You'll need a well-structured monitoring schedule to protect your manufacturing process from ESD damage. Start with daily static level documentation and checklist completion. Conduct weekly ground system tests using surface resistance megohmmeters for RTG and RTT measurements. Perform monthly equipment calibration checks against certified standards. Schedule quarterly facility assessments to map static-sensitive zones. Don't forget personnel training reviews, surface resistance testing, and emergency response drills. Following these essential monitoring practices helps maintain compliance while preventing costly static-related failures. Our all-encompassing guide will show you how to implement each step effectively.
Daily Static Level Documentation
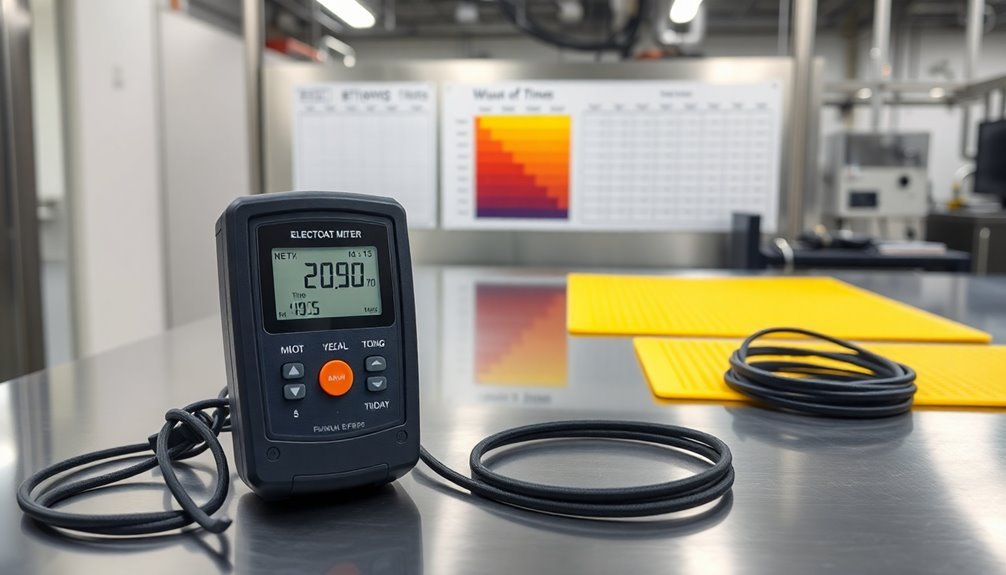
With manufacturing processes becoming increasingly sensitive to static electricity, daily static level documentation serves as a critical cornerstone of quality control and regulatory compliance.
You'll need to implement standardized procedures and clear checklists to maintain consistent monitoring across all shifts and teams. Regular updates to monitoring protocols ensure adaptation to emerging static control challenges.
Start by customizing your documentation system to match your specific operational requirements. You should integrate digital checklists with your existing systems, enabling real-time data tracking and analysis.
Make certain you're training your employees thoroughly on proper documentation procedures and the importance of static control monitoring.
Your daily documentation should include safety checklists that address potential static-related hazards and guarantee compliance with industry regulations.
You'll want to regularly update these checklists to reflect any changes in your operations or new regulatory requirements.
Weekly Ground System Tests
Building on your daily documentation practices, weekly ground system tests provide a systematic approach to maintaining your ESD control infrastructure. Ensuring proper testing methods helps meet IEC 61340-5-1 standards. When conducting these tests, you'll need to focus on several key components to guarantee thorough protection of your sensitive products.
Start by using a surface resistance megohmmeter with 5# electrodes to perform RTG and RTT tests on your worksurfaces and floors. You'll want to verify that all floor materials meet your specified requirements and that ground connections remain intact.
Check your continuous monitors to confirm they're providing reliable notifications of any ground disconnects, which helps prevent product handling during system failures. For accurate measurements, use a three-wire extension cord when testing RTG to equipment ground.
Don't forget to inspect your static control footwear through lot sampling and resistance testing at acceptance points. While continuous monitors eliminate the need for daily wrist strap testing, you'll still need to verify their functionality regularly.
These weekly checks are essential for maintaining productivity and quality standards, especially if you're subject to annual customer audits. By implementing systematic testing, you'll protect valuable products and maintain your ESD control program's effectiveness.
Monthly Equipment Calibration Checks
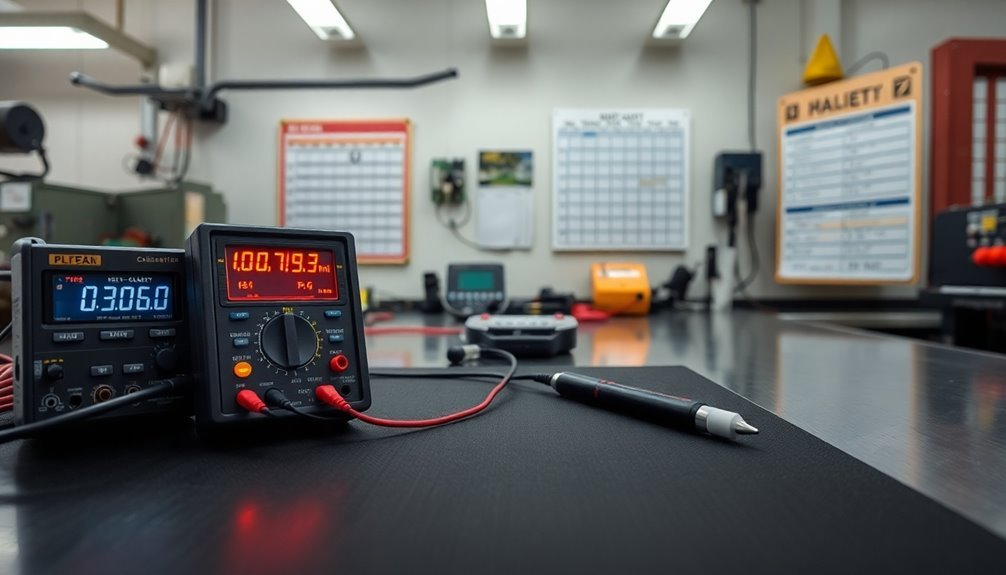
To maintain your static control program's reliability, you'll need to verify the accuracy of your calibration tools through regular testing against certified standards.
You can start by marking your calendar with preventive testing dates for each piece of monitoring equipment, ensuring these checks align with manufacturer recommendations and industry standards. Implementing a calibration management system helps automate scheduling and tracking while reducing administrative work.
Remember to document all calibration results and adjust your testing schedule based on equipment usage patterns and environmental conditions in your facility.
Verify Calibration Tool Accuracy
Regular calibration checks serve as the foundation of reliable static control monitoring. You'll need to verify your calibration tools' accuracy based on both usage frequency and environmental conditions that could affect their performance.
A Test Uncertainty Ratio of 4:1 should be maintained between your calibration tools and reference standards. Make certain you're following industry standards like ASTM D7091 and SSPC-PA 2 to maintain compliance.
When verifying your calibration tools, you'll want to distinguish between verification and actual calibration. While you can perform accuracy checks in your facility, formal calibration must be done in a controlled environment by authorized personnel or accredited laboratories.
Don't forget to make necessary adjustments before taking measurements, accounting for specific substrate characteristics.
You should maintain detailed records of all verification activities and create a scheduled maintenance program for your calibration tools. If you're working with critical equipment, prioritize their verification schedule and use automated reminders to stay on track.
Remember to use only certified standards when checking accuracy, and ascertain your operators are properly trained in verification procedures. By following manufacturer instructions and keeping thorough records, you'll maintain the reliability of your calibration tools and, ultimately, your static control monitoring system.
Schedule Preventive Testing Dates
Consistently scheduling preventive testing dates forms the cornerstone of an effective static control monitoring program. To maintain compliance with ANSI/ESD S20.20 standards and guarantee your equipment's continuous functionality, you'll need to implement a systematic approach to preventive testing.
Start by creating a time-based schedule that aligns with your equipment's manufacturer guidelines and usage patterns. Regular assessment of Risk Priority Numbers will help determine which equipment needs the most frequent testing. You'll want to use preventive maintenance software to track and manage these activities, setting up automatic reminders for upcoming tasks.
Make sure you're including detailed checklists and instructions for your technicians to follow during monthly checks of your ESD Process Control System.
You can maximize the benefits of your calibration schedule by identifying critical assets that require regular monitoring. You'll see reduced downtime, increased productivity, and longer equipment lifespan when you maintain consistent testing dates.
Train your workers on the preventive maintenance schedule and guarantee they understand their roles in the process. By establishing clear testing dates and following through with regular calibration checks, you'll be able to predict and prevent potential ESD events while maintaining the integrity of your static control system.
Quarterly Facility Assessment Protocol
Your facility audit must begin with an extensive mapping of static-sensitive zones, following the established quarterly assessment protocol to identify areas of highest risk.
You'll need to document each zone's unique characteristics, including humidity levels, equipment placement, and existing static control measures during your walkthrough inspection. Similar to healthcare facilities that require systematic data collection, implement comprehensive checklists and reporting tools to maintain detailed records.
Based on your findings, you can then develop targeted action steps that address specific static control needs in each identified zone, ensuring thorough protection across your manufacturing space.
Facility Audit Action Steps
A well-structured facility audit protocol forms the backbone of effective static control monitoring.
Focusing on quality and safety helps protect both workers and products during manufacturing operations. You'll need to start with thorough pre-audit preparations, including document reviews and customized checklists that align with your industry's standards. Remember to notify facility management and schedule interviews with key personnel before beginning the assessment.
During the on-site audit phase, focus on these critical actions:
- Conduct systematic reviews using your prepared checklists, paying special attention to equipment inspection and material handling compliance.
- Document all observations meticulously, including non-compliance issues, and categorize them by severity.
- Interview staff members to verify their understanding of static control procedures and assess training effectiveness.
After completing your audit, compile a detailed report outlining your findings and recommended corrective actions.
You'll want to prioritize CAPA measures based on severity and implement them promptly. Schedule follow-up assessments to verify that these corrections are working effectively.
Make certain you're maintaining continuous monitoring between quarterly assessments to catch potential issues early. This proactive approach helps guarantee your static control measures remain consistently effective and compliant with industry regulations.
Static Risk Zone Mapping
Strategic zone mapping forms the foundation of effective static control in manufacturing facilities. You'll need to conduct quarterly assessments using proven tools like HAZOP and SCOR to identify and categorize risk zones throughout your facility. By implementing a systematic mapping process, you're creating a proactive approach to risk management rather than reacting to problems after they occur. Establishing a central data repository streamlines the assessment process and ensures consistent tracking of supplier information across all zones.
Assessment Area | Action Required |
---|---|
Data Collection | Gather facility information, supplier networks, and material flow patterns |
Risk Analysis | Apply HAZOP and SCOR tools to identify critical risk zones |
Documentation | Create visual maps and maintain detailed risk registers |
Your mapping process must include specific attention to temperature-controlled areas and facility conditions using the FCI index. When you're conducting your quarterly assessments, guarantee you're documenting all findings in your risk register and updating your visual maps accordingly. You'll need to train your team on risk identification and mitigation procedures, maintaining awareness through regular communication. Don't forget to integrate feedback from previous assessments into your continuous improvement process, guaranteeing your static risk zone mapping remains relevant and effective for your facility's specific needs.
Environmental Monitoring Frequency Guidelines
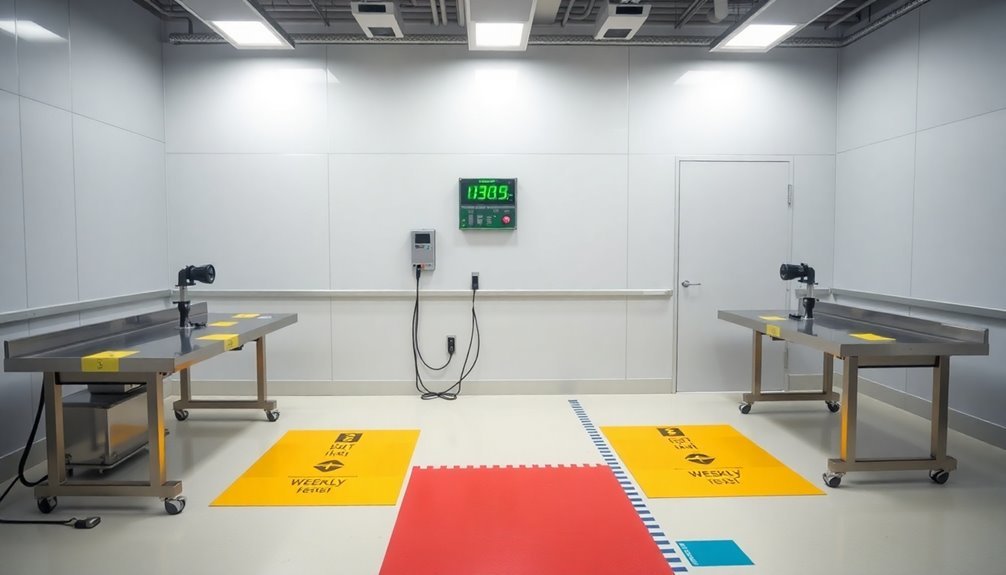
Establishing proper environmental monitoring frequencies is essential for maintaining cleanroom integrity and product quality. You'll need to align your monitoring schedule with regulatory requirements while considering your specific cleanroom grade and process risks.
For Grade A areas, you must implement continuous viable air monitoring throughout critical processes and equipment assembly. Grade B areas require similar vigilance, though you can adjust frequencies based on your aseptic processing risk assessment.
When monitoring Grade C and D areas, you can reduce sampling frequency while maintaining consistent sample volumes.
- Set monitoring durations of 1-4 hours for lower-class cleanrooms to capture representative environmental snapshots.
- Include post-operational monitoring after disinfection and batch completion to verify cleanliness.
- Adjust your monitoring frequency based on trend analysis and historical data from your facility.
Your monitoring plan should reflect product sensitivity and process criticality. Remember to document your sampling methods, whether you're using active air sampling, surface contact plates, or personnel monitoring.
When you detect deviations, implement immediate corrective actions according to your predefined procedures and maintain detailed records for continuous improvement.
Annual Compliance Audit Schedule
While maintaining a cleanroom environment requires daily vigilance, your annual compliance audit schedule serves as a thorough checkpoint for your static control program.
You'll need to align your audit frequency with both industry requirements and risk levels associated with your manufacturing processes.
For high-risk areas of your static control program, you should conduct audits quarterly or semi-annually. Don't wait for the annual review if these critical processes could impact product quality.
Lower-risk areas can follow the standard annual schedule, provided they've shown consistent compliance.
You'll want to structure your audit schedule using a risk-based approach. Start by identifying areas that have undergone recent changes or have historically shown compliance issues.
Make sure you've allocated sufficient resources and trained auditors for each scheduled assessment. During the audit, document all observations thoroughly and gather concrete evidence for any nonconformities you identify.
Remember to follow up on all findings with appropriate corrective actions. You should regularly review and adjust your audit schedule based on findings and changing requirements.
Keep your auditors' training current, especially regarding new regulatory standards or industry best practices for static control monitoring.
Personnel Training Review Periods
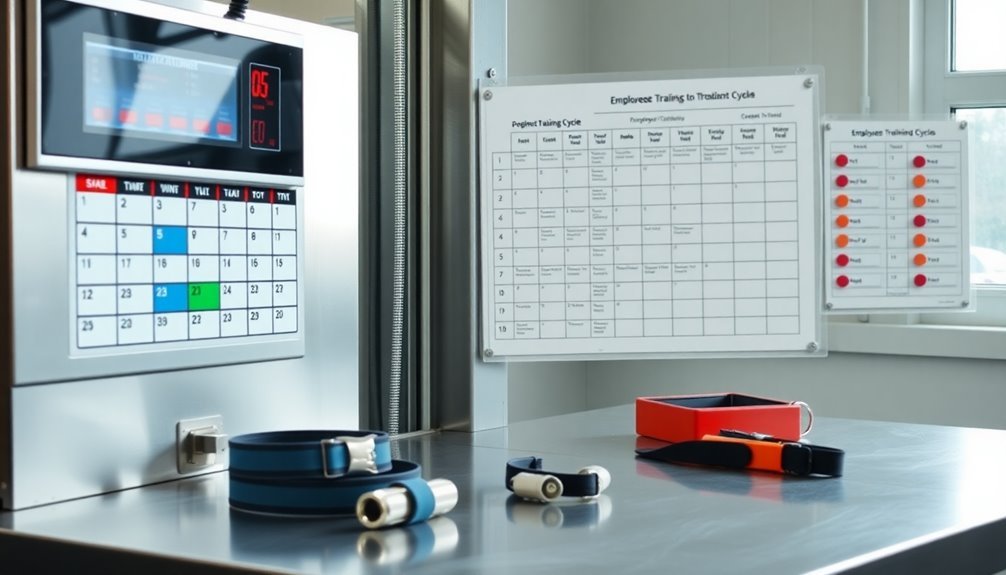
You'll want to establish quarterly competency assessments to confirm your team's understanding of ESD control procedures and identify any knowledge gaps.
Your training effectiveness measurements should align with regular compliance verification cycles, allowing you to track improvements and address deficiencies promptly.
Knowledge tests need updating every 3-5 years based on risk assessment, though high-risk areas require annual updates to guarantee personnel stay current with critical control measures.
Quarterly Competency Assessment Cycles
Maintaining robust quarterly competency assessments is essential for manufacturers implementing static control programs. You'll need to schedule these evaluations during low-production periods to minimize operational disruptions while guaranteeing your team stays current with static control protocols and procedures.
Make your assessment cycles more effective by implementing these key strategies:
- Combine hands-on training with discussions and blended learning approaches to reinforce static control concepts
- Use documented processes and specific assessment tools like Form 21600-02 to evaluate competency levels
- Schedule retraining sessions whenever procedures are updated or when employees need additional support
Your quarterly assessments should align with broader business objectives while supporting continuous improvement. Develop individualized training plans based on each employee's major responsibilities, and guarantee Quality Assurance maintains oversight of the assessment process.
You'll want to utilize both in-person and online platforms to deliver training content effectively. Track your team's progress through regular monitoring and evaluation of their training status.
Remember to collect feedback from your employees after each assessment cycle – this input helps refine and improve your training program's effectiveness while maintaining high static control standards.
Training Effectiveness Measurement Windows
Building upon your quarterly competency assessments, establishing clear measurement windows for training effectiveness creates a structured approach to personnel development.
You'll need to choose between quarterly, mid-year, or annual review cycles based on your facility's specific needs and resources.
Quarterly reviews offer frequent touchpoints to address performance gaps quickly and align with your fiscal calendar. While they require more administrative resources, they're ideal for tracking rapid skill development and project completion metrics.
Mid-year reviews strike a balance between thorough evaluation and manageable workload, giving employees sufficient time to demonstrate improvement in static control practices.
Annual reviews provide the most thorough assessment window but shouldn't delay necessary performance interventions.
You'll want to implement the Kirkpatrick Model across your chosen measurement window to evaluate training effectiveness systematically. This four-level approach helps you track immediate reactions, learning outcomes, behavioral changes, and bottom-line results of your static control training programs.
Update Knowledge Test Intervals
Effective knowledge test intervals form the backbone of a robust personnel training program. You'll need to establish a balanced frequency that avoids overwhelming your team while guaranteeing consistent knowledge retention. Base your intervals on historical data, technical analysis, and demonstrated control through regular assessments.
To maintain an efficient testing schedule, consider these vital factors:
- Keep your assessments short and focused on specific learning objectives, utilizing clear instructions and a low-stress environment.
- Monitor calibration status continuously to prevent outdated standards from affecting your training effectiveness.
- Adjust intervals based on measurement assurance data and feedback from previous knowledge checks.
You'll want your Technical Manager to oversee the adjustment of intervals using valid statistical analysis. Make sure your knowledge checks remain relevant to job requirements and align with your training program's structure.
When implementing updates, use pilot testing with small groups to identify potential issues or unclear questions. Remember to integrate feedback from each assessment to enhance your training program's effectiveness.
Surface Resistance Testing Timeline
Regular surface resistance testing checks form the backbone of a robust ESD control program. You'll need to conduct these tests quarterly to maintain effective static control in your manufacturing environment.
When performing these checks, you should use a calibrated surface resistance meter to measure both resistance to ground (RTG) and point-to-point resistance (RTT) following ASTM D257 standards.
Don't skip testing worn or dirty areas of your worksurfaces – use non-random sampling to focus on these potential trouble spots. If you're dealing with critical manufacturing processes, you might need to implement continuous monitoring systems.
Remember to maintain a lower resistance limit of 1 x 10^6 ohms for your worksurfaces to prevent Charged Device Model damage.
Your testing procedure should include placing standard-sized specimens between two electrodes and applying voltage for 60 seconds to measure resistance. You'll need to document all results in your database for quality control purposes.
While quarterly testing is standard, you should adjust your testing frequency based on your specific production environment and product sensitivity levels.
Keep your testing equipment properly calibrated to guarantee accurate measurements, and integrate these checks into your Static Management Program for thorough compliance verification.
Emergency Response Testing Intervals
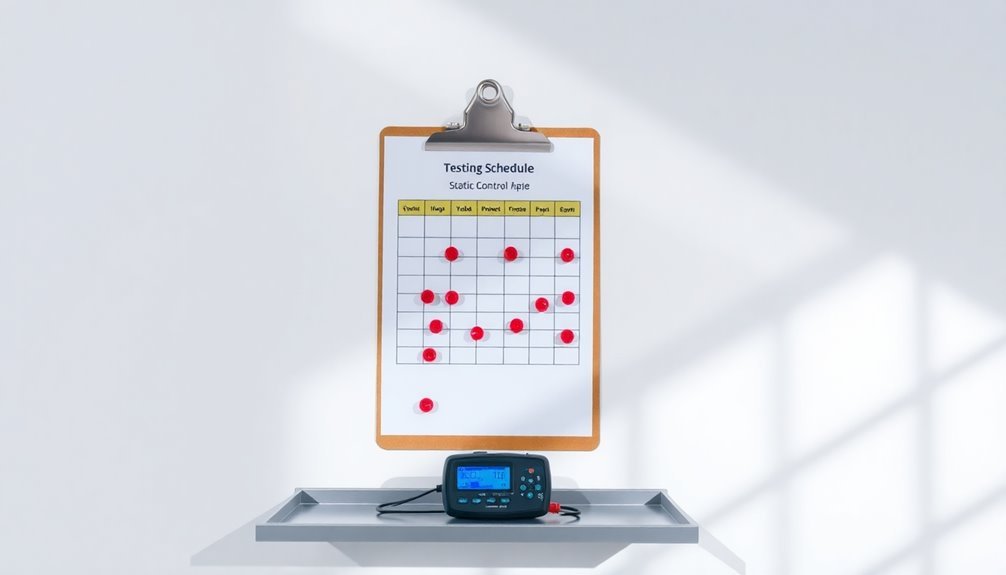
In accordance with NFPA 110 standards, your emergency response testing program needs to follow specific intervals for maximum reliability. You'll need to conduct weekly inspections of all emergency power system components, while performing monthly tests under load for your generator sets and transfer switches.
Don't forget the annual testing requirement for circuit breakers and other critical components. Your thorough testing schedule should include these key intervals:
- Weekly visual inspections of all EPSS components and fuel systems
- Monthly operational tests under load conditions for generators and transfer switches
- Full system testing annually, with a detailed 36-month load capacity evaluation
You'll want to verify qualified personnel perform all testing and maintain detailed records of each inspection.
While 44% of organizations test their emergency notification systems twice yearly, and 14% opt for monthly testing, you should determine your testing frequency based on your specific needs and compliance requirements.
Remember to balance testing frequency to avoid user desensitization while maintaining system reliability. Keep manufacturer guidelines in mind, and always document your test results for compliance and troubleshooting purposes.
This structured approach will help maintain your emergency response system's readiness.
ESD Protection Verification Schedule
Setting up an extensive ESD protection verification schedule secures your manufacturing processes remain protected from costly static damage.
You'll need to establish a thorough compliance verification plan that includes specific intervals for testing all your ESD control products and equipment.
Start by creating a detailed checklist of daily verifications, focusing on wrist straps that aren't continuously monitored.
Make sure you're testing your grounding systems regularly, as they're essential for effective static control.
You'll want to implement a mix of daily, weekly, monthly, quarterly, and semi-annual checks based on your specific needs and equipment requirements.
You must follow ANSI/ESD S20.20 standards while developing your verification schedule.
Document all your testing activities thoroughly, as this documentation proves compliance and helps identify trends in equipment performance.
Don't forget to train your personnel regularly on proper ESD control procedures and maintain clear identification of ESD-susceptible items.
Monitor your failure data carefully – you can potentially extend the time between verifications if your results consistently show reliability.
Remember to conduct both internal and external audits to confirm you're meeting all planned requirements and maintaining effective static control throughout your facility.
Frequently Asked Questions
How Do Seasonal Weather Changes Affect Static Control Monitoring Requirements?
You'll need more frequent static monitoring during dry, cold winters since low humidity increases static build-up. During warmer, humid seasons, you can reduce monitoring frequency while maintaining regular checks.
What Backup Systems Should Be in Place if Monitoring Equipment Fails?
You'll need a UPS system for power backup, redundant monitoring devices for continuous coverage, data loggers for automatic recording, and backup sensors to maintain uninterrupted static control monitoring during equipment failures.
Can Static Monitoring Systems Integrate With Existing Manufacturing Execution Software?
Yes, you'll find MESConnect fully integrates your static monitoring systems with existing MES software through OPC UA protocols, enabling real-time data flow, centralized control, and automated reporting across your manufacturing operations.
How Does Product Material Composition Influence Static Control Monitoring Schedules?
You'll need to adjust your monitoring frequency based on your product's materials. Non-conductive plastics require more frequent checks, while conductive materials need less monitoring due to their natural static-dissipating properties.
When Should Static Monitoring Frequencies Be Adjusted for Different Shift Patterns?
You should adjust static monitoring frequencies when switching between fixed and variable shifts, implementing new work schedules, or observing changes in production patterns. It's essential to align thresholds with actual workplace activity.
In Summary
Following these static control monitoring schedules will help you maintain a robust ESD protection program in your manufacturing facility. You'll need to stay consistent with your documentation, testing, and verification processes. Don't skip scheduled checks or postpone calibrations – they're essential for preventing costly damage to sensitive components. Remember, your ESD control system is only as effective as your commitment to monitoring it.
Leave a Reply