When choosing anti-static mats for your cleanroom, you'll need to verify key performance standards and material specifications. Look for mats with surface resistance between 1×10^6 and 1×10^9 ohms, and ascertain they meet ANSI ESD-S20.20 standards. Select mats with two-layer construction featuring a static dissipative top layer and conductive bottom layer. You'll want proper grounding connections and regular testing capabilities. Consider factors like chemical resistance, UV protection, and low VOC emissions. The right mat requires careful evaluation of these technical specifications, placement requirements, and maintenance protocols – there's more to effective static control than meets the eye.
Understanding ESD Mat Basics
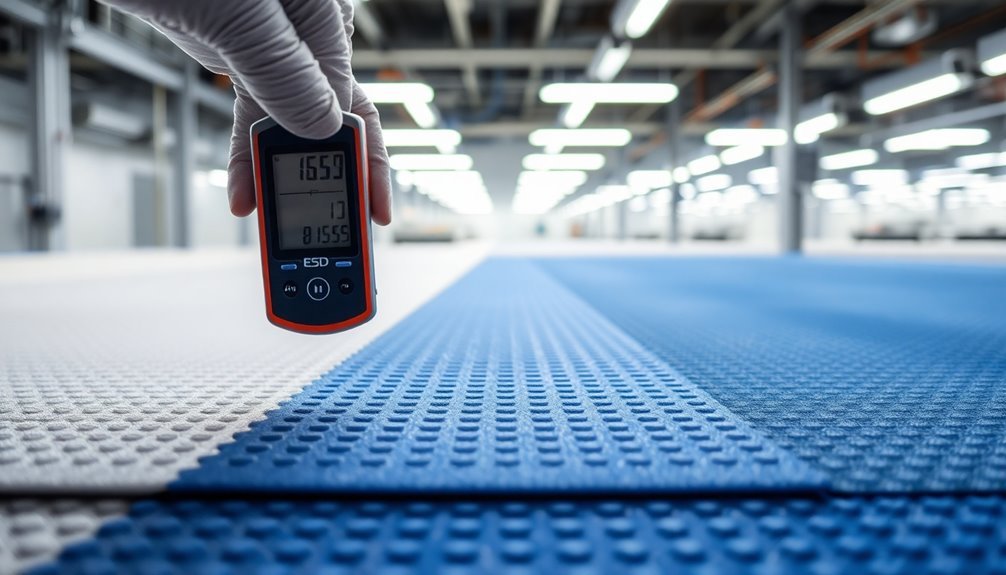
A typical ESD (Electrostatic Discharge) mat stands as your first line of defense against static electricity in cleanroom environments.
You'll find these mats constructed in various configurations, from single homogeneous conductive layers to multi-layer designs featuring conductive materials sandwiched between dissipative layers.
When you're working with sensitive electronic components, you'll need to understand that ESD mats differ from standard anti-static mats. They're engineered to rapidly dissipate static charges through proper grounding, while anti-static mats merely slow down charge buildup.
You must guarantee proper grounding connections to prevent potential shock hazards, especially when handling live electrical equipment. The mats come with common point grounding hardware including cords and snaps for complete protection.
You'll discover these mats are specifically designed for different applications, including workbench surfaces, flooring, and portable solutions.
Their construction incorporates conductive or static dissipative materials that create a reliable path to ground, effectively protecting your sensitive devices.
In cleanroom settings, you'll benefit from their ultra-clean, non-outgassing properties.
The mats' Class 1 fire rating and superior durability make them ideal for demanding environments, while their minimal cleaning requirements help maintain your cleanroom's integrity.
Key Performance Requirements
You'll need to verify that your ESD mat meets the standard resistance range of 1 x 10^5 to 1 x 10^11 ohms/square for dissipative materials or less than 1 x 10^5 ohms/square for conductive materials.
Testing your mat's surface conductivity is essential and should be performed regularly using a surface resistance meter to guarantee consistent ESD protection.
Your mat's performance must remain stable across different environmental conditions, particularly in cleanroom settings where humidity levels can fluctuate.
Single and multi-layer compositions are available to optimize ESD control performance based on specific cleanroom requirements.
Resistance Range Standards
Understanding resistance range standards is essential when selecting anti-static mats for cleanroom environments. You'll need to ascertain your mat falls within specific resistance ranges to provide proper static protection.
For static dissipation, look for mats with resistance between 1 x 10e6 and 1 x 10e12 ohms, while static conductivity requires less than 1 x 10e6 ohms. Our recommended mat provides excellent electrical performance with a charge decay time of 0.01 seconds.
When testing your mat's performance, you'll need to conduct both RTG and RTT tests using a surface resistance meter. Place your test electrodes 10 inches apart, keeping them 2 inches from edges and 3 inches from grounding points.
The acceptable RTG range should fall between 1 x 10e6 and 1 x 10e9 ohms, following ANSI/ESD S4.1 guidelines.
Your mat's material must be static dissipative and non-insulative, with a typical thickness of 0.080 inches for durability.
Choose mats that meet Class 1 fire ratings under BFPA 76 and ASTM E-84 standards.
Don't forget to verify that your mat includes proper grounding hardware, such as common point ground cords and grounding snaps, to maintain its effectiveness in your cleanroom setting.
Surface Conductivity Testing
Surface conductivity testing forms the backbone of anti-static mat performance validation in cleanroom environments.
Proper grounding requirements ensure ESD mats function effectively during testing.
You'll need to conduct both resistance-to-ground (RTG) and resistance-to-resistance (RTT) measurements using a Surface Resistivity Meter, following ANSI/ESD S4.1 guidelines. These tests employ 5-pound electrodes to guarantee accurate surface resistance readings.
When testing your anti-static mats, you're looking for surface resistance values between 1 x 10^6 and 1 x 10^9 ohms. For conductive materials, you'll want measurements below 1 x 10^5 ohms/square, while dissipative materials should fall between 1 x 10^5 and 1 x 10^11 ohms/square.
You'll need to test both RTT and RTG to guarantee thorough performance evaluation.
Different mat constructions affect testing results. Homogeneous mats provide consistent readings across their surface, while multi-layer mats combine materials for enhanced electrical performance.
If you're testing foam-backed mats, remember they'll show different electrical characteristics. To maintain compliance with ESD-S20.20 standards, you'll need to perform periodic testing to verify your mats continue meeting these specifications over time.
Types of Cleanroom Mats
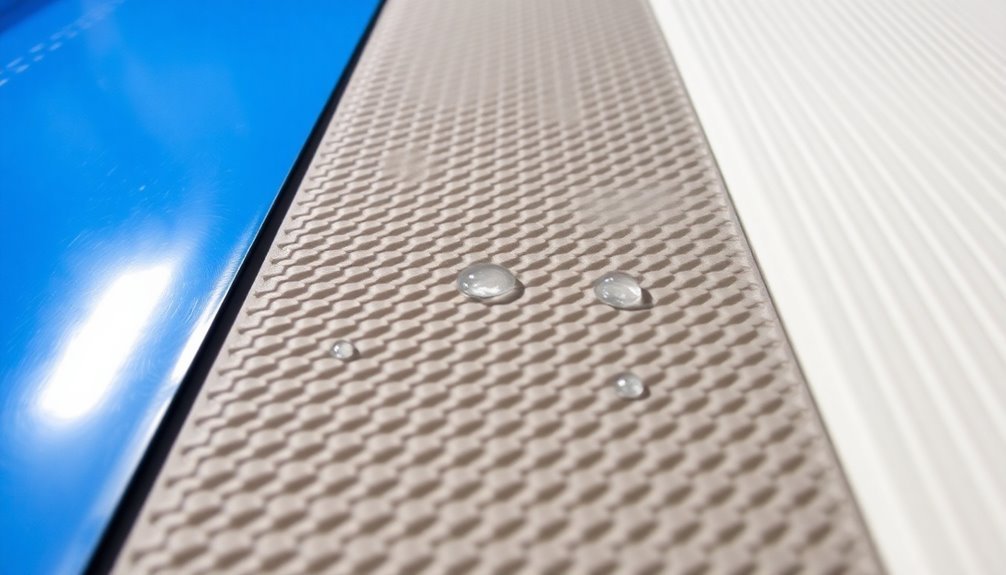
When selecting cleanroom mats, you'll need to choose between sticky mats that trap particles through adhesive layers and static dissipative mats that prevent electrical discharge.
Your choice should factor in the mat's construction type, with adhesive mats offering peelable layers for easy replacement and static control mats featuring durable single-piece designs with conductive materials throughout. The four mats per case packaging ensures adequate supply for maintaining consistent contamination control.
Both varieties must meet strict material standards for cleanroom use, with sticky mats requiring consistent adhesive performance and static mats demanding verified electrical resistance properties.
Sticky vs. Static Mats
Selecting the right mat for your cleanroom requires understanding the distinct advantages of sticky and static mats. While sticky mats capture dust and particulates with adhesive layers that can be peeled away after roughly 50 uses, static mats provide essential protection against electrostatic discharge through their anti-conductive properties. These mats are treated with antimicrobial agents to enhance overall cleanliness standards.
You'll find sticky mats are 27% effective at preventing contamination from foot and wheel traffic, making them suitable for areas with smaller, homogeneous particles at lower concentrations. They require proper floor preparation with alcohol and deionized water for ideal adhesion.
Static mats, particularly those made of nitrile rubber, offer superior ESD protection compared to PVC alternatives. They're especially valuable in electronics, pharmaceuticals, and aerospace applications where static discharge could damage sensitive equipment or components.
You'll appreciate their resistance to chemicals, oil, and fuel, making them ideal for heavy-traffic areas.
When choosing between the two, consider your specific needs. If you're dealing with ESD concerns, opt for nitrile rubber static mats. For general contamination control, sticky mats might suffice.
Remember that reusable alternatives like Dycem mats can offer better long-term value and environmental benefits compared to disposable sticky mats.
Layered Construction Types
Cleanroom mats come in two primary layered configurations: 30-layer and 60-layer options, each designed with removable sheets for maximum contamination control. You'll find these mats constructed with low-density polyethylene (LDPE), providing smooth surfaces that effectively trap particles while maintaining durability under heavy foot traffic. The four mats per case packaging ensures facilities maintain adequate supply for consistent contamination control.
Feature | Specification | Benefit |
---|---|---|
Material | LDPE Film | Guarantees surface smoothness and durability |
Adhesive | Medium-tack | Optimizes particle capture without residue |
Tracking | Numbered sheets | Simplifies maintenance monitoring |
Each layer features consistent adhesive coating and numbered labeling for easy tracking and removal. You'll appreciate how the ultra-tough polyethylene film withstands constant use while maintaining its particle-trapping effectiveness. When installing these mats, you can choose between frame-mounted or direct-floor applications, depending on your specific needs and surface type.
The construction allows for quick removal of contaminated layers, revealing a fresh, clean surface underneath. You'll find these mats particularly effective when placed at entry and exit points of your cleanroom, where they'll help maintain your facility's cleanliness standards while providing safe, reliable performance.
Material Durability Standards
High-quality anti-static mats for cleanrooms must meet strict material and durability standards to confirm reliable performance. When selecting a mat, you'll need to verify it meets key durability requirements, including chemical resistance, UV protection, and flame-retardant properties. The material should also demonstrate low VOC emissions to maintain cleanroom air quality. The Ultimat™ White Clean Room Mat ensures optimal safety with its odor-free composition.
For maximum durability, choose rubber mats over vinyl ones, as they typically offer superior longevity and wear resistance. Your mat should comply with ANSI ESD-S20.20 standards and provide consistent electrical performance throughout its lifespan.
Look for materials that offer anti-microbial properties to maintain cleanroom hygiene standards. The mat's construction should include appropriate cushioning and texture suited to your specific application, while featuring easy-to-clean surfaces that won't degrade with regular maintenance.
Verify that your chosen mat meets RoHS compliance and holds relevant ISO certifications. If you're dealing with European facilities, confirm it carries the CE marking.
For enhanced maintenance efficiency, you might consider mats with peel-off layers that allow quick surface renewal without complete replacement. Remember to check the manufacturer's specified lifespan to assess the mat's long-term value.
Material Selection Criteria
Making informed decisions about anti-static mat materials requires understanding several key factors. When selecting materials for cleanroom environments, you'll need to balance durability, performance, and specific cleanroom requirements. The choice between vinyl and rubber materials should align with your application needs, with vinyl offering excellent cushioning for tabletop use and rubber providing superior heat and chemical resistance.
Key selection criteria to evaluate:
- Material composition: Look for two-layer construction with a static dissipative top layer backed by a conductive layer, ensuring consistent performance throughout the mat's lifetime.
- Cleanroom compatibility: Choose materials that are non-outgassing and free of particulates, particularly those featuring IDP-STAT alloy for reliable static dissipation.
- Durability standards: Select materials that meet ANSI ESD-S20.20 and ANSI/ESD STM4.1 standards, with appropriate thickness for your application.
Don't let cost be the primary factor in your decision-making process, as low-quality matting can compromise cleanroom integrity. Instead, focus on materials that offer permanent static dissipation, chemical resistance, and compliance with fire safety standards.
Reflect on how the material will integrate with your constant monitoring systems and cleaning protocols.
Proper Grounding Methods
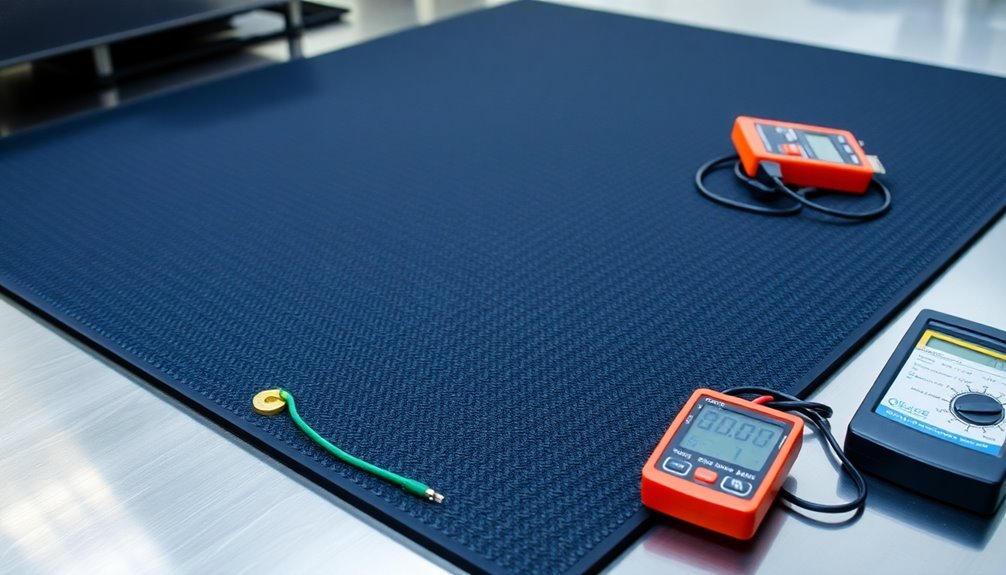
Setting up proper grounding methods stands out as the most critical aspect of anti-static mat installation. You'll need to connect each mat to a reliable earth ground using dedicated cables with a resistance of 1 megohm ± 20%.
Don't attempt to daisy chain multiple mats – each one requires its own grounding connection.
You can choose between two primary grounding methods: mat ground cables that connect directly to electrical outlets using eyelet or #10 ring terminals, or common point ground cables that link both your mat and wrist straps to a single ground point.
When installing the grounding connection, you'll need to carefully insert conductive snaps into the mat's corner, guaranteeing proper contact with the inner conductive scrim.
To maintain effective static dissipation, you must test your grounding setup daily. Use ESD resistance meters to verify the mat's dissipative properties and vector impedance testing for ground verification.
You can also install real-time monitors for automatic failure detection. Remember to secure all fasteners tightly and regularly clean your mats and straps to promote peak performance.
If you're working in a cleanroom environment, it's crucial to maintain consistent ground monitoring protocols.
Maintenance and Cleaning Protocols
Maintaining your anti-static mats requires three essential cleaning approaches: dry cleaning, wet cleaning, and specialized solutions.
You'll need to implement a regular cleaning schedule that combines these methods to guarantee peak performance and longevity of your mats.
For daily maintenance, use dry cleaning methods like sweeping or dry-mopping to remove surface debris and prevent humidity-related issues.
When it's time for deeper cleaning, use water or specialized static-control solutions, but avoid alcohol-based cleaners that can damage the mat's properties.
Make certain you're not over-saturating the mat during wet cleaning, and always use solutions that won't leave residue behind.
- Test your mats after each cleaning session to verify they meet anti-static requirements
- Create a cleaning schedule based on usage frequency – daily for high-traffic areas, weekly for moderate use
- Use only biodegradable, quick-drying, and non-flammable cleaning solutions designed specifically for ESD mats
Remember that concentrated cleaning formulas typically last longer than diluted ones.
Sizing and Installation Guidelines

When selecting anti-static mats for your cleanroom, proper sizing and installation are vital factors that directly impact their effectiveness. You'll find standard rolls available in 24", 30", 36", and 48" widths, typically coming in 50' or 60' lengths.
While pre-cut mats with grounding hardware offer convenience, they're usually more expensive than cutting your own from full rolls.
To guarantee proper installation, you'll need to connect your mat to ground using a cord with a built-in resistor for controlled discharge. The ground cord should attach to the center screw of an electrical outlet.
If you're covering larger areas, consider mats with interlocking sections for easier installation and maintenance.
For specific workstation applications, you can opt for pre-sized mats like 2'x3' or 3'x5'. When planning your layout, remember that you can easily customize the material to fit your space.
It's smart to purchase full rolls if you anticipate future expansion or need to cover multiple areas. Position your mats strategically at entry points and high-traffic areas where static control is most vital for your cleanroom operations.
Quality Testing Standards
The quality testing of anti-static mats follows rigorous standards to confirm reliable static control in cleanroom environments. Each mat undergoes extensive testing for 100 hours, with a total certification requirement of 500 hours across five samples.
You'll need to ascertain your mats meet both static dissipative properties and grounding requirements to maintain cleanroom integrity.
When evaluating anti-static mats, you should focus on these critical testing parameters:
- Surface resistance measurements must show RTT (resistance-top-to-top) ≥ 1 x 10^6 ohms and RTG (resistance-to-groundable point) between 1 x 10^6 and 1 x 10^9 ohms
- The bottom surface should have resistance less than 1 x 10^6 ohms for proper grounding
- Testing must comply with ANSI/ESD S4.1 standards using certified ESD meters
You'll want to verify that your mats have been tested in controlled environments simulating actual usage conditions.
The mat's top surface should be static dissipative while the bottom surface remains conductive, typically achieved through carbon impregnation.
Regular testing using ESD resistance meters will help you maintain compliance and confirm continued protection against static discharge in your cleanroom.
Environmental Impact Considerations
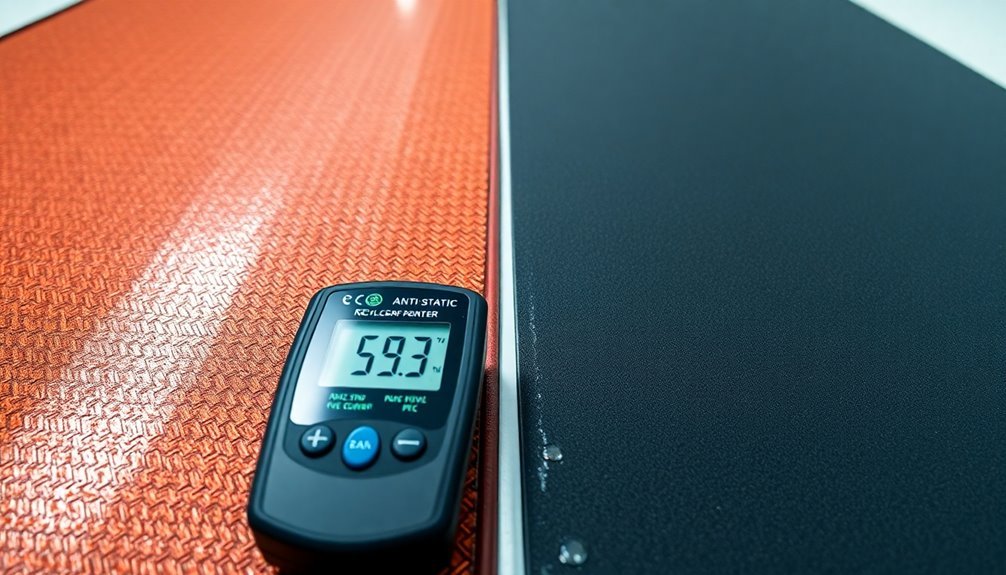
From an environmental standpoint, selecting anti-static mats requires careful consideration of their ecological impact throughout their lifecycle. While most anti-static mats use polyethylene (PE), which isn't biodegradable, you'll be glad to know it's recyclable. The mats' non-toxic, water-soluble adhesives minimize environmental harm, and their multi-layer peel-off design optimizes material usage.
You'll want to focus on sustainable features when choosing your mats. Look for products with multiple peel-off layers, as they reduce the frequency of complete replacements and minimize waste generation. The stackable design makes disposal more efficient, and some mats come with reusable backing sheets that further reduce environmental impact.
When evaluating manufacturers, check their compliance with environmental regulations and ISO standards. You should verify that they follow eco-friendly manufacturing processes and maintain sustainable supply chain practices.
Consider the mat's end-of-life recycling potential and guarantee proper disposal methods are available in your area. By selecting mats from manufacturers who prioritize environmental responsibility, you're not only meeting cleanroom requirements but also contributing to sustainable practices in your facility.
Frequently Asked Questions
Can ESD Mats Be Stacked on Top of Each Other?
You shouldn't stack ESD mats, as this can interfere with proper grounding and create safety hazards. It'll reduce their static-dissipating effectiveness and increase your risk of trips, falls, and workplace injuries.
How Often Should Anti-Static Mats Be Tested for Conductivity Performance?
You should test your anti-static mats daily for critical operations, but weekly testing is acceptable for standard environments. Don't forget to test after cleaning or maintenance to guarantee proper conductivity performance.
Do Anti-Static Mats Work Effectively in High Humidity Environments?
Yes, your anti-static mats will work effectively in high humidity. In fact, they'll perform better when humidity's above 40% as moisture in the air helps dissipate static charges more efficiently through increased conductivity.
Can Regular Carpet Cleaners Be Used on ESD Floor Mats?
You shouldn't use regular carpet cleaners on ESD floor mats. They'll damage the mat's static-fighting abilities and leave insulative residue. Instead, use specialized ESD cleaners designed to maintain your mat's conductivity and performance.
What Happens if an ESD Mat Accidentally Gets Wet?
If your ESD mat gets wet, you'll need to dry it immediately as moisture can disrupt its anti-static properties. You're risking reduced effectiveness and potential damage until it's completely dry and properly tested.
In Summary
You'll need to carefully consider all aspects when selecting anti-static mats for your cleanroom, from material composition to grounding requirements. Choose mats that meet your facility's specific cleanliness standards while providing reliable ESD protection. Remember to implement proper maintenance protocols and regularly test your mats' effectiveness. With the right selection and care, your anti-static mats will help maintain a safe, controlled cleanroom environment.
Leave a Reply