Military spec static shield bags must meet seven critical requirements to protect your sensitive electronic components. You'll need bags that comply with ANSI/ESD S541 and MIL-STD-3010 standards, featuring three-layer construction with static dissipative coatings. They must demonstrate surface resistivity below 1×10^11 ohms, withstand puncture resistance of 12+ pounds, and show electrostatic decay times under 2 seconds from ±5kV. Your bags should pass Faraday Cup testing with less than 20nJ energy penetration and include proper traceability measures. Understanding these specifications guarantees you're getting the right protection for your military-grade components.
Essential Military Standards Compliance
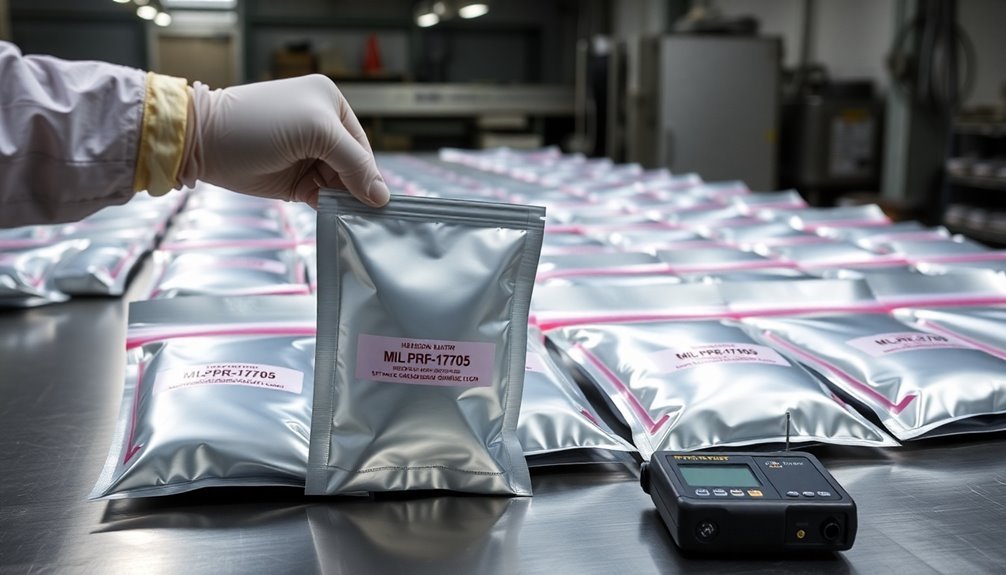
Meeting military specifications for static shield bags requires strict adherence to multiple industry standards, including ANSI/ESD S541, ANSI/ESD S20.20-2014, and MIL-STD-3010 4046.
You'll need to verify your bags meet rigorous testing criteria, including environmental testing under specific conditions of 12%±3% relative humidity at 73°F±5°F. The ESD shielding must demonstrate less than 20nJ energy penetration according to ANSI/ESD STM11.31 testing protocols. Advanced testing facilities must conduct electrostatic decay tests with worst-case scenarios at ±500 volts.
Your static shield bags must maintain surface resistance below 1.0 x 10^11 Ω on both interior and exterior surfaces. Additionally, you're required to implement traceability measures following ANSI/ESD S11.4, which mandates clear manufacturer identification and lot code information on all bags.
You must also comply with MIL-STD-129 and MIL-STD-130 for proper marking and labeling requirements.
To maintain compliance, you'll need to work with vetted ESD test labs and maintain detailed documentation of all testing procedures and results. This includes keeping detailed records of packaging specifications, inspection data, and certification documentation to demonstrate your commitment to military standards and specifications.
Material Construction and Layering
You'll find military-grade static shield bags incorporate a robust metallized layer construction featuring a 3.1 mil thickness with aluminum laminate for ideal EMI shielding.
The polyester shield integration relies on a specialized static dissipative coating that works in conjunction with the metal-in layer to achieve surface resistivity below 10^12 Ohms per square inch. These bags provide faster charge dissipation compared to standard anti-static bags.
The five-layer protection standard combines static dissipative polyethylene, conductive aluminum, and treated polyester to create a complete Faraday cage structure that meets strict military specifications for puncture resistance and seam strength.
Metallized Layer Construction Basics
Designed with precision, military-spec static shield bags feature a sophisticated three-layer construction that creates an effective Faraday cage for protecting sensitive electronic components.
Each layer serves a distinct purpose in the "metal-in" pattern design. The inner layer consists of static dissipative polyethylene that prevents static electricity buildup near your sensitive components.
The middle layer, made of aluminum or carbon, acts as the primary conductor. It's here that the real magic of the Faraday cage happens – charges are collected and grounded before they can reach your product. The surface resistivity rating remains less than 1×10^12 ohms/sq for optimal static dissipation.
The outer layer utilizes polyester with a static dissipative coating that removes external electrical charges on contact.
At 3 mil thick, these bags provide excellent puncture and tear resistance while maintaining transparency for easy content identification.
They're manufactured to meet stringent military standards, including MIL-STD-3010 and ANSI/ESD STM11.11. You'll also find they comply with EIA-541 and ANSI/ESD S541 standards for static shielding.
The construction is completely RoHS compliant, using no restricted substances, and they're both lead-free and amines-free to meet environmental requirements.
Polyester Shield Integration Methods
The integration of polyester shields in military-spec static shielding bags relies on precise layering techniques and material compatibility. You'll find polyester primarily in the outer layer, where it's combined with a static dissipative coating to effectively remove external electrical charges. Similar to how nano-sized particles enhance radiation shielding effectiveness, the smaller coating particles provide better static dissipation performance.
This layer works in conjunction with the inner polyethylene and middle conductive layers to create a thorough Faraday cage effect.
When you're integrating the polyester shield, you'll need to make certain it meets specific military standards like MIL-PRF-81705E. The polyester layer's thickness must be carefully controlled, and its compatibility with other materials must be verified to maintain the bag's protective properties. You'll also need to pay attention to the coating's effectiveness, as it's vital for static dissipation.
The sealing method is particularly important when incorporating polyester shields. You must achieve proper heat sealing to maintain the moisture barrier and make sure the layers work together effectively. If you're handling sharp components, you'll need to think about additional puncture protection measures.
Remember that the entire construction must comply with ANSI/ESD S541 and MIL-STD-3010 4046 standards to meet military specifications.
Multi-Layer Protection Standards
Building upon the polyester shield integration methods, military-spec static shield bags require strict adherence to multi-layer protection standards. You'll find these bags constructed with three essential layers: an inner static dissipative polyethylene layer, a middle conductive layer using carbon or aluminum, and an outer polyester layer with static dissipative coating. Together, these layers create a Faraday cage that effectively shields contents from ESD. The bags' enhanced durability comes from their metalized layer placement between protective sheets.
Layer Type | Protection Features | Performance Metrics |
---|---|---|
Inner Layer | Static dissipative polyethylene | Surface resistivity < 10^12 ohms/square |
Middle Layer | Conductive materials (carbon/aluminum) | Static decay < 0.05 seconds |
Outer Layer | Polyester with dissipative coating | Static shielding < 30 volts |
The material construction must meet rigorous physical requirements, including a minimum thickness of 3.1 mil and tensile strength exceeding 25 lbs. You'll need to guarantee compliance with ANSI/ESD S541 and EIA 625 standards, while maintaining RoHS and REACH requirements. The bags must demonstrate static shielding below 10 nJ and charge generation less than 0.09 nC/sq.in., with seamless integration into MIL-STD-2073 packaging practices.
Surface Resistivity Requirements
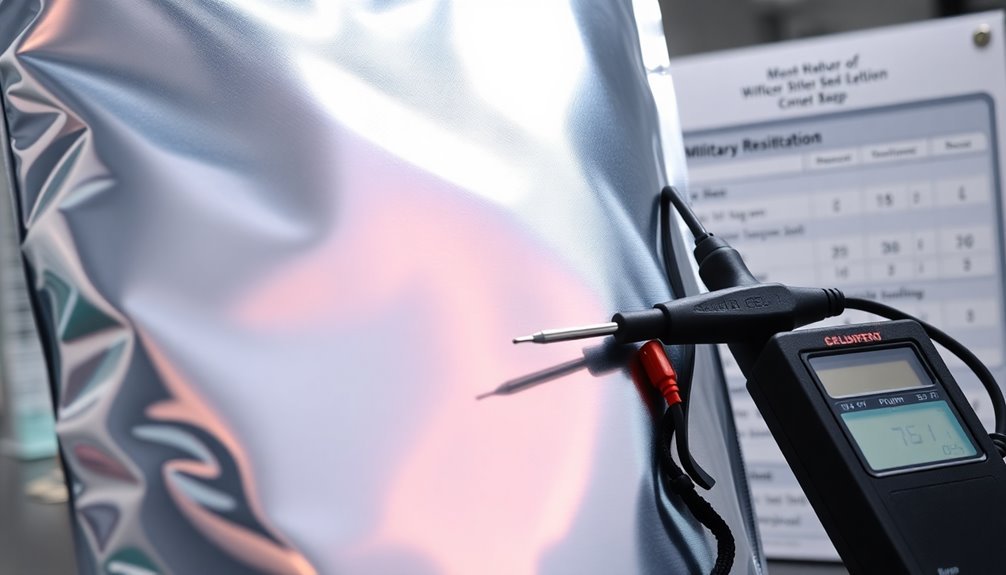
Among critical military specifications, surface resistivity requirements establish precise thresholds for static shield bags across three material categories: electrostatic shielding, conductive, and antistatic materials.
For electrostatic shielding, you'll need materials with surface resistivity less than 1 x 10^4 ohms per square, while complying with ASTM D257 test methods and ANSI/ESD STM11.11 standards.
For conductive materials, you'll find two distinct classifications. Surface conductive materials must have resistivity less than 1 x 10^5 ohms per square, while volume conductive materials require less than 1 x 10^4 ohm-centimeter.
Antistatic materials maintain higher thresholds, ranging from 1 x 10^5 to 1 x 10^12 ohms per square for surface resistivity.
You'll need to evaluate environmental factors when testing these requirements. Materials must maintain their protective properties at 12 ±3% relative humidity and 73 ±3° Fahrenheit, except for rigid plastics, which are humidity-dependent. Performance-based acquisition guides manufacturers to demonstrate these specifications through rigorous testing protocols.
Surface resistivity can increase as relative humidity drops, so you'll need to monitor these conditions carefully to maintain consistent protection.
Additionally, your materials shouldn't outgas in ways that could compromise the packaged products.
Physical Properties and Testing
When you're evaluating military-grade static shield bags, you'll need to verify their tensile strength meets the 4600 PSI requirement and puncture resistance exceeds 12 pounds.
Your testing must follow strict ANSI/ESD STM11.31 protocols under controlled conditions of 23°C and 12% relative humidity. Surface resistance values should be maintained below 1 x 10^11 ohms during evaluation.
These bags must pass six discharge tests with less than 20 nJ penetration, while maintaining seam integrity at 11 pounds of force.
Layer Strength Requirements
Military-grade static shield bags must meet rigorous strength requirements across multiple physical properties.
You'll need to verify that your bags meet a minimum tensile strength of 25 pounds according to ASTM D882 standards, with specific requirements of over 5,000 PSI in the machine direction and over 5,500 PSI in the transverse direction.
When testing puncture resistance, your bags must withstand at least 12 pounds of force under FTMS 101C Method 2065.1.
The tear strength specifications require a minimum of 2 pounds using ASTM D1004-94A testing, with machine direction exceeding 2 pounds and transverse direction surpassing 2.8 pounds.
You'll also need to verify that seam strength meets or exceeds 12 pounds per inch under ASTM D882 guidelines.
The bags' multi-layer construction, consisting of polyester, metal, and polyethylene laminates, must maintain a uniform thickness of 3.1 mils throughout. This consistent thickness is vital for maintaining the Faraday cage effect and guaranteeing reliable protection.
Each layer must bond securely while maintaining the specified physical properties to create an effective static shield that meets military specifications.
Rigorous Testing Standards
Static shield bags for military applications undergo thorough physical testing protocols to validate their protective capabilities.
You'll need to guarantee compliance with specific test methods, including PST #001 for thickness measurements and PST #002 for yield testing. The bags must pass puncture resistance testing using FTMS 101C Method 2065, while tearing strength is verified through ASTM-D-1004-94A standards.
Electrical properties require equally stringent validation. You must test surface resistivity using ASTM D-257 at 15% RH, while ESD resistance follows ANSI/ESD STM 11.11 protocols. Static shielding capabilities are confirmed through EOS/ESD S11.31, and electrostatic decay testing adheres to FTMS 101 Method 4046.
Environmental testing conditions are precisely controlled. You'll need to maintain 12%±3% relative humidity at 73±5°F for a minimum of 48 hours during testing. The bags must undergo preconditioning at 160°F for 14 days per Mil-STD-3010C.
Don't forget to conduct Faraday Cup testing at 12% RH after 48 hours of preconditioning. All testing must comply with ANSI/ESD S20.20 standards, and you'll need proper certification documentation meeting DoD requirements under MIL-STD-2073.
Static Decay Performance
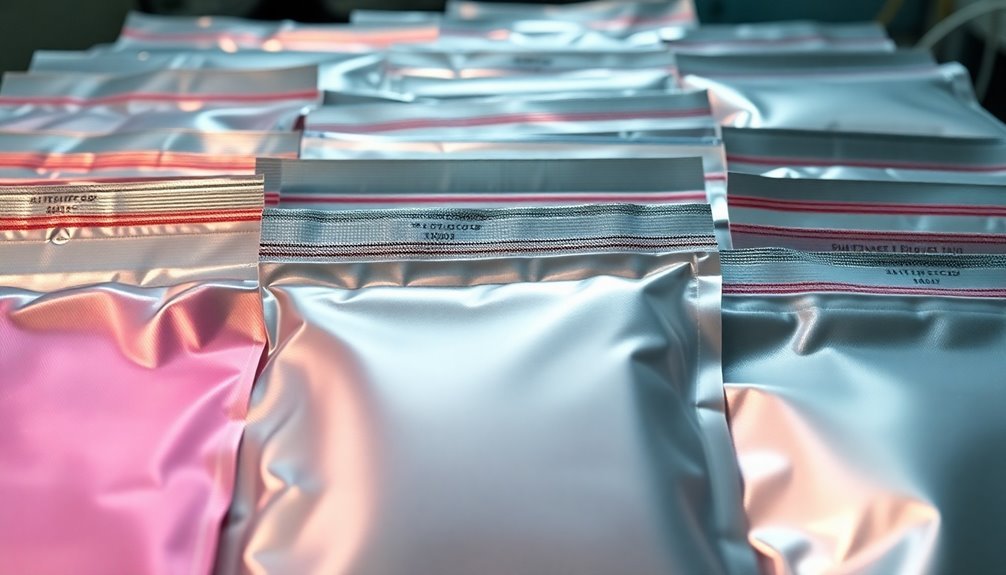
Manufacturers must meet rigorous testing standards to guarantee proper static decay performance in military specification shield bags. These standards require bags to dissipate static charges from ±5kV to ±500 volts or lower within 2 seconds, as specified by MIL-STD-3010C, Method 4046.
The static decay performance requirements you need to understand include:
- Your bags must demonstrate decay times under 2 seconds for both Type I and Type III specifications
- You'll need to achieve surface resistance measurements below 1.0 x 10^11 Ω on both inner and outer surfaces
- Your static shielding performance can't exceed 10 nJ energy transfer
- You must maintain charge retention below 1.0 nC in Faraday Cup testing
Testing occurs under strictly controlled conditions at 12%±3% relative humidity and 73°F±5°F.
Testing equipment includes concentric ring fixtures for surface resistance measurements and environmental chambers for controlled conditions. All tests use standardized 3" x 5" samples to verify consistency.
You'll need to comply with multiple standards, including MIL-PRF-81705E and ANSI/ESD STM11.31, which define specific protocols for static shielding and decay testing performance.
Heat Sealing Specifications
Proper heat sealing is critical for maintaining the protective qualities of static shield bags in military applications. When sealing these bags, you'll need to maintain temperatures between 250°F and 375°F while applying pressure between 30 and 70 PSI.
The sealing process should take between 0.5 and 3.5 seconds to guarantee ideal results.
You'll need to use specialized heat sealing equipment that prevents electrostatic discharge during the process. The bags must be constructed from specific materials, including polyethylene, polyester, and metal layers, with thicknesses ranging from 2.8 to 3.1 mils.
Your sealing methods can include jaw type, band type, or rotary type sealers, but they must produce seams that meet MIL-DTL-117 specifications.
To comply with military standards, you must achieve seam strengths of at least 11 pounds or 48 N, meeting MIL-PRF-81705 requirements. During the sealing process, you'll need to avoid creating any splits, tears, wrinkles, or unsightly marks.
The final product should demonstrate high-quality craftsmanship with properly formed seams that can withstand rigorous testing procedures outlined in MIL-STD-3010.
Quality Control and Traceability
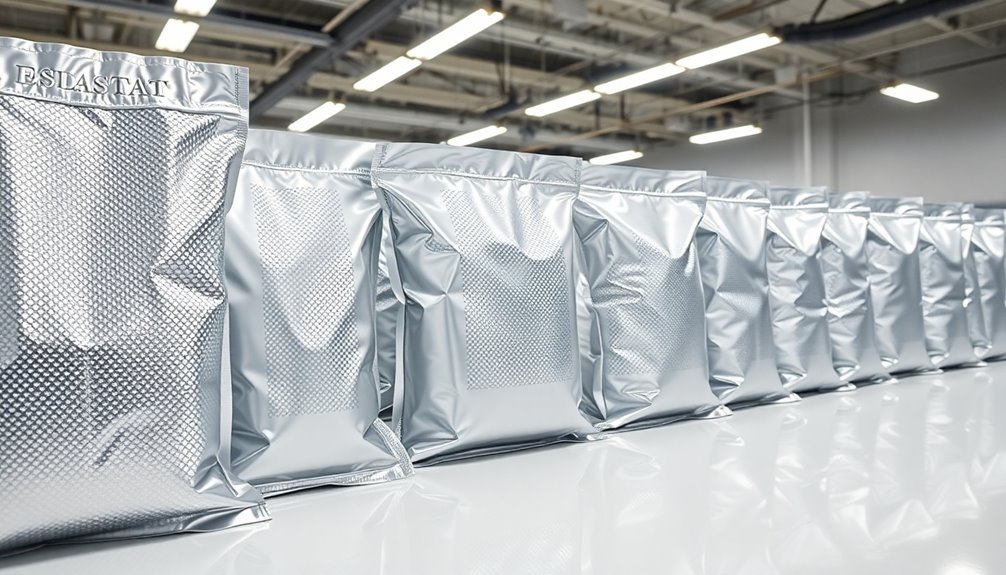
All quality control testing for static shield bags must occur under strictly controlled conditions of 73°F±5°F at 12%±3% relative humidity for a minimum of 48 hours. You'll need to guarantee proper calibration of your electrometer and concentric ring fixture to measure both the inside and outside surfaces of the bags accurately.
To maintain compliance with ANSI/ESD S20.20-2014 standards, you'll need documented test data from either in-house testing or third-party verification.
Your testing process should include:
- Surface resistance measurements following ANSI/ESD STM11.11 protocols
- Volume resistance testing according to ANSI/ESD STM11.12 specifications
- Electrostatic decay evaluations based on MIL-STD-3010C requirements
- Charge retention assessments following ESD Adv.11.2 guidelines
Don't forget about traceability requirements – it's vital that your bags display proper manufacturer identification, date codes, and lot numbers. If you're working with MIL-PRF-81705E specifications, you'll also need to clearly indicate the class of bag type.
Regular verification testing should be part of your quality control program to guarantee your static shield bags continue meeting these stringent military specifications.
Faraday Cage Protection Methods
Beyond quality control measures, understanding Faraday cage protection serves as the foundation for static shield bag effectiveness. You'll find that these bags work by creating an electromagnetic shield that blocks both static and non-static fields, including radio waves and microwaves.
The protection method relies on conductive materials like copper or aluminum that redistribute charges to cancel incoming electromagnetic waves.
When you're selecting materials for military-spec static shield bags, you'll need to evaluate the conductivity and thickness of the materials, as these factors directly impact shielding effectiveness. You'll typically see polyethylene and polyester bags with aluminum layers that provide the necessary static protection.
The construction must feature minimal gaps and tight seals to maintain maximum effectiveness.
To guarantee compliance with military specifications, you'll need bags that meet ANSI/ESD S541 and EIA 625 standards. The testing process includes surface resistance, volume resistance, and electrostatic decay evaluations under controlled conditions.
While grounding isn't strictly necessary for the Faraday cage effect, you'll want to implement it for safety purposes and to reduce electric shock risks in military applications.
Frequently Asked Questions
Can Static Shield Bags Be Reused Multiple Times for Different Components?
You can reuse static shield bags multiple times if they're undamaged, but you'll need to inspect them carefully before each use. Always check for tears, holes, or wrinkles that could compromise their protective qualities.
What Is the Typical Shelf Life of Military-Grade Static Shield Bags?
You'll find that properly stored static shield bags can last up to 5 years in controlled environments. However, you should regularly check them for damage and store them away from moisture, sunlight, and extreme temperatures.
How Should Damaged or Compromised Static Shield Bags Be Disposed Of?
You'll need to follow specific disposal guidelines: send reusable bags to ERA if they're undamaged, recycle large quantities (30+) through pickup services, or dispose of contaminated bags according to DoD Manual 4160.21 hazardous material procedures.
Are These Bags Safe for Direct Contact With Bare Circuit Boards?
Yes, you can safely place bare circuit boards in direct contact with static shield bags. Their polyethylene inner layer prevents static buildup, while multiple protective layers shield your sensitive electronics from ESD damage.
Can These Bags Be Safely Stored in Extreme Temperature Environments?
While your bags can handle various temperatures, you shouldn't store them in extreme conditions. Though they're resilient, extreme heat or cold may compromise their protective qualities. Keep them in moderate, controlled environments instead.
In Summary
You'll need to confirm your static shield bags meet all seven military specifications to protect sensitive electronic components effectively. Make sure they're tested for proper surface resistivity, static decay, and Faraday cage shielding. Don't overlook quality control documentation and heat sealing requirements. By following these standards, you're ensuring maximum protection for military-grade electronic equipment during storage and transport.
Leave a Reply