | Climate Control | Maximum Protection |
ESD-Safe Containers | Component-Specific | High Protection |
You can maximize your investment by choosing storage solutions with adjustable components that adapt to your changing needs. Consider implementing high-density storage systems that reduce your footprint by up to 85% while maintaining ESD protection standards. For the best value, select solutions that integrate with your existing ERP systems, allowing real-time inventory tracking and reducing costly picking errors. These smart investments in ESD protection will pay off through decreased component damage and improved operational efficiency.
ESD Bags and Pouches
When you're looking for reliable ESD protection, you'll find that ESD bags and pouches come in various constructions, from basic antistatic polyethylene to advanced multi-layer static shielding materials with metallized barriers.
These protective materials offer surface resistivity ranging from 10^3 to 10^5 ohms/square and often include features like loc-top seals, cushioning layers, and moisture barriers to safeguard your sensitive electronic components. Quality ESD storage solutions require regular resistance testing to maintain compliance with anti-static standards.
You can select from an array of sizes and specialized designs, including moisture barrier bags with desiccant packs for moisture-sensitive devices and high shield cushion pouches for components requiring both static and mechanical protection during transport.
Shielding Material Properties
The complexity of shielding materials in ESD-protective bags and pouches demands careful examination of their electrical and physical properties. You'll find various materials engineered specifically for ESD protection, including metallized bags that combine polyester with aluminum layers, and carbon-loaded polyethylene for static dissipation. Tribocharging effects can generate static charges when materials rub together during handling and storage.
When selecting shielding materials, you'll need to evaluate their resistance range, which typically falls between 10^5 to 10^9 ohms for conductive materials. The thickness of these materials directly affects their volume resistivity and breakdown voltage capabilities.
You'll benefit from the Faraday cage effect in metallized bags, which redirects harmful energy away from sensitive components.
The durability of your chosen material is crucial. Metal-in shielding bags offer superior longevity compared to metal-out versions, and you can expect a shelf life of over two years for metallized bags and five years for anti-static options.
For maximum protection, you should maintain an air gap between the device and the bag, which can shield against ESD up to 30 kilovolts. Materials like MVB bags provide additional protection against moisture while maintaining effective EMI/RFI shielding properties.
Construction and Design Features
Building upon these shielding properties, modern ESD bags and pouches incorporate sophisticated construction features that maximize protection for sensitive electronic components.
You'll find these storage solutions are engineered with multiple layers of specialized materials, including carbon-infused compounds and high-strength composites that create effective static dissipation pathways.
Surface resistivity ranges between 10^5 to 10^11 ohms/square guarantee reliable static discharge protection.
Moisture barrier vacuum technology prevents damaging contamination while maintaining ESD safety.
Smooth surfaces and radial edges facilitate safe handling while reducing the risk of friction-induced charges.
The construction features you'll need depend on your specific application. For basic protection, anti-static bags offer fundamental static prevention, while multi-layer shielding pouches provide thorough defense against ESD damage.
You'll also find various closure mechanisms, from ziplock to adhesive seals, designed to maintain protective integrity during storage and transport.
Most modern ESD storage solutions are transparent for easy identification and meet rigorous industry standards like ANSI/ESD S541 and IEC 61340-5-1, guaranteeing you're getting reliable protection for your sensitive components.
Sizes and Applications
From small microchips to complete circuit boards, ESD storage solutions come in a wide range of sizes to accommodate diverse electronic components.
You'll find static shielding bags with multiple aluminum layers that create a Faraday Cage effect, perfect for protecting sensitive electronics during transport and storage. These bags range from small pouches for individual components to larger sizes for complete assemblies.
For less sensitive items used in ESD-safe environments, you can opt for antistatic poly bags, which come in thicknesses between 2-8 mil. If you're dealing with moisture-sensitive components, ESD moisture barrier bags at 3.6 mil thickness offer thorough protection against static, moisture, and physical damage.
When you need permanent ESD protection, consider conductive bags made from carbon-loaded polyethylene. They're particularly useful for electronics and chemical handling applications where consistent grounding is essential. Remember to keep all bags properly sealed to maintain their protective properties.
For critical electronics and disk drive manufacturing, you'll want to use metal-out bags, which provide lower resistance and enhanced protection. Always guarantee your chosen storage solution complies with relevant standards like MIL-PRF-81705D and ANSI/ESD S20.20.
Static-Safe Storage Containers
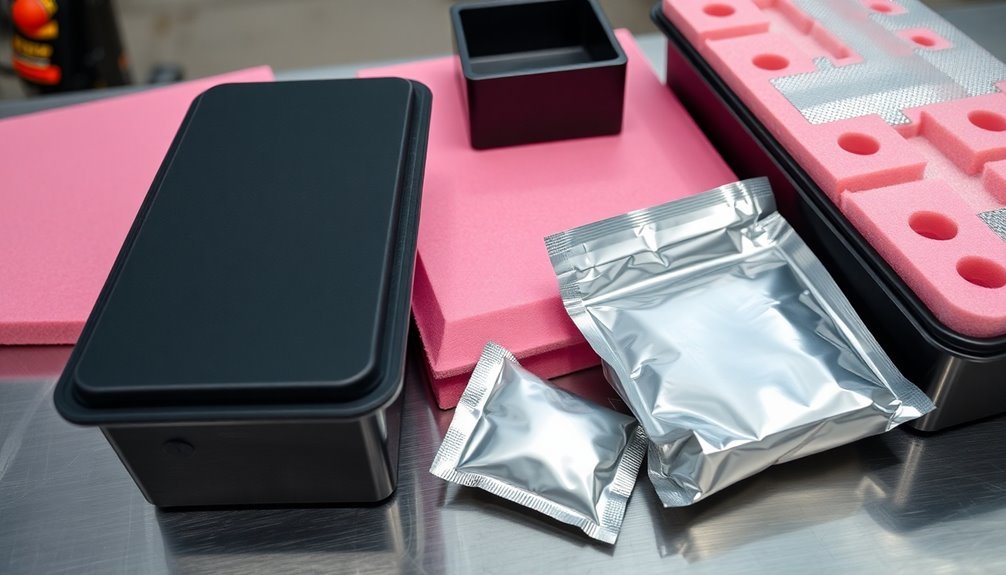
In accordance with modern electronics protection standards, static-safe storage containers serve as essential barriers against electrostatic discharge (ESD) damage. You'll find various types available, including anti-static HDPE containers, conductive polypropylene bins, and static dissipative polystyrene options, each designed to meet specific protection requirements.
When choosing static-safe storage, you should consider these critical features:
- Surface resistance less than 10^12 ohms per square inch
- High-impact strength materials for durability
- Stackable designs with reinforced walls for space efficiency
These containers don't just protect your electronic components; they're also designed for practical workplace use. Most options come with dividable compartments, nesting capabilities, and anti-slide tabs for secure stacking.
They're particularly valuable in clean room environments where you need both ESD protection and contamination control.
For the best protection, you'll want to maintain a relative humidity of at least 15% when using anti-static materials. These containers can save you significant costs by preventing ESD damage to sensitive components, while their stackable and hangable features help maximize your storage space.
ESD Cabinets and Shelving Systems
While protecting sensitive electronic components requires multiple safeguards, ESD cabinets and shelving systems provide a thorough storage solution that combines security with static discharge protection. You'll find these systems built with 18-gauge welded steel construction, featuring ESD-dissipative shelving and multiple ground points for connection to your facility's ground system.
Feature | Cabinets | Shelving Systems |
---|---|---|
Material | Heavy-duty steel | ESD-safe materials |
Protection | ESD, theft, fire | Static discharge |
Grounding | 4 ground points | Integrated system |
Customization | Shelf dividers | Modular design |
Applications | PCB storage | Production facilities |
When you're setting up your ESD protection system, these storage solutions offer significant benefits. You'll achieve compliance with ESD control standards while reducing costs associated with component damage. The modular design allows you to customize your setup based on your specific needs, whether you're organizing a production facility or equipping repair workshops. You'll appreciate the adjustable shelving options and the ability to add vertical dividers for better organization. These systems integrate seamlessly with ESD workstations, providing extensive protection throughout your facility.
Protective Foams and Cushioning
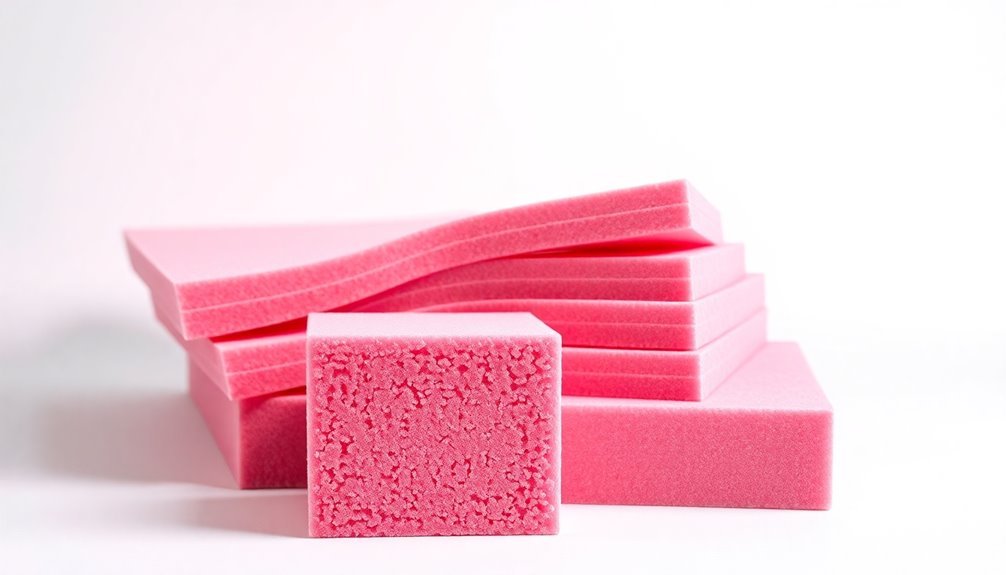
Selecting the right protective foam for your electronic components requires understanding the distinct properties of ESD-safe cushioning materials. You'll find three main types of protective foams: anti-static, conductive, and static dissipative, each serving specific protection needs.
- Anti-static foam (pink) offers surface resistance between 10^9 – 10^12 ohms and works best for short-term storage, though it's not reusable and depends on humidity for effectiveness.
- Conductive foam (black) provides electromagnetic shielding with surface resistance below 10^6 ohms, but you'll need to watch for battery drain if conductive ends make contact.
- Static dissipative foam strikes a middle ground with 10^5 to 10^9 ohms resistance, allowing controlled discharge while preventing human contact issues.
When choosing your foam material, consider the component's sensitivity and your storage duration. For long-term storage, you'll want permanent ESD foams that retain their properties, while temporary shipping can use short-term solutions.
Material options include crosslink polyethylene for tote dunnage, EVA foam for clean environments, and carbon-loaded urethanes for versatile applications. Always match your foam's protection level to your components' ESD susceptibility and environmental conditions.
ESD Totes and Bins
Beyond protective foams, proper storage containers form the backbone of any ESD protection strategy. You'll find that ESD totes and bins made from carbon-filled copolymers and HDPE with carbon black provide essential protection for your sensitive electronic components. These specialized containers feature surface resistivity of 10^5 ohms per square inch or less, guaranteeing proper dissipation of static charges.
Feature | Benefit |
---|---|
Carbon-filled materials | Prevents dangerous charge buildup |
Static dissipative surfaces | Protects your valuable components |
Homogeneous construction | Guarantees consistent ESD protection |
Multiple size options | Adapts to your specific needs |
When you're working in data centers or clean rooms, you'll want containers that won't generate problematic discharge currents. These totes and bins excel in static-controlled environments, offering safe transport and storage for circuit boards, microchips, and semiconductor components. You'll appreciate that anti-static materials don't slough conductive particles, making them ideal for clean room applications. Remember that while voltage isn't your primary concern, controlling current is vital – these containers are specifically designed to limit discharge currents that could damage your sensitive electronics.
Static-Dissipative Work Surface Options
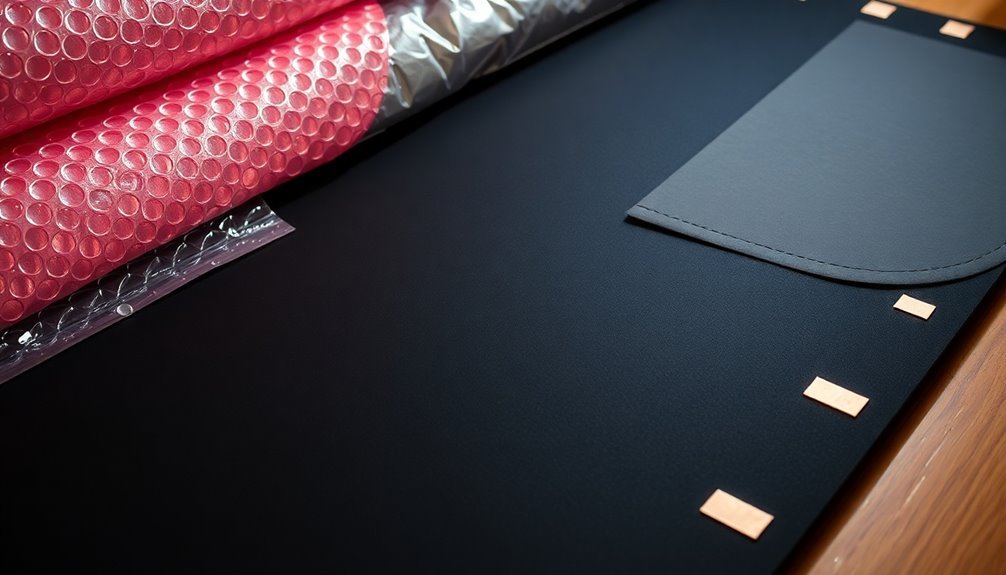
Effective static-dissipative work surfaces form a critical line of defense in your ESD protection strategy. When choosing materials for your workspace, you'll find several proven options that offer reliable static protection while meeting durability requirements.
- HR CompoStat provides superior performance with its homogeneous vinyl construction and buried conductive layer
- Interstat offers cost-effective protection through its 3-layer design with metalized fleece
- Ultimat delivers RoHS-compliant protection with its two-layer rubber elastomer construction
You'll want to guarantee your chosen surface maintains a controlled discharge rate – neither too fast nor too slow – to prevent component damage. Look for materials that meet EOS 20/20 and IEC 613450-5-1 specifications while offering resistance to solvents, heat, and abrasion.
These surfaces work effectively in various settings, from cleanroom assembly lines to field service applications.
To maintain peak performance, you can clean your static-dissipative surface with mild soap and water or ESD-safe cleaners. Consider factors like thickness, color options, and warranty coverage when making your selection.
Implementing Proper Storage Practices
While static-dissipative work surfaces protect components during handling, proper storage practices will safeguard your sensitive electronics when they're not in use.
You'll need to maintain a controlled environment with appropriate humidity levels and clean storage areas to minimize static charge buildup.
When storing components in ESD bags, handle them by their edges or outer surfaces to prevent static transfer. Don't stack components directly on top of each other, and use compartmentalized containers to keep items separated.
You'll want to inspect your ESD bags regularly for wear or damage, replacing them immediately if you spot any compromises.
Store your components in grounded, anti-static shelves or cabinets, and verify they're properly labeled with part numbers and handling instructions. You should document your bag usage and inspection dates for quality control purposes.
Keep your storage area free from dust and debris, and maintain consistent temperature levels to protect sensitive electronics.
Remember to check components upon receipt, verifying they're free from moisture and contaminants before placing them in storage.
If you're using ESD bags, avoid exposing them to extreme temperatures or direct sunlight, as these conditions can compromise their protective properties.
Maintaining ESD Protection Standards
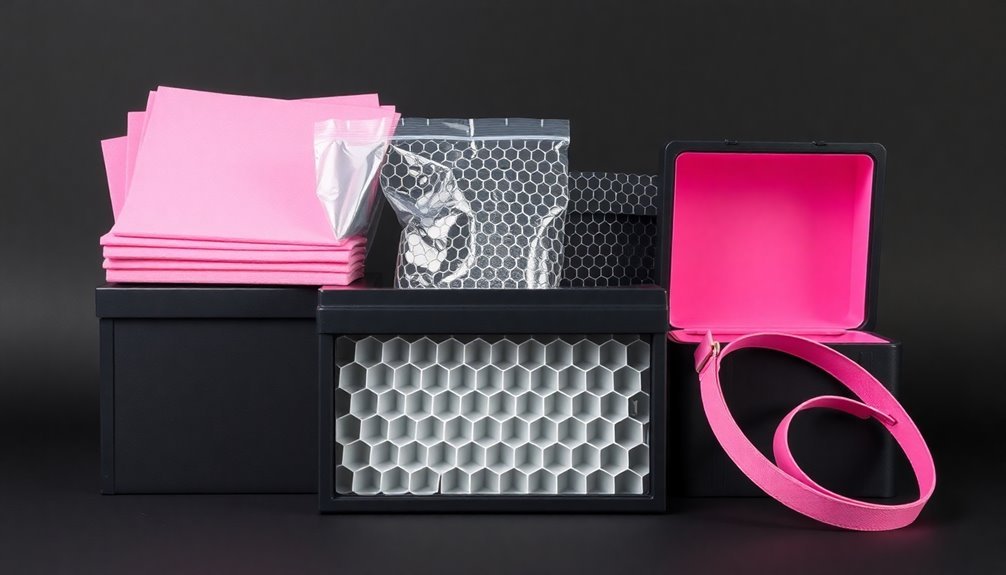
You'll need to conduct regular testing and certification of your ESD storage materials to guarantee they maintain their protective properties over time.
Follow standardized storage guidelines that specify proper handling, maintenance, and replacement schedules for ESD-protective containers and packaging.
Keep detailed documentation of your testing results and conduct periodic audits to verify compliance with ESD protection standards and identify areas that require immediate attention.
Regular Testing and Certification
Maintaining robust ESD protection standards requires a thorough system of regular testing and certification protocols. You'll need to implement standardized verification techniques and verify that your testing personnel hold valid ESD Association certifications. It's vital to document all testing activities and maintain detailed records for compliance purposes.
To establish an effective testing program, focus on these key elements:
- Regular material testing and qualification, including periodic verification of ESD ratings and proper storage conditions to prevent degradation of protective materials.
- Scheduled compliance audits conducted by certified third-party professionals, with immediate implementation of corrective actions based on findings.
- Ongoing certification maintenance through recognized training programs and timely renewal of required credentials.
Your testing protocols should align with industry standards like ANSI/ESD S20.20 and incorporate continuous monitoring systems. Don't forget to regularly review and update your testing procedures to reflect the latest ESD standards and practices.
You'll need to maintain extensive audit records and use these findings to drive continuous improvement in your ESD protection measures. Remember that proper material handling during testing is essential to prevent damage and verify accurate results.
Standardized Storage Guidelines
Proper testing procedures work hand-in-hand with standardized storage guidelines to create a thorough ESD protection system. You'll need to guarantee your storage containers meet key requirements, including the use of electrostatic dissipative materials and low charge generation components that comply with ANSI/ESD S20.20 and IEC 61340-5-1 standards.
When implementing storage solutions, you must maintain intimate contact with dissipative or conductive materials while providing adequate ESD shielding.
Your storage area should feature proper environmental controls, including monitored temperature and humidity levels. You'll want to install humidifiers or dehumidifiers as needed and maintain good air circulation to prevent static buildup.
Don't forget to equip your storage area with conductive surfaces and ESD-safe tools. You'll need to ground all equipment properly and may require ionization techniques for enhanced protection.
Make sure you're training your staff on proper handling procedures, including the use of wrist straps or conductive footwear when accessing stored components. It's critical to enforce a strict no-hand-contact policy with ESD-sensitive items and regularly clean your storage area to remove static-generating dust and debris.
Documentation and Audit Procedures
In accordance with industry standards, thorough documentation and regular audits form the backbone of an effective ESD protection program.
You'll need to maintain detailed records of your ESD protection measures, including design processes, testing validations, and employee training certifications. Regular audits verify that your ESD protection systems remain effective and compliant with current standards.
To maintain proper documentation and audit procedures, you should focus on these critical areas:
- Design and Manufacturing Records: Keep detailed documentation of product design phases, manufacturing processes, and solutions to ESD-related issues.
- Testing and Validation Documentation: Maintain records of ESD testing results, equipment calibration, and verification of protective measures.
- Certification and Compliance Files: Store all relevant certificates, audit reports, and employee training records in an organized system.
Your audit procedures should include scheduled facility inspections, equipment functionality checks, and employee compliance evaluations.
Don't forget to document all findings and implement necessary corrective actions.
Frequently Asked Questions
How Long Does ESD Protection Last in Storage Materials Before Needing Replacement?
Your ESD protection materials can last up to 5 years in controlled environments, but you'll need to test them annually. It's best to follow manufacturer warranties, which typically guarantee protection for 1 year.
Can ESD Storage Materials Be Safely Cleaned Without Compromising Their Protective Properties?
Yes, you can safely clean ESD storage materials using ESD-specific cleaners and soft microfiber cloths. You'll need to avoid harsh chemicals and abrasive tools to maintain the material's protective properties during cleaning.
What Temperature Ranges Are Safe for ESD Storage Materials?
You'll find most ESD storage materials are safe between 40°F to 225°F, though specific ranges vary. Anti-static rubber handles -40°C to 120°C, while standard polystyrene boxes work from -10°C to +70°C.
Do ESD Storage Materials Need Special Disposal Methods When No Longer Usable?
You don't need special disposal methods for uncontaminated ESD storage materials. However, you'll need to label them as "Used" or "Damaged," keep them separate from regular trash, and follow local disposal regulations.
Can Regular Plastic Containers Be Converted Into Esd-Safe Storage Solutions?
You can't convert regular plastic containers into ESD-safe storage. Their basic polymer structure lacks the necessary conductive properties, and applying surface treatments won't provide adequate protection for your sensitive electronic components.
In Summary
You'll find that proper ESD storage materials are essential for protecting your valuable electronics. By selecting the right combination of anti-static bags, containers, and work surfaces, you're creating a thorough protection system. Don't forget to regularly check your storage solutions' effectiveness and maintain compliance with ESD standards. When you've implemented these practices correctly, you're safeguarding your components from costly static damage.
Leave a Reply